Trans. Nonferrous Met. Soc. China 23(2013) 1689-1693
Production of in situ TiB2+TiC/Fe composite coating from precursor containing B4C-TiO2-Al powders by laser cladding
Xin-hong WANG1, Xiang-ning PAN2, Bao-shuai DU3, Shuai LI1
1. Key Laboratory for Liquid-Solid Structural Evolution and Processing of Materials (Ministry of Education), Shandong University, Ji’nan 250061, China;
2. School of Mechanical, Electrical and Information Engineering, Shandong University at Weihai, Weihai 264209, China;
3. Shandong Electric Power Research Institute, Ji’nan 250002, China
Received 13 April 2012; accepted 10 July 2012
Abstract: Steel matrix composites reinforced with TiB2+TiC reinforcement were produced by laser melting mixture of B4C, TiO2, Al and Fe-based self-melting alloy powders. The results show that TiB2+TiC ceramic particles were synthesized from the reaction of B4C, TiO2 and Al alloys during laser cladding process. The reinforcement particles were evenly distributed in the coating. TiB2 grew in rectangle shape, but TiC presented irregular cubic shape. The wear resistance of the coating was higher than that of the substrate of 1045 steel; meanwhile, the friction coefficient of the coating was considerably lower than that of 1045 steel.
Key words: TiB2-TiC; laser cladding; microstructure; wear properties
1 Introduction
It is well know that TiB2 and TiC have low friction coefficient, high elastic modulus, high hardness, high melting temperature and low theoretical density [1]. They have received significant attention as reinforcement in metal matrix composites (MMCs). Recent years, multiple ceramic particles reinforced MMCs, such as TiB2-TiC/Fe [2,3], TiB2-TiC/Ni [4], Al2O3-TiB2/Al [5], Al2O3-TiC/Fe [6], have been developed. These efforts have resulted in the combination of properties that are not available in a single ceramic material. Conventional production method, such as high-temperature sintering, often requires adding the ceramic reinforcement phases into the metal matrix directly. However, it often leads to poor wetting behavior between ceramic phase and metal matrix, resulting in segregation of reinforcing phases as well. To overcome the disadvantage of the directly adding ceramic phase technique, a novel processing route has evolved, where the reinforcement can grow in situ in the metal matrix utilizing either the exothermic nature of reactions or the crystallization during solidification.
Recently, laser in situ synthesis technology has been widely used in fabricating ceramic reinforced metal matrix surface composite coating because of its rapid cooling rate and high efficiency. In comparison with other technologies, highly confined and controlled local heat generated by the laser beam can yield the in situ-fabrication of a ceramic composite coating with metallurgical bonding to the substrate without destroying the properties of the substrate. The key feature of this technology is the localized melting and solidification in shallow depth within a short time, meanwhile the substrate material remains cool and serves as an infinite heat sink. Thus, a wide variety of chemical and microstructural states cannot be destroyed owing to the rapid heating and cooling process. Laser in situ synthesis technology has been used for fabricating ceramic phase of TiB2, TiC or TiB2-TiC reinforced metal matrix composite coatings [7-9]. However, there are few published literatures of laser in-situ synthesis technology on the fabrication of TiB2-TiC ceramic via melting mixture of B4C, TiO2 and aluminum powders.
In the present investigation, an attempt is made to synthesize TiB2-TiC multiple ceramic reinforcement by laser beam melting of the precursor of B4C, TiO2 and Al blended powders on AISI 1045 steel substrate.
2 Experimental
The powder mixture of the coating alloy was prepared from Al (99% purity), TiO2 (anatase, 99% purity), and B4C (90% purity, balance B2O3 and C). To improve the formation of the coating, Fe-based self-melting alloys and CaF2 (98.5% purity) were added to the raw clad powders. The sizes of TiO2, Al and B4C particles were estimated to be 36, 10 and 20 μm, respectively. The normal mole ratio of TiO2, B4C and Al corresponds to the following reaction:
B4C+3TiO2+4Al=2TiB2+TiC+2Al2O3 (1)
In order to achieve a homogeneous distribution, the raw powders were mixed in a blender for 1 h under protection of argon gas. The precursor was mixed with organic binder and then pre-placed on a steel plate to a thickness of approximately 1.2 mm for the laser cladding process.
The AISI 1045 steel plates with dimensions of 100 mm×100 mm×10 mm were used as the substrate. They were polished with emery paper and washed with acetone subsequently in order to provide a clean surface.
