Article ID: 1003-6326(2005)03-0631-05
Numerical simulation for permanent mold centrifugal cast TiAl exhaust valve
SHENG Wen-bin(盛文斌)1, 2, LI Dong(李 东)2
(1. Department of Mechanical Engineering, Shandong University of Technology,
Zibo 255049, China;
2. Titanium Alloy Laboratory, Institute of Metal Research,
The Chinese Academay of Sciences, Shenyang 110016, China)
Abstract: The filling and solidification in centrifugal field, as well as the forming mechanism of off-center porosities were summarized, based on the mathematical model established for the centrifugal cast TiAl exhaust valves. The calculated results show that the centrifugal field results in the phenomenon that the flow in the valve cavity consists of forward flow and backward flow. The unsymmetrical initial temperature field causes continuous unsymmetrical variation in the following solidification, which makes the final solidified region depart from the cavity axis and then leads to the occurrence of off-center porosity. A series of optimized parameters, including the entrance velocity of 0.6-1.3m/s, the rotation speed higher than 300r/min, 80mm or longer entrance length and 400℃ or higher preheated temperature of the mold, are suggested for the manufacture of permanent mold centrifugal cast TiAl exhaust valves.
Key words: TiAl alloy; exhaust valve; permanent mold; mathematical model; off-center porosity CLC
number: TG249.4; TG621.74 Document code: A
1 INTRODUCTION
In the past decades, there has been an enormous increase in the research on titanium aluminides, in particular, on the TiAl compounds[1-3]. The low density combined with the high-strength at high temperature make titanium aluminide alloy an excellent candidate for automotive exhaust valve applications[4-7]. The key to successful application of TiAl exhaust valves is neither the strength nor the ductility, but a large output and low cost manufacturing method[8-10].
Numerical simulation for the filling and solidification of castings has been researched for a long time and many papers have been published[11-15], but the mathematical model is always established based on the assumption that the system is in a uniform force field. As for the conventional computer simulation, it is very difficult to explain the special phenomena existing in the permanent mold cast TiAl exhaust valves, such as the off-center porosity. Therefore, the model for the filling and solidification of TiAl exhaust valves should be established with emphasis on the effect of the centrifugal field.
This paper summarizes the variations of filling velocity and temperature, as well as the forming mechanism of off-center porosity, in course of the permanent mold centrifugal casting of TiAl valves. Furthermore, some optimized parameters derived from the calculated results of numerical simulation have been suggested for the manufacturing procedure of TiAl valves.
2 FILLING AND SOLIDIFICATION IN CENTRIFUGAL FIELD
2.1 Process description
Ti-48Al-2Cr-2Nb(molar fraction, %) exhaust valve blanks were manufactured in a preheated steel mold that consisted of two layers, with 6 cavities assembled circularly in each layer. The mold rotated around the axis at a rotation speed of ω0. The distance from the axis to the entrance of valve stem was defined as L0.
A model with emphasis on the effect of centrifugal field on the filling and solidification process of molten TiAl was established by combining the equation of continuity, the equation of conservation of momentum and the equation of general energy, in which the centrifugal force and the Coriolis force were treated as two additional terms. In addition, the movement of TiAl melt in the valve cavity was regarded as a steady-status flow and the temperature distribution when the cavity has just been filled fully was defined as the initial temperature field for the subsequent solidification process. The model was solved by establishing the corresponding difference equations and programming.
2.2 Velocity distribution
For given alloy melt, the initial velocity usually determines the characteristic of the filling and solidification process in the gravitational field. However, in the course of permanent mold cast of TiAl exhaust valves, the centrifugal field leads to the appearance of centrifugal force and Coriolis force. Furthermore, it results in the transition from an ordinal filling to a centrifugal filling that consists of forward flow and backward flow[11]. At a rotation speed of 300r/min, the velocity curves in different sections being vertical to the cavity axis are shown in Fig.1.
