DOI: 10.11817/j.ysxb.1004.0609.2021-39646
电极形状对异种不等厚铝合金电阻点焊接头形貌的影响
毛镇东1,阚 盈2,韩晓辉1,陈怀宁2,李帅贞1
(1. 青岛四方机车车辆股份有限公司,青岛 266111;
2. 中国科学院金属研究所 中国科学院核用材料与安全评价重点实验室,沈阳 110016)
摘 要:为了准确预测异种不等厚铝合金电阻点焊熔核尺寸及表面形貌,本文综合考虑电阻点焊过程中电极与工件、工件与工件间接触面积的动态变化以及材料力学性能对接触电阻的影响,建立了较为完善的电阻点焊有限元模型,研究异种不等厚铝合金电阻点焊熔核形成机理以及电极圆角半径对接头形貌的影响规律。结果表明:熔核最先在焊点边缘形成,然后向中心扩展,随着焊接时间的延长,熔核截面由椭圆形向方形转变;电极圆角半径增大,点焊熔核尺寸、压痕深度和凸起高度增加。模型计算得到的熔核尺寸和焊点表面形貌与实验结果符合较好,验证了模型的有效性。
关键词:铝合金;电阻点焊;数值模拟;熔核形状;表面形貌
文章编号:1004-0609(2021)-02-0333-09 中图分类号:TG146.1 文献标志码:A
引文格式:毛镇东, 阚 盈, 韩晓辉, 等. 电极形状对异种不等厚铝合金电阻点焊接头形貌的影响[J]. 中国有色金属学报, 2021, 31(2): 333-341. DOI: 10.11817/j.ysxb.1004.0609.2021-37713
MAO Zhen-dong, KAN Ying, HAN Xiao-hui, et al. Influence of electrode shape on resistance spot welding joint morphology of dissimilar unequal thickness aluminum alloys[J]. The Chinese Journal of Nonferrous Metals, 2021, 31(2): 333-341. DOI: 10.11817/j.ysxb.1004.0609.2021-37713
铝合金因具有密度小、比强度高等优点而被广发应用于航空航天、汽车制造、轨道交通等领域[1]。电极形状是影响铝合金电阻点焊熔核质量的关键因素之一[2]。目前,国内外有许多关于电极形状对焊点质量影响的研究[3-5]。ZHANG等[6]研究了电极磨损对DP600钢点焊熔核尺寸的影响,发现随着球面电极的磨损,熔核尺寸减小。TUCHTFELD等[7]研究发现,当电极端面直径相同时,电极锥角增大熔核尺寸减小。然而这些研究大多集中在球面电极和锥形电极中,对平面电极研究较少。平面电极的优点是在保证熔核尺寸的同时可以获得较浅的压痕深度,但由于铝合金导热和导电性良好,通常使用大电流、短时间、高压力的“硬规范”进行电阻点焊,加速了电极的磨损和粘连,导致点焊电极端面圆角半径增大,进而影响熔核大小和焊点表面质量。
