J. Cent. South Univ. (2017) 24: 2238-2244
DOI: https://doi.org/10.1007/s11771-017-3633-3

Effect of cathode composition on microstructure and tribological properties of TiBN nanocomposite multilayer coating synthesized by plasma immersion ion implantation and deposition
L
Wen-quan(吕文泉)1, CAO Yong-zhi(曹永智)2, WANG Lang-ping(王浪平)1,
WANG Xiao-feng(王小峰)1, GU Zhi-wei(顾至伟)1, YAN Yong-da(闫永达)2, YU Fu-li(于福利)2
1. State Key Laboratory of Advanced Welding & Joining (Harbin Institute of Technology), Harbin 150001, China;
2. Center for Precision Engineering, Harbin Institute of Technology, Harbin 150001, China
Central South University Press and Springer-Verlag GmbH Germany 2017
Abstract: Nanocomposite multilayer TiBN coatings were prepared on Si (100) and 9Cr18Mo substrates using TiBN composite cathode plasma immersion ion implantation and deposition technique (PIIID). Synthesis of TiBN composite cathodes was conducted by powder metallurgy technology and the content of hexagonal boron nitride (h-BN) was changed from 8% to 40% (mass fraction). The as-deposited coatings were characterized by energy dispersive spectrometer (EDS), grazing incidence X-ray diffraction (GIXRD), Fourier Transform Infrared Spectroscopy (FTIR) and high resolution transmission electron microcopy (HRTEM). EDS results show that the B content of the coatings was varied from 3.71% to 13.84% (molar fraction) when the composition of the h-BN in the composited cathodes was changed from 8 % to 40% (mass fraction). GIXRD results reveal that the TiBN coatings with a B content of 8% has the main diffraction peak of TiN (200), (220) and (311), and these peaks disappear when the B content is increased. FTIR analysis of the multilayer coatings showed the presence of h-BN in all coatings. TEM images reveal that all coatings have the characteristics of self-forming nanocomposite multilayers, where the nanocomposites are composed of face-centered cubic TiN or h-BN nanocrystalline embedded in amorphous matrix. The tribological tests reveal that the TiBN coatings exhibit a marked decrease of coefficient at room temperature (~0.25). The improved properties were found to be derived from the comprehensiveness of the self-forming multilayers structure and the h-BN solid lubrication effects in the coatings.
Key words: TiBN coatings; nanocomposite; multilayer; plasma immersion ion implantation and deposition
1 Introduction
With the increasing technological and environmental concerns, various modern equipments are required to be designed to be able to work in an even severer condition, pushing components to the very limits of their capabilities [1, 2]. Especially for aerospace and other high-tech fields such as high speed precision instruments, reducing the heat yield of the devices is the basic demand for precise work piece stability [3]. Because the process of friction results from the interaction between two or more bodies in relative motion in a particular environment, surface engineering can be applied as the key technology to enable high performance needed for demanding operational conditions [4, 5] and effectively reduce the coefficient of friction. Surface modification technology can significantly improve the surface performance with micro size decals while containing mechanical properties of the matrix, and thus attract wide interest in recent years [6]. In addition, the application of multilayered PVD coatings has been documented as an efficient way for prolonging the coated tool life [7, 8]. Coatings with a multilayered structure can be harder, low coefficient, or better corrosion resistance than homogeneous coatings of the same materials [9, 10]. Since the layered structure obstructs dislocation glide and crack propagation [11, 12], toughening by a multilayered architecture can be attributed to the effects of interfaces on dissipating crack energy and deflecting cracks [13]. However, the design of the appropriate material system must be guided by an accurate understanding of the degradation mechanisms and the surface response to loading, which frequently acts in synergy [14–16].
Solid lubrication coatings have attracted a tremendous amount of interest in because of its capabilities of working in ultra-high vacuum, high/low temperature, strong oxidation or reduction, strong radiation, high load conditions compared with fluid lubrication method, which breaks the limitation of lubricating oil, grease lubrication, and meets the needs of the transmission mechanism under hard working condition [17–19]. Till now, solid lubrication has been widely applied in satellite, spaceship, aerospace equipment, and the space station [20]. Further, solid lubrication materials, such as MoS2, V2O5, DLC, and WS2 have been developed and widely applied in many kinds of fields [21–23]. However, few of these coating systems have the capacity of containing low coefficient in high temperature condition [3, 24], which is a crucial part in improving the speed of industrial development, especially in the field of aerospace [25, 26].
