
Preparation of ZrN-Si3N4 composite powder with zircon and carbon black as raw materials
MA Bei-yue(马北越), YU Jing-kun(于景坤)
School of Materials and Metallurgy, Northeastern University, Shenyang 110004, China
Received 22 December 2008; accepted 1 April 2009
Abstract: ZrN-Si3N4 composite powder with low cost from zircon was prepared by carbothermal reduction-nitridation process. The influence of mass ratio of C to ZrSiO4 (m(C)/m(ZrSiO4)) and soaking time on phase composition and microstructure of the products was studied by means of XRD and SEM-EDS. The formation process of ZrN-Si3N4 composite powder was also analyzed in detail. The results show that with the increase of m(C)/m(ZrSiO4) and soaking time, the formation of Si3N4 and ZrN can be promoted obviously. The ZrN-Si3N4 composite powder with size of 1-2 μm can be obtained at 1 773 K for 12 h when m(C)/m(ZrSiO4) is 0.4.
Key words: ZrN; Si3N4; zircon; carbothermal reduction
1 Introduction
In recent years, some nitrides ceramic and composite materials have been gained much attention, due to their high melting point, hardness and strength, excellent oxidation and corrosion resistance, such as zirconium nitride(ZrN)[1], silicon nitride(Si3N4)[2], Si3N4-TiN[3], Si3N4-Al[4] and SiAlON[5]. Their application fields involve metallurgical, mechanical, electronic and space navigation industries. To obtain high-quality ceramic powder is of much importance for fabrication of outstanding ceramic materials. Si3N4 powder can be obtained successfully by many technology processes, such as combustion synthesis[6], microwave synthesis[7], sol-gel synthesis[8] and carbothermal reduction-nitridation process[9]. Carbothermal reduction-nitridation process has been regarded as a potentially beneficial method to synthesize Si3N4 powder with low cost, using cheap raw materials like diatomite[10] and sepiolite[11] as well as waste materials such as iron ore tailings[12] and rice husks[13]. So far, there has been less report on synthesis of ZrN-Si3N4 composite powder from zircon.
In this work, zircon (ZrSiO4) and carbon black were used as raw materials for preparation of ZrN-Si3N4 composite powder by carbothermal reduction-nitridation process. The influence of mass ratio of C to ZrSiO4 (m(C)/m(ZrSiO4)) and soaking time on phase composition and microstructure of the products was investigated by X-ray powder diffraction analysis and scanning electronic microscopy with energy dispersive spectroscopy.
2 Experimental
2.1 Raw materials
Zircon and carbon black were used as the raw materials. Average size of zircon is less than 44 μm, and the chemical compositions of zircon in mass fraction are 66.75% ZrO2, 32.34% SiO2, 0.42% Al2O3, 0.11% TiO2, 0.07% Fe2O3, 0.02% CaO and 0.02% MgO. Carbon black was chosen as the reducing agent with average particle size less than 30 μm. C content in carbon black in mass fraction was 98.0%, and the purity of nitrogen gas (N2) was 99.99%.
2.2 Preparation of samples
The overall reaction equation for the fabrication of ZrN-Si3N4 composite powder from zircon by carbothermal reduction-nitridation process can be expressed as
6ZrSiO4(s)+24C(s)+7N2(g)=6ZrN(s)+2Si3N4(s)+24CO(g) (1)
According to Eq.(1), the mass ratio of carbon black to zircon (m(C)/m(ZrSiO4)) is 0.26. In the present work, m(C)/m(ZrSiO4) was chosen as 0.2, 0.3, 0.4 and 0.5, respectively. This over-stoichiometry of carbon black is necessary to promote the carbothermal reduction- nitridation reaction. The powders of zircon and carbon black were mixed (in anhydrous ethanol) for 24 h in a ball mill, dried fully at 333 K and then mixed for 10 h. The samples with 20 mm in diameter and 5 mm in thickness were pressed at 60 MPa, dried fully at 393 K, put into a graphite crucible, placed in a vertical tubular furnace with 1.0 L/min nitrogen gas and heated at 1 773 K for 6, 9 and 12 h, respectively. After the desired reaction temperature and time were reached, the system was cooled to room temperature in air. The heated samples were oxidized in air at 973 K for 2 h to remove residual carbon.
