软锰矿在辉钼矿焙烧过程中的固硫作用
符剑刚, 钟 宏, 吴江丽, 张小军
(中南大学 化学化工学院, 湖南 长沙, 410083)
摘要: 为克服辉钼矿传统焙烧-氨浸工艺中含硫烟气对环境的严重污染, 提出联产钼酸铵和硫酸锰的软锰矿与辉钼矿共同焙烧新工艺, 并从热力学角度和通过热重分析等手段在理论上论证该新工艺的可行性。 根据焙烧产物的性质, 设计了软锰矿和辉钼矿共同焙烧新工艺的工艺流程, 采用分段升温焙烧, 研究了辉钼矿与软锰矿的物料配比对固硫率的影响。 研究结果表明: 加入软锰矿可以显著降低辉钼矿的焙烧温度, 在450~550 ℃时, MoS2的分解率可达100%, 产物以MnMoO4为主; 焙烧过程中的固硫率随着MnO2含量增加而升高, 固硫效果非常明显, 当n(MnO2)∶n(MoS2)=9时, 固硫率接近98%。
关键词: 辉钼矿; 焙烧; 软锰矿; 固硫; 溶剂萃取
中图分类号:TQ136.1+2 文献标识码:A 文章编号: 1672-7207(2005)06-0994-07
Sulfur-retained in roasting process of molybdenite concentrate by pyrolusite
FU Jian-gang, ZHONG Hong, WU Jiang-li, ZHANG Xiao-jun
(School of Chemistry and Chemical Engineering, Central South University, Changsha 410083, China)
Abstract: In order to avoid pollutant SO2 in the traditional process of roasting and ammonia-leaching for molybdenite, the new process of molybdenite and pyrolusite co-roasting, in which (NH4)2MoO4 and MnSO4 could be obtained at the same time, was put forward, and its practicability was demonstrated theoretically through thermodynamics analysis and thermogravimetry. According to the properties of products, principle technological flow of the new process of molybdenite and pyrolusite co-roasting was designed. The effects of material ratio between MoS2 and MnO2 on sulfur-retained ratio were investigated under the condition of temperature-gradient method roasting. The results show that the roasting temperature can be decreased observably after the addition of pyrolusite, and dissolution ratio of MoS2 can reach 100% at 450~550 ℃, and that MnMoO4 is the major product. The effect of sulfur-retained is very evident, furthermore, the sulfur-retained ratio increases with the dosage of MnO2. When n(MnO2)∶n(MoS2) is 9, the sulfur-retained ratio reaches about 98%.
