文章编号:1004-0609(2015)-05-1285-09
Co2+含量对镀Ti金刚石-Ni-Co复合电沉积的影响
张 鹂,王日初,彭超群,张 纯,谭时雨,王乃光
(中南大学 材料科学与工程学院,长沙 410083)
摘 要:采用电镀法制备镀Ti金刚石-Ni-Co复合镀层,研究镀液中Co2+含量对镀层形貌和性能的影响,并通过电化学阻抗谱研究Ni-Co复合电沉积过程。结果表明:当镀液中未添加Co2+时,所制备的镀Ti金刚石-Ni复合镀层内凹痕较多;镀液中添加Co2+后,镀Ti金刚石-Ni-Co复合镀层内凹痕消失,晶粒均匀。随着镀液中Co2+含量的增加,所制备的镀Ti金刚石复合镀层的显微硬度先增加后减少。当镀液中Co2+含量为6%(摩尔分数)时,在-0.85 V电位下Ni-Co共结晶电化学阻抗谱的电荷转移电阻最大,制备的镀Ti金刚石-Ni-Co镀层内金刚石含量最高。此外,当镀液中Co2+含量增加至8%时,镀Ti金刚石-Ni-Co复合镀层内金刚石粉体的沉积量最少。
关键词:Ni-Co合金;金刚石;镀钛;复合电沉积;交流阻抗
中图分类号:TG153 文献标志码:A
Effects of Co2+ content on Ti-coated diamond-Ni-Co composite electrodeposition
ZHANG Li, WANG Ri-chu, PENG Chao-qun, ZHANG Chun, TAN Shi-yu, WANG Nai-guang
(School of Materials Science and Engineering, Central South University, Changsha 410083, China)
Abstract: The Ti-coated-diamond-Ni-Co coating was prepared by electroplating process. Moreover, the effect of Co2+ content variation on the morphology and property of the Ti-coated diamond-Ni-Co coating was investigated. Meanwhile, the composite electrodeposition process was studied by electrochemical impedance spectroscopy (EIS). The results show that there are many dents on the Ti-coated diamond-Ni coating when Co2+ is not added in the plating bath. However, the dents disappear and the grain size becomes more uniform when Co2+ is added into the plating bath. Moreover, with the increase of Co2+ content in the plating bath, the microhardness of the composite coatings rises firstly and then declines. As Co2+ content in the plating bath is 6% (mole fraction), the