J. Cent. South Univ. (2012) 19: 231-237
DOI: 10.1007/s11771-012-0996-3
Properties and mechanism of red mud in preparation of ultra-lightweight sludge-red mud ceramics
LU Da-wei(陆达伟), QI Yuan-feng(齐元峰), YUE Qin-yan(岳钦艳), XI Fei(郗斐), GAO Bao-yu(高宝玉)
Shandong Key Laboratory of Water Pollution Control and Resource Reuse,
School of Environment Science and Engineering, Shandong University, Ji’nan 250100, China
? Central South University Press and Springer-Verlag Berlin Heidelberg 2012
Abstract: New ultra-lightweight sludge-red mud ceramics (ULS-RMC) were prepared by red mud (RM), clay and dried sewage sludge (DSS). The properties and mechanism of RM in the preparation of ULS-RMC were discussed. The chemical components, thermal properties and mineral phases of RM were determined by energy dispersive X-ray (EDX), differential scanning calorimetry/thermal gravimetric analysis (DSC/TGA) and X-ray diffraction (XRD), respectively. Constant dosage of DSS to clay and different amounts of RM were utilized in the preparation of ULS-RMC. Physical properties test (bulk density, grain density, water absorption and expansion ratio), XRD and scanning electron microscopy (SEM) were employed to characterize the ULS-RMC. The results show that RM exhibits high hydroscopic property and good water-retention property, and bloating property and fluxing property of RM are caused by abound of gaseous components and flux, respectively. The two chemical properties are utilized to discuss the mineral phases and microstructures differences between ULSC and ULS-RMC.
Key words: ultra-lightweight ceramic; red mud; sludge; bloating mechanism
1 Introduction
In China, more and more sewage and wastewater treatment plants are founded, and the discharged sludge which will cause secondary pollution increases annually [1-2]. Researches are focused on the disposal of sludge, such as incineration, sanitary landfill, compost, production of activated carbon, oil and methane [3-8] etc. Red mud (RM) is the solid waste residue from the caustic soda leaching of bauxite ores during the preparation of alumina. Only a small fraction of the produced red mud is utilized in other industrial processes or applications [9-12]. Ceramic materials, which have favorable properties such as low density, heat insulation and quake-proof, are wildely used in building materials and environmental protection [13-16]. According to the bulk density [17], the ceramic materials could be classified into normal ceramic (the bulk density larger than 1 100.0 kg/m3, and could be used in wastewater treatment), lightweight ceramic (the bulk density ranged from 510.0 to 1 100.0 kg/m3, and could be used in wastewater treatment and lightweight concrete bricks) and ultra-lightweight ceramic (the bulk density less than 510.0 kg/m3, and could be used in ultra-lightweight concrete bricks). Because of the shortage of natural materials and the increasing demand of civil engineering, dried sewage sludge (DSS) or RM was studied by many researchers for preparing ceramic materials. MERINO et al [18-19] and CHEESEMAN and VIRD [20] developed normal ceramics with clay and DSS, the bulk densities of which were 1 549.0 kg/m3 and 1 350.0 kg/m3, respectively. WANG et al [21] and MUN [22] developed lightweight ceramics with clay and DSS, the bulk densities of which were 930.0 kg/m3 and 600 kg/m3, respectively. SGLAVO et al [23-24] developed normal ceramics with RM and Italy clay, England clay, respectively, the bulk densities of which were 1 500.0 kg/m3 and 1 600.0 kg/m3, respectively. RM was utilized for the preparation of ceramics materials by SRIKANTH [25], and the minimum bulk density was 1 700.0 kg/m3.
It is apparent that: 1) the above mentioned ceramic materials mostly are lightweight, normal or heavy ceramics, and ultra-lightweight ceramics are rarely found; and it is “shrinkage ratio” rather “expansion ratio” that has frequently been used during the characterization of those sludge or RM ceramic materials; 2) during the preparation of certain ceramics, both the properties and mechanism of single phases or two-phases raw material system can be studied quite easily, for example, clay and DSS (clay-DSS system, utilized in Refs. [18-22]), clay and RM (clay-RM system, utilized in Ref. [24]), and RM (single system, utilized in Ref. [26]). But if three or more raw materials are utilized for ceramic materials, which can be called three-phase raw material system and more-phase raw material system, respectively, the stages of research will be complex [25]; 3) until now, there are few studies on the properties and mechanism of RM in the preparation of ultra-lightweight ceramics.
