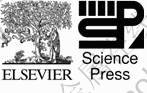
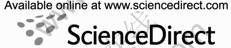
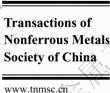
Trans. Nonferrous Met. Soc. China 22(2012) 305-311
Effect of Ti-Si-Mg-Al wire on microstructure and mechanical properties of plasma arc in-situ welded joint of SiCp/Al composites
LEI Yu-cheng1, 2, XUE Hou-lu1, HU Wen-xiang1, YAN Jiu-chun2
1. School of Material Science and Engineering, Jiangsu University, Zhenjiang 212013, China;
2. State Key Laboratory of Advanced Welding and Joining, Harbin Institute of Technology, Harbin 150001, China
Received 5 January 2011; accepted 25 October 2011
Abstract: The influence of Ti-Si-Mg-Al wire on microstructure and mechanical properties of SiCp/Al metal matrix composite joints produced by plasma arc in-situ weld-alloying was investigated. Argon-nitrogen mixture was used as plasma gas and Ti-Si-Mg-Al flux-cored wires as filled composites. Weldments were submitted to tensile test. Meanwhile, the macro morphology and microstructure of the joints were examined. The result shows that the formation of needle-like harmful phase Al4C3 is effectively inhibited and the wettability of molten pool is improved by adding Ti-Si-Mg-Al flux-cored wires. With 15Ti-5Si-5Mg-Al flux-cored wire as filled composite, the maximum tensile strength of the welded joint is 267 MPa, which is up to 83% that of the matrix composites under annealed condition.
Key words: plasma arc; in-situ welding; aluminium matrix composites; Ti-Si-Mg-Al flux-cored wire
1 Introduction
At present, aluminum metal matrix composites (Al MMCs) are more and more widely applied in aerospace, spaceflight, auto manufacturing, optical instrument and sports industry due to their excellent combination properties of high specific strength, specific stiffness, elastic modulus, wear-resistance and temperature resistance [1, 2]. However, as structural materials, they are often subjected to restrictions on the performance of secondary processing technology with practical application [3], and the welding technique is the key to industry application for Al MMCs [4].
In previous investigations, Ti-Al sheet was employed as filler to form an in-situ alloying molten pool during welding. Titanium and carbide form TiC preferably in the molten pool, in that case, the formation of needle-like brittle phases Al4C3 can be prevented [5] and the strength of the joint increases. But the strength of the joint cannot be improved as the bulky phases Al3Ti form, which would penetrate the crystal grains and break the continuity property of metal matrix [6], the maximum tensile strength of joint is still lower than that of the base material [7].
In order to improve the weldability of SiCp/Al MMCs, in this study, both techniques and metallurgy were taken into consideration. Adjusting heat input to the molten pool and improving the welding process are the main approaches in techniques [8]. Adding some elements to the weld during welding could not only improve the fluidity and wettability of molten pool but also inhibit the interface reaction, which is the main approach in metallurgy. To improve the structure and performance of joint during plasma arc in-situ welding of SiCp/Al MMCs, flux-cored wire composed of Al foil and Ti-Si-Mg-Al metal powders was used. The microstructures and mechanical properties of the weld were investigated.
2 Experimental
The morphology of SiCp/6061Al MMCs containing 10% (volume fraction) SiC particles (particle size 6 μm) made by the method of foundry is shown in Fig. 1. The maximum tensile strength of the base metal was 320 MPa in the annealed state. Rectangular specimens with size of 60 mm×20 mm×3 mm were cut by wire spark machining. The chemical compositions of the matrix for experimental materials are listed in Table 1. 8Ti-3Si-3Mg-Al and 15Ti-5Si-5Mg-Al flux-cored wires were selected as fillers in the present work.
