
Preparation of AZ91 alloy by powder metallurgy method
JIANG Hai(姜 海)1, HE Xin-bo(何新波)1, QU Xuan-hui(曲选辉)1,2, I. S. HUMAIL2 , WANG Xi-tao(王西涛)2
1. School of Materials Science and Engineering, University of Science and Technology Beijing,
Beijing 100083, China;
2. State Key Laboratory for Advanced Metals and Materials, University of Science and Technology Beijing,
Beijing 100083, China
Received 28 July 2006; accepted 15 September 2006
Abstract: Magnesium alloy AZ91 was prepared by powder metallurgy method, and the effect of sintering temperature on the densities and microstructures of the alloys was investigated. The results show that tight control of the sintering temperature within a narrow range around the liquidus level generates structures with high integrity and reduces some of the disadvantages caused by the higher temperatures. The matrix consists of α-Mg grains/cells surrounds by discontinuous precipitates of Mg17Al12 intermetallics which are normally located at the grain boundaries and triple junction.
Key words: AZ91 alloy; powder metallurgy; sintering temperature
1 Introduction
Increasing interest has been given to the development and application of magnesium alloys. Due to its lower density, higher capacity for shielding against electromagnetic interference and better resistance to collision, magnesium alloys are available for producing some structural parts such as the coverings of mobile telephones, notebook computers and portable mini-disks (MD). Due to its less commercial availability as well as limited manufacturing methods, This alloy was not widely used as a structural material in the past[1]. But die-casting of the magnesium alloys has become the prevailing method for manufacturing in many fields in recent years. Alloy AZ91, as a leading magnesium alloy used for structural applications, contains aluminum and zinc as principal alloying elements. This alloy is sometimes produced by semi-solid injection molding (thixomolding), whereas normally by die-casting. Both methods have their disadvantages. Die-cast alloy AZ91 has the casting defect of pores because of underfill or misrun[2]. Semi-solid injection molded AZ91 also has the defect of pores and in addition the cost of the molding equipment is high[3]. With the aim to find an even better way for net-shape forming of Mg-9Al-1Zn alloy in a low cost, powder metallurgy method was tested.
As we all know, in powder metallurgy industry, the design of the mold and the choice of the sintering processing conditions used to rely mostly upon previous experiences and a trial-and-error method which may result in a long set-up time, a high mold cost and a poor productivity[4]. In order to minimize such economic losses, it would be a great help to have some simulated tests to find an optimum sintering temperature for powder metallurgical producing AZ91 alloy’s sintering process.
The objectives of these researches were to set up a sintering process in a simulated way using compacted AZ91 alloy powder. It was anticipated that the positive outcome of this experiment would further expand the ways of net-shape forming of PIM AZ91 alloy.
2 Experimental
AZ91 alloy powder was used in this study. Table 1 shows the chemical composition and properties of this powder. Fig.1 shows the morphology of the gas atomized magnesium powder.
The powder used was mixed for 10 h in a milling pot with ethanol as solvent. Then the powder was deposited immovably till it was dry. It was then compressed into the shape of small cylinders measuring d10 mm×4 mm by using a hydrostatic press with a pressure of 2 MPa. The cylinders were then sintered in a flowing H2 at a given rate in a tube furnace. The 5 samples were heated from 10 ℃ to specified temperatures for a period of 90 min, and then they were soaked at a certain temperature for 60 min, at last they were left to cool naturally. The samples orderly named M1, M2, M3, M4, M5 were sintered at 570, 580, 590, 600, 610 ℃. After being sintered, these samples were used to test the density by Archimedes’ water immersion method. Moreover, the surfaces of the samples were prepared for optical microscopy by polishing up to 0.05 ?m. To reveal microstructure, the surfaces were etched with 2% tartaric acid aqueous solution. The microchemistry of the samples was measured with an X-ray micro-analyzer. X-ray diffractometry with Cu Kα radiation was applied for the phase and crystallographic characterizations of materials.
Table 1 Chemical composition and property of AZ91 alloy powder
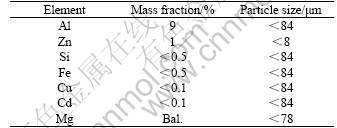
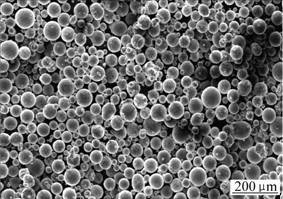
Fig.1 SEM micrograph of magnesium powder
3 Results and discussion
Fig.2 shows the Mg-rich portion of the binary Mg-Al diagram with the locations of 9% aluminum content observable, the liquidus points are clearly visible[5]. As earlier tests of the alloy at solidus temperatures demonstrate, its relative density is below 86%, which is the highest possible density obtained by sintering an alloy produced by the above-mentioned method[6]. In this research the alloy was tested at around liquidus temperatures. In order to gain a high density, the sintering temperatures were retained for 60 min for each sample. The samples were then left to cool naturally.
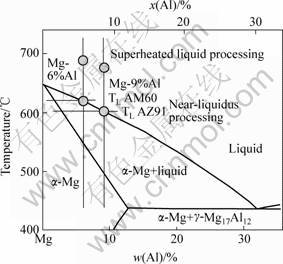
Fig.2 Mg rich portion of Mg-Al diagram
It was observed that the density increased approximately with the sintering temperature increase. But when the temperature exceeded 580 ℃, the density dropped to a lower level. As the optical microscopy shows with the higher sintering temperature over 580 ℃, there were more pores on the surface of the specimen which is well explained by the number of superheated part of the alloy in picture. Fig.4 shows that specimen M2 has fewer pores compared with specimen M3. Fig.5 shows the dendritic microstructure formed around the flaws which were caused by the superheat of alloy[7].
