DOI:10.19476/j.ysxb.1004.0609.2018.12.20
采用铝阴极从硫酸锰溶液中电沉积金属锰
杨 凡,蒋良兴,于枭影,杨 健,赖延清,吕晓军,李 劼
(中南大学 冶金与环境学院,长沙 410083)
摘 要:在MnSO4-(NH4)2SO4溶液中,以铝板为阴极电沉积金属锰,分别研究电流密度、电解液成分、温度等因素对阴极电流效率、能耗和阴极产物的影响。结果表明:在含Mn2+溶液浓度为30 g/L、(NH4)2SO4浓度为130 g/L、SeO2浓度为0.04g /L、初始pH值为7.0、电流密度为400 A/m2、电解温度为35 ℃时,铝阴极的阴极电流效率为85.8%,能耗为4870.9 kW·h/t,得到的金属锰纯度高于99.5%,晶型为α-Mn。与传统不锈钢阴极(0Cr19Ni9)对比,Mn2+在铝阴极表面的起始沉积电位与在不锈钢阴极表面的相同,但在电沉积初期可以抑制H2的析出;铝阴极可加速Mn2+的电沉积,增加阴极电流效率,降低直流电耗;同时,铝阴极可以抑制SeO32-的还原,减小添加剂SeO2的消耗量,提高阴极锰的纯度。因此,金属铝具备替代不锈钢作为电沉积金属锰的潜力。
关键词:锰电解;铝阴极;电流效率;能耗;SeO2
文章编号:1004-0609(2018)-12-2568-12 中图分类号:TF813 文献标志码:A
金属锰作为一种重要的工业金属添加剂,大量应用于钢铁、有色金属合金和电子元件制造行业[1-3]。生产电解金属锰是典型的“两高一资”(高能耗、高污染和资源性)行业[4-6]。在电解锰生产过程中,电耗和阴极电流效率主要取决于电极表面锰的电沉积和析氢反应的相互竞争。由于金属锰的沉积电位(vs SHE)较负(φ(Mn2+/Mn)=-1.18 V),需要尽量提高析氢反应的过电位,降低析氢速率,而析氢过电位与电解液的成分以及电极材料等因素关系密切[7]。目前,大量研究集中于锰电解过程中添加剂的加入对析氢过程的影响[8-15],关于阴极材料本身对锰的沉积过程、沉积形貌以及电流效率影响的研究较少。电解锰过程一直沿用不锈钢作为阴极,钛基材料和哈氏合金作为阴极也有过应用报道[16]。不同的阴极材料会对初始锰沉积层产生显著影响,选择具有较高析氢过电位的基底能降低初始阶段析氢反应的能耗。工业用不锈钢阴极的析氢过电位较金属锰的约低120 mV,采用不锈钢沉积金属锰时,初期的阴极电流效率较低,当金属锰逐渐覆盖不锈钢表面后,电流效率随之提高。为了降低析氢反应造成的能耗损失,加速锰离子在不锈钢表面的形核,需要在电解液中加入SeO2等添加剂,这不仅增加了成本、降低了产品的质量,还造成了环境污染[17]。随着高质量锰矿资源日益匮乏,如何高效、环保地利用有限的资源,从电极材料角度出发,降低电解过程的能耗对锰行业的可持续发展有重要意义[18]。
理想的锰电解阴极材料需具备以下性能:高的析氢过电位;在阴极液中稳定;较好的导电性和延展性、阴极基底和锰镀层的结合能力适中[16]。有研究表明[19]:在MnSO4-(NH4)2SO4溶液体系中,不同的阴极基底对应的析氢过电位由高到低为:Al,Mn,Ti,Cu,不锈钢。由于不锈钢中不同程度地含有Ni,而Ni及其合金能催化阴极表面的析氢反应,析氢反应的强烈程度随不锈钢中Ni含量的增加而增加[20-21]。锌电积过程常选用纯铝板做阴极,其原因是:铝的导电能力强,在酸性溶液中有强的耐腐蚀性和高的析氢过电 位[22]。与不锈钢相比,若将铝用于锰电解阴极,将具备以下特点。
1) 铝的氧化/还原电位(vs SHE)较负(-1.66 V),但其表面极容易自发生成一层致密的氧化膜层,该膜层与基体结合牢固,在酸性溶液中的耐腐蚀能力较不锈钢强,可以减小极板在溶解残锰过程中造成的极板损失以及杂质离子铁的引入。2) 更高的析氢过电位有利于提高锰电解初期的阴极电流效率,减小析氢反应造成的能耗损失。3) 铝板的质量较不锈钢轻,可以减轻工作人员在出装槽时的工作强度,避免极板划破隔膜造成电解液pH波动带来的风险。4) 铝的导电能力较不锈钢好,可提高电力线的分布均匀性。5) 铝板的价格较不锈钢板低,可以降低极板的生产成本,带来较大的经济利润。因此,铝具有较大潜力作为电解锰用阴极材料。
本文拟以纯铝阴极为研究对象,重点研究电流密度、电解液成分、温度等因素对阴极电流效率、能耗和沉积产物的影响,优化电解工艺条件,并与不锈钢阴极对比,评价纯铝作为电解锰过程阴极材料的可行性和技术经济指标,促进锰电解过程的节能降耗。
1 实验
1.1 实验试剂
电解液采用自制二次蒸馏水溶解一定质量的分析纯一水合硫酸锰(MnSO4·H2O)、硫酸铵((NH4)2SO4) 和二氧化硒(SeO2) 制得。
1.2 电沉积实验
电沉积实验在自制的有机玻璃槽中进行,电解槽由对称分布的阴、阳极室构成,通过隔膜分开,每个室的有效体积为0.2 L。阴极为304不锈钢板或铝板,将其切割成20 mm×20 mm×3 mm的试样,经焊接Cu导线和义齿基托树脂密封获得工作面积为4 cm2的工作电极。阳极采用Pb-0.9%Ag合金(质量分数),将其切割成15 mm×15 mm×3 mm的试样,同样经焊接Cu导线和义齿基托树脂密封获得2.25 cm2的工作面积。
