Trans. Nonferrous Met. Soc. China 24(2014) 1289-1294
Refinement and consolidation of pure Al particles by equal channel angular pressing and torsion
Ping LI, Ke-min XUE, Xiao-xi WANG, Chen-hao QIAN
School of Materials Science and Engineering, Hefei University of Technology, Hefei 230009, China
Received 8 May 2013; accepted 3 September 2013
Abstract: Consolidation of pure Al powder was conducted at 200 °C by equal channel angular pressing and torsion (ECAPT) method. The grain refinement and consolidation behavior were deeply investigated by scan electronic microscopy (SEM) and transmission electronic microscopy (TEM). The density, hardness and room temperature compression properties of the deformed samples were measured. The experiment results show that ECAPT is an effective method of consolidating powders at relatively low temperatures. Pure Al particles are successfully consolidated into dense bulk material after 4 passes of ECAPT at 200 °C. The consolidated material possesses fine grain structure and excellent mechanical properties. The refinement and consolidation mechanisms were analyzed. ECAPT is a promising method to produce the high-performance bulk materials from particles.
Key words: refinement; consolidation; equal channel angular pressing and torsion; Al powder
1 Introduction
The mechanical properties of powder materials can be improved qualitatively when the density increases to a theoretical value. Otherwise, excellent physical and mechanical properties are obtained when the grains are refined to submicron level. The traditional methods of powder metallurgy and plastic forming are difficult to obtain high density and ultra-fine grains [1,2]. Therefore, it is desirable to develop new favorable processes to synthesize bulk materials with high density and fine grains at relatively low temperatures. XIA and WU [3] consolidated pure Al particles at 100 °C by back pressure equal channel angular consolidation (BP–ECAC). PAYDAR et al [4] consolidated pure Al particles at 200 °C by equal channel angular pressing-forward extrusion (ECAP–FE). But repetitive deformations are not permitted using ECAP–FE, and higher load is required.
Equal channel angular pressing and torsion (ECAPT) is a novel severe plastic deformation (SPD) technique which improves the conventional equal channel angular pressing (ECAP) by manufacturing a twist channel in horizontal stage of ECAP [5]. ECAPT process is shown in Fig. 1. Compared to conventional ECAP [6], ECAPT has some superior characteristics. During ECAPT process, the sample experiences two severe shear deformations of ECAP and twist extrusion (TE) [7,8] in a single tool. At the same time, high hydrostatic pressure is obtained because of the back pressure exerted by the twist channel. So, good contact between particles is realized, which improves the deformation and densification of powder. Otherwise, the sample still maintains the same cross-sectional area so that repetitive deformations are permitted, which leads to higher total strains and better refinement and consolidation [9,10]. So, it is expected that consolidation of powder can be realized by ECAPT process at relatively low temperature.
The aim of this study is to investigate the effects of ECAPT on refinement and consolidation of pure Al powder. It has a great significance to science and technology of particle consolidation and supplies essential foundation for fabricating bulk materials from particles with SPD.
2 Experimental
The pure Al powders with chemical compositions of Fe (<0.6%, mass fraction), Cu (<0.05%), Si (<0.3%) were prepared. The particle size distribution was determined using a laser diffraction analyzer. The mean size of powder particles was 40.6 mm. Figure 2 shows SEM image of the Al particles.
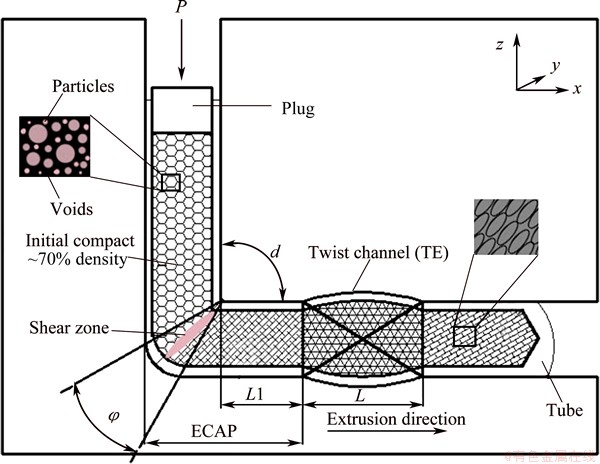
Fig. 1 Schematic diagram of ECAPT process
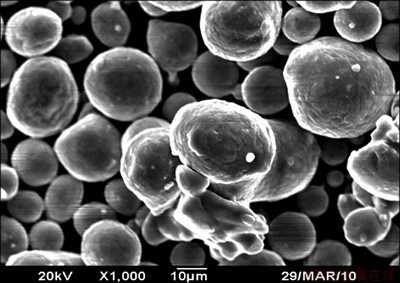
Fig. 2 SEM image of Al particles
ECAPT experiments were carried out using a RZU2000HF pressing and torsion machine. The die consisted of two orthogonal channels which had equal cross section with dimensions of 10 mm×10 mm. The length of twist channel was 30 mm and the cross- sectional rotation angle was 90°. The pure Al powder with initial relative density of 0.75 was wrapped in a pure Al tube (10 mm×10 mm×50 mm) and inserted into the entrance channel with graphite lubricant applied. Then a plunger was placed on it. Four passes of ECAPT were carried out through processing route A (no rotation of the specimen between consecutive passes) at 200 °C. The ram velocity was 1 mm/s.