在高铁车体铝合金点焊的实际应用中,考虑到结构强度和轻量化等因素,需要对异种不等厚铝合金进行电阻点焊连接。目前,对异种不等厚铝合金电阻点焊工艺的研究主要采用实验的方法,然而铝合金的厚度、种类和热处理状态等都会对点焊熔核质量产生影响。每一种厚度和种类组合的铝合金电阻点焊工艺都需要反复实验,工艺优化周期长。此外,铝合金电阻点焊的瞬时性给点焊熔核形成机理的研究带来很大困难。数值模拟可以弥补实验研究的不足,近年来许多学者利用数值模拟技术对电阻点焊过程进行了研究[8-11],但目前少有采用有限元法研究电极形状对异种不等厚铝合金点焊质量影响的报道。
本文综合考虑电阻点焊过程中电极与工件、工件与工件间接触面积的动态变化以及材料力学性能对接触电阻的影响,建立了较为准确的异种不等厚铝合金电阻点焊有限元模型。通过数值模拟研究异种不等厚铝合金点焊熔核形成机理及平面电极端面圆角半径对熔核尺寸及表面形貌的影响规律,为控制异种不等厚铝合金电阻点焊质量提供理论依据。
1 有限元模型
本文建立的电阻点焊有限元模型如图1所示,为二维轴对称模型。上、下电极尺寸相同,直径为19 mm,电极端面的倒圆角半径R为1~4 mm。待焊工件为6 mm厚5083和4 mm厚7N01铝合金板材。模型中待焊工件的半径为25 mm。通过在电极-工件、工件-工件界面上设置接触对的方法模拟界面的接触行为。
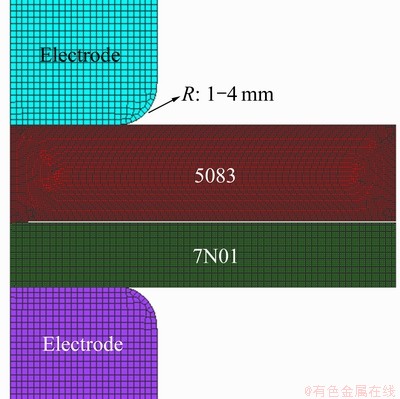
图1 电阻点焊有限元模型
Fig. 1 Resistance spot welding simulation model
采用Bay-Wanheim[12]模型计算界面间的接触电阻率
,该模型形式如下:
(1)
式中:
接触界面上较软材料的流动应力;
是界面法向上的压力;
、
分别是接触面上两材料的电阻率;
是界面涂层、污染物等的电阻率。利用Bay-Wanheim模型可综合考虑材料流动应力、接触压力和界面污染物对接触电阻的影响,为准确计算异种铝合金的接触电阻提供基础。
网格尺寸对模拟结果有重要影响,综合考虑模拟准确性和计算效率,对上下板接触处的网格进行局部细化,最小网格边长为0.05 mm,其余部分的网格边长为0.3 mm。模拟中采用的工艺参数为:焊接电流47 kA,时间25 ms,电极压力18 kN,与实际焊接工艺参数一致。
计算中使用的电极和待焊母材的热物性和力学性能参数见图2[7, 13]。7N01和5083铝合金的室温应力应变曲线如图3所示,高温下7N01和5083铝合金的的流动应力
和
分别用式(2)和式(3)计算[14-15]:
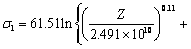
(2)
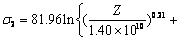
(3)
其中,
(4)
式中:
为应变速率;T为温度;R为摩尔气体常数;Q为变形激活能,7N01和5083铝合金的Q分别为152和164 kJ/mol。