每次实验取配好的溶液0.4 L加入电解槽中,水浴加热电解液至目标温度后用NH3·H2O或H2SO4调节阴极液的pH至目标值。将打磨并清洗好的电极插入两个极室,保持阴、阳极极间距为3 cm。采用恒流源控制电流强度,通过水浴加热控制电解液温度变化范围在±1 ℃,实验过程记录槽电压和阴极电位的变化。电积2 h后快速取出阴极并用去离子水冲洗电极表面残余的电解液,随即将阴极放入3%的重铬酸钾溶液中钝化处理1 min,去离子水冲洗后快速吹干。将阴极置于电热鼓风干燥箱内在70 ℃下干燥12 h后称量,计算电积前后阴极质量的变化,通过式(1)计算阴极电流效率,式(2)计算电能消耗。
(1)
式中:η为阴极电流效率,%; m为阴极电解前后质量的变化,kg;n为电子数,n=2;F为法拉第常数,F=96485 C/mol; I为电流强度,A;t为电解时间,s;M为锰的相对原子质量,MMn=55。
(2)
式中:W为能耗,kW·h/t;U为槽电压,V;QMn为金属锰析出的理论耗电量,975.87 kA·h/t。
将阴极产物从极板上剥离,采用SEM-EDS (Quanta-200) 观察阴极产物的形貌。通过XRD (D/max-2200) 在2θ为10°~85°,扫描速度8.0 (°)/min条件下检测阴极产物的结晶特性。
采用pH3c型精密酸度计测量并记录电解液的酸度,取部分阴极液稀释后用PS-6型电感耦合等离子体原子发射光谱仪 (ICP-AES 美国 baird) 检测溶液中Se的浓度。
1.3 阴极极化测试
阴极的极化测试在PARSTAT 2273电化学工作站进行,采用传统的三电极体系。工作电极选用与电积实验相同的铝板或304不锈钢板,工作面积经为1 cm2。工作电极打磨清洗后在硝酸溶液(体积比为1:1) 中超声震荡20 min,无水乙醇中震荡20 min,最后用二次蒸馏水洗涤数次后再超声震荡20 min待用。对电极采用表观面积为4 cm2的石墨电极,参比电极为 Hg/Hg2SO4/饱和K2SO4 (0.64 V vs SHE)。如无特殊说明,文中所有电位均参照该参比电极。
1.4 电积过程原理
电积过程的阴极反应如式(3)和(4)所示:
Mn2++2e=Mn,
-1.82 V (3)
2H2O+2e=H2+2OH-,
-1.31 V (4)
式(4)是锰沉积过程的副反应,降低式(4)的反应速率可以有效地提高阴极电流效率。由于不锈钢表面氢气的析出过电位较高,使得Mn2+和H2O能在阴极同时放电析出。由Tafel公式(见式(5))可知,在高极化区,H2在金属上的析出过电位与电流密度的对数值存在线性关系,其中Tafel常数a、b主要由电极材料的自身性质决定,通过常数b可分析析氢反应的速控步骤。在中性或偏碱性溶液中式(4)通常经历H2O在电极表面放电生成吸附氢(见式(6))、吸附氢的复合解析(见式(7))或吸附氢的电化学解析(见式(8))几个步骤[23]。
η=a+b log J (5)
H2O+e=Hads+OH- (b=118 mV/dec, α=0.5) (6)
2Hads=H2 (b=29.5 mV/dec) (7)
H2O+Hads+e=H2+OH- (b=39.3 mV/dec, α=0.5) (8)
铝的氧化/还原电位较负,但铝表面极易生成一层致密的氧化膜层,析氢反应和锰的电沉积反应主要在氧化膜层上进行。电子在到达阴极的反应活性位点前需要跨越金属和氧化膜层之间的位垒,氧化膜层的存在增加了析氢反应的表观活化能,从而增加了H2的析出难度。有研究表明[24],中性溶液中,铝表面析氢反应的速率控制步骤为式 (6),即吸附氢的生成反应。增加吸附氢的生成难度有利于抑制析氢反应的发生。吸附氢的生成主要受电极材料的性质和电解液的成分控制。锰电解过程中需要加入硫酸铵来增加溶液的导电能力和抑制硫酸锰的水解,但在高的极化电位下NH4+也会发生以下反应[7, 13, 16, 25]:
NH4++e→Hads+NH3ads (9)
NH4+的放电会增加电极表面的吸附氢,从而诱导析氢反应。铝通过抑制吸附氢的生成,可减弱硫酸铵的催化析氢效应,从而降低电沉积初期的反应能耗。
2 结果与分析
2.1 电解条件优化实验
采用单因素试验方法,与电解锰常用的304不锈钢阴极对比,考察铝阴极在不同电流密度、(NH4)2SO4浓度、初始Mn2+浓度、初始阴极液pH值、初始SeO2浓度、电解温度6个条件下对电流效率和能耗的影响。
2.1.1 阴极电流密度
实验条件如下:电解时间2 h、初始阴极液pH值7.0、(NH4)2SO4浓度110 g/L、初始Mn2+浓度20 g/L、初始SeO2浓度0.02 g/L、电解温度30 ℃,改变阴极电流密度,考察阴极电流密度对锰沉积的影响。实验结果如图1所示。
