稀有金属 2012,36(06),979-984+2-6
微波焙烧回收汽车尾气废催化剂湿法浸出渣中铑
陈安然 张泽彪 王仕兴 彭金辉 王万坤 王子阳
昆明理工大学冶金与能源学院
云南省质量检测研究院
摘 要:
铑的浸出率低是回收汽车尾气废催化剂中贵金属的难题之一,贵金属铑的溶解过程主要存在的问题是:溶解周期长,溶解效率低,试剂消耗大,溶解过程复杂,浸出率低,环境污染严重等。提高汽车尾气废催化剂中铑的浸出率,并进行清洁高效提取,一直是研究重点。目前主要的溶解技术是中温氯化法和硫酸氢钠(钾)熔融法,但均不同程度的存在技术问题。本工艺采取微波焙烧回收汽车尾气废催化剂湿法浸出渣中的铑,分别考察了反应温度,反应时间和物料试剂配比3个主要因素对浸出渣中铑浸出率的影响,结果表明:微波加热有利于促进分子振动,造成颗粒破裂,增大固液反应面积,增强物质间的传热传质,增加反应速率,减小试剂消耗,能显著地提高浸出率。在最佳实验条件下:配比1∶10,反应温度600℃,反应时间1 h,铑的总体浸出率可以达到99.79%。本工艺环境污染较小,溶解效率高,且浸出率高,具有较大的发展前景,为汽车尾气废催化剂中贵金属铑的清洁高效提取提供一定的技术指导。
关键词:
铑;汽车尾气废催化剂;湿法冶金;微波焙烧;
中图分类号: X705
作者简介:陈安然(1986-),男,陕西渭南人,硕士研究生;研究方向:稀贵金属回收与利用;彭金辉(E-mail:jhpeng72@hotmail.com);
收稿日期:2012-05-28
Recovery Rh from Leached Residue of Spent Automobile Catalysts by Microwave Roasting
Abstract:
One of difficult problems is the low recovery of rhodium during the recovery of precious metals from spent automobile catalysts,the main problems of the dissolution technique of rhodium are long dissolution period,low dissolution efficiency,high reagent consumption,complex operation,and serious environment pollution.In order