
Preparation of carbon brushes with thermosetting resin binder
XIA Jin-tong(夏金童), HU Zhong-liang(胡忠良),
CHEN Zhen-hua(陈振华), DING Guo-yun(丁国芸)
College of Materials Science and Engineering, Hunan University, Changsha 410082, China
Received 15 July 2007; accepted 10 September 2007
Abstract: Carbon brushes with a resin binder were prepared according to an industrial process and the effects of the molding pressure, grains size and cure temperature on the properties of brush samples were discussed. The results show that the bulk density, bending strength and Rockwell hardness increase, while resistivity decreases with increasing molding pressure. Cure temperature has much more influence on the properties of brushes than molding pressure and grains size. Isothermal differential scanning calorimetry(DSC) was used to estimate the degree of cure of resin binder and a novel method of using the true density to measure the degree of cure of resin binder was presented and discussed briefly. Based on optimal process parameters carbon brushes were manufactured, durability tests for brushes were carried out on an alternate current motor and scanning electron microscope(SEM) was adopted to observe the morphology of worn surface of brushes. The results show that a luster oxide film can be formed on the surface of brushes and their service life reaches 380 h.
Key words: carbon brushes; properties; cure process; thermosetting resin
1 Introduction
Recently, China motors industry has developed rapidly and many new types of motors with a low power and high speed have been invented[1-3]. The rotational speed of the motors often exceeds 10 000 r/min, even reaches 30 000 r/min, the brushes fixed in the motors must have excellent commutation ability, otherwise, large sparks and big noises are produced between brushes and commutators. This makes brushes wear quickly and have a short service life.
Electrical brushes were invented a century ago in England and the development of them was accompanied with that of motors[4]. The earliest brush was made of clusters of copper wires, but modified motors with higher and higher performance made primitive brushes not match them, so carbon brushes (which were mainly made of carbon materials) were invented[5]. Early carbon brushes were firstly bonded by sugar, then by pitch, but these brushes were not suitable for high-speed motors, while carbon brushes with a resin binder, which is lately developed, could well match the motors.
Carbon brushes with a resin binder are generally composed of carbon materials, solid lubricant, resin binder and additive. Graphite has a lamellar structure and anisotropic properties that induce a good friction and wear behaviour, so it constitutes the main component of the carbon materials of brushes[6]. Molybdenum disulfide is often chosen as a solid lubricant due to its good lubricant property[7]. Carbon brushes are of high resistivity induced by the insulation of its binder, so they have good commutation ability, and they are very suitable for the high-speed motors[8]. Although the manufacturing process of the brushes is not complicated, the development of the brushes demands a high technique level. Developed countries such as Japan and England have developed such brushes with high performances[9-10], but for commercial and secret reasons it is difficult to find related literatures except a few patents. At present, this type of brushes home made have a shorter service life and cannot compete with foreign products, in order to improve the competitive power of domestic brushes and find some basic rules for scientific research, the subject study on brushes with a resin binder was performed in this study.
2 Experimental
2.1 Sample preparation
Carbon brushes were manufactured following an industrial process shown in Fig 1.
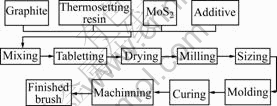
Fig.1 Manufacturing process for brushes
Raw materials were composed of 75% graphite, 20% thermosetting resin, 2% MoS2 and 3% additive (mass fraction).
Firstly, all materials were put into a mixing machine to mix for 1 h, the mixture was then tabletted, dried, milled and sized to a required size. Secondly, the blend was molded to a cuboid at different pressures. Thirdly, the molded specimens were cured at a certain temperature for 1 h. Finally, the specimens were machined to the desired shape: 5.2 mm×5.5 mm×32.0 mm.
2.2 Properties and characterization of samples
The properties of brush samples such as bulk density, true density, resistivity, Rockwell hardness and bending strength were measured according to the corresponding China National Standard. Isothermal DSC and SEM were adopted to estimate the degree of cure of resin and observe the worn morphology of brushes, respectively.