由图1(a)可知,随阴极电流密度的增加,两种阴极表现出相同的变化规律,当阴极电流密度小于400 A/m2时,阴极电流密度的增加有助于电流效率的提高。阴极表面除了进行着析氢和沉锰反应之外,还存在着沉积锰的溶解反应。通过检测阴极电位发现,阴极电位随着电流密度的升高而向负方向移动。一般来说,阴极电位较正时,锰的自溶解速率较大,造成低电流密度时电流效率的降低。电流密度为400 A/m2时,不锈钢和铝阴极的电流效率均达到考察范围内的最大值,分别为82.68%和82.93%。超过极值电流密度后电流效率开始下降,但不锈钢阴极的下降速率大于铝阴极的。舒余德等[26]采用分电流曲线的方法证实了高电流密度条件下氢的分电流密度急剧增加,即电流密度增大后H2O的放电速率增大,Mn2+的放电受到抑制,析氢反应加剧,导致阴极电流效率降低。铝阴极较大的析氢过电位导致在高的电流密度下Mn2+的放电优于不锈钢的,这可以通过阴极液的pH值来验证。随电流密度的增加,阴极液的pH值均呈现增大的趋势,不锈钢和铝阴极电解2 h后阴极液的pH值分别为7.40和7.32,说明电流密度升高后不锈钢阴极的析氢反应更剧烈,该结果与LU等[27]的结论一致。说明采用铝阴极可在较宽的电流密度范围内沉积金属锰,对扩大锰电解的产能有利。
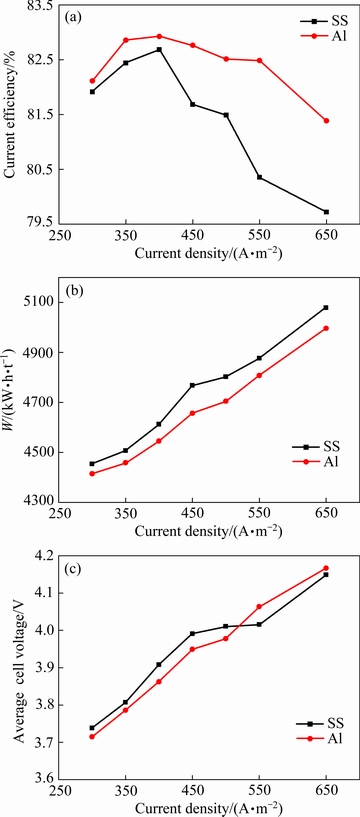
图1 不同阴极条件下阴极电流密度对阴极电流效率、能耗和平均槽压的影响
Fig. 1 Effects of cathode current density on cathodic current efficiency(a), energy consumption(b) and average cell voltage(c) with different cathodes
由图1(b)可知,电解能耗随电流密度的增加呈现不断上升的趋势,与槽电压的变化趋势基本一致,说明能耗增加的原因主要来自于槽电压的升高。
由图1(c)可知,当阴极电流密度大于450 A/m2时,平均槽电压出现一个较小的平台;当阴极电流密度超过500 A/m2后,铝阴极的平均槽压明显高于不锈钢阴极的。在选择电流密度时需要同时考虑阴极的产量和槽电压,电流密度较低时槽电压较低,单位时间内阴极的产量也较低。综合考虑,本文选择400 A/m2为阴极电流密度。
2.1.2 (NH4)2SO4浓度
实验条件如下:电解时间2 h、电流密度400 A/m2、初始阴极液pH值7.0、初始Mn2+浓度20 g/L、初始SeO2浓度0.02 g/L、电解温度30℃,改变(NH4)2SO4浓度,考察(NH4)2SO4浓度对锰沉积的影响。实验结果如图2所示。
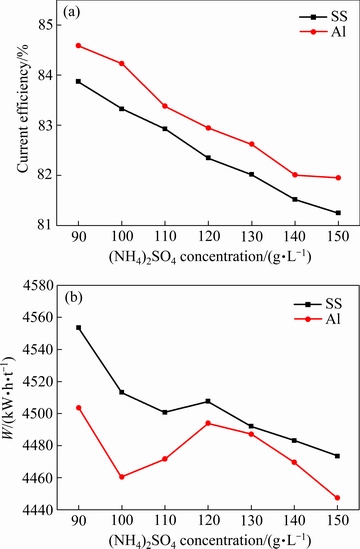
图2 不同阴极条件下(NH4)2SO4浓度对阴极电流效率和能耗的影响
Fig. 2 Effects of cathode current density on cathodic current efficiency(a) and energy consumption(b) with different cathodes
由图2可知,随(NH4)2SO4浓度的增加,阴极电流效率逐渐降低。但(NH4)2SO4的加入可以提高溶液的电导率,减小溶液电阻,进而减小阴阳极板之间的溶液电压降。(NH4)2SO4浓度由90 g/L增至150 g/L时,槽电压由3.9 V降至3.7 V。(NH4)2SO4浓度的增加会增大锰离子放电过程的复杂性,由式(8)可知,NH4+在阴极放电会增加溶液中的NH3浓度,溶液中的Mn2+可以与NH3形成Mn(NH3)2+、Mn(NH3)22+等离子配位体[16]。锰氨络合物是良好的缓冲剂,自由Mn2+的浓度随(NH4)2SO4浓度的增加而减小,从而抑制了Mn2+的水解,但同时也增加了Mn2+放电反应的活化能。锰氨络合物放电通常经历以下步骤:1) 脱去配位体;2) 放电形成吸附态的Mnads+;3) Mnads+放电后并入晶格形成金属锰[28]。锰氨络合物的形成增加了金属锰的析出难度[7],导致电流效率随硫酸铵浓度的升高而降低。同时,电极表面的Hads也随(NH4)2SO4浓度的增加而增加,而铝阴极可以有效地抑制Hads生成,故在高浓度的(NH4)2SO4溶液中,铝阴极的电流效率更高,电积能耗低于不锈钢阴极的。
分析阴极产物的形貌可知,低的(NH4)2SO4浓度下,沉积锰表面分布有较多枝晶,当(NH4)2SO4浓度高于110 g/L后枝晶消失。但(NH4)2SO4浓度过高时,NH4+浓度的增加会加剧氨的挥发,电解锰过程中会有明显的氨气析出[29],从而加速整个电解体系中氨的损失。综合考虑,本文选择(NH4)2SO4浓度130 g/L。
2.1.3 初始Mn2+浓度
实验条件如下:电解时间2 h、电流密度400 A/m2、初始阴极液pH值7.0、(NH4)2SO4浓度130 g/L、初始SeO2浓度0.02 g/L、电解温度30 ℃,改变初始Mn2+浓度,考察Mn2+浓度对锰沉积的影响。实验结果如图3所示。
由图3可知,阴极电流效率随初始Mn2+浓度的升高而增加,能耗则随初始Mn2+浓度的升高而降低。溶液中的自由Mn2+随初始Mn2+浓度的升高而增加,当Mn2+浓度较低时,阴极表面的析氢现象明显,阴极液的pH值迅速增加;当Mn2+浓度较高时,析氢反应受到抑制[12],从而增加电流效率,降低能耗。但当Mn2+浓度高于30 g/L后,电极附近的OH-极容易与自由Mn2+形成Mn(OH)2,增大了电解过程的复杂性。同时Mn2+浓度高于30 g/L后电极表面的枝晶大量生长,降低了沉积层的平整度。
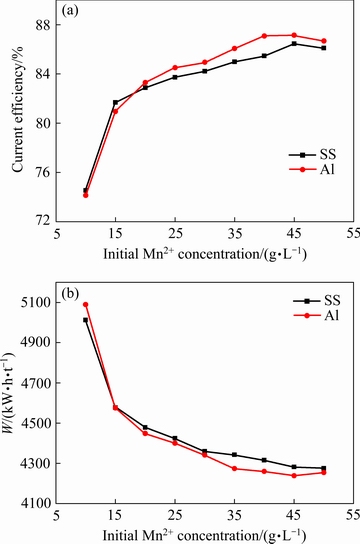