charge transfer resistance of the Ni-Co codeposition evaluated from the EIS at -0.85 V reaches the maximum value, and the content of diamond in the composite coating is the highest. In addition, as Co2+ content in the plating bath increases to 8%, the content of diamond in the composite coatings is the least.
Key words: Ni-Co alloy; diamond; Ti plating; composite electrodeposition; alternating current impedance
复合电沉积是吸附阳离子的固体颗粒与金属离子同时沉积于基体表面的过程。BAKHIT等[1]的根据固体颗粒的沉积状态建立复合电沉积模型,该模型认为在复合电沉积过程中固体颗粒需经过吸附离子、迁移、扩散、阴极吸附、部分包覆和完全包覆等步骤。复合电沉积过程一般不需在高温、高压条件下进行,具有操作方便、经济实惠等优点。采用复合电沉积方法制备的金属基复合镀层一般具有良好的耐蚀性、耐磨性和热稳定性,同时具有独特的力学性能,能满足人们的不同需求。
复合电沉积过程中常用的金属基体有Fe、Zn、Ni、Ag、Cu及其合金等[2-9]。其中,Ni-Co合金具有粘附能力强、应力低、硬度高、耐磨耐蚀性好、催化活性强等特点,主要用在手机生产中[10]。常用的固体颗粒有氧化物(Al2O3[11-12]、TiO2[13]和SiO2[14]等)、碳化物(SiC[1]和WC[15]等)、金刚石[16]、石墨[17]等。其中,金刚石是自然界中硬度最大的物质,具有良好的切削性能。目前,金刚石-Ni复合电沉积已广泛应用于金刚石线锯的生产过程中[18-19]。由于金刚石与金属基体间浸润性差,在金刚石线锯的使用过程中,极易出现金刚石剥落的现象,从而影响金刚石线锯的切割效率和使用寿命。由于Ni-Co合金镀层的硬度、耐磨性等性能优于纯Ni镀层,因此,本文作者选用镀Ti金刚石作为共沉积固体颗粒,Ni-Co合金作为共沉积金属基体,通过测量镀液pH值的变化研究不同Co2+含量镀液中金刚石的吸附特性,结合交流阻抗谱测试研究镀液中Co2+含量对镀Ti金刚石-Ni-Co复合镀层电结晶形核-生长的影响。采用扫描电镜(SEM)和能谱仪(EDS)、显微硬度测试计等研究镀液中Co2+含量对镀Ti金刚石-Ni-Co复合镀层显微组织和性能的影响。
1 实验
1.1 金刚石-Ni复合镀层的制备
表1所列为镀液的主要成分及其质量浓度,该质量浓度根据各成分摩尔浓度换算所得。其中,镀液中Co2+含量是指镀液中Co2+占总金属离子的摩尔分数,即x(Co2+)。调节Co2+含量分别为0、2%、4%、6%和8%(摩尔分数)。实验中采用的镀Ti金刚石粉体平均粒径均为40 μm。利用稀H2SO4将各组镀液的pH值调节至3.5左右。