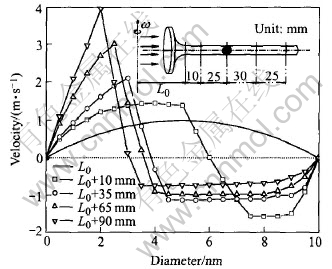
Fig.1 Velocity distribution in different sections under rotation speed of 300r/min
At the entrance of cavity, the melt located near the cavity axis has the maximum filling velocity, while the maximum shear stress acts on the melt bordering upon the cavity frontal boundary. This stress is equal to the one that acts on the unit next to back boundary, but they point to reverse directions (one is positive and the other is negative). In addition, the minimum velocity gradient exists near the axis and the shear stress tends to be zero. Therefore, it is concluded that the distributions of the velocity and the shear stress at the cavity entrance are similar to those in the steady-status flow in a full-filled tube.
Subsequently, the Coriolis force makes the melt move towards the back boundary. As a result, the stress acting on the melt center keeps increasing. Similar tendency also appears in the development of the axial filling velocity. The filling velocity of the melt next to frontal boundary also keeps increasing, while the shear stress shows a contrary tendency. It can be summarized that the stress is maximum at the cavity entrance and points to the cavity end, and then gradually decreases to zero and finally turns into a negative value. Accordingly, the shear stress acts as a factor slowing down the flow instead of accelerating it.
Having reached the cavity end boundary, the forward flow turns into a reverse one and fully fills the cavity end first, then gradually moves to the entrance, which results in the appearance of the co-flow region due to the shear stress at the interface, referring to Fig.2. If the two parts show the same filling velocity (v1=v2), the resultant velocity near the co-flow interface tends to be zero and two affected regions have the same thickness. Under the condition that v1 is larger than v2, the resultant velocity is in the same direction of v1. When v1〈v2, the resultant velocity points to that of v2.
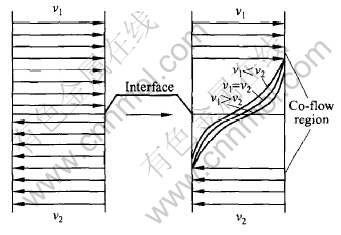
Fig.2 Schematic diagram of velocity transition in co-flow region
In the co-flow region, the velocity distribution becomes irregular near the interface because the viscous interaction here is more powerful, perhaps leading to the occurrence of turbulence, even some eddies. The variation also affects the flow in the regular velocity distribution part, which always leads to the appearance of higher velocity gradient near the interface.
2.3 Temperature distribution
Generally, the model established for the filling and solidification is based on assumption that the casting system is in a uniform field. Furthermore, the initial temperature field can be regarded as the melt temperature and the environmental temperature, respectively.
In this research, the simulation for the solidification of TiAl exhaust valve emphasizes on an uneven initial temperature field defined as the temperature distribution when the cavity has just been fully filled, which is important for minimizing the calculated error. The axial horizontal section is selected to represent the temperature variation in TiAl exhaust valve formed at a rotation speed of 300r/min and the initial temperature distribution in this section is shown in Fig.3.
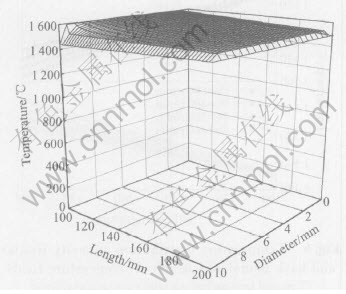
Fig.3 Initial temperature distribution in axial horizontal section at rotation speed of 300 r/min
The calculated result shows that a sharp decease in temperature occurs in the regions bordering upon the cavity frontal, back and end boundaries due to the powerful heat conduction of the permanent mold. In addition, an elevated rotation speed has no obvious influence on the temperature distribution. Fig.4 shows the temperature profiles in the selected horizontal section at a rotation speed of 300r/min.
The curves recorded on four selected points indicate the variations of the temperature with the solidifying time, as shown in Fig.5. It can be known that the melt temperature decreases quickly at the start moment, and then the variation tends to be stable due to the release of latent heat. During the subsequent solidification process, the elevated mold temperature slows down the heat conduction, which leads to the less and less decrease in temperature. The effect of the rotation speed on the solidification can not be concluded by referring to above results.