图3 不同阴极条件下Mn2+浓度对阴极电流效率和能耗的影响
Fig. 3 Effects of Mn2+ concentration on cathodic current efficiency(a) and energy consumption(b) with different cathodes
对比不同的阴极可知,当初始Mn2+浓度低于20 g/L时,在沉积金属锰的过程中,不锈钢阴极的电流效率略高于铝阴极的。考虑原因可能来自于Mn2+在铝阴极上的放电速率高于在不锈钢阴极上的:当Mn2+放电较快时,初始Mn2+浓度越低,则越容易造成电极附近Mn2+的贫化,锰的电结晶受阻,电流效率随之降低。当初始Mn2+浓度高于20 g/L后,归功于铝更好的抑制析氢能力,铝阴极沉积金属锰的电流效率高于不锈钢阴极。综合考虑,本文选择初始Mn2+浓度30 g/L。
2.1.4 初始pH值
实验条件如下:电解时间2 h、电流密度400 A/m2、初始Mn2+浓度30 g/L、(NH4)2SO4浓度130 g/L、初始SeO2浓度0.02 g/L、电解温度30 ℃,改变阴极液初始pH值,考察初始pH值对锰沉积的影响。实验结果如图4所示。
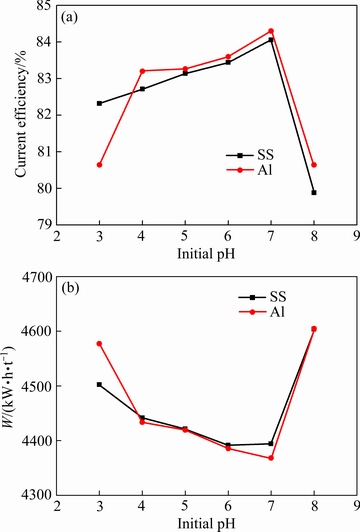
图4 不同阴极条件下初始pH值对阴极电流效率和能耗的影响
Fig. 4 Effects of initial pH value on cathodic current efficiency(a) and energy consumption(b) with different cathodes
由图4可知,随电解液初始pH值的升高,两种阴极表现出相似的变化规律:在低的初始pH值时,电流效率随初始pH值的增加而增加。当初始pH值升高至7时,不锈阴极和铝阴极的电流效率分别增加至84.06%和84.30%;继续增加初始pH值至8后,电流效率又分别降低至79.88%和80.64%。实验过程发现,槽电压基本不随初始pH值发生变化,说明能耗主要受阴极电流效率影响。初始pH值越低,电极表面的析氢反应越剧烈,析氢反应和锰沉积层的自溶解反应会降低电流效率。由Mn-(NH4)2SO4-H2O系的电位-pH图[1]可知,当溶液pH值超过7.5后,Mn(OH)2容易生成,阴极液的颜色变为黄色,黏度增大。且Mn(NH3)2+、Mn(NH3)22+等络合物的浓度随pH值的增加而增加,自由的Mn2+随pH值的增加而降低,从而降低阴极电流效率,故阴极液的初始pH值不宜高于8。
对比不锈钢阴极和铝阴极可知,当初始pH值等于3时,不锈钢阴极的电流效率较高,能耗较低;当初始pH值大于等于4后,铝阴极的电流效率较高,能耗较低。由XING等[30]的研究可知,α-MnSe化合物的生成能显著提高锰电解的电流效率。含硒化合物的稳定性主要受电位和溶液的pH值控制,在低pH值条件下MnSe化合物不稳定,其溶解趋势大于沉积趋势;当pH值大于3后,MnSe化合物逐渐趋于稳定。当pH值等于3时,可能由于MnSe化合物在铝表面的稳定性较差,抑制了初始镀层的形核和生长,使铝阴极的电流效率偏低。pH值大于或等于4后,MnSe化合物在阴极上的沉积趋势大于溶解趋势,含硒化合物在两种阴极表面均达到稳定状态,此时铝阴极的电流效率高于不锈钢的。综合考虑,本文选择初始阴极液pH值为7。
2.1.5 初始SeO2浓度
实验条件如下:电解时间2 h、电流密度400 A/m2、初始Mn2+浓度30 g/L、(NH4)2SO4浓度130 g/L、初始阴极液pH值7.0、电解温度30 ℃,改变初始SeO2浓度,考察SeO2浓度对锰沉积的影响。实验结果如图5所示。
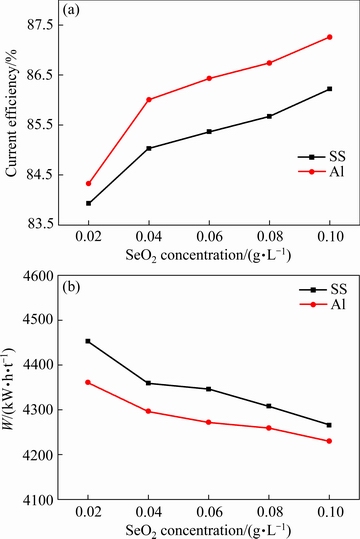
图5 不同阴极条件下 SeO2浓度对阴极电流效率和能耗的影响
Fig. 5 Effects of SeO2 concentration on cathodic current efficiency(a) and energy consumption(b) with different cathodes
由图5 (a) 可知,随SeO2浓度的增加,阴极电流效率均逐渐升高,SeO2浓度超过0.02 g/L后电流效率增加趋势变缓。当SeO2浓度由0.02 g/L增加至0.1 g/L时,不锈钢阴极和铝阴极对应的电流效率分别由83.93%和84.33%增加至86.22%和87.26%。由图5 (b) 可知,能耗的变化趋势与阴极电流效率相反,能耗的降低主要来自于电流效率的提高,槽电压基本稳定于3.80 V左右。大量研究表明[8-16]:SeO2可以强烈抑制析氢反应,增加不锈钢表面的析氢过电位。中性电解液中SeO2主要以SeO32-的形式存在,电解过程中SeO32-在阴极还原为Se0,其在阴极容易继续得到电子还原为多聚阴离子,硒的多聚阴离子吸附于电极表面后增加了氢气的析出难度[31],MnSe化合物的形成可以促进锰在阴极表面的电结晶。故SeO2的加入能显著增加电流效率,降低析氢的能耗。
采用ICP-AES检测两种阴极在不同条件下电解2 h后阴极液中的总硒浓度,结果见图6。
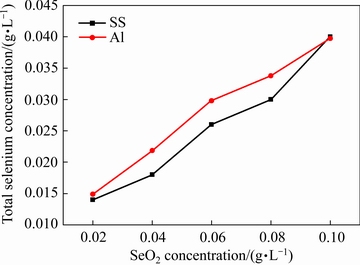