2.3 Durability tests for carbon brushes
Carbon brushes were manufactured based on optimal process parameters and durability tests for brushes were performed on an HGH5435M120 alternate current motor. The performance parameters of the motor are listed in Table 1. All tests were conducted when the motor was with A5 rotor wheel load and carried out under the same condition. The relative humidity was 50%, the ambient temperature was 25 ℃ and the spring loads were 5 N/cm2.
Table 1 Performance parameters of motor
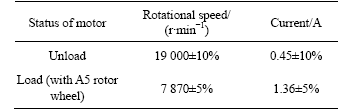
3 Results and discussion
3.1 Effects of molding pressure on properties of brushes samples
The properties of carbon brushes samples have much to do with the molding pressure (the grains was sized by 75 μm sieve and the samples were all cured at 180 ℃). From Figs.2 and 3, it is obviously seen that the properties of brushes regularly vary with the molding pressure. The bulk density, bending strength and Rockwell hardness increase with molding pressure increasing while resistivity presents an opposite tendency.
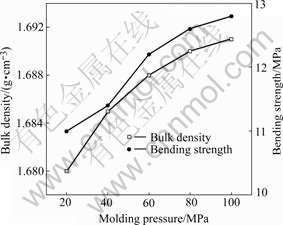
Fig.2 Bulk density and bending strength as function of molding pressure
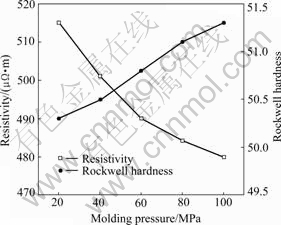
Fig.3 Resistivity and Rockwell hardness as function of molding pressure
From Fig.2, it can be seen that the rate of increment of the bulk density becomes less with increasing pressure. This is because the gap between carbon grains becomes less with increasing force and thus it becomes more difficult to compact the samples.
Bending strength of carbon materials is related to their porosity and the powder size, as shown in Knibbs equation[11]:
(1)
where k and b are empirical constants; D and P are the maximum diameter of grains and porosity, respectively; σ is bending strength.
Eqn.(1) shows the relationship between bending strength and porosity. Porosity decrement due to molding pressure increment results in the increment of bending strength, as clearly shown in Fig.2.
The curve of resistivity of brushes versus molding pressure is shown in Fig.3 and it can be illustrated for the following reasons. Conduction components in carbon brushes are graphite grains, the increasing molding pressure leads the gap between grains to become less and it makes the conduction grains unit volume increase, so electric resistivity decreases.
Rockwell hardness of brushes is mainly decided by materials composing them, so Rockwell hardness changes little because of the same components and yet a little increment in hardness with a larger pressure can be explained as the rule that more compact materials tend to raise their hardness.
3.2 Effects of grain sizes on properties of brushes samples
The properties of brushes for different grain sizes are listed in Table 2. The specimens were all molded at 100 MPa and cured at 200 ℃.
Table 2 Properties of brushes samples with different grain sizes
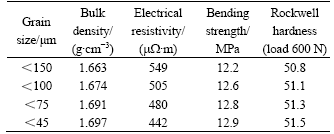
From Table 2, it can be seen that the bulk density, bending strength and Rockwell hardness increase with decreasing grain sizes while resistivity shows an opposite tendency.
With a smaller grain size, more micro powders are compacted into pores of the specimen, so the porosity becomes higher, and the bending strength is related to the porosity and maximum diameter of grains (seen in Eqn.(1)), both factors help to increase the bending strength.
The relationship between resistivity and grain size can be explained according to similar reasons described in section 3.1. The more conduction micro graphite grains are compacted to fill the porosity to improve their conductibility.
The evolution of hardness with grain size in Table 2 can be interpreted that a smaller grains help to increase the bulk density (seen above analysis) while more compact materials tend to raise their hardness.