Fig.4 Temperature fields in selected section at different times(ω=300r/min)
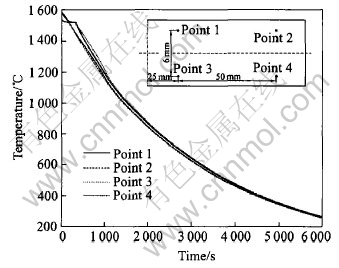
Fig.5 Temperature—time curves at four selected points at rotation speed of 300r/min
As mentioned above, the centrifugal field has an obvious effect on the flow in the valve cavity and makes the melt fill cavity in a special way. Furthermore, it results in an uneven initial temperature distribution for the following solidification process.
3 FORMATION OF OFF-CENTER POROSITY
Some researchers have observed the off-center porosity in centrifugal cast TiAl valves[8, 10, 16], but no clear explanation is offered to clarify the forming process. The existence of this kind of porosities possibly leads to the fact that the valves have to be discarded before the performance test, such as a bent valve stem during subsequent HIPping.
Formation of the shrinkage porosity in the valves is closely related to the solidifying process and can be interpreted by analyzing the temperature variation at the initial temperature field borders. In the selected horizontal section, the temperature curves in the melt next to the cavity frontal and back boundaries under different rotation speeds are shown in Fig.6. In the course that the high temperature melt enters the cavity and moves to the end, temperature of the melt next to the back boundary keeps decreasing with the increase in the filling distance. The variation of temperature with the rotation speed shows that the decrease becomes smaller and smaller with an elevated rotation speed, which is contrary to that in the melt next to the frontal boundary.
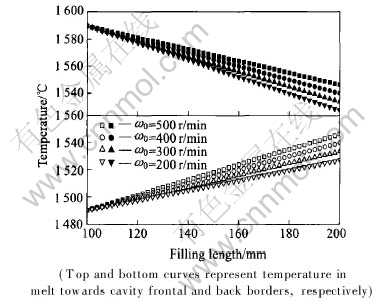
Fig.6 Temperature distribution at cavity frontal and back boundaries in initial temperature fields
The cavity length and the entrance velocity are both constants, which results in an invariable fully filling time. Hence, at the cavity entrance, the time difference between the forward filling melt and the reverse one is a constant.
It can be seen that the unsymmetrical feature of the initial temperature field in the selected section causes a continuous unsymmetrical variation in the temperature field during the process of subsequent solidification. As a result, the final solidified region departs from the valve axis. Considering some metallurgical and thermodynamic parameters of TiAl alloy, it is evident that solidification starts in the border area and after a short time a solid bridge forms in the central area. Therefore, feeding will be restricted, then leading to the formation of off-center porosities.
The results of several laboratory tests show that optimizing some cast parameters can minimize the offset of the porosities, such as the entrance length, the rotation speed and the preheating temperature.
4 EXPERIMENTAL VERIFICATIONS
TiAl valves should be manufactured in such a way that no macroscopic shrinkage cavities appear in the valve body and the micro-porosities are predominantly in the central axis of the valve. In past work[16], twelve as-cast TiAl valve blanks manufactured in this way were HIPped and five of them could not be applied to the engine test due to their bent stems.
By optimizing the parameters, the following values were suggested: entrance velocity 0.6-1.3m/s; rotation speed >300r/min; entrance length >80mm; preheating temperature of the mold >400℃. In this way, 48 TiAl valve blanks were manufactured and no obvious off-center porosity was observed. Moreover, 12 blanks were HIPped and none of them appeared in a bent stem.
5 CONCLUSIONS
1) The effect of centrifugal field results in the phenomenon that flow in the valve cavity consists of forward flow and backward one.
2) Unsymmetrical initial temperature distribution in the valve cavity will cause a continuous unsymmetrical variation in the following solidification, which makes final solidified region depart from the cavity axis and then leads to the occurrence of off-center porosity.
