DOI: 10.11817/j.ysxb.1004.0609.2020-39394
基于Image-J图像法和电化学法的微弧氧化涂层孔隙率评价
崔学军1, 2,宁闯明1,宋世杰1,王 淋1,杨若豪1
(1. 四川轻化工大学 材料科学与工程学院,自贡 643000;
2. 中国科学院 海洋新材料与应用技术重点实验室,宁波 315201)
摘 要:为精确量化和评价微弧氧化(MAO)涂层的孔隙率,在硅酸盐电解液中通过恒压MAO方法于AZ31B镁合金表面制备氧化物涂层。利用线性极化、电化学交流阻抗谱(EIS)和Tafel曲线分别计算涂层的极化电阻并考察其腐蚀防护性能,重点采用Image-J图像法和两种极化电阻比值法评价了涂层孔隙率,提出了适合MAO涂层孔隙率的评价方法。结果表明:当氧化电压由260 V升至290 V时,MAO样品的自腐蚀电流密度由2.8 μA/cm2增加至5.6 μA/cm2。结合线性极化电阻和EIS拟合结果,证实涂层腐蚀防护性能随氧化电压的升高而降低。同时,Image-J图像法计算的表面孔隙率由10.14%增加至11.48%,线性极化电阻计算的通孔孔隙率由3.51%增加至7.08%,表明涂层腐蚀防护性能与其孔隙率呈负相关,即随孔隙率增加而降低。与电化学交流阻抗谱或Tafel曲线所得极化电阻比值法相比,简单的线性极化电阻比值法更适合量化MAO涂层的通孔孔隙率,而Image-J图像法适合通过MAO涂层的表面SEM像量化表面孔隙率及孔径大小的分布情况。
关键词:镁合金;微弧氧化;孔隙率;极化电阻;Image-J
文章编号:1004-0609(2020)-05-1101-09 中图分类号:TG174.4 文献标志码:A
微弧氧化(MAO)技术,因其涂层结构可控及优异的防腐抗磨性能,已成为镁合金表面防护的重要手段之一[1-2]。然而,已有研究[3]证实MAO涂层中存在约20%(孔隙率)的亚微米级(10~100 nm)通孔。AGHION等[4]研究表明,在含有Mg(OH)2的NaCl溶液中,空隙率14%~19%的泡沫镁的腐蚀速率为4~10 mg/(cm2·d),是铸造镁腐蚀速率的10倍。其他研究[5-7]也表明,MAO涂层中的通孔容易为腐蚀介质提供通道,除了纯涂层内部的化学和电化学腐蚀外,还将发生MAO层/镁合金基体腐蚀微电池,从而加速涂层剥离和基体腐蚀。可见微孔的尺寸、数量及分布制约着MAO涂层的腐蚀防护性能。因此,涂层孔隙的测定及调控一直是科研和技术人员提高涂层性能的重要途径[3-8]。
涂层孔隙率的测定方法有物理法(包括密度法、水银法、氦比重法、BET吸附测量、金相法、扫描电镜法以及Image-J图像法等)[3-4, 9]、化学法(中性和醋酸盐雾、二氧化硫暴露、指示剂法)[5, 9-11]、电化学法(Tafel曲线外推法、线性极化法和交流阻抗谱法)[7, 9-10]。化学法通过长时间的化学反应,腐蚀产物可能会堵塞微孔而导致孔隙率误差较大,重现性差,很难实现孔隙率量化。相比较而言,Image-J图像法[7, 10-12]和电化学法[13-15]检测更直观、可量化,在研究文献中使用较多。Image-J图像法孔隙率,是通过清晰的涂层表面形貌分析计算而得到的表面孔隙区域所占分析区域的百分比[16]。因此,图像法得到的孔隙率实际上是一种表面孔隙率。相反,电化学法孔隙率是利用涂层对腐蚀介质的阻挡(极化电阻)程度来计算的,一些文献[10, 17]认为电化学法计算的是涂层通孔的孔隙率。DIETZEL等[5]研究表明,在酸性介质中,MAO镁合金的耐蚀性主要依赖于基体的化学组成;而在中性介质中就完全取决于MAO涂层孔隙率。孔隙率越低,涂层就越致密,对腐蚀介质的阻挡程度就越高。因此,电化学法计算的孔隙率更准确地反应了涂层的致密程度。然而,电化学法计算孔隙率通常需要与Tafel曲线外推法、线性极化法和交流阻抗谱法等[7, 9-10]结合,该方法虽然在PVD涂层[14, 17]、磷化膜[18]中得到了详细的研究,但在MAO涂层孔隙率计算方面的研究不足,缺乏对各方法之间孔隙率的比较及普适性研究。
