
Effect of holding time on microstructure of Mg-9Al-1Si alloy during semisolid isothermal heat treatment
MA Guo-rui(马国睿), LI Xin-lin(李新林), LI Qing-fen(李庆芬)
Center for Biomedical Materials and Engineering, College of Materials Science and Chemical Engineering,Harbin Engineering University, Harbin 150001, China
Received 23 September 2009; accepted 30 January 2010
Abstract: The effects of isothermal holding time on the semisolid microstructure of Mg-9Al-1Si (mass fraction,%) alloy were investigated. The research results indicate that the Mg-9Al-1Si alloy with non-dendritic microstructure can be produced by the semi-solid isothermal heat treatment. With holding time varying from 5 to 30 min, the volume fraction of liquid is gradually enlarged from 29.3% to 38.6%, the morphology of α-Mg grains changes from initial dendritic shape to spherical types and their average sizes increases from 41.1 to 56.1 μm. In addition, during the isothermal heat treatment, the eutectic Mg2Si phase changes from the initial Chinese script shape to granule and/or polygon shape in Mg-9Al-1Si alloy. The modification of Mg2Si phase is possibly attributed to a shift of the eutectic composition of the liquid in semi-solid slurries, towards lower silicon contents with increasing Al content due to a redistribution of Al during isothermal heat treatment.
Key words: Semi-solid; isothermal heat treatment; Mg2Si phase; modification
1 Introduction
Mg-Al-Si alloys have been used as die casting alloys at elevated temperature in automotive and aerospace industries for a long time[1-2]. However, the Mg2Si phases in the Mg-Al-Si alloys are prone to forming undesirable, coarse Chinese script shape under low solidification rate resulting from the eutectic reaction, which will damage the mechanical properties of the magnesium alloys. In order to modify the Chinese script shaped Mg2Si phases in the Mg-Al-Si magnesium alloys, many methods such as hot extrusion[3-4], rapid solidification[5-6], mechanical alloying[7-8] and micro-alloying (with the addition of Ca, P, Sb, Sr)[9-13] were studied. But some investigations indicated that these methods may lead to the increase of the production cost and other problems[10, 13].
The semi-solid isothermal heat treatment is a relatively novel method and recent results indicate that the Chinese script shaped Mg2Si phases in Mg-6Al-1Zn- 0.7Si alloy could be modified to granule and/or polygon shapes by semi-solid isothermal heat treatment[14]. Therefore, the semisolid isothermal heat treatment is considered as a potential method for the modification of Chinese script shaped Mg2Si phase in Mg-Al-Si magnesium alloys.
The present study aims at investigating the effects of holding time on the microstructure of Mg-9Al-1Si alloys during semi-solid isothermal heat treatment. The purpose is to develop a simplified method for modification of Chinese script shaped Mg2Si phases. It is expected that the preliminary results can be significant in promoting the fabrication of high quality Mg-Al-Si alloys.
2 Experimental
Commercially pure Mg (>99.9%), Al (>99.8%) and Si (>99.4%) were used to prepare the experimental alloy. The experimental alloy was molten in a graphite crucible in an electric resistance furnace and finally was poured into a steel mould to produce plate samples. The composition of the magnesium alloy was measured by an ARL4460 metals analyzer, and given as: 89.92 Mg, 9.32 Al, and 0.76 Si (mass fraction, %), thus the alloy can be termed Mg-9Al-1Si alloy. Subsequently, the plate samples were cut into a series of cubic specimens with a size of 10 mm×10 mm×10 mm. The specimens were heated to 565 ?C and held for 5, 10, 20 and 30 min in the electric resistance furnace under the protective atmosphere of CO2 and SF6. After the isothermal heat treatment, the samples were taken out rapidly and put into cooling water immediately. The samples were etched by 3% HNO3 in alcohol. Microstructure and intermetallic phase identification were conducted using optical microscopy (OM) (Axiovert 200 MAT, Germany), scanning electron microscopy (SEM) (JSM-6480A) and X-ray diffractometry (XRD) (X’Pert PRO, Holand). The temperature of the eutectic reaction was measured using a Diamond differential scanning calorimeter (DSC) (Pekin-Elmer, USA) at a heating rate of 5 ?C/min. Quantitative metallography analyses including the volume fraction and size of α-Mg grains were conducted using the quantitative analysis system (Omnimet Imaging Systems-Buehler, USA) to study the evolution of the microstructures during the isothermal heat treatment.
