
J. Cent. South Univ. (2018) 25: 2349-2359
DOI: https://doi.org/10.1007/s11771-018-3919-0

Safe utilization of chromium-bearing vanadate residue by recovery of vanadium and chromium based on calcium circulation
LIU Gui-hua(刘桂华), WU Guo-yu(吴国玉), JIANG Hai-lang(江海浪), QI Tian-gui(齐天贵), PENG Zhi-hong(彭志宏), ZHOU Qiu-sheng(周秋生), LI Xiao-bin(李小斌)
School of Metallurgy and Environment, Central South University, Changsha 410083, China
Central South University Press and Springer-Verlag GmbH Germany, part of Springer Nature 2018
Abstract: A safe, economical treatment of hazardous chromium-bearing vanadate residue (CVR) will significantly benefit the clean production of chromate-bearing salts. This study investigated recovery of sodium vanadate and sodium chromate from CVR in sodium bicarbonate solution. Results indicate that the stability of calcium vanadate and calcium chromate depends on pH and [HCO3-]. CaV2O6·4H2O transforms into CaV2O6·4H2O, CaV2O6·2H2O, CaV2O6, Ca2V2O7·2H2O, and Ca5(VO4)3(OH) when pH increases from 7.51 to 12.32. Increasing pH and reducing CVR dosage improve the vanadate extraction rate, and high V2O5 and Na2Cr2O7·2H2O extraction rates are achieved in dilute NaHCO3 solution. Moreover, addition of NaOH positively contributes to the recovery of vanadate and chromate from CVR. Over 95% V2O5 and Na2Cr2O7·2H2O in CVR can be extracted from 60 g/L NaHCO3 and 30 g/L NaOH solutions at 90 °C for 2 h. In order to reduce the hazardous residue containing chromate after recovery of CVR, calcium circulation is presented. Results show that more than 60% lime can be saved with fresh residue addition to remove vanadate from sodium chromate solution due to the active CaCO3. Moreover, no lime is required in removal of vanadate when the roasting residue is added. Therefore, a novel process is developed for utilization of CVR.
Key words: chromium-bearing vanadate residue; NaHCO3; calcium vanadate; calcium chromate; sodium chromate; calcium circulation
Cite this article as: LIU Gui-hua, WU Guo-yu, JIANG Hai-lang, QI Tian-gui, PENG Zhi-hong, ZHOU Qiu-sheng, LI Xiao-bin. Safe utilization of chromium-bearing vanadate residue by recovery of vanadium and chromium based on calcium circulation [J]. Journal of Central South University, 2018, 25(10): 2349–2359. DOI: https://doi.org/10.1007/ s11771-018-3919-0.
1 Introduction
Chromium-bearing vanadate residue (CVR) is precipitated from sodium chromate solution during vanadate anion removal by adding excess lime in the current lime-free roasting process [1]. CVR contains calcium vanadate (about 3% V2O5) and calcium chromate (about 10% Na2Cr2O7·2H2O), which is extremely hazardous waste. CVR is often stored in considerably expensive manner because of the presence of Cr(VI) [2–5]. However, CVR is a valuable resource because it contains substantial amounts of vanadium, chromium [6–8], and calcium. Therefore, a safe, economical process should be developed to utilize CVR comprehensively.
Similar to CVR in composition, chromium- bearing vanadate slag is produced during iron- making process [9]. The traditional vanadium and chromium extraction is carried out by roasting with sodium-bearing salts (such as NaCl, Na2SO4, and Na2CO3) and subsequent leaching in carbonate solution [10–15], and more than 90% vanadium and chromium, respectively. However, high production cost and considerable amount of toxic SO2 or Cl2 gases released during roasting limit its application. Furthermore, some chromium(VI)-bearing compounds left in the residue after leaching still requires expensive subsequent treatment.
Recovery of V2O5 and Na2Cr2O7·2H2O from CVR is scarcely studied because low vanadate concentration in sodium chromate solution only presents minimal negative effect on chromate- bearing salts production by the traditional lime-soda roasting process. Nevertheless, the CVR amount remarkably increases in the extensive application of lime-free roasting, and safe utilization of CVR is extremely difficult due to existence of various calcium-bearing compounds generated from CrO42–, SO42–, CO32–, Al(OH)4–, SiO32– and various vanadate anion in sodium chromate solution. WEBER et al [16] reported that 97.2% V2O5 and 95.9% Na2Cr2O7·2H2O in CVR were recovered from the concentrated solution (387.5 g/L Na2CO3) at 90 °C for 2 h; while low V2O5 and Na2Cr2O7·2H2O extraction rates were found in the mixed solution of 336.4 g/L NaHCO3 and 90.9 g/L Na2CO3. However, the residue containing 0.67 wt% V2O5 and 1.02 wt% Na2Cr2O7·2H2O is a hazardous waste, and it is extremely difficult to extract 100% chromate (Cr(VI)) from the residue because of insoluble calcium-bearing salts (KspCa(OH)2=2.5×10–6, KspCaCO3=2.8×10–9, KspCaCrO4=7.1×10–4, 298 K) and less solubility of calcium chromate at elevating temperature [17, 18]. In addition, the resulting concentrated sodium carbonate solution containing vanadate requires considerable amount of sulfuric acid to precipitate V2O5·xH2O, and then a substantial hazardous waste water containing concentrated Na2SO4 is produced.
