文章编号:1004-0609(2010)S1-s0500-05
钛合金开坯锻造过程的有限元模拟
于德军1,柏春光1,徐东生1,李渭清2,何书林2,雷家峰1,刘羽寅1,杨 锐1
(1. 中国科学院 金属研究所,沈阳110016;2. 宝钛集团有限公司,宝鸡 721014)
摘 要:运用弹塑性有限元方法对钛合金开坯锻造过程进行三维热力耦合模拟,分析不同条件下各过程中温度、应力和应变的空间分布变化规律。模拟研究发现,道次变形量对开坯效果有着重要影响,变形量太小则会产生搓皮现象;连续锻造过程中两锤之间的重叠对应变分布及坯料质量有着重要影响,接缝处表面附近应变较大,而芯部应变较小,非接缝区域应变分布与之相反,应调整锻锤重叠区域以提高产品质量;方坯锻造应力应变有叠加效应,控制不当将影响产品质量甚至导致缺陷。在综合讨论分析的基础上,对钛合金开坯锻造工艺设计提出调整建议。
关键词:钛合金;锻造;有限元模拟
中图分类号:TF 804.3 文献标志码:A
FEM simulation of forging of Ti alloy
YU De-jun1, BAI Chun-guang1, XU Dong-sheng1, LI Wei-qing2,
HE Shu-lin2, LEI Jia-feng1, LIU Yu-yin1, YANG Rui1
(1. Institute of Metal Research, Chinese Academy of Sciences, Shenyang 110016, China;
2. Baoti Group Co., Ltd., Baoji 721014, China)
Abstract: The forging process of TA15 ingot was investigated using three dimensional thermal-mechanical coupled simulations based on finite element method. The forging process was optimized on the bases of deformation and strain analysis after the simulation under different deformation condition, hammer overlapping, and forging process.
Key words: Ti alloy; forging; TEM simulation
钛合金因具有较高的比强度和耐蚀性能等,是最具潜力的轻型结构材料之一,近年来受到极大关 注[1-5]。钛合金广泛应用于当铝合金、高强钢或镍基高温合金在强度、耐蚀性、质量等不能满足的航空产品中。限制钛合金实际应用的最大障碍是其缺乏足够的延性和较差的变形加工性能。经过多年的努力,国内外已在钛合金的加工工艺方面取得长足进展[6-10],但关于钛合金开坯的报道却很少。由于钛合金热加工温度高且窗口较窄,锭坯开坯锻造难度较大,需要采用较大的锻造设备和合理的锻造工艺,有效避免锭坯锻造过程中出现各种缺陷,从而保障后续的加工和最终产品的质量。如何通过优化锻造开坯工艺来提高产品质量是摆在科研人员面前的一个重要课题。
有限元模拟在新材料设计及工艺优化中显示出越来越多的优越性,已成为一种强大的科研辅助手 段[11]。本研究采用有限元方法模拟开坯锻造过程以期指导生产工艺设计。
1 研究方法
1.1 材料物性
锭坯TA15合金的热物性数据参考ASM材料手 册[12],其中热导率、比热容和热膨胀系数均为温度的函数。合金的力学性能数据取自中国航空材料手册[13]和ASM材料手册。图1所示为TA15合金在不同温度和应变速率下的峰值流变应力。由图1可见,合金的变形行为受温度、应变和应变速率的影响较大。随温度降低和应变速率的提高,变形抗力大幅上升。TA15钛合金的塑性随温度升高而增大,在900~1 200 ℃范围内塑性好,但预热温度不能过高,否则晶粒长大迅速而影响成品质量,因而可加工的温度范围较窄。高温下随变形程度的增加,钛合金会出现一定程度的加工软化,有利于合金的变形。
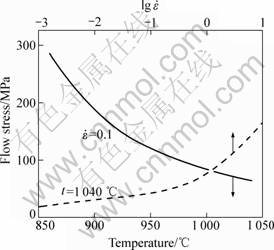
图1 TA15合金的流动应力随温度和应变速率的变化
Fig.1 Flow stress of TA15 alloy at different temperatures and strain rates
