J. Cent. South Univ. Technol. (2009) 16: 1034-1038
DOI: 10.1007/s11771-009-0171-7

Vibration compaction characteristics of rock filling embankment
YANG Ming-hui(杨明辉), LIU Guang-xuan(刘广轩), ZHAO Ming-hua(赵明华)
(College of Civil Engineering, Hunan University, Changsha 410082, China)
Abstract: The dynamic model experiment of the rock filling embankment was carried out to investigate the vibration compaction mechanism. The rock filling materials were compacted by the plate-vibrated compactor, and the characteristics of the rock filling materials, such as settlement, pressure change and response waveform, were measured by the dynamic earth pressure gauge and accelerometer. Moreover, a new method for detecting the compactness of the rock filling embankment was proposed based on the maximum dry density and modulus of deformation. The results show that the process of vibration compaction includes compact, elastic deformation and loose stages, and the vibratory pressure transfers to the surroundings from the vibration center in non-linear rule. Furthermore, the test results obtained by the present method are basically in agreement with those obtained by the traditional method, and the maximum relative error between them is about 0.5%.
Key words: rock filling; embankment; model test; vibration compaction; compactness
1 Introduction
During the construction of the highway in mountainous area characterized by rocks and soil, the rock filling embankment is the major style. However, the key issue of the rock filling embankment is the quality of the compaction. Therefore, it is important to investigate the mechanism of vibration compaction of the rock filling embankment[1-6]. The basic control criterion of the quality of the rockfill embankment compaction is the compactness. However, most of the studies and the test criteria are based on the water or sand filling test, which takes a lot of time and labor and damages the roadbed, and there are the test standard and the filling standard for the rock filling embankment in geotechnical engineering[7-8]. Obviously, it is important to find a suitable test method for rock filling embankment in practice. LIU et al[9] used transient hammer-impacting technology to measure the compactness of the soil. LI et al[10] applied the direct shear wave method to evaluating the compactness of the subgrade nondestructively. VAGHELA[11] proposed the resonant column test for the determination of elastic modulus of the compacted subgrade soils. Moreover, the additional weight method was applied to measuring the density of the rock fill of the dam[12-13]. IVANSSON and KARASALO[14] presented a simple method to establish the frequency scatter curve of Raleigh wave in different media. KIM and PARK[15] used spectral analysis of surface waves method to evaluate the ground densification. MALISCHEWSKY[16] tested the earth filling embankment and established the confirmed formula of the compactness. However, the accuracies of the above methods cannot meet the requirement of engineering if the filling material is rock.
According to the practice of engineering, a laboratory test on the vibration deformation properties and mechanism of the rock filling embankment was carried out. The mechanism of vibration compaction was achieved. Moreover, a new method for detecting the compactness of rock filling embankment was proposed.
2 Experimental
2.1 Parameters of experiment
According to the similarity theory, the model test was carried out to investigate the vibration compaction of the rock filling embankment. Fig.1 shows the details of the experiment of the rock filling embankment. The basic properties of the prototype embankment and model are shown in Table 1.
2.2 Experiment apparatus
2.2.1Vibration compaction equipment
Vibration compaction is the most effective process to compact the rockfill. The mass of vibration roller is more than 12 t. In this experiment, two kinds of flat panel vibration machines with dimensions of 50 cm×60 cm were used, the vibration forces of these two machines were 10 and 20 kN respectively, and their frequencies were 3 000 r/min.