2 模拟结果与分析
2.1 异种不等厚铝合金电阻点焊熔核形成机理
图4所示为电极圆角半径2 mm时不同焊接时间下焊点温度分布云图。从图4可以看到,点焊熔核最先在工件-工件接触界面的边缘形成,然后沿界面向焊点中心扩展,进一步延长通电时间后,熔核截面由近似椭圆形向方形转变,如图4(d)所示。最终得到的熔核与实验得到的熔核形态及尺寸一致(见图4(e)),证明了有限元模型的有效性。
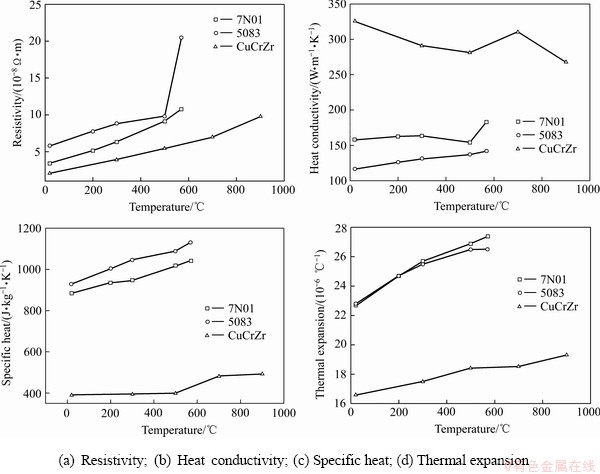
图2 电极和待焊母材的热物性能和力学性能参数
Fig. 2 Thermo-physical and mechanical properties of electrode and base metals
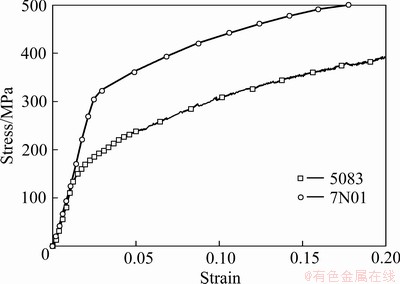
图3 7N01和5083铝合金室温应力-应变曲线
Fig. 3 Stress-strain curves of 5083 and 7N01 at 20 ℃
图5所示为不同焊接时间下工件-工件界面上的压力分布曲线。可以看到,在点焊过程中,界面中心的接触压力始终大于界面边缘的接触压力。根据公式(1)可知,接触电阻率与接触压力成反比,因此点焊熔核易于在接触压力较小的接触边缘形成。图6所示为点焊过程中电极-工件、工件-工件间接触半径随时间变化曲线。可以看到,焊接过程中工件-工件间的接触半径呈增大趋势,电极-工件间的接触半径先减小后增大。这是由于电极下方材料加热后体积膨胀,使待焊工件表面向外弓出,工件表面与电极接触半径减小,随着焊接时间增长,材料温度升高,流动应力下降,在电极压力作用下,工件发生变形,因此电极与工件接触半径增大。进一步观察图6和图4(c)可以发现,电极-工件接触半径产生拐点时,对应着熔核形态由近似椭圆形向方形转变的开始,随着电极-工件接触半径由减小转为增大,熔核上部和下部沿平行于板材的方向扩展,形成截面近似为方形的熔核。
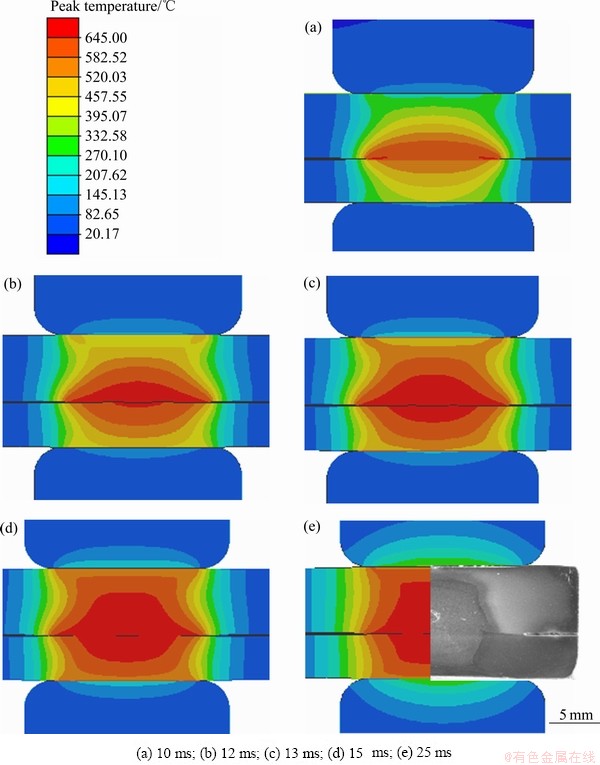
图4 电极圆角半径为2 mm时不同焊接时间下的温度场
Fig. 4 Temperature distribution at different time with electrode fillet radius of 2 mm
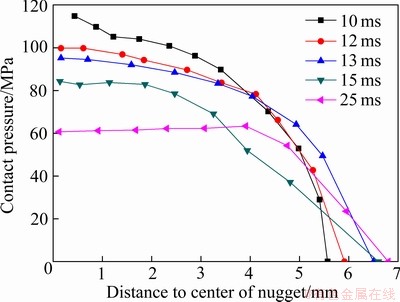
图5 不同焊接时间下工件-工件界面接触压力
Fig. 5 Contact pressure between workpieces with time
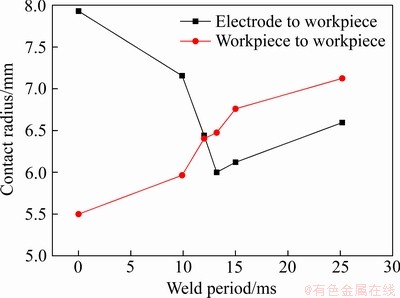
图6 界面接触半径随时间变化曲线
Fig. 6 Change of contact radius of interfaces with time
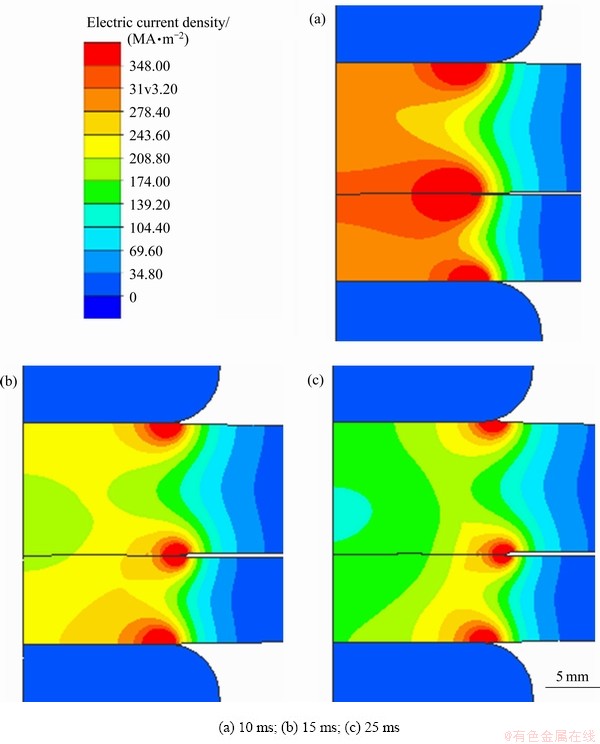