2.3 Characterization of samples
All the products obtained under different experimental conditions were characterized by XRD (X-ray powder diffraction) with Cu Kα radiation at 30 kV and 30 mA, SEM (scanning electronic microscope), and EDS (energy dispersive spectroscope).
3 Results and discussion
3.1 Phase composition and microstructure of products
In Fig.1 the samples with various m(C)/m(ZrSiO4) of 0.2(S20), 0.3(S30), 0.4(S40) and 0.5(S50) were heated at 1 773 K for 9 h. It is shown that raw materials composition has an obvious effect on phase composition of the products. With the increase of carbon black content in sample, the diffraction peak intensities of ZrN and Si3N4 phases increase gradually, indicating that increasing the carbon content in sample can promote the carbothermal reduction-nitridation reaction. However, surplus carbon can accelerate the formation of SiC, such as the sample S50 at 2θ≈60? as shown in Fig.1. It was reported that surplus carbon had an active effect on the formation of both Si3N4 and SiC during the synthesis process of Si3N4 by carbothermal reduction-nitridation reaction at above 1 743 K[14]. Therefore, the proper m(C)/m(ZrSiO4) to synthesize ZrN-Si3N4 composite powder from zircon by carbothermal reduction- nitridation process is 0.4.
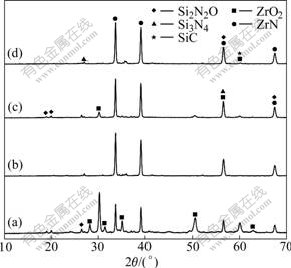
Fig.1 XRD patterns of samples with m(C)/m(ZrSiO4) of 0.2 (a), 0.3 (b), 0.4 (c) and 0.5 (d) heated at 1 773 K for 9 h
Fig.2 shows the XRD patterns of the samples with m(C)/m(ZrSiO4) of 0.4 heated at 1 773 K for 6, 9 and 12 h, respectively. It can be seen that with the increase of soaking time, the diffraction peak intensities of ZrN and Si3N4 increase gradually; however, the intensities of ZrO2 and Si2N2O weaken. The product synthesized at 1 773 K for 6 h includes ZrN, ZrO2, Si2N2O and Si3N4 phases. ZrN phase is mainly crystal one, and the diffraction peak intensity of Si3N4 phase is very weaker than that of others. When the soaking time reaches 9 h, some Si2N2O in the product synthesized at 1 773 K for 6 h converts into Si3N4, at 2θ≈26.5? as shown in Fig.2. In addition, when the soaking time reaches 12 h, the ZrO2 and Si2N2O phases vanish, the product is composed of ZrN and Si3N4 phases, and the diffraction peak intensity of ZrN or Si3N4 is higher than that obtained at 1 773 K for 6 h or 9 h. This indicates that increasing the soaking time can promote the formation of ZrN and Si3N4.
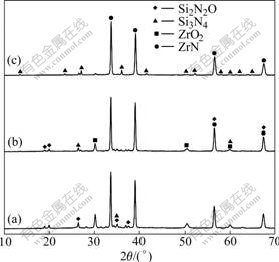
Fig.2 XRD patterns of samples with m(C)/m(ZrSiO4) of 0.4 heated at 1 773 K for 6 h (a), 9 h (b) and 12 h (c)
Fig.3 shows the SEM photographs of the samples with various m(C)/m(ZrSiO4) heated at 1 773 K for 9 h. It is seen in Fig.3(a) that m(C)/m(ZrSiO4) of 0.2 is not sufficient for reduction of zircon, which leads to the formation of Si2N2O and a small amount of Si3N4. In addition, the acicular Si3N4 whiskers are produced by gas-gas mechanism (reaction (2)). Silicon monoxide (SiO) and carbon monoxide (CO) are produced by the reaction between ZrSiO4 and C in sample (reaction (3)). For m(C)/m(ZrSiO4) values of 0.3 and 0.4, the products consist of granular and columnar materials, and the nitrides are grown well. While for the sample with m(C)/m(ZrSiO4) of 0.5, a small amount of SiC with exiguous crystal grain produces.