With the increase of CVR, a novel technology without hazardous solid waste and waste water is strongly expected. Considering that Ca(HCO3)2 is soluble in weak alkaline solution, and that extraction of V2O5 and Na2Cr2O7·2H2O depends on the conversion of calcium-bearing salts, a novel method is then presented as follows: CVR is leached in dilute sodium bicarbonate solution (pH<9) to recover V2O5 and Na2Cr2O7·2H2O, calcium carbonate in the residue from leaching process is then returned to remove vanadate anion in sodium chromate, no hazardous waste is finally discharged. Thus, the paper firstly studied the reaction behavior of calcium vanadate and calcium chromate in NaHCO3 solution by thermodynamic calculation. The effects of temperature, pH, and CVR dosage on the extraction rates of vanadium and chromium in dilute sodium bicarbonate solution were then discussed. In addition, the wet and roasting residues were returned to remove vanadate anion in sodium chromate solution. Finally, a safe, economical process was presented. Results will improve the understanding about conversion of insoluble calcium-bearing compounds and further benefit the green production of chromate-bearing salts.
2 Thermodynamic analysis on reaction behavior of calcium chromate and calcium vanadate in NaHCO3 solution
2.1 Thermodynamic calculations
The solubility of calcium vanadate and calcium chromate is related to the extraction rates of sodium vanadate and sodium chromate.
Given that CVR is precipitated at pH range of 7–14, calcium vanadate may exist in the forms of CaV2O6, Ca2V2O7, Ca3V2O8, and CaCrO4 [19]. Moreover, VO43-, V2O74-, VO3-, HVO42-, H2VO4-, HV2O73-, H2V2O72-, CrO42-, HCrO4-, or Cr2O72- ions may also exist in a solution of pH>5 [20–22]. Table 1 gives the Gibbs free energy of the above substances. Table 2 provides a list of the reaction equations and corresponding reaction constants at 25 °C.
On basis of the mass balance and charge neutrality, the total concentrations of vanadate and chromate anions (denoted as [V]T and [Cr]T, respectively) are expressed as follows:
[V]T=[VO43–]+2×[V2O74–]+[VO3–]+[HVO42–]+ [H2VO4–]+2×[HV2O73–]+2×[H2V2O72–] (16)
[Cr]T=[CrO42–]+[HCrO4–]+[H2CrO4]+2×[Cr2O72–] (17)
Table 1 Gibbs free energy of vanadium ions, calcium ions, or compounds at 25 °C [23, 24]

Table 2 Reaction equation and their equilibrium constant at 25 °C [25, 26]
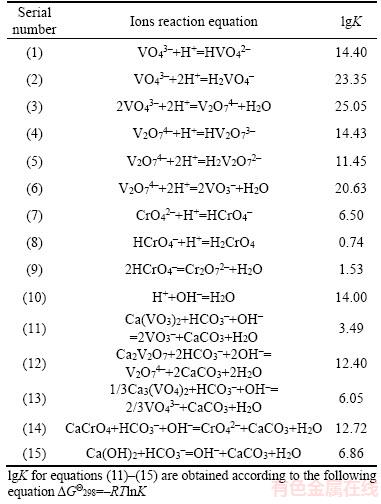
Assuming that the ion concentration is nearly equal to its activity in the dilute solution, the distribution of various vanadate anions was calculated at different pH values.
2.2 Reaction behavior of calcium vanadate
Figure 1 shows the equilibrium phase diagram of calcium vanadate in the dilute NaHCO3 solution. CaV2O6, Ca2V2O7, Ca3V2O8, and Ca(OH)2 are stable in [HCO3-] <10-7 mol/L solution at the corresponding pH ranges of 6.00–10.12, 10.12– 10.83, 10.83–13.84, and >13.84, respectively. The results in Figure 1 show that various calcium vanadate can be changed into Ca(OH)2 or CaCO3 in alkaline solution, and suggest that CVR should be leached in the alkaline system. Additionally, the increase in pH and [HCO3-] favors the conversion of calcium vanadate to CaCO3, and the increase in total vanadate concentration widens the region of various calcium vanadates.
2.3 Reaction behavior of calcium chromate
Figure 2 presents the phase diagram of calcium chromate in the dilute NaHCO3 solution. Results indicate that CaCrO4 exists stably at the pH range of 6.00–10.51. In addition, increasing chromate ion concentration favors the formation of CaCrO4. CaCrO4 can transform into CaCO3 and Ca(OH)2 with the increase in pH, increase of HCO3– concentration promotes the formation of CaCO3.
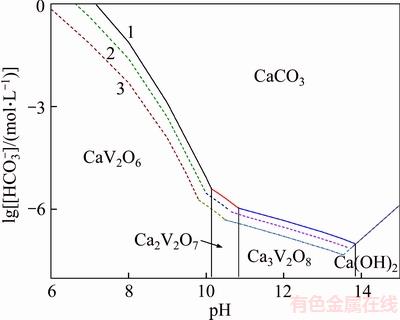
Figure 1 Phase diagram of calcium vanadium in HCO3-– CO32- system at 25 °C (1–[V]T=0.1 mol/L, 2–[V]T=0.08 mol/L, 3–[V]T=0.02 mol/L)

Figure 2 Phase diagram of calcium chromate in HCO3-–CO32- system at 25 °C (1–[Cr]T=0.08 mol/L, 2–[Cr]T=0.04 mol/L, 3–[Cr]T=0.01 mol/L)
In brief, increase in HCO3– concentration and pH benefits the transformation of calcium chromate and calcium vanadate into calcium carbonate, meanwhile the formation of soluble Ca(HCO3)2 may not restrain the leaching process. In addition, half of H2SO4 will be saved during precipitation of V2O5·xH2O in resulting NaHCO3 leaching system compared in resulting Na2CO3 solution [14, 15] in theory. Therefore, the treatment of CVR in the dilute NaHCO3 solution was further investigated in the following experiments.