基于本课题组之前的研究工作[19-20],深入研究MAO涂层孔隙率评价及其与涂层性能的关联性,对揭示MAO涂层形成机理及结构-性能调控具有重要的指导意义。本文利用极化曲线和电化学交流阻抗谱研究两种电压条件下MAO涂层对镁合金AZ31B的腐蚀防护性能,重点通过Image-J图像法和电化学法计算涂层孔隙率,分析MAO涂层孔隙率与涂层腐蚀防护性能的关系,讨论涂层孔隙率测试方法之间的差异并提出适合MAO涂层孔隙率计算的方法,以期为MAO涂层孔隙率评价、控制及性能优化提供理论依据。
1 实验
选用轧制AZ31B(规格:30 mm×25 mm×2 mm)镁合金为基体,其化学组成(质量分数,%)为:2.94 Al,0.9 Zn,0.23 Mn,0.01 Si,0.01 Cu,0.00053 Ni,0.003 Fe,余量Mg。依次对试样进行碱洗除油→超声清洗→吹干→打磨(240#~1200# SiC砂纸)→丙酮超声→水洗→吹干处理,保鲜膜包裹待用。
MAO涂层制备设备及工艺见文献[19],本论文中仅在恒压工艺条件下制备260 V和290 V两种涂层样品(分别简称为260M和290M样品),对其进行结构、耐蚀性及孔隙率分析。
采用扫描电子显微镜(SEM,VEGA 3 SBU,Tescan,Czechia)表征涂层表面形貌,加速电压为10~15 kV。并利用Image-J图像法[16]分析MAO涂层表面形貌,计算孔径尺寸、分布及孔隙率(孔隙面积占总面积的比例)。
采用电化学工作站(Solartron 1287+1260)于室温条件下测试样品在3.5% NaCl(质量分数)溶液中的电化学行为。饱和甘汞电极(SCE)为参比电极,3 cm2的Pt片为辅助电极,待测试样为工作电极,其有效暴露面积为1 cm2。测量前,先将样品在NaCl 溶液中浸泡1 h,然后对其进行开路电位测试。若开路电位波动小于10 mV时,则分别进行线性极化、电化学交流阻抗谱(EIS)和Tafel曲线测试。线性极化的电位扫描范围为相对开路电位±0.02 V,Tafel曲线测量的电位扫描范围为相对于开路电位±0.25 V,扫描速率为0.167 mV/s。电化学交流阻抗谱测量的激励信号扰动幅值为相对开路电位±5 mV,频率范围为10 mHz~100 kHz。为确保测量结果的准确性和可重复性,每个样品取不同位置三点测量,结果相同或相近时取平均值作为最终测量结果。测试结束后,利用Cview 3.3c和ZSimpWin 3.21软件拟合电化学相关参数。Tafel曲线外推法即对极化曲线上相对开路电位±(60~120) mV的直线段拟合求出电化学参数。
MAO涂层本身是一种电化学惰性层,其阻值远大于镁合金基体的。因此,当MAO涂层用于镁合金基体的腐蚀防护时,涂层的孔隙率(P)可由式(1)计算[14]:
(1)
式中:Rps为空白基体的极化电阻;Rpc为涂层样品的极化电阻。
此外,当涂层为惰性层时,依据MATTHES等[21]提出的孔隙率计算公式,涂层的孔隙率也可由式(2)计算[7, 15, 22]:
(2)
式中:Rps为空白基体的极化电阻;Rpc为涂层样品的极化电阻;△φcorr为涂层样品与空白基体自腐蚀电位之差;ba为空白基体阳极Tafel斜率。
2 结果与讨论
2.1 SEM像及Image-J图像
图1所示为不同电压下所得MAO涂层样品表面形貌及表面孔隙分布。MAO涂层表面(见图1(a)、(c)、(e)、(g))存在很多“火山口”形貌特征的微孔,这是典型的MAO涂层特征,是伴随MAO过程的火花放电现象而产生的[3]。随着MAO电压的升高,涂层表面微孔尺寸应该会增大[19],但低倍表面形貌(见图1(a)和(e))及表面微孔分布图(见图1(b)和(f))中的区别并不明显。若比较涂层的高倍表面形貌(见图1(c)和(g)),可观察到260M样品表面大尺寸微孔数量较多,但这种比较结果不能量化。