图6 不同阴极条件下SeO2浓度对电解后液中总硒浓度的影响
Fig. 6 Effect of SeO2 concentration on total selenium concentration in catholyte after electrolysis with different cathodes
由图6可知,随SeO2浓度的增加,SeO2的消耗量越大,说明有更多的硒在阴极参与共沉积反应。对比两种阴极可知,采用铝阴极沉积金属锰时,阴极液中的总硒浓度更高,说明铝阴极沉积金属锰时消耗的SeO2较少。取初始SeO2浓度为0.04 g/L电解液得到的阴极产物进行SEM-EDS分析,铝阴极和不锈钢阴极表面产物中硒含量分别为0.34%和0.72%,锰含量分别为99.66%和99.28%。铝阴极产物中的硒含量明显低于不锈钢阴极,该结果与阴极液的ICP检测结果相吻合,说明采用铝阴极电积金属锰可以降低阴极产物中的硒含量,减少SeO2的消耗。
为了对比SeO32-在两种阴极表面的电化学行为,取初始SeO2浓度为0.1 g/L的电解液为研究对象,在-0.8~-1.9V范围内进行循环伏安扫描,溶液温度为30 ℃,扫描速度为20 mV/s。其结果如图7所示。

图7 不同阴极条件下的循环伏安曲线
Fig. 7 Cyclic voltammetry with different cathodes
由图7可知,在-0.8~-1.9V电位区间内,两种阴极表现出明显不同的阴极电化学行为。由XU等[12]的研究和后面的CV曲线可知,该电位区间内主要存在H2的析出反应和SeO32-的还原反应。在负向扫描过程中不锈钢阴极的电流密度明显高于铝阴极,说明该电位区间内,不锈钢阴极的析氢反应更为剧烈。图7中插图所示为-0.8~-1.4V范围内的局部放大图,不锈钢阴极由-0.8 V负向扫描至-1.4 V过程中存在两个明显的还原峰C1(-0.9 V)和C2(-1.25 V),其中C1峰对应SeO32-还原为Se0,C2峰对应Se0进一步还原为Se2-;在正向扫描过程中存在两个明显的氧化峰A1(-1.1 V)和A2(-0.9 V),其中A1峰对应Se2-氧化为Se0,A2峰对应Se0进一步氧化为SeO32- [9, 12, 15, 29]。与不锈钢阴极相比,铝阴极在扫描过程中的电流信号响应微弱,SeO32-较难在铝阴极上发生氧化还原反应,说明铝阴极能有效地抑制SeO32-的还原。金属锰在阴极上的电沉积属于异相形核,SeO32-在不锈钢阴极上的还原电位较Mn2+的还原电位正,Se的快速沉积有助于提供金属锰在不锈钢阴极上形核的中心,故电解液中部分的SeO2损失于基底表面的初始沉积层。铝阴极通过抑制SeO32-的还原从而减少了SeO2的损失,增加了阴极锰的纯度。但由于铝阴极表面具有更高的析氢过电位,阴极电流效率反而有所增加。
由于电解液及阴极产物中的Se含量均随SeO2用量的增加而增加,SeO2的用量不能过高。同时,随电解时间的延长,SeO32-在电泳作用下会富集于隔膜,造成隔膜结板阻碍分子的穿过,从而增加槽电压。综合考虑,本文选择初始SeO2的加入量为0.04 g/L。
2.1.6 溶液温度
实验条件如下:电解时间2 h、电流密度400 A/m2、初始Mn2+浓度30 g/L、(NH4)2SO4浓度130g/L、初始阴极液pH 7.0、初始SeO2浓度0.04 g/L,改变溶液温度,考察温度对锰沉积的影响。实验结果如图8所示。
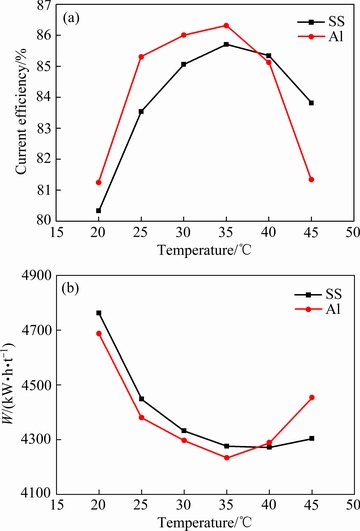
图8 不同阴极条件下温度对阴极电流效率和能耗的影响
Fig. 8 Effect of initial temperature on cathodic current efficiency(a) and energy consumption(b) with different cathodes
由图8可知,温度较低时阴极电流效率随温度升高迅速增加,当温度高于35 ℃后逐渐降低,能耗则随温度的升高先降低后增大。升高温度能增大溶液的电导率,加快离子的传递和扩散,有效地降低溶液电阻和槽电压。电解液温度由20 ℃升高至45 ℃时,不锈钢阴极和铝阴极对应的槽电压分别由3.92 V和3.90 V降低至3.71 V和3.70 V。同时,升高温度能显著地提高反应的速率,降低反应的活化能从而加速锰的沉积。但升高温度的同时也会降低阴极的析氢过电位,加速析氢反应,氢气的大量析出会导致沉积层出现起壳的现象。同时温度过高后电解液体系变得更为复杂,溶液中的Mn2+在高温条件下容易被氧化[32],造成电流效率的降低和能耗的增加。
对比两种阴极可知,当温度低于35 ℃时,铝阴极的电流效率高于不锈钢阴极,当温度高于35 ℃后,铝阴极的电流效率迅速降低。电流效率降低的原因来自于锰沉积层出现起壳脱落的现象,铝阴极的起壳现象较不锈钢阴极严重。说明铝阴极对高温的容忍能力较不锈钢阴极弱。考虑原因来自于高温条件下,铝表面的析氢过电位降低较快,造成电极表面发生强烈的析氢反应,降低了镀层与基底的结合能力,电沉积初期,锰片较薄、抗氢压较小,当气体压力增加到一定程度时,锰片由内向外破裂成卷曲。综合考虑,选择电解温度为35 ℃。
2.2 最佳电解条件
