Trans. Nonferrous Met. Soc. China 25(2015) 1454-1459
Microstructures of PM Ti-45Al-10Nb alloy fabricated by reactive sintering
Hong-fei SUN1, Xue-wen LI2, Wen-bin FANG1,2
1. School of Materials Science and Engineering, Harbin Institute of Technology, Harbin 150001, China;
2. School of Materials Science and Engineering, Harbin University of Science and Technology, Harbin 150040, China
Received 30 June 2014; accepted 8 December 2014
Abstract: Powder metallurgy Ti-45Al-10Nb alloys was successfully fabricated by reactive sintering of milled powders at 1350 °C for 2 h in vacuum. The microstructure, in particular, constituent phases, grain size, precipitates of the product was investigated in detail. The results indicate that a double phase γ+α2 microstructure containing Ti2AlC precipitate is obtained under the sintering condition, and the alloy exhibits a fine and homogenous microstructure compared with traditional TiAl base. In fine grain structure, the average grain sizes for the γ and α2 phases are (2.3±0.05) and (5.6±0.05) μm, respectively. Additionally, numerous dislocations are observed in the alloy, and the dislocation density in γ phase is significantly higher than that in α2 phase. The formation mechanisms of the dislocation in the present alloy were also discussed in detail.
Key words: high Nb-TiAl alloy; powder metallurgy; microstructure; dislocation
1 Introduction
TiAl based alloys are highly promising for elevated temperature structural applications in aerospace and automotive industries, due to their attractive properties, such as low density, good elevated temperature strength, high resistance to oxidation, and excellent creep properties [1-3]. However, the low room temperature ductility and poor deformability cause the conventional manufacturing operations such as rolling, forging, or drawing to be difficult and has restricted their application [4,5]. Accordingly, it is of great significance to develop effective techniques for preparation and forming for this alloy system. The powder metallurgy (PM) process is a near-net or net-shape manufacturing process and has been considered to be an attractive process in order to produce TiAl alloys with a fine-grained microstructure [6,7]. Compared with IM processes, PM methods, when a pre-alloyed TiAl powder is used, can decrease the retention of B2 phase in the microstructure [8], and fine and homogenous microstructure can be obtained. Besides, the PM-TiAl alloy does not need the subsequent strenuous thermomechanical process aiming to obtain a fine and homogenous microstructure, which is indispensable to the TiAl alloy fabricated by IM due to the solidification defects [9]. Among the powder metallurgy techniques studied recently, elemental powder metallurgy (EPM) has drawn intensive attention because of its low cost, good formability and convenient addition of alloy elements. Thus, some efforts have been conducted to the fabrication of the TiAl alloy through the EPM process [10-12]. However, the reactions taking place in such process are often complicated and have not been well understood due to the TiAl matrix phases formed as a result of complex reactions during the consolidation. Thus, we investigated the phase formation and the microstructure in the Ti-Al-Nb systems after the fabrication of the TiAl alloy. It is expected that the understanding of the reaction behaviors in the present systems can permit a better control of the reaction process through the regulation of processing parameters, and also provide a guide for producing the high-content Nb TiAl alloys with tailored microstructures and properties.
In the present work, PM Ti-45Al-10Nb (mole fraction, %) alloys were synthesized with the mechanical milling and reactive sintering process. The results of investigations on the microstructural development within the sintered alloy, as well as the formation mechanisms, were reported here. It is expected that this study would further promote the development and engineering applications of high niobium containing gamma TiAl alloys.
2 Experimental
Commercial powders of Ti (99.6% purity, ~44 μm), Al (99.9% purity, ~47 μm), Nb (99.6% purity, ~44 μm), and stearic acid (C18H36O2) were used as the starting materials. Ti-45Al-10Nb alloy with stearic acid addition of 1% (mass fraction) was fabricated by an elemental powder metallurgy process which involves mechanical milling and subsequent reactive sintering. The synthesis of the milled powders to fully dense compacts was conducted at 1350 °C under load of 50 MPa for 2 h with a heating rate of 5 °C/min, and then the compacts were annealed at 1050 °C for 2 h. The phase contents of as-fabricated alloys were examined by X-ray diffraction (XRD) using Cu Kα radiation (λ=0.1546 nm). The detailed microstructures were subsequently examined using optical microscopy (OM), scanning electron microscopy (SEM) and transmission electron microscopy (TEM). SEM observations were operated on an FEI Quanta 200F scanning electron microscope, equipped with backscattered electron image. Conventional TEM observations were conducted on a FEI Tecnai F30 operating at 130 kV. TEM foils were prepared by a standard twinjet electropolishing technique in an electrolyte of 60% methanol, 35% butyl alcohol and 5% perchloric acid at ~15 V and -30 °C.