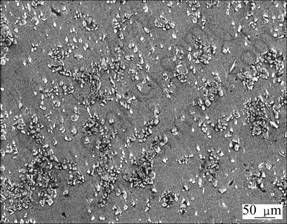
Fig. 1 Microstructure of SiC reinforced 6061Al MMCs
Table 1 Chemical composition of aluminum alloy (mass fraction, %)

The specimens were joined in ion gas of argon and nitrogen by plasma arc welding torch of Hpt-180 type. Before welding, the flux-cored wires were put into vacuum oven and kept at 200 °C for 3 h, and then both the flux-cored wires and specimens were burnished and cleaned with No.180 SiC sand paper and acetone. Metallographic transverse sections of the welds perpendicular to the weld direction were prepared using standard metallographic procedures and etched by Keller’s reagent. The microstructure of the weld was characterized using an optical microscope and scanning electron microscope. Phase analysis was carried out by X-ray diffractometry and energy dispersive spectroscopy. The diffraction angle was changed from 20° to 80° at an angular velocity of 4(°)/min. Hardness measurement for the joints was carried out with the help of the HVS-1000 micro hardness tester, each site was measured 3 times and then averaged as the point hardness value. The tensile strength of the welded joints was measured with electronic universal testing machine and the cross-head velocity was 0.5 mm/min.
3 Results and discussion
3.1 Micro-morphology of weld
Figure 2 shows the front and back of the welded joint. There is a good appearance on both sides of the weld, and no obvious defects (such as porosity and inclusions) are observed. It indicates that through strictly controlling the welding process, the method of plasma arc in-situ weld-alloying welding of SiCp/Al MMCs with flux-cored wire as filler could solve the forming problem of the weld.
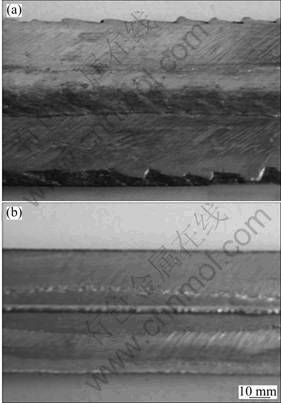
Fig. 2 Macro morphology of welded joint with 15Ti-5Si- 5Mg-Al flux-cored wire: (a) Front of weld; (b) Back of weld
3.2 Microstructure of weld
Figure 3 shows the SEM images of the welded joint, which is produced by in-situ plasma arc welding on SiCp/6061Al MMC with Ti-Si-Mg-Al flux-cored wire filler. Figure 3(a) shows the microstructure of the weld center, which is obtained by using 8Ti-3Si-3Mg-Al flux-cored wire as filler in the welding process. There are few strip-like phases detected in the weld. But the concentration of the reinforcing phase distributed in the grain boundaries is slightly higher than that in the grains. To some extent, it would reduce the binding force between the grain boundaries and decrease the tensile strength of the joint. The cluster phenomenon of particles can be also seen in the partially melted zone of the weld, as shown in Fig. 3(b).
Figure 4 shows the microstructures of the weld center which uses 15Ti-5Si-5Mg-Al flux-cored wire as filler in the welding process. In Fig. 4(a), there is a large number of fine reinforcing particles generated in the weld and the particles uniformly distribute in the grains and boundaries. There is no obvious welding defect besides a few welding bubbles. The microstructure fusion zone is shown in Fig. 4(b). The number and species of reinforcing phase are reduced while the defects become serious compared with the weld center.
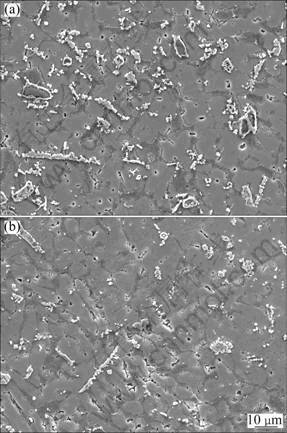
Fig. 3 SEM images of welded joint with 8Ti-3Si-3Mg-Al flux-cored wire filler: (a) Weld center of joint; (b) Partially melted zone of joint
The whole welding tests were taken under the same condition except the proportion of the alloy elements in the flux-cored wires. There are some grain boundary segregations in the weld with 8Ti-3Si-3Mg-Al flux-cored wire as filler, but none in the joint filling with 15Ti-5Si-5Mg-Al flux-cored wire. This is mainly caused by the different interface moving speed of molten pool.