The cross section vertical to pressing direction of the sample was used for microstructure observation. Electron backscatter diffraction (EBSD) measurement was performed using a JSM-7001F scanning electron microscope. JEM-2100F transmission electron microscope was used for microstructure characterization.
The density of the consolidated sample was measured based on the Archimedes principle. The Vickers hardness (HV) was measured using 0.49 N load for 10 s on the cross section of the sample. Compression tests were performed for the consolidated specimen with dimensions of d5 mm×7 mm with a MTS809 machine at room temperature and a constant strain rate of 10-3 s-1.
3 Results and discussion
3.1 Microstructure analyses
Microstructures of the samples after different passes of ECAPT, obtained by EBSD, are shown in Figs. 3 and 4, respectively.
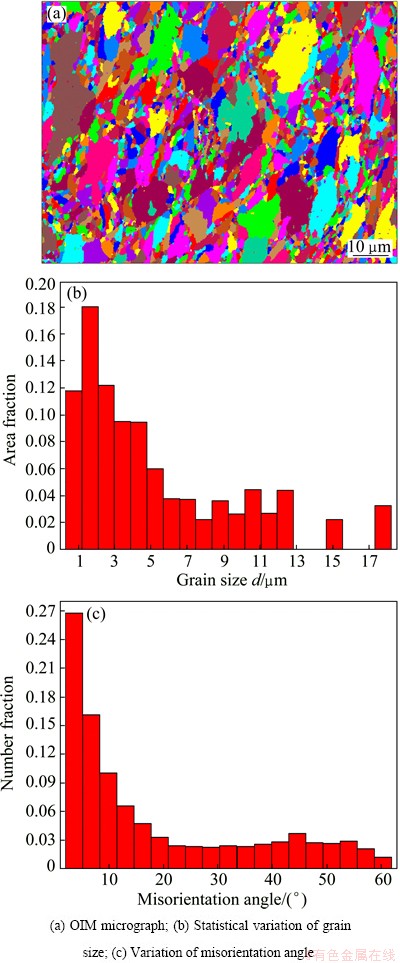
Fig. 3 Microstructure and variation of sample after 1 pass of ECAPT
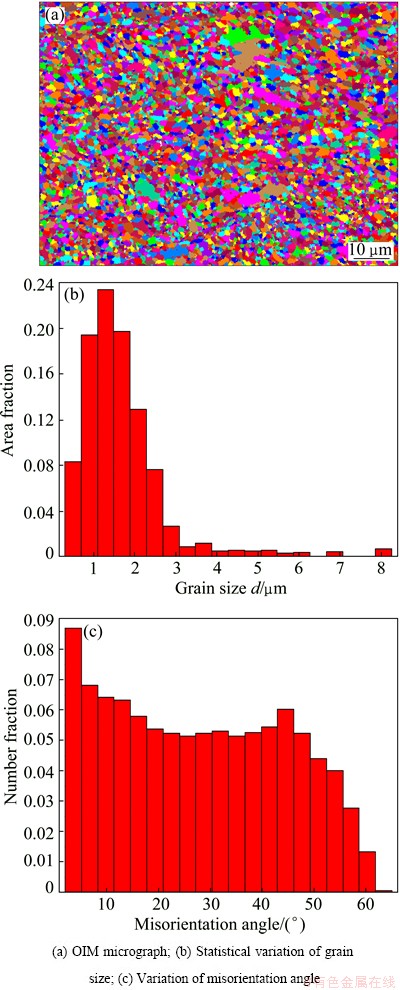
Fig. 4 Microstructure and variation of sample after 4 passes of ECAPT
After 1 pass of ECAPT, majority of the pores are closed under high hydrostatic stress and large shear deformation. Otherwise, the retained pores are changed from sphere to ellipse, which is beneficial for pore closure in the following deformation [11-13]. The grains are elongated along the shear deformation direction and refined greatly. But the grain size distribution is non- uniform. The statistical variation of grain size shows that the average size is about 5.2 mm and 12% of the scanned area has grains less than 1 mm in size. Majority of the substructure boundaries in the grain interior are low-angled. The histogram for the misorientation angle shows that the average misorientation angle is 18°, and 41% of the boundaries have misorientation angles higher than 16°.
