文章编号:1004-0609(2012)02-0343-07
热处理对不同冷速Al合金共晶相形貌及含量的影响
赵光伟1,李新中1,徐达鸣1,郭景杰1,傅恒志1,贺跃辉2,杜 勇2
(1. 哈尔滨工业大学 材料科学与工程学院,哈尔滨 150001;
2. 中南大学 粉末冶金国家重点实验室,长沙 410083)
摘 要:选取成分为Al-5.17Cu-2.63Si(合金A)、Al-4.29Cu-1.09Mg(合金B)和Al-2.09Si-1.66Mg(合金C)三元铝合金,分别进行不同冷速下的凝固实验。对比研究不同凝固速率下得到的共晶相形貌与含量在接近各合金体系三元共晶温度下热处理前后的变化行为。结果表明:同一合金冷速越慢,得到的原始组织二次枝晶间距越大,合金A的石墨型、砂型、保温型冷却组织的二次枝晶间距分别为24.17、63.32和99.88 μm,合金B的二次枝晶间距分别为24.35、82.78和139.42 μm。均匀化热处理的热扩散过程可以明显地溶解非平衡共晶相,由于原始组织的尺度不同,共晶相所处的溶解阶段与溶解程度不同。合金A的石墨型、砂型、保温型组织热处理后与热处理前的共晶相含量比值分别为0.44、0.49和0.68,合金B的共晶相含量比值分别为0.084、0.30和0.38。
关键词:凝固速率;共晶相;均匀化处理;三元Al合金
中图分类号:TG166.3 文献标志码:A
Influence of heat treatment on morphology and quantity of
eutectic phases of Al alloys with different cooling rates
ZHAO Guang-wei1, LI Xin-zhong1, XU Da-ming1, GUO Jing-jie1, FU Heng-zhi1, HE Yue-hui2, DU Yong2
(1. School of Materials Science and Technology, Harbin Institute of Technology, Harbin 150001, China;
2. State Key Laboratory of Powder Metallurgy, Central South University, Changsha 410083, China)
Abstract: The solidification experiment with different solidification rates was carried out on three ternary alloys of Al-5.17Cu-2.63Si (alloy A), Al-4.29Cu-1.09Mg (alloy B) and Al-2.09Si-1.66Mg (alloy C). The influence of heat treatment on morphology and quantity of the non-equilibrium eutectic phases at the temperature close to the ternary eutectic point was investigated. The results show that the second dendrite space increases with decreasing the solidification rate. The secondary dendrite spacing of alloy A is 24.17 μm for the graphite mould, 63.32 μm for the sand mould, and 99.88 μm for the insulated mould, respectively, and the corresponding values of alloy B are 24.35, 82.78 and 139.42 μm. The nonequilibrium eutectic phases can be dissolved in the diffusion process during the heat treatment process. And the quantity of the dissolved eutectic phases depends on the initial microstructure. For alloy A the ratio of eutectic phase volume fraction after heat treatment to that before heat treatment are 0.44, 0.49 and 0.68, for the initial microstructure of graphite mould, sand mould and insulated mould, respectively, and the corresponding values of alloy B are 0.084, 0.30 and 0.38.