根据单因素条件实验结果,得出最佳电解条件如下:电流密度400 A/m2、(NH4)2SO4浓度130 g/L、初始Mn2+浓度30 g/L、初始pH 7.0、SeO2浓度0.04 g/L、电解温度35℃。为检验各参数的实际效果,取有效面积为41.25cm2的铝板和不锈钢板做阴极,有效面积为23.20 cm2的Pb-0.9%Ag合金板做阳极,进行3组平行验证实验,结果如表1所示。由表1可知,在最优条件下电解2h,与不锈钢阴极相比,铝阴极的电流效率由83.4%提高到85.8%,能耗由4918.7 kW·h/t降低到小4870.9 kW·h/t,表现出很好的节能降耗的潜力。
表1 优化条件下平行验证实验结果
Table 1 Confirmatory experiment results under optimum conditions
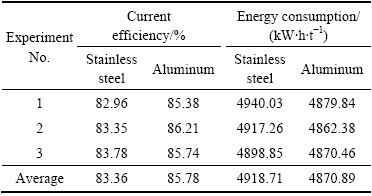
2.2.1 电解锰的表面形貌
在优化条件下,两种阴极沉积得到的锰的表面形貌如图9所示。金属锰主要呈现块状和三角锥状颗粒堆叠而成,其粒径分布较为均匀。其中,铝表面生长的锰颗粒平整致密,粒径较大 (10~15 μm),颗粒多以块状为主。不锈钢表面生长的锰颗粒表面光滑,粒径较小(5~10 μm),多以三角锥状为主。
2.2.2 电解锰的XRD谱
铝阴极和不锈钢表面产物的XRD谱如图10所示。两种阴极得到的电积产物都是α-Mn。其中铝阴极上沉积锰的衍射峰强度按以下顺序递减:(411)、(721)、(400)、(510),不锈钢阴极上沉积锰的衍射峰强度按以下顺序递减:(411)、(721)、(510),铝阴极表面金属锰暴露面(400) 的出现使其表面形貌较不锈钢阴极有所不同。SULCIUS等[33]在不同电极材料上沉积金属锰时发现,金属锰的晶型主要受阴极基底和添加剂的影响。采用铝阴极替换传统的不锈钢阴极在现有的工艺条件下可以产出相同结构的金属锰。
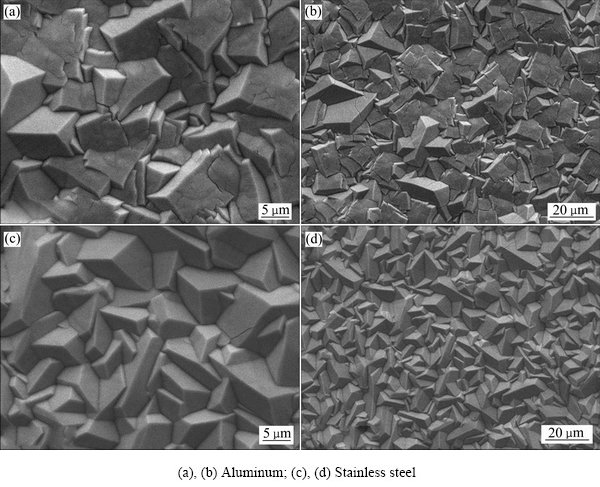
图9 电解锰的SEM像
Fig. 9 SEM images of electrolytic manganese from different cathodes
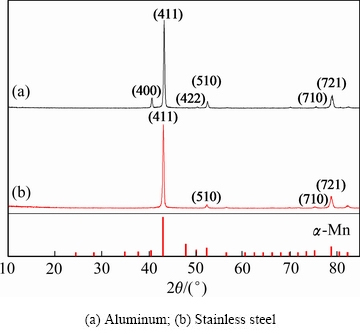
图10 电解锰的XRD谱
Fig. 10 XRD patterns of electrolytic manganese from different cathodes
2.3 CV曲线
为进一步分析铝和不锈钢作为电解锰阴极的差异,在-0.8~-2.4 V范围内对两电极在优化电解液中进行了循环伏安扫描,电解液温度为35 ℃,扫描速率为5 mV/s。其结果如图11所示。
由图11可知,两种阴极表现出明显不同的阴极电化学行为。铝阴极负扫至-1.7 V时电极表面有气泡生成,说明此时有氢气的析出,当电位负扫至-1.98 V时出现锰离子的还原峰,即在-1.3~-1.98 V范围内主要发生析氢反应和硒的沉积反应,-1.98~-2.4 V范围内主要发生锰的沉积反应和析氢反应。当电位回扫至-1.9 V时出现锰的氧化峰,对应铝表面金属锰的溶解,氧化峰对应的峰值电位和电流密度分别为-1.48 V和116.8 mA/cm2。不锈钢阴极负扫至-1.3 V时电极表面就有气泡生成,当电位负扫至-1.97 V时出现锰离子的还原峰。当电位回扫至-1.9 V时出现锰的氧化峰,该氧化峰对应的峰值电位和电流密度分别为-1.45 V和108.9 mA/cm2。对比两个阴极可知,铝阴极的析氢电位较负,说明铝有较高的析氢过电位,能显著地抑制析氢反应,与条件实验的分析一致。铝阴极和不锈钢阴极的析锰电位几乎相同,说明铝的析锰过电位与不锈钢的几乎相同,铝对锰的沉积过程没有明显影响。由图11(b)可知,在低于-2.0 V的电位区间内,虽然铝阴极的电流密度小于不锈钢阴极的,但铝阴极表面的氧化峰面积明显大于不锈钢阴极的,说明该电位区间内,铝阴极能有效地抑制析氢反应,加速Mn2+的沉积,从而有效提高初始时期的阴极电流效率,该结果与条件实验相吻合。

图11 不同阴极条件下的循环伏安曲线
Fig. 11 Cyclic voltammetry with different cathodes
3 结论
1) 采用铝阴极电解金属锰的优化条件为:电流密度400 A/m2、(NH4)2SO4浓度130 g/L、初始Mn2+浓度30 g/L、初始pH值7.0、SeO2浓度0.04 /L、电解温度35 ℃。该条件下电解2 h可以达到86%的阴极电流效率,直流电耗较不锈钢阴极降低47 kW·h/t。所得产物为晶粒致密、粒径较大、块状结构为主的α-Mn。
2) 铝表面的析氢过电位高于不锈钢,起始析锰电位和不锈钢相同。从而在一定的温度范围内抑制氢气的析出,提高阴极电流效率。同时,铝阴极可以抑制SeO32-的还原,减少杂质Se的共沉积,获得更低Se含量的阴极锰。
3) 与传统不锈钢阴极相比,铝有更高的阴极电流效率、更低的直流电耗和SeO2消耗量,具备替代不锈钢板作为锰电解过程阴极材料的潜力。
REFERENCES
[1] 梅光贵. 中国锰业技术[M]. 长沙: 中南大学出版社, 2004.