1.2 模拟方法
锻造实验选用液压机,上锤头和下砧板尺寸为 1 600 mm×600 mm,锻速可调。坯料尺寸为 d 920 mm×2 000 mm,初始坯料加热温度为1 150 ℃。采取四竖、四横交替排锻造8道次,每锤变形量约为9%~20%,加两道滚圆工艺完成。采用弹塑性有限元法进行热力耦合模拟。网格划分采用正六面体单元,网格划分总量约2.2万单元,模拟软件以MARC为基础,模拟工作在Dell计算机集群上完成。计算中考虑工件表面的热传导、热辐射、工件与上锤头和下砧板之间的接触热交换,同时考虑塑性变形热、摩擦热作用。为简化计算,将上锤头和下砧板理想化为恒温传热刚体,忽略工件与机械手间热交换及工件出炉转移时过程的热交换热损失。模拟中材料参数主要来自文献[12-13],其它参数根据参照实验工艺赋值,超出实验范围的数据通过外推法线性插值取得。
2 结果与讨论
2.1 TA15合金锭传热过程模拟
钛合金开坯锻造工艺的难点在于影响因素多,通常找不到合适的工艺路线,如何通过模拟辅助工艺设计提高成品率和产品质量尤为重要。锻造过程的散热改变了被锻合金锭坯的温度分布,进而影响锻造效果,分析锻造过程的温降对于钛合金这类加工温度窗口窄的材料尤为重要。首先对开坯前TA15钛合金锭进行空冷过程的温度场计算,模拟工件转移过程中的温降。对于尺寸为d 920 mm×2 000 mm的钛合金锭,初始温度设为1 000 ℃,空冷时间10 min。观察钛合金锭整体及内部各截面的温度分布情况及变化规律,为制订开坯工艺提供基础数据。
图2(a)所示为合金坯料空冷5 min时中纵剖面及部分锭端面的温度分布。由图2(a)可见,边角及外表面处温降较大,其余大部分区域温度基本均匀。图2(b)所示为合金坯料空冷时不同部位(端面边角圆周线上点A、中切面圆周线上点B、距离中切面圆周线20 mm点C、柱体体中心点D)的温度随时间的变化曲线。由于合金坯料体积较大,短时间内除边角与表面温降较大外,体内大部分温降并不明显,表明合金坯料整体降温较慢且温度分布相对比较均匀,这对锻造有利。虽然坯料运转的短时间内温降较小,但如锻造时间过长,降温仍很明显,要求尽可能提高锻造速度,以节约时间从而保证锻造温度
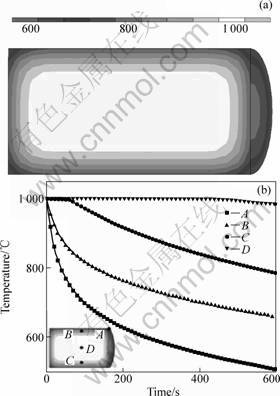
图2 合金坯料空冷5 min时纵中剖面及端表面温度分布和坯料不同位置的温度随时间变化
Fig.2 Temperature distribution and evolution at different positions
2.2 TA15合金锻造过程温度场分析
由于塑性变形热引起的锻件内部的温升对确定锻造工艺很重要,本节对锻造区温度变化进行重点考察。
图3(a)和(b)所示为开始锻造和经翻转锻造后被锻部分的横剖面温度分布。可见外边缘部分,尤其是与锤头接触部分有一定温降。这是由于热辐射和热传导所致。温降向中心对称递减,但在锤头下方50~100 mm区域出现明显的相对温升。这是由塑性变形热所导致,温升的大小与该区域的应变相关,该变形量下变形区域主要集中在锤下50~100 mm区域。
初锻过程中塑性变形热引起被锻体不均匀温升,最高温区为锤下为50~100 mm区域,再锻过程情况类似,但由于锻造方向旋转90?,升温剧烈区域与初锻过程不同,升温累加效果不明显。
图3(c)所示为一次翻转后锻造过程合金锭的纵剖面温度分布。可见外表面部分,尤其是与锤头接触部分温降明显,但在锤下50~100 mm区域也出现明显温升,与图3(a)和(b)类似。需注意的是锤头边缘附近,合金的温升更加明显,表明锤间接缝处表面附近应变较大。实际生产中易在此处产生缺陷,应对办法可采取加大锤头倒角、减小道次变形量、避免同一地点多次为锤间接缝而产生累积效应。
图3(d)所示为二次翻转锻成方坯后继续锻造过程被锻部分的横剖面温度分布。可见外边缘部分都有较大的温降,而锤下50~100 mm区域明显升温,可见该处变形较集中。预计中的45?剪刀叉区域没有出现明显升温,芯部形变量很小。分析表明,圆坯锻造时锤头下方50~100 mm附近区域由于加工软化,承担了大部分形变,减弱了45?剪刀叉区域的形变。不同变形量模拟比较显示,开坯变形量9%太小,此即工程上所说的打不透、搓皮,可见开坯过程的道次变形量不能太小(下文模拟开坯变形量达20%)。