Based on the preparation of ultra-lightweight sludge ceramic in Ref. [17] (two-phases system, viz clay-DSS system), this work tries to investigate the properties and mechanism of RM in the preparation of ultra-lightweight sludge-red mud ceramics (ULS-RMC, three-phase raw material system).
2 Experimental
2.1 Pretreatment of raw materials
Dehydrated sewage sludge (DSS) was obtained from Ji’nan Wastewater Treatment Plant. Clay, which showed a dead dark brown and more suitable for the preparation of ultra-lightweight ceramic, was obtained from a brickfield in Zibo City, Shandong Province, China [17]. Red mud was obtained from the Shandong Branch of Aluminum Corporation of China Limited as a mixture containing about 60%-70% (mass fraction) of solids. DSS, RM and clay were dried in stove at 105 °C for 4 h, crushed in a ball mill, sieved with a mesh with the diameter of 0.154 mm, and preserved in polyethylene vessels until being used to avoid humidification. The moisture content, volatile content, loss on ignition, and calorific value of sewage sludge are 76.43%, 46.51% (dry basis), 65.83% (dry basis, mass fraction) and 18.50 MJ/kg (dry basis), respectively. In addition, there existed abundant organic substance in DSS which could cut down the cost of additional energy. The chemical components of DSS and clay are reported in Table 1.
Table 1 Chemical components of DSS and clay (mass fraction, %)
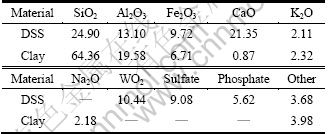
The high content of phosphate and sulfate which caused odor of the DSS was attributed to the wastewater treatment process that was in lack of phosphorus removal process.
2.2 Property test of RM
The chemical components of RM were determined by energy dispersive X-ray (EDX) detector, and DZ10-100 equipment was used during the determination. Before the thermal properties test, RM was stored in a porcelain dish at 25 °C in air (air humidity of 50%) for 24 h. The thermal properties of RM were analyzed with thermal gravimetric analysis (TGA) and differential scanning calorimetry (DSC). SDT Q600 equipment was used and heated in air at a rate of 10 °C/min in the range between room temperature and 1 100 °C. Data shown as percentages of mass loss were a function of temperature. DSC spectrum was obtained by SDT Q600 equipment at the same time. The mineral phases of RM (clay was tested at the same time) were determined by XRD (D/MAX-RA equipment, made in Japan) and a diagram record was made with a goniometer, which explored the interval of 2θ angles from 20°-70°.
2.3 Preparation of ULS-RMC
The mass ratio of clay to DSS was 8:2, which was constant all through the preparation process. Red mud was added into the clay-DSS system at mass fractions of 1%, 3%, 5%, 7% and 9%, respectively. Clay, RM and DSS were stirred in a dry powder stirrer for 10 min (B10-20B, made in China), and then the mixture was poured into a pelletizer (DZ-20 equipment) to produce pellets (about 7% (mass fraction) of water was added in this process). Two sieves (the diameter of meshes was 5 mm and 6 mm, respectively) were used to sift the raw pellets, which were selected for the subsequent treatment. Before thermal treatment, raw pellets were settled in a draught cupboard at room temperature for 24 h. After the drying treatment, the raw pellets were preheated at 400 °C for 20 min in a muffle furnace (anaerobic condition) and then were rapidly shifted into an electric tube furnace at sintering temperature of 1 150 °C for 10 min. The physical properties (bulk density, grain density, water absorption and expansion ratio) were used to determine the effect of the addition of RM on the preparation of ULS-RMC. In order to describe these processes more concisely and briefly, the constant dosage of clay to DSS (8:2, mass ratio) was called clay-DSS system, and the additions of RM ranging from 1% to 5% and from 5%-9% into clay-DSS system was called ULS-RMC (1%-5%) system and ULS-RMC (5%-9%) system for short, respectively. The above- mentioned physical properties were obtained as follows:
(1)
(2)
(3)
(4)
where ρb is the bulk density; m is the mass of ceramic body; Vb is the bulk volume of ceramic bodies; ρg is the grain density; V is the volume of ceramic bodies; aw is the water absorption; ms is the saturated mass of ceramic bodies; md is the mass of dry ceramic bodies; re is the expansion ratio; Vs is the volume of sintered ceramic bodies; Vr is the volume of raw pellets bodies.