Key words: molybdenite; roast; pyrolusite; sulfur retained; solvent extract
我国是钼资源大国, 钼精矿生产约7万t/a[1], 相应的工业氧化钼生产厂家达百家之多, 但绝大部分厂家仍然是采用焙烧-氨浸工艺, 加上冶炼厂生产规模小, 工艺及设备落后, 总体质量不高。 生产方式除个别规模较大的企业采用8~12层多膛炉外, 其他中小厂家(占总产量的1/3以上)均用反射炉或回转窑焙烧钼精矿, 且绝大部分厂家不具备二氧化硫的回收能力, 由此每年向大气中排放大量的低浓度含硫烟气(排出SO2约40 kt/a[2]), 对环境造成了严重污染。 环保问题制约着钼工业的稳定、 可持续性发展, 因而, SO2烟气的治理成了亟待解决的关键问题。
要解决SO2烟气污染问题有2种思路: 一是焙烧过程固硫或烟气脱硫; 二是利用含硫烟气制酸。 工业实践证明, 制酸的投资较高, 只有生产规模较大(≥8000 t/a)、 焙烧设备较先进(多膛炉、 沸腾炉等)的条件下制酸才经济可行。 针对国内冶炼厂规模较小、 工艺设备落后且布局分散的特点, 要解决SO2烟气污染只有第一种思路切实可行。
金属综合回收率(Mo和Re等)低、 产品质量差是传统工艺的另一弊端。 主要是因为传统工艺所要求的焙烧温度过高, 使部分Mo和Re随烟气挥发而损失; 另外, 辉钼矿中的Cu, Pb, Zn和Fe等杂质生成的钼酸盐与MoO3的共晶温度低, 易在焙烧过程中发生物料的局部熔化, 产生烧结现象, 既不利于生产操作, 又使烧结物料内部不能被充分氧化, 导致产品中硫与金属杂质含量偏高, 同时也制约了传统焙烧-氨浸工艺在非标准钼精矿方面的应用。 要解决传统焙烧-氨浸工艺的弊端, 关键是探索一种比石灰、 纯碱性能更优异的物质, 在焙烧过程中起到固硫作用, 同时能催化或促进辉钼矿的氧化分解, 降低焙烧温度和分散物料, 防止或抑制烧结, 使硫化矿物氧化充分。 在此, 作者提出了软锰矿和辉钼矿共同焙烧新工艺。
1 辉钼矿与软锰矿共同焙烧新工艺
MoS2的燃点不高(365~465 ℃, 粒度愈小, 燃点温度愈低), 氧化分解时(MoS2+7/2O2→MoO3+SO2)显著放热, 其反应平衡常数也非常大, 而实际生产过程要求温度一般控制在600~700 ℃, 这主要是矿物表面易被生成的氧化物钝化膜所覆盖, 阻碍了氧和二氧化硫2种气体通过表膜向相反方向扩散, 氧化膜的结构与性状同时也决定了气体的扩散速度。 400 ℃左右氧化膜是非常致密的, 而达到600 ℃时氧化膜变得多孔疏松, 温度愈高, 氧化膜愈易变松散和被破坏, 600 ℃时矿物的氧化速率大约为9 μm/min[3]。 通过实验发现, 二氧化锰(软锰矿或化学二氧化锰CMD)是最佳的物质选择, 可以通过软锰矿-辉钼矿共同焙烧新工艺来强化辉钼矿的氧化分解。 软锰矿来源广且价格低廉, 曾用于含硫烟气的湿法脱硫工艺, 它松散多孔且疏水, 在辉钼矿中分散均匀, 利于气体的传输, 增大有效反应面积和反应活性中心; 另外, MnO2氧化性极强, 在较低温度下能直接或促进辉钼矿的氧化分解, 产生的SO2气体能被MnO2氧化转化成为较稳定的硫酸锰。
软锰矿由于性质稳定, 不溶于酸和碱, 工业生产上锰的提取要求通过还原(添加还原剂)转化成为酸溶性的低价Mn(Ⅱ)氧化物, 然后经硫酸酸解、 除杂等工序制得硫酸锰产品。 目前, 国内30多个生产厂家采用还原焙烧—硫酸浸出工艺生产硫酸锰, 生产能力达到30 kt/a, 还原时焙烧温度要求高达700~1000 ℃, 同时还消耗大量粉煤作为还原剂, 生产过程能耗高, 流程长, 污染严重。
