J. Cent. South Univ. (2016) 23: 1899-1905
DOI: 10.1007/s11771-016-3245-3

Magnetizing roast and magnetic separation of iron in rare-earth tailings
YANG He(杨合), RONG Yi(荣宜), HAN Chong(韩冲), TANG Rong(唐荣), XUE Xiang-xin(薛向欣),
LI Yong(李勇), LI Ying-nan(李英楠)
School of Metallurgy, Northeastern University, Shenyang 110819, China
Central South University Press and Springer-Verlag Berlin Heidelberg 2016
Abstract: Magnetic separation of iron in rare-earth tailings was achieved by magnetizing roast process with coal as reductant. Effects of the temperature, carbon to oxygen ratio, and cooling type on magnetic susceptibility and composition of rare-earth tailings were investigated. The results show that roast conditions with the temperature of 650 °C, carbon to oxygen ratio of 3.85, and holding time of 2.5 h are in favor of reduction of Fe2O3 to Fe3O4 when the roasted rare-earth tailings is cooled along with furnace. Under these roast conditions, magnetic susceptibility of rare-earth tailings is 2.36 that is very close to theoretical value (2.33). However, magnetic separation results of iron in rare-earth tailings cooled along with furnace are not satisfactory. Through comparing magnetic separation results of iron in rare-earth tailings cooled by different ways, it is found that water cooling is more favored of magnetic separation of iron in the roasted rare-earth tailings than furnace cooling and air cooling. Grade and recovery of iron in concentrate from rare-earth tailings cooled by water are 45.00%-49.00% and 65.00%-77.50%, respectively.
Key words: rare-earth tailings; iron; magnetizing roast; magnetic separation; iron grade; iron recovery
1 Introduction
Magnetizing roast and magnetic separation process has become an effective method to deal with refractory iron ore [1-10]. The ore is heated and reacts with oxidant or reductant during magnetizing roast process. Magnetism of weak magnetic iron-containing minerals is significantly enhanced while magnetism of gangue minerals almost remains. Thus, iron can be successfully separated according to magnetic differences of iron-containing minerals and gangue minerals. After magnetizing roast of siderite with O2 as oxidant, JIU et al [1] obtained concentrate with iron grade of higher than 58.21% and iron recovery of more than 79.39% by magnetic separation. It was reported that ZHANG et al [2] dealed with limonite by magnetizing roast with CO as reductant and produced concentrate with iron grade of 60.67% and iron recovery of 94.49% by magnetic separation. When limonite was reduced by coal during magnetizing roast, concentrate with high iron grade and iron recovery was also obtained by magnetic separation [5]. Additionally, WANG et al [10] produced concentrate with iron grade of 58.40% and iron recovery of 87.86% by magnetic separation when hematite was reduced by coal during magnetizing roast process [10]. These demonstrate that magnetizing roast and magnetic separation process has caused extensive attention in dealing with refractory iron ore.
At present, demand of iron ore continues to increase with the fast development of economy. It is necessary to study the technology of iron separation from iron tailings which can be an important source of iron in the future. Main mining way of rare earth ore located at Bayan Obo in Baotou, China, is to extract iron. However, iron grade and iron recovery are only 50% and 50%-60%, respectively, which results in existence of lots of iron and rare earth in rare-earth tailings. Therefore, reasonable methods should be adopted to obtain iron and rare earth source from tailings. Separation of iron and rare earth in tailings has been reported [11-17]. However, iron grade and iron recovery of the produced concentrate are low, which could not well extract iron source from rare-earth tailings [12, 16]. Therefore, more effective methods should be studied to separate iron from rare-earth tailings.
In this work, magnetizing roast and magnetic separation of iron in rare-earth tailings were studied. Effects of temperature, carbon to oxygen ratio (molar ratio of carbon to the lost oxygen during the process of Fe2O3 reduced to Fe3O4, C/O ratio), holding time, and cooling type on magnetic susceptibility of rare-earth tailings were investigated in detail. Concentrate yield, iron grade and iron recovery were used to evaluate results of magnetizing roast and magnetic separation of iron in rare-earth tailings. It was hoped to provide theoretical basis for separation of iron in rare-earth tailings.