3 Results and discussion
Fig.1 shows the XRD pattern and SEM image of the as-cast Mg-9Al-1Si alloy. The XRD result reveals that the main phases in as-cast alloy are α-Mg, Mg17Al12 and Mg2Si. It can be seen clearly from Fig.1(b) that the typical microstructure of the as-cast Mg-9Al-1Si alloy contains three constituents: α-Mg dendrites, gray second Mg17Al12 phases and coarse Chinese script shaped Mg2Si phases. In general, the Mg2Si phases in Mg-Al-Si based alloys are prone to form coarse Chinese script shape under low solidification rate[2, 15]. Therefore, under the permanent mould casting of this investigation, the Mg2Si phases in the Mg-9Al-1Si alloy exhibit typical Chinese script shaped morphology.
Fig.2 shows the semi-solid microstructural evolution of Mg-9Al-1Si alloy treated at 565 ?C for different holding time from 5 to 30 min. The semi-solid microstructure of Mg-9Al-1Si alloy consists of α-Mg grains, liquid phases and entrapped liquid inside the α-Mg grains, which is different from the as-cast one. It is further found that the as-cast coarse Chinese script shaped Mg2Si phases are fragmented, and the Mg2Si phases in the semi-solid Mg-9Al-1Si alloy exhibit granule and/or polygon shape. With the increase of holding time, the volume fraction of liquid increases, the amount of the α-Mg grains decreases, the average size of the α-Mg grains grows larger and the shape of the α-Mg grains becomes more globular.
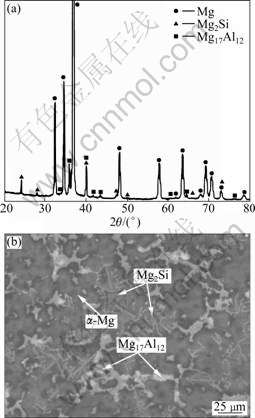
Fig.1 XRD pattern (a) and SEM image (b) of as-cast Mg-9Al- 1Si alloy
The further relation of the liquid volume fraction and the average size of the α-Mg grains with the holding time can be revealed from Figs.3 and 4, which is obtained using the quantitative analysis system. With the increase of holding time, the metallurgical observation shows that, on one hand, with the isothermal holding time varying from 5 to 30 min, the volume fraction of the liquid is gradually enlarged from 29.3% to 38.6%, as depicted in Fig.3. On the other hand, with the isothermal holding time varying from 5 to 30 min, the measured average size of the α-Mg grains in the semisolid microstructures increases from 41.1 to 56.1 μm, as depicted in Fig.4.
Fig.5 shows the DSC endothermic curve of the Mg-9Al-1Si alloy. It can be seen that the eutectic temperature of α-Mg+Mg2Si in the microstructures of the alloy is 485.4 ?C. Because the isothermal holding temperature is higher than the eutectic temperature of the alloy, partial remelting of the low melting point phases such as the divorced eutectic Mg17Al12 (437 ?C) and the α-Mg+Mg2Si eutectic appears at grain boundaries. Subsequently, secondary dendrite arms of α-Mg grains touch each other, resulting in the formation of the “liquid islands”. With increase of the holding time, solute atoms diffuse from the areas of higher curvature to those of
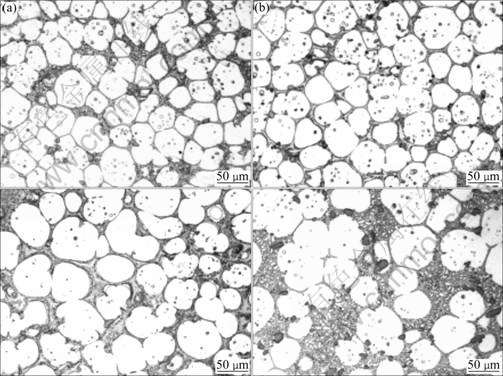
Fig.2 OM images of Mg-9Al-1Si alloy treated at 565 ?C for different time: (a) 5 min; (b) 10 min; (c) 20 min; (d) 30 min
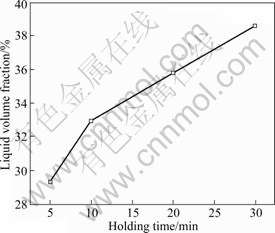
Fig.3 Relationship between liquid volume fraction and holding time
lower curvature, due to the effect of interface curvature, and the particles spheroidizing takes place in order to decrease the free energy. Further coarsening Ostwald ripening takes place, which leads to an increase in the volume fraction of liquid, since the small particles with “liquid islands” dissolve and the “liquid islands” join the bulk liquid. The present experimental results agree well with those reported previously[16].