Since h-BN has the property of high oxidation resistance under high temperature conditions (≤900 °C), and good lubrication properties just like graphite, it has a great potential in solid lubrication applications [27, 28]. However, previous studies mainly focused on adding boron into the coatings to form cubic BN (c-BN), and these strengthening phases can effectively improve the hardness of the coatings [24, 29]. Many other methods were also applied to synthesizing TiBN/Ti(B)CN/WBN coatings with high hardness (≥30 GPa) because of the forming of c-BN phase [30–32]. As the h-BN is a material of nonconductor which districts the application of h-BN in the plasma field and right now, most solid lubrication material added h-BN was mainly used by powder metallurgy technology which greatly deducted the hardness of the material [33].
In our study, we expect to synthesize a TiBN coating with h-BN phase as the solid lubrication phase. To resolve the problems of the nonconductor properties of h-BN, powder metallurgy technology was used with different compositional ratios of Ti and h-BN powders to forming composite cathode which has the ability of good conduction working in plasma immersion ion implantation and deposition (PIIID) process, and the detail information on the phase composition, structure and mechanical properties, such as tribological properties of the as-deposited TiBN coatings were studied systematically.
2 Experimental details
Synthesis of the Ti-BN composite cathode was conducted by powder metallurgy technology. The sizes of Ti and h-BN powders were both ~20 μm. Ti and h-BN powders with the mass fraction of h-BN of 8%, 15%, 30%, 40% were mixed uniformly, then forged under the pressure of 83 MPa and heated at 1050 oC in a vacuum container with the pressure of 4.0×10–3 Pa for 3 h. The Ti-BN composite cathodes have good electrical conductivity which can be used in the PIIID process. Ternary TiBN coatings were deposited on single Si (400) wafers and 9Cr18Mo substrates using our PIIID facility [34] equipped with the TiBN composite cathode. The element contents of the 9Cr18Mo substrate are listed in Table 1. In the PIIID process, the base pressure in the chamber was 5×10–3 Pa and the working pressure was 3×10–1 Pa. To remove residual pollutants and native oxide, the substrates were cleaned by Ar+ sputtering at a bias voltage of 6 kV for 30 min prior to deposition. Composite Ti and BN plasma was generated by a pulsed cathodic arc source in the PIIID facility, and the discharge voltage and current of the cathodic arc were (22±3) V and (60±5) A, respectively. The composite plasma was guided into the processing chamber through a 90° magnetic duct. Nitrogen (N2) with a mass flow of 50 mL/min was introduced into the chamber synchronously when the composite plasma was formed. A pulsed bias with a voltage of 20 kV, a repetition frequency of 75 Hz, a pulse duration time of 60 μs was applied on the substrate. The total deposition time for every sample was 4 h, and the thickness of the TiBN coatings was about 2 μm.
Table 1 Compositions of 9Cr18Mo (mass fraction, %)
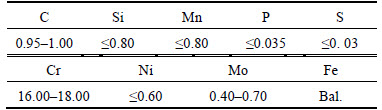
The crystal structure of the as-deposited coatings was examined by grazing incidence X-ray diffraction (GIXRD, Empyrean) using an angle of 1° and Cu Ka radiation. The presence of chemical bonding in the coatings was studied by Fourier Transform Infrared spectroscopy (FTIR, PerkinElmer, Spectrum One). The compositions of TiBN coatings were tested by energy dispersive spectrometer (EDS). The microstructures of the coatings were investigated by transmission electron microscopy (TEM, FEI-Tecnai-30) with an acceleration voltage of 300 kV. Hardness of the composite coatings was evaluated using a nano-indentation system (Nano Indenter G 200). To minimize the influence of the substrate on hardness, the indentation depth was kept below 10% of the coating thickness. The tribological properties of TiBN coatings were evaluated using a ball-on-disc tester with a linear velocity of 0.05 m/s. The tests were carried out under dry running condition of a 6.3 mm Si3N4 ball and a load of 30 g with the friction radius of 2 mm for 20 min.
