
Different grain refinement mechanisms of minor zirconium and
cerium in magnesium alloys
YU Kun(余琨), LI Wen-xian(黎文献), WANG Ri-chu(王日初), ZHANG Shi-Jun(张世军)
School of Materials Science and Engineering, Central South University, Changsha 410083, China
Received 15 July 2007; accepted 10 September 2007
Abstract: Zirconium and rare earth element cerium were added in magnesium and magnesium alloys to study their different grain refinement mechanisms. The results show that zirconium has an obvious refinement effect on the cast grain of magnesium and its alloys without the alloy element Al because the crystal structure of zirconium is the same as magnesium matrix, and the lattice parameters are close to magnesium. Zirconium can decrease the grain size of magnesium from 150 to 20 μm. The rare earth cerium also has a grain refinement effect on Mg and Mg-Al alloy. The cerium atoms tend to remain in the liquid rather than solidify with the solvent atoms magnesium at the solid-liquid interface. The liquid constitutional undercooling can provide a heterogeneous crystal nucleation. The grain is refined from 200 μm to 40-80 μm. These two elements have different grain refinement mechanism on Mg alloy. The mechanism of zirconium is that it acts as the nuclei of α-Mg. But the mechanism of cerium is that it increases the liquid constitutional undercooling that can provide a heterogeneous crystal nucleation for the alloy.
Key words: Mg alloy; grain refinement; zirconium; cerium
1 Introduction
Magnesium and magnesium alloys have a low density, good specific strengthen and excellent recycling capabilities so that they are attractive materials for using in a wide range of structural applications recently[1-2]. Controlling of the microstructures of magnesium alloy, especially the grain size, is a key factor for the use of magnesium because the uniform fine grains of magnesium matrix are preferred for improving both the cast and the wrought abilities of magnesium alloys[2]. Many researches have proved that the strength and ductility of the grain refinement magnesium alloys increase obviously. Therefore, finding an effective grain refining method and studying the grain refinement mechanism play an important role in producing high quality magnesium alloys[3] Some researches have been done on the grain refinement of magnesium alloys during the casting processing[2-4]. For example, rapid cooling and stirring of the solidifying melt effectively refine the grain structure in some high-pressure die casting processing. Superheating of the magnesium alloy melt, which was used extensively in the past for grain refining, is probably by the formation of heterogeneous nuclei FeCl3 precipitates[4-5]. And some intermetallic compounds such as Al4C3 probably act as grain nuclei to refine the magnesium alloys. Zirconium additions have been the dominating grain refining method for many magnesium alloys without Al due to the zirconium-rich precipitates acting as nuclei for the α-Mg grains[5-9]. In the present work, the rare earth element cerium also has an effective grain refinement on pure magnesium, Al-containing and non Al-containing magnesium alloys. The grain refinement mechanism of cerium was discussed and compared with that of zirconium.
2 Experimental
The experimental materials include pure magnesium, ZK60 (Mg-6%Zn) alloy and AZ31 (Mg-3%Al) alloy. The cerium or zirconium added in the experimental alloys was used for the Mg-20%Ce or Mg-35%Zr master alloys. Zirconium was added in magnesium at about 0.7% to ensure the refinement effect of zirconium precipitates act as the nuclei of α-Mg grains. But it can not be added in Mg-3%Al alloy because the reaction of aluminum and zirconium would create an Al3Zr phase that weakens the heterogeneous nuclei of zirconium in magnesium matrix. The cerium can be added in pure magnesium, Mg-6%Zn alloy and Mg-3%Al alloy with contents of 0.4%, 0.8% and 1.2%, respectively. The experimental alloys were melted by the protection of flux at 760-800 ℃ and were cast into iron mould with a diameter of 50 mm. And the microstructures of the ingot specimens were observed using Polyvar-MET optical microscope with a VSM2000 quantitative analysis system and KYKY2800 SEM.
3 Results and discussion
3.1 Grain refinement of zirconium in magnesium
The microstructures of zirconium added in pure magnesium are shown in Fig.1. It can be seen that the grain sizes of magnesium decrease greatly with the addition of zirconium, as shown in Figs.1(a) and (b). Zirconium can decrease the grain of Mg from about 150 μm to about 20 μm. Many globular nuclei exist in the center of α-Mg matrix. With a SEM analysis of the nuclei (Fig.2), it is found that such particles are pure zirconium. Zirconium has a hexagonal close-packed (HCP) crystal structure with the lattice parameters a=0.323 nm and c=0.514 nm. The crystal structure of zirconium is the same as magnesium and the lattice parameters are very close to those of magnesium (a=0.320 nm, c=0.520 nm)[10]. Furthermore, the Mg-Zr binary phase diagram is a peritectic reaction at the Mg-rich end. Therefore, zirconium is an optimal grain refinement to α-Mg matrix.