3SiO(g)+3CO(g)+2N2(g)=Si3N4(s)+3CO2(g) (2)
ZrSiO4(s)+C(s)=ZrO2(s)+SiO(g)+CO(g) (3)
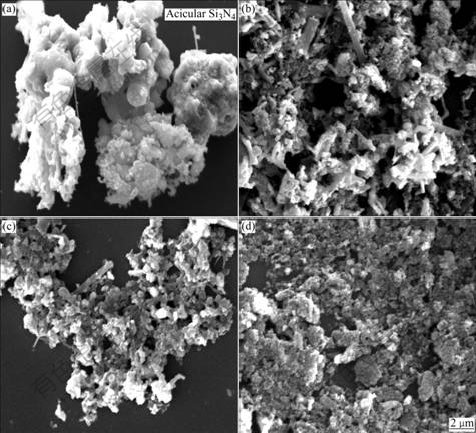
Fig.3 SEM images of samples with various m(C)/m(ZrSiO4) of 0.2 (a), 0.3 (b), 0.4 (c) and 0.5 (d) heated at 1 773 K for 9 h
Fig.4 shows the SEM photographs of the samples with m(C)/m(ZrSiO4) of 0.4 heated at 1 773 K. The average particle size of the powders synthesized at 1 773 K for 6, 9 and 12 h is 1-2 μm. EDS analysis indicates that the near-spherical materials as shown in Fig.4(c) are composed of ZrN and Si3N4 as well as a small amount of ZrO2 and C.
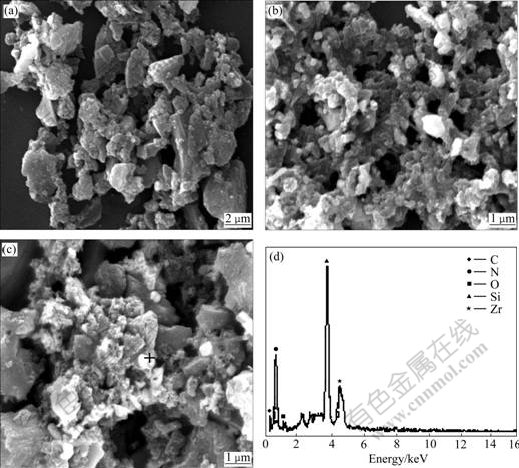
Fig.4 SEM images of samples with m(C)/m(ZrSiO4) of 0.4 heated at 1 773 K for 6 h (a), 9 h (b) and 12 h (c) and EDS spectrum (d) of synthesized powder at 1 773 K for 12 h
3.2 Analysis of synthesis process
In this experimental condition, the synthesis process of ZrN-Si3N4 composite powder by carbothermal reduction-nitridation reaction is very complex and involves many chemical reactions. During the synthesis process, an important intermediate gas phase product is carbon monoxide. With the change of the raw materials composition (m(C)/m(ZrSiO4)), the reaction products maybe involve ZrO2, Si2N2O, Si3N4, ZrN and SiC. According to the relational thermodynamic data as listed in Ref.[15], the relationship between standard Gibbs energy
and temperature(T) can be calculated. The chemical reactions likely to occur during the synthesis process and the relational expression of
and
are as follows:
2ZrSiO4(s)+3C(s)+N2(g)=2ZrO2(s)+Si2N2O(s)+3CO(g)
(J/mol) (4)
3/2ZrSiO4(s)+3C(s)+N2(g)=
3/2ZrO2(s)+1/2Si3N4(s)+3CO(g)
(J/mol) (5)
ZrSiO4(s)+7/2C(s)+N2(g)=
ZrN(s)+1/2Si2N2O(s)+7/2CO(g)
(J/mol) (6)
6/7ZrSiO4(s)+24/7C(s)+N2(g)=
6/7ZrN(s)+2/7Si3N4(s)+24/7CO(g)
(J/mol) (7)
2ZrSiO4(s)+10C(s)+N2(g)=
2ZrN(s)+2SiC(s)+8CO(g)
(J/mol) (8)
Fig.5 shows the diagram of
—T for nitrides obtained from the reactions (4)-(8).