表1所列为通过Image-J软件分析得出的260M和290M涂层样品在不同放大倍数下各尺寸区域微孔的分布数据。可见两种电压下所得涂层表面微孔尺寸分布及孔隙率存在显著差别。对低倍MAO涂层表面形貌分析,发现Feret孔径≤0.7 μm时,290M样品表面孔隙数高于260M样品的;在0.7~2.1 μm之间,两种涂层的表面孔隙数比较接近;而当孔径>2.1 μm时,290M样品表面微孔数量逐渐增多,最终孔隙数量高于260M样品的;而且,260M样品表面微孔的最大孔径为4.424 μm,小于290M样品表面微孔的最大孔径(5.825 μm)。通过孔隙率比较,也证实了290M样品表面孔隙率高于260M样品的,表明260 V电压所得MAO涂层具有更好的腐蚀防护性能,这与之前的研究结果[19]一致。
当放大倍数增大时,MAO涂层表面可以看到孔隙中又有小孔隙结构(见图1(c)和(g))。利用Image-J软件分析时,无法从形貌图(见图1(d)和(h))中观察到这些细微的小孔。通过对微孔粒径分布处理(见表1)可知,Feret孔径>0.7 μm时,两种电压所得涂层的孔径数量相差不大;而微孔Feret孔径≤0.7 μm时,290M样品的孔径数量是260M样品的1.6倍(低倍时是1.2倍)。这表明对孔径分析时,是把大孔内的小孔计算在内的。比较Image-J软件对低/高倍数SEM像孔隙分析,两种放大倍数下都能反映出相同的孔隙率变化趋势,但从高倍SEM像观察的区域面积小,不能反映整个样品表面微孔孔径大小及其分布情况(见表1),260M样品的最大孔隙直径是3.369 μm,大于290M样品的2.915 μm,进而容易误导由孔径大小判断的涂层腐蚀防护能力。
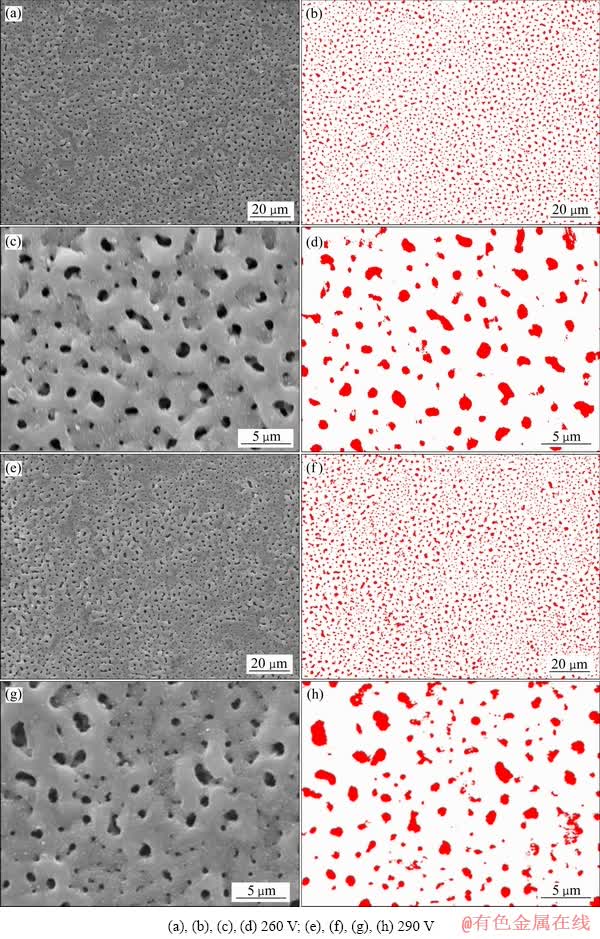
图1 不同电压下所得MAO涂层样品表面形貌及表面孔隙分布
Fig. 1 Surface morphologies((a), (c), (e), (g)), and pore distributions((b), (d), (f), (h)) of MAO coated AZ31B Mg alloy
表1 MAO涂层表面孔的孔径分布及孔隙率
Table 1 Distribution and porosity of surface pore of MAO coated Mg alloy
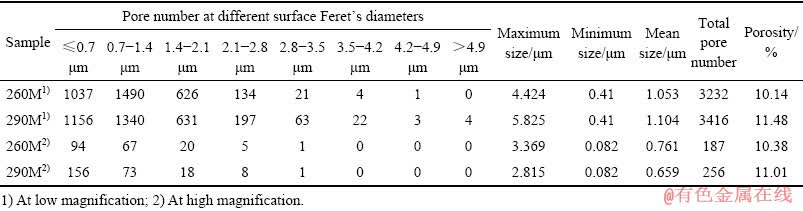
2.2 电化学及孔隙率
2.2.1 极化曲线
图2所示为镁合金及MAO涂层样品在3.5%NaCl溶液中的Tafel曲线。由图2可见,MAO涂层样品的Jcorr低于空白基体的,且260M样品的Jcorr最低。根据图2的Tafel曲线外推法(±(60~120) V)拟合结果(见表2),MAO涂层样品的Jcorr低于空白基体的近两个数量级;而260M样品的Jcorr最低,其值为2.8 μA/cm2,表明此电压下制备的MAO涂层具有最佳的腐蚀防护性能,与3.1MAO表面孔隙率的分析结果一致。
此外,极化电阻(Rp)也是腐蚀电化学中一个重要的动力学参数[23]。根据斯特恩(Stern)公式,Rp与Jcorr呈反比,Jcorr愈小,极化电阻就愈大,这与表2中的Tafel曲线外推法拟合结果一致。但严格来说,真实的极化电阻是极化曲线在Δφ=0处切线的斜率,而使用传统的Tafel曲线外推法拟合时,必须对腐蚀体系进行强极化。由于极化值大、扫描速率慢、时间长会导致测量过程中对腐蚀体系影响和干扰大,故由此所得的阻值误差较大。线性极化通过在Δφ很小的“直线区”测量,可以测得真实极化电阻的近似值 —— 线性极化电阻(