Key words: cooling rates; eutectic phases; granulation process; ternary Al alloys
铸造铝合金具有密度小、比强度高等优点,并有良好的抗蚀性和铸造工艺性,可进行各种成型铸造。但是,由于铸锭组织中不可避免会产生组织和成分不均匀性,如出现非平衡第二相和过多的过剩相及偏析等,使合金的性能受到影响[1]。均匀化处理过程,也称均匀化退火或扩散退火,由于温度高、原子扩散 快,可以在一定程度上消除铸锭组织的不均匀性,枝晶间偏析将消失,沿晶界分布的非平衡共晶相以及其它非平衡相将被全部或部分溶解,有的过剩相还可能被球化,从而显著提高合金的塑性和组织的化学稳定性[2-3]。
国内外有很多学者开展了均匀化热处理过程中铸锭组织形貌演变方面的工作,这些研究集中于均匀化热处理对Al-Si和Al-Cu等二元合金中非平衡共晶相的溶解、粒状化以及粗化的演变过程与机理[2-6],也有工作研究了多元Al基合金的非平衡二次相形貌及成分偏析在热处理过程中的演变[7-10]。在实际铸造生产中,特别是对于多元多相合金,冷却速率对凝固组织形态、相的析出次序、种类及数量都具有重要的影响。因此,同种合金在不同冷速下得到的凝固组织是不同的,进而热处理过程中的非平衡相的演变行为也会不同。本文作者采取不同成分的三元Al合金进行凝固实验,得到不同的铸态组织,重点研究不同冷却速率下得到的凝固非平衡组织在均匀化热处理过程中的演变行为,包括共晶相的溶解、粒状化及形貌的变化等。
1 实验
配料采用99.99%工业纯铝、99.80%电解铜板、99.90%纯Mg,及工业纯Si,在高纯石墨坩埚电阻炉中熔配出Al-Cu、Al-Si中间合金,再加入上述纯金属配出所需成分,3种实验合金成分分别为:合金A,Al-5.17Cu-2.63Si(质量分数,下同);合金B,Al-4.29Cu- 1.09Mg;合金C,Al-2.09Si-1.66Mg。
为使同成分合金在3种差别较大的冷却速度下凝固,熔炼后分别浇注到3种导热能力不同的铸型:石墨型、水玻璃砂型、硅酸铝纤维毡保温型(型腔表面涂刷ZnO,简称保温型)。浇注过程使用K型热电偶进行温度数据采集。图1所示为铸型尺寸、测温位置以及铸态组织与均匀化热处理组织试样的取样位置。热处理温度是通过Thermal-Calc软件对3种合金的三相共晶平衡结晶温度进行核算,并结合冷却曲线测得的共晶平台温度算入误差,最终分别确定如下:合金A为490 ℃,合金B为480 ℃,合金C为535 ℃。另外,为使溶质元素尽可能充分扩散,均匀化热处理时间均取为30 h,并用石英管进行了真空封装。微观组织观察采用了Hitachi S-4700型扫描电子显微镜(SEM),试样进行了打磨、抛光,未做任何腐蚀。
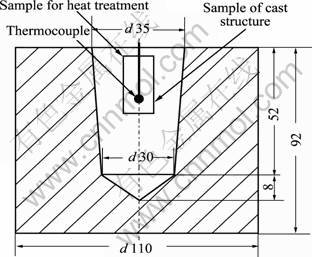
图1 铸型尺寸示意图、测温热电偶安放位置及取样位置
Fig. 1 Dimensions of mold and positions of thermocouple and samples (mm)
2 实验结果
图2(a)~(c)所示分别为合金A(Al-5.17Cu-2.63Si)的石墨型、砂型及保温型试样凝固组织的SEM像。可以看到,随着冷速的降低,枝晶间距变大,凝固组织也变得粗大。基体上分布的暗色较大块的组织为两相共晶中的Si相,而亮色与尺寸相对较小的(含针状)暗色组织的混合区为三相共晶(α+θ+Si),其中α为α(Al),θ相位Al2Cu,Si即表示Si相(下同)。合金A在3种铸型中的凝固路径为(L→α)→(L→α+Si)→ (L→α+θ+Si)。图2(d)~(f)所示分别为石墨型、砂型及保温型试样在490 ℃经过30 h均匀化热处理得到的凝固组织的SEM像。由图2(d)可以看出,石墨型试样的三相共晶中的Si相并没有全部消失,θ相出现了明显的熔断及粒状化,原有的枝晶形貌已经基本消失。图2(e)中,砂型试样的两相共晶中大部分Si保留下来,只是形貌发生了变化,尖角出现圆整化,而三相共晶中的针状Si也是部分被溶解。而保温型试样(见图2(f))的两相共晶与三相共晶中的Si相大部分被保留。三相共晶中的Si相明显趋于粒状化,而两相共晶中Si相形貌的圆整化程度明显不如三相共晶中的Si相。另外保温型试样两相共晶中的Si相的粒状化程度也不如砂型试样组织明显,保留了部分的平直界面。
