
Wear and corrosion properties of laser
cladded Cu47Ti34Zr11Ni8/SiC amorphous composite coatings on AZ91D magnesium alloy
HUANG Kai-jin(黄开金)1, 2, 3, 4, YAN Li(闫 里)1,WANG Cun-shan(王存山)3,
XIE Chang-sheng(谢长生)1,ZHOU Chang-rong (周昌荣)4
1. State Key Laboratory of Materials Processing and Die & Mould Technology,
Huazhong University of Science and Technology, Wuhan 430074, China;
2. State Key Laboratory of Advanced Welding Production Technology,
Harbin Institute of Technology, Harbin 150001, China;
3. State Key Laboratory of Materials Modification by Laser, Ion and Electron Beams,
Dalian University of Technology, Dalian 116024, China;
4. Guangxi Key Laboratory of Information Materials,
Guilin University of Electronic Technology, Guilin 541004, China
Received 23 September 2009; accepted 30 January 2010
Abstract: To improve the wear and corrosion properties of AZ91D magnesium alloys, Cu-based amorphous composite coatings were fabricated on AZ91D magnesium alloy by laser cladding using mixed powders of Cu47Ti34Zr11Ni8 and SiC. The wear and corrosion behaviours of the coatings were investigated. The wear resistance of the coatings was evaluated under dry sliding wear condition at room temperature. The corrosion resistance of the coatings was tested in 3.5% (mass fraction) NaCl solution. The coatings exhibit excellent wear resistance due to the recombined action of amorphous phase and different intermetallic compounds. The main wear mechanisms of the coatings and the AZ91D sample are different. The former is abrasive wear and the latter is adhesive wear. The coatings compared with AZ91D magnesium alloy also exhibit good corrosion resistance because of the presence of the amorphous phase in the coatings.
Key words: magnesium alloy; AZ91D alloy; laser cladding; wear; corrosion; amorphous phase
1 Introduction
Magnesium alloys have many advantages, such as light weight, high specific strength, high specific stiffness, excellent damping characteristics, large thermal conductivity, good electromagnetic shielding characteristics, and good machinability, and are widely used in many fields such as automotive, communication, electron and aerospace. However, low surface hardness and poor corrosion resistance hinder their widespread use in many applications. To improve their wear resistance and corrosion resistance, many surface modification techniques such as electrochemical plating, conversion coating, anodizing, gas-phase deposition process and organic coating have been used. However, all of them have their disadvantages. For example, electrochemical plating concerns waste disposal; chromate conversion coatings represent a serious environmental risk due to the presence of leachable hexavalent chromium in the coatings; the coatings produced by anodizing are porous ceramic-like and need further sealing; gas-phase coating processes are difficult to uniformly coat complex shapes and the coatings contain holes or deep recesses; and organic coatings are inadequate without pretreatment and there are some environmental concerns with the use of solvent borne organic coatings. So, further research is still required to develop better, simpler, and cheaper coating technologies.
With the development of laser technology, non-traditional surface engineering techniques, such as laser surface modification technique, including laser surface re-melting[1-2], laser surface alloying[3-4], and laser cladding[5-15] have attracted growing interest in recent years for improving the wear and corrosion properties of magnesium alloys. For example, Zr-based amorphous composite coatings on pure magnesium substrate fabricated by laser cladding showed the possibility of potential application, because of the combination of good corrosion resistance of amorphous phase and high wear resistance of nanocrystalline and/or microcrystalline[7-8]. However, the monolithic amorphous alloys themselves face the problem of low ductility. The typical plastic strain to failure for monolithic amorphous alloy is normally less than 2% in compression and virtually zero in tension[16-17]. This is mainly due to the ease with which highly localized shear bands are formed. The fact is that, although the local plastic strain in a single shear band can be quite large, only a few shear bands are active before failure. In order to improve the mechanical properties of the monolithic amorphous alloys, ceramic reinforcements are introduced into the glassy matrix to synthesize particle reinforced amorphous matrix composite. These composites show enhanced plastic strain compared with the monolithic amorphous alloys[18-19]. As to the laser cladding of particle reinforced amorphous matrix composite coatings on magnesium substrates, few publications can be found except for YUE and SU[10] and HUANG et al[13].