图7 不同时间下工件中电流密度
Fig. 7 Change of current density in workpiece with time
以下结合点焊过程中电流密度分布分析电极-工件接触半径对熔核形状影响的机理(见图7)。如图7所示,随着焊接时间增长,工件中整体电流密度呈下降趋势,电流密度最大处一直位于电极-工件界面边缘和工件-工件界面边缘。一方面,点焊过程中,工件-工件界面接触电阻和电流密度逐渐降低,焊点中心产热减少,熔宽扩展缓慢;另一方面,电极-工件接触半径逐渐增大导致焊点上下表面最大电流密度向边缘移动,促进熔核由椭圆向方形截面转变。
2.2 电极圆角半径对熔核尺寸及表面形貌的影响
图8所示为点焊接头形状参数定义示意图,其中上板熔宽、下板熔宽和熔深为熔核尺寸参数,凸起高度和压痕深度为接头表面形貌参数。在点焊过程中,平面电极会发生磨损,导致端面圆角增大。参考实际电极的磨损情况,本文模拟了端面圆角半径R为1~4 mm时点焊接头形状参数变化,结果如图9和10所示。可以看到,随着电极圆角半径增大,熔核尺寸、压痕深度和凸起高度增大,当压头圆角半径为4 mm时,点焊接头表面凸起高度显著增加。
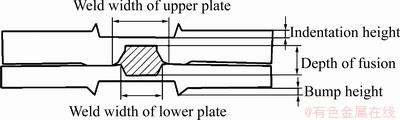
图8 点焊接头形状参数示意图
Fig. 8 Schematic diagram of shape parameters of joint
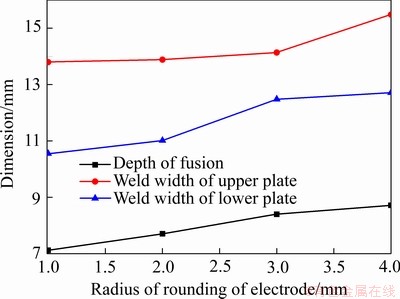
图9 不同电极圆角半径时的熔核尺寸
Fig. 9 Size of nugget under different corner radiuses
图11所示为使用R4电极点焊过程中等效塑性应变分布云图,借此可以深入分析点焊接头表面凸起高度显著增加的原因。由图11可以看到,点焊过程中变形首先出现在工件-工件界面处,其等效塑性应变的最大值位于界面边缘。随着点焊进行,在通电7 ms时与电极圆角处接触的工件开始发生塑性变形,延长通电时间,工件表面材料的塑性变形进一步增大,在电极周围堆积形成凸起。
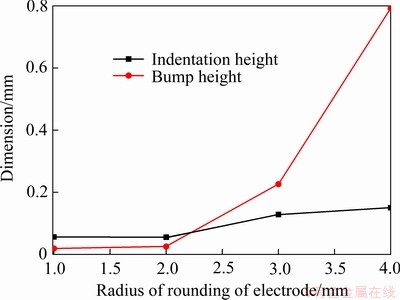
图10 不同电极圆角半径时的压痕深度和凸起高度
Fig. 10 Indentation depth and pile-up height under different corner radiuses
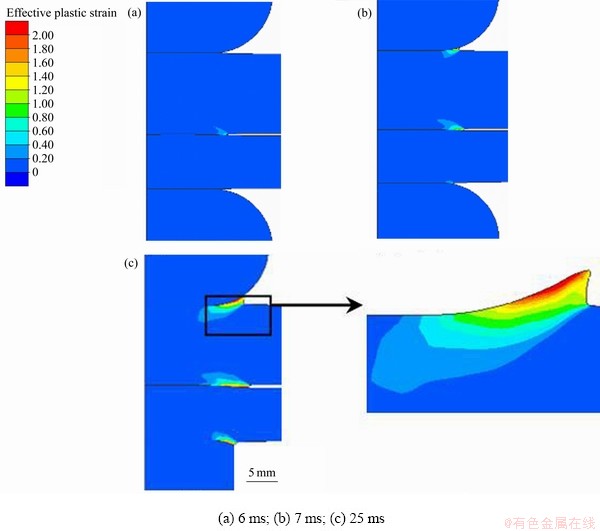
图11 半径4 mm圆角电极点焊过程中母材等效应变分布云图
Fig. 11 Effective plastic strain distribution along time for base metal during resistance spot welding using R4 mm electrode