After 4 passes of ECAPT, the pores are basically closed. More ultrafine grains with high-angle grain boundaries appear and the microstructure is more homogeneous. The average grain size is 1.7 mm and 27% of the scanned area has grains less than 1 mm in size. The grain boundaries with high-angle increases. The histogram for the misorientation angle shows that the average misorientation angle is 28°, and 72% of the boundaries have misorientation angles higher than 16°.
TEM images of the specimens after different passes of ECAPT are shown in Fig. 5. After 1 pass of ECAPT, deformation bands are observed and high-density dislocations occur. A few subgrains with low misorientations and size less than 1 mm appear between the banded grains. The microstructure is inhomogeneous. Majority of the subgrain boundaries formed in the grain interior are low-angled.
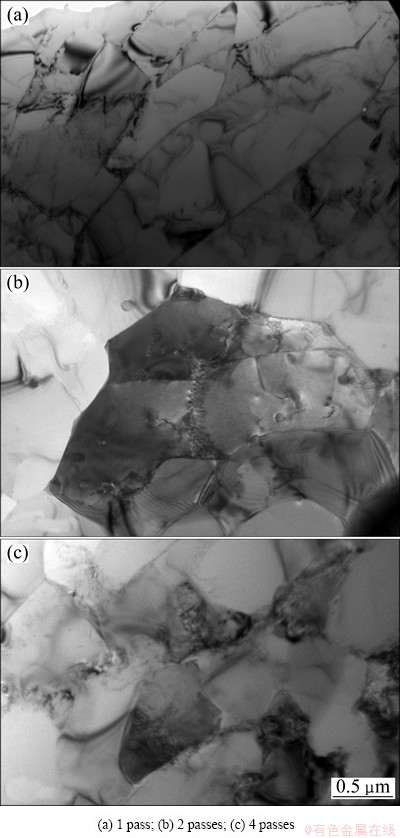
Fig. 5 TEM images of specimens after different passes of ECAPT
After 2 passes of ECAPT, the refined grains gradually transform into equiaxed ones, and contain relatively low-density dislocations in their interiors. A large number of dislocations stack around grain boundaries, which leads to low-angle subgrains formation [14].
After 4 passes of ECAPT, the sample experiences severe plastic deformation and lattice dislocations are accumulated. The subgrain boundaries gradually evolve into high angle grain boundaries through dislocation absorption. Therefore, near equiaxed ultrafine grains separated by straight high-angle grain boundaries are formed. The grains are refined greatly.
3.2 Density and hardness
The relative density increases from 0.75 to 0.95 after 1 pass of ECAPT. The Vickers hardness is 43.1. That is, significant hardening occurs due to the relatively fine microstructure and high-density dislocation substructures of the material after 1 pass of ECAPT. With the increasing of ECAPT passes, shear deformation increases continually, which is beneficial to powder densification. Otherwise, ultrafine grains with high angle grain boundaries are formed, which increases strength of the material. Therefore, after 4 passes of ECAPT, the relative density of the sample increases to 0.997, and the Vickers hardness reaches 48.5. Thus, pure Al particles are successfully consolidated into fully dense bulk material by ECAPT at 200 °C.
3.3 Compression properties
The compression true stress–strain curves of the samples after different passes of ECAPT are plotted in Fig. 6. It is noticed that the sample after 4 passes ECAPT exhibits higher-strain hardening at the early stage of compression deformation. The room temperature compression strength exhibits a marked increase. The yield strength of the sample after 1 pass ECAPT is 43.8 MPa, which increases to 87.3 MPa after 4 passes. And the ultimate strength increases from 53.6 MPa to 123.3 MPa. The refined microstructure free from pores and high boundary misorientation angles can account for the higher strain hardening and compression strength of the sample after 4 passes of ECAPT.