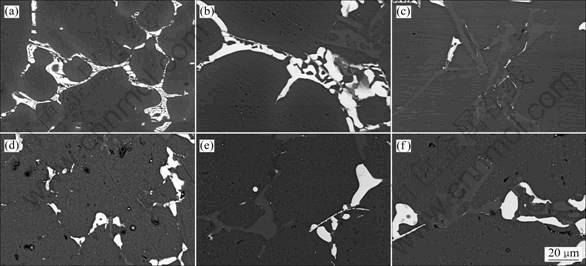
图2 不同冷速合金A(Al-5.17Cu-2.63Si)试样在490 ℃热处理30 h前后的组织对比
Fig. 2 Comparison between microstructures before and after solid-state solution treatments (490 ℃, 30 h) for Al-5.17Cu-2.63Si specimens solidified under different cooling rates: (a) Before, graphite mold, 5.685 ℃/s; (b) Before, sand mold, 0.454 ℃/s; (c) Before, insulated mold, 0.067 6 ℃/s; (d) After, graphite mold specimen; (e) After, sand mold specimen; (f) After, insulated mold specimen
图3(a)~(c)所示分别为合金B(Al-4.29Cu-1.09Mg)的石墨型、砂型及保温型试样凝固组织的SEM像。其中较大块亮相为两相共晶中的θ,而较细小的黑白相间组织为三相共晶(α+θ+S),其中S相为Al2CuMg。合金B在3种铸型中的凝固路径为(L→α)→(L→α+θ)→(L→α+θ+S)。图3(d)~(f)所示分别为石墨型、砂型及保温型试样在480 ℃经过30 h均匀化热处理得到的凝固组织电镜照片。由图3(d)可以看到,均匀化热处理过程对于石墨型试样的共晶组织形貌的影响十分明显,枝晶形貌已经完全消失,变成弥散分布的第二相颗粒。热处理前样品中黑白相间的三相共晶中只剩下亮的粒状的θ相颗粒,两相共晶中的θ相的粒状化效果也比较好。而对于图3(e)和(f)显示的砂型与保温型试样也观察到类似的现象,三相共晶中的S相已经消失,只剩下少量的θ相。但是砂型与保温型热处理后两相共晶中的θ相的粒状化效果明显比石墨型差,枝晶尖端出现圆整化,尖角消失,较细的枝晶出现熔断现象,但是保留了部分枝晶形貌。

图3 不同冷速合金B(Al-4.29Cu-1.09Mg)试样在480 ℃热处理30 h前后的组织对比
Fig. 3 Comparison between microstructures before and after solid-state solution treatments (480 ℃, 30 h) for Al-4.29Cu-1.09Mg specimens solidified under different cooling rates: (a) Before, graphite mold, 7.220 ℃/s; (b) Before, sand mold, 0.474 ℃/s; (c) Before, insulated mold, 0.063 5 ℃/s; (d) After, graphite mold specimen; (e) After, sand mold specimen; (f) After, insulated mold specimen
图4(a)~(c)所示分别为合金C(Al-2.09Si-1.66Mg)的石墨型、砂型及保温型试样的凝固组织的SEM像。其中较大块黑色相为两相共晶中的Mg2Si相,而比较细小的灰黑相间的组织为三相共晶(α+Mg2Si+Si),图4(f)中高亮组织为少量Fe杂质形成的富铁相。合金C在3种铸型中的凝固路径为(L→α)→(L→α+Mg2Si)→ (L→α+Mg2Si+Si)。图4(d)~(f)所示分别为石墨型、砂型及保温型试样在535 ℃经过30 h均匀化热处理得到的凝固组织的SEM像。分别对比图4(a)与(d)、(b)与(e)可知,石墨型与砂型试样中的枝晶状Mg2Si相呈现出明显的球状化并且已经粗化(从低倍组织照片中可以看到Si相并没有完全溶解,而是有少量剩余并出现粒状化及粗化)。而对比图4(c)与(f)可以看到,保温型三相共晶组织中Mg2Si相基本消失,Si相并没有完全消失而是呈现出粒状化以及粗化现象;两相共晶中Mg2Si的粒状化及粗化程度要低于石墨型与砂型试样的,仍然保留了部分原有的枝晶形貌。