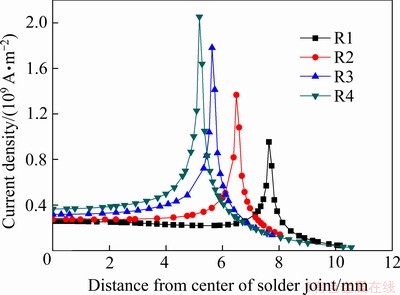
图12 7 ms时不同圆角半径下工件表面电流密度
Fig. 12 Current density on surface under different corner radiuses at 7 ms
图12和13所示分别为通电7 ms时工件表面电流密度分布和温度分布图。从图12可以看到,随着电极圆角半径增大,工件表面的电流密度最大值升高,因此较大圆角半径的电极对应的工件表面温度较高,如图13所示,电极半径为4mm时,表面形成了呈环状分布的600℃高温带,该温度下铝合金的流动应力很低[13],在电极压力作用下该环状带容易发生塑性变形,从而在材料表面形成堆积。图14是采用R2和R4电极点焊后焊点的表面形貌宏观照片,可以看到R2电极焊点表面无凸起,而R4电极焊点表面凸起明显,与如图4(e)和图11(c)所示的模拟结果基本一致,图14(b)中的凸起高度不均匀,这主要是由于实际点焊过程中电极及工件位置不能完全对称,而高温下材料变形抗力较小,因此在不均匀的受力状态下材料容易向一侧堆积。
3 结论
1) 建立了异种不等厚铝合金电阻点焊的电- 热-力耦合的有限元模型,实现了异种不等厚铝合金电阻点焊熔核尺寸和表面形貌的准确预测。
2) 异种不等厚铝合金点焊熔核形成规律为:熔核最先在工件-工件接触边缘形成,然后向焊点中心扩展,随着焊接时间增加,熔核截面由椭圆形向方形转变。
3) 点焊熔核尺寸、压痕深度和凸起高度随电极圆角半径增大而增大。
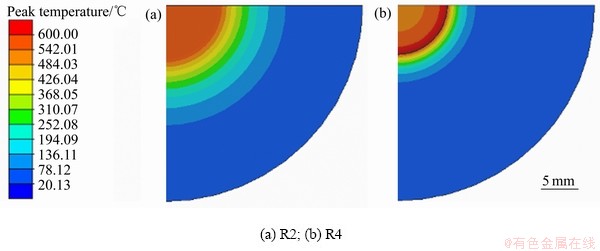
图13 7 ms时不同圆角半径下工件表面温度
Fig. 13 Temperature distribution on surface under different corner radiuses at 7 ms
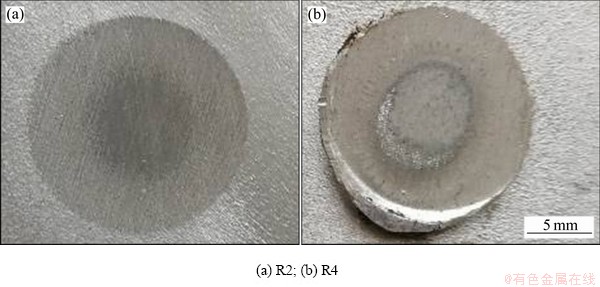
图14 不同电极圆角半径时焊点表面形貌
Fig. 14 Surface morphologies under different corner radiuses at 7 ms
REFERENCES
[1] 邓运来, 张新明. 铝及铝合金材料进展[J]. 中国有色金属学报, 2019, 29(9): 2115-2141.
DENG Yun-lai, ZHANG Xin-ming. Development of aluminium and aluminium alloy[J]. The Chinese Journal of Nonferrous Metals, 2019, 29(9): 2115-2141.
[2] WEI P S, WU T H. Numerical study of electrode geometry effects on resistance spot welding[J]. Science and Technology of Welding and Joining, 2013, 18(8): 661-670.