3 Results and discussion
Table 2 shows the composition of the as-deposited TiBN coatings tested by EDS. Samples a, b, c and d are defined as the one fabricated by the composited Ti-BN cathode with the h-BN content of 8%, 15%, 30% and 40%, respectively. The mass fraction of h-BN in the TiBN cathode was changed from 8% to 40%. In the TiBN coatings, the element contents were labeled as atom percentage (at.%) and we can see that the content of B in the as-deposited coating was varied from 3.71% to 13.84%. In addition, the content of Ti decreased obviously while the B, N and O keep stable relatively when the B content was increased. That because the B atomic mass is lower than Ti which is easier to change the direction when undergoing the electric field force or ions collide. The N and O contents are relative stable although the change of TiBN cathodes.
Table 2 Compositions of as-deposited coatings determined by EDS
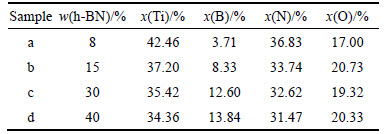
Figure 1(a) shows the GIXRD patterns of the as-deposited TiBN coatings with different B contents. According to Bragg angles (2θ) of 42.59° and 61.8° (JCPDS No.38-1420), we can see that the GIXRD peaks of the TiBN coatings with a B content of 3.71wt% and 8.33at% exhibit three characteristic TiN peaks of (200), (220) and (311) planes of face-centered cubic (fcc) TiN. It can also be found that the h-BN phase has been formed in sample b with the evidence of (002) (JCPDS No.34–0421) in the TiBN coating. When the content of the B is continuously increased, the h-BN phase disappears and TiN peak of (200) plane weakens, which hints that the TiBN coating will change to an amorphous structure under a high B content.
To investigate the chemical bonding structure of BN in more detail, FTIR spectra of the TiBN coatings are shown in Fig. 1(b). In order to discriminate the peaks of h-BN clearly, the FTIR spectra of pure h-BN powders (sample S0) are shown in this figure also. As the characteristic peaks of elongation vibrational mode at 1380 cm–1 and the bending vibrational mode nearby 800 cm–1 [35] are clear, we can confirm that the h-BN has been formed in all coatings. In addition, since the FTIR characteristic peaks of c-BN locate at 1065 cm–1 (transverse optical wave) and 1310 cm–1 (longitudinal optical wave ) [36], we can deduce that the content of c-BN can be neglected in all TiBN coatings.
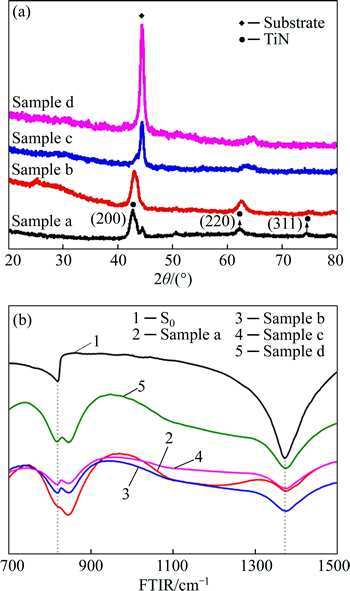
Fig. 1 X-ray diffraction patterns (a) and FTIR spectra (b) of TiBN coatings with different BN contents
The structures of TiBN coatings formed by PIIID process are mainly determined by the factor of ion energy, ion composition and their percentage. We cannot ignore the temperature during the coatings deposition. The cathode is different from the TiB2 cathode which is mainly used in preparation of TiBN coatings, the powder metallurgy TiBN composite cathodes have good conduction, but the pulsed cathode arc sports should have distinct with the molten state cathode which changes the ion composition and their percentage. These changes lastly form the structure of the TiBN coatings.
Figure 2 exhibits the HRTEM images and corresponding diffraction patterns for different TiBN coatings. TEM images shown in Figs. 2(a), (c), (e) and (g) reveal that all coatings have the characteristics of multilayered structure. The HRTEM images shown in Figs. 2(b), 2(d), 2(f) and 2(h) exhibit that each layer of the multilayer is composed of nanocrystals embedded in amorphous matrix. In addition, it can be found that the size of the nanocrystal decreases with the increase of the B content. From the corresponding diffraction patterns inserted in Figs. 2(b) and (d), it can be found that several diffraction rings have been formed, and the calibration of different diffraction rings shows that face-centered cubic structure of TiN is the main content of the nanocrystals in the coating corresponding to Fig. 1(a). In addition, as shown in Fig. 2(d), an h-BN diffraction ring for (002) and (100) plane can be found when the B content is 8.33at.%, which hints that h-BN can be crystallized in a proper PIIID process. However, with further increase of the B content in the coating, the diffraction rings of TiN and BN are diminished, which is in consistent with the GIXRD results. Since h-BN is obvious in all coatings, the amorphous phase should mainly be composed of h-BN and other oxides. As we know that the radius of the B+ (0.230
) is much smaller than that of the Ti+ (0.605
), the solid solution of B atoms to TiN crystal or replace some Ti atoms may occur during the deposition process which causes the non-crystallization process.