A continuous CO2 laser with a maximum power of 5000 W was employed to perform the laser cladding process. Multimode laser beam was delivered using optic reflective mirror and defocused to a beam diameter about 3 mm. The laser cladding parameters used in the experiment were laser power 2000 W, scan speed 5 mm/s and protective gas 10 L/min (argon). Multi-track cladding with 33% overlap ratio was made to create the coating.
All specimens were etched with a solution of 3% nital. The microstructure and compositions were analyzed on a SU-70 field emission scanning electron microscope (FESEM) and transmission electron microscope (TEM). The chemical compositions were identified by energy dispersive spectroscopy (EDS) coupled with FESEM. A type of D/Max-2500PC X-ray diffractometer (XRD) with Cu Kα radiation operated at 60 kV and 40 mA was used to analyze the phase structure. Dry sliding wear tests were carried out on an M-2000 block-on-ring wear tester at room temperature applied test load of 49 N, relative sliding speed of 0.84 m/s and a sliding distance of 1260 m, and average value of wear volume loss was taken from three measurements.
3 Results and discussion
3.1 Microstructure and phase structure
The typical XRD pattern of the coating is shown in Fig. 1. It is clearly indicated from Fig. 1 that the phases of the coating are mainly TiB2, TiC, a-Fe(Ni,Cr), γ-Fe(Ni,Cr) and M7C3, providing that TiB2 and TiC reinforcements are obtained through the metallurgical reaction. However, there are no any Al2O3 peaks in the XRD pattern because the reaction of Al and TiO2 to form Al2O3 primarily occurs at about 1000 °C [10]. The density of the Al2O3 (r=3.8 g/cm3) is less than that of iron melting, which leads to Al2O3 particles to float upward the melting pool and form the slag. In addition, while the appropriate mole ratio of B4C, TiO2 and Al is used, the coating is in the absence of brittle phases, such as Fe2B, FeB, FeTi and Fe2Ti. The avoidance of such brittle phase is important to the cracking-resistance of laser-clad coating.
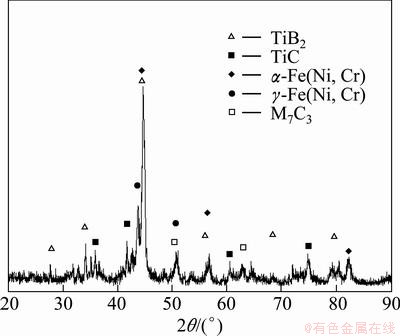
Fig. 1 XRD pattern of laser synthesized composite coating
Figure 2(a) shows the typical macro-morphology of the composite coating. Overlapped laser track with a relatively smooth surface can be observed. It reveals that the coating demonstrates enough toughness, which can be proved by the fact that no cracks are shown in the coating. In addition, a sound metallurgical joint between the coating and substrate is also observed (shown in Fig. 2(b)). The region adjacent to the coating experiences thermal cycling during the laser processing and the heat affected zone forms.
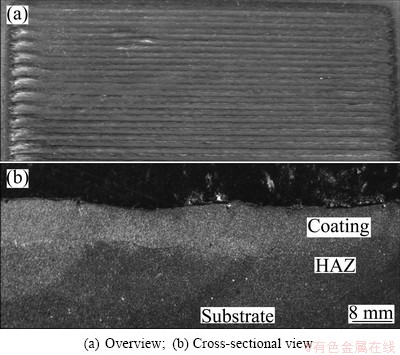
Fig. 2 Macroscopic view of composite coating
Figure 3 shows the SEM image of the composite coating and the EDS results. It can be seen that the coating presents a microstructure essentially consisting of reinforcing particles dispersed in a metal matrix. The morphology of the reinforcements can be approximately categorized into two kinds: deep grey with rectangular shape and light grey with irregular cubic shape. EDS results of the reinforcement (marked as A and B) are shown in Figs. 3(b) and (c), respectively, which indicate that there is titanium concentration in rectangular and irregular cubic phase, and boron mainly concentrates in the rectangular phase; however, carbon mainly concentrates in the irregular cubic phase. Moreover, both of them are lack of iron element. Thus, combing the XRD result, it can be deduced that those deep gray reinforcements with rectangular shape are TiB2, while light grey reinforcements with irregular cubic shape are TiC particles. In addition, it is important to note that most of TiC particles cling to TiB2, implying that TiB2 particles are formed before TiC.