Fig.5 Diagram of
—T for nitrides in ZrSiO4-C-N2 system
According to the thermodynamic analysis,
for reaction (4) keeps negative at the temperatures higher than 1 700 K. In this study, when temperature rises to 1 773 K, ZrSiO4 can react with C to produce Si2N2O easily, which is confirmed by the XRD patterns (Fig.1).
and
for reactions (5), (6), (7) and (8) decrease with the increase of temperature, and become negative when temperature reaches 1 835, 1 807, 1 867 and 1858 K, respectively. These tempera- tures are higher than the actual ones that Si2N2O, Si3N4, ZrN and SiC can be synthesized. The main reason is that the thermodynamic analysis is on the assumption that all the pressures of gas phases are 1.0×105 Pa, while the actual pressure of CO gas are very low in this experimental condition. In addition, surplus carbon in sample may also reduce the formation temperatures of Si2N2O, Si3N4, ZrN and SiC. It can also be seen that compared with reaction (4), the reactions (5)-(8) cannot generate easily at 1 773 K.
Moreover, between 1 700 and 1 773 K (the experimental temperature),
for reactions (4)-(8) are in the order as follows:
(ZrO2 or Si2N2O)<
(ZrO2 or Si3N4)<
(ZrN or Si2N2O)<
(ZrN or Si3N4)<
(ZrN or SiC). This indicates that Si2N2O can be more easily synthesized than Si3N4 in the same experimental condition. With the increase of carbon black content (m(C)/m(ZrSiO4)=0.3, 0.4 and 0.5), Si2N2O can convert into Si3N4 (reactions (9) and (10)). Meanwhile, surplus carbon can promote the formation of SiC (reactions (11) and (12)).
Si2N2O(s)+SiO2(s)+3C(s)+N2(g)=Si3N4(s)+3CO(g) (9)
3Si2N2O(s)+3C(s)+N2(g)=2Si3N4(s)+CO(g) (10)
Si2N2O(s)+3C(s)=2SiC(s)+CO(g)+N2(g) (11)
Si3N4(s)+3C(s)=3SiC(s)+2N2(g) (12)
During the synthesis process, ZrO2 is converted into ZrN gradually:
2ZrO2(s)+4C(s)+N2(g)=2ZrN(s)+4CO(g) (13)
In this experiment, the formation process of ZrN-Si3N4 composite powder can be summarized as follows:
1) When carbon content in sample is lower than 0.26, SiO2 in sample reacts with C and N2 to produce Si2N2O, and there is an extremely small amount of acicular Si3N4. At the same time, part of ZrO2 in sample is nitridized to form ZrN.
2) When carbon content in sample is higher than 0.26, SiO2 in sample can react with C and N2 to synthesize Si2N2O, and further to produce Si3N4. The carbothermal reduction-nitridation process is accompanied by the nitridation of ZrO2 to form ZrN.
4 Conclusions
1) ZrN-Si3N4 composite powder can be successfully prepared from zircon by carbothermal reduction- nitridation process, and the proper parameters at 1 773 K to synthesize ZrN-Si3N4 are m(C)/m(ZrSiO4) of 0.4 and soaking time of 12 h.
2) SEM results show that the nitrides as-received in this experiment exist in granular, columnar and acicular shape, and the average particle size of the synthesized powders is 1-2 μm.