MEI Guang-gui. Technology of China manganese industry[M]. Changsha: Central south University Press, 2004
[2] 王运敏. 中国的锰矿资源和电解金属锰的发展[J]. 中国锰业, 2004, 22(3): 26-30.
WANG Yun-min. Resources of Mn-ores and development of EMM[J]. China’s Manganese Industry, 2004, 22(3): 26-30.
[3] 曾湘波. 中国电解金属锰行业的发展趋势[J]. 中国锰业, 2014, 32(1): 1-4.
ZENG Xiang-bo. Development trend of EMM in China[J]. China’s Manganese Industry, 2014, 32(1): 1-4.
[4] 李旭华, 周长波, 朱宁芳, 王 璠, 党春阁, 方 刚. 电解锰行业污染治理技术评估研究[J]. 环境工程技术学报, 2013, 3(6): 514-518.
LI Xu-hua, ZHOU Chang-bo, ZHU Ning-fang, WANG Fan, DANG Chun-ge, FANG Gang. Evaluation of the technologies for EMM industry pollution control[J]. Journal of Environmental Engineering Technology, 2013, 3(6): 514-518.
[5] 段宁, 但智钢, 宋丹娜. 中国电解锰行业清洁生产技术发展现状和方向[J]. 环境工程技术学报, 2011, 1(1): 75-81.
DUAN Ning, DAN Zhi-Gang, SONG Dan-na. Current status and directions for development of cleaner production technology of electrolytic manganese metal industry in China[J]. Journal of Environment Engineering Technology, 2013, 3(6): 514-518.
[6] 王洪才, 时章明, 刘 波, 陈 波, 杨钦皓, 叶 铮. 电解锰生产流程中物流对理想能耗的影响[J]. 中国有色金属学报, 2016, 26(8): 1774-1781.
WANG Hong-cai, SHI Zhang-ming, LIU Bo, CHEN Bo, YANG Qin-hao, YE Zheng. Influence of material flows in electrolytic manganese metal process on its optimal energy intensity[J]. The Chinese Journal of Nonferrous Metals, 2016, 26(8): 1774-1781.
[7] 孙健哲, 陈虎魁, 郭进宝, 杨新科. 金属锰电解的电化学原理分析[J]. 宝鸡文理学院学报(自然科学版), 1997, 17(1): 33-38.
SUN Jian-zhe, CHEN Hu-kui, GUO Jin-bao, YANG Xin-ke. On the electrochemical principles of electrolysis for metal manganese[J]. Journal of Baoji College of Arts and Science (Natural Science) , 1997, 17(1): 33-38.
[8] XUE Jian-rong, ZHONG Hong, WANG Shuai, LI Chang-xin, WU Fang-fang. Influence of sodium silicate on manganese electrodeposition in sulfate solution[J]. Transactions of Nonferrous Metals Society of China, 2016, 26(4): 1126-1137.
[9] JIAO Peng-peng, XU Fu-yuan, LI Jian-hua, DUAN Ning, CHEN Guan-yi, JIANG Lin-hua. The inhibition effect of SeO2 on hydrogen evolution reaction in MnSO4-(NH4)2SO4 solution[J]. International Journal of Hydrogen Energy, 2016, 41(2): 784-791.
[10] PADHY S K, PATNAIK P, TRIPATHY B C, BHATTACHARYA I N. Microstructural aspects of manganese metal during its electrodeposition from sulphate solutions in the presence of quaternary amines[J]. Materials Science and Engineering B, 2015, 193: 83-90.
[11] PADHY S K, PATNAIK P, TRIPATHY B C, GHOSH M K, BHATTACHARYA I N. Electrodeposition of manganese metal from sulphate solutions in the presence of sodium octyl sulphate[J]. Hydrometallurgy, 2016, 165: 73-80.
[12] XU Fu-yuan, DAN Zhi-gang, ZHAO Wei-nan, HAN Gui-mei, SU Ze-hui, XIAO Ke, JIANG Lin-huan, DUAN Ning. Electrochemical analysis of manganese electrodeposition and hydrogen evolution from pure aqueous sulfate electrolytes with addition of SeO2[J]. Journal of Electroanalytical Chemistry, 2015, 741: 149-156.
[13] RUDNIK E. Effect of gluconate ions on electroreduction phenomena during manganese deposition on glassy carbon in acidic chloride and sulfate solutions[J]. Journal of Electroanalytical Chemistry, 2015, 741: 20-31.
[14] DING Li-feng, FAN Xing, DU Jun, LIU Zuo-hua, TAO Chang-yuan. Influence of three N-based auxiliary additives during the electrodeposition of manganese[J]. International Journal of Mineral Processing, 2014, 130: 34-41.
[15] SUN Yan, TIAN Xi-ke, HE Bin-bin, YANG Chao, PI Zhen-bang, WANG Yan-xin, ZHANG Su-xin. Studies of the reduction mechanism of selenium dioxide and its impact on the microstructure of manganese electrodeposit[J]. Electrochimica Acta, 2011, 56(24): 8305-8310.
[16] LU Jian-ming, DREISINGER D, GLüCK T. Manganese electrodeposition—A literature review[J]. Hydrometallurgy, 2014, 141: 105-116.
[17] 韩桂梅, 徐夫元, 降林华, 但智刚, 高小娟, 段 宁. 锰电解过程关键因素研究及技术经济性分析[J]. 电化学, 2013, 20(3): 282-287.
HAN Gui-mei, XU Fu-yuan, JIANG Lin-hua, DAN Zhi-gang, GAO Xiao-juan, DUAN Ning. Key Factors and techno- economic analyses of manganese electrolysis process[J]. Journal of Electrochemistry, 2013, 20(3): 282-287.