3 Results and discussion
3.1 Phases of as-prepared TiAl alloys
An XRD pattern generated from as-prepared TiAl alloy of composition Ti-45Al-10Nb is shown in Fig. 1. It reveals that the alloy primarily consists of γ phase, α2 phase and a small amount of Ti2AlC phases. The volume fraction of Ti2AlC phase calculated by the adiabatic method according to the XRD result is about 8.9%. The carbon element in the Ti2AlC phase was from the decomposition of the stearic acid C18H36O2. When the sintering temperature was about 400 °C, the stearic acid was decomposed, and the carbon was left in the composite powder. Moreover, the diffraction peak of Nb was not detected in the TiAl composites. According to previous work [13], Nb has a solubility of about 20% in TiAl alloys, depending on temperature. The Nb element in the TiAl composites is mainly in the form of solid solution. This result indicates that two-phase TiAl composites reinforced with Ti2AlC could be fabricated in situ by the method of the hot press consolidation of milled powder in the Ti-Al-Nb-C system. Based on these considerations, a detailed analysis of the sintered microstructures is presented in the following sections.
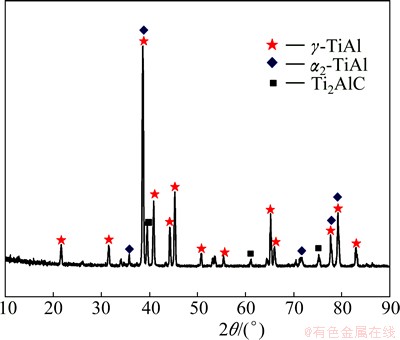
Fig. 1 XRD pattern (Cu Kα) generated from as-prepared alloy sample
3.2 As-sintered microstructure
In general, a two-phase (γ and α2) fully lamellar microstructure is developed in the α-phase field within the alloys fabricated at 1350 °C. Figure 2 shows the microstructures of the sample sintered at 1350 °C. Obviously, a distinct microstructure marked by A and B can be observed in different regions of the micrograph shown in Fig. 2(a). Detailed views of regions A and B in Fig. 2(a) at high magnification are shown in Figs. 2(b) and (c), respectively. In region A, grayish precipitates are homogeneously dispersed in the matrix. EDX point analyses have shown that in the grayish particle, the mole fractions of Ti, Al and Nb elements are 59.14%, 34.58% and 6.18%, respectively. According to the above XRD results, the grayish phase is identified as Ti2AlC. On the reverse, in region B (Fig. 2(c)), the Ti2AlC precipitate is less discernable. EDS analyses have shown that Nb is concentrated in these regions, as shown in Table 1. This explains why the phases in region A exhibit a clearer bright contrast than those in region B. The OM images of the two areas are shown in Figs. 3(a) and (b), respectively. It is clear that, in region A, the alloy shows duplex microstructure made of a mixture of lamellar colonies and of γ grains. A great deal of twin structures can also be observed. However, in region B, the microstructure is near full lamellar (α2 and γ plates) with a grain size of 20-60 μm (Fig. 3(b)). In addition, there is a very small percentage of equiaxed γ phase, which exists at the grain boundaries. The presence of lamellar colonies in the sintered condition can be ascribed to the fact that the sintered temperature is above Tα. Evidently, inhomogeneity of the microstructure of the sintered alloy is caused by the distribution of elements in the milled powder.