Generally, the interaction between reinforcement particles and crystal front of liquid/solid interface depends on the solidification rate of the weld pool, and every coagulation system has a critical solidification rate Rcr. The particles are pushed to the front of the liquid/solid interface when the solidification rate is less than Rcr and the segregation occurs. But segregation phenomenon does not happen when the solidification rate of the molten pool is higher than Rcr. In this test, when the 15Ti-5Si-5Mg-Al flux-cored wire is used for plasma arc welding SiCp/Al MMCs, there is no obvious segregation in the weld. Mg in the molten pool can accelerate the cooling rate, which is greater than the Rcr and the particles are swallowed up by the liquid/solid interface. With the 8Ti-3Si-3Mg-Al flux-cored wire as filler, Mg in the weld pool is too little to speed up the cooling rate. So the grains are pushed by the liquid/solid interface and agglomerated together at the end.
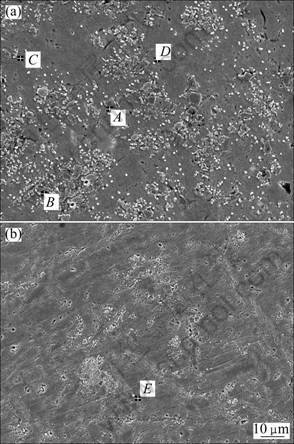
Fig. 4 SEM images of welded joint with 15Ti-5Si-5Mg-Al flux-cored wire filler: (a) Weld center of joint; (b) Partially melted zone of joint
The organization obtained by filling 15Ti-5Si- 5Mg-Al flux-cored wire during welding was analyzed by means of EDS (Fig. 5) and XRD (Fig. 6). The results indicate that the reinforcing particles in the weld are SiC, Al3Ti, TiC, TiN, MgAl2O4, AlN and so on.
The formation of needle-like Al4C3 is inhibited. During the welding process, Ti reacts with C and some other alloying elements in the weld and forms lots of fine particles, which makes up for the burning of SiC particles [7]. The effect of Si in the weld consists of two parts. On one hand, Al-Si eutectic alloy is formed to improve the fluidity of molten pool; on the other hand, high concentration of Si could inhibit the decomposition of SiC and reduce the carbon interfacial reaction [9-11]. Mg mainly as oxygen absorbents in the weld could improve the wettability of liquid metal [12].
It can be seen from Figs. 3(a) and 4(a) that the quantity of reinforcing particles generated in the molten pool is different. When using 15Ti-5Si-5Mg-Al flux-cored wire filler, the quantity of reinforcing particles is significantly greater than that using 8Ti-3Si-3Mg-Al flux-cored wire filler and the reinforcing particles such as Al3Ti distribute more uniformly. When the quantity of reactants increases, the number of nucleation particles also increases, the reactants nucleation rate is greater than the growth rate of reaction products in the molten pool, and there is no time for reaction products to grow up before the molten pool crystallization; for another thing, the generation of particles has a good lattice match performance with Al matrix, so the grains are refined and the distribution of particles are improved in the weld [13].