基本锻成方坯后继续锻造过程中,塑性变形热引起锤下50~100 mm区域明显相对升温。由于方坯锻造方向固定,升温区域与前锻偏移不大,显现升温累加,所以锻造过程应尽量避免在同一区域连续锻造,以避免局部温升过高。最好是在工艺设计时采用八角循环锻工艺,可最大限度降低局部相对温升,且各处累计应变量相对均匀,对提高材料的整体均匀性有利。
2.3 TA15合金锻造过程应力应变分析
应变控制对难塑性加工材料的锻造工艺设计非常重要。拉应力是裂纹产生的驱动力,而拉伸强度通常仅为压缩强度三分之一,在拉应力低于拉伸强度时微裂纹就可能产生。因此塑性变形的应力应变分布对产品的最终质量影响很大。

图3 不同锻造阶段锻件剖面温度分布云图
Fig.3 Temperature distribution of billet under different forgings
图4所示为开坯锻造不同工序的应变应力分布情况。图4(a)为第一锤后锻件的横截面应变分布; 图4(b)为锻件旋转90?后锻造第二道次时应变分布。由图4(a)和(b)可见,应变主要集中在锤头下方45?剪刀区域,表明该区域塑性变形较大,坯料整体形变较 均匀。
图4(c)为第一锤后锻件横截面应力分布;图4(d)为锻件旋转90?后第二道次时锻件的横截面应力分布。可见应力主要集中在锤头下方约50 mm内和45?剪刀区域。由应变分析可知:锤头下方50 mm以内塑性变形并不大。但应力较大,是因为锤头的热传导使表面接触区域降温很大,容易超出TA15的塑性变形区,是易产生缺陷的地方。
图5所示为方坯终锻后锻件双纵剖面在3个方向(x、y、z方向,z方向为轴向)的总等效应变分布。可见应变沿纵向以每锤锻造长度为单位呈周期性分布,表面附近两锤间接缝区域应变较大,而中心附近对应两锤间接缝区域相对应变较小,表明落锤的位置影响锻件整体的应变分布。由锤间接缝导致的锻件变形不均匀的特点是锻锤间接缝处表面附近和体心附近影响效果相反。
图6所示为方坯终锻后四分之一体的体表、45?角切面和双纵剖面的总等效应力分布。分布情况基本同应变分布相符,但由于表面降温影响使表面两锤间接缝区域应力更加明显,容易导致缺陷发生,应保证道次变形量不能过大,以减小缺陷发生的可能。因纵向锻造过程中的锤间接缝无法避免,应尽量利用接缝处表面附近和体心附近影响效果相反这一结果。在锻造工艺设计时可以通过控制工件纵向移动距离,尽量使各锤锻造的接缝区域相互错开的工艺路线,以调整锻件体内的应变,使各处累计应变量相对均匀,提高材料性能的整体均匀性。表面温降引起的应力主要集中在体表附近,该区域也是最容易产生缺陷的地方,应采取尽量缩短整体锻造时间,降低锤头和工件接触时间或提高锤头温度等措施减少表面温降。
2.4 有限元模拟与锻造实验的比较
模拟结果和开坯锻造生产实践结合取得了较好的结果,模拟结果对锻造生产的工艺设计具有一定的指导意义。
3 结论
1) 开坯锻造时道次变形量不应太小,否则将产生搓皮现象,达不到开坯效果,而道次变形量过大则容易产生缺陷。
2) 锻锤接触区边缘锻件内应力应变分布不均,且表面和中心趋势相反,设计合理的锤间重叠工艺有利于提高材料的整体均匀性,从而提高产品质量。

图4 不同锻造阶段时锻件剖面应变(a,b)、应力(c,d)分布云图
Fig.4 Strain (a, b) and stress (c, d) distribution of billet during forging

图5 方坯终锻时锻件剖面不同方向应变分布云图
Fig.5 Normal strain distribution of billet: (a) x-axis; (b) y-axis; (c) z-axis
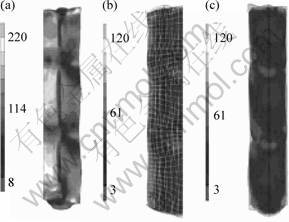
图6 方坯终锻时锻件不同剖面应力分布云图
Fig.6 Stress distribution of billet in different sections: (a) Surface; (b) 45? section; (c) Longitudial section
3) 开成方坯再滚圆的锻造方案因变形叠加效应易产生缺陷,从而影响产品质量,采用八角循环锻有助于控制形变均匀性。
REFERENCES
[1] SEMIATIN S L, SEETHARAMAN V, WEISS I. Flow behavior and globularization kinetics during hot working of Ti-6Al-4V with a colony alpha microstructure[J]. Mater Sci Eng A, 1999, 263(2): 257-271.