The Cu-based amorphous composite coatings have successfully been fabricated on AZ91D magnesium alloy by laser cladding using mixed powders of Cu47Ti34Zr11Ni8 (Coating A) or Cu47Ti34Zr11Ni8+ 20%SiC (Coating B)[13]. In the present work, the wear and corrosion behaviours of the coatings are given in details.
2 Experimental
The detailed experimental procedure was given in Ref.[13].
The dry sliding wear resistance of the laser-cladded coatings was evaluated using a block-on-ring dry sliding wear tester at room temperature. The cladded specimens for the wear test were cube blocks with dimensions of 10 mm×10 mm×10 mm, which were slid against a rotating ring of hardened bearing steel AISI52100 (Fe-1.0C-1.5Cr-0.25Si-3.0Mn, mass fraction, %) with a hardness of HRC 60 (HV0.1 700). The test load used was 98 N. The relative sliding speed was 0.418 7 m/s. The wear test cycle lasted for 75 min and the corresponding total wear sliding distance was 1 884 m. The as-received AZ91D magnesium alloy was selected as the reference material for all wear tests. Each test was repeated three times. The wear mass loss was measured using an electronic balance (Bartorius BS110) with an accuracy of 0.1 mg.
The potentiodynamic polarization test was employed to evaluate the corrosion behaviour of the coating. The test was conducted in 3.5% (mass fraction) NaCl solution using saturated calomel electrode (SCE) as reference electrode and platinum as counter electrode. Polarization was carried out from -1.8 to 2 V at a scanning rate of 1 mV/s. Before the polarization test, the specimens were kept in the solution for 200 s.
The surface morphologies of the worn specimens and the corrosive specimens were examined by a Quanta 200 scanning electron microscope (SEM) with an energy dispersive X-ray spectroscopy (EDS). A micro-hardness tester (MICROMET 3) using a test load of 0.98 N and a load-dwelling time of 15 s was employed to measure the microhardness of the coating.
3 Results and discussion
3.1 Wear behaviours
Fig.1 shows the mass loss of the different coatings and the untreated AZ91D sample under dry testing condition. The mass loss decreases according to the sequence of the untreated AZ91D specimen, the laser cladded specimen of coating A and the laser cladded specimen of coating B. In other words, the wear-resistance of the coatings A and B is obviously better than that of AZ91D substrate because the mass loss of AZ91D substrate is about 2.9 times and 4.2 times larger than that of the coating A and the coating B, respectively. The wear-resistance results of different samples are consistent with the corresponding microhardnesses of different specimens (Fig.2), and the higher the microhardness, the better the wear resistance.
The Cu-based coatings mainly consist of amorphous phase and different intermetallic compounds[13]. The microstructure provides the coating with excellent wear resistance under dry wear condition, as indicated in
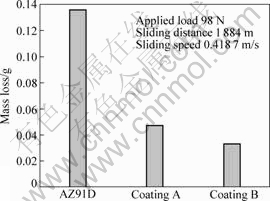
Fig.1 Mass loss of different specimens
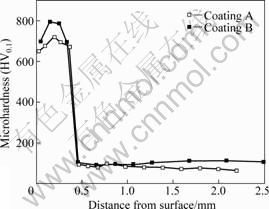
Fig.2 Microhardness of different coatings
Fig.3. As shown in Fig.3, both the worn surfaces of the untreated and laser-cladded specimens exhibit plastic deformation zones and have a plough-shaped appearance. In other words, the worn surfaces are characterized by fairly long continuous grooves and plastic deformation. However, the untreated specimen AZ91D suffers from severe adhesive wear. This is evident by the feature of heavy plastic deformation (Fig.3(a)) and the large mass wear rate (Table 1). On the contrary, the laser-cladded specimens only suffer relatively mild adhesive wear, but experience severe abrasive wear. This is evident by the relatively mild plastic deformation but with many small particles of wear debris found at the surface (Figs.3(b) and (c)) and small mass wear rate (Table 1). The results of the EDS analysis show that these particles are mainly composed of iron oxides (Table 2). Apparently, the above characteristics of the worn surface are related to the surface microhardness of different specimens.