2.4 Characterization of ULS-RMC
The mineral phases of ULS-RMC (9% of RM addition) and ULSC (prepared by the dosage of clay to DSS of 8:2) were examined by X-ray diffraction (XRD). In addition, the mineral phases of ULS-RMC and RM were described in comparison with ULSC and clay. The surface and fracture surface images (Au coated) of ULS-RMC (9% of RM addition) were examined by scanning electron microscope (SEM) to investigate the microstructures (in comparison with ULSC).
3 Results and discussion
3.1 Chemical components of RM
The chemical components of RM are shown in Table 2.
Table 2 Chemical components of RM (mass fraction, %)

The major chemical components in RM are CaO (26.62%) and SiO2 (25.66%), followed by Al2O3 (18.12%), Fe2O3 (13.50%), Na2O (9.55%), TiO2 (4.31%) and MgO (2.22%). The efflorescence properties of RM are directly attributed to the high content of CaO and Na2O, and the high content of Fe2O3 causes an orange-red color of red mud. The chemical components of clay and RM could be classified into three groups [27]: the glassy phases (SiO 2 and Al2O3, which form the framework and surfaces of ceramics); the gaseous components (carbon and Fe2O3, which generate gases and bloat the ceramic bodies in the sintering process); flux (alkali metal oxide and alkaline earth metal such as CaO, Na2O, K2O and MgO, which lower down the melting point). The mentioned three groups of RM and clay are compared in Fig. 1. As can be seen, glassy phases in clay are 83.94%, which exceeds the glassy phases in RM (43.78%) very much, but the flux in clay is fewer than that in RM. However, the content of gaseous components in RM is more than that in clay. It could be inferred that RM has high properties both in bloating the ceramic and lowering down the melting point of the clay-DSS system, but could not provide enough glassy phases to form the framework inside and outside the ceramics.
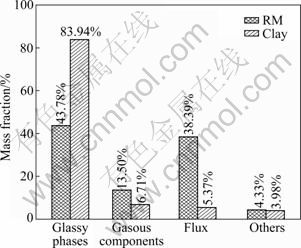
Fig. 1 Comparisons between RM and clay in chemical components
3.2 Thermal analysis of RM
The thermal analysis, viz DSC/TGA curves are reported in Fig. 2.
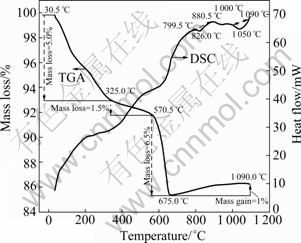
Fig. 2 Thermal analysis (DSC/TGA) of RM
As the TGA curve shows in Fig. 2, a consequent mass loss (about 5%) happens from 30.5 °C to 325.0 °C, and then trends smoothly before 570.5 °C. The mass loss between 325.0 °C and 570.5 °C is 1.5%. A sharp drop exists between 570.5 °C and 675.0 °C, and the mass loss is 6.5%, which precisely equals the mass loss from 30.5 °C to 570.5 °C. As the DSC curve reports before 675.0 °C, two consequent endothermic broad peaks exist at 200-430 °C and 500-675.0 °C, which are attributed to the emission of water. But, the water evaporating from different temperature ranges has different origins: 1) when the temperature ranges from 30.5 °C to 325.0 °C, the mass loss is caused by the emissions of absorbed water (the RM sample is stored in a porcelain dish at 25 °C in air with air humidity of 50%) and part of interstitial water, which indicates that RM has high hydroscopic property [18-19]; 2) when the temperature ranges from 325.0 °C to 570.5 °C, water which belongs to interstitial water evaporated slowly. It could be inferred that RM has good water-retention property; 3) when the temperature achieves 675.0 °C, the structural water [18] existing in hydrate salts causes the sharp drop of mass loss. Two endothermic peaks are shown on DSC curve at 826.0 °C and 1 050 °C, respectively. The prime endothermic peaks ranging from 799.5 °C to 880.5 °C are probably attributed to the decomposition of carbonate or the melt of alkali metal oxide [17]; the following endothermic peaks (ranging from 1 000 °C to 1 090 °C) would be attributed to the melt of alkaline-earth metal oxide. About 1% of mass gain is reported on TGA curve ranging from 675.0 °C to 1 090 °C, which is probably attributed to new mineral phases formed by oxygen in air and the original mineral phases.