3) Following values are suggested by optimizing some parameters for the manufacture of TiAl valves: entrance velocity 0.6-1.3m/s; rotation speed >300r/min; entrance length >80mm; preheating temperature of the mold >400℃.
REFERENCES
[1]Dimiduk D M, Miracle D B, Ward C H. Development of intermetallic materials for aerospace systems [J]. Materials Science and Technology, 1992, 8(3): 367-375.
[2]PENG Chao-qun, HE Yue-hui, HUANG Bai-yun, et al. Effects of rapid heating cyclic heat treatment on microstructures and compression mechanical properties of TiAl based alloy [J]. Trans Nonferrous Met Soc China, 2001, 11(3): 459-463.
[3]HE Yue-hui, LIU Ye-xiang, HUANG Bai-yun. Effect of Pb addition on TiAl based alloys [J]. Trans Nonferrous Met Soc China, 1994, 4(1): 75-79.
[4]CHEN Ling-hui, HUANG Bai-yun, QU Xuan-hui. The study of a multi-thermal-mechanical process for TiAl based alloys [J]. The Chinese Journal of Nonferrous Metals, 1996,6(1): 120-126. (in Chinese)
[5]Eylon D, Newman J R, Thone J K. Titanium and Titanium Alloy Castings [M]. ASM Handbook. Formerly Tenth Edition. ASM International, 1992. 634-646.
[6]Tanaka T. New development in titanium elaboration-sponge, melting and casting [A]. Processings of the Sixth World Conference on Titanium [C]. France, 1988. 11-22.
[7]Zwicker U. Evaluation of centrifugally cast TiAl5-Fe2.5 alloy for implant material, titanium science and technology [A]. Proceedings of the Fifth International Conference on Titanium [C]. FRG, 1984. 112-118.
[8]Blum M, Choudhury A, Scholz H, et al. Properties of low cost TiAl automotive valves produced by cold wall induction melting and permanent mold centrifugal casting [A]. Kim Y M, Dimiduk D M, Loretto M H. Gamma Titanium Aluminides [C]. The Minerals, Metals & Materials Society, 1999. 35-39.
[9]HUANG Zhao-hui. Isothermal forging of γ-TiAl alloys [J]. Trans Nonferrous Met Soc China, 2003, 13(6): 1225-1328.
[10]Allison J E, Sherman A M, Bapna M R. Titanium in engine valve system [J]. Journal of Metals, 1987(3): 15-18.
[11]SHENG Wen-bin, LI Dong, YANG Rui, et al. An analysis of the filling process of Ti6Al4V alloy melt poured in permanent mold during centrifugal casting process [J]. Trans Nonferrous Met Soc China, 2001,11(3): 353-357.
[12]Hwang W S, Stoehr R A. Fluid flow modeling for computer-aided design of castings [J]. Journal of Metals, 1983, 8: 22-30.
[13]Jonsson P. Fluid phenomena in the filling of cylindrical molds using newtonian(turbulent) and non-newtonian(power law) fluids [J]. AFS Trans, 1991, 291-297.
[14]LI Ya-min, XING Shu-ming, ZHAI Qi-jie. Numerical simulation of semisolid continuous casting process [J]. Trans Nonferrous Met Soc China, 2001, 11(3): 378-381.
[15]Wang J Q, Hansen S F, Hansen P N. 3-D modeling and simulation of mold filling using PCs [A]. Giamei A F, Abbaschian G J. Modeling of Casting and Welding Process Ⅳ [C]. TMS, 1988. 741-753.
[16]SHENG Wen-bin, LI Dong, YANG Rui, et al. Researching on the Ti-48Al-2Cr-2Nb automobile exhaust valve formed in permanent mold during centrifugal casting process [J]. J Mater Sci Tech, 2001, 17(1): 1-4.
(Edited by YANG Bing)
Received date: 2004-06-10; Accepted date: 2005-03-24
Correspondence: SHENG Wen-bin, PhD; Tel: +86-533-2786815; E-mail: wbsheng@sdut.edu.cn