2 Experimental
2.1 Material
Rare-earth tailings were from Baotou iron and steel group in China. Chemical compositions of rare-earth tailings are listed in Table 1. Iron content, rare earth content and niobium content are 13.06%, 7.09% and 0.1%, respectively. In rare-earth tailings, main iron- containing mineral is hematite and main rare-earth minerals are bastnaesite and monazite. Additionally, rare- earth tailings also contain various gangue minerals such as fluorite, quartz and barite. The anthracite with ash content of less than 9% and fixed carbon content of higher than 82% from Shizuishan, China, was used to reduce rare-earth tailings during magnetizing roast process.
2.2 Magnetizing roast and magnetic separation of rare-earth tailings
During magnetizing roast process, hematite (Fe2O3) in rare-earth tailings is reduced to magnetite (Fe3O4) while magnetism of gangue minerals almost remains no-change. However, Fe2O3 may react with reductant as Reactions (1)-(4). Therefore, appropriate conditions should be determined to reduce Fe2O3 to Fe3O4. Based on magnetic difference of Fe3O4 and other minerals, iron concentrate can be produced by magnetic separation.
3Fe2O3(s)+C(s)=2Fe3O4(s)+CO(g) (1)
3Fe2O3(s)+CO(g)=2Fe3O4(s)+CO2(g) (2)
Fe3O4(s)+CO(g)=3FeO(s)+CO2(g) (3)
FeO(s)+CO(g)=Fe(s)+CO2(g) (4)
Rare-earth tailings and coal were ground by ball-milling for 3 min, respectively. And then, these two materials were sieved using 74 μm sieve and mixed for 9.5 h by mixer. The mixture was compressed into cylinders with diameter of 30 mm and height of 12 mm using tablet machine. The cylinders were put in the muffle and roasted under different temperature, C/O ratio and holding time. After magnetizing roast, the rare-earthtailings were cooled to room temperature through different cooling types such as furnace cooling, air cooling and water cooling. The roasted rare-earth tailings were ground by ball-milling and its magnetic susceptibility was determined. The roasted rare-earth tailings (5-10 g), which were sieved through 74 μm sieve, were weighed to separate iron concentrate by the magnetic tube (XCGS-50). Magnetic field intensity was controlled by changing current intensity in the magnetic tube.
The magnetic susceptibility (w(TFe)/w(FeO)) is used to assess the reduction degree of Fe2O3 to Fe3O4 during magnetizing roast process. w(TFe)/w(FeO) is 2.33 when Fe2O3 is completely transformed into Fe3O4. When w(TFe)/w(FeO) is larger than 2.33, it means that Fe2O3 is incompletely reduced to Fe3O4. When w(TFe)/w(FeO) is lower than 2.33, it means that Fe2O3 is overly reduced to FeO or Fe2SiO4. The concentrate yield, iron grade and iron recovery are used to assess magnetic separation results of iron. The concentrate yield (r) is defined as the mass fraction of the concentrate in rare-earth tailings. Theoretically, chemical composition of iron concentrate should be Fe3O4. Thus, iron grade (TFe), which assesses quality of iron concentrate, should be 72.4% in theory. Iron recovery is defined as mass fraction of iron in concentrate to iron in rare-earth tailings.
2.3 Characterization methods
Hysteresis loops of samples were measured through vibrating samples magnetometer (HH-10, Nanjing university instrument plant, China). Chemical compositions of samples were analyzed using X-ray diffractometer (XRD, X’Pert Pro MPD/PW3040, Panalytical company in Netherlands) with Cu Kα radiation under 40 kV and 50 mA. The scanned range was 2θ=10°-90°. Morphology of samples was analyzed by scanning electron microscope (SEM, SSX-550, Shimadzu Corporation in Japan).
3 Results and discussion
3.1 Effects of magnetizing roast on hysteresis loops
To identify the feasibility of magnetizing roast and magnetic separation of iron in rare-earth tailings, it is necessary to determine that magnetism of iron- containing minerals is enhanced while magnetism of other minerals remains. Therefore, hysteresis loops of roasted rare-earth tailings and concentrate and residue of magnetic separation are measured. As shown in Fig. 1, roasted rare-earth tailings and residue are not magnetized to saturation when magnetic field intensity is 39790 A/m. However, concentrate is magnetized to saturation when magnetic field is 8714.01 A/m. The saturation magnetization of concentrate is 1.23 A·m2/kg, suggesting that the concentrate has the strong magnetism.