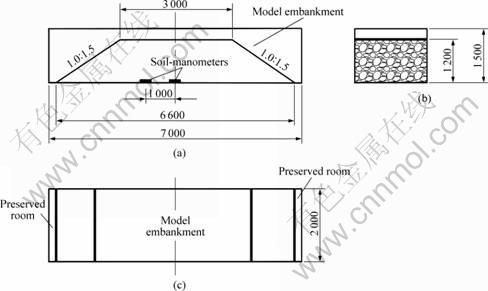
Fig. 1 Experiment model of rock filling embankment (Unit:mm): (a) Cross section; (b) Side view; (c) Top view
Table 1 Main parameters of model experiment

2.2.2 Exciter machines
Two kinds of exciter machines were used: one exciter generated simple-harmonic vertical vibratory force, with the maximum value of 100 kN, and the frequency was 30-60 Hz. Moreover, the power amplifier and the signal generator were applied. Other exciter used the lightmass dynamic penetration apparatus and the hammer sensor. This exciter could generate immediate impulse force that was transmitted forward in the pulse style.
2.2.3 Signal collection system
The piezoelectric accelerometer was used to collect the Rayleigh wave, which was installed on the magnetic base by the agglomerant. The machines were charged by the amplifier, and the signal collector was used as the correlative configuration apparatus.
2.3 Experimental procedure
Two soil-manometers were placed at the bottom of the model, and the rock embankment was filled and compacted with each floor of 20 cm. The speed of compaction was controlled by the vibration, and the numbers of roll times were 2, 4 and 6, respectively. During the rolling, the data of soil-manometer were collected, and the thicknesses of the incompact layer and the settlement of the compaction were obtained. Based on these values, 10 test points were set in the level measurement, which were used to calculate the mean value of settlement.
The heights of the embankment model were filled to be 40, 80 and 120 cm respectively by the compaction of incompact layer. Then the exciter, the dynamic penetrating hammer with lightmass and the hammer sensor settled on the stiff bearing plate, were adopted to carry out the dynamic load experiment. During the process of excitation, the excitation frequency was adjusted from 30 to 60 Hz, and the distance of two accelerometers was set on the same lines. The excitation points were adjusted from 0.5 to 3.0 m. Moreover, the piezoelectric accelerometer collected the correlative signals of the soil-manometer and accelerometer.
To investigate the effects of the moisture capacity, when the heights of the embankment model were filled to 40, 80, and 120 cm, respectively, the compactness water filling tests of two different locations were carried out at the same time, and then the rock digged in the water filling test was used to measure the moisture capacity.
3 Results and discussion
3.1 Deformation characteristic
The relationship between the vibration compaction times and the settlement of the embankment is shown in Fig.2, indicating that the vibration compaction of rock can be divided into three stages. The first stage is the compaction stage. In this stage the settlement of the rockfill layer varies obviously, and the compactness grows rapidly with the increase of compaction times. The second stage is the elastic stage. The variation of settlement is little and the rockfill is elastic in this stage, and the compactness is basically stable. The third stage is loosening. The compactness reduces in this stage. Therefore, it is shown that the optimum value of compaction times for rock filling embankment is 5 or 6.
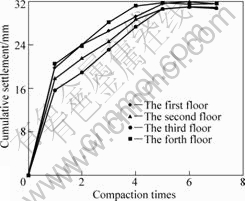
Fig.2 Relationship between settlement and compaction times
3.2 Transmission of vibration force
Generally, the embedded soil-manometers in embankment can measure the vertical soil pressure at different filling heights, different gravity loads and two kinds of vibrator loads. In this work, the soil pressures were the peaks of the response curve.
Fig.3 shows the distribution of the horizontal additional soil pressure of the rock filling embankment at an excitation amplification of 20 kN. Fig.4 shows the distribution of the vertical additional soil pressure under different plumb distances away from the vibration center. It is shown that the vibration energy is nonlinearly transferred from the vibration center to the surrounding. In Fig.3, when the horizontal distance is more than 100 cm, the horizontal additional soil pressure is 0.4 kPa, which is nearly 0.6% of the original vibratory load (67 kPa). In Fig.4, at a depth of higher than 120 cm, vertical additional soil pressure is 6.72 kPa, which is
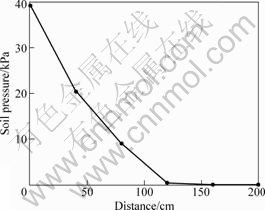
Fig.3 Relationship between horizontal additional soil pressure and horizontal distance away from vibration center
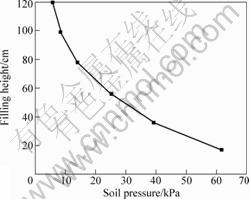
Fig.4 Relationship between vertical additional soil pressure and filling height
nearly 10% of the original vibratory load (67 kPa). Therefore, the influencing ranges of rock filling embankment are approximately 2.4 times of load width in vertical direction and 2.0 times of load width in horizontal direction.