3) The formation process of ZrN-Si3N4 composite powder includes the formation of Si2N2O and Si3N4 as well as the nitridation process of ZrO2.
References
[1] FU B, GAO L. Synthesis of nanocrystalline zirconium nitride powders by reduction-nitridation of zirconium oxide [J]. J Am Ceram Soc, 2004, 87(4): 696-698.
[2] CHOCKALINGAM S, AMARAKOON V R W. 2.45 GHz microwave sintered Si3N4-ZrO2 composites [J]. J Ceram Soc Japan, 2008, 116(6): 700-705.
[3] TATAMI J, KODAMA E, WATANABE H, NAKANO H, WAKIHARA T, KOMEYA K, MEGURO T, AZUSHIMA A. Fabrication and wear properties of TiN nanoparticle-dispersed Si3N4 ceramics [J]. J Ceram Soc Japan, 2008, 116(6): 749-754.
[4] AKHTAR F, GUO Shi-ju. Development of Si3N4/A1 composite by pressureless melt infiltration [J]. Trans Nonferrous Met Soc China, 2006, 16(3): 629-632.
[5] YAMAKAWA T, WAKIHARA T, TATAMI J, KOMEYA K, MEGURO T. Synthesis of β-SiAlON from a zeolite by reduction nitridation in a miture of NH3-C3H8 [J]. J Ceram Soc Japan, 2008, 116(2): 325-328.
[6] CHEN Y X, LI J T, DU J S. Cost effective combustion synthesis of silicon nitride [J]. Mater Res Bull, 2008, 43(6): 1598-1606.
[7] YANG Jun, XIA Guang-bin, PENG Hu, LI Zhi-jie. Microwave synthesis of Si3N4 powder [J]. Materials Review, 2007, 21(11A): 127-129. (in Chinese)
[8] GAO J M, XIAO H N, DU H Q. Effect of Y2O3 addition on ammono sol-gel synthesis and sintering of Si3N4-SiC nanocomposite powder [J]. Ceram Int, 2003, 29(6): 655-661.
[9] ORTEGA A, ALCAL? M D, REAL C. Carbothermal synthesis of silicon nitride (Si3N4): Kinetics and diffusion mechanism [J]. J Mater Process Tech, 2008, 195(1/3): 224-231.
[10] ARIK H. Synthesis of Si3N4 by the carbo-thermal reduction and nitridation of diatomite [J]. J Eur Ceram Soc, 2003, 23(12): 2005-2014.
[11] KURT A O, DAVIES T J. Synthesis of Si3N4 using sepiolite and various sources of carbon [J]. J Mater Sci, 2001, 36(24): 5895-5901.
[12] ZHANG Shu-hui, XUE Xiang-xin, L? Qing, HUANG Da-wei. Study on synthesis of silicon nitride powders from iron ore tailings [J]. Iron and Steel, 2008, 43(9): 82-87. (in Chinese)
[13] REAL C, ALCAL? M D, CRIADO J M. Synthesis of silicon nitride from carbothermal reduction of rice husks by the constant-rate-thermal-analysis (CRTA) method [J]. J Am Ceram Soc, 2004, 87(1): 75-78.
[14] QIU Tai, XU Jie, GONG Yi-nong, LI Yuan-qiang. A study of synthesis of Si3N4 powder by carbothermal reduction [J]. Bull Chin Ceram Soc, 1995, 23(5): 14-19. (in Chinese)
[15] LIANG Ying-jiao, CHE Yin-chang. Handbook of thermodynamic data in inorganic [M]. Shenyang: Northeastern University Press, 1993. (in Chinese)
Foundation item: Project(50274021) supported by the National Natural Science Foundation of China and Baoshan Iron and Steel Co., Ltd.
Corresponding author: MA Bei-yue; Tel: +86-24-83673860; Fax: +86-24-83687731; E-mail: beiyue_ma@yahoo.com.cn
DOI: 10.1016/S1003-6326(08)60432-X
(Edited by YANG Hua)