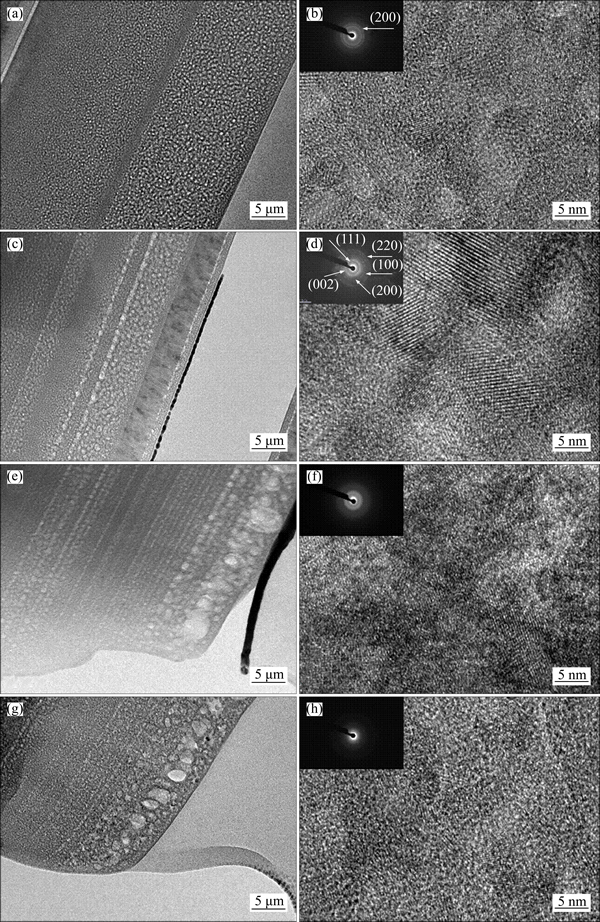
Fig. 2 TEM images (a, c, e, g) and corresponding HRTEM images with SAD pattern (b, d, f, g) of TiBN coatings with BN contents of 8wt.% (a, b), 15wt.% (c, d), 30wt.% (e, f) and 40wt.% (g, h)
The nano-hardness of the TiBN coatings with different contents of B is listed in Fig. 3. The nanohardness of the TiBN coatings shows a downward trend with the increasing of B content. When the B content is 3.71at.%, the nano-hardness of TiBN reaches the highest, 14 GPa, and it reduces to 7.2 GPa when the B content is increased to 13.84at.%. The nanohardness obtained in our experiments is much lower than those reported values in c-BN composite coatings (22–42 GPa) [33, 37], which should be derived from the large content of h-BN phase other than c-BN phase in these coatings. We know that the c-BN phase has the high hardness while the h-BN has low hardness but good solid lubrication properties which cause low coefficient.
Figure 4 compares the friction curves of the TiBN coating with different contents of B at room temperature. We can see that the sample with the smallest B content had the largest friction coefficient of ~0.3. However,since the dry friction coefficient between the Si3N4 ball and the substrate is near 0.7, the obvious decrease of friction coefficient should be attributed to the formation of h-BN in the coating. With the increase of B content, the friction coefficient decreases to about 0.25, which hints that a large content of B may form more h-BN, which benefits the solid lubrication process during the tribological test.