However specimen M5 exhibited the highest relative density of 95.0% at the sintering temperature of 610 ℃ with a sintering time of 60 min. Fig.6 shows that there was nearly no pores in specimen M5. The cause of the density difference between specimen M5 and others is the result of sintering temperature at 610 ℃ which is already higher than the AZ91 liquidus temperature. That means specimen M5 is melted already during the long sintering time by the evidence of a very badly distortion. Other than specimen M5, the highest density was got by specimen M2.
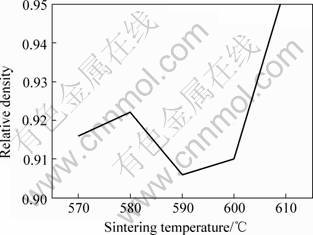
Fig.3 Density of sintered specimens
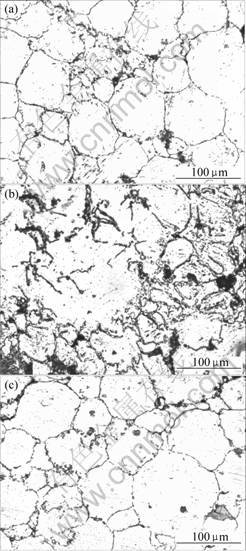
Fig.4 Microstructures of different samples: (a) Specimen M2; (b) Specimen M3; (c) Specimen M5
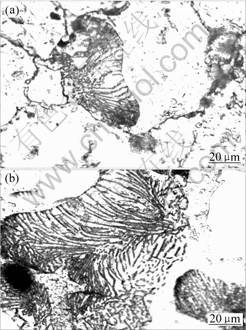
Fig.5 Microstructures of different samples: (a) Specimen M3; (b) Specimen M4
X-ray diffraction provides information about the crystallography of phases, their contents and an estimation of the preferred orientation. The AZ91 alloy sintered around liquidus range, contained α-Mg and intermetallic phase of Mg17Al12 (Fig.6), at least five peaks of Mg17Al12 were detected.
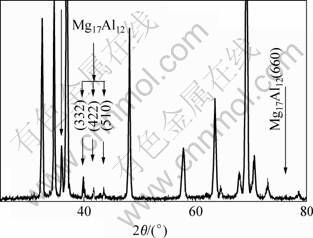
Fig.6 XRD pattern of specimen M3 with intensive peaks of Mg17Al12 at orientation index
A comparison of peak intensities on the diffraction pattern suggests that both phases were randomly oriented[8]. As we can see from Fig.7, discontinuous precipitates of the intermetallic phase Mg17Al12 is located at grain boundaries and triple junction. It is reported that the existence of Mg17Al12 has a significant effect on the enhancement of the tensile strength and elongation of AZ91 alloy[9]. So the intermetallic phase is what we should pay attention to in the further study.
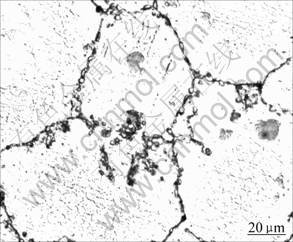
Fig.7 Mg17Al12 precipitates at grain boundaries and triple junction in specimen M5
4 Conclusions
For the hydric gas sintering of the compressed AZ91 alloy powder, effective densification takes place in the range around liquidus level. Sintering at temperature over 580 ℃ results in distortion and appearance of overheated part where is adaptive to the growth of dendritic microstructure. The X-ray diffraction shows the existence of Mg17Al12 intermetallic phase which is a key direction for the further study to achieve a high tensile strength and elongation.
References
[1] NAKANISHI M, MABUCHI M, SAITO M, NAKAMURA M. Tensile properties of the ZK60 magnesium alloy produced by hot extrusion of machined chip[J]. Mater Sci Lett, 1998, 17: 2003–2005.
[2] CHEN Zhen-hua. Magnesium alloy[M]. Beijing: Chemical Industry Press, 2004: 130-132.
[3] CHEN Zhen-hua. Magnesium alloy[M]. Beijing: Chemical Industry Press, 138-140.
[4] LIU Z Y, LOH N H, KHOR K A, TOR S B. Sintering of injection molded M2 high-speed steel[J]. Material Letters, 2000, 45: 32.
[5] CZERWINSKI F. Near-liquidus molding of Mg-Al and Mg-Al-Zn alloys[J]. Acta Materialia, 2005, 53: 1973-1984.
[6] GERMAN R M. Powder Injection Molding[M]. Changsha: Central South University Press, 2001: 10-15.
[7] CZERWINSKI F. Size evolution of the unmelted phase during injection molding of semisolid magnesium alloys[J]. Scripta Materialia, 2003, 48: 327-331.
[8] CZERWINSKIC F. On the generation of thixotropic structures during melting of Mg-9%Al-1%Zn alloy[J]. Acta Materialia, 2002, 53: 3265-3281.
[9] CZERWINSKI F, ZIELINSKA-LIPIEC A, PINET P J. Correlating the microstructure and tensile properties of a thixomolded AZ91D magnesium alloy[J]. Acta Materialia, 2001, 49: 1225-1235.
(Edited by CHEN Ai-hua)
Foundation item: Project (50404012) supported by the National Natural Science Foundation of China
Corresponding author: JIANG Hai; Tel: +86-10-62349550; E-mail:ice.00@126.com