图4 不同冷速合金C(Al-2.09Si-1.66Mg)试样在535 ℃热处理30 h前后的组织对比
Fig. 4 Comparison between microstructures before and after solid-state solution treatments (535 ℃, 30 h) for Al-2.09Si-1.66Mg specimens solidified under different cooling rates: (a) Before, graphite mold, 6.908 ℃/s; (b) Before, sand mold, 0.541 ℃/s; (c) Before, insulated mold, 0.052 5 ℃/s; (d) After, graphite mold specimen; (e) After, sand mold specimen; (f) After, insulated mold specimen
3 分析与讨论
3.1 不同冷速原始组织的非平衡共晶相的减少
在实际生产条件下的凝固过程中,由于固液相溶质元素都不可能充分扩散,因此会产生非平衡二次相。均匀化热处理过程,由于温度高,原子扩散快,且溶质元素在α(Al)基体的固溶度远高于室温下的,因此可以使非平衡二次相发生溶解。本文作者对合金A、B热处理前后共晶相含量进行了统计与对比分析。共晶相含量统计采用ImagePro软件[11],对于Al-Cu-Si合金,由于Si与Al的原子序数相近,Si相与基体α(Al)相在扫描电镜下亮度几乎一样,在此,对只对热处理前后的θ相含量进行了统计与对比;低倍下Al-Cu-Mg合金的两相共晶与三相共晶难于区分,因此统计了所有的亮相:两相共晶中θ相、三相共晶中的(θ+S)相。
图5(a)和(b)所示分别为合金A、B热处理前后的共晶相含量对比(体积分数),可以看到两个合金共晶相的含量都随着凝固速率而增加,而热处理之后共晶相的含量明显减少。另外,热处理后与热处理前共晶相含量的比值变化是随冷速减慢依次增加的。该现象可用FLEMINGS等[4]提出的固溶退火理论来定性解释,当热处理温度与最大固溶线温度接近时,热处理前后共晶相的相对含量可以表示为
(1)
式中:
与
分别为热处理前后的共晶相含量;Ds为Cu的扩散系数(由于Cu在α(Al)的扩散系数比Mg的要小,因此认为热扩散过程受Cu的扩散控制[7]);t为热处理时间;l0为二次枝晶间距的一半。当热处理时间确定后,热处理前后的共晶相含量仅与l0有关。
本实验中的情况与式(1)并不完全相同,由于所选的合金成分α(Al)的固溶区之外(见图6,利用ThermoCalc计算的本实验中合金系在热处理温度的等温截面图及合金位置),因此即使热处理时间足够长,共晶相也不会全部消失。因此热处理前的共晶相(
)包含平衡共晶相与非平衡共晶相两部分。基于以上原因,这里就本实验合金给出共晶相溶解的定性解释。以合金B为例,热处理前石墨型、砂型、保温型的两相共晶的二次枝晶间距的分别为24.35、82.78和139.42 μm,依次增加,因此由式(1)可知,热处理后与热处理前共晶相含量的比值(
/
)应呈递增的趋势,而测量值分别为0.084、0.30、0.38,与式(1)一致。另外,对于同一成分合金,随着凝固速率增加,原始组织中的平衡共晶相的含量是一定,而非平衡共晶相部分的含量越高(即
越大),而热处理过程使非平衡共晶相大部分溶解,平衡共晶相趋于一致(即
趋于一致),这是造成
/
随冷速减慢而增加的原因。同理合金A也满足相同的规律,石墨型、砂型、保温型凝固试样的二次枝晶间距分别为24.17、63.32和99.88 μm;热处理后与热处理前共晶相含量的比值(
/
)分别为0.44、0.49和0.68。