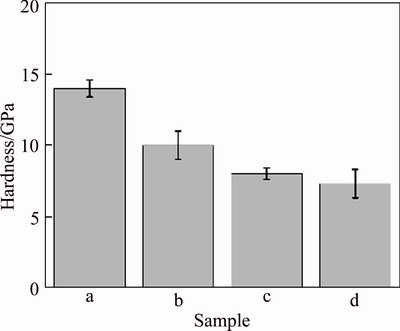
Fig. 3 Nanohardness of TiBN coating with different contents of BN
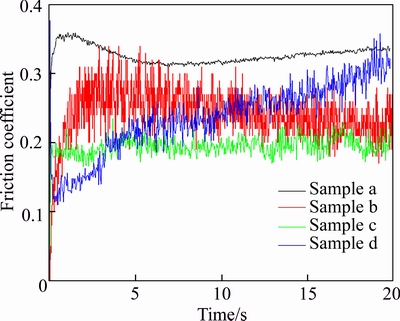
Fig. 4 Friction curves of TiBN coatings at room temperature
Figure 5 shows the wear tracks of samples a–d after the ball-on-disk test. The widths of the wear track for samples a, b, c and d are 640, 500, 650 and 600 μm, respectively. In addition, the as-deposited coatings were worn off in samples a, c and d, while the sample b keeps complete after the tribological test. As a result, it is clear that the TiBN coating with the B content of 8.33at.% exhibits excellent wear resistance.
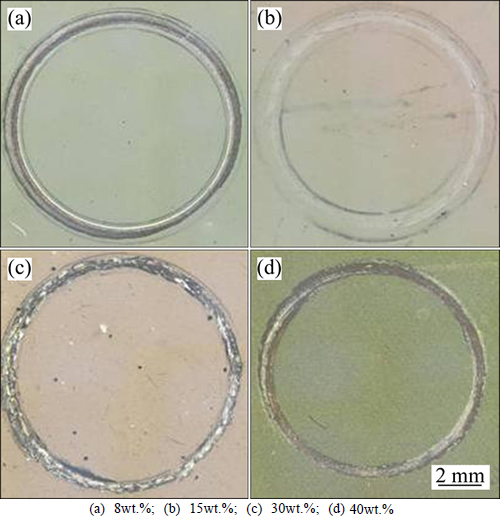
Fig. 5 Wear tracks of TiBN coatings with BN content after tribological tests:
4 Conclusions
In summary, TiBN coatings prepared by the composite cathode with different contents of h-BN were deposited on single Si (100) wafer and 9Cr18Mo substrates by a TiBN composite cathode PIIID technique. All coatings have the characteristics of self-forming nanocomposite multilayer structures, where the nanocomposites are composed of face-centered cubic TiN or hexagonal BN nanocrystalline embedded in amorphous matrix, and the amorphous phase should mainly be composed of h-BN and other oxides. In addition, the TiBN coatings exhibit a marked decrease of coefficient (~0.25) at room temperature. From the wear scratch morphology we can define that the wear mechanism is adhesive wear which is easier to form the solid lubrication layers during the wear process and the h-BN phases in the coatings can supply the raw material for solid lubrication and can effectively guarantee that the process of friction remains stable. The coating with the B content of 8.33at.% exhibits excellent wear resistance.
Acknowledgments
This work is supported by Heilongjiang Postdoctoral Foundation of China (No.LRB07-140), and Introducing Talents of Discipline to Universities (No. B07018), China
References
[1] Bousser E, Martinu L, Klemberg-Sapieha J E. Solid particle erosion mechanisms of protective coatings for aerospace applications [J]. Surface and Coatings Technology, 2014, 257: 165–181.
[2] Gong F, Guo B. Effects of solid lubrication film on SKD11 in micro sheet forming [J]. Surface and Coatings Technology, 2013, 232: 814–820.
[3] Voevodin A A, Muratore C, Aouadi S M. Hard coatings with high temperature adaptive lubrication and contact thermal management: Review [J]. Surface and Coatings Technology, 2014, 257: 247–265.
[4] Mollart T P, Haupt J, Gilmore R, Gissler W. Tribological behavior of homogeneous TiBN, TiBNC and TiN/hBN/TiB2 multilayer coatings [J]. Surface and Coatings Technology, 1996, 86–87: 231–236.
[5] Qin Y, Xiong D, Li J. Tribological properties of laser surface textured and plasma electrolytic oxidation duplex-treated Ti6Al4V alloy deposited with MoS2 film [J]. Surface and Coatings Technology, 2015, 269: 266–272.
[6] Rebholz C, Schneider J M, Voevodin A A, Steinebrunner J, Charitidis C, Logothetidis S, Leyland A, Matthews A. Structure, mechanical and tribological properties of sputtered TiAlBN thin films [J]. Surface and coatings technology, 1999, 113: 126–133.