Table 1 Main chemical composition of rare-earth tailings (mass fraction, %)

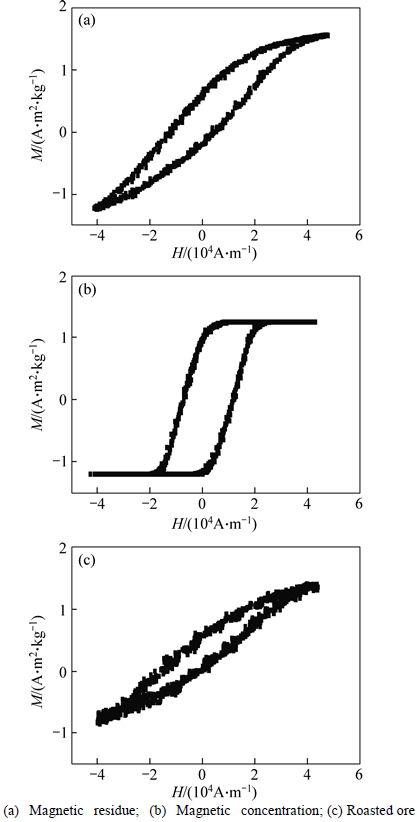
Fig. 1 Hysteresis loops of roasted rare-earth tailings, concentrate and residue with calcination conditions of temperature of 700 °C, C/O ratio of 3.5 and holding time of 2.0 h:
3.2 Effects of calcination conditions on magnetization susceptibility and compositions
As shown in Fig. 2(a), effect of temperature on magnetic susceptibility of rare-earth tailings was investigated under calcination conditions with C/O ratio of 3.85 and holding time of 3.0 h. When temperature increases from 570 °C to 650 °C, magnetic susceptibility of rare-earth tailings decreases from 5.55 to 2.46, suggesting that increase of temperature is in favor of reduction of Fe2O3 to Fe3O4. However, when temperature increases to 700 °C, magnetic susceptibility of rare-earth tailings decreases to 1.36, meaning that Fe2O3 may be overly reduced to weak magnetic wustite or ferro-silicate. To analyze influence of temperature on iron-containing minerals, changes in compositions of rare-earth tailings are investigated by XRD.
As shown in Fig. 2(b), peaks of Fe2O3 are enhanced while peaks of Fe3O4 are weakened with temperature increasing from 570 °C to 650 °C. This can be the reason that magnetic susceptibility of rare-earth tailings approaches to the theoretical value (2.33) with increasing temperature. At 700 °C, appearance of Fe2SiO4 peaks demonstrates that Fe2O3 in rare-earth tailings has been overly reduced, resulting in the decrease of magnetic susceptibility of rare-earth tailings.
Figure 3(a) exhibits changes of magnetic susceptibility of rare-earth tailings with increasing C/O ratio under calcination conditions with temperature of 650 °C and holding time of 2.5 h. Magnetic susceptibility of rare-earth tailings decreases from 6.12 to 2.36 with increasing C/O ratio from 1.00 to 3.85, which is ascribed to reduction of more Fe2O3 to Fe3O4 at higher C/O ratio. However, when the C/O ratio increases from 3.85 to 6.30, magnetic susceptibility of rare-earth tailings increases from 2.36 to 2.99. Excess coal can hinder interaction of Fe2O3 with reducing gas CO from carbon gasification, leading to incomplete reduction of Fe2O3 to Fe3O4. Figure 3(b) shows the XRD patterns of roasted rare-earth tailings at different C/O ratios. It is noticed that peaks of Fe3O4 are weakened with increasing C/O ratio from 3.85 to 6.30. This demonstrates that excess coal is not favored of formation of Fe3O4 and increase of magnetic susceptibility of rare-earth tailings.
Effects of holding time on magnetic susceptibility of rare-earth tailings are investigated under calcination conditions with temperature of 650 °C and C/O ratio of 3.85. As shown in Fig. 4(a), magnetic susceptibility of rare-earth tailings decreases from 3.43 to 2.36 with increasing holding time from 1.0 to 2.5 h, suggesting that sufficient reaction time is necessary during the reduction process of Fe2O3 to Fe3O4. When holding time increases from 2.5 to 3.5 h, magnetic susceptibility of rare-earth tailings increases from 2.36 to 3.45. Figure 4(b) shows the XRD patterns of roasted rare-earth tailings at different holding time. Peaks of Fe3O4 are enhanced with increasing holding time from 1.0 to 2.5 h, contributing to changes of magnetic susceptibility in the range of 1.0-2.5 h. Peaks of Fe3O4 in roasted rare-earth tailings at holding time of 3.0 h are weaker than that at holding time of 2.5 h. This can be ascribed to excessive time that causes complete consumption of coal and cease of reductant formation. Thus, some of Fe3O4 can interact with oxygen and can be oxidized to Fe2O3, which is not favored of increase of magnetic susceptibility of rare- earth tailings.