3 Experiment
3.1 Experimental materials
Sodium dichromate, sodium bicarbonate, and sodium hydroxide (analytical purity) were used to prepare all solutions with deionized water. The average CVR particle size (d50) (Gansu Jin Shi Chemical Co., Ltd.) was 27.69 μm. Table 3 provides a list of the CVR ingredients (chromium and vanadium contents in solid sample are often denoted as Na2Cr2O7·2H2O and V2O5, respectively).
Table 3 Ingredients of chromium-bearing vanadate residue (CVR) (mass fraction, %)
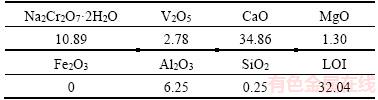
Figure 3 shows that there are CaSO4·2H2O, CaCrO4, Ca1.5Na3.5(OH)0.55(SO4)3(H2O)0.44, and CaCO3 in CVR. However, the peaks assigned to calcium vanadate were not observed due to the low content or peak overlap. Figure 4 illustrates the X-ray diffraction (XRD) patterns of the CVR.
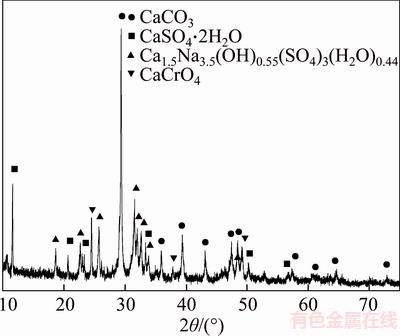
Figure 3 X-ray diffraction (XRD) patterns of CVR
In addition, to further elucidate the phase evolution in the different solutions, pure calcium vanadate was synthesized using CaCl2 and NaVO3 according to stoichiometric ratio at room temperature in solution of pH 7 for 4 h. Following filtration and washing with deionized water, the synthetic calcium vanadate was dried at 50 °C for 10 h. Only CaV2O6·4H2O without other phases was observed in the synthetic calcium vanadate (as shown in Figure 4), which was different from Ca3(VO4)2·xH2O formed in the strong alkaline solution (pH>12) during removal of vanadate in sodium chromate with adding lime.
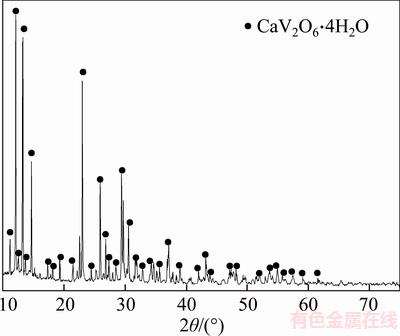
Figure 4 XRD patterns of synthetic CaV2O6·4H2O
3.2 Procedures
CVR leaching in NaHCO3 solution was carried out in a stainless bomb (150 mL) heated with glycerol bath. The leaching slurry was filtered after the leaching process. The residue (filter cake) was washed with hot distilled water. The filtrate was then diluted to 1000 mL to determine the concentration of chromate, and the dried residue was used to detect the vanadium and chromium contents as well as to analyse phase evolution of calcium-bearing compounds.
Removal of vanadate anion in sodium chromate solution was also finished in bomb as mention above.
3.3 Methods
The vanadium content in the solid sample was determined as follows. Sample was mixed with Na2O2 and NaOH, and the mixture was then roasted at 750 °C for 30 min. After leaching in water and slurry vacuum filtration, the resulting solution was used to determine the vanadium concentration [27]. Moreover, the chromium content in solid sample was detected according to the following procedure: sample was dissolved in sulfuric and phosphoric acids according to a molar ratio of 1:1, and the resulting solution was titrated with ferrous ammonium sulfate to determine the chromium concentration [28]. Finally, the extraction rates of chromate or vanadate (denoted as Na2Cr2O7·2H2O and V2O5) were obtained.
XRD patterns were conducted with D8 X-ray diffraction system (Philips), and scanning was finished at a rate of 10 (°)/min between 10° and 75°.
4 Results and discussion
4.1 Extraction of vanadate and chromate from CVR in NaHCO3 solution
4.1.1 Effect of NaHCO3 concentration
Calcium vanadate may be reacted with NaHCO3 solution in theory according to Eq. (11) in Table 2. Increasing NaHCO3 concentration benefits the transformation of calcium vanadate and calcium chromate into calcium carbonate, as displayed in Figures 2 and 3. Moreover, decreasing NaHCO3 concentration will significantly reduce H2SO4 consumption in subsequent V2O5·xH2O precipitation. Thus, the effect of NaHCO3 concentration on the extraction rate of vanadate and chromate was studied, and the results are presented in Table 4 and Figure 5.
As shown in Table 4, the increase of NaHCO3 concentration remarkably reduces the V2O5 and Na2Cr2O7·2H2O contents in residue. 0.32% V2O5 in residue can be found in 100 g/L NaHCO3 solution, which is lower than 0.67% V2O5 in concentrated Na2CO3 solution [16]. This observation is mainly due to the low pH values in NaHCO3 solution compared with the same concentration of Na2CO3 solutions [29]. Another reason may lie in the formation of soluble Ca(HCO3)2 in NaHCO3 solution. Figure 5 shows the sharp increase in V2O5 extraction rate in NaHCO3 solution (<60 g/L) and slow increases in solution of above 60 g/L NaHCO3. By contrast, over 85% extraction rate of Na2Cr2O7·2H2O can be observed, while increase in NaHCO3 concentration slowly raises the extraction rate of Na2Cr2O7·2H2O. Thus, 60 g/L NaHCO3 concentration is recommended.