)。由图3可见,空白镁合金及涂层样品在20 mV的微极化区内具有很好的线性关系,通过拟合并计算其斜率,可得到真实极化电阻的近似值(
),如表2所示。MAO涂层样品的
大于空白基体的,且260M样品具有最大的阻值,从而进一步证实260M样品具有最佳的耐蚀性能。同时可发现
的值小于
的,这个差值应源于强极化测量过程中对腐蚀体系的影响和干扰。因此,微极化区的测量结果更具可靠性。
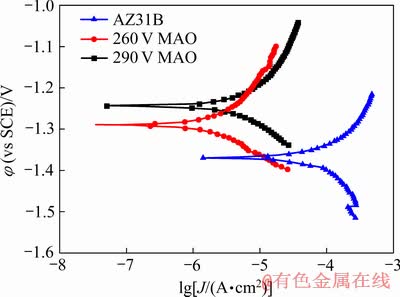
图2 镁合金及MAO涂层样品在3.5% NaCl溶液中的Tafel曲线
Fig. 2 Tafel curves of bare and MAO coated Mg alloys in 3.5% NaCl solution
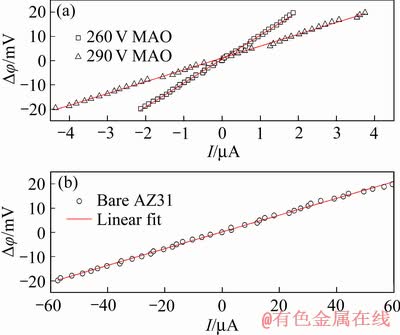
图3 镁合金及MAO涂层样品在3.5%NaCl溶液中的线性极化曲线
Fig. 3 Linear polarization curves of bare and MAO coated Mg alloys in 3.5% NaCl solution
表2 空白镁合金及MAO涂层样品的Tafel曲线拟合参数和孔隙率
Table 2 Fitting parameters of Tafel curves of bare and MAO coated Mg alloys and porosity
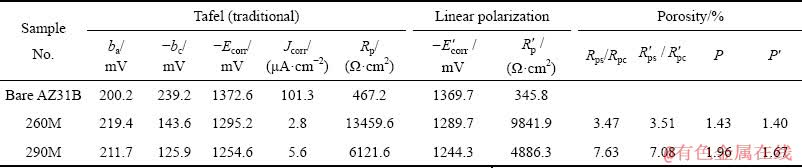
2.2.2 交流阻抗谱
图4所示为镁合金及MAO涂层样品在3.5%NaCl溶液中的Nyquist图。显然,Nyquist图呈现出高频单容抗弧和低频感抗弧响应,可采用图5所示的等效电路描述。Rs为溶液电阻,Q为MAO涂层等效的双电层电容,R1为涂层电阻,L为电感,RL为与电感相对应的阻值。拟合曲线如图4中实线所示,拟合数据如表3所示。随着氧化电压的增加,容抗弧半径增大,涂层电阻增大,涂层腐蚀防护性能增加,这与极化曲线的分析结果一致。一般而言,涂层表面孔隙率越高,表面积就越大,从而双电层电容值就大[20]。由表3可见,260M样品的Q值低于290M样品的,进而表明290 V电压所得MAO涂层具有较高的孔隙率。
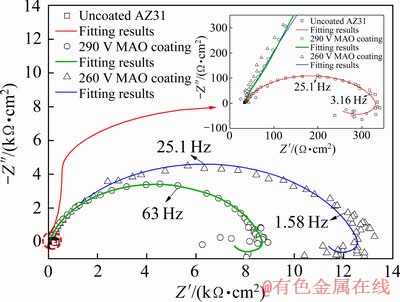
图4 镁合金及MAO涂层样品在3.5% NaCl溶液中的Nyquist图
Fig. 4 Nyquist diagram of bare and MAO coated Mg alloys in 3.5% NaCl solution
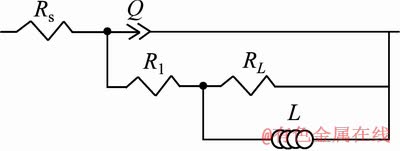
图5 EIS等效电路
Fig. 5 Equivalent circuit of EIS plot
2.2.3 电化学孔隙率
极化电阻可分别通过Tafel曲线直线外推法(强极化)和线性极化法(微极化)拟合计算得到,由式(1)计算得到的涂层孔隙率如表2所示。260M样品在微极化区测量所得孔隙率为3.51%,强极化区测量所得的孔隙率为3.47%,与微极化区测量值的误差为-1.14%;同理,290M样品在微极化区测量所得孔隙率为7.08%,强极化区测量所得孔隙率为7.63%,与微极化区测量值的误差为+7.77%。误差绝对值小于10%,表明不同方法拟合所得极化电阻计算出的孔隙率差别较小。但无论哪种条件下计算的极化电阻,其孔隙率均表现出相同的变化趋势,即290M样品的孔隙率约是260M样品的2倍,这也与二者的腐蚀电流密度的倍数关系一致。孔隙率低,涂层致密性好,具有更优的腐蚀防护性能。
式(2)进一步完善了式(1)的不足,引入了涂层样品与空白基体的极化值Δφ和空白基体的阳极Tafel斜 率[17, 21]。如表2所示,260M样品经微极化和强极化所得的孔隙率分别为1.40%和1.43%;而290M样品经微极化和强极化所得的孔隙率分别为1.67%和1.96%,略高于260M样品的(不到2倍)。显然,由式(2)所得涂层孔隙率值低于式(1)所得的,但仍可证实260M样品具有良好的耐蚀性能。