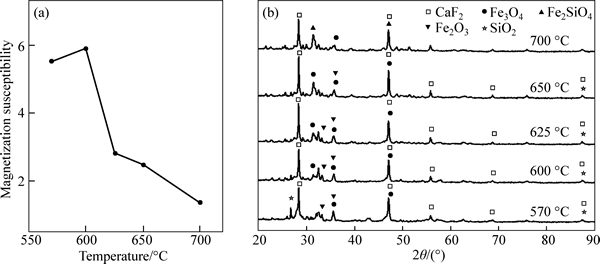
Fig. 2 Changes in magnetic susceptibility (a) and XRD patterns (b) of rare-earth tailings at different temperatures with holding time of 3.0 h and C/O ratio of 3.85

Fig. 3 Changes in magnetic susceptibility (a) and XRD patterns (b) of rare-earth tailings at different C/O ratios with holding time of 2.5 h and temperature of 650 °C

Fig. 4 Changes in magnetic susceptibility (a) and XRD patterns (b) of rare-earth tailings at different holding time with temperature of 650 °C and C/O ratio of 3.85
3.3 Magnetic separation of iron in roasted rare-earth tailings
Iron is separated from the roasted rare-earth tailings with magnetic susceptibility being close to 2.33. As listed in Table 2, concentrate yield, iron grade and iron recovery are 10.50%-17.00%, 23.00%-38.50% and 18.00%-40.00%, respectively. If all of iron in rare-earth tailings exists in Fe2O3, theoretical yield of concentrate should be 18.60% according to TFe of 13.07% in rare-earth tailings. Therefore, low yield of concentrate can be related to incomplete reduction of Fe2O3 to Fe3O4. The concentrate also contains some gangue minerals including CaF2 and SiO2, which may be contributed to the symbiotic relationship of gangue minerals and iron-containing minerals. The concentrate is analyzed using SEM to identify the symbiotic relationship. As shown in Fig. 5(a), particles exhibit irregular shape and adhesion phenomenon. Typical particles are further analyzed by area-scan in Figs. 5(b)-(e). F and Ca are widespread and usually existed as CaF2. During the magnetic separation process, CaF2 with very weak magnetism cannot be separated. Therefore, the symbiotic relationship of fluorite and iron-containing minerals results in the existence of fluorite and low iron grade in concentrate. Distribution areas of Fe and Si are almost the same, meaning that Fe and Si may form iron silicate to decrease iron recovery.
Table 2 Magnetic separation results of iron in roasted rare- earth tailings

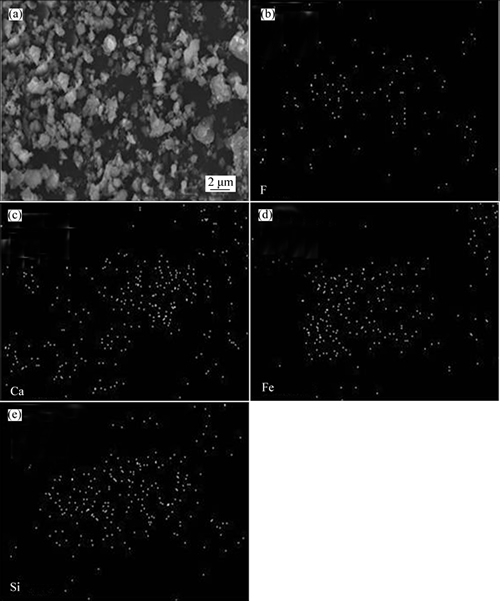
Fig. 5 SEM image (a) and area-scan images (b)-(e) of main elements in magnetic concentrate of sample 1
It should be pointed out that roasted rare-earth tailings are cooled along with furnace in the above experiments. New formed Fe3O4 is easily oxidized to Fe2O3 by oxygen when temperature is higher than 400 °C, which can reduce iron grade and iron recovery. Therefore, appropriate cooling types should be used to decrease the retention time of rare-earth tailings at the temperature higher than 400 °C. Under calcination conditions with temperature of 570 °C, C/O ratio of 3.85 and holding time of 0.5 h, effects of furnace cooling, air cooling and water cooling on magnetic susceptibility of roasted rare-earth tailings are investigated, as shown in Fig. 6. Compared to that of roasted rare-earth tailings cooled along with furnace, magnetic susceptibility of roasted rare-earth tailings cooled by air and water is more close to 2.33. This can be ascribed to faster cooling speed of roasted rare-earth tailings by air and water, which in oxidation of Fe3O4 to Fe2O3 at temperature of higher 400 °C.