4 New method of detecting compactness
4.1 Calculation model of compactness
The traditional technique for detecting compactness of the rock filling embankment is the water or sand filling test. However, it may destroy the subgrade, and the detecting speed is too slow to meet the requirement of the construction. Therefore, it is very important to propose a new rapid technique to detect the compactness of the rock filling embankment[17]. To achieve this aim, a new compactness model is established according to the maximum dry density and modulus of the deformation. The basic process is as follows.
According to the Boussenesq theory, the settlement of subgrade surface is[18-19]:
(1)
where P is the concentrated load; a and b are fitting parameters that can be obtained by the linear fitting of the results of static cone penetration test. If the radius of the flat-bottomed circular probe is r0, a and b can be written as
(2)
(3)
where m is Poisson ratio; E0 is the modulus of deforma- tion; and n0 is the initial void ratio and is defined as
(4)
Therefore, the compactness of rock filling embankment K can be written as
(5)
where ρm is the density of the rock filling materials; and ρdmax is the maximum dry density obtained by compaction test.
4.2 Test verification
In order to verify the rationality and feasibility of the new technique, the compactness of three testing points was detected by the new technique and water filling test. The basic parameters are determined as: E0=23.65 MPa, rm=2.67 g/cm3, and rdmax=2.46 g/cm3. Parameters a and b are obtained by linearly fitting the results of static cone penetration test. The linear fitting curves are shown in Fig.5, and the compactness is
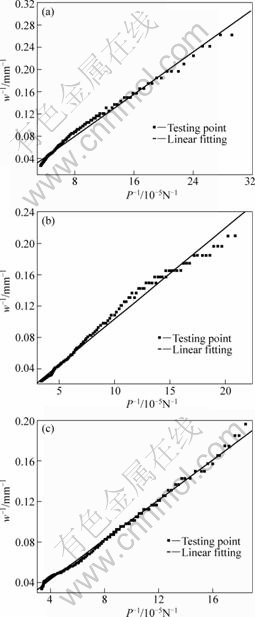
Fig.5 Linear fitting for different testing points: (a) Point 1; (b) Point 2; (c) Point 3
obtained by Eq.(5). The comparison of compactness between the new technique and water filling test is shown in Table 2. The maximum relative error between them does not exceed 0.5%, which indicates that the results of the new method agree with those of the traditional method.
Table 2 Comparison for compactness at different testing points
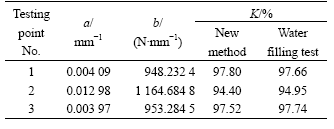
5 Conclusions
(1) The compactness increases rapidly with the increase of the compaction times during the vibration compact. It is stable if the compaction times reaches 5 or 6. There exists an optimal compact times affected by the rock parameters and compaction energy.
(2) The influencing ranges of rock filling embankment are approximately 2.4 times of the load width in vertical direction, and 2.0 times of the load width in horizontal direction.
(3) A new method for detecting compactness for rock filling embankment is proposed, which can improve the testing speed and reduce the damage to the roadbed.
References
[1] CHAI He-jun, CHEN Qian-ying, KONG Xiang-yun. Overview of soil-stone high embankment construction study[J]. Rock and Soil Mechanics, 2004, 25(6):1005-1010.