利用软锰矿的氧化性和硫化矿的还原性, 20世纪70年代发展了硫化矿物(如黄铁矿、 闪锌矿、 黄铜矿)与软锰矿的联合浸出工艺[4-7], 该工艺具有流程短、 设备简单、 环境污染小的特点, 部分已成功地实现工业化生产, 由于软锰矿与辉钼矿共同焙烧既有一定的相关实践基础, 在理论上又切实可行, 因而该工艺有望成为能综合回收钼、 铼、 锰的一种资源化、 短流程的洁净冶金工艺。
2 焙烧体系的热力学分析
2.1 MoS2的单独氧化焙烧
在焙烧过程中常见的MoS2的氧化产物为MoO3和MoO2, 其中, MoO2不溶于水或氨水, 浸出工艺中留在渣相, 会降低Mo的回收率。 图1[8]所示为不同温度下MoS2与MoO3在氩气介质中的相互反应, 图2[9]所示为900 K时Mo-S-O体系的优势区域图。 从图1、 图2可以看出, 在辉钼矿的焙烧氧化过程中MoO2的产生原因有如下几种: 一是生成的氧化产物MoO3与MoS2反应(6MoO3+MoS2=7MoO2+2SO2)的产物, 该反应在一定温度条件下极易发生; 二是焙烧过程中供氧不足引起辉钼矿氧化不完全, 或焙烧温度不够高而导致氧化程度低 (MoS2+3O2=MoO2+2SO2); 三是MoO3与其他金属(Fe, Cu, Zn, Pb等)钼酸盐易形成低熔点共晶, 使得包裹在内的辉钼矿物氧化不透彻。 在一般的工艺设备(反射炉、 回转窑)条件下, 由于不完全的氧化产物造成钼回收率损失达5%, 甚至更高。 图2表明, 在较高的焙烧温度条件下, 辉钼矿的氧化趋势很大, 对氧化气氛的要求较低, 因而强化辉钼矿的焙烧分解应从其他工艺条件着手。
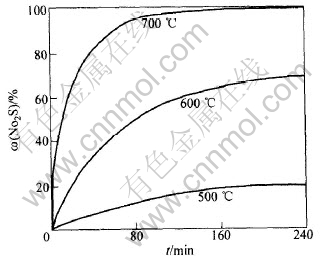
图 1 MoS2与MoO3在氩气介质中的相互反应速度
Fig. 1 Reaction speed between MoS2 and MoO3 in argon
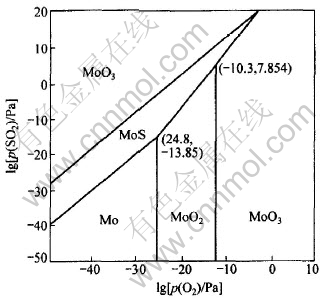
图 2 900 K时Mo-S-O的优势区域图
Fig. 2 Phase stability diagraph for Mo-S-O system at 900 K
2.2 辉钼矿与软锰矿共同焙烧体系
辉钼矿与软锰矿共同焙烧体系中涉及的反应主要有: MoS2和其他金属硫化物的氧化(氧化剂为氧气或MoO3, MnO2), MnO2的分解、 还原(还原剂为SO2或金属硫化物)。 Mo和Mn涉及的主要反应及其热力学计算结果如表1所示。
反应(1)~(3)的自由能均为负, 说明辉钼矿的氧化分解反应能进行彻底。 从反应(6)和(10)可以看出, 理论上(热力学)软锰矿或其分解产物Mn2O3均能够吸收二氧化硫并转化成为稳定的MnSO4, 反应基本上不可逆, 且焙烧温度愈低, 反应趋势愈大。 反应(12)表明软锰矿能作为氧化剂, 能直接将辉钼矿氧化成为MoO3, 而反应(15)则表明软锰矿能强化辉钼矿的分解, 将氧化不完全的产物MoO2进一步转化成为MoO3, 能促进钼的浸出, 提高金属的最终回收率, 同时有可能降低焙烧所需温度。
提高焙烧温度, SO2气体产生的速率加快, 其逸出矿物物料表面的速度也越大, 不利于被吸收, 考虑到反应(10)极易发生, 且产物在0~700 ℃时均很稳定, 因此, 采用分段升温进行焙烧的方案。 先在较低温度下, 使辉钼矿发生较慢的氧化反应, 尽可能使释放出SO2气体的速度与其被软锰矿所吸收的速度匹配或相近, 温度愈低时, 反应(10)进行得愈彻底; 然后, 升高焙烧温度, 以便使产物中低价Mo氧化物进一步氧化, 而被固定下来了的硫不会因此发生改变, 且该过程在工业上可方便地实现(采用不同温度区间焙烧)。
表 1 焙烧体系可能发生的反应及自由能
Table 1 Possible reactions and their free energy in roasting system