Fig. 5 EDS spectra of particles in Fig. 4: (a) SiC; (b) Al3Ti; (c) TiC; (d) TiN; (e) MgAl2O4
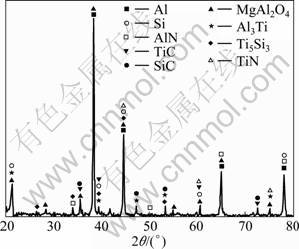
Fig. 6 XRD pattern of welded joint with 15Ti-5Si-5Mg-Al flux-cored wire filter
3.3 Microhardness of weld
Due to welding thermal cycle, the intensity is different in different positions, so the hardness distribution of welded joints is uneven. Therefore, the weld hardness was measured according to the order "weld metal—fusion zone—heat affected zone—base material". Figure 7 shows the hardness of joints, which indicates that the hardness in the center of welded joints with 15Ti-5Si-5Mg-Al is a little higher than that of the joint with 8Ti-3Si-3Mg-Al. This is because there are more fine reinforcements formed in the weld when using 15Ti-5Si-5Mg-Al flux cored wire filler, especially the fine grain Al3Ti phase, which could increase the weld hardness obviously. But the hardness of these two different welded joints is both higher than that of the base material. Due to the welding heat cycle, it also can be seen that the hardness in the heat affected zone of joint is the lowest in the whole joint, and it is softened seriously.
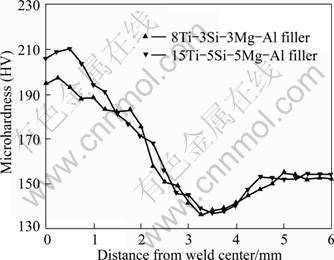
Fig. 7 Hardness of parent material and welded Joint
3.4 Tensile strength of weld joint
Tensile strength tests were carried out on welded joints with different flux-cored filled wires during welding. The result shows that when using 8Ti-3Si-3Mg-Al flux-cored wire, the maximum tensile strength of the joint is 235 MPa, while using 15Ti-5Si-5Mg-Al flux cored wire, the maximum value is 267 MPa, which reaches 83.4% that of the base metal.
Figure 8 shows the fractographs of the welded joints with two kinds of flux-cored wires. In Fig. 8(a), the joint fracture shows evident brittle rupture, the dimples are few and shallow. Microstructure analysis of the welded joint (Fig. 3) show that the deformation can be hindered greatly by the segregation particles (AlN, TiC and TiN). Therefore, the dislocation density nearby increases significantly, which would debase the capacity of plastic deformation of the joint. In Fig. 8(b), there is a large number of micro-tear marks distributed in a large dimple and the joint fracture shows certain toughness characteristics. This is mainly because the segregation phenomenon of the new particles (AlN, TiN and TiC) is avoided by filling 15Ti-5Si-5Mg-Al flux cored wires in the welding process and the hindrance of dislocation movement of particles is weakened, while the plasticity of welded joints is improved. On the other hand, the surface tension between the particles and liquid metal is reduced and the wetting property is improved by the in-situ plasma arc welding. In this case, particles can be caught and swallowed by the metal pool more easily, and the interfacial bonding strength between particles and Al matrix is enhanced.
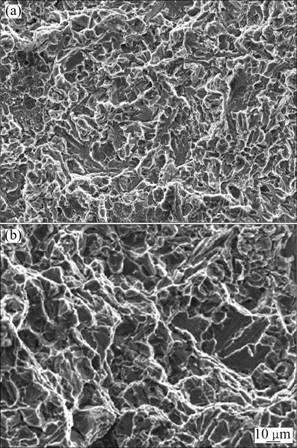
Fig. 8 Fractograph of joint with 8Ti-3Si-3Mg-Al (a) and 15Ti-5Si-5Mg-Al (b) as flux-cored wire fillers
Figure 9 shows the macroscopic fracture surface of the joint obtained by filling 15Ti-5Si-5Mg-Al flux cored wire. It can be seen that the tensile specimens fracture from the left side of joint, 1.5-2 mm from the seam center. Figure 10 shows the cross section microstructure of the weld, which contains the weld center, partially melted zone and heat affected zone. It can be found that the particles are fine and well distributed in the weld center. There is no obvious weld defect in the HAZ except some coarse grains, but there are a lot of defects in the partially melted zone such as cracks, porosity and inclusions.
Combined with the analysis in Figs. 7, 9 and 10, it can be concluded that the tensile fracture lays in the transition region between the weld center and the HAZ with the 15Ti-5Si-5Mg-Al flux cored wire as filler during welding.