Table 4 Effect of NaHCO3 concentration on vanadate and chromate contents in residue
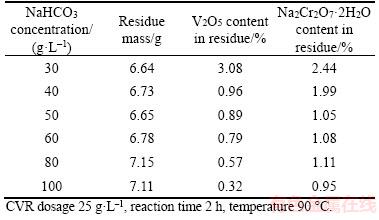
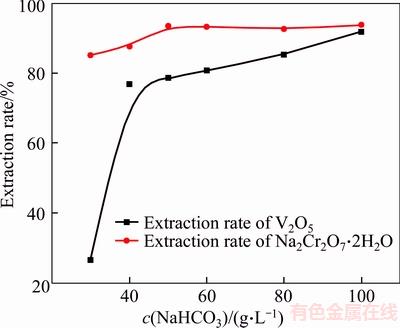
Figure 5 Effect of NaHCO3 concentration on extraction rate of vanadate CVR dosage 25 (g/L), reaction time 2 h, temperature 90 °C
4.1.2 Effect of CVR dosage
Figure 6 shows the effect of CVR dosage on the extraction rate of vanadate and chromate.
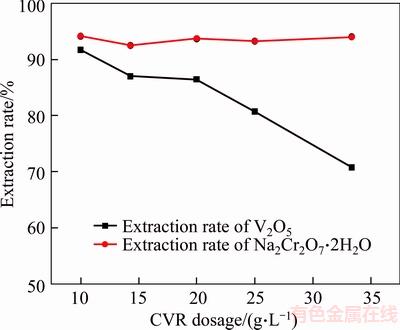
Figure 6 Effect of CVR dosage on extraction rate of vanadate and chromate NaHCO3 60 g/L reaction time 2 h , temperature 90 °C
Figure 6 indicates that decreasing CVR dosage remarkably benefits the extraction rate of V2O5. Similar to the results in Figure 6, the extraction rate of Na2Cr2O7·2H2O nearly remains constant at approximately 93% within CVR dosage range of 10 g/L–35 g/L. These findings are mainly attributed to considerable sodium chromate incorporated into the coarse CVR particle during vanadate removal from the solution and easy dissolution of sodium chromate during leaching. Moreover, calcium chromate may readily change into calcium carbonate in NaHCO3 solution [15]. Thus, the CVR dosage is 20 g/L.
4.1.3 Effect of pH
Increasing pH favors the transformation of calcium vanadate and calcium chromate into calcium carbonate in NaHCO3 solution, as illustrated in Figures 2 and 3. Therefore, NaOH was added to adjust the pH of NaHCO3 solution. Table 5 shows the effect of pH on the extraction rate of V2O5 and Na2Cr2O7·2H2O.
As shown in Table 5, increasing pH decreases the V2O5 and Na2Cr2O7·2H2O contents in residue, so does the residue mass, the extraction rates of vanadate and chromate correspondingly increase. This observation suggests that NaOH accelerates the phase evolution from calcium vanadate to CaCO3 and enhances CaCO3 stability. However, the residue containing 0.69% Na2Cr2O7·2H2O is still defined as a hazardous waste, although the extraction rates of V2O5 and Na2Cr2O7·2H2O reach 96.20% and 95.94%, respectively.
NaOH is generally assumed to react preferentially with NaHCO3 to form Na2CO3, and then Na2CO3 is deemed to react with CVR. To further determine the role of NaOH, Na2CO3 is added into NaHCO3 solution when the total NaHCO3 concentration (Na2CO3 is expressed as NaHCO3) remains constant at 60 g/L. The results are shown in Table 6.
Table 6 indicates that the highest content of V2O5 and Na2Cr2O7·2H2O in residue is found in Na2CO3 solution (No. 4). NaOH addition in Na2CO3 solution not only decreases V2O5 and Na2Cr2O7·2H2O content in residue, but also reduces the residue mass (No. 3). Moreover, NaHCO3 addition in Na2CO3 solution achieves high extraction rate of V2O5 or Na2Cr2O7·2H2O. All results suggest that high pH and NaHCO3 favors the recovery of vanadate and chromate from CVR. Furthermore, the Na2Cr2O7·2H2O content in residue after leaching in NaHCO3+Na2CO3 solution is higher than that in Na2CO3+NaOH (No. 3) and in NaHCO3+NaOH (Table 5, No. 2–6) solutions. Meanwhile, the extraction rate of Na2Cr2O7·2H2O in NaHCO3+Na2CO3 solution is lower than 95.94%. These results demonstrate that NaOH plays a positive role. HCO3- is proven to react slowly with OH- [29, 30]. Thus, considerable amount of HCO3- will favor the formation of Ca(HCO3)2 and benefit the recovery of vanadate and chromate from CVR.
4.2 Effect of pH on phase evolution of calcium vanadate
To further elucidate the recovery mechanism of vanadate from CVR, the effect of pH on the phase evolution of calcium vanadate is shown in Figure 7.
As pH increases in Figure 7, the synthetic CaV2O6·4H2O transforms into CaV2O6·2H2O, CaV2O6, Ca2V2O7·2H2O, and Ca5(VO4)3(OH) in sequence. The transformation of CaV2O6·4H2O to Ca5(VO4)3(OH) also decreases the molar ratio between vanadium and calcium, which favors the extraction of vanadate in NaHCO3 solution [31–33]. This fact confirms that increasing pH benefits the CVR leaching process. Moreover, the complex phase transformation of calcium vanadate implies occurrence of co-precipitation, resulting in lower vanadate extraction rate compared with that of chromate in NaHCO3 solution, as displayed in Figure 6.