2.3 辉钼矿与软锰矿的热重分析
采用热分析仪(STA2409PC型, 德国NETZSCH公司)在空气气氛中, 以10 ℃·min-1的升温速率测定辉钼矿(取自江西德兴某铜矿钼精矿, w(Mo)=47.91%)、 辉钼矿+MnO2(分析纯, 含量大于85%, n(MoS2)∶n(MnO2)=1∶2)及MnO2, 其热重分析曲线如图3~5所示, 对3条热重曲线进行比较, 结果如图6所示。

图 3 辉钼矿的热重分析曲线
Fig. 3 Thermogravimetric curves for molybdenite concentrates
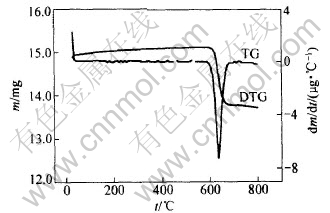
图 4 辉钼矿与MnO2(n(MoS2)∶n(MnO2)=1∶2)的热重分析曲线
Fig. 4 Thermogravimetric curves for mixture of molybdenite and MnO2
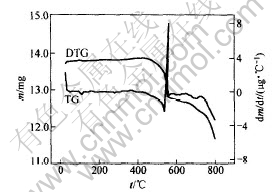
图 5 MnO2的热重分析曲线
Fig. 5 Thermogravimetric curves for MnO2
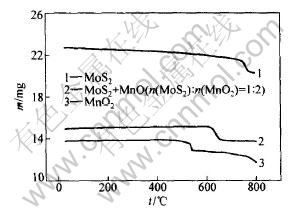
图 6 热重分析曲线比较
Fig. 6 Thermogravimetric curves for MoS2, MnO2 and mixture MoS2 and MnO2
由图3可以看出, 辉钼矿在50~750 ℃时一直处于“失重”状态。 在50~200 ℃, 矿物中浮选药剂的挥发或分解; 在200~550 ℃, MoS2开始缓慢氧化和其他硫化矿物(黄铜矿、 硫铁矿等)发生氧化分解, 释放出二氧化硫; 在550~780 ℃, 辉钼矿的氧化速度加剧, 样品质量急剧减小; 当温度高于780 ℃时变化甚微, 氧化产物约余90%, 此时辉钼矿正好分解完全(MoS2→MoO3)。
随着温度升高, MnO2质量减小(见图5), 在490 ℃左右时质量慢慢减小, 在该过程中样品中灰分杂质挥发; 当温度升到520~550 ℃时, MnO2剧烈分解, 放出氧气, 质量减小, 分解产物为三氧化二锰; 温度升高时, 三氧化二锰继续发生分解, 释放出氧气, 生成四氧化三锰。 在0~600 ℃, 样品的质量略有增长(图4)。 对照图3和图5可知, 辉钼矿和其他金属硫化矿物氧化分解放出的SO2气体, 大部分被MnO2吸收, SO2的吸收程度与MnO2添加质量有关。 从图4、 图6还可以看出, 样品氧化完全的温度由辉钼矿单独焙烧时的780 ℃降低到2种矿物共同焙烧时的650 ℃左右, 说明MnO2的加入一方面能起固硫作用, 抑制含硫烟气的排放, 另一方面能促进辉钼矿的氧化分解, 显著降低焙烧温度, 强化焙烧过程。
3 焙烧试验
根据焙烧产物的性质, 设计的联产钼酸铵和硫酸锰的软锰矿和辉钼矿共同焙烧新工艺的原则工艺流程如图7所示。
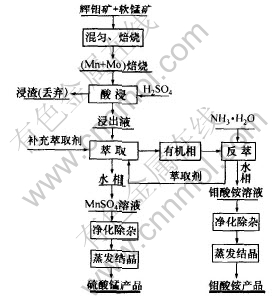
图 7 软锰矿和辉钼矿共同焙烧新工艺的原则工艺流程
Fig. 7 Flow sheet of co-roasting with molybdenite and pyrolusite
辉钼矿与软锰矿共同焙烧的实验装置必须能实现SO2气体的在线检测。 结合工业三氧化钼生产现有工艺或设备, 设计的焙烧试验装置如图8所示。
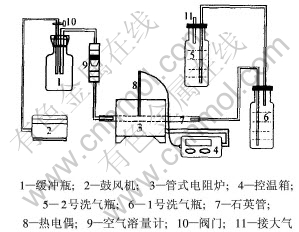
图 8 软锰矿与辉钼矿共同焙烧的实验装置
Fig. 8 Diagraph of co-roasting equipments for molybdenite and pyrolusite
软锰矿与辉钼矿共同焙烧时的尾气采用碘液吸收, 未反应完全的I2用Na2S2O3溶液返滴定, 以此来计算逸出的SO2质量, 固硫率η按下式计算:
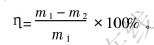
式中: m1为辉钼矿中S的质量, g; m2为逸出SO2中S的质量, g。
4 焙烧试验结果
4.1 固硫试验
采用分段升温法研究辉钼矿与软锰矿物料配比对固硫率的影响, 结果如表2所示。 从表2可以看出, 软锰矿的加入可以显著降低辉钼矿的焙烧温度, 即使温度不高于550 ℃, MoS2的分解率也可以达到100%; 焙烧过程中的固硫率随着MnO2含量增加而升高, 当n(MnO2)∶n(MoS2)=9时, 固硫率达到98%左右, 固硫效果非常明显。 通过优化焙烧工艺条件, 如温度、 风量、 混料状况等, 可在较低软锰矿用量下获得较理想的固硫率。
4.2 焙烧产物的物相分析
取试验2的焙烧产物进行料物相分析, X射线衍射图如图9所示。
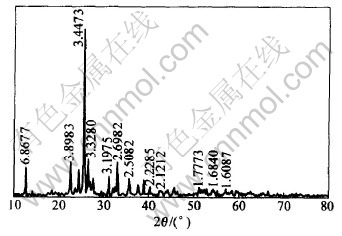
图 9 辉钼矿和软锰矿共同焙烧产物的物相分析
Fig. 9 XRD pattern of calcine from co-roasting molybdenite and pyrolusite
图9表明, 焙烧产物以MnMoO4为主, 相应的特征角(2θ)为12.880, 22.793, 24.691, 25.832, 26.766, 27.879, 31.292, 32.178, 33.176, 35.769, 37.828, 39.102, 40.442, 44.420, 51.367, 其余峰对应SiO2, MoO3, MnSO4等。 焙烧过程生成MnMoO4可能的反应有:
MoS2+7/2O2→MoO3+2SO2;
MnO+MoO3→MnMoO4;
9MnO2+MoS2→MnMoO4+6MnO+2MnSO4。
实验表明, 钼酸锰溶于酸性(pH≤4)溶液, MoO3溶于强酸或强碱溶液, 而在强酸溶液中(ρ(H2SO4)≥100 g/L), Mo易形成络合物离子([MoO2(SO4)2]2-)[11-12]而被N235所萃取[13-15], 可以实现与其他金属阳离子的分离。
表 2 辉钼矿和软锰矿共同焙烧新工艺固硫试验结果
Table 2 Roasting results of molybdenite and pyrolusite
选取实验3的焙烧产物, 经质量浓度为180 g/L的硫酸浸出后, 利用萃取剂(20%N235+10%仲辛醇+70%磺化煤油)进行萃取, 有机相用17%(质量分数)的氨水反萃, 反萃液经净化、 蒸发结晶得到钼酸铵; 萃余相用CaO调整pH值, 再除杂、 精制得到硫酸锰产品。 具体工艺条件及回收率如表3所示。
表 3 浸出工艺条件及结果
Table 3 Leaching conditions and results
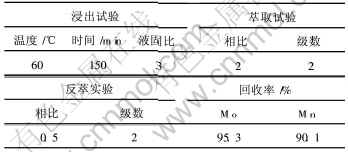
5 结 论
a. 为克服辉钼矿传统焙烧-氨浸工艺中含硫烟气严重污染环境的弊端, 提出了联产钼酸铵和硫酸锰的软锰矿与辉钼矿共同焙烧新工艺。 从热力学角度和通过热重分析等手段从理论上论证了该新工艺的可行性。
b. 采用分段升温焙烧, 研究了辉钼矿与软锰矿的物料配比对固硫率的影响。 实验结果表明, 软锰矿的加入可以显著降低辉钼矿的焙烧温度, 在450~550 ℃时, MoS2的分解率可达100%, 产物以MnMoO4为主; 焙烧过程中的固硫率随着MnO2含量增加而升高, 固硫效果非常明显, 当n(MoS2)∶n(MnO2)>7时, 固硫率可超过91%; 根据焙烧产物的性质, 设计了软锰矿和辉钼矿共同焙烧新工艺的原则工艺流程, Mo和Mn的最终回收率分别在95%和90%以上。
参考文献:
[1]罗振中. 钼的应用及其发展[J]. 中国钼业, 2003, 27(2): 7-11.