[7] Bouzakis K D, Bouzakis E, Kombogiannis S, Makrimallakis S, Skordaris, N Michailidis G, Charalampous P, Paraskevopoulou R, Saoubi R M, Aurich J C, BarthelmA F, Biermann D, Denkena B, Dimitrov D, Engin S, Karpuschewski B, Klocke F, Qzel T, Poulachon G, Rech J, Schulze V, Settineri L, Srivastava A, Wegener K, Uhlmann E, Zeman P. Effect of cutting edge preparation of coated tools on their performance in milling various materials [J]. CIRP Journal of Manufacturing Science and Technology, 2014, 7: 264–273.
[8] Bouzakis K D, Hadjiyiannis S, Skordaris G, Anastopoulos J, Mirisidis I, Michailidis N, Efstathiou K, Knotek O, Erkens G, Cremer R, Rambadt S, Wirth I. The influence of the coating thickness on its strength properties and on the milling performance of PVD coated inserts [J]. Surface and Coatings Technology, 2003, 174–175: 393–401.
[9] Wang T, Zhang G, Jiang B. Comparison in mechanical and tribological properties of CrTiAlMoN and CrTiAlN nano-multilayer coatings deposited by magnetron sputtering [J]. Applied Surface Science, 2016, 363: 217–224.
[10] Zare i, Moghadam R, Ahmadvand H, Jannesari M. Design and fabrication of multi-layers infrared antireflection coating consisting of ZnS and Ge on ZnS substrate [J]. Infrared Physics & Technology, 2016, 75: 18–21.
[11] Stueber M, Holleck H, Leiste H, Seemann K, Ulrich S, Ziebert C. Concepts for the design of advanced nanoscale PVD multilayer protective thin films [J]. Journal of Alloys and Compounds, 2009, 483: 321–333.
[12] Lu Y Y, Kotoka R, Ligda J P, Yarmolenko S N, Schuster B E, Wei Q. Morphological and mechanical stability of HCP-based multilayer nanofilms at elevated temperatures [J]. Surface and Coatings Technology, 2015, 275: 142–147.
[13] Callisti M, Lozano-Perez S, Polcar T. Structural and mechanical properties of γ-irradiated Zr/Nb multilayer nanocomposites [J]. Materials Letter, 2016, 163: 138–141.
[14] Banerjee T, Chattopadhyay A K. Structural, mechanical and tribological properties of WS2-Ti composite coating with and without hard under layer of TiN [J]. Surface and Coatings Technology, 2014, 258: 849–860.
[15] Danyluk M, Dhingra A. Rolling contact fatigue using solid thin film lubrication [J]. Wear, 2012, 274–275: 368–376.
[16] Budna K P, Neidhardt J, Mayrhofer P H, Mitterer C. Synthesis-structure-property relations for Cr-B-N coatings sputter deposited reactively from a Cr-B target with 20 at% B [J]. Vacuum, 2008, 82: 771–776.
[17] Guleryuz C G, Krzanowski J. Mechanisms of self- lubrication in patterned TiN coatings containing solid lubricant microreservoirs [J]. Surface and Coatings Technology, 2010, 204: 2392–2399.
[18] Bartl M H. Nanostructure-driven functionalities in thin films and coatings [J]. Scripta Materialia, 2014, 74: 1–2.
[19] Fazel M, Jazi M R G, Bahramzadeh S, Bakhshi S R, Ramazani M. Effect of solid lubricant particles on room and elevated temperature tribological properties of Ni–SiC composite coating [J]. Surface and Coatings Technology, 2014, 254: 252–259.
[20] Baker M A, Klose S, Rebholz C, Leyland A, Matthews A. Evaluating the microstructure and performance of nanocomposite PVD TiAlBN coatings [J]. Surface and Coatings Technology, 2002, 151–152: 338–343.
[21] Han Y, Zhou J, Dong J. Electronic and magnetic properties of MoS2 nanoribbons with sulfur line vacancy defects [J]. Applied Surface Science, 2015, 346: 470–476.
[22] Franz R, Mitterer C. Vanadium containing self-adaptive low- friction hard coatings for high-temperature applications: A review [J]. Surface and Coatings Technology, 2013, 228: 1–13.
[23] Wang Lang-ping, Huang Lei, Wang Yu-hang, Xie Zhi-wen, WANG Xiao-feng. Duplex DLC coatings fabricated on the inner surface of a tube using plasma immersion ion implantation and deposition [J]. Diamond and Related Materials, 2008, 17: 43–47.