3.3 Effects of cure temperature on properties of brushes and analysis of cure process
The properties of composite materials are much related to the cure process of resins[12-14] and this rule is also suitable for carbon brushes. The cure process is mainly controlled by the cure temperature and cure time. In this study, the effects of cure temperature on the properties were investigated when the other parameters were fixed to the same values (molding pressure: 100 MPa, grains size: <75 μm, cure time: 1 h).
Figs.4 and 5 show the variations of properties of brushes with the cure temperature, from which it can be seen that the resistivity decreases, the bending strength and Rockwell hardness increase with increasing cure temperature while the bulk density appears to have a more complicated relation to the cure temperature.
In Fig. 4, the bulk density of carbon brushes at first decreases with increasing cure temperature, but when the cure temperature reaches 160 ℃, it increases with increasing cure temperature.
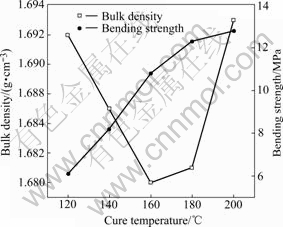
Fig.4 Variations of bulk density and bending strength with cure temperature
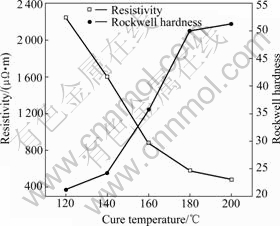
Fig.5 Variations of resistivity and Rockwell hardness with cure temperature
It should also be paid attention that the cure temperatures in Figs.4 and 5 have much bigger slopes than corresponding curves in Figs.3 and 4 (except bulk density). This proves that the cure temperature and cure process of resins have much more influence on the properties than molding pressure and grains size.
The variation of properties with the cure temperature must be connected to the chemical reactions occurring in the specimen during cure process.
So it is essential to study the cure process and the cure degree of resins. At present, much work has been done to study the mechanism of resins in polymer matrix composites[15-17], however, few studies can be found on the cure of resins as a binder in carbon materials. Dynamic DSC is usually used to measure the kinetics and degree of cure for resin matrix composites[18-20], but it is not suitable for composites with resin binder for following reasons: 1) a small percentage of resin in the specimen produced the exothermic heat which is not enough to yield an explicit peak; 2) the cure process often needs a relatively long time while the rate of heating-up is often so fast that the cure temperature corresponding to the peak in DSC is higher than the true cure temperature.
Fig.6 shows the isothermal DSC spectrum of specimens cured at different temperatures versus heating time and isothermal scan was carried out at 210 ℃. From Fig.6 the degree of cure can be calculated according to Eqn.(2) [21]:
(2)
where Ht and Hr represent the exothermic heat of a specimen cured at a temperature and the uncured specimen.
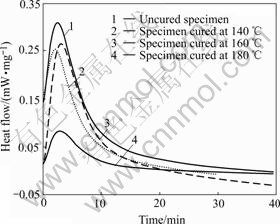
Fig.6 DSC curves of specimens cured at different temperatures
Based on Eqn.(2) and data in Fig.6, the cure degrees of resins were calculated to be 23%, 34%, 95% and 100% for specimens cured at 140, 160, 180 and 200 ℃, respectively (the curve for 200 ℃ is almost linear and omitted in Fig.6 ).
The cure of the resin decreases its volume and its volumetric shrinkage is only a function of the degree of cure[22], so it is reasonably inferred that the degree of cure is just a function of the density of the resin binder. Because graphite is nonreactivity at the cure temperature, so the degree of cure was only linked to the true density of the specimen.
Fig.7 shows the relationship between true density evolution and the cure temperature. Before cure reactions taking place the true density almost keeps constant, when the cure temperature increases the true density becomes larger until it reaches a certain value when the cure reactions have completed. The true density variation is due to the volumetric shrinkage and mass change of the resin induced by chemical cure reactions. As shown in Fig.7, the true density is a monotone increasing function as cure temperature during cure process, and so is the degree of cure. Based on above analysis it is justified and viable to measure the degree of cure by the true density.