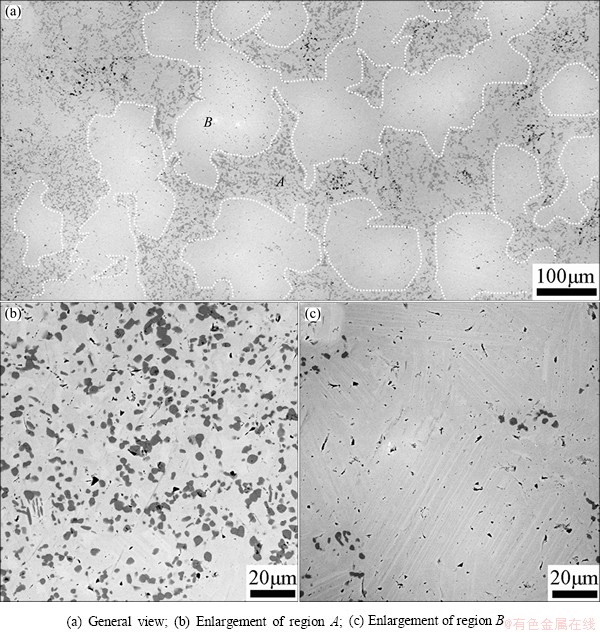
Fig. 2 SEM-BSE microstructures of Ti-45Al-10Nb alloy sintered at 1350 °C
Table 1 EDS analysis of regions A and B in Fig. 2(a)

To further investigate the structure and composition of the micro-constituent phases within the microstructures mentioned above, TEM analysis was performed. A typical microstructure can be found in different regions of the micrograph shown in Fig. 4(a). According to selected area diffraction (SAD) analyses, the coarse grains (1-4 μm) in the middle region have α2 structure and the fine grains (0.5-1 μm) around the coarse grains are mainly a mixture of γ and α2 grains. The two-phase microstructure composed of equiaxed γ (L10, TiAl) and α2 (DO19, Ti3Al) grains were formed via the α→γ+α→γ+α2 transition reactions. Typical lamellar microstructures within colony grains observed from the sintered alloys are shown in Fig. 4(b). The colony grain sizes are 20-60 μm, the width of γ lamellae varies between 0.17 μm and 1.2 μm and the width of α2 lamellae varies between 0.06 and 0.41 μm. These values are considerably finer than the values in lamellar TiAl alloys fabricated by conventional processing techniques [14,15]. In addition, the alloy also contains many elongated grains of Ti2AlC phase, as shown in Fig. 4(c). The
zone diffraction pattern of the Ti2AlC phase is shown in Fig. 4(d). The synthesized Ti2AlC particles mainly distribute at grain boundaries, which can improve the strength of TiAl composite. Despite some heterogeneities in the local chemical composition and the repartition of the Ti2AlC precipitates detected, the alloy exhibits much fine-grained microstructure compared with traditional TiAl base. To homogenize the alloy at the aim of improving its properties, subsequent thermal treatments would be performed.
3.3 Dislocations in as-sintered alloy
As illustrated in Fig. 4(c), in the γ phase, numerous dislocations are generally curved or bowed and dislocation lines are extensively intersected and pinned. The dislocations in the lamellae and at the grain boundary gamma in lamellar samples are mostly 1/2<110> ordinary dislocations but some are 1/2<112> super-dislocations. They are believed to originate from the thermal stresses (coherency stress) generated between different lamellae during cooling from high temperature. Other types of dislocations are also identified in the sintered microstructure, as indicated in Fig. 5. Figures 5(a) and (b) show rectilinear dislocations which are anchored at many pinning points, as very frequently observed in the γ phase of deformed TiAl alloys [16,17]. Such morphology illustrates that slip systems are operating simultaneously and locks are formed during the densification step. The dislocation density in γ phase is obviously higher than that in the α2. The high density of dislocations confirms that the γ grain is not recrystallized, but strongly deformed at the end of the reactive sintering process. Similar anomalous microstructure has been observed in γ-TiAl alloys [18].