此外,涂层样品的极化电阻可以通过EIS拟合得到[18, 24],即Rp=Rs+R1+RL,然后根据图2中Tafel曲线外推法获得的△φcorr、ba数据,再利用式(1)或式(2)计算涂层的孔隙率。如表4所示,由式(1)和(2)所得的涂层孔隙率均低于Tafel曲线和线性极化曲线拟合所得的计算值。并且,由式(1)计算的孔隙率仍保持相同的变化趋势,即260 V电压所得涂层具有最低的孔隙率。然而,根据式(2)计算时,尽管260M样品具有较高的极化电阻,但其孔隙率计算结果表明290M样品具有最低的孔隙率,这与Image-J图像法及Tafel曲线、线性极化曲线拟合所得的结果相反。这主要与式(2)中引入与涂层表面状态相关的自腐蚀电位有关。
表3 图4中Nyquist图拟合结果
Table 3 Fitting results of Nyquist plots from Fig. 4
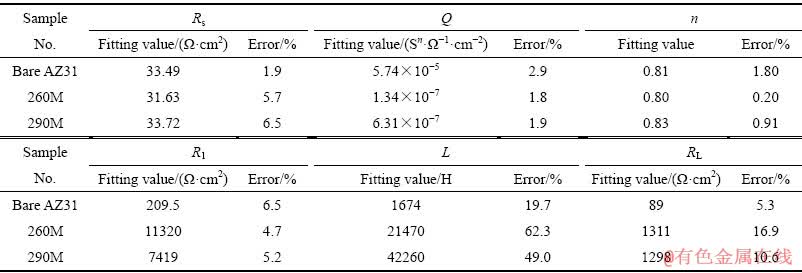
表4 EIS拟合Rp所得MAO涂层样品孔隙率
Table 4 Porosity of MAO coated Mg alloys from EIS Fitting parameters
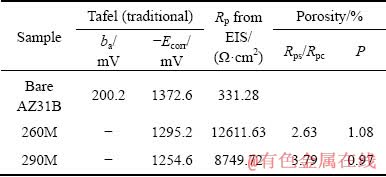
2.3 讨论
2.3.1 Image-J图像法孔隙率分析原则
Image-J图像法可以清晰地获得涂层表面孔隙分布情况(见图1),但这种分布图不能量化孔隙,很难区分出孔隙率比较接近的形貌图。然而,图像法的优势就是能对形貌图进一步分析,不但可以获得表面孔隙率,而且还能获得表面微孔尺寸分布情况(见表1)。因此,利用图像法可有效获得涂层表面孔隙率及孔径大小的分布情况,为进一步比较涂层性能提供有力的数据支撑[16]。此外,由表1分析可见,260M和290M样品在不同放大倍数下的微观形貌所计算的孔隙率略有差异,但两种涂层在高倍形貌下的孔隙率变化规律与低倍形貌的一致。可见,不同倍数形貌图对表面孔隙率的变化趋势影响不大。
但进一步比较孔径尺寸分布及数量情况,发现孔径≥3.5 μm时,低倍形貌的分析结果是260M样品的孔隙数量低于290M样品的孔隙数,但高倍形貌图却未检测到孔隙。而且,260M样品在低倍和高倍下的最大孔径分别为4.424 μm和3.369 μm;而290M样品在低倍和高倍下的最大孔径分别为5.825 μm和2.815 μm。可见,同一样品在不同放大倍数下所得的孔径尺寸及分布不具有可比性。同时,通过比较也发现260M和290M样品在高倍时的最大孔径尺寸与低倍形貌的变化趋势不一致。导致这种情况的主要原因是MAO涂层的真实表面形貌具有三维几何形态,微观上孔隙的分布不具有均匀性。因此,利用图像法分析MAO涂层表面孔隙率,在清晰图片的前提下,对相同低倍数的形貌图可直接进行孔隙率及孔径分布的比较;但高倍数的形貌图只可进行孔隙率比较,不宜进行孔径分布及尺寸分析。
2.3.2 电化学法孔隙率评价方法
通过式(1),并利用Tafel曲线外推法、线性极化法以及电化学交流阻抗谱拟合计算空白基体及涂层样品的极化电阻,都可得到涂层的孔隙率。经计算,发现290M样品的孔隙率分别是7.63%、7.08%和3.79%,分别是260M样品的2.2倍、2.0倍和1.4倍,涂层孔隙率都呈现出随氧化电压升高而增大的趋势。当利用式(2)并结合以上电化学方法计算时,发现涂层的孔隙率都比较低,290M样品的孔隙率降低到了1.96%、1.67%和0.97,分别是260M样品的1.4倍、1.2倍和0.9倍。式(2)是在式(1)基础上引入了△φcorr和ba,并且二者的比值处于指数位置,其微小偏差便可引起孔隙率很大的变化,这可能是导致290M样品的EIS涂层孔隙率降低且与其他方法计算结果不一致的主要原因。