3.3 Physical properties during preparation of ULS- RMC
The physical properties (volume expansion ratio, bulk density, grain density and water absorption (by mass fraction)) of ULSC and ULS-RMC are reported in Fig. 3.
The bulk density, grain density, water absorption and expansion ratio of ULSC are 353.7 kg/m3, 869.0 kg/m3, 24.6% and 18.8%, respectively. It is obviously shown in Fig. 3 that when the addition of RM is 5%, the samples have the maximum expansion ratio (22.2%) and minimum bulk density (310.0 kg/m3) and grain density (789.0 kg/m3). In the ULS-RMC (1%-5%) system, the expansion ratio increases with the increase of the addition of RM, but the bulk density and grain density decrease with the increase of addition of RM. Directly opposite appearances of expansion ratio, bulk density and grain density are reported in the ULS-RMC (5%-9%) system. The water absorption reveals permanent decreasing trends with the addition of RM.
3.4 XRD analysis of RM, clay, ULSC and ULS-RMC
The mineral phases existing in RM, clay, ULSC and ULS-RMC (9% of RM addition) were tested by XRD and reported in Fig. 4.
Based on the XRD analysis, the following information can be found: 1) Mineral phases existing in clay are quartz (SiO2), anorthoclase (CaAl2Si2O8) and brinrobertsite ((Na,K,Ca)0.35(Al,Fe,Mg)4(Si,Al)8O20OH)4·3.54(H2O)). 2) The mineral phases in ULSC are quartz (SiO2) and albite-calcian ordered (NaCaAl (SiAl)2O8). The mineral phase, albite-calcian ordered, in ULSC is generated from the decomposition and dehydration of brinrobertsite in clay. The quartz in ULSC probably originates from clay. 3) The mineral phases in RM are chesterite ((MgFe2)17Si2O55(OH)6), calcium silicate oxide (Ca3(SiO4)O), quartz (SiO2) and riebeckite ((NaCa)2- (FeMgAl)5(Si,Al)8O22(OH)2). The water generated from the dehydration of riebeckite and chesterite (hydroxyl ions) causes the mass loss in Fig. 2, and this finite amount of water belongs to the structural water. During the thermal analysis of RM, ferrous iron in chesterite reacts with oxygen in air at the testing temperature ranging from 675.0 °C to 1 090.0 °C. It could be inferred that it is the oxidizing reaction that causes the mass gain in TGA curve. In addition, the mineral phase, calcium silicate oxide (Ca3(SiO4)O), could be rewritten as CaSiO3·2CaO, and the efforescence properties of RM are probably attributed to CaO in calcium silicate oxide. 4) The mineral phases in ULS-RMC (9% of RM addition) are anorthoclase (CaAl2Si2O8) and andesine (Na0.685- Ca0.347Al1.46Si2.54O8). By comparing the XRD patterns of ULSC and ULS-RMC, the disappearance of quartz is attributed to the fluxing properties of RM, and the inference mentioned in Section 3.1 and Fig. 2 is confirmed.
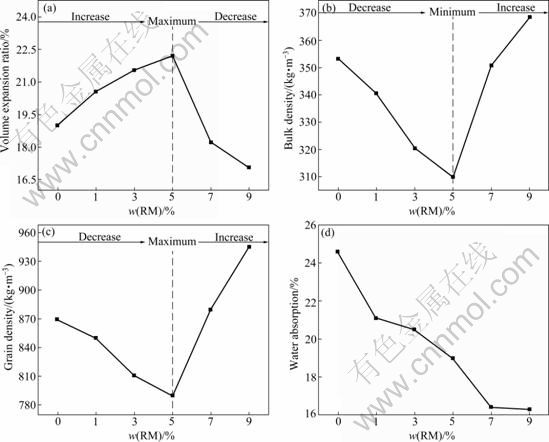
Fig. 3 Physical properties of ULS-RMC prepared with RM, clay and DSS: (a) Volume expansion ratio; (b) Bulk density; (c) Grain density; (d) Water absorption
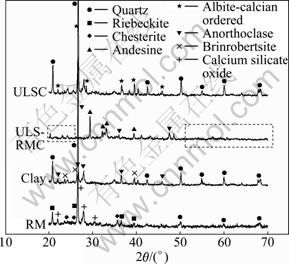
Fig. 4 XRD patterns of phases of RM, clay, ULSC and ULS- RMC (9% of RM added)
3.5 Microstructures comparisons of ULSC and ULS- RMC
The SEM images of ULSC and ULS-RMC (9% of RM addition) are shown in Fig. 5.