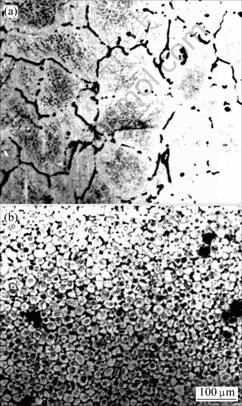
Fig.1 Microstructures showing effect of zirconium on grain refinement of magnesium: (a) Grains of magnesium without zirconium; (b) Grains of magnesium with zirconium

Fig.2 SEM image(a) of zirconium as nuclei in magnesium grains and EDS pattern(b)
3.2 Grain refinement of rare earth cerium in pure magnesium, ZK60 and AZ31 alloy
Compared with its effective grain refinement in pure magnesium, zirconium hardly has the refinement influence in Mg-Al system alloy, such as AZ31 alloy. But it is found that the rare earth cerium has the refinement effect. Different contents of cerium (0.4%, 0.8% and 1.2%) were added in pure magnesium and the morphologies of the ingots are shown in Fig.3. The pure magnesium has obvious pillar shape grains but they will change to refined equiaxed grains with the addition of of cerium[8].
According to the Mg-Ce phase diagram, Mg9Ce compound is formed with the addition of cerium in magnesium. Such Mg9Ce phase can not act as the nuclei of magnesium matrix because it is a eutectic compound and its crystal structure and lattice parameters are different from that of magnesium. So the cerium must have another grain refine mechanism. Based on the Mg-Ce phase diagram, the maximum solubility of cerium in Mg is less than 0.5%. So, the small amounts of cerium as the solute elements profoundly affect the solidification of alloy. On freezing, the cerium atoms tend to remain in the liquid rather than solidify with the solvent atoms magnesium at the solid-liquid interface. The freezing point of liquid decreases because the cerium atoms were enriched ahead of a freezing solid-liquid interface. With a DTA measure of the solidification behavior of alloy, the maximum freezing temperature decreases in the liquid is 37.1-51.5 K (Table 1). And the liquid constitutional undercooling can provide a heterogeneous crystal nucleation for the alloy[11-14].
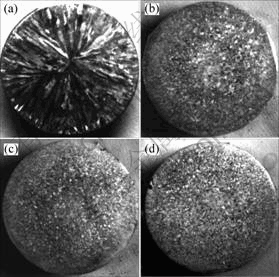
Fig.3 Grain refinement of cerium in pure magnesium: (a) Pure magnesium; (b) Mg-0.4%Ce; (c) Mg-0.8%Ce; (d) Mg- 1.2%Ce
The grain refinement of cerium in magnesium can also be shown in ZK60 alloy and AZ31 alloys. In ZK60 alloy, the grain size decreases from 120 to 50 μm with 1.2%Ce (Fig.4). And in AZ31 alloy, the grain size decreases from about 200 μm to 40-80 μm with 0.8%Ce (Fig.5). The grain mechanism of cerium in such two alloys is the same as in pure magnesium. But some new phases will form in magnesium alloy such as Al4Ce compound in AZ31 alloy and can enhance the super-cooling effect in these alloys[9, 15-16].
Table 1 Temperature difference of liquid and solid in super-cooling zone
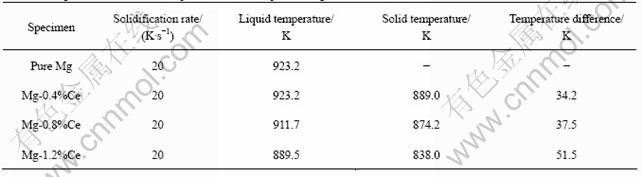
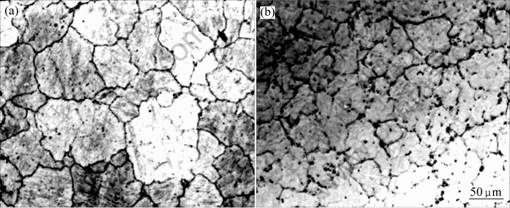
Fig.4 Grain refinement of cerium in Mg-6%Zn alloy: (a) Mg-6%Zn alloy; (b) Mg-6%Zn-0.8%Ce alloy
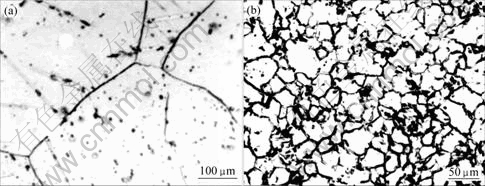
Fig.5 Grain refinement of cerium in Mg-3%Al alloy: (a) Mg-3%Al alloy; (b) Mg-3%Al-0.8%Ce alloy
4 Conclusion
1) Zirconium has an effective grain refinement on the cast grain of Magnesium and its alloys without the alloy element Al because its crystal structure is the same as magnesium matrix and the lattice parameters are close to magnesium.