It is indicated that under the condition of room- temperature dry sliding wear test, the surface of the untreated specimen AZ91D would first adhere to the surface of the hardened AISI52100 steel ring and then smear off because of its low hardness of the untreated specimen (Fig.3(a)). On the other hand, the worn surfaces of the laser-cladded coatings are covered with wear debris particles including iron oxide (Figs.3(b), (c) and Table 2). Such results are not observed on the untreated samples. It should be pointed out that the morphologies of the worn surfaces of the two kinds of laser-cladded coatings are similar (Figs.3(b) and (c)).
In normal sliding tests, there is a material-to- material contact, followed by welding or fusing of the contacting asperities. When sliding continues, the

Fig.3 SEM morphologies of worn surface (Wear time 75 min, test load 98 N): (a) Untreated AZ91D; (b) Coating A; (c) Coating B
Table 1 Mass wear rate of different specimens (μg/s)

Table 2 EDS results of worn surface in Fig.3 (mass fraction, %)

asperities of the weaker material may shear off and transfer to the opposite surface[20]. In the present work, in the case of the untreated specimen AZ91D, the hardened AISI52100 steel ring, whose main constituent is Fe, shears the soft magnesium phase off, as a result, small content of iron is deposited on the worn surface (Table 2). On the contrary, the microhardness of the coatings (Fig.2) is higher than that of the hardened AISI52100 steel ring (HV0.1 700), and the material from the ring is sheared off, as a result, large content of iron is deposited on the worn surface (Table 2). At the same time, the amorphous phase and different intermetallic compounds[13] would be broken up by the dry sliding action and smeared along the surface.
In conclusion, according to the morphology of the worn surfaces (Fig.3) and the results of EDS (Table 2), the dominant type of wear mechanism of the relatively soft untreated AZ91D, whose microhardness is lower than that of the hardened AISI52100 steel (Fig.2), is considered to be adhesive wear process. On the other hand, the type of wear mechanism of the laser-cladded specimens, whose microhardness is higher than that of the hardened AISI52100 steel (Fig.2), is dominated by abrasive wear process. Nevertheless, oxidation and friction wear might also be involved in the cases of the untreated AZ91D sample and the laser-claded specimens.
3.2 Corrosion behaviours
The potentiodynamic polarization plots of the different coatings are shown in Fig.4. Table 3 lists the corrosion parameters of different specimens in 3.5% NaCl solution. The results show that the different coatings are superior to the untreated AZ91D substrate in corrosion properties. For example, the corresponding corrosion potentials (φcorr) of coatings A and B are -1.294 1 V and -1.370 7 V, which are 171.6 mV and 95 mV more positive than the corrosion potential of the untreated AZ91D substrate, respectively. The open-circuit corrosion current density (Jcorr) of the untreated AZ91D substrate is about 1.12 times and 1.82 times that of coating A and coating B, respectively. The corresponding polarized resistances (Rp) of coatings A and B are about 1.12 times and 1.82 times that of the untreated AZ91D substrate, respectively. The corrosion rate (RC) of the untreated AZ91D substrate is about 2.07 times and 3.35 times that of coating A and coating B, respectively. Fig.5 shows the SEM morphologies of corrosive surfaces of different specimens.