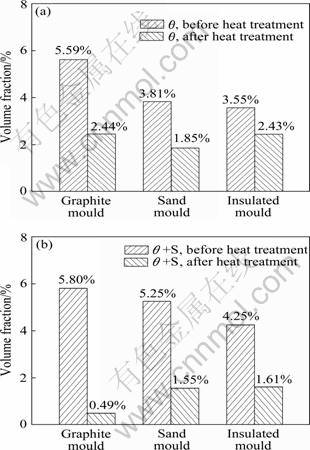
图5 合金A、B热处理前后共晶相含量对比
Fig. 5 Comparisons of quantity of eutectic phases before and after heat treatment: (a) Alloy A; (b) Alloy B
3.2 不同冷速原始组织的共晶相粒状化及粗化
所谓第二相粒状化是指第二相在热处理过程中由非粒状(如片状、树枝状、纤维状等)转变为粒状的过程。粒状化过程的热力学条件为:第二相的减少引起界面自由能减少,第二相畸变能降低,体系总的自由能下降;动力学条件:组成第二相的元素在基体中必须有一定的溶解度并有一定的扩散速度。热处理过程中,非平衡第二相将经历熔断、粒化和粗化三个相互影响且交叉进行的变化阶段[10, 13]。对于二元合金[2-5],共晶相的尺度比较平均、单一,上述3个过程在时间上分界比较明显。在本实验中,由于同种成分合金在不同冷速下冷却,共晶相又包括两相共晶与三相共晶,因此,凝固组织出现了3种不同的特征尺度,分别为三相共晶片间距λ3E、两相共晶片间距λ2E、初生相二次枝晶间距d2,对于不同尺度的共晶相来说,上述3个阶段是交叉进行的。
对于合金A,由图2热处理前后的组织对比也可以看到,不同冷速组织由于尺度不同,所处的热处理阶段不同,石墨型组织的θ相由于枝晶尺度较小,已经完成熔断,正处于粒状化阶段;砂型组织大部分熔断,并出现部分粒状化形貌;而保温型组织的θ相只是尖端出现圆整化,还有较多的短杆状形貌,并且短杆状枝晶上有枝晶凹槽,可见该试样正处于热处理初期的熔断阶段。由于原始组织尺度不同而造成非平衡相所处热处理粒状化阶段不同的现象在图3合金B中更加明显,石墨型组织中的共晶相已经大部分消失,剩余的也出现粒状化;砂型组织中较细小的枝晶已经熔断并粒状化或消失,较粗大的组织正在熔断;而保温型组织中的θ相正处在熔断阶段。另外,需要注意的,合金B各铸型的三相共晶中S相消失而θ相却保留下来,该现象的热力学解释可以从图6(b)给出,可以看到,480 ℃时合金B处于Al-Cu-Mg三元合金等温截面图的(α+θ)两相区内并且距(α+S)的区域较远,因此如果时间足够长,S会完全被溶解;而动力学方面,480 ℃时,Mg在α(Al)基体中的扩散速率约是Cu的2.5倍[11],这也是原因之一。
粒状化过程及粗化过程的第二相的长大可以用LSW模型来定性解释[14-16],当第二相粒子在基体中的扩散速率一定时:
(2)
式中:K为粗化速率常数;t为时间;Ri为经过时间t的第二相半径;R0为第二相初始半径;λ为无量纲常数;c0为第二相原子在基体中的平衡浓度;D为第二相原子在基体中的扩散系数;Vm为第二相原子体积;γ=σA,为界面张力σ与界面总面积A的乘积,表示第二相与基体之间(设各向同性)的总界面能;R为摩尔气体常数;T为绝对温度。
由于实验中各组试样热处理的温度T与时间t相同,同种共晶相第二相原子的扩散系数D以及原子体积Vm也相同,因此对于同种形貌的枝晶,影响粒状化及粗化的因素只剩下:初始第二相粒子半径R0,总的界面能γ,以及第二相原子在基体中的平衡浓度c0。
对于合金A和合金B,由图2及3可以明显看到,随着冷速的升高,保温型、砂型、石墨型凝固组织的粒状化效果依次变好。具体有如下3个方面的原因:1) 随着凝固速率升高,凝固枝晶的原始尺寸越细小且共晶相含量越高,因此,界面面积A越大从而导致界面能γ越高;2) 凝固枝晶的原始尺寸越细小,枝晶分支及凹槽等能态较高的缺陷部位较多,所以更加容易熔断。一方面熔断枝晶更加细小,可以缩短原子从枝晶尖端扩散到中部的距离,另一方面熔断枝晶数量增加可以进一步增加界面面积A从而导致界面能γ越高;3) 凝固速率越快,枝晶间的偏析会更加明显,由于各合金体系的溶质分配系数都小于1,因此导致第二相原子在基体中的浓度c0升高。