[3] 张 敏, 孔 谅, 王 敏. 电极形状对AA5182铝合金电阻点焊性能的影响[J]. 焊接学报, 2018, 39(4): 84-88.
ZHANG Min, KONG Liang, WANG Min. Study of electrode tip morphology on the performance in resistance spot welding of AA5182 aluminum alloy[J]. Transactions of the China Welding Institution, 2018, 39(4): 84-88.
[4] WANG B, HUA L, WANG X, et al. Effects of electrode tip morphology on resistance spot welding quality of DP590 dual-phase steel[J]. The International Journal of Advanced Manufacturing Technology, 2016, 83(9): 1917-1926.
[5] 孙大千, 张月莹, 苏 雷, 等. 电极形状对铝-钢点焊接头组织及力学性能的影响[J]. 机械工程学报, 2016, 52(24): 36-43.
SUN Da-qian, ZHANG Min, SU Lei, et al. Effects of electrode morphology on microstructures and mechanical properties of spot welded Al-steel joints[J]. Journal of Mechanical Engineering, 2016, 52(24): 36-43.
[6] ZHANG X Q, CHEN G L, ZHANG Y S. Characteristics of electrode wear in resistance spot welding dual-phase steels[J]. Materials & Design, 2008, 29(1): 279-283.
[7] TUCHTFELD M, HEILMANN S, FüSSEL U, et al. Comparing the effect of electrode geometry on resistance spot welding of aluminum alloys between experimental results and numerical simulation[J]. Welding in the World, 2019, 63(2): 527-540.