[18] ELSHERIEF A E. A study of the electroleaching of manganese ore[J]. Hydrometallurgy, 2000, 55(3): 311-326.
[19] ILEA P, TISSOT P, ONICIU L. Hydrogen overpotential on several materials for the electrodeposition of manganese from sulfate solutions[J]. Bulletin of Electrochemistry (India), 2000, 16(3): 133-135.
[20] RADHAKRISHNAMURTHY P, SATHYANARAYANA S, REDDY A K N. Kinetics of hydrogen evolution reaction on a stainless steel electrode[J]. Journal of Applied Electrochemistry, 1977, 7(1): 51-55.
[21] OLIVARES-RAMIREZ J M, CAMPOS-CORNELIO M L, GODINEZ J U, BORJA-ARCO E, CASTELLANOS R H. Studies on the hydrogen evolution reaction on different stainless steels[J]. International Journal of Hydrogen Energy, 2007, 32(15): 3170-3173.
[22] 栗 韬, 黄 惠, 郭忠诚. 超硬铝合金作为阴极在锌电积过程中的电化学行为[J]. 工程科学学报, 2016, 38(6): 767-772.
LI Tao, HUANG Hui,GUO Zhong-cheng. Electrochemical behavior of the super high strength aluminum alloy as a cathode in zinc electrodeposition[J]. Chinese Journal of Engineering,2016, 38(6): 767-772.
[23] METIKOS-HUKOVIC M, BABIC R, GURBAC Z, BRINIC S. Inhibition of the hydrogen evolution reaction on aluminium covered by ‘spontaneous’ oxide[J]. Journal of Applied Electrochemistry, 1994, 24(4): 325-331.
[24] VIJH A K. Electrolytic hydrogen evolution reaction on aluminum, oxide-covered electrodes[J]. The Journal of Physical Chemistry, 1969, 73(3): 506-513.
[25] KOZIN L F, MASHKOVA N V, MANILEVICH F D. Hydrogen overvoltage at manganese in ammonium-bromide-perchloric solution[J]. Protection of Metals and Physical Chemistry of Surfaces, 2009, 45(1): 25-30.
[26] 舒余德, 符德学, 缪 绢. 硒酸钠对锌锰合金电沉积影响的研究[J]. 电镀与涂饰, 2002, 21(1): 1-4.
SHU Yu-de, FU De-xue, MIAO Juan. Studies on the effect of sodium selenate on electrodeposition of zinc-manganese alloy. Electroplating & Finishing[J]. 2002, 21(1): 1-4.
[27] LU Jian-ming, DREISINGER D, GLüCK T. Electrolytic manganese metal production from manganese carbonate precipitate[J]. Hydrometallurgy, 2016, 161: 45-53.
[28] KOZIN L F, MASHKOVA N V, MANILEVICH F D. Kinetics and mechanism of the discharge-ionization of manganese in an ammonium chloride solution[J]. Protection of Metals, 2007, 43(6): 537-541.
[29] 王敬民. 电解金属锰阴极过程初探[J]. 中国锰业, 1994, 12(1): 47-49.
WANG Jing-ming. Approach on the cathode process of electrolyte metal manganese[J]. China’s Manganese Industry, 1994, 12(1): 47-49.
[30] FAN Xing, XI Su-yun, SUN Da-gui, LIU Zuo-hua, DU Jun, TAO Chang-yuan. Mn-Se interactions at the cathode interface during the electrolytic-manganese process[J]. Hydrometallurgy, 2012, 127: 24-29.
[31] DHANANJAYAN N, BANERJEE T. Structure of electro- deposited manganese[M]. National Metallurgical Laboratory, 1969.
[32] WEI Qi-feng, REN Xiu-lian, DU Jie, WEI Si-jie, HU Su-rong. Study of the electrodeposition conditions of metallic manganese in an electrolytic membrane reactor[J]. Minerals Engineering, 2010, 23(7): 578-586.
[33] SULCIUS A, GRISKONIS E, KANTMINIENE K, ZMUIDZINAVICIENE N. Influence of different electrolysis parameters on electrodeposition of γ-and α-Mn from pure electrolytes—A review with special reference to Russian language literature[J]. Hydrometallurgy, 2013, 137: 33-37.
Electrodeposition of Mn from manganese sulfate solution by aluminum cathode
YANG Fan, JIANG Liang-xing, YU Xiao-ying, YANG Jian, LAI Yan-qing, Lü Xiao-jun, LI Jie
(School of Metallurgy and Environment, Central South University, Changsha 410083, China)
Abstract: Aluminum was adopted as cathodic material for manganese electrodeposition from the MnSO4-(NH4)2SO4 solution. The influences of the current density, electrolyte composition and temperature were studied on the cathodic current efficiency, energy consumption and cathodic products. The results show that, the cathodic current efficiency and the energy consumption can reach to 85.8% and 4870.9 kW·h/t, under the following conditions: Mn2+ concentration of 30 g/L, (NH4)2SO4 concentration of 130 g/L, SeO2 concentration of 0.04 g/L, temperature of 35 ℃, pH of 7.0 and cathode current density of 400 A/m2. The purity of product can achieve more than 99.5% and the crystal form is α-Mn. Compared with traditional stainless steel (0Cr19Ni9), the onset potential of manganese electrodeposition on aluminum cathode is not changed, while the hydrogen evolution is suppressed at initial period of electrodeposition. Aluminum cathode can accelerate the discharge rate of Mn2+ and improve the cathodic current efficiency, and then decrease the energy consumption. The reduction of SeO32- on aluminum cathode is weakened, which can reduce the consumption of SeO2 and improve the purity of product. This study indicates that aluminum has the potential to be candidate of stainless steel for manganese electrodeposition.
Key words: manganese electrodeposition; aluminum cathode; current efficiency; energy consumption; SeO2
Foundation item: Project(51374240) supported by the National Natural Science Foundation of China
Received date: 2017-11-01; Accepted date: 2018-02-28
Corresponding author: JIANG Liang-xing; Tel: +86-731-88830474;E-mail: lxjiang@csu.edu.cn
(编辑 何学锋)
基金项目:国家自然科学基金资助项目(51374240)
收稿日期:2017-09-05;修订日期:2017-11-16
通信作者:蒋良兴,副教授,博士;电话:0731-88830474;E-mail: lxjiang@csu.edu.cn