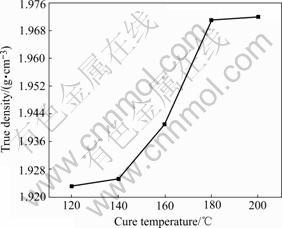
Fig.7 True density variation with cure temperature
The dependence of the degree of cure on true density is listed in Table 3. Using isothermal DSC curve to estimate the degree of cure is a time-consuming and inconvenient method while using the true density is a simple and fast one. Further study on the method will be important to optimize the technological parameters and improve the quality of carbon materials.
The bulk density in Fig.4 shows different tendency compared with true density in Fig.7. This might be because at higher temperature the resin expands, cross linking and coupling reactions take place and this makes the porosity of specimens change. As shown in Fig.8, the porosity first increases with increasing cure temperature, but when the cure temperature reaches 180 ℃, it begins
Table 3 Dependence of degree of cure on true density
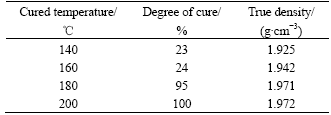
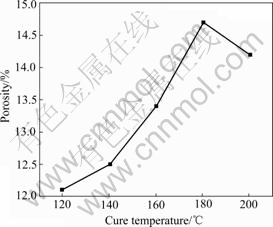
Fig.8 Porosity of specimens cured at different cure temperatures
to decrease. In Fig.4, the bulk density first decreases due to increment of porosity, but when the increment extent of true density exceeds that of porosity, the bulk density then becomes larger.
Bending strength curve in Fig.4 can be illustrated that with increasing cure temperature, the degree of cure becomes larger, the cure reactions make resins form cross linking and coupling structure, which makes graphite grains connect firmly and results in the increment of bending strength.
With respect to the Rockwell hardness it is thought that the cure reactions change the state of graphite grains and polar groups link to the surface of grains to raise the hardness of the specimen.
A higher cure temperature leads to increase the degree of cure, and more cure reactions take place to form cross linking structure. This makes the conductive graphite grains have more probability to contact each other, so the conductivity of specimens increases and the resistivity decreases.
3.4 Results of durability tests for carbon brushes
Under optimal parameters carbon brushes were manufactured and durability tests for carbon brushes were carried out on a HGH5435M120 motor. It is observed that small sparks are produced between the brushes and commutators and a luster oxide film is formed on the surface of brushes. The uniform oxide film is clearly seen in Fig.9 and it can reduce the rate of wear of brushes[23-24] and helps to prolong the service life. Durability tests indicate that the service life of the brushes reaches 380 h and they can replace the import brushes.
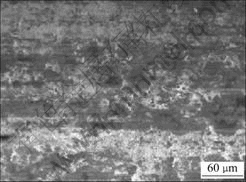
Fig.9 Morphology of worn surface of brushes
4 Conclusions
1) With increasing molding pressure, the bulk density, bending strength and Rockwell hardness of the specimen increase while resistivity decreases.
2) A smaller grain size can raise the bulk density, bending strength, Rockwell hardness and electric conductivity of the specimen.
3) The cure temperature has much more influence on the properties of carbon brushes. Compared with isothermal DSC curve, the method of using true density to measure the degree of cure is a simple and convenient one and further study on it will be important to optimize the technological parameters.
4) The service life for carbon brushes in this study reaches 380 h that is approximately equal to that for advanced import brushes.
References
[1] ZHAO Ji-cun, ZHOU Wei, SUN Qiong, DUAN Jun, ZHANG Rui. Preparation of brushes for new types of micromotors [J]. Micromotors, 2000, 33(4): 43-44.
[2] JIANG Wen-zhong, JIANG Ying. Technological research on brushes for high speed electrical machinery [J]. Carbon (China), 2000(4): 26-27.
[3] LU Xue-feng, XIA Jin-tong, ZHANG Wen-hao, TU Chuan-jun. Research on the manufacture of new type high resistivity carbon brushes [J]. Natural Science Journal of Xiangtan University, 2005, 27(2): 131-135.