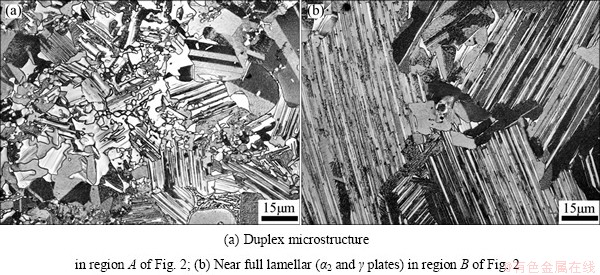
Fig. 3 OM micrographs of Ti-45Al-10Nb sample sintered at 1350 °C with double-phase microstructure
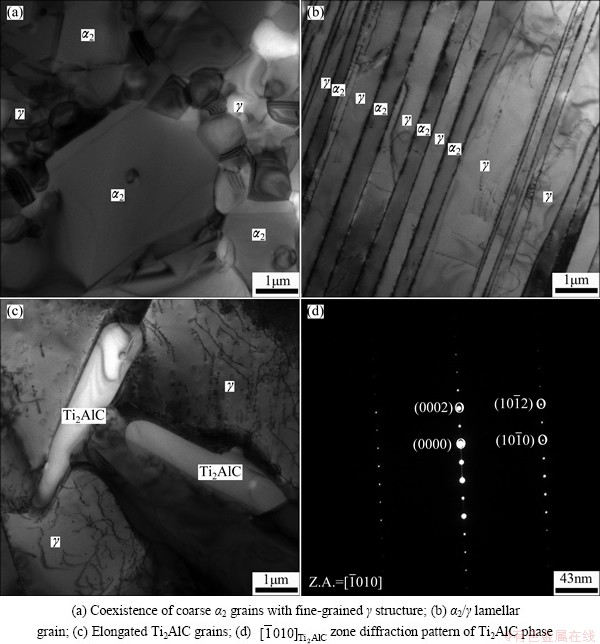
Fig. 4 TEM micrographs of duplex microstructures
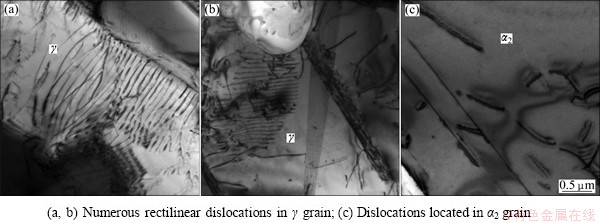
Fig. 5 TEM images of dislocations observed in specimen sintered at 1350 °C
4 Conclusions
1) The microstructure of powder metallurgy TiAl alloys with nominal compositions Ti-45Al-10Nb consists of double-phase (α2+γ) microstructure containing some fine Ti2AlC ceramic precipitates.
2) The coarse grains of α2/γ lamellar and fine grains of γ and α2 are found in the sintered compacts. The heterogeneities in the local chemical composition and the repartition of the B2 precipitates are also detected.
3) The dislocations in the lamellae and at the grain boundary gamma in lamellar samples are mostly 1/2<110> ordinary dislocations. The dislocation densities in γ phase are higher than those in α2 phase.
References
[1] KABIR M R, CHERNOVA L, BARTSCH M. Numerical investigation of room-temperature deformation behavior of a duplex type γ TiAl alloy using a multi-scale modeling approach [J]. Acta Materialia, 2010, 58: 5834-5847.
[2] DIMIDUK D M. Gamma titanium aluminide alloys—An assessment within the competition of aerospace structural materials [J]. Materials Science and Engineering A, 1999, 263: 281-288.
[3] ZHOU Can-xu, LIU Bin, LIU Yong, QIU Cong-zhang, HE Yue-hui. Effect of carbon on microstructures of Ti-45Al-3Fe-2Mo-xC alloy [J]. Transactions of Nonferrous Metals Society of China, 2014, 24(6): 1730-1736.
[4] APPEL F, PAUL J D H, OEHRING M. Gamma titanium aluminide alloys: Science and technology [M]. Weinheim: Wiley–VCH Verlag & Co., 2011: 71-240.
[5] LU Bin, HUANG Lan, LIU Yong, LIANG Xiao-peng, LIU Bin, HE Yue-hui, LI Hui-zhong. Evolution of lamellar structure in Ti-47Al- 2Nb-2Cr-0.2W alloy sheet [J]. Transactions of Nonferrous Metals Society of China, 2013, 23(5): 1293-1298.
[6] JABBAR H, MONCHOUX J, HOUDELLIER F, DOLLE M, SCHIMANSKY F, PYCZAK F. THOMAS M, COURET A. Microstructure and mechanical properties of high niobium containing TiAl alloys elaborated by spark plasma sintering [J]. Intermetallics, 2010, 18: 2312-2321.