Fig.6 shows the optical image of the Mg-9Al-1Si alloy treated at 565 ?C for 20 min. It is observed that the Mg2Si phases in the semi-solid microstructure of
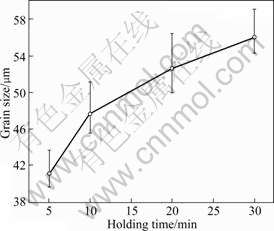
Fig.4 Relationship between average size of α-Mg grains and holding time
experimental alloy exhibit granule and/or polygon shape (as shown by arrows in Fig.6). The liquid phase of Mg-9Al-1Si alloy with semi-solid microstructures mainly consists of remelting of divorced eutectic Mg17Al12 and (a-Mg+Mg2Si) eutectic. According to factual liquid volume fraction (without regarding the “liquid islands”) in the semi-solid microstructure of Mg-9Al-1Si alloy treated at 565 ?C for 20 min, the mass fraction of the Al and Si in semi-solid liquid of the Mg-9Al-1Si alloy can be calculated as 25.4% and 1.95%, respectively.
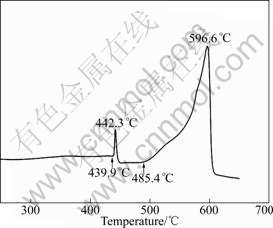
Fig.5 DSC curve of as-cast Mg-9Al-1Si alloy
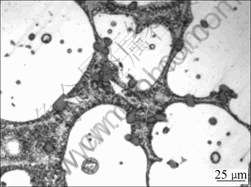
Fig.6 Optical image of Mg-9Al-1Si alloy treated at 565 ?C for 20 min
With the increase of Al content, the eutectic composition shifts significantly to a lower silicon content, which induces the formation of more polygonal shape primary Mg2Si. Since primary Mg2Si can exist in the as-cast Mg-9Al-1Si alloy when Si content is 0.765 48% (mass fraction), and Si content calculated in the semi-solid microstructure is larger than the Si content of eutectic point, the Mg2Si in the semi-solid microstructure is prone to form the primary Mg2Si. Due to water quenching process, inhibiting the growth of primary Mg2Si dendrite makes the morphology of the primary Mg2Si become granule and/or polygon shape.
From the previous study[14], the mass fraction of the Al and Si in semi-solid liquid phase of Mg-6Al-1Zn-0.7Si alloy can be calculated as 28.6% and 3.3%, respectively, and the eutectic composition of the liquid in semi-solid slurries shifts to lower silicon contents with increasing Al content, which is obviously appropriate to the formation of polygon shaped primary Mg2Si. Therefore, the amount of eutectic Mg2Si significantly vanishes in the final microstructure. However, ZHA et al[17] reported that the eutectic Mg2Si in Mg-5Si-1Al alloy turns from granular shape into Chinese script morphology by partial remelting due to the low Al content.
In spite of the reasons above, the modi?cation mechanism of Chinese script shaped Mg2Si phases during semisolid isothermal heat treatment is not completely clear, and further investigation needs to be carried out.
4 Conclusions
1) It is possible to produce Mg-9Al-1Si alloy with non-dendritic microstructures by the semi-solid isothermal heat treatment. With increase in the isothermal holding time from 5 to 30 min at 565 ?C, the non-dendritic microstructure with 29.3%-38.6% (volume fraction) liquid content and the average grain size in a range of 41.1-56.1 μm are obtained.
2) The semi-solid isothermal heat treatment can modify the Chinese script shaped Mg2Si phases in Mg-9Al-1Si alloy. During the isothermal heat treatment, the eutectic Mg2Si phase changes from the initial Chinese script shape to granule and/or polygon shape in Mg-9Al-1Si alloy. The modification of Mg2Si phases is attributed to a shift of the eutectic composition of the liquid towards lower silicon contents due to a redistribution of Al during partial remelting and isothermal heat treatment.