Table 5 Effect of pH on extraction rate of vanadate and chromate
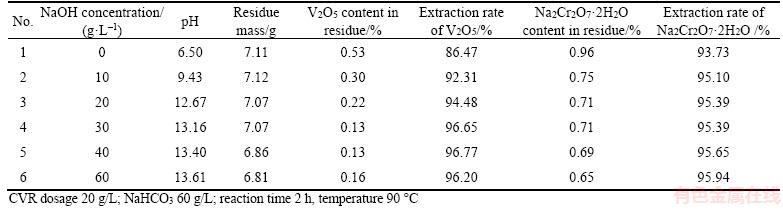
Table 6 Effect of Na2CO3 on extraction rate of vanadate and chromate anions
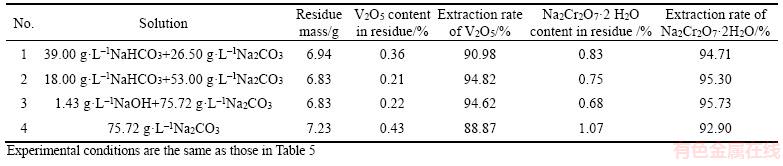
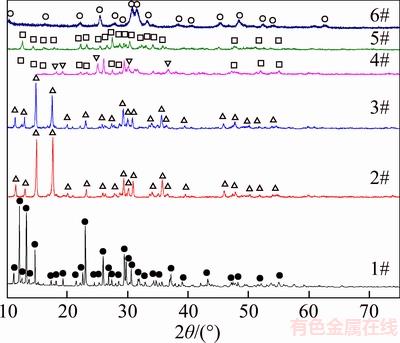
Figure 7 XRD patterns of residue after synthetic CaV2O6·4H2O reacted with water at different pH (●–CaV2O6·4H2O, △–CaV2O6·2H2O, ▽–CaV2O6, □–Ca2V2O7·2H2O, ○–Ca5(VO4)3(OH), 1#–synthetic CaV2O6·4H2O, 2#–pH=7.51, 3#–pH=9.07, 4#–pH=10.04, 5#–pH=11.07, 6#–pH=12.32, Reaction time 2 h, temperature 25 °C, calcium vanadate 10 g/L)
5 Removal of vanadate anion in sodium chromate solution by adding residue or roasting residue
Although extraction of vanadate and chromate is fairly efficient, residue with more than 0.13% V2O5 and 0.71% Na2Cr2O7·2H2O is still identified as the hazardous waste. Moreover, the predominant CaCO3 in residue can be changed into CaO, Ca(OH)2, of which CaO is used to remove vanadate ion from sodium chromate solution in chromate- bearing salts production. Therefore, circulation utilization of calcium element is proposed to reduce CVR amount or to eliminate waste solid resulted from CVR. In the paper, two approaches to remove vanadate were investigated by adding wet fresh residue or the roasted residue.
5.1 Removal of vanadate from sodium chromate by adding residue
Our experimental results showed that the wet fresh CaCO3 could readily transform into CaC2O4·H2O and 3CaO·Al2O3·6H2O in sodium oxalate and sodium aluminate solution, respectively [34]. Likewise, the fresh residue was added into sodium chromate solution at pH ~7 to precipitate calcium vanadate, and the results can be seen in Table 7.
Table 7 Effect of pH on removal of vanadate anion from sodium chromate solution by adding fresh residue
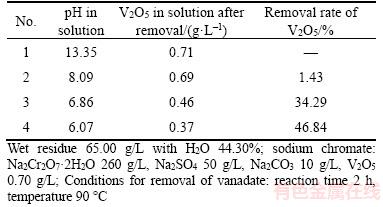
Table 7 shows that increasing pH improves the removal rate of V2O5, and that the removal rate is 46.84% at pH 6.07. These facts prove the removal of vanadate from sodium chromate solution by adding wet fresh residue although solubility of some calcium vanadate is more than calcium carbonate (KspCaCO3=2.8×10–9, KspCa(VO3)2·4H2O=3.7×10–5, KspCa2V2O7·2.5H2O=2.05×10–6). However, no transformation occurs in the strong alkaline solution, although the stable Ca3(VO4)2 in Figure 7 is formed (KspCa(VO4)2·8.5H2O=2.62×10–11). The observations prove that the fresh calcium carbonate is active.
Less than 90% V2O5 removal rate cannot satisfy the production requirement of chromate- bearing salts. Therefore, the fresh residue, together with lime, is added into solution to remove vanadate. Table 8 provides a list of the results.
As shown in Table 8, the vanadate removal rate increases with addition of lime in presence of the fresh residue. Over 91.63% vanadate removal rate is achieved with addition of 4 g/L lime. By contrast, over 10 g/L*lime is added during vanadate removal in practice. These facts suggest that over 60% lime can be saved. In practice, the application of the fresh residue in removal of vanadate demonstrated that about 50% lime was saved and reduced about over 55% CVR.
Table 8 Effect of residue as additive on vanadate removal

5.2 Removal of vanadate in sodium chromate with addition of roasting residue
Although adding the wet residue can save lime, a small amount of hazardous waste must require expensively safely other treatments. As CaCO3 forms the predominant phase in residue and readily changes into CaO by roasting process, the roasted residue can act as the additive to remove vanadate. Figure 8 presents the XRD patterns of the roasting residue.

Figure 8 XRD patterns of roasted residue at different temperatures (Residue was roasted at 800 °C, 900 °C and 1000 °C for 1 h, respectively)
Well-characterized peaks assigned to CaCO3 can be observed in the fresh residue (Figure 8), whereas other substances cannot be detected, which high content of CaCO3 occurs in residue. Moreover, all of the peaks assigned to CaO can be found in roasting temperatures above 800 °C. The results suggest that the roasted residue can be substituted for lime in vanadate removal from sodium chromate solution. Table 9 shows the removal rate of vanadate with addition of the roasting residue.