另外,需要注意的是本实验中的3组合金中,只有合金C两相共晶中的Mg2Si产生了明显的粗化现象,而合金A、B并没有出现明显的粗化现象。原因之一是合金C处于Al-Si-Mg合金的535 ℃等温界面的(α+Mg2Si+Si)三相区内(见图6),热处理过程并不能是共晶相全部消失,粒状化过程完成之后,粗化过程逐渐占据主导地位;另外,从动力学角度考虑,在本研究选取的热处理温度下:Al-Si-Mg合金中Si和Mg在α(Al)中的扩散系数分别为46.77×10-8 mm2/s与23.00×10-8 mm2/s,Al-Cu-Si合金中Cu和Si分别为3.44×10-8 mm2/s与14.48×10-8 mm2/s,而Al-Cu-Mg合金中Cu和Mg在480 ℃的扩散系数分别为2.60×10-8 mm2/s与6.59×10-8 mm2/s [11]。可以看到,合金C在热处理温度下溶质的扩散系数远大于其它两个合金体系的,因此在热处理时间相同的情况下,合金C的共晶相可以更快的完成熔断、粒状化过程而进入粗化阶段。

图6 实验合金体系在热处理温度下的等温截面图及合金位置
Fig. 6 Positions of investigated alloys on isothermal section at heat treatment temperature: (a) Al-Cu-Si alloy, 490 ℃; (b) Al-Cu-Mg, 480 ℃; (c) Al-Si-Mg, 535 ℃
4 结论
1) 冷却速率对凝固组织影响明显,随着冷却速率的降低,二次枝晶间距增大。合金Al-5.17Cu-2.63Si的石墨型、砂型、保温型冷却组织的二次枝晶间距分别为24.17、63.32和99.88 μm,合金Al-4.29Cu-1.09Mg的二次枝晶间距分别为24.35、82.78和139.42 μm。
2) 均匀化热处理的热扩散过程可以明显地溶解非平衡共晶相,由于原始组织的尺度不同,共晶相的溶解程度不同。合金Al-5.17Cu-2.63Si的石墨型、砂型、保温型组织热处理后与热处理前的共晶相含量比值分别为0.44、0.49和0.68,合金Al-4.29Cu-1.09Mg的共晶相含量比值分别为0.084、0.30和0.38。
3) 在均匀化热处理温度与时间一定的情况下,原始组织越细小,粒状化效果也越好。石墨型试样的枝晶组织基本消失,得到粒状化组织;砂型试样粒状化明显,但仍保留了部分的枝晶形貌;保温型试样由于凝固组织粗大,粒状化程度最轻,而且仍然保留了大部分的枝晶形貌。
4) 在同一热处理工艺过程中,由于原始组织的尺度不同,同种非平衡第二相可处于溶解、溶断、粒化和粗化等不同的阶段。
REFERENCES
[1] 刘晓涛, 董 杰, 崔建中, 赵 刚. 高强铝合金均匀化热处理[J]. 中国有色金属学报, 2003, 13(4): 909-913.
LIU Xiao-tao, DONG Jie, CUI Jian-zhong, ZHAO Gang. Homogenizing treatment of high strength aluminium alloy cast under electric magnetic field[J]. The Chinese Journal of Nonferrous Metals, 2003, 13(4): 909-913.
[2] 刘启阳, 李庆春, 朱培钺. 共晶合金中第二相粒状化学动力学[J]. 金属科学与工艺, 1987, 1(6): 65-77.
LIU Qi-yang, LI Qing-chun, ZHU Pei-yue. Kinetics of granulation of the minor phase in eutectic alloys[J]. Metal science and technology, 1987, 1(6): 65-77.
[3] 孙 瑜, 陈 晋, 孙国雄. 铝硅合金硅相演变及其对力学性能的影响[J]. 特种铸造及有色合金, 2001, 6: 1-3.
SUN Yu, CHEN Jin, SUN Guo-xiong. Microstructural evolution of Si phase in Al-Si alloy and the influence on the mechanical properties[J]. Special Casting and Nonferrous Alloys, 2001, 6: 1-3.