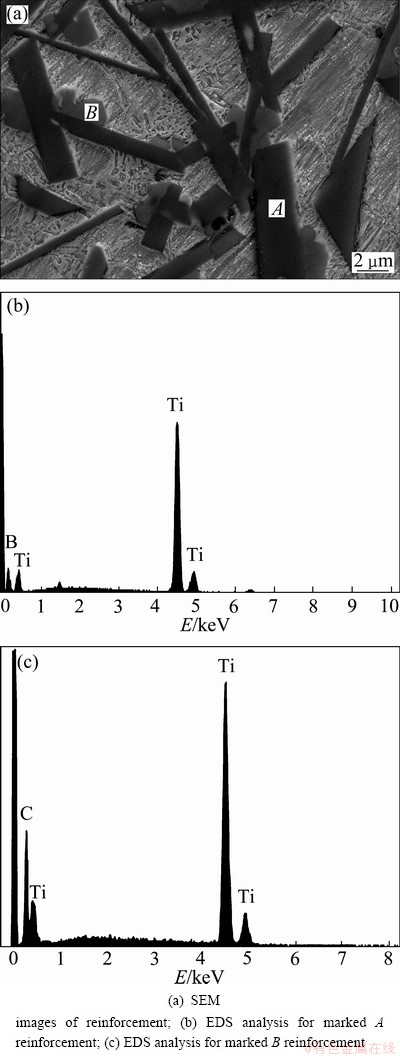
Fig. 3 Microstructure of laser synthesized coating
Figure 4 shows the curves of the Gibbs free energy vs temperature of the above reactions [11-15]. It can be seen that the reaction of TiO2 and Al has the lowest Gibbs free energy, implying that Al2O3 is firstly to form, and then synthesize TiB2 and TiC. Moreover, TiB2 has the highest melting point, therefore it is likely to separate first from the melt during the cooling process of the laser cladding. In other words, TiB2 can be formed via the nucleation-growth mechanism. The TiB2 blocky morphology can be rationalized based on its C32 crystal structure. The TiB2 crystal is formed by trigonal prisms closely packed in different directions, with growth along the [0001] and <
> directions involving alternating Ti and B layers in both cases [16,17]. Therefore, crystal of TiB2 growing unconstrained from the melt tends to form the blocky morphology. On the other hand, TiC is known to have a rock-salt NaCl-type structure that Ti atoms array the face centered cubic (FCC) sublattice while carbon atoms occupy the free sites of the octahedral configuration forming another FCC sublattice [18], therefore, its growth mechanism is well known to be the lateral growth [19]. That is, the <001> direction is a fast growing direction for an FCC crystal structure during solidification. In theory, the fast growing rate in this direction leads to the formation of the main dendrite arms of TiC under slow cooling solidification conditions. However, in the present study, TiC shows irregular cubic shape. This may attribute to high cooling rate of the laser processing, leading to the rapid rate of solidification. Moreover, growth of TiC particles is restricted by the rectangle TiB2. Therefore, the growth of dendrite TiC is restrained.
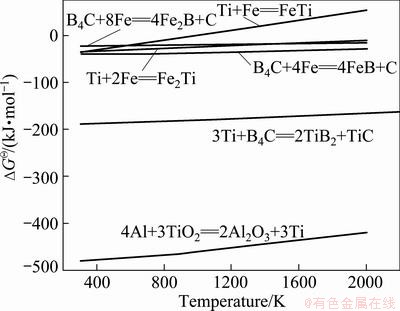
Fig. 4 Curves of Gibbs free energy vs temperature for reaction
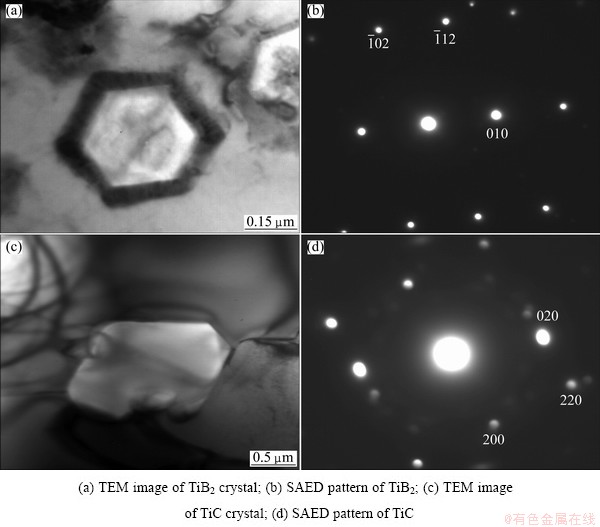
Fig. 5 TEM images and SAED patterns of TiB2 and TiC
TEM images of the TiB2 and TiC in the coating are illustrated in Figs. 5(a) and (c), respectively. The corresponding selected area electron diffraction (SAED) patterns of the TiB2 and TiC crystal are shown in Figs. 5(b) and (d), respectively. It further proves that TiB2 and TiC have been in-situ synthesized in the composite coating. Straight and clean interface between reinforce- ments and ferrite matrix without the presence of reaction product was observed. Such an interface is typical for the in situ synthesized composites, and it is also beneficial for the improvement of wear resistance.