Table 9 shows that increasing roasting temperature reduces the V2O5 concentration in solution and remarkably promotes removal rate of V2O5 with addition of the roasted residue. Therefore, 1000 °C is determined during residue roasting process. Nevertheless, less than 68% removal rate of V2O5 at 1000 °C cannot produce qualified chromate-bearing salts mainly due to the presence of Na2CO3 10 g/L. Thus, more roasted residue was added with consideration of existence of Na2CO3 in sodium chromate. Table 10 shows the effect of the roasted residue dosage on vanadate removal.
Table 10 indicates that the vanadate removal rate significantly increases when the amount of the roasted residue raises. The vanadate removal rate reaches up to 90.63% and the V2O5 concentration in the solution remains less than 0.1 g/L with addition of 10 g/L the roasted residue. Consequently, the purified solution satisfies the production of chromate-bearing salts. Unlike the addition of more than 10 g/L lime in vanadate removal, no lime will be required when the roasted residue substitutes for lime by calcium circulation. This finding suggests that no hazardous waste will be discharged. Thus, a novel process for CVR is presented in Figure 9. This method comprises the extraction of V2O5·xH2O and sodium chromate from CVR as well as removal of vanadate by adding the roasted residue.
Figure 9 provides a promising calcium circulation to recover V2O5 and sodium chromate from CVR. No hazardous residue from CVR is discharged and no fresh lime is added.
6 Conclusions
1) The stability of calcium vanadate and calcium chromate depends on pH and [HCO3-]. CaV2O6·4H2O transforms into CaV2O6·4H2O, CaV2O6·2H2O, CaV2O6, Ca2V2O7·2H2O, and Ca5(VO4)3(OH) when pH increases from 7.51 to 12.32.
Table 9 Effect of roasting temperature on residue during removal of vanadate in solution
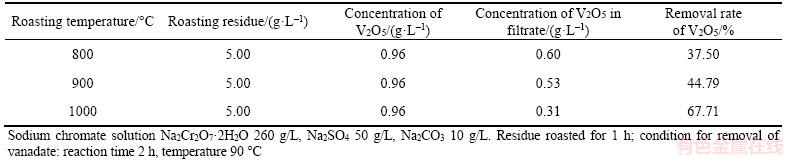
Table 10 Effect of the roasting residue on vanadate removal
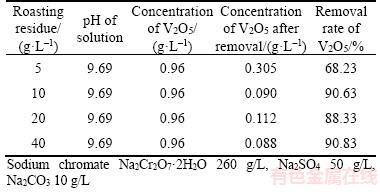
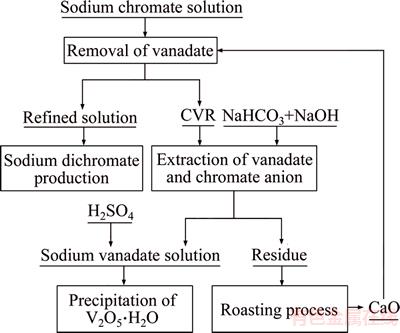
Figure 9 Flowchart of an environmentally friendly treatment for CVR
2) Increasing pH and reducing CVR dosage improve the extraction rates of vanadate and chromate in NaHCO3 solution. Adding NaOH into NaHCO3 solution favors CVR leaching because NaOH in NaHCO3 solution plays a positive role during such process. More than 95% V2O5 and Na2Cr2O7·4H2O extraction rates were obtained under the following conditions: 60 g/L NaHCO3, 20–25 g/L CVR dosage, and 30–40 g/L NaOH at 90 °C for 2 h.
3) Two approaches were provided to reuse the residue after extraction of V2O5 and sodium chromate from CVR. Adding the wet fresh residue can save over 60% lime during the removal of vanadate anion in sodium chromate compared with adding lime. However, some hazardous waste will be still expensively stored. Meanwhile, 10 g/L of the roasted residue at the roasting temperature of 1000 °C can be substituted for lime and no lime is required in the removal of vanadate. Thus, a safe, economical approach is developed through extraction of vanadate and chromate extraction and calcium circulation.
References
[1] MOSKALYK R R, ALFANTAZI A M. Processing of vanadium: A review [J]. Minerals Engineering, 2003, 16(9): 793–805. DOI: 10.1016/S0892-6875(03)00213-9.
[2] JAMES M T, CRAIG H B, TUNCER B E. Treatment of Cr (VI) in COPR using ferrous sulfate-sulfuric acid or cationic polysulfides [J]. Geotechnical and Geoenvironmental Engineering, 2008, 134: 1791–1803. DOI: 10.1061/ (ASCE)1090-0241(2008)134: 12(1791).
[3] MARKIEWICZ B, KOMOROWICZ I,
D. Accurate quantification of total chromium and its speciation form Cr(VI) in water by ICP-DRC-IDMS and HPLC/ICP-DRC-IDMS[J]. Talanta, 2016, 152: 489–497. DOI: 10.1016/j.talanta.2016.02.049.
[4] CHEN Gang, WANG Jia-jun, WANG Xiao-hui, ZHENG Shi-li, DU Hao, ZHANG Yi. An investigation on the kinetics of chromium dissolution from Philippine chromite ore at high oxygen pressure in KOH sub-molten salt solution [J]. Hydrometallurgy, 2013, 139(3): 46–53. DOI: 10.1016/ j.hydromet.2013.07.004.