References
[1] POLMEAR I J. Magnesium alloys and their application [J]. Mater Sci Technol, 1994, 10(1): 1-5.
[2] LUO A, PEKGULERYUZ M Z. Cast magnesium alloys for elevated temperature applications [J]. J Mater Sci, 1994, 29(20): 52-59.
[3] MABUCHI M, KUBOTA K, HIGASHI K. Tensile strength, ductility and fracture of magnesium-silicon alloys [J]. J Mater Sci, 1996, 31(6): 1529-1535.
[4] KUBOTA K, MABUCHI M, HIGASHI K. Elevated temperature mechanical properties of magnesium alloys containing Mg2Si [J]. Mater Sci Technol, 1996, 12(1): 35-39.
[5] CZERWINSKI F. On the generation of thixotropic structures during melting of Mg-9%Al-1%Zn alloy [J]. Acta Mater, 2002, 50(12): 3267-3283.
[6] RAGHUNATHAN N, SHEPPARD T. Microstructural development during annealing of hot rolled Al-Mg alloys [J]. Mater Sci Technol, 1989, 5(6): 542-547.
[7] ZHANG J, FAN Z, WANG Y Q, ZHOU B L. Microstructural development of Al-15wt.%Mg2Si in situ composite with mischmetal addition [J]. Mater Sci Eng A, 2000, 281(1/2): 104-112.
[8] FROMMEYER G, BEER S, von OLDENBERG K. Microstructure and mechanical properties of mechanically alloyed intermetallic Mg2Si-Al alloys [J]. Metallkde, 1994, 85(5): 372-377.
[9] KIM J J, KIM D H, SHIN K S, KIM N J. Modification of Mg2Si morphology in squeeze cast Mg-Al-Zn-Si alloys by Ca or P addition [J]. Scripta Mater, 1999, 41(3): 333-340.
[10] YANG Ming-bo, PAN Fu-sheng, SHEN Jia, BAI Liang. Comparison of Sb and Sr on modification and refinement of Mg2Si phase in AZ61-0.7Si magnesium alloy [J]. Transactions of Nonferrous Metals Society of China, 2009, 19(2): 287-292.
[11] YANG Ming-bo, SHEN Jia, PAN Fu-sheng. Effect of Sb on microstructure of semi-solid isothermal heat-treated AZ61-0.7Si magnesium alloy [J]. Transactions of Nonferrous Metals Society of China, 2009, 19(1): 32-39.
[12] NAM K Y, SONG D H, LEE C W, LEE S W, PARK Y H, CHO K M, PARK I M. Modification of Mg2Si morphology in as-cast Mg-Al-Si alloys with strontium and antimony [J]. Mater Sci Forum, 2006, 510/511(10): 238-241.
[13] QUIMBY P D, LU S Z, PLICHTA M R, VISSER D K, JACOBE K P. Effects of minor addition and cooling rate on the microstructure of cast magnesium-silicon alloys [C]// LUO A, NEELAMEGGHAM N, BEALS R. Magnesium Technology. San Antonio, Texas: TMS, 2006: 535-537.
[14] YANG Ming-bo, PAN Fu-sheng, CHENG Ren-ju, BAI Liang. Effect of semi-solid isothermal heat treatment on the microstructure of Mg-6A1-1Zn-0.7Si alloy [J].J Mater Process Technol, 2008, 206(1/3): 374-381.
[15] DARGUSCH M S, DUNLOP G L, BOWLES A L, PETTERSEN K, BAKKE P. The effect of silicon content on the microstructure and creep behavior in die-cast magnesium AS alloys [J]. Met Mater Trans A 2004, 35(6): 1905-1909.
[16] FAN Z. Semisolid metal processing [J]. Int Mater Rev, 2002, 47(2): 49-85.
[17] ZHA M, WANG H Y, XUE P F, LI L L, LIU B, JIANG Q C. Microstructural evolution of Mg-5Si-1Al alloy during partial remelting [J]. J Alloys Compd, 2009, 472(1/2): 18-22.
(Edited by FANG Jing-hua)
Foundation item: Project(HEUFT05038) supported by the Basic Research Foundation of Harbin Engineering University, China; Project(2009AA03Z423) supported by the National High-Tech Research and Development Program of China
Corresponding author: LI Xin-lin; Tel.:+86-451-82518173; Fax:+86-451-82518644; E-mail: lixinlin@hrbeu.edu.cn