[2] WANG Peng, GUA Cheng-chao. The application of PFWD in sub-grade compactness test[C]// GeoHunan International Conference. Changsha, 2009: 84-91.
[3] CATTANEO P W. Optimal measurement of signal over noise ratio with constrained filter transfer functions[J]. Nuclear Instruments and Methods in Physics Research, 2002, 23(3): 726-728.
[4] JAROSLAV F. Notes on the effect of grain crushing on the granular soil behavior[J]. Engineering Geology, 2002, 6(3): 93-98.
[5] DENG Jian, BIAN Li. Response and energy dissipation of rock under stochastic stress waves[J]. Journal of Central South University of Technology, 2007, 14(1): 111-114.
[6] PEIRIS L M, MADABHUSHI S P, SCHOFIELD A N. Centrifuge modeling of rock-fill embankments on deep loose saturated sand deposits subjected to earthquakes[J]. Geotechnical and Geoenvironment Engineering, 2008, 134(9): 1364-1374.
[7] SHA Qing-lin. Road compaction and compaction standard[M]. Beijing: China Communications Press, 2001: 50-55. (in Chinese)
[8] LIU Li-ping, ZHE Xue-sen. Compaction standard and application of earth-rock mixture in mountain area[J]. China Civil Engineering Journal, 2006, 39(2): 122-125. (in Chinese)
[9] LIU Hui-xun, LI Qing-shan, DING Hong-yan. Transient hammer-impacting detection technology of highway engineering[J]. China Journal of Highway and Transport, 2008, 21(4): 37-42. (in Chinese)
[10] LI Shao-bo, ZHANG Xian-min, ZHI Sheng-ying. Detecting subgrade compactness by direct shear wave method[J]. Journal of Highway and Transportation Research and Development, 2008, 25(3): 32-37. (in Chinese)
[11] VAGHELA J G, STOKOE K H. Small-strain dynamic properties of dry sand from the free-free resonant column[R]. Geotechnical Engineering Report GT95-1. Geotechnical Engineering Center, University of Texas at Austin, 1995.
[12] CAI Jia-xing, ZHANG Zhi-jie. Analysis and evaluation on application effect of density measurement of rock fill object by additive mass method[J]. Journal of Yangtze River Scientific Research Institute, 2008, 25(5): 186-190. (in Chinese)
[13] ZHANG Min, HUANG Ming. Test and analysis of additive mass method in new airport of Kunming[J]. Architecture Technology, 2009, 40(5): 445-448. (in Chinese)
[14] IVANSSON S, KARASALO I. Computation of model wave numbers using an adaptive wingding-number integral method with error control[J]. J Sound Vib, 1993, 161: 173-180.
[15] KIM D S, PARK H C. Evaluation of ground densification using SASW and resonant column tests[J]. Canadian Geotechnical Journal, 1999, 36(2): 291-299.
[16] MALISCHEWSKY P G. Some special solutions of Rayleigh’s equation and the reflections of body waves at a free surface[J]. Geophysical International, 2000, 39(2): 155-160.
[17] MASSARSCH K R, FELLENIUS B H. Vibratory compaction of coarse-grained soils[J]. Canadian Geotechnical Journal, 2001, 38(3): 695-709.
[18] CAO Wen-gui, HU Tian-hao, LUO Hong. Discussion on a new technique for detecting compactness of soil-rock mixture roadbed[J]. Journal of Hunan University: Natural Science, 2008, 35(2): 22-26. (in Chinese)
[19] XU Zhi-lun. Elastic mechanics[M]. Beijing: Higher Education Press, 2003. (in Chinese)
(Edited by CHEN Wei-ping)
Foundation item: Project (50708033) supported by the National Natural Science Foundation of China; Project (20070532067) supported by Doctoral Foundation of Ministry of Education of China
Received date: 2009-01-26; Accepted date: 2009-05-25
Corresponding author: YANG Ming-hui, Associated professor; Tel: +86-731-88821654; E-mail:yamih@126.com