3.2 Wear properties of coatings
The block-on-ring wear test results as cumulative mass loss over a period of 25 min are shown in Fig. 6.
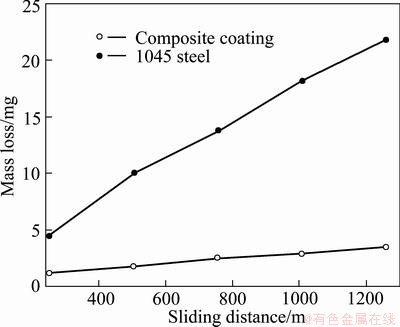
Fig. 6 Wear mass loss of substrate and composite coating as function of sliding distance
It can be seen that the composite coating indicates much superior wear resistance to the uncoated substrate, implying that a significantly enhanced wear resistance is caused by the in situ TiB2 and TiC particles in the composite coatings.
Figure 7 indicates the variations of friction coefficient for the substrate and laser clad coating as a function of sliding distance under dry sliding wear test conditions. The friction coefficient of the coating (oscillated around 0.45) is considerably lower than that of substrate (oscillated around 0.65). This may be attributed to the higher hardness of the composite resulting in lower real area of contact, therefore, a smaller number of junctions which require less energy to get sheared during sliding as compared with the substrate; on the other hand, TiB2 and TiC ceramics have lower friction coefficients (TiB2:0.45; TiC: 0.25), and reinforcements reduce the contact area of the matrix with the counterface, leading to minimizing the smearing effect of the Fe-based coating on the counterface surface. Hence, the composite coating may enhance the hardness and wear resistance without evidently increasing the friction coefficient of the coatings.
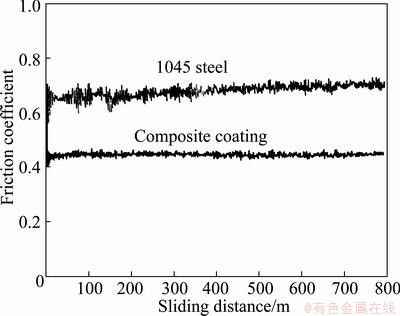
Fig. 7 Variations of friction coefficient for 1045 steel substrate and composite coating as function of sliding distance
4 Conclusions
1) Using TiO2, B4C and Al powders as precursor, TiB2-TiC reinforced iron matrix laser clad composite coating on medium carbon steel substrate was obtained.
2) Phase constituents of the coating are mainly a-Fe, TiB2 and TiC. The microstructure of the composite coating consists of rectangle TiB2 and irregular cubic TiC particles distributed uniformly in the a-Fe. TiB2 presents deep grey, but TiC shows light grey. Moreover, TiC clings to TiB2 particles growth.
3) In situ TiB2-TiC/Fe composite coating has an excellent wear resistance and a lower friction coefficient under dry sliding condition because of the presence of TiB2 and TiC reinforcement in the composite coating.
References
[1] NAVAS C, CONDE A, FERNANDEZ B J, ZUBIRI F, DAMBORENEA J D. Laser coatings to improve wear resistance of mould steel [J]. Surf Coat Technol, 2005, 194: 136-142.
[2] VALLAURI D,
A I C, CHRYSANTHOU A, TiC-TiB2 composites: A review of phase relationships, processing and properties [J]. J Euro Ceramic Soc, 2008, 28: 1697-1713.
[3] DU B S, PAITAL S R, DAHOTRE N B. Phase constituents and microstructure of laser synthesized TiB2-TiC reinforced composite coating on steel [J]. Scr Mater, 2008, 59: 1147-1150.
[4] IU Jing-jing, LIU Zong-de. An experimental study on synthesizing TiC-TiB2-Ni composite coating using electro-thermal explosion ultra-high speed spraying method [J]. Mater Lett, 2010, 64: 684-687.
[5] CHATTERJEE S, SHARIFF S M, PADMANABHAM G, DUTTA M J, ROY C A. Study on the effect of laser post-treatment on the properties of nano structured Al2O3-TiB2-TiN based coatings developed by combined SHS and laser surface alloying [J]. Surf Coat Technol, 2010, 205: 131-138.