to improve the leaching efficiency of rhodium,many researchers focused on clean dissolution and high efficient technique.At the present,the applied dissolution techniques were intermediate temperature chloride-dissolution method and sodium(potassium) bisulfate fusion-dissolution method with some problems.In this work,microwave roasting was used to recovery rhodium from the leached residue of spent automobile catalysts.The impacts of various factors;reaction temperature,reaction time and proportion of solid to reagent on the rhodium leaching efficiency were studied.The result indicates that microwave heating,through accelerating molecular vibration,smashing the particles,and enhancing the contacting area of solid and liquid,increasing heat and mass transfer processes,finally speeds up the reaction,reduces reagent consumption and obviously improves leaching efficiency.Under the best experimental condition,the proportion of material and reagent is 1∶ 10,the reaction temperature is 600 ℃ and the holding time is 60 min.Leaching ratio of rhodium reaches 99.79%.The technique that with less environment pollution,high efficiency of dissolution and high leaching rate has a wide application prospect provides a technical guidance for the recovery of rhodium from spent catalysts of automobile exhaust.
Keyword:
rhodium;spent automobile catalysts;hydrometallurgy;microwave roasting;
Received: 2012-05-28
近年来由于汽车尾气净化用的铂族金属催化剂的使用日益普及,催化剂中起催化作用的铂族金属的用量逐年增加[1],催化剂中毒失效后,很大一部分不能再生,而全世界每年要产生大量的废贵金属催化剂,如何适当处理并充分利用这些二次资源显得日益重要和紧迫[2],从汽车尾气废催化剂中回收铂族金属已是世界各国研究的重点。目前从汽车尾气废催化剂中回收铂族金属有火法和湿法两种途径[3,4,5,6,7]。湿法流程有:载体溶解法、溶解活性组分法及全溶解法等多种工艺路线[8],湿法流程具有铂族金属Pt,Pd选择性浸出率高,得到的贵金属溶液成分相对简单,并且溶液浓度高,有利于后续的提取、分离,而且反应条件温和等优点,展现出了良好的工业前景,在实际生产中被广泛应用。Jimenez de Aberasturi等[9]曾开展过全湿法浸出工艺提取汽车尾气废催化剂中的Pt,Pd的工作,该方法具有选择性浸出,试剂简单,对设备腐蚀性小,对环境友善,溶液成分简单等优点,Pt,Pd浸出率大于95%,而铂族金属Rh只有部分溶出。
目前运用湿法流程从汽车尾气废催化剂中回收铂族金属的主要问题是铑的回收率极低,在氧化剂存在的盐酸溶液可溶解催化剂中的铂、钯及其氧化物,但铑和铑的氧化物在大多数酸性溶液中是不溶解的,在王水中也极难溶解[10,11,12],而大多数汽车催化剂中,铑的价值又占铂族金属总价值的很大部分,所以研究浸出Rh的有效方法,提高铑的回收率是很有意义的[13,14]。Wu等[15]采用添加氟化物离子的盐酸+硫酸浸出液并周期性或连续加入双氧水浸出经过甲酸钠、硼氢化钠和氢气进行预处理的汽车尾气废催化剂中的贵金属。研究结果表明,铑的回收率均可达到90%以上。Anon,陈景等采用加压氰化法浸出汽车尾气废催化剂中铂族金属,铑的浸出率有明显提高[16,17]。