腐蚀电位是腐蚀过程作用的结果,并不是一个热力学参数,它可以判断腐蚀的倾向,但不能决定腐蚀的速度,即它与涂层的组成及表面状态有很大的关联性。而影响电极(涂层样品)电化学反应过程的关键速度控制步骤主要有荷电粒子穿越电极界面的放电过程和紧靠金属材料表面的腐蚀介质中的传质过程[23]。而对MAO涂层样品进行腐蚀电化学测试时,一般认为电极表面是均匀的,且不受电极表面的传质过程影响。因此,可认为MAO涂层样品腐蚀过程受控于荷电粒子穿越电极界面的放电过程,其主要的动力学参数是交换电流密度和Tafel斜率。交换电流密度反应的是电极反应的难易程度,而Tafel斜率反映的是改变双电层的电场强度对于反应速率的影响。由此推断在式(2)中引入与涂层表面状态相关的腐蚀电位,不适合计算MAO涂层的孔隙率。
此外,Tafel曲线外推法需要测试的涂层样品进入强极化区,其测量过程中对腐蚀体系影响和干扰大,且在Tafel线性区拟合过程中容易引入人为误差,将导致涂层孔隙率计算偏差较大。而EIS测试的频率范围宽,需要涂层样品长时间浸泡在腐蚀介质中,这可引起涂层腐蚀,孔径变大,从而导致测试初期涂层的孔隙率与测试结束后涂层孔隙率不一致[17]。并且,EIS数据拟合过程中各元件的选择及等效电路的判断也容易引入数值误差。若EIS拟合获得极化电阻后,利用式(2)计算,还需要通过Tafel曲线外推法获得△φcorr和ba,从而给孔隙率计算带来更多的不确定因素。
综上所述,既然影响MAO涂层样品腐蚀反应的关键动力学参数是交换电流密度和Tafel斜率,就可以通过极化电阻来计算涂层样品的孔隙率。因此,采用线性极化电阻并结合式(1),更能准确量化MAO涂层样品的通孔孔隙率。
2.3.3 Image-J图像法与电化学法孔隙率的适用性
如引言中所述,Image-J图像法孔隙率实际上是一种表面孔隙率;而电化学法计算的是涂层通孔的孔隙率。然而,MAO过程中总是从涂层相对薄弱的微观区域起弧,涂层先形成的放电通道(即微观孔隙)总是被新生成的氧化熔融物所覆盖,致使MAO涂层的孔隙并不直通,所以内部孔隙就比表面孔隙数少,那么通孔的孔隙率也就比表面孔隙率低[16]。所以文中由Image-J图像法计算所得孔隙率都高于电化学法的。
综上所述,Image-J图像法的优势是即可以获得表面孔隙率,也能获得表面孔尺寸分布情况;而电化学法却能准确量化涂层通孔孔隙率。但电化学法中,由于式(2)中引入了△φcorr和ba,在利用Tafel曲线、电化学交流阻抗谱计算时都将引入更多不确定性因素,如Tafel曲线强极化测量对腐蚀体系影响和干扰大、EIS长时间测试导致涂层腐蚀和孔径变大等,故不适合MAO涂层孔隙率评价。相反,通过线性极化、电化学交流阻抗谱、Tafel曲线计算极化电阻,再利用式(1)计算涂层孔隙率,可以判断不同工艺所得涂层腐蚀防护性能的变化趋势,其中,采用线性极化电阻计算涂层孔隙率,更能有效评价涂层的腐蚀防护性能。
3 结论
1) 随着氧化电压由260V增加至290V,线性极化、电化学交流阻抗谱和Tafel曲线分析表明微弧氧化涂层的腐蚀防护性能降低,与Image-J图像法孔隙率和简单的极化电阻比值法孔隙率增加趋势一致。
2) Image-J图像法能够通过清晰的MAO涂层表面SEM像计算表面孔隙率,且涂层表面孔隙分布不均匀时选取低倍形貌图亦能有效反映涂层孔隙率变化趋势及孔径大小的分布情况。
3) 简单的极化电阻比值法能够通过线性极化、电化学交流阻抗谱或Tafel曲线所得极化电阻计算MAO涂层的通孔孔隙率,且线性极化法所得极化电阻误差低,更能准确地反映MAO涂层样品的通孔孔隙率。
REFERENCES
[1] 崔学军, 平 静. 微弧氧化及其在镁合金腐蚀防护领域的研究进展[J]. 中国腐蚀与防护学报, 2018, 38(2): 87-104.