For AZ91D magnesium alloy, the mass fraction of Mg is about 90% (Table 2). Mg is a very active metal, the equilibrium potential of Mg is -2.37 V, and the equilibrium potential in conventional media is also very low. Moreover, the oxide film of magnesium is generally loose and porous; therefore, AZ91D magnesium alloy

Fig.4 Potentiodynamic polarization curves of different specimens in 3.5% NaCl solution
Table 3 Corrosion parameters of different specimens in 3.5% NaCl solution
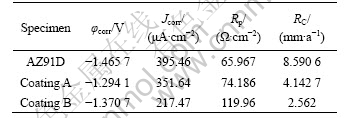
normally has fairly poor corrosion resistance. The electrochemical corrosion of AZ91D magnesium alloy is mainly the process of releasing hydrogen with its quick dissolution. So, the corrosion of AZ91D magnesium alloy is severe (Table 3 and Fig.5(a)).
The relatively better corrosion properties of coatings A and B compared with the untreated AZ91D substrate are related to the presence of excellent corrosion-resistance of amorphous phase in the coatings[13]. Of course, microgalvanic corrosion also exists in the coating due to different intermetallic compounds, and a small quantity of corrosion products are kept on the corrosive surface (Figs.5(b) and (c)).
In addition, the reason of the relatively weak corrosion properties of coating A compared with coating B (Fig.4 and Table 2) is considered to be due to the different volume fractions of the amorphous phases in the coatings[13]. Apparently, the higher the volume fraction of amorphous phase in the coating B, the smaller the corrosion rate because of the excellent corrosion-resistance of amorphous phase.
4 Conclusions
1) Under the dry sliding wear condition, the wear resistance of Cu-based amorphous composite coating is considerably higher than that of the untreated AZ91D magnesium alloy.
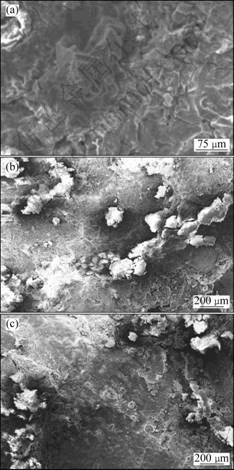
Fig.5 SEM morphologies of corrosive surfaces: (a) Untreated AZ91D; (b) Coating A; (c) Coating B
2) The main wear mechanism for the untreated AZ91D specimens is dominant by adhesive wear, while for the Cu-based amorphous composite coating specimens, it is the abrasive wear.
3) The corrosion resistance of Cu-based amorphous composite coating in 3.5% NaCl solution is considerably better than that of the untreated AZ91D magnesium alloy, due to the presence of amorphous phase in the coatings with excellent corrosion-resistance.
References
[1] GHAZANFAR A, LI L, UZMA G, LIU Z. Effect of high power diode laser surface melting on wear resistance of magnesium alloys [J]. Wear, 2006, 260(1/2): 175-180.
[2] MAJUMDAR J D, GALUN R, MORDIKE B L, MANNA I. Effect of laser surface melting on corrosion and wear resistance of a commercial magnesium alloy [J]. Materials Science and Engineering A, 2003, 361(1/2): 119-129.
[3] MAJUMDAR J D, CHANDRA B R, MORDIKE B L, GALUN R, MANNA I. Laser surface engineering of a magnesium alloy with Al+Al2O3 [J]. Surface and Coatings Technology, 2004, 179(2/3): 297-305.
[4] GALUN R, WEISHEIT A, MORDIKE B L. Improving the surface properties of magnesium by laser alloying [J]. Corrosion Reviews, 1998, 16(1/2): 53-74.
[5] YANG Y, HU J D, WANG H Y, LIU S Y, LI Y X, GUO Z X. Laser (Nd:YAG) cladding of AZ91D magnesium alloys with Al+Ti+C nanopowders [J]. Lasers in Engineering, 2006, 16(1/2): 9-17.
[6] BAKKAR A, GALUN R, NEUBERT V. Microstructural characterization and corrosion behaviour of laser cladded Al-12Si alloy onto magnesium AS41/carbon fibre composite [J]. Materials Science and Technology, 2006, 22(3): 353-362.
[7] YUE T M, SU Y P, YANG H O. Laser cladding of Zr65Al7.5Ni10Cu17.5 amorphous alloy on magnesium [J]. Materials Letters, 2007, 61(1): 209-212.