[6] MASANTA M, GANESH P, KAUL R, NATH A K, CHOUDHURY A R. Development of a hard nano-structured multi-component ceramic coating by laser cladding [J]. Mater Sci Eng A, 2009, 508: 134-140.
[7] EMAMIAN A, CORBIN S F, KHAJEPOUR A. Effect of laser cladding process parameters on clad quality and in situ formed microstructure of Fe-TiC composite coatings [J]. Surf Coat Technol, 2010, 205: 2007-2015.
[8] WANG X H, QU S Y, DU B S, ZOU Z D. In situ synthesized TiC particles reinforced Fe-based composite coating produced by laser cladding [J]. Mater Sci Technol, 2009, 25: 388-392.
[9] OCYLOK S, WEISHEIT A, KELBASSA I. Increased wear and oxidation resistance of titanium aluminum alloys by laser cladding [J]. Adv Mater Res, 2011, 278: 515-520.
[10] FENG C F, FRDYEN L. In-situ synthesis of Al2O3 and TiB2 particulate mixture reinforced aluminum matrix composites [J]. Scr Mater, 1997, 36: 467-473.
[11] ZHU He-guo, WANG Heng-zhi, E Liang-qi, CHEN Shi, WU Shen- qing. Formation of composites fabricated by exothermic dispersion reaction in Al-TiO2-B2O3 system [J]. Transactions of Nonferrous Metals Society of China, 2007, 17: 590-594.
[12] ZOU B L, SHEN P, CAO X Q, JIANG Q C. Reaction path of the synthesis of α-Al2O3-TiC-TiB2 in an Al-TiO2-B4C system [J]. Int J Refract Met Hard Mater, 2011, 29: 591-595.
[13] SHEN P, ZOU B L, JIN S B, JIANG Q C. Reaction mechanism in self-propagating high temperature synthesis of TiC-TiB2/Al composites from an Al-Ti-B4C system [J]. Mater Sci Eng A, 2007, 454: 300-309.
[14] LIANG Ying-jiao, CHE Yin-chang. Handbook of inorganic thermo-chemistry data [M]. Shenyang: Northeast University Press, 1991. (in Chinese).
[15] KNACKE K O, HESSELMANN K. Thermo-chemical properties of inorganic substances [M]. 2nd ed. New York: Springer-Verlag, 1991.
[16] ABDEL H A A, HAMAR S T, HAMAR R. Crystal morphology of the compound TiB2 [J]. J Crys Grow, 1985, 71: 744-750.
[17] HYMAN M E, MCCULLOUGH C, VALENCIA J J, LEVI C G, MEHERABIAN R. Microstructure evolution in TiAl alloys with B additions: Conventional solidification [J]. Metall Trans, 1989, 20: 1847-1859.
[18] SUN G, BHATTACHARYA S, DINDA G P, DASGUPTA A. Microstructure evolution during laser-aided direct metal deposition of alloy tool steel [J]. Scr Mater, 2011, 64: 454-457.
[19] DO N A M, OCELIK V, IERARDI M C F, DE H J T M. Microstructure of reaction zone in WCp/duplex stainless steels matrix composites processing by laser melt injection [J]. Surf Coat Technol, 2008, 202: 2113- 2120.
激光熔覆B4C-TiO2-Al粉末制备原位TiB2+TiC/Fe复合涂层
王新洪1,潘向宁2,杜宝帅3,李 帅1
1. 山东大学 材料液-固态结构演变与加工教育部重点实验室,济南 250061;
2. 山东大学(威海分校) 机电与信息工程学院,威海 264209;
3. 山东电力研究院,济南 250002
摘 要:采用B4C、 TiO2、Al以及Fe基自熔合金粉末为前驱体,利用激光熔覆技术在钢基体上制备TiB2+TiC颗粒增强Fe基复合涂层。结果表明,激光熔覆过程通过B4C-TiO2-Al反应生成了均匀分布于基体的TiB2-TiC复合陶瓷相。TiB2 颗粒呈长条块状,TiC以不规则形状分布于基体中。涂层具有比基材1045钢更好的耐磨性能,但涂层的摩擦因数小。
关键词:TiB2-TiC;激光熔覆;显微组织;耐磨性能
(Edited by Hua YANG)
Foundation item: Project (2011GGX10327) supported by Shandong Development Program of China
Corresponding author: Xin-hong WANG; Tel: +86-531-88392208; E-mail: xinhongwang@sdu.edu.cn
DOI: 10.1016/S1003-6326(13)62649-7