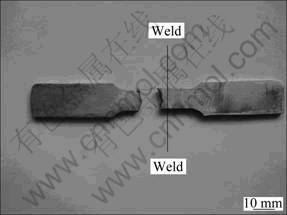
Fig. 9 Photo of fractured welded joint of specimen
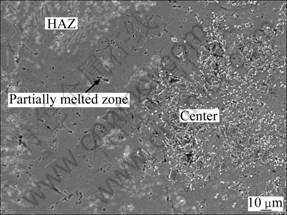
Fig. 10 Microstructure of end face in welded joint
The tensile specimen does not have obvious plastic deformation before broken (Fig. 9). This is mainly because a large heat input and fast welding speed are selected during welding to keep the in-situ welding reacted completely in the molten pool and ensure the harmful gases escaped smoothly from the pool. In this process, although the needle-like phase Al4C3 is inhibited and the formation of pores is reduced by in-situ welding, the mechanical properties of the base metal in HAZ are decreased due to high heat input [14, 15]. As the base metal in HAZ is influenced by welding thermal cycle which is equivalent of an aging treatment to the parent metal, the base metal in HAZ is softened obviously. In addition, there is no obvious plastic deformation of the tensile specimens mainly because the stiffness of plasma arc is so high that the plastic deformation of HAZ is too narrow to be seen.
Besides, kinds of defects in weld such as bubbles restrict the further improvement of the performance of joints. This will be the next problem to solve.
4 Conclusions
1) The welded joints are produced by plasma arc in-situ alloy-welding on SiCp/6061Al MMCs with argon-nitrogen mixture as plasma gases and Ti-Si-Mg-Al flux-cored wires as filler. The needle-like harmful phases Al4C3 are completely prevented, joint with good performance can be obtained by controlling the welding process rigorously.
2) The maximum tensile strength of the welded joint by plasma arc in-situ weld-alloying of SiCp/6061 Al MMCs with 15Ti-5Si-5Mg-Al flux-cored wire filler is 265 MPa, which is 83% that of the base metal. The mechanical performance of joint is enhanced by the new reinforced particles such as TiN, TiC, AlN, Al3Ti, MgAl2O4 and SiC in the welded joint. The joint fracture shows certain toughness characteristics and the tensile fracture lays in the transition region between the weld center and the HAZ.
References
[1] ELLS M B D. Joining of aluminum based metal matrix composites [J]. International Materials Reviews, 1996, 41(2): 41-58.
[2] ZOU Jia-sheng, CHEN Zheng, XU Ru-qiang, ZHAO Qi-zhang. Vacuum brazing of SiCp/LY12 metal matrix composites [J]. The Chinese Journal of Nonferrous Metal, 2004, 14(1): 74-78. (in Chinese)
[3] YAN J C, XU H B, MA L, YANG S Q. Modeling behavior of oxide film during vibration diffusion bonding of SiCp/A356 composites in air [J]. Mater Sci Technol, 2004, 20: 1489-1492.
[4] NIU Ji-tai, ZHANG De-ku, JI Guo-juan. Effect of pulse parameters on microstructure of joint in laser beam welding for SiCp/6063 composite [J]. Transactions of Nonferrous Metals Society of China, 2003, 13(2): 289-293.
[5] LEI Yu-cheng, YUAN Wei-jin, ZHU Fei, BAO Xu-dong. In-suit weld-alloying of plasma arc welding of SiCp/Al MMC [J]. Transactions of the China Welding Institution, 2005, 26(12): 13-16. (in Chinese)
[6] ZHANG Zhen. Technological study of plasma arc in-situ welded joint of SiCp/Al metal matrix composites [D]. Zhengjiang: Jiangsu University, 2007. (in Chinese)
[7] LEI Yu-cheng, YUAN Wei-jin, CHEN Xi-zhang, ZHU Fei, CHENG Xiao-nong. In-situ weld-alloying plasma arc welding of SiCp/Al MMCs [J]. Transactions of Nonferrous Metals Society of China, 2007, 17(2): 313–317.