[5] ZHAO Qing, LIU Cheng-jun, LI Bao-kuan, RON Zevenhoven, HENRIK Saxén, JIANG Mao-fa. Recovery of chromium from residue of sulfuric acid leaching of chromite [J]. Process Safety & Environmental Protection, 2017, 113: 78–87. DOI: 10.1016/j.psep.2017.10.002.
[6] LI Lan-jie, DU Hao, YANG Na, WANG Shao-na, ZHENG Shi-li, ZHANG Yi. Solubility in the Quaternary Na2O-V2O5-CaO-H2O System at (40 and 80) °C [J]. Journal of Chemical & Engineering Data, 2011, 56(10): 3920–3924. DOI: 0.1021/je200679b.
[7] CHEN Gang, WANG Xiao-hui, WANG Jia-jun, DU Hao, ZHANG Ying, ZHENG Shi-li, ZHANG Yi. A new metallurgical process for the clean utilization of chromite ore [J]. International Journal of Mineral Processing 2014, 131: 58–68. DOI: 10.1016/j.minpro.2014.07.002.
[8] WANG Ming-yu, CHEN Bian-fang, HUANG Sheng, WANG Xue-wen, LIU Biao, GE Qi, XIE Shu-shan. A novel technology for vanadium and chromium recovery from V-Cr-bearing reducing slag [J]. Hydrometallurgy, 2017(171): 116–122. DOI: 10.1016/j.hydromet.2017.05.007.
[9] FU Nian-xin, ZHANG Wei-long, ZHANG Lin-nan, DU Xing-hong, SUI Zhi-tong. Dissolution behavior of calcium chromates in acid or alkali solution [J]. Journal of Shenyang University of Technology, 2012, 34(6): 639–643. (in Chinese)
[10] SHLEWIT HABIB, ALIBRAHIM MOUSSA. Extraction of sulfur and vanadium from petroleum coke by means of salt-roasting treatment [J]. Fuel, 2006, 85(5): 878–880. DOI: 10.1016/j.fuel.2005.08.036.
[11] KONG Xiang-feng, TIAN Tao, XUE Sheng-guo, HARTELY W, HUANG Long-bin, WU Chuan, LI Chu-xuan. Development of alkaline electrochemical characteristics demonstrates soil formation in bauxite residue undergoing natural rehabilitation [J]. Land Degradation and Development, 2018, 29(1): 58–67. DOI: 10.1002/ldr.2836.
[12] ZHAO Long-sheng, WANG Lina, QI Tao, CHEN De-sheng. ZHAO Hong-xin, LIU Ya-hui. A novel method to extract iron, titanium, vanadium, and chromium from high-chromium vanadium-bearing titanomagnetite concentrates [J]. Hydrometallurgy, 2014, 149: 106–109. DOI: 10.1016/j.hydromet. 2014.07.014.
[13] LI Hong-yi, FANG Hai-xing, WANG Kang, ZHOU Wang, YANG Zhao, YAN Xiao-man, GE Wen-sun, LI Qian-wen, XIE Bing. Asynchronous extraction of vanadium and chromium from vanadium slag by stepwise sodium roasting–water leaching [J]. Hydrometallurgy, 2015, 156: 124–135. DOI: 10.1016/j. hydromet. 2015.06.003.
[14] LI Hong-yi, WANG Kang, HUA Wei-hao, YANG Zhao, ZHOU Wang, XIE Bing. Selective leaching of vanadium in calcification-roasted vanadium slag by ammonium carbonate [J]. Hydrometallurgy, 2016, 160: 18–25. DOI: 10.1016/ j.hydromet.2015.11.014.
[15] LI Xin-sheng, XIE Bing. Extraction of vanadium from high calcium vanadium slag using direct roasting and soda leaching [J]. International Journal of Minerals, Metallurgy and Materials, 2012, 19(7): 595–601. DOI: 10.1007/s12613- 012-0600-8.
[16] WEBER R, BLOCK H D, BATZ M. Process for the utilization of vanadium bound in chromium ore as vanadium (V) oxide by electrolysis:US,0045834 [P]. United States Patent Application 20040045834.
[17] MIN Xiao-bo, WANG Yang-yang, CHAI Li-yuan, YANG Zhi-hui, LIAO Qi. High-resolution analyses reveal structural diversity patterns of microbial communities in chromite ore processing residue (COPR) contaminated soils [J]. Chemosphere, 2017, 183: 266–276. DOI: 10.1016/ j.chemosphere. 2017.05.105.
[18] WANG Tian-gui, LI Zuo-hu. Dissolution kinetics of calcium chromate and its solubilities measurement [J]. Chemical Engineering(China), 2005, 33(6): 48–50. (in Chinese)
[19] XIAO Xi-yuan, JIANG Zhi-chao, GUO Zhao-hui, WANG Ming-wei, ZHU Hui-wen, HAN-Xiaoqing. Effect of simulated acid rain on leaching and transformation of vanadium in paddy soils from stone coal smelting area [J]. Process Safety and Environmental Protection, 2017, 109: 697–703. DOI: 10.1016/j. psep.2017.05.006.
[20] LIU Gui-hua, ZHANG Yu-feng, ZHOU, Qiu-sheng. Acidification process of sodium chromate solution [J]. Journal of Central South University: Science and Technology, 2012, 43(4): 1227–1232. (in Chinese)
[21] CHAI Li-yuan, DING Chun-lian, TANG Chong-jian, YANG Wei-chun, Yang Zhi-hui, Wang Yang-yang, LIAO Qi, LI Jia-wei. Discerning three novel chromate reduce and transport genes of highly efficient Pannonibacter phragmitetus BB: From genome to gene and protein [J]. Ecotoxicology and Environmental Safety, 2018, 162: 139–146. DOI: 10.1016/ j.ecoenv.2018.06.090.