[8] HAMEDI M, ATASHPARVA M. A review of electrical contact resistance modeling in resistance spot welding[J]. Welding in the World, 2017, 61(2): 269-290.
[9] MANLADAN S M, YUSOF F, RAMESH S, et al. A review on resistance spot welding of aluminum alloys[J]. The International Journal of Advanced Manufacturing Technology, 2017, 90(1): 605-634.
[10] WAN Z, WANG H, WANG M, et al. Numerical simulation of resistance spot welding of Al to zinc-coated steel with improved representation of contact interactions[J]. International Journal of Heat and Mass Transfer, 2016, 101: 749-763.
[11] 张 禹, 毕 敬, 罗 震, 等. 异种不等厚铝合金电阻点焊分流的数值模拟[J]. 焊接学报, 2017, 38(10): 61-65.
ZHANG Yu, BI Jing, LUO Zhen, et al. numerical simulation of shunting in resistance spot welding for dissimilar unequal-thickness aluminum alloys[J]. Transactions of the China Welding Institution, 2017, 38(10): 61-65.
[12] BAY N, WANHEIM T. Real area of contact and friction stress at high pressure sliding contact[J]. Wear, 1976, 38(2): 201-209.
[13] WANG J, WANG H, LU F, et al. Analysis of Al-steel resistance spot welding process by developing a fully coupled multi-physics simulation model[J]. International Journal of Heat and Mass Transfer, 2015, 89: 1061-1072.
[14] 刘君城, 金龙兵, 何振波, 等. 7N01铝合金热压缩流变行为研究[J]. 稀有金属, 2011, 35(6): 812-817.
LIU Jun-cheng, JIN Long-bing, HE zhen-bo, et al. Hot deformation behavior of 7N01 aluminum alloy[J]. Chinese Journal of Rare Metals, 2011, 35(06): 812-817.
[15] 高文理, 关宇飞. 5083铝合金热压缩应力-应变曲线修正与热加工图[J]. 中国有色金属学报, 2018, 28(9): 1737-1745.
GAO Wen-li, GUAN Yu-fei. Correction of flow stress-strain curve and processing maps of 5083 aluminum alloy during hot compression[J]. The Chinese Journal of Nonferrous Metals, 2018, 28(9): 1737-1745.
Influence of electrode shape on resistance spot welding joint morphology of dissimilar unequal thickness aluminum alloys
MAO Zhen-dong1, KAN Ying2, HAN Xiao-hui1, CHEN Huai-ning2, LI Shuai-zhen1
(1. CRRC Qingdao Sifang Co., Ltd., Qingdao 266111, China;
2. CAS Key Laboratory of Nuclear Materials and Safety Assessment, Institute of Metal Research, Chinese Academy of Sciences, Shenyang 110016, China)
Abstract: In order to accurately predict the nugget size and surface morphology of the resistance spot welded dissimilar unequal thickness aluminum alloy joint, a finite element model was established. The dynamic contact between the electrode and the workpieces and the influence of mechanical behavior of the workpieces on the contact resistivity were considered in the model. The nugget formation mechanism of the aluminum alloy during resistance spot welding and the influence of corner radius of the electrode on the joint were analyzed. The calculated results show that the initial nugget forms at the edge of the weld point, then propagates to the center. With the welding time increasing, the cross section of the nugget changes from generally elliptical to square. Besides, the nugget size, the indentation depth and pile-up height increase with the corner radius of the electrode increasing. The effectiveness of the numerical model was verified by comparing the calculated result with experimental result.
Key words: aluminum alloy; resistance spot welding; numerical simulation; nugget shape; surface morphology
Received date: 2020-01-10; Accepted date: 2020-05-20
Corresponding author: KAN Ying; Tel: +86-24-23971932;E-mail: ykan@imr.ac.cn
(编辑 龙怀中)
收稿日期:2020-01-10;修订日期:2020-05-20
通信作者:阚 盈,副研究员,博士;电话:024-23971932;E-mail:ykan@imr.ac.cn