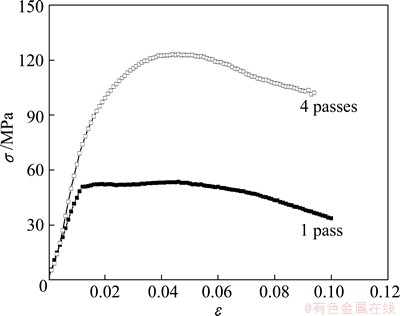
Fig. 6 Compression true stress-true strain curves of samples after ECAPT at room temperature
SEM images of the typical fracture morphologies of the samples after different passes of ECAPT are shown in Fig. 7. After 1 pass of ECAPT, the fracture surface is uneven and lamellar distribution is obvious, which result from the decohesion between adjacent particles due to incomplete densification of the material. There are many pores among particles. The cracks originate from the pores and propagate along the particle interfaces [15]. After 4 passes of ECAPT, the fracture surface is smooth, which is typical character of cleavage fracture. Shear slip and tiny dimples characterized by tough fracture are observed. It shows that particle consolidation can be achieved.
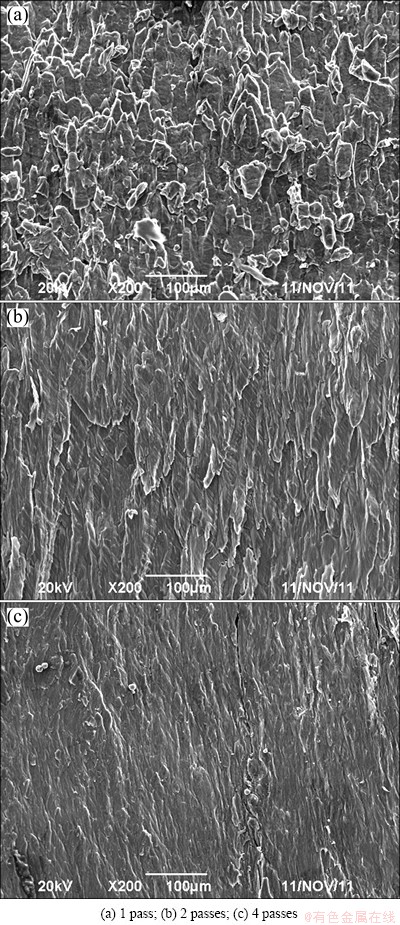
Fig. 7 SEM images of fracture surfaces after different passes of ECAPT
Table 1 lists the mechanical properties of the samples after 4 passes of ECAPT. For comparison, the results of the ingot sample annealed at 200 °C for 3 h and sintered sample pressed and vacuum sintered at 400 °C for 4 h are also presented in Table 1. The results show that the mechanical properties of the bulk sample produced by ECAPT are remarkably higher than those of the ingot or sinter sample.
Table 1 Mechanical properties of ingot, sinter and ECAPT samples
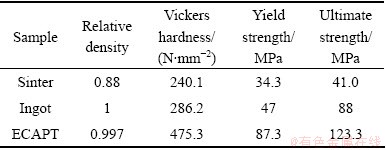
These studies show that the position, shape and size of initial Al particles are continually changed during ECAPT. Hydrostatic stress and shear strain induce pore closure and good contact among particles, break oxide films around particle surfaces, refine grains and produce a lot of fresh and clean surfaces [16]. Otherwise, the back pressure exerted by TE channel promotes the self-diffusion of particles at the interface and decreases the activity energy. These conditions are favorable to particle consolidation. Therefore, it can be concluded that ECAPT is an effective method of metallic powder consolidation at lower temperatures than that used in conventional powder metallurgy. The grains are refined greatly and the material is considerably strengthened.
4 Conclusions
1) A novel technique of equal channel angular pressing and torsion (ECAPT) was proposed to consolidate Al powder at 200 °C. Al particles were successfully consolidated into fully dense bulk material with excellent bonding between the particles under the high hydrostatic stress and large shear strain of ECAPT.
2) The grains were refined greatly, and near equiaxed ultrafine grains with straight high-angle grain boundaries were obtained. The mechanical properties of the consolidated material were improved. ECAPT was a promising process for producing high-performance bulk materials from metallic powders.
References
[1] VALIEV R Z, LANGDON T G. Principles of equal-channel angular pressing as a processing tool for grain refinement [J]. Progress in Materials Science, 2006, 51: 881-981.
[2] SENKOV O N, SENKOVA S V, SCOTT J M, MIRACLE D B. Compaction of amorphous aluminum alloy powder by direct extrusion and equal channel angular extrusion [J]. Materials Science and Engineering A, 2005, 393: 12-21.
[3] XIA K, WU X. Back pressure equal channel angular consolidation of pure Al particles [J]. Scripta Materialia, 2005, 53: 1225-1229.
[4] PAYDAR M H, REIHANIAN M, BAGHERPOUR E, SHARIFZADEH M, ZARINEJAD M, DEAN T A. Equal channel angular pressing–forward extrusion (ECAP–FE) consolidation of Al particles [J]. Materials and Design, 2009, 30: 429-432.