各组镀液经机械搅拌24 h,并用数显酸度计测试其搅拌前后的pH值。实验基体工作面为直径10 mm的不锈钢,将基体工作面在400、600和800号砂纸下打磨光亮。经10%NaOH(质量分数)超声波除油3 min,用去离子水漂至中性。然后,经5% H2SO4(质量分数)超声波除锈30 s,再用去离子水漂至中性,用冷风吹干备用。以500 mL烧杯为电镀槽,内置搅拌磁子后置于CJJ-6六联磁力搅拌机上,保持搅拌速度恒定。不锈钢阴极呈45°角向下,阳极为4 cm2镍板,与阴极正对,阳极与阴极间距离保持为1.5 cm。电流密度为1.5 A/dm2,保持镀液温度为(48±2) ℃,接通直流稳压电源后施镀15 min。此后将镀层超声波清洗3 min,用冷风吹干。
表1 镀液的成分及质量浓度
Table 1 Chemical compositions and mass concentrations of plating bath

1.2 镀Ti金刚石-Ni-Co复合共沉积的电化学测试
采用CHI660D电化学工作站结合三电极体系测试不锈钢在不同镀液中的阴极循环伏安曲线和电化学阻抗谱,其中工作电极为不锈钢(直径为10 mm),参比电极为232型饱和甘汞电极(SCE),辅助电极为铂电极(面积为4 cm2),测量时采用水浴锅保持镀液温度为(48±2) ℃。交流阻抗谱测试扰动电压振幅为5 mV,频率范围为10 mHz~100 kHz,电位分别为-0.45和-0.85 V。
1.3 镀Ti金刚石-Ni-Co复合镀层的形貌及性能
采用Quanta-200环境扫描电镜(SEM)观察镀液中Co2+含量变化时,镀Ti金刚石-Ni-Co复合镀层的基质形貌和镀Ti金刚石的上砂效果,并通过能谱分析(EDS)测量复合镀层中Ni、Co元素的含量。采用HVS-1000自动显微硬度计测试各镀Ti金刚石-Ni-Co复合镀层的显微硬度,载荷为2.94 N,各镀层均进行6次测试,去除最大值和最小值后,取平均值为测试结果。
2 结果与讨论
2.1 Co2+含量对镀Ti金刚石吸附特性的影响
图1所示为各组镀液搅拌后pH值的变化情况(镀液搅拌后pH值与搅拌前pH值之差,即ΔpH)。当镀液中未添加Co元素时,即镀液的Co2+含量为0时,经搅拌24 h镀液的pH值增加0.31。这表明随着镀液酸性的降低,镀液中游离的H+含量减少。减少的H+吸附于镀Ti金刚石表面,使镀Ti金刚石带正电。同时,这也表明金刚石表面镀覆Ti后仍保持良好的H+吸附特性。此外,金刚石在吸附H+的同时也会吸附Ni2+[20]。
在镀液中添加Co元素后,镀液中ΔpH随着Co2+含量的增加呈先减小后增加的趋势。当镀液中的Co2+含量为2%时,搅拌后镀液的pH值仅增加0.05,这表明镀Ti金刚石对H+的吸附量减少,而对Ni2+和Co2+的吸附量增加,镀Ti金刚石表面带电量增加。当镀液中的Co2+含量为4%时,搅拌后镀液的pH值减小0.03。这表明镀Ti金刚石表面吸附的Ni2+和Co2+的数量进一步增多,而吸附的H+数量进一步减少。同时,由于Ni2+和Co2+可水解为NiOH+和CoOH+,促进镀液中水解产生的H+含量增加,使镀液pH值减少[21-22]。当镀液的Co2+含量为6%时,镀液的pH值也减小0.03,此时镀Ti金刚石对Ni2+、Co2+和H+的吸附达到饱和状态。当镀液中的Co2+含量为8%时,镀液经搅拌后pH值增加0.01。镀Ti金刚石吸附少量H+后,镀液pH值略微增加,同时,由于镀液中Co2+含量的增加,吸附少量正电荷的镀Ti金刚石与Co2+间静电斥力增大,阻碍镀Ti金刚石对Co2+的吸附。此时,镀Ti金刚石表面吸附的阳离子含量小于其他各实验组的。周海飞等[23]研究发现金刚石的吸附和脱附是同时存在的可逆过程。在电镀过程中,当溶液温度逐渐升高时,该可逆过程向脱附方向进行,使金刚石粉体表面的正电荷吸附量降低,从而降低金刚石粉体的沉积量。