[2] BALASUBRAHMANYAM V V, PRASAD Y V R K. Deformation behaviour of beta titanium alloy Ti-10V- 4.5Fe-1.5Al in hot upset forging[J]. Mater Sci Eng A, 2002, 336(1/2): 150-158.
[3] BRUSCHI S, POGGIO S, QUADRINI F, TATA M E. Workability of Ti-6Al-4V alloy at high temperatures and strain rates[J]. Mater Lett, 2004, 58(27/28): 3622-3629.
[4] BAO R Q, HUANG X, CAO C X. Deformation behavior and mechanisms of Ti-1023 alloy[J]. Transactions of Nonferrous Metals Society of China, 2006, 16: 274-280.
[5] 罗 皎, 李淼泉, 李 宏, 于卫新. TC4 钛合金高温变形行为及其流动应力模型[J]. 中国有色金属学报, 2008, 18(8): 1395-1401.
LUO Jiao, LI Miao-quan, LI Hong, YU Wei-xin. High temperature deformation behavior of TC4 titanium alloy and its flows stress model[J]. The Chinese Journal of Nonferrous Metals, 2008, 18(8): 1395-1401.
[6] LUKAC I, PETRIK J, KOKARDA V, HROCH P. The occurrence of localized shear bands at non-isothermal hot-forging of Ti alloys[J]. Kovove Materialy-Metallic Materials, 1988, 26(2): 188-199.
[7] ROBERTSON D G, MCSHANE H B. Analysis of high temperature flow stress of titanium alloys IMI 550 and Ti-10V-2Fe-3Al during isothermal forging[J]. Materials Science and Technology, 1998, 14(4): 339-345.
[8] KODESS B N. Microstructure evolution in Ti-alloys during severe deformation by electric upsetting and impact fused-forging modeling-New power-saving technologies[J]. Investigations and Applications of Severe Plastic Deformation, 2000, 80: 211-218.
[9] ZHAO Z L, WANG B, YAO Z K, LIU Y Y. The effect of isothermal forging process parameters on the microstructure and the properties of TA15 near a titanium alloy[J]. Advanced Materials and Processing, 2007, 26/28: 367-1364.
[10] NONOYAMA F, SATOU T, DANNO A. Formation of non-equilibrium phases by repeated forging of Al-Ti alloys[J]. Journal of the Japan Institute of Metals, 1996. 60(1): 92-99.
[11] 徐东生, 胡青苗, 柏春光, 王 刚, 王 嗥, 杨 锐. 钛合金力学行为的多尺度计算[J]. 稀有金属材料与工程, 2005, 34(增刊3): 633-636.
XU Dong-sheng, HU Qing-miao, BAI Chun-guang, WANG Gang, WANG Hao, YANG Rui. Multi-scale modeling of mechanical behavior of titanium alloys[J]. Rare Metal Materials and Engineering, 2005, 34(suppl.3): 633-636.
[12] BOYER R. Materials properties handbook: titanium alloys[J]. OH: ASM International, Metal Park, 1994.
[13] 中国航空材料手册: 结构钢、不锈钢[M]. 北京: 中国标准出版社, 1988.
Chinese aeronautical materials handbook: structural steel and stainless steel[M]. Beijing: Standards Press of China, 1988.
(编辑 袁赛前)
通信作者:徐东生;电话:024-23971946;E-mail: dsxu@imr.ac.cn