LUO Zhen-zhong. Application and development of molybdenum[J]. China Molybdenum Industry, 2003, 27(2): 7-11.
[2]黄海芳. 钼精矿焙烧的污染浪费及对策[J].铁合金, 2002, (1): 16-19.
HUANG Hai-fang. Pollution and waste of baking molybdenite concentrate and the countermeasures[J]. Ferro-alloys, 2002, (1): 16-19.
[3]向铁根. 钼冶金[M]. 长沙: 中南大学出版社, 2002.
XIANG Tie-gen. Molybdenum Metallurgy[M]. Changsha: Central South University Press, 2002.
[4]Sahoo R N, Naik P K, Das S C. Leaching of manganese from low-grade manganese ore using oxalic acid as reductant in sulphuric acid solution[J]. Hydrometallurgy, 2001, 62: 157-163.
[5]袁明亮, 梅贤功, 庄剑鸣, 等. 软锰矿两矿法选择性浸出[J]. 中国有色金属学报, 1996, 6(3): 22-25.
YUAN Ming-liang, MEI Xian-gong, ZHUANG Jian-ming, et al. Selective leaching of manganese dioxide ore with two ore method[J]. The Chinese Journal of Nonferrous Metals, 1996, 6(3): 22-25.
[6]Abou-El-Sherbini K S. Simultaneous extraction of manganese from low-grade manganese dioxide ore and beneficiation of sulphur slag[J]. Separation and Purification Technology, 2002, 27(1): 67-75.
[7]Das P K, Mishra D, Anand S, et al. Reduction of Mn(IV) oxide by NH SO in the presence of metal ions in ammoniacal medium[J]. Hydrometallurgy, 1999, 52(1): 91-104.
[8]赵业松. 钼铁生产用氧化钼的焙烧方法[J]. 有色金属(冶炼部分), 1998, (5): 24-26.
ZHAO Ye-song. Roasting method of molybdenum oxide for produce ferromolybdenum[J]. Nonferrous Metal (Smelting Section), 1998, (5): 24-26.
[9]许志宏. 无机热力学数据库[M]. 北京: 科学出版社, 1987.
XU Zhi-hong. Inorganic Thermodynamics Database[M]. Beijing: Science Press, 1987.
[10]叶大仑. 实用无机物热力学数据库手册[M]. 北京: 冶金工业出版社, 2002.
YE Da-lun. Practical Thermodynamics Data Handbook of Inorganic Substances[M]. Beijing: Metallurgy Industry Press, 2002.
[11]Gerhardt N I, Palant A A, Dungan S R. Extraction of tungsten VI, molybdenum VI and rhenium VII by diisododecylamine[J]. Hydrometallurgy, 2000, 55(1): 1-15.
[12]Gupta C K. Extractive metallurgy of molybdenum[M]. London: CRC Press, 1992.
[13]Sweetser J, William H, Leonard N. Process for autoclaving molybdenum disulfide[P]. US5804151, 1998-09-08.
[14]曾平, 胡静宇. 伯胺N1923萃取钼的机理研究[J]. 高等学校化学学报, 1994, 15(11): 1588-1591.
ZENG Ping, HU Jing-yu. Studies on the extraction mechanism of molybdenum by primary amine N1923 in kerosene[J]. Chemical Journal of Chinese University, 1994, 15(11): 1588-1591.
[15]Juneja J M. Investigations on the extraction of molybdenum and rhenium values from low-grade molybdenite concentrate[J]. Hydrometallurgy, 1996, 41(3) : 201-209.
收稿日期:2005-04-25
作者简介:符剑刚(1975-), 男, 湖南桃江人, 讲师, 博士研究生, 从事化工冶金方面的研究
论文联系人: 符剑刚, 男, 讲师; 电话: 0731-8836309(O); E-mail: fu_jiangang@126.com