As the SEM images show in Fig. 5, both ULSC and ULS-RMC have porous structure. Analyzing surface and fracture surface of ULSC (Figs. 5(a)-(d)) and ULS- RMC (Figs. (e)-(h)), the following information could be found: 1) The surface of ULS-RMC is smoother than that of ULSC, and fewer apertures exist in the shell of ULS-RMC. It is inferred that the surfaces of ULS-RMC turn smoother with the increase of addition of RM, and lower down the water absorption, progressively. 2) The framework and diameter of aperture inside ULS-RMC is more powerful and larger than those in ULSC, which is probably due to the fluxing properties and high content of gaseous components of RM.
3.6 Effects and mechanism of RM in preparation of ULS-RMC
As mentioned in Section 3.1, abundance of gaseous components and flux but fewer glassy phases exist in RM. Combining the three chemical properties of RM, the characterizations of ULS-RMC, the previous studies [17], and investigations of DUCMAN and MIRTIC [28], it could be inferred that:
1) With the increase of addition of RM (ranging from 1% to 5%) into clay-DSS system, the high content of gaseous components in RM and the initial gaseous components in clay-DSS system would generate more gases which could further bloat the ceramic bodies (compared with gases generated in ULSC), and the shrinkage tension (generated by the glassy phases) decreases because of the increase of RM (fewer glassy phases than those in clay) at the same time. The bloating force [17, 28] would be more powerful than the shrinkage tension (but the bloating force decreases faster with the volume of the ceramic bodies), and the ceramic bodies keep expanding until the two forces achieve a balanced state. The abound gaseous components existing in RM are the main reason for the decrease of bulk density and grain density and the increase of expansion ratio in the ULS-RMC (1%-5%) system.
2) In the ULS-RMC (5%-9%) system, more RM is added, which results in even more gases released by both the added RM and the clay-DSS system, and the generated bloating force is more powerful than that generated in ULS-RMC (1%-5%) system and clay-DSS system, but the changes of shrinkage tension are opposite because of the reduction of glassy phases and the abundant flux in RM which flux and melt the glassy phases. Then, the bloating force would be much more powerful than the shrinkage tension, and the gases would break through the shell outside the ceramic. After a finite amount of gases is escaped, the bloating force would be more powerless than the shrinkage tension, and the ceramic bodies begin to shrink until the two forces achieve a balanced state. The amount of gaseous components and flux, the deficiency of glassy phases in RM are the reasons for the decrease of bulk density and grain density and the increase of expansion ratio in the ULS-RMC (1%-5%) system.
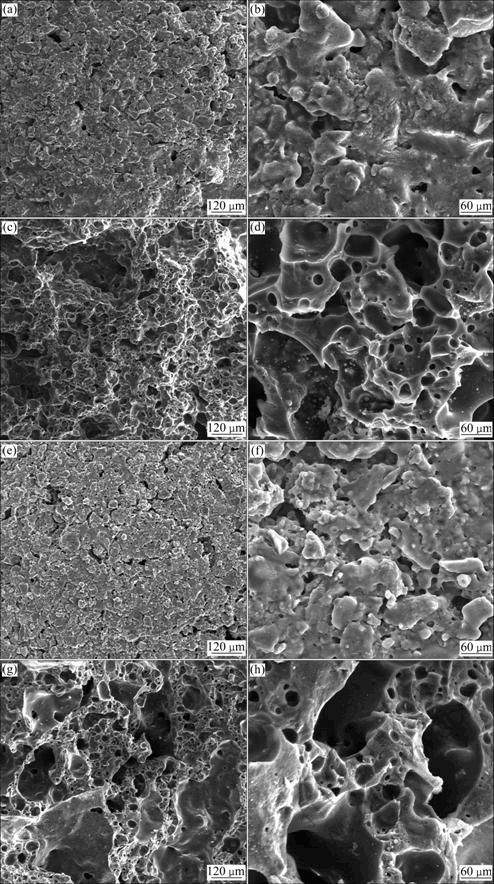
Fig. 5 SEM images of ULSC and ULS-RMC (9% of RM addition): (a), (b) Surface images of ULSC; (c), (d) Fracture surface images of ULSC; (e), (f) Surface images of ULS-RMC; (g), (h) Fracture surface images of ULS-RMC
3) Because of the fluxing properties of RM, the glassy phases of ULS-RMC (1%-5%) system and ULS- RMC (5%-9%) system would be easily melted than clay-DSS system. The melted glassy phases could form the shell easily and smoothly. That is the reason for the decrease of the water absorption with the increase of addition of RM and the less crystal phases existing in ULS-RMC than ULSC and the smoother surfaces and larger pores in ULS-RMC.