[22] CRUYWAGEN J J. Protonation, oligomerization and condensation reactions of vanadate(V), molybdate(VI) and tungstate(VI) [J]. Advances in Inorganic Chemistry, 2000, 49: 127–182.
[23] POST K, ROBINS R G. Thermodynamic diagrams for the vanadium-water system at 298.15K [J]. Electrochimica Acta, 1976, 21(6): 401–405. DOI: 10.1016/0013-4686(76)85115-8.
[24] BRAIN, l. Thermochemical data of pure substances [M]. Beijing: Science Press, 2003. (in Chinese)
[25] LIAO Shi-ming, BO Tan-lun. Foreign vanadium metallurgy [M]. Beijing: Metallurgical Industry Press, 1985. (in Chinese)
[26] DEAN J A. Lange’s handbook of chemistry [M]. 2nd eds Beijing: Science Press, 2003. (in Chinese)
[27] WEI Xiao-xiang, YU Li-li. Tantalum extraction photometric was employed to determine trace vanadium in alloy steel [J]. Chemical Engineering and Equipment, 2010(3): 148-149. (in Chinese)
[28] XIAO Xi-yuan, WANG Ming-wei, ZHU Hui-wen, GUO Zhao-hui, HAN Xiao-qing, ZENG Peng. Response of soil microbial activities and microbial community structure to vanadium stress [J]. Ecotoxicology and Environmental Safety, 2017, 142: 200–206. DOI: 10.1016/j.ecoenv.2017.03.047.
[29] ZHU Feng, HOU Jing-tao, XUE Sheng-guo, WU Chuan, WANG Qiong-li, HARTELY W. Vermicompost and gypsum amendments improve aggregate formation in bauxite residue [J]. Land Degradation and Development, 2017, 28(7): 2109–2120. DOI: 10.1002/ldr.2737.
[30] ZHANG Yi-min, BAO Shen-xu, LIU Tao, CHEN Tie-jun, HUANG Jing. The technology of extracting vanadium from stone coal in China: History, current status and future prospects [J]. Hydrometallurgy, 2011, 109(1, 2): 116–124. DOI: 10.1016/j.hydromet.2011.06.002.
[31] ZHU Feng, LIAO Jia-xin, XUE Sheng-guo, HARTELY W, ZOU Qi, WU Hao. Evaluation of aggregate microstructures following natural regeneration in bauxite residue as characterized by synchrotron-based X-ray micro-computed tomography [J]. Science of the Total Environment, 2016, 573(24): 155–163. DOI: 10.1016/j.scitotenv.2016.08.108.
[32] GUPTA S K, RAO P V R, NARASARAJU T S B. Physico-chemical aspects of calcium vanadate apatite [J]. Journal of Materials Science, 1986, 21(1): 161–164. DOI: 10.1007/BF01144715.
[33] RAO P V R, GUPTA S K, NARASARAJU T S B. Studies on some physico-chemical aspects of lead vanadate apatite [J]. Journal of Material Science Letters, 1986, 5(3): 323–325. DOI: 10.1007/BF01748092.
[34] LIU Gui-hua, DONG Wen-bo, QI Tian-gui, ZHOU Qiu-sheng, PENG Zhi-hong, LI Xiao-bin. Behavior of calcium oxalate in sodium aluminate solutions [J]. Transactions of Nonferrous Metals Society of China, 2017, 27(8): 1878–1887. DOI: 10.1016/S1003-6326(17)60212-7.
(Edited by HE Yun-bin)
中文导读
基于钒、铬回收和钙循环时的含铬钒渣安全利用
摘要:含铬钒渣的安全经济处理是铬盐清洁化生产的关键。本文在碳酸氢钠溶液体系中,研究了钒酸钠和铬酸钠的资源化利用。结果表明:铬酸钙和钒酸钙的稳定性取决于溶液pH值和[HCO3-]浓度。当7.51
2O6·4H2O可依次转化为 CaV2O6·2H2O, CaV2O6, Ca2V2O7·2H2O和 Ca5(VO4)3(OH)。在NaHCO3的稀溶液中,随着体系pH的升高和含铬钒渣加入量的减少,钒酸盐的回收率相应提高;且在较稀的NaHCO3溶液中可取得较高的钒、铬回收率。此外,在NaHCO3体系中加入NaOH可促进钒、铬的回收。在NaHCO3和NaOH浓度分别为60 g/L、30 g/L,温度90 °C,时间2 h的条件下, 钒、铬的浸出率分别高达96.65%和95.40%。含铬钒渣处理后仍是危废弃,基于钙循环提出了减少处理后渣的方法。加入新鲜的处理后渣用于脱除铬酸钠中钒,比传统石灰脱钒减少60%的石灰加入量,主要原因是新鲜的CaCO3具有活性;而铬酸钠溶液脱钒时加入焙烧的处理后渣,则不必加入石灰。随后,本文提出了含铬钒渣安全经济处理新工艺。
关键词:含铬钒渣;NaHCO3;钒酸钙;铬酸钙;铬酸钠;钙循环
Foundation item: Project(51274242) supported by the National Natural Science Foundation of China; Project(2015CX001) supported by the Innovation-driven Plan of Central South University, China
Received date: 2017-07-28; Accepted date: 2017-12-08
Corresponding author: WU Guo-yu; Tel/Fax: +86–731–88830453; E-mail: wuguoyu@csu.edu.cn; ORCID: 0000-0002-7761-6976