考虑到传统的加热方法存在着能耗大,升温慢,温度场不均匀,物料传热特性影响大的缺点。为了解决湿法回收中汽车尾气废催化剂中Rh浸出率不高的问题,本研究拟对湿法浸出渣二次处理,以浸出大部分残留的Rh。因此,为提高Rh的浸出率,又避免传统火法所用的高温捕集,本文提出了对汽车尾气废催化剂湿法酸浸的浸出渣采用微波煅烧酸浸-水浸提取Rh的新工艺。考察了微波焙烧提取Rh工艺的可行性和较佳工艺参数。研究表明,本工艺技术简单,试剂无污染,耗能低,最终铑的总浸出率达到95%~99%。
1实验
1.1原料
实验所用的原料为经过一次湿法盐酸浸出的汽车尾气废催化剂,其主要成分还是镁质堇青石,各元素的化学组成如表1所示。
1.2设备
微波加热熔融实验所用加热设备为15 kW箱式微波反应器,最大微波功率为1.5 kW。SHZ-D(Ⅲ)循环水式真空泵,耐高温陶瓷坩埚(定制)。常规焙烧实验所用加热设备为意丰电炉(KSY-15-16),最高温度为1200℃。
1.3方法
浸出渣按照一定的配比与回收剂混合均匀,放于耐高温陶瓷坩埚中,在坩埚外壁包覆保温材料,置于微波反应器中,设定电流值为(3.2~3.5 A)(电压值为88.5~95.8 V)。反应达到预定条件后,关闭微波,取出坩埚,待冷却到室温时,取出烧结物,加水搅拌溶解,真空抽滤过滤,固液分离,取样分析最终滤渣中Rh的含量。在常规焙烧实验中,浸出渣和回收剂按配比混合均匀,放于耐高温陶瓷坩埚中,置于马弗炉,反应达到预定条件后,关闭电源,随炉冷却,其后样品处理过程和微波焙烧实验中相同。
1.4分析
使用分光光度法进行测定,设备为岛津(UV2550)紫外-可见光分光光度计,分析方法依照GB/T23277-2009进行。
表1 酸浸渣的主要化学成分(%,质量分数)Table 1 Main chemical compositions of leaching residue of spent automobile catalyst(%,mass fraction) 下载原图

表1 酸浸渣的主要化学成分(%,质量分数)Table 1 Main chemical compositions of leaching residue of spent automobile catalyst(%,mass fraction)
2结果与讨论
2.1反应温度对浸出率的影响
浸出渣与回收剂的配比为1∶8,反应时间为1 h,Rh的浸出率随微波实验反应的温度的变化如图1所示。