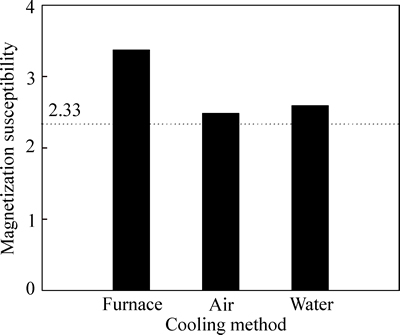
Fig. 6 Influences of cooling methods on magnetization susceptibility of roasted rare-earth tailings (dotted line is theoretical value of magnetization susceptibility)
Magnetization susceptibility, concentrate yield, iron grade and iron recovery are summarized in Table 3 when roasted rare-earth tailings are cooled by air. Magnetization susceptibility of roasted rare-earth tailings at temperature of 650 °C and holding time of 2.5 h is 1.48, suggesting over reduction of Fe2O3. Magnetization susceptibility of roasted rare-earth tailings is 2.48 when temperature is 570 °C and holding time is 0.5 h. Iron grade and iron recovery are 41.30% and 66.99%, respectively, which are larger than those cooled along with furnace at optimal conditions (650 °C and 2.5 h). Magnetization susceptibility of roasted rare-earth tailings is 3.16 at temperature of 500 °C and holding time of 1.0 h, suggesting incomplete reduction of Fe2O3. Concentrate yield is 23.50%-28.00% which is higher than the theoretical value (18.60%), meaning the existence of some gangue minerals in concentrate.
Table 4 lists the magnetization susceptibility, concentrate yield, iron grade and iron recovery when roasted rare-earth tailings are cooled by water. Magnetization susceptibility of roasted rare-earth tailings under various calcination conditions is in the range of 2.10-2.60, which is close to theoretical value (2.33). Concentrate yield is in the range of 20.50%-23.50% which is less than that of roasted rare-earth tailings cooled by air, suggesting lower content of gangue minerals in concentrate from roasted rare-earth tailings cooled by water. Iron grade and iron recovery are 45.00%-49.00% and 65.00%-77.50%, respectively, which are higher than those in concentrate from roasted rare-earth tailings cooled along with furnace and by air. This demonstrates that water cooling is more favor of magnetizing roast and magnetic separation of iron in rare-earth tailings.
Table 3 Magnetic separation results of iron in roasted rare-earth tailings cooled by air

Table 4 Magnetic separation results of iron in roasted rare-earth tailings cooled by water

4 Conclusions
During magnetizing roast process, the temperature, C/O ratio and holding time play important roles in magnetization susceptibility and composition of rare-earth tailings. When furnace cooling type is used to cool roasted rare-earth tailings, magnetization susceptibility of rare-earth tailings gradually approaches to 2.33 and Fe2O3 is gradually reduced to Fe3O4 with increasing temperature from 570 °C to 650 °C, C/O ratio from 1.00 to 3.85 and holding time from 1.0 to 2.5 h. However, iron grade and iron recovery are not satisfactory. After being roasted under the same conditions, cooling types could significantly influence magnetization susceptibility of rare-earth tailings. Compared to that of roasted rare-earth tailings cooled along with furnace and by air, magnetic separation results of iron in roasted rare-earth tailings cooled by water are better. Iron grade and iron recovery are 45.00%-49.00% and 65.00%-77.50%, respectively.
References
[1] JIU Shao-wu, XUE De-long, LI H, SONG Hai-xia, ZHANG L. An investigation into magnetization of siderite powder by roasting in suspension state [J]. Metal Mine, 2008, 386(8): 33-35. (in Chinese)
[2] ZHANG Han-quan, YU Yong-fu, PENG Ze-you, CHEN W. Study on flash magnetizing roasting of Huangmei Limonitic ore [J]. Iron and Steel, 2009, 44(7): 11-14. (in Chinese)
[3] LI Chao, DUN Heng-hu, BAI Jing, LI Long-tu. Innovative methodology for comprehensive utilization of iron ore tailings: Part 1. The recovery of iron from iron ore tailings using magnetic separation after magnetizing roasting [J]. Journal of Hazardous Materials, 2010, 174(1/2/3): 71-77.