CUI Xue-jun, PING Jing. Research progress of micro-arc oxidation for corrosion protection of Mg alloys[J]. Journal of Chinese Society for Corrosion and Protection, 2018, 38(2): 87-104.
[2] BARATI DARBAND G H, ALIOFKHAZRAEI M, HAMGHALAM P, VALIZADE N. Plasma electrolytic oxidation of magnesium and its alloys: Mechanism, properties and application[J]. Journal of Magnesium and Alloys, 2017, 5(1): 74-132.
[3] CURRAN J A, CLYNE T W. Porosity in plasma electrolytic oxide coatings[J]. Acta Materialia, 2006, 54(7): 1985-1993.
[4] AGHION E, PEREZ Y. Effects of porosity on corrosion resistance of Mg alloy foam produced by powder metallurgy technology[J]. Materials Characterization, 2014, 96:78-83.
[5] DIETZEL W, KLAPKIV M, NYKYFORCHYN H, POSUVAILO V, BLAWERT C. Porosity and corrosion properties of electrolyte plasma coatings on magnesium alloys[J]. Materials Science, 2004, 40(5): 585-590.
[6] SONG G L, SHI Z. Corrosion mechanism and evaluation of anodized magnesium alloys[J]. Corrosion Science, 2014, 85(4): 126-140.
[7] CUI L Y, ZENG R C, GUAN S K, QI W C, ZHANG F, LI S Q, HAN E H. Degradation mechanism of micro-arc oxidation coatings on biodegradable Mg-Ca alloys: The influence of porosity[J]. Journal of Alloys & Compounds, 2017, 695: 2464-2476.
[8] JAYARAJ R K, MALARVIZHI S, BALASUBRAMANIAN V. Optimizing the micro-arc oxidation(MAO) parameters to attain coatings with minimum porosity and maximum hardness on the friction stir welded AA6061 aluminium alloy welds[J]. Defence Technology, 2017, 13(2): 111-117.
[9] NOTTER I M, GABE D R. Porosity of electrodeposited coatings: Its cause, nature, effect and management[J]. Corrosion Reviews, 1992, 10(3/4): 217-280.
[10] WALSH F C, LEON C P D, KERR C, COURT S, BARKER B D. Electrochemical characterisation of the porosity and corrosion resistance of electrochemically deposited metal coatings[J]. Surface & Coatings Technology, 2008, 202(21): 5092-5102.
[11] BLAWERT C, HEITMANN V, DIETZEL W, NYKYFORCHYN H M, KLAPKIV M D. Influence of electrolyte on corrosion properties of plasma electrolytic conversion coated magnesium alloys[J]. Surface & Coatings Technology, 2007, 201(21): 8709-8714.
[12] THIRUMALAIKUMARASAMY D, SHANMUGAM K, BALASUBRAMANIAN V. Establishing empirical relationships to predict porosity level and corrosion rate of atmospheric plasma-sprayed alumina coatings on AZ31B magnesium alloy[J]. Journal of Magnesium & Alloys, 2014, 2(2): 140-153.
[13] CREUS J, MAZILLE H, IDRISSI H. Porosity evaluation of protective coatings onto steel, through electrochemical techniques[J]. Surface & Coatings Technology, 2000, 130(2/3): 224-232.
[14] TATO W, LANDOLT D. Electrochemical determination of the porosity of single and duplex PVD coatings of titanium and titanium nitride on brass[J]. Journal of the Electrochemical Society, 1998, 145(12): 4173-4181.
[15] CAI J S, CAO F H, CHANG L R, ZHENG J J, ZHANG J Q, CAO C N. The preparation and corrosion behaviors of MAO coating on AZ91D with rare earth conversion precursor film[J]. Applied Surface Science, 2011, 257(8): 3804-3811.
[16] 吕维玲. AZ91D镁合金微弧氧化膜制备的调控及膜层表征方法的研究[D]. 兰州: 兰州理工大学, 2010.
Lü Wei-ling. Control principle of fabrication and characterization for micro-structure and properties of microarc oxidation coating on AZ91D magnesium alloys[D]. Lanzhou: Lanzhou University of Technology, 2010.
[17] AHN S H, LEE J H, KIM H G, KIM J G. A study on the quantitative determination of through-coating porosity in PVD-grown coatings[J]. Applied Surface Science, 2004, 233(1/4): 105-114.
[18] LINS V D F C, REIS G F D A, ARAUJO C R D, MATENCIO T. Electrochemical impedance spectroscopy and linear polarization applied to evaluation of porosity of phosphate conversion coatings on electrogalvanized steels[J]. Applied Surface Science, 2006, 253(5): 2875-2884.