由图1可知,在600℃以下,随温度的升高,浸出率升高,但是温度高于600℃时浸出率反而下降。温度高于600℃时回收剂分解速率增加,同时回收剂分解产物不能浸出铂族金属Rh,反而增加了催化剂基体的刻蚀速率。常规加热实验随温度升高浸出率提高,是由于物料主要组成为堇青石,其传热性差,物料内部升温慢,即使在炉膛温度达到反应温度,内部物料仍然未与回收剂进行反应或者反应速率较慢;随温度升高,物料内部温度也相应升高才促进了反应进行。微波加热试验浸出率较常规实验高,这是由于微波辐射引发分子振动的原因。微波加热试验中温度升高浸出率增加幅度比常规实验低的原因,一方面是,微波辐照促进了固液反应的速率,在较低温度下浸出率就明显高于常规方法的浸出率;另一方面是在常规实验中较高的反应温度有利于液体的翻滚搅动,增强固液交换,增加了反应速率。因此从图1可以看出采用微波加热提取残渣中的Rh最佳温度为600℃最宜。
2.2反应时间对浸出率的影响
浸出渣与回收剂的配比为1∶8,温度为600℃时,Rh的浸出率随微波实验反应时间的变化如图2所示。
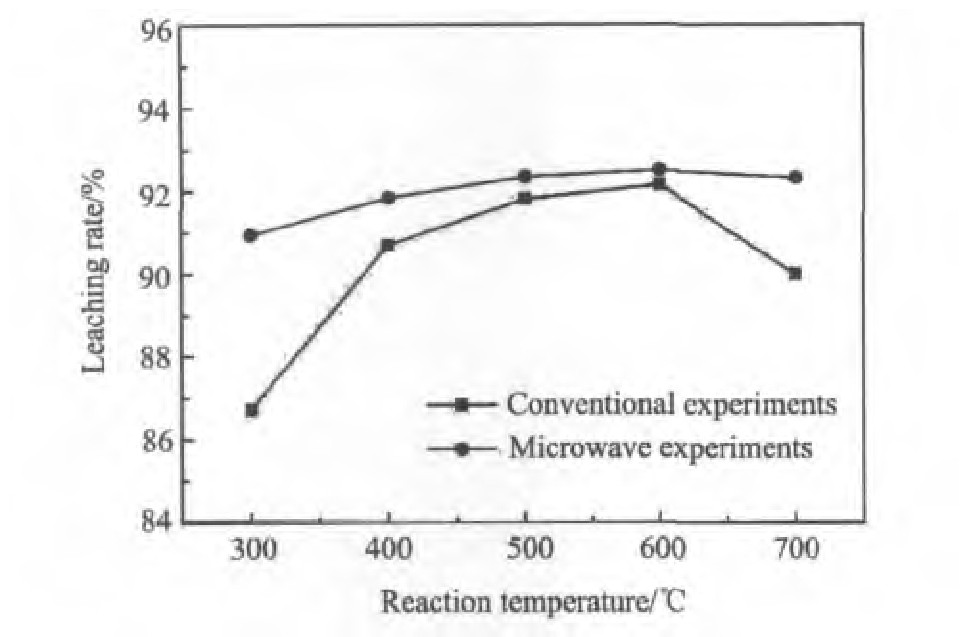
图1 反应温度对铂族金属Rh浸出率的影响Fig.1 Effect of reaction temperature on ratio of Rh leaching
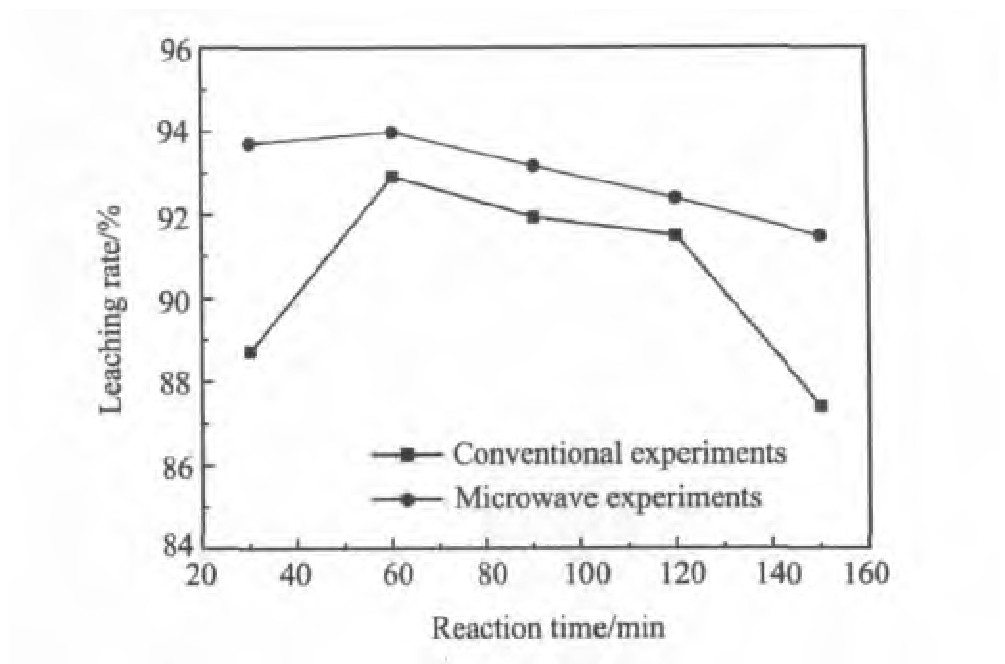
图2 反应时间对铂族金属Rh浸出率的影响Fig.2 Effect of reaction time on ratio of Rh leaching
由图2可见,在整个保温过程中微波加热实验的浸出率始终较常规加热实验的浸出率高;这是由于微波加热速度快,增加了回收剂和基体的反应,一定程度上打开了基体对铂族金属的包裹,使其充分反应。图2也表明保温时间小于60 min时,两种方法的浸出率随反应时间的增加而提高;保温时间大于60 min时,浸出率随时间增加而降低。对微波反应产物进行水浸和过滤时,发现随保温时间增加过滤时间也增加,同时出现了胶体状物质,这些表明增加保温时间,基体的刻蚀程度也在增加。因此本研究选择的保温时间定为60 min。
2.3物料试剂配比对浸出率的影响
反应温度为600℃,反应时间为1 h,Rh的浸出率随浸出渣与回收剂配比的变化如图3所示。