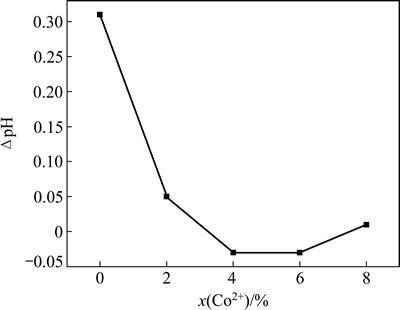
图1 镀液中Co2+含量和ΔpH的关系
Fig. 1 Relationship between Co2+ content and ΔpH in plating bath
2.2 Co2+含量对镀Ti金刚石-Ni-Co电结晶的影响
为研究镀液中Co2+含量对镀Ti金刚石-Ni-Co电沉积过程的影响,在-0.45 和-0.85 V电位下进行电化学阻抗谱测试。在-0.45 V电位下,未达到Ni-Co的共沉积电位,阻抗谱测试后阴极表面不出现镀层;而-0.85 V时,已达到沉积电位,阴极表面出现明显镀层。
图2所示为在-0.45 V电位下不同Co2+含量复合镀液中 Ni-Co电结晶的电化学阻抗谱。由图2可见,镀液中Co2+含量为0、2%、4%、8%时,Ni-Co共结晶的电化学阻抗谱表现为双容抗弧的组合,表明该结晶过程有两个时间常数。高频区容抗弧是由电极-溶液界面间双电层电容和Ni-Co共沉积的电荷转移电阻引起的。此时,Ni和Co的阻抗谱重合,仅表现为一个时间常数。一般来说,电位为-0.1 V时已有明显的析氢反应发生,在-0.45 V电位下低频区容抗弧与氢气的析出和在双电层内的吸附有关[6]。
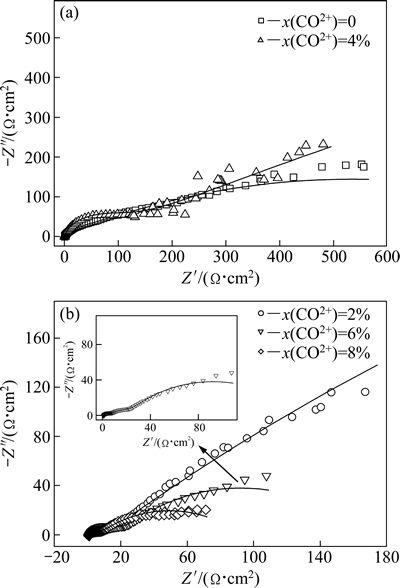
图2 在-0.45 V电位下不同Co2+含量镀液的电化学阻抗谱
Fig. 2 Electrochemical impedance spectroscopies of plating bathes with different Co2+ contents at -0.45 V
当镀液中Co2+含量为6%时,在-0.45 V电位下Ni-Co共结晶的电化学阻抗谱表现为三容抗弧的组合。该阻抗谱内低频区容抗弧同样与氢气析出和在双电层内的吸附有关。而高频区和中频区容抗弧的存在说明Ni、Co的沉积过程不同时发生,存在两个时间常数。由于Co的电化学活性略高于Ni的电化学活 性[24],高频区容抗弧与Co的电结晶过程中电荷转移有关,中频区容抗弧则由Ni-Co共结晶过程的电荷转移所引起。而QIAO等[25]认为,Ni-Co共沉积时Co的沉积过程由扩散控制,而Ni的沉积过程主要由电极反应程度控制。Co扩散先于Ni的电极反应发生也可能是高频和中频区出现两个容抗弧的原因。高频区容抗弧(镀液中Co2+含量为0、2%、4%、8%)或中频区容抗弧(镀液中Co2+含量为6%)直径大小可表征Ni-Co共结晶过程中电荷转移电阻的大小。电荷转移电阻越大,Ni-Co共结晶阻力越大。
图3所示为在-0.85 V电位下不同Co2+含量的镀液中Ni-Co电结晶的电化学阻抗谱。由图3可见,在Co2+含量不同的镀液中,在-0.85 V电位下Ni-Co电结晶阻抗谱均为高频区容抗弧与低频区感抗弧的组合。高频区容抗弧与双电层电容和Ni-Co共沉积时电荷转移电阻有关。Ni-Co共沉积过程有两类反应:第一类是Ni2+和Co2+均吸附两个电子,直接还原为Ni-Co合金,这部分反应在沉积过程中起主导作用;另一类是部分Ni2+和Co2+仅吸附一个电子,还原为NiOH+和CoOH+。低频区感抗弧则与氢的化合物(NiH+和CoH+)和氢的中间产物(NiOH+和CoOH+)等在阴极表面的吸附有关[21]。当镀液中Co2+含量为6%时,容抗弧半径最大。这表明Ni-Co电荷转移电阻越大,共结晶阻力越大,从而抑制晶粒的形核与生长。感抗弧直径越大,表明阴极表面的吸附越强烈,从而抑制Ni-Co合金的晶粒生长[26]。