[8] ZHAO Yu-hou, YAN Wen, ZHOU Jing-en. Influence of Si and Mg on shape of Al3Ti reinforcing phase in in-situ Al-based composite [J]. Ordnance Materials Science and Engineering, 2001, 24(2): 34-37. (in Chinese)
[9] WANG H M, CHEN Y L, YU L G. In-situ weld-alloying/laser beam welding of SiCp/6061Al MMC [J]. Materials Science and Engineering A, 2000, 293: 1-6.
[10] JIANG Rui-jiao, JIANG Long-tao, SUN Li-xin, CHEN Guo-qin, XIU Zi-yang, WU Gao-hui. Aging behavior of sub-micron Al2O3P/Al-Mg-Si composites [J]. Acta Materiae Compositae Sinica, 2009, 26(2): 1-5. (in Chinese)
[11] URE?A A, ESCALERA M D, GIL L. Influence of interface reactions on fracture mechanisms in TIG arc-welded aluminium matrix composites [J]. Composites Science and Technology, 2000, 60(4): 613-622.
[12] JIANG Long-tao, WU Gao-hui, SUN Dong-li, ZHANG Qiang, CHEN Jian-fei, KOUNO N. Microstructure and mechanical behavior of sub-micro particulate reinforced Al matrix composites [J]. J Mater Sci Lett, 2002, 21(8): 609-611.
[13] Wu Jie-jun. WANG Dian-bin, CUI Jian, YUAN Guang-jiang. Analysis of casting defects in SiCp reinforced aluminum matrix composites [J]. Acta Metallurgica Sinica, 1999, 35(1): 103-108. (in Chinese)
[14] LEI Yu-cheng, ZHANG Zhen, NIE Jia-jun, CHEN Xi-zhang. Effect of Ti-Al on microstructures and mechanical properties of plasma arc in-situ welded joint of SiCp/Al MMCs [J]. Transactions of Nonferrous Metals Society of China, 2008, 18(4): 809-813.
[15] ZHAO Yong-chun. Microstructure and mechanical behaviors of particle-reinforced aluminum matrix composites [D]. Harbin: Harbin Institute of Technology, 1997. (in Chinese)
Ti-Si-Mg-Al焊丝对SiCp/Al 基复合材料等离子弧原位焊接焊缝组织和性能的影响
雷玉成1, 2, 薛厚禄1, 胡文祥1, 闫久春2
1. 江苏大学 材料科学与工程学院,镇江 212013;![]()
2. 哈尔滨工业大学 先进焊接与连接国家重点实验室,哈尔滨 150001
摘 要:研究Ti-Si-Mg-Al焊丝对等离子弧原位合金化焊接制备SiC颗粒/铝金属基复合材料的微观结构和力学性能的影响。以氩氮混合气体为离子气,采用Ti-Si-Mg-Al药芯焊丝作为填充材料,对焊接接头进行拉伸试验,并对宏观形态和微观组织进行分析。结果表明:以Ti-Si-Mg-Al药芯焊丝作为原位反应填充材料,可以有效抑制针状脆性相Al4C3的生成。 以15Ti-5Si-5Mg-Al药芯焊丝作为填充材料时,焊接接头的最大抗拉强度为267 MPa,达到退火条件下基体材料强度的83%。
关键词:等离子弧焊;原位合金化焊接;铝基复合材料;Ti-Si-Mg-Al药芯焊丝
(Edited by FANG Jing-hua)
Foundation item: Project (09003) supported by the Open-Fund Research of State Key Laboratory of Advanced Welding and Joining, Harbin Institute of Technology, China; Project (JD0805) supported by the Science and Technology Innovation Team, Jiangsu University, China
Corresponding author: LEI Yu-cheng; Tel: +86-511-88790798; E-mail: yclei@ujs.edu.cn
DOI: 10.1016/S1003-6326(11)61175-8