[24] Mayrhofer P H, Stoiber M, Mitterer C. Age hardening of PACVD TiBN thin films [J]. Scripta Materialia, 2005, 53: 241–245.
[25] PalDey S, Deevi S C. Single layer and multilayer wear resistant coatings of (Ti,Al)N: A review [J]. Materials Science and Engineering A, 2003, 342: 58–79.
[26] Deng X, Kousaka H, Tokoroyama T, Umehara N. Deposition and tribological behaviors of ternary BCN coatings at elevated temperatures [J]. Surface and Coatings Technology, 2014, 259: 2–6.
[27] Zhang R F, Sheng S H, Veprek S. Stability of Ti-B-N solid solutions and the formation of nc-TiN/a-BN nanocomposites studied by combined ab initio and thermodynamic calculations [J]. Acta Materialia, 2008, 56: 4440–4449.
[28] Dreiling I, Raisch C, Glaser J, Stiens D, Chasse T. Temperature dependent tribo-oxidation of Ti-B-N coatings studied by Raman spectroscopy [J]. Wear, 2012, 288: 62–71.
[29] Keunecke M, Bewilogua K, Wiemann E, Weigel K, Wittorf R, Thomsen H. Boron containing combination tool coatings-characterization and application tests [J]. Thin Solid Films, 2006, 494: 58–62.
[30] Aouadi S M, Namavar F, Gorishnyy T Z, Rohde S L. Characterization of TiBN films grown by ion beam assisted deposition [J]. Surface and Coatings Technology, 2002, 160: 145–151.
[31] Shimada S, Takahashi M, Kiyono H, Tsujino J. Coatings and microstructures of monolithic TiB2 films and double layer and composite TiCN/TiB2 films from alkoxide solutions by thermal plasma CVD [J]. Thin Solid Films, 2008, 516: 6616–6621.
[32] Yu Li-hua, Zhao Hong-jiang, Xu Jun-hua. tribological and corrosion performance of WBN composite films deposited by reactive magnetron sputtering [J]. Applied Surface Science, 2014, 315: 380–386.
[33] Lv Wen-quan, Wang Lang-ping, Cao Yong-zhi, Gu Zhi-wei, Wang Xiao-feng, Yang yong-da, Yu Fu-li. Effect of cathode composition on microstructure and tribological properties of TiBN nanocomposite multilayer coating synthesized by plasma immersion ion implantation and deposition [J]. Chinese Physics Letters, 2015, 270: 290–298.
[34] Wang lang-ping, Xie Zhi-wen, Huang Lei, Wang Xiao-feng. MoS2/Ti multilayer deposited on 2Cr13 substrate by PIIID [J]. Nuclear Instruments and Methods in Physics Research Section B: Beam Interactions with Materials and Atoms, 2008, 266: 730–733.
[35] Mirkarimi P B, McCarty K F, Medlin D L. Review of advances in cubic boron nitride film synthesis [J]. Materials Science and Engineering R: Reports, 1997, 21: 47–100.
[36] McKenzie D R, McFall W D, Sainty W G, Davis C A, CollinS R E. Compressive stress induced formation of cubic boron nitride [J]. Diamond and Related Materials, 1993, 2: 970–976.
[37] ThEvenot F. Boron carbide—A comprehensive review [J]. Journal of the European Ceramic Society, 1990, 6: 205–225.
(Edited by YANG Hua)
Cite this article as: L
Wen-quan, CAO Yong-zhi, WANG Lang-ping, WANG Xiao-feng, GU Zhi-wei, YAN Yong-da, YU Fu-li. Effect of cathode composition on microstructure and tribological properties of TiBN nanocomposite multilayer coating synthesized by plasma immersion ion implantation and deposition [J]. Journal of Central South University, 2017, 24(10): 2238–2244. DOI:https://doi.org/10.1007/s11771-017-3633-3.
Foundation item: Projects(21573054, 21327002, 51401201) supported by the National Natural Science Foundation of China; Project(U1537214) supported by the Joint Funds Key Project of the National Natural Science Foundation of China; Project(51535003) supported by the State Key Program of National Natural Science of China
Received date: 2016-05-12; Accepted date: 2016-10-20
Corresponding author: CAO Yong-zhi, Associate Professor, PhD; Tel: +86–13796028137; E-mail: cflying@hit.edu.cn