4 Conclusions
1) The thermal analysis shows that RM has high hydroscopic and good water-retention property.
2) Compared with the chemical components of clay, there are many gaseous components and flux in RM, which causes the bloating and fluxing properties of RM. During the preparation of ULS-RMC, the two chemical properties are used to explore the mechanism of clay-DSS system, ULS-RMC (1%-5%) system and ULS-RMC (5%-9%) system. The differences between ULSC and ULS-RMC (9% of RM addition) are mainly attributed to the bloating and fluxing property of RM, and differences of mineral phases between ULSC and ULS-RMC are mainly due to the fluxing property of RM.
3) The efflorescence property of RM is directly attributed to the high contents of CaO and Na2O, and the high content of Fe2O3 causes an orange-red color of red mud.
References
[1] Ministry of Environmental Protection of the People’s Republic of China. Solid waste. http://www.sepa.gov.cn/cont/gthw/
[2] Ministry of Environmental Protection of the People’s Republic of China. Pollution control. http://www.sepa.gov.cn/cont/index.htm
[3] LUCIE H, JAROSLAV B, VLADIMIR U, THOMAS E. Thermal processing of sewage sludge (II) [J]. Appl Therm Eng, 2008, 28(16): 2083-2088.
[4] LUOSTARINEN S, LUSTE S, SILLANPAA M. Increased biogas production at wastewater treatment plants through co-digestion of sewage sludge with grease trap sludge from a meat processing plant [J]. Bioresource Technology, 2009, 100(1): 79-85.
[5] LIANG M S, XU Q. Research on high temperature compost technology in sludge processing [C]// Proceedings of the 2nd International Conference on Bioinformatics and Biomedical Engineering. Shanghai: Shanghai Jiaotong University, 2008: 4202- 4205.
[6] ROY B. Sludge processing [J]. Pollut Eng, 2005, 37: 20-23.
[7] PATTERSON D A, STEMARK L, HOGAN F. Pilot-scale supercritical water oxidation of sewage sludge [C]// Proceedings of the 6th European Biosolids and Organic Residuals Conference. Wakefield: Aqua. Environ. Consultancy Services, 2001: 11-15.
[8] ROZADA F, OTERO M, MOR?N A. Activated carbons from sewage sludge and discarded tyre: Production and optimization [J]. J Hazard Mater, 2005, 124(1/2/3): 181-191.
[9] YANG J K, ZHANG D D, HOU J, HE B P, XIAO B. Preparation of glass-ceramics from red mud in the aluminium industries [J]. Ceram Int, 2008, 34(1): 125-130.
[10] PEREZ R G A, GUITIAN R F, de AZA PENDAS S. Industrial obtaining of ceramic materials from the Bayer process red mud’s [J]. Bol Soc Esp Ceram, 1999, 38: 220-226.
[11] BOTT R, LANGELOH T, HAHN J. Re-usage of dry bauxite residue [C]// Proceedings of the 7th International Alumina Quality Workshop, Perth Australia: AQW, 2005: 236-241.
[12] PARAMGURU R K, RATH P C, MISRA V N. Trends in red mud utilization-A review [J]. Miner Process Extr M, 2005, 26(1): 1-29.
[13] HAN S X. YUE Q Y, YUE M, GAO B Y, ZHAO Y Q, CHEN W J. Effect of sludge-fly ash ceramic particles (SFCP) on synthetic wastewater treatment in an A/O combined biological aerated filter [J]. Bioresource Technology, 2009, 100(3): 1149-1155.