[7] ZHANG Wei, LIU Yong, LIU Bin, LI Hui-zhong, TANG Bei. Deformability and microstructure transformation of PM TiAl alloy prepared by pseudo-HIP technology [J]. Transactions of Nonferrous Metals Society of China, 2010, 20(4): 546-552.
[8] LIU B, LIU Y, ZHANG W, HUANG J S. Hot deformation behavior of TiAl alloys prepared by blended elemental powders [J]. Intermetallics, 2011, 19: 154-159.
[9] QIU Cong-zhang, LIU Yong, HUANG Lan, LIU Bin, ZHANG Wei, HE Yue-hui, HUANG Bai-yun. Tuning mechanical properties for β(B2)-containing TiAl intermetallics [J]. Transactions of Nonferrous Metals Society of China, 2012, 22(11): 2593-2603.
[10] FANG W B, HU L X, HE W X, WANG E D, LI X Q. Microstructure and properties of a TiAl alloy prepared by mechanical milling and subsequent reactive sintering [J]. Materials Science and Engineering A, 2005, 403: 186-190.
[11] SUN Hong-fei, LI Xue-wen, FENG Jie, FANG Wen-bin. Characterization of TiAl-based alloy with high-content Nb by powder metallurgy [J]. Transactions of Nonferrous Metals Society of China, 2012, 22(S2): s491-s495.
[12] WANG Yan-hang, LIN Jun-pin, HE Yue-hui, WANG Yan-li, LIN Zhi, CHEN Guo-liang. Reaction mechanism in high Nb containing TiAl alloy by elemental powder metallurgy [J]. Transactions of Nonferrous Metals Society of China, 2006, 16(4): 853-857.
[13] HELLWIG A, PALM M, IIDEN G. Phase equilibria in the Al-Nb-Ti system at high temperatures [J]. Intermetallics, 1998, 6: 79-94.
[14] ZHANG J, JING Y J, FU M J, GAO F. Microstructure optimization of ingot metallurgy TiAl [J]. Intermetallics, 2012, 27: 21-25.
[15] APPEL F, OEHRING M, PAUL J D H. Nano–scale design of TiAl alloys based on β-phase decomposition [J]. Advanced Engineering Materials, 2006, 8: 371-376.
[16] ZHANG C P, ZHANG K F. Tensile behaviors of fine–grained γ-TiAl based alloys synthesized by pulse current auxiliary sintering [J]. Materials Science and Engineering A, 2009, 520: 101-104.
[17] PAIDAR V, INUI H, KISHIDA K, YAMAGUCHI M. Dislocation dissociation in TiAl alloys [J]. Materials Science and Engineering A, 1997, 233: 111-115.
[18] JABBAR H, MONCHOUX J P, THOMAS M, COURET A. Microstructures and deformation mechanisms of a G4 TiAl alloy produced by spark plasma sintering [J]. Acta Materialia, 2011, 59: 7574-7585.
反应烧结制备Ti-45Al-10Nb合金的显微组织
孙宏飞1,李学问2,房文斌1,2
1. 哈尔滨工业大学 材料科学与工程学院,哈尔滨 150001;
2. 哈尔滨理工大学 材料科学与工程学院,哈尔滨 150040
摘 要:对球磨后的粉末在1350 °C保温2 h进行反应烧结,制备Ti-45Al-10Nb合金。对烧结坯料的显微组织,尤其对相组成,晶粒尺寸及颗粒的分布进行细致研究。结果表明,在此烧结条件下,材料的显微组织主要由Ti2AlC颗粒强化的双相γ+α2组织组成,相对于传统TiAl基合金,该合金呈现出细小、均匀的显微组织。在细晶区,γ相和α2相的平均晶粒尺寸分别为(2.3±0.05)和(5.6±0.05) μm。此外,合金中存在大量位错,且γ相中的位错密度远高于α2相中的位错密度,对位错形成机理进行分析。
关键词:高Nb-TiAl合金;粉末冶金;显微组织;位错
(Edited by Yun-bin HE)
Corresponding author: Xue-wen LI; Tel: +86-451-86418713; E-mail: lixuewen2000@163.com
DOI: 10.1016/S1003-6326(15)63745-1