[5] WANG X X, XUE K M, LI P, WU Z L, LI Q. Equal channel angular pressing and torsion of pure Al powder in tubes [J]. Advanced Materials Research, 2010, 97-101: 1109-1115.
[6] XU Shu-bo, QIN Zhen, LIU Ting, JING Cai-nian, REN Guo-cheng. Effect of severe plastic deformation on microstructure and mechanical properties of bulk AZ31 magnesium alloy [J]. Transactions of Nonferrous Metals Society of China, 2012, 22(S1): s61-s67.
[7] WANG Cheng, LI Ping, XUE Ke-min, LI Xiao, ZHANG Kai. Numerical simulation and experimental research on pure copper by twist extrusion [J]. The Chinese Journal of Nonferrous Metals, 2011, 21: 3071-3075. (in Chinese)
[8] ORLOV D, BEYGELZIMER Y, SYNKOV S, VARYUKHIN V, TSUJI N, HORITA Z. Microstructure evolution in pure Al processed with twist extrusion [J]. Materials Transactions, 2009, 50: 96-100.
[9] EL-DANAF E A, SOLIMAN M S, ALMAJID A A, EL-RAYES M M. Enhancement of mechanical properties and grain size refinement of commercial purity aluminum 1050 processed by ECAP [J]. Materials Science and Engineering A, 2007, 458: 226-234.
[10] KARAMAN I, HAOUAOUI M, MAIER H J. Nanoparticle consolidation using equal channel angular extrusion at room temperature [J]. Journal of Materials Science, 2007, 42: 1561-1576.
[11] LI Ping, XUE Ke-min, ZHOU Ming-zhi. Microstructure and properties evolution and mechanism analysis of sintered powder aluminum powder during equal channel angular pressing [J]. Chinese Journal of Materials Research, 2009, 23: 577-581. (in Chinese)
[12] XIA K, WU X, HONMA T, RINGER S P. Ultrafine pure aluminium through back pressure equal channel angular consolidation (BP-ECAC) of particles [J]. Journal of Materials Science, 2007, 42: 1551-1560.
[13] LAPOVOK R, TOMUS D, MUDDLE B C. Low-temperature compaction of Ti-6Al-4V powder using equal channel angular extrusion with back pressure [J]. Materials Science and Engineering A, 2008, 490: 171-180.
[14] MAZURINA I, SAKAI T, MIURA H, SITDIKOV O, KAIBYSHEV R. Grain refinement in aluminum alloy 2219 during ECAP at 250 °C [J]. Materials Science and Engineering A, 2008, 473: 297-305.
[15] ZHANG L C, XU J, MA E. Consolidation and properties of ball-milled Ti50Cu18Ni22Al4Sn6 glassy alloy by equal channel angular extrusion [J]. Materials Science and Engineering A, 2006, 434: 280-288.
[16] CHANG S Y, LEE K S, CHOI S H, SHIN D H. Effect of ECAP on microstructure and mechanical properties of a commercial 6061Al alloy produced by powder metallurgy [J]. Journal of Alloys and Compounds, 2003, 354: 216-220.
纯铝颗粒等径角挤扭中的细化和固结
李 萍,薛克敏,王晓溪,钱陈豪
合肥工业大学 材料科学与工程学院,合肥 230009
摘 要:采用等径角挤扭新工艺(ECAPT)在200 °C条件下实现纯铝粉末颗粒的固结。采用扫描电子显微镜(SEM)和透射电子显微镜(TEM)深入研究粉末细化和固结行为,并对变形后试样的密度、硬度和室温压缩性能等进行测试。结果表明:等径角挤扭工艺是实现在相对较低的温度下粉末固结的有效方法。在200 °C下经4道次变形后,成功将纯Al颗粒固结为致密的块体材料,固结后的材料具有较细的晶粒结构和良好的力学性能。深入分析了晶粒细化和固结机理。等径角挤扭工艺是具有良好前景的以粉末为原材料制备高性能块体材料的工艺。
关键词:细化;固结;等径角挤扭;铝粉
(Edited by Chao WANG)
Foundation item: Project (50875072) supported by the National Natural Science Foundation of China; Project (121053) supported by Fok Ying Tong Education Foundation; Project (20100111110003) supported by Specialized Research Fund for the Doctoral Program of Higher Education, China
Corresponding author: Ping LI; Tel: +86-551-62901368; E-mail: li_ping@hfut.edu.cn
DOI: 10.1016/S1003-6326(14)63190-3