[19] 崔学军, 王 荣, 魏劲松, 白成波, 林修洲. 电参数对AZ31B 镁合金微弧氧化膜微观形貌及耐蚀性的影响[J]. 中国腐蚀与防护学报, 2014, 34(6): 495-501.
CUI Xue-jun, WANG Rong, WEI Jing-song, BAI Cheng-bo, LIN Xiu-zhou. Effect of electrical parameters on micromorphology and corrosion resistance of micro-arc oxidation coating on AZ31B Mg alloy[J]. Journal of Chinese Society for Corrosion & Protection, 2014, 34(6): 495-501.
[20] CUI X J, LIN X Z, LIU C H, YANG R S, ZHENG X W, GONG M. Fabrication and corrosion resistance of a hydrophobic micro-arc oxidation coating on AZ31 Mg alloy[J]. Corrosion Science, 2015, 90: 402-412.
[21] MATTHES B, BROSZEIT E, AROMAA J, RONKAINEN H, HANNULA S P, LEYLAND A, MATTHEWS A. Corrosion performance of some titanium-based hard coatings[J]. Surface & Coatings Technology, 1991, 49(1/3): 489-495.
[22] LIU C, BI Q, LEYLAND A, MATTHEWS A. An electrochemical impedance spectroscopy study of the corrosion behaviour of PVD coated steels in 0.5 N NaCl aqueous solution: Part Ⅱ: EIS interpretation of corrosion behaviour[J]. Corrosion Science, 2003, 45(6): 1257-1273.
[23] 曹楚南. 腐蚀电化学原理[M]. 北京: 化学工业出版社, 2008: 27-157.
CAO Chu-nan. Principle of electrochemistry of corrosion[M]. Beijing: Chemical Industry Press, 2008: 27-1137.
[24] ELSENER B, ROTA A, BOHNI H. Impedance study on the corrosion of PVD and CVD titanium nitride coatings[J]. Materials Science Forum, 1991, 44/45(1): 29-38.
Porosity evaluation of micro-arc oxidation coating through Image-J and electrochemical methods
CUI Xue-jun1, 2, NING Chuang-ming1, SONG Shi-jie1, WANG Lin1, YANG Ruo-hao1
(1. School of Materials Science and Engineering, Sichuan University of Science and Engineering, Zigong 643000, China;
2. Key Laboratory of Marine Materials and Related Technologies, Ningbo Institute of Materials Technology and Engineering, Chinese Academy of Sciences, Ningbo 315201, China)
Abstract: To accurately determine and evaluate the porosity of micro-arc oxidation (MAO) coating, an MAO coating was fabricated on AZ31B Mg alloy via a constant voltage mode in a Na2SiO3 base aqueous solution. The polarization resistance and anti-corrosion property of the coatings were investigated by linear polarization resistance, electrochemical impedance spectroscopy(EIS) and Tafel polarization curve measurements, respectively. The focus was on the calculation and evaluation of the porosity by Image-J and two optimized polarization resistance ratio methods, and presenting an assessment method for the porosity of MAO coatings. The corrosion current density (Jcorr) of the MAO coated Mg alloy increases from 2.8 μA/cm2 to 5.6 μA/cm2 with the oxidation voltage increasing from 260 V to 290 V. Combined with the results of linear polarization resistance and EIS fitting, the corrosion protection performance of the coating decreases with increasing the oxidation voltage. Additionally, the surface porosity calculated by Image-J method increases from 10.14% to 11.48%, and the through-hole porosity calculated by linear polarization resistance method increases from 3.51% to 7.08%, implying that the anti-corrosion of the coating is negatively correlated with its porosity, i.e. it decreases with the increase of porosity. Among several methods for polarization resistance and porosity assessment methods, the linear polarization resistance measurement is more suitable for determining the through-hole porosity of the MAO coating, while the Image-J method can be used to quantify surface porosity, the distribution of pore size by the SEM image of an MAO coating.
Key words: magnesium alloy; micro-arc oxidation; porosity; polarization resistance; Image-J
Foundation item: Project(2016JZ0032) supported by the Science and Technology Planning Project of Sichuan Province, China; Project(2018Z01) supported by the Key Laboratory of Marine Materials and Related Technologies, Ningbo Institute of Materials Technology and Engineering, China; Project (201810622001) supported by the Students Innovation Training Planning of Chinese Academy of Sciences
Received date: 2019-05-02; Accepted date: 2019-10-28
Corresponding author: CUI Xue-jun; Tel: +86-831-5505620; E-mail: cxj_2046@163.com
(编辑 龙怀中)
基金项目:四川省科技支撑计划资助项目(2016JZ0032);中国科学院海洋新材料与应用技术重点实验室开放基金资助项目(2018Z01);大学生创新创业项目(201810622001)
收稿日期:2019-05-02;修订日期:2019-10-28
通信作者:崔学军,教授,博士;电话:0831-5505620; E-mail:cxj_2046@163.com