[4] UECKER A. Lead-free carbon brushes for automotive starters [J]. Wear, 2003, 255: 1286-1290.
[5] KUHLMAN D. Electrical fiber brushes—theory and observations [J]. IEEE Transactions on Components, Packaging and Manufacturing Technology—Part A, 1996, 19: 360-375.
[6] SENOUCI A, FEREN J, ZAIDI H. Wear mechanism in graphite-copper electrical sliding contact [J]. Wear, 1999, 255: 949-953.
[7] ZHANG Wen-zheng, YAO Shu. An advance in the research of preparation and application of molybdenum disulfide lubricant [J]. Lubricating Oil, 2006, 21: 19-25.
[8] HUANG Wei-de. Electrical brushes with a resin binder [J]. Electric Carbon Products, 1997, 11: 8-11.
[9] ISAO S. Carbon brush for miniature motors and method of making same [P]. US 5136198, 1990-04-05.
[10] ROBERGE R. Carbon brush performance and application in the pulp and paper environment [J]. National Electrical Carbon Products, 2001(1): 184-191.
[11] KNIBBS R H, MORRIS J B. Some effects of oxidation on the properties of graphite [C]// Third SCI Conference on Industrial Carbons and Graphites. London: Society of Chemical Industry, 1972: 297-308.
[12] GANGLANI M, CARR S H, TORKELSON J M. Influence of cure via network structure on mechanical properties of a free-radical polymerizing thermoset [J]. Polymer, 2002, 43: 2747-2760.
[13] HSIAO K T, LITTLE R, RESTREPO O, MINAIE B. A study of direct cure kinetics characterization during liquid composite molding [J]. Composites (Part A), 2006, 37: 925-933.
[14] LI M, TUCKER C L. Optimal curing for thermoset matrix composites: Thermochemical and consolidations [J]. Polym Compos, 2002, 23: 739-757.
[15] KIM W G, LEE J Y. Contributions of the network structure to the cure kinetics of epoxy resin systems according to the change of hardeners [J]. Polymer, 2002, 43: 5713-5722.
[16] BANG K G, KWON J W, LEE D G, LEE W L. Measurement of the degree of cure of glass fiber-epoxy composites using dielectrometry [J]. J Mater Process Technol, 2001, 113: 209-214.
[17] WINGARD C D. Characterization of prepreg and cured epoxy/fiberglass composite materials for use in advanced composite piping systems [J]. Thermochimica Acta, 2000, 357/358: 293-301.
[18] BUGGY M, TEMIMHAN T, BRADDELL O. Curing of carbon fibre reinforced epoxy matrix composites [J]. J Mater Process Technol, 1996, 56: 292-301.
[19] ROSU D, CASCAVAL C N, MUSTATA F, CIOBANU C. Cure kinetics of epoxy resins studied by non-isothermal DSC data [J]. Thermochimica Acta, 2002, 383: 119-127.
[20] SBRIRAZZUOLI N, VYAZOVKIN S. Learning about epoxy cure mechanisms from isoconversional analysis of DSC data [J]. Thermochimica Acta, 2002, 388: 289-298.
[21] PRIME R B. Thermal characterization of polymeric materials [M]. New York: Academic Press, 1981: 81-82.
[22] LI C, POTTER K, WISNOM M R. In-situ measurement of chemical shrinkage of MY750 epoxy resin by a novel gravimetric method [J]. Composites Science and Technology, 2004, 64: 55-64.
[23] HOLM R. Electric contacts [M]. Berlin: Springer Verlag, 1958: 133-134.
[24] HU Zhong-liang, CHEN Zhen-hua, XIA Jin-tong. Study on surface film in the wear of electrographite brushes against copper commutators for variable current and humidity [J]. Wear, 2007, (in press, dio: 10.1016/j.wear.2007.01.034)
(Edited by LI Xiang-qun)
Foundation item: Project(59972009) supported by the National Natural Science Foundation of China
Corresponding author: HU Zhong-liang; Tel: +86-13975873284; E-mail: david10103@sina.com