当电位由-0.45 V降低到-0.85 V,不同Co2+含量的镀液中Ni-Co共沉积的电荷转移电阻均减小,这表明阴极表面离子的扩散加强,这可以促进活性生长的迁移、加速晶粒生长。当电位越负时,形核率越高,晶粒缺陷越少,同时,晶粒生长速率越大,晶粒尺寸越大[26]。
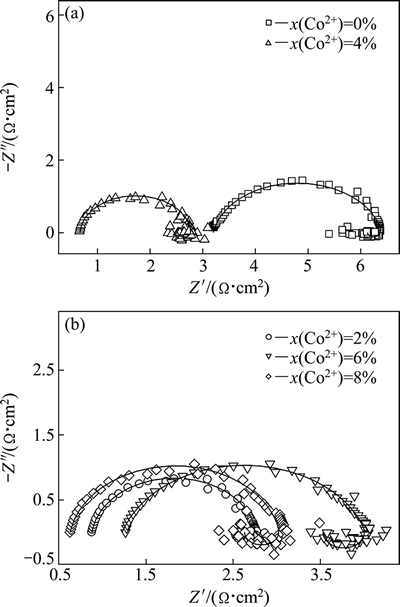
图3 在-0.85 V电位下不同Co2+含量镀液的电化学阻抗谱
Fig. 3 Electrochemical impedance spectroscopies of plating bathes with different Co2+ contents at -0.85 V
利用Zview软件对各组电化学阻抗谱进行电路拟合,其拟合电路图分为3类,如图4所示。图4(a)所示为双容抗弧拟合电路,图4(b)所示为容抗弧与感抗弧组合的拟合电路,图4(c)所示为三容抗弧拟合电路。在图4中,Rs为溶液电阻;Qdl、Qdl1、Qdl2分别为不同状态的常相位无件CPEdl、CPEdl1、CPEdl2的双电层电容;RCo为Co在电结晶过程中的电荷转移电阻;RNi-Co为Ni-Co共结晶过程的电荷转移电阻;QH和RH分别为与氢气析出与吸附相关的CPEH常相位元素的双电层电容和电荷转移电阻。
2.3 Co2+含量对复合镀层形貌和金刚石上砂效果的影响
图5所示为当电流密度为1.5 A/dm2、电镀温度为(48±2) ℃、电镀时间为15 min时镀液中Co2+含量变化对复合镀层中Ni-Co镀层形貌的影响。图5(a)~(e)分别为镀液中Co2+含量为0~8%时制备的镀Ti金刚 石-Ni-Co复合镀层中金属镀层的表面形貌。镀液中未添加Co元素时,镀Ti金刚石-Ni复合镀层呈现金属光泽, 晶粒较大且不均匀,表面存在凹痕(见图5(a))。添加Co元素后,镀Ti金刚石-Ni-Co复合镀层金属光泽变暗,晶粒明显细化且大小均匀,镀层表面无明显凹痕,较为平整(见图5(b)~(e))。因此,Co元素的添加可有效改善复合镀层显微结构,减少缺陷的产生。镀Ti金刚石-Ni-Co复合镀层与镀Ti金刚石-Ni复合镀层均呈圆形,这说明当镀液中Co2+含量为2%~8%时制备的复合镀层与未添加Co元素时复合镀层显微组织一致。随着镀液中Co2+含量的增加,镀Ti金刚石-Ni-Co复合镀层的晶粒逐渐长大。Ni为面心立方(FCC)晶体结构,此时,Co与Ni可完全固溶,这些Ni-Co合金镀层均为FCC晶体。当沉积-生长率或晶体结构不同时,镀层表面形貌不同,为针尖状或圆形。CORREIA等[27]认为镀液中Ni2+含量增加时复合镀层由Co富集相向Ni富集相转变,Ni-Co复合镀层形貌将从针尖状变为圆形。QIAO等[25]认为当镀液中CoSO4·7H2O质量浓度小于25 g/L时,Ni-Co复合镀层为FCC晶体。尽管电沉积条件不同以及镀Ti金刚石的存在,当镀液中CoSO4·7H2O质量浓度为25.374 g/L时,Ni-Co合金复合镀层也表现为FCC结构。Ni-Co合金共沉积是异常共沉积,镀层中Co含量远高于镀液中Co含量。
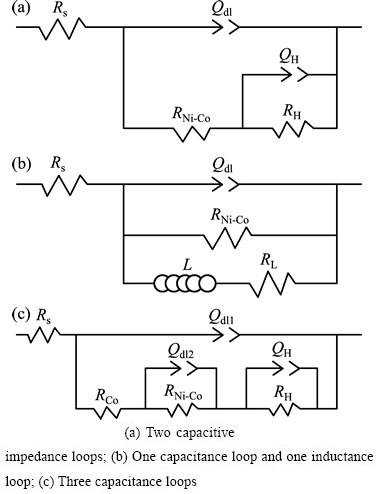
图4 等效电路图
Fig. 4 Corresponding equivalent circuits
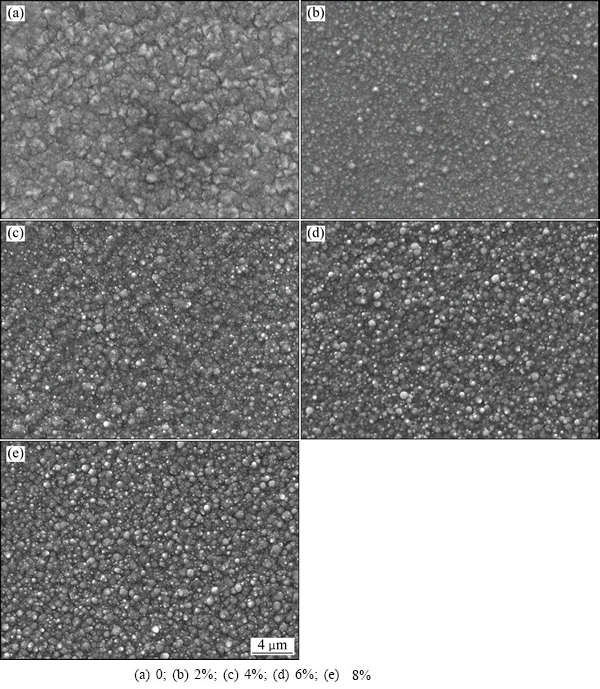
图5 不同Co2+含量镀液中制备的镀Ti金刚石-Ni-Co复合镀层的SEM像
Fig