由图3可见,在微波浸出过程中,浸出率随物料与回收剂配比的增加而增加,在1∶10时铑的总浸出率已达到99.42%,但是在配比超过1∶10后,浸出率不再随物料与回收剂配比的增加而增加。常规加热浸出实验,虽然浸出率也随物料与回收剂配比的增加而增加,但是铑的浸出率明显低于微波浸出时的浸出率。因为试剂用量的增加有利于物料和试剂的充分接触,使物料中的铂族金属Rh更有机会和回收剂反应,微波加热实验在配比达到1∶10时,物料中的金属Rh已基本反应完全,而回收剂用量过多则会增加基体的溶解。常规加热过程中没有搅拌物料,废催化剂导热系数小,因此传热传质均较缓慢。将微波技术应用到回收汽车尾气废催化剂中铂族金属过程,能起到强化浸出过程的作用,微波加热是通过物料内部的介电损耗直接将化学反应所需要的能量传递给反应的分子或原子,在足够强度的微波能量密度下,这种原位能量转换方式使得微观区域得到快速的能量累积,并能降低化学反应和扩散过程所要克服的能垒,从而促进反应和扩散过程快速进行;同时有效地解决了传统加热颗粒时存在的“冷中心”问题,促进了反应过程中的能量传递过程。因此,尽管催化剂物料的热传导性较差,也可在极短的时间内达到加热温度,缩短浸出时间,有效地降低能耗。故微波加热实验的最佳配比较常规加热实验有了很大提高。实验也表明,随着回收剂用量的增加,溶液的过滤时间也会相应延长,微波加热实验配比在1∶14时,过滤时间是配比为1∶10时的5倍,考虑基体中Al,Si融解过多,有胶体的形成。
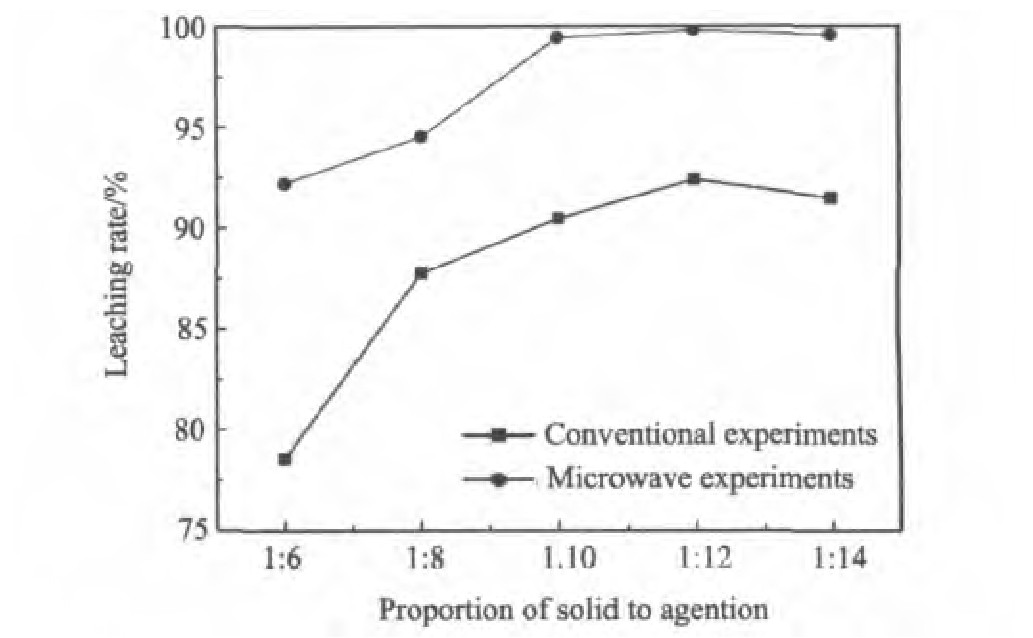
图3 物料试剂的配比对铂族金属Rh浸出率的影响Fig.3 Effect of proportion of solid to reagent on ratio of Rh leac-hing
2.4反应机制讨论
在高温使用环境下,汽车尾气废催化剂中的铂族金属颗粒会因热烧结或者热扩散进入载体内部被包裹而失效,还有一部分铂族金属颗粒会因高温变为氧化物而失去催化性能,也阻碍了颗粒内部铂族金属和汽车尾气的接触[18],由于汽车尾气催化剂在使用过程中会有α-Al2O3生成,将铂族金属包覆于不溶或难溶解的α-Al2O3载体催化剂中[19],所以提取过程中先要打开载体的包裹,促进传热传质,使铂族金属能更好地和试剂相互反应,本研究采用微波处理措施,既将难溶解Al2O3溶解,同时打开载体对铂族金属颗粒的包裹,将铂族金属转化成易溶于水的化合物。
图4和5是酸浸渣和微波加热实验后的渣相的X射线衍射图,由图可见,酸浸渣和微波实验浸出渣的主要成分均是镁质堇青石,微波实验浸出渣中镁质堇青石的谱线较酸浸渣中已有明显减弱,说明载体结构有了很大的破坏,大量的Al2O3和SiO2参与了反应,这足以让铂族金属Rh暴露出来和试剂进行反应,并且微波实验浸出渣中有大量新物相生成,也表明了反应是有效的。