[4] SINGH S N, BARDES B P, FLEMINGS M C. Solution treatment of cast Al-4.5 pct Cu alloy[J]. Metal Trans A, 1970, 1: 1383-1970.
[5] WU Z W, CHEN Y, MENG L. Microstructure and properties of Cu-Fe microcomposites with prior homogenizing treatments[J]. Journal of Alloys and Compounds, 2009, 481: 236-240.
[6] 李庆林, 兰晔峰, 王富寿, 魏珉孔. 热扩散处理对Al-24%Si合金中初晶硅形态的影响[J]. 材料热处理学报, 2010, 31(12): 29-32.
LI Qing-lin, LAN Ye-feng, WANG Fu-shou, WEI Min-kong. Influence of heat treatment on primary silicon morphology in Al-24%Si hypereutectic alloy[J]. Transactions of Materials and Heat Treatment, 2010, 31(12): 29-32.
[7] XIAO Y L, QING L P, XI F, YUN B H, WEN B L, WEN J L. Microstructural evolution of Al-Cu-Mg-Ag alloy during homogenization[J]. Journal of Alloys and Compounds, 2009, 484: 790-794.
[8] 宋佩维, 郭学锋, 井晓天, 张忠明, 徐春杰. Mg-4Al-2Si 合金固溶处理过程中Mg2Si相颗粒的球状化[J]. 材料工程, 2007, 3: 34-37.
SONG Pei-wei, GUO Xue-feng, JING Xiao-tian, ZHANG Zhong-ming, XU Chun-jie. Spheroidization of Mg2Si particles in Mg-4Al-2Si alloys during solution treatment process[J]. Materials Engineering, 2007, 3: 34-37.
[9] 李成侣, 潘清林, 刘晓艳, 何运斌, 李文斌. 2124铝合金的均匀化热处理[J]. 中国有色金属学报, 2010, 20(2): 209-216.
LI Cheng-lü, PAN Qing-lin, LIU Xiao-yan, HE Yun-bin, LI Wen-bin. Homogenizing heat treatment of 2124 aluminum alloy[J]. The Chinese Journal of Nonferrous Metals, 2010, 20(2): 209-216.
[10] 李荣德, 于海朋, 古可成, 施长铎. 亚共晶铝硅铜镁铸造合金共晶硅相在固溶处理过程中形貌变化的定量金相分析[J]. 铸造, 1997, 6: 5-9.
LI Rong-de, YU Hai-peng, GU Ke-cheng, SHI Chang-duo. Quantitative metallographic analysis for morphology change of eutectic silicon in Al-Si-Cu-Mg hypoeutectic casting alloy during the solution heat treatment[J]. Foundry, 1997, 6: 5-9.
[11] YAN X, CHEN S, XIE F, CHANG Y A. Computational and experimental investigation of microsegregation in a Al-Rich Al-Cu-Mg-Si quaternary alloy[J]. Acta Mater, 2002, 50: 2199-2207.
[12] USTA M, GLICKSMAN M E, WRIGHT R N. The effect of heat treatment on Mg2Si coarsening in aluminum 6105 alloy[J]. Metall Trans A, 2009, 35: 435-438.
[13] APELIAN D, SHWKUAR S, SIGWORTH G. Fundamental aspects of heat treatment of cast Al-Si-Mg alloys[J]. AFS Transactions, 1989, 97: 727-742.
[14] MCLEAN M. Particle coarsening in a temperature gradient[J]. Scripta Mater, 1975, 9(5): 439-445.
[15] VEDULA K M, HECKEL R W. Spheroidization temperatures of binary Fe-C alloys over a range of temperatures[J]. Metall Trans A, 1970, 1: 9-18.
[16] USTA M, GLICKSMAN M E, WRIGHT R N. The effect of heat treatment on Mg2Si coarsening in aluminum 6105 alloy[J]. Metall Trans A, 2004, 35: 435-438.
(编辑 龙怀中)
基金项目:国家重点基础研究发展计划资助项目(2011CB610406);国家自然科学基金资助项目(50771041, 50801019);中南大学粉末冶金国家重点实验室开放课题(2008112042)
收稿日期:2011-03-14;修订日期:2011-08-18
通信作者:赵光伟,博士;电话:0451-86896351;E-mail: zgwhit@163.com