[4] YANG Hui-fen, JING Li-li, ZHANG Bao-gang. Recovery of iron from vanadium tailings with coal-based direct reduction followed by magnetic separation [J]. Journal of Hazardous Materials, 2011, 185(2/3): 14.5-1411.
[5] LEON Y S, CHANDRA V. A process for enhanced removal of iron from bauxite ores [J]. International Journal of Mineral Processing, 1991, 31(3/4): 233-246.
[6] LI Mi, PENG Bing, CHAI Li-yuan, PENG Ning, YAN Huan, HOU Dong-ke. Recovery of iron from zinc leaching residue by selective reduction roasting with carbon [J]. Journal of Hazardous Materials, 2012, 237-238: 323-330.
[7] ZHANG Ya-li, LI Huai-mei, YU Xian-jin. Recovery of iron from cyanide tailings with reduction roasting–water leaching followed by magnetic separation [J]. Journal of Hazardous Materials, 2012, 213-214: 167-174.
[8] SUN Yong-sheng, HAN Yue-xin, Gao Peng, WANG Ze-hong, REN Duo-zhen. Recovery of iron from high phosphorus oolitic iron ore using coal-based reduction followed by magnetic separation [J]. International Journal of Minerals, Metallurgy, and Materials, 2013, 20(5): 411-419.
[9] YIN Jia-qing, LV Xue-wei, BAI Chen-guang, QIU Gui-bao, MA Shi-wei, XIE Bing. Dephosphorization of iron ore bearing high phosphorous by carbothermic reduction assisted with microwave and magnetic separation [J]. ISIJ International, 2012, 52(9): 1579-1584.
[10] WANG Cheng-hang, TONG X, SUN Ji-peng. Research on the magnetizing roasting and magnetic separation of an oolitic hematite ore [J]. Metal Mine, 2009(5): 57-59. (in Chinese)
[11] YANG Dao-guo, GU Tian-long, ZHOU Huai-ying, ZENG Jian-min, JIANG Zheng-yi. Recovery of niobium from baogang tailings by carbochlorination [J]. Advanced Materials Research, 2011, 201-203: 1691-1698.
[12] ZHAO Rui-chao, ZHANG Bang-wen, LI Bao-wei. Experimental research on separation of iron from the flotation tailings of Bayun Obo rare-earth minerals [J]. Multipurpose Utilization of Mineral Resources, 2008, 4: 34-38. (in Chinese)
[13] YANG He, RONG Yi, TANG Rong, XUE Xiang-xin, LI Yong. Recovery of iron from Baotou rare earth tailings by magnetizing roast [J]. Rare Metals, 2013, 32(6): 616-621.
[14] ZHANG Yong, MA Peng-qi, CHE Li-ping, QIAN Jian-biao, MA Yan-ping, REN Jun-huan. Study on rare earth flotation from Baogang tailings [J]. Chinese Rare Earths, 2010, 30(2): 93-96. (in Chinese)
[15] ZHANG Li, CHEN Shu, XIONG Xiang-jun, YU Xian-wang, WANG Jun-jie. Directional migration behavior of cerium during sintering process of mischmetal doped cemented carbide [J]. Journal of Central South University of Technology, 2008, 15(1): 6-10.
[16] WANG Jian-ping, YU Ke-xu. Experimental study on gas curtain-assisted high gradient magnetic separation of iron tailing [J]. Multipurpose Utilization of Mineral Resources, 2012, 3: 38-41. (in Chinese)
[17] ZhANG Li-qing, ZHAO Ling-yan, ZHOU Hua-feng, YUAN Ben-fu. Co-extraction of rare earth and iron from baogang tailings [J]. The Chinese Journal of Process Engineering, 2012, 12(2): 218-222. (in Chinese)
(Edited by FANG Jing-hua)
Foundation item: Project(2012CBA01205) supported by National Basic Research Program of China; Projects(50934004, 51274061) supported by the National Natural Science Foundation of China; Project(N110502002) supported by the Fundamental Research Funds for the Central Universities, China
Received date: 2015-06-01; Accepted date: 2015-12-28
Corresponding author: YANG He, Associate Professor, PhD; Tel: +86-24-83684086; E-mail: yangh@smm.neu.edu.cn