[8] YUE T M, SU Y P. Laser multi-layer cladding of Zr65Al7.5Ni10Cu17.5 amorphous alloy on magnesium substrates [J]. Journal of Materials Science, 2007, 42(15): 6153-6160.
[9] YUE T M, LI T. Laser cladding of Ni/Cu/Al functionally graded coating on magnesium substrate [J]. Surface and Coatings Technology, 2008, 202(13): 3043-3049.
[10] YUE T M, SU Y P. Laser cladding of SiC reinforced Zr65Al7.5Ni10Cu17.5 amorphous coating on magnesium substrate [J]. Applied Surface Science, 2008, 255(5): 1692-1698.
[11] VOLOVITCH P, MASSE J E, FABRE A, BARRALLIER L, SAIKALY W. Microstructure and corrosion resistance of magnesium alloy ZE41 with laser surface cladding by Al-Si powder [J]. Surface and Coatings Technology, 2008, 202(20): 4901-4914.
[12] YANG Y, WU H. Improving the wear resistance of AZ91D magnesium alloys by laser cladding with Al-Si powders [J]. Materials Letters, 2009, 63(1): 19-21.
[13] HUANG Kai-jin, XIE Chang-sheng, YUE T M. Microstructure of Cu-based amorphous composite coatings on AZ91D magnesium alloy by laser cladding [J]. Journal of Materials Science and Technology, 2009, 25(4): 492-498.
[14] LIU Hong-bin, WANG Cun-shan, GAO Ya-li, CHI Li-na. Laser cladding amorphous composite coating of Cu-Zr-Al on magnesium alloy surface [J]. Chinese Journal of Lasers, 2006, 33(5): 709-713. (in Chinese).
[15] GAO Ya-li, WANG Cun-shan, XIONG Dang-sheng, LIU Hong-bin. Influence of laser technology parameters on preparation of amorphous coatings on magnesium alloy [J]. Transactions of Materials and Heat Treatment, 2009, 30(4): 146-150, 155. (in Chinese)
[16] FAN C, INOUE A. Ductility of bulk nanocrystalline composites and metallic glasses at room temperature [J]. Applied Physics Letters, 2000, 77(1): 46-48.
[17] INOUE A, FAN C, SAIDA J, ZHANG T. High-strength Zr-based bulk amorphous alloys containing nanocrystalline and nanoquasicrystalline particles [J]. Science and Technology of Advanced Materials, 2000, 1(2): 73-86.
[18] KATO H, HIRANO T, MATSUO A, KAWAMURA Y, INOUE A. High strength and good ductility of Zr55Al10Ni5Cu30 bulk glass containing ZrC particles [J]. Scripta Materialia, 2000, 43(6): 503-507.
[19] KATO H, INOUE A. Synthesis and mechanical properties of bulk amorphous Zr-Al-Ni-Cu alloys containing ZrC particles [J]. Materials Transactions JIM, 1997, 38(9): 793-800.
[20] KELLY J, NAGARATHNAM K, MAZUMDER J. Laser cladding of cast aluminum-silicon alloys for improved dry sliding wear resistance [J]. Journal of Laser Applications, 1998, 10(2): 45-54.
(Edited by YANG Bing)
Foundation item: Project(AWPT08-10) supported by the Open Fund of the State Key Laboratory of Advanced Welding Production Technology in Harbin Institute of Technology, China; Project(mmlab0706) supported by the Open Fund of the State Key Laboratory of Materials Modification by Laser, Ion and Electron Beams in Dalian University of University, China; Project(0710908-05-K) supported by the Research Funds of the Guangxi Key Laboratory of Information Materials in Guilin University of Electronic Technology, China
Corresponding author: HUANG Kai-jin; Tel: +86-13607150408; Fax: +86-27-87543776; E-mail:huangkaijin@yahoo.com.cn
DOI: 10.1016/S1003-6326(09)60303-4