2) 0.7% zirconium can decrease the grain of Mg from about 150 μm to about 20 μm. The rare earth cerium (0.4%-1.2%)also has a grain refinement effect on Mg, Mg-Al and Mg-Zn alloy because it can improve the super-cooling degree ahead the solid grain growth front and lead to the grain refining from 200 μm to 40-80 μm.
3) Zirconium and cerium has different grain refinement mechanisms so they should be added to different alloys.
References
[1] ASM International. Magnesium and magnesium alloy[M]. Ohio: Metal Park, 1999: 1-130.
[2] LI Wen-xian. Magnesium and magnesium alloy[M]. Changsha: Central South University Press, 2005: 338-380. (in Chinese)
[3] YU Kun, LI Wen-xian, WANG Ri-chu. Research, development and application of wrought magnesium alloys[J]. The Chinese Journal of Nonferrous Metals, 2003, 13(2): 277-282.(in Chinese)
[4] POLMEAR I J. Overview: magnesium alloys and applications[J]. Materials Science and Technology, 1994, 10: 1-16.
[5] MOTEGI T, SATO E, OBATA K. Cast structures and grain refinement of superheat-treated Mg-Al alloy[J]. Light Metals, 1994, 44(8): 427-430.
[6] TAKAMURA H, MIYASHITA T. Grain size refinement in Mg-Al-based alloy by hydrogen treatment[J]. Journal of Alloys and Compounds, 2003, 356/357: 804-808.
[7] KAMADO S, ASHIE T, YAMADA H, et al. Improvement of tensile properties of wrought magnesium alloys by grain refining[J]. Mater Sci Forum, 2000, 50/51: 65.
[8] BUSSIBA A, BEN ARTZY A, SHTECHMAN A. Grain refinement of AZ31 and ZK60 Mg alloys—towards superplasticity studies[J]. Mater Sci Eng A, 2001, 302: 56-62.
[9] JIAN Zeng-yuan, CHANG Fang-e, MA Wei-hong, et al. Nuclear and super-cooling of metal[J]. Science in China Series E, 2000, 30(1): 9. (in Chinese)
[10] RAVI KUMAR N V, BLANDIN J J, DESRAYAUD C. Grain refinement in AZ91 magnesium alloy during thermomechanical processing[J]. Mater Sci Eng A, 2003, 359: 150-157.
[11] DAHLE A K, ARNBERG. On the assumption of an additive effect of solute elements in dendrite growth[J] Mater Sci Eng A, 1997, 225: 38-46.
[12] LUO A. Magnesium castings for automotive applications[J]. JOM, 1995, 47: 28-31.
[13] MIYAZAKI T, SUGAMATA M. Structures and properties of rapidly solidified Mg-Ca based alloys[J]. Mater Sci Eng A, 1994, 182: 1410-1414.
[14] YAMASHITA T, KELLY P M, CAVALLARO P, HISA M. Effects of age hardening of magnetic and transport properties of Mg-1.3wt% Ce alloys[J]. Acta Materialia, 1998, 46(9): 2977-2981.
[15] PLANKEN J. Precipitation hardening in magnesium-tin alloys[J]. J Mater Sci Lett, 1969, 4: 927-929.
[16] LIU H M, CHEN Y G, TANG Y B, HUANG D M, TU M J, ZHAO M, LI Y G. Effect of Zr-adding on microstructure and mechanical properties for Mg-5Sn alloy[J]. Rare Metal Materials and Engineering, 2006, 35(12): 1912-1915.
Foundation item: Project (2006BAE04B02-3) supported by the National Key Technologies R&D Program of China
Corresponding author: YU Kun; Tel: +86-731-8879341; E-mail: kunyu2001@163.com
(Edited by LONG Huai-zhong)