图6和7是酸浸渣和最佳微波实验条件下得到的浸出渣的扫描电镜图。微波实验浸出渣颗粒上明显可见有大量裂纹,表明物料在参与反应的同时,内部分子振动也引起了自身结构的破坏,将包裹的Rh暴露出来,因此促进了反应。而酸浸渣的结构表明固液反应只能单纯的在物料颗粒表面进行,传热传质过程也仅发生在颗粒的表面上,试剂要与载体颗粒内部的铂族金属反应,就必须先破坏载体,所以在常规实验中,必须增加试剂量和反应温度,才能提高浸出率。因此微波加热浸出具有明显的优越性。
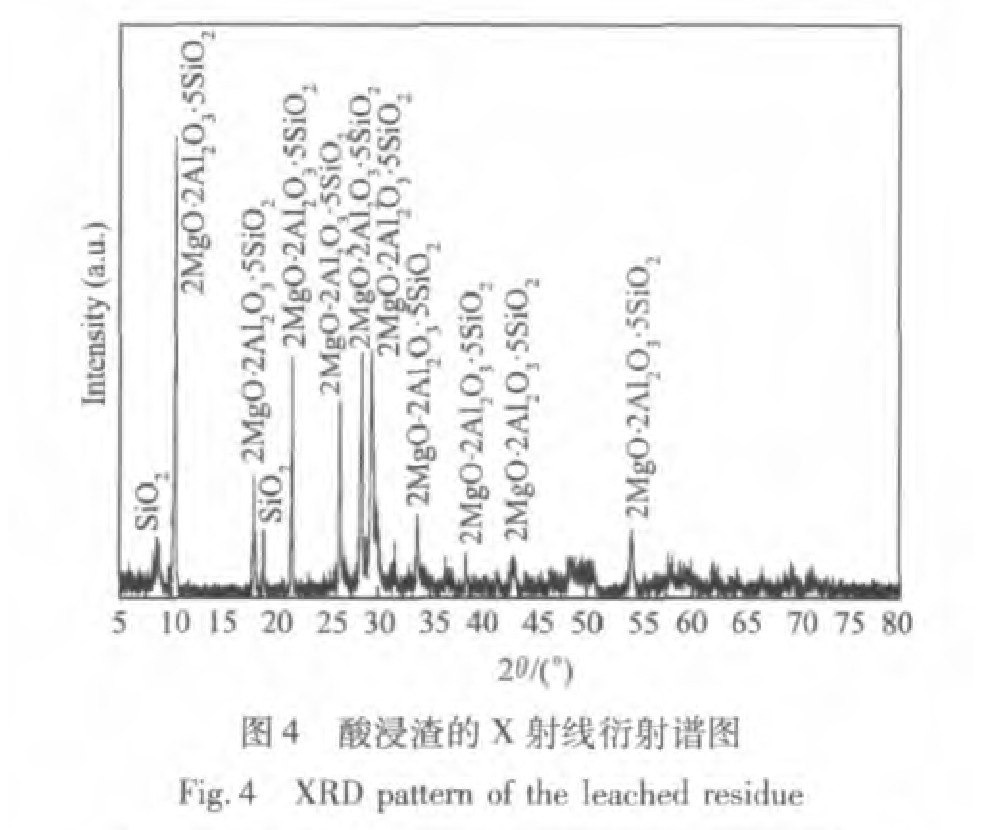
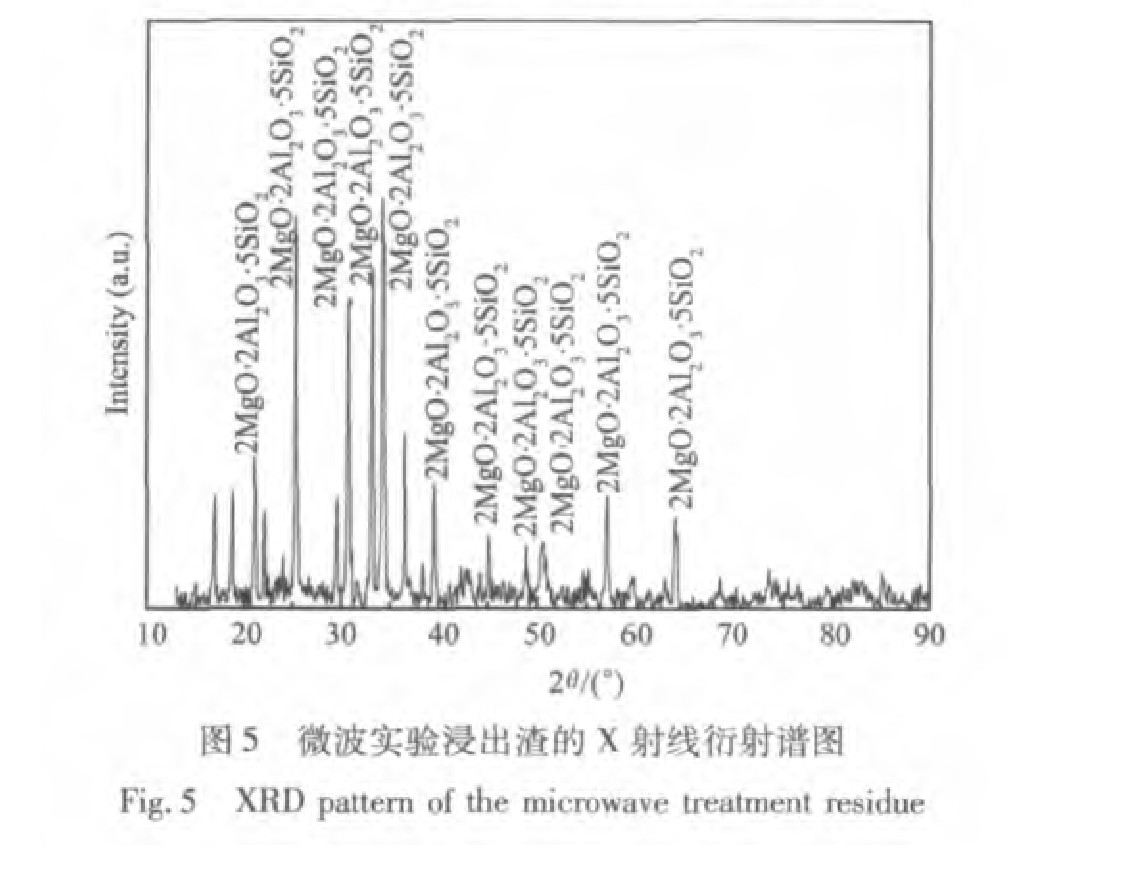
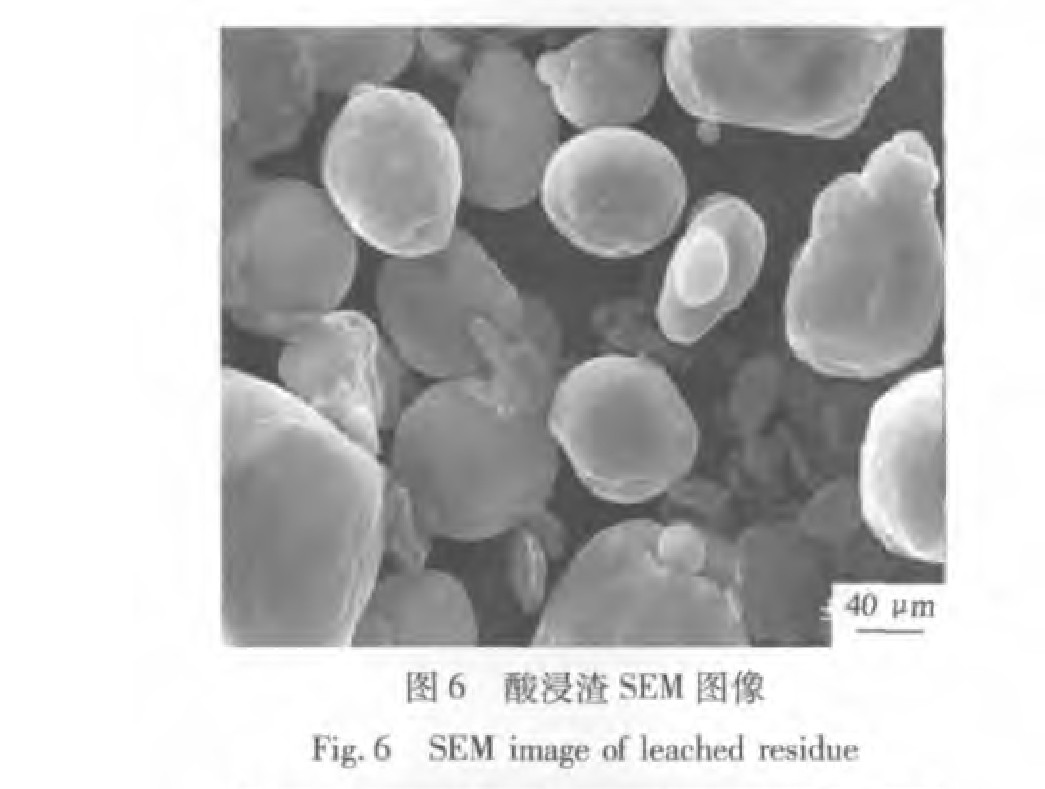
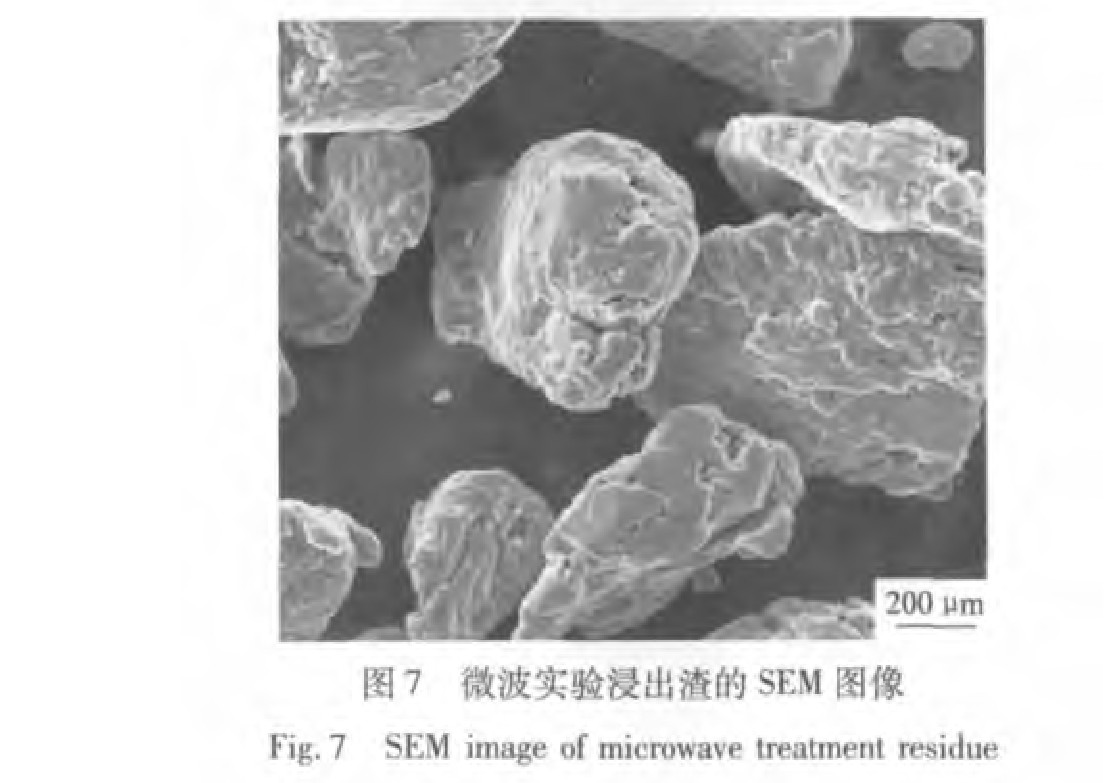
3结论
1.对汽车尾气废催化剂酸浸渣中铂族金属Rh采取微波焙烧工艺回收,考察了微波焙烧浸出时各工艺参数对浸出率的影响,筛选出的最佳工艺条件为:物料试剂配比为1∶10,反应温度600℃,反应时间1 h。在最佳条件下,铂族金属Rh的浸出率可达到99.79%。
2.微波焙烧回收工艺较常规焙烧工艺降低了反应温度和反应时间,并且显著提高了浸出率。通过扫描电子显微镜(SEM)观察,其原因在于:采取微波焙烧可以引发分子振动使颗粒破碎,打开载体金属对铂族金属的包裹,促进反应的进行,增强了能量传递过程。
3.在达到相同的浸出率的条件下,采用微波焙烧的方法较传统火法处理温度低,试剂消耗小,节能高效。
本文系统的分析了采取微波焙烧工艺回收汽车尾气废催化剂酸浸渣中铂族金属Rh时,反应温度、反应时间、物料试剂配比对浸出率的影响,和微波焙烧工艺较传统火法处理时的优势,为汽车尾气废催化剂中贵金属铑的清洁高效提取提供一定的技术指导。本工艺有着一定的应用前景。
参考文献
[1] Xie X M,Liu L.Research progress in recovery of noble metalsfrom spent catalysts[J].Liaoning Chemical Industry,2009,11(4):802.(薛小梅,刘利.废催化剂中贵重金属回收的研究进展[J].辽宁化工,2009,11(4):802.
[2] Zhang B A.Recover platinum group metals from auto-catalysts[J].China Resources Comprehensive Utilization,2004,8:15.(张邦安.从失效汽车尾气净化催化剂中回收铂族金属[J].中国资源综合利用,2004,8:15.)
[3] Liu S J.Progress of PGMs extraction technology[J].PreciousMetals,1997,18(3):53.(刘时杰.铂族金属提取冶金技术进展[J].贵金属,1997,18(3):53.
[4] Hoffman J E.Recovering platinum group metals from auto-cata-lysts[J].JOM,1988,40(6):40.)
[5] Mishra P K,Ramadorai G.Hydrometallurgical recovery of plat-inum group metals from automobile converters[A].Proceedingsof the 117th Annual AIME Meeting[C].New York:AIME,1988.
[6] Huang K,Chen J.High temperature cyanide leaching of plati-num group metals from spent automobile catalytic converters[J].Chinese Journal of Nonferrous Metals,2003,13(6):1559.(黄昆,陈景.从失效汽车催化剂中加压氰化浸出铂族金属[J].中国有色金属学报,2003,13(5):1559.)
[7] Wu G Y,Dai Y N.Concentration of precious metals in wastedcatalyst[J].Chinese Journal of Rare Metals,2005,26(3):231.(吴国元,戴永年.失效贵金属催化剂中贵金属的富集[J].稀有金属,2005,26(3):231.)
[8] Huang K,Chen J.Progress in recovery of platinum group met-als from spent automobile catalytic converters[J].Journal ofNonferrous Metals,2004,56(1):70.(黄昆,陈景.从失效汽车尾气净化催化转换器中回收铂族金属研究进展[J].有色金属,2004,56(1):70.)
[9] Jimenez de Aberasturi D,Pinedo R,Ruiz de Larramendi I,Ruizde Larramendi J I,Rojo T.Recovery by hydrometallurgical ex-traction of the platinum-group metals from car catalytic converters[J].Minerals Engineering,2011,24:505.
[10] Jing C,Kun H.A new techniques for extraction of platinumgroup metal by pressure cyanidation[J].Hydrometallurgy,2006,82(3):164.
[11] Harjanto Sri,Cao Yucai,Shibayama Atsushi.Leaching of Pt,Pd and Rh from automotive catalyst residue in various chloridebased solutions[J].Materials Transactions,2006,47:129.
[12] Dong H G.Progress in dissolution technique of precious metalrhodium materials[J].Chinese Journal of Rare Metals,2011,35(6):939.(董海刚.稀贵金属铑物料溶解技术研究进展[J].稀有金属,2011,35(6):939.)
[13] Du X,Zhang X W,Zhou Y H,Yang J H,LüJ W.Hydromet-allurgical processes of platinum group metals recovery from ex-haust catalysts[J].China Mining Magazine,2009,18(4):82.(杜欣,张晓文,周耀辉,杨金辉,吕俊文.从废催化剂中回收铂族金属的湿法工艺研究[J].中国矿业,2009,18(4):82.)
[14] Wang Y L,Liu Z H.Recovery of Platinum Group Metals[M].Changsha:Central South University of Technology Press,2005.10.(王永录,刘正华.金银及铂族金属再生回收[M].长沙:中南工业大学出版社,2005.10.)
[15] Wu K Y,Amanda.Recovery of Precious Metals from Automo-tive Catalytic Converters[M].University Microfilms InternationalA Bell&Howell Information Company,1993.343.
[16] Anon.Cyanide leaching of PGMs from auto-catalysts[J].Cali-fornia Mining Journal,1992,62(4):31.
[17] Huang K,Chen J,Chen Y R,Zhao J C,Li Q W,Yang Q X.Recovery of precious metals from spent auto-catalysts by method ofpressure alkaline treatment-cyanide leaching[J].Chinese Jour-nal of Nonferrous Metals,2006,16(2):363.(黄昆,陈景,陈奕然,赵家春,李奇伟,杨秋雪.加压碱浸处理-氰化浸出法回收汽车尾气废催化剂中的贵金属[J].中国有色金属学报,2006,16(2):363.)
[18] Li Y W,Qi X D.Study on leaching of platinum-group metalsfrom spent auto-catalysts[J].Journal of South China Normal U-niversity(Natural Science Edition),2008,53(2):84.(李耀威,戚锡堆.废汽车催化剂中铂族金属的浸出研究[J].华南师范大学学报(自然科学版),2008,53(2):84.)
[19] Liu S J.Mining and Metallurgy of Platinum Group Metals[M].Beijing:Metallurgical Industry Press,2001.163.(刘时杰.铂族金属矿冶学[M].北京:冶金工业出版社,2001.160.)