[14] ZHAO Y Q, YUE Q Y, LI R B, YUE M, HAN S X, GAO B Y, LI Q, YU H. Research on sludge-fly ash ceramic particles (SFCP) for synthetic and municipal wastewater treatment in biological aerated filter (BAF) [J]. Bioresource Technology, 2009, 100(21): 4955-4962.
[15] YUE Q Y, HAN S X, YUE M, GAO B Y, LI Q, YU H, ZHAO Y Q, QI Y F. The performance of biological anaerobic filters packed with sludge-fly ash ceramic particles (SFCP) and commercial ceramic particles (CCP) during the restart period: Effect of the C/N ratios and filter media [J]. Bioresource Technology, 2009, 100(21): 5016-5020.
[16] HAN S X, YUE Q Y, YUE M, GAO B Y, LI Q, YU H, ZHAO Y Q, QI Y F. The characteristics and application of sludge-fly ash ceramic particles (SFCP) as novel filter media [J]. J Hazard Mater, 2009, 171(1/2/3): 809-814.
[17] QI Y F, YUE Q Y, HAN S X, YUE M, GAO B Y, SHAO H Y T. Preparation and mechanism of ultra-lightweight ceramics produced from sewage sludge [J]. J Hazard Mater, 2010, 176(1/2/3): 76-84.
[18] MERINO I, AREVALO L F, ROMERO F. Characterization and possible uses of ashes from wastewater treatment plants [J]. Waste Manage, 2005, 25(10): 1046-1054.
[19] MERINO I, AREVALO L F, ROMERO F. Preparation and characterization of ceramic products by thermal treatment of sewage sludge ashes mixed with different additives [J]. Waste Manage, 2007, 27(12): 1829-1844.
[20] CHEESEMAN C R, VIRD G S. Properties and microstructure of lightweight aggregate produced from sintered sewage sludge ash [J]. Resour Conserv Recy, 2005, 45(1): 18-30.
[21] WANG X R, JIN Y Y, WANG Z Y, MAHAR R B, NIE Y F. A research on sintering characteristics and mechanisms of dried sewage sludge [J]. J Hazard Mater, 2008, 160(2/3): 489-494.
[22] MUN K J. Development and tests of lightweight aggregate using sewage sludge for nonstructural concrete [J]. Constr Build Mater, 2007, 21(7): 1583-1588.
[23] SGLAVO V M, MAURINA S, CONCI A, SALVIATI A, CARTURAN G, COCCO G. Bauxite ‘red mud’ in the ceramic industry: Part 2. Production of clay-based ceramics [J]. J Eur Ceram Soc, 2000, 20(3): 245-252.
[24] SGLAVO V M, MAURINA S, CONCI A, SALVIATI A, CARTURAN G, COCCO G. Bauxite ‘red mud’ in the ceramic industry: Part 1. Thermal behaviour [J]. J Eur Ceram Soc, 2000, 20(3): 235-244.
[25] SRIKANTH S, RAY A K, BANDOPADHYAY A, RAVIKUMAR B, ANIMESH J. Phase constitution during sintering of red mud and red mud-fly ash mixtures [J]. J Am Ceram Soc, 2005, 88(9): 2396-2401.
[26] PONTIKES Y, RATHOSSI C, NIKOLOPOULOS P, ANGELOPOULOS G N, JAYASEELAN D D, LEE W E. Effect of firing temperature and atmosphere on sintering of ceramics made from Bayer process bauxite residue [J]. Ceram Int, 2009, 35(1): 401-407.
[27] TSAI C C, WANG K S, CHIOU I J. Effect of SiO2-Al2O3-flux ratio change on the bloating characteristics of lightweight aggregate material produced from recycled sewage sludge [J]. J Hazard Mater, 2006, 134(1/2/3): 87-93.
[28] DUCMAN V, MIRTIC B. The applicability of different waste materials for the production of lightweight aggregates [J]. Waste Manage, 2009, 29(8): 2361-2368.
(Edited by HE Yun-bin)
Foundation item: Project(2010013111005) supported by the Ph.D Programs Foundation of Ministry of Education of China
Received date: 2011-02-27; Accepted date: 2011-09-27
Corresponding author: YUE Qin-yan, Professor; Tel: +86-531-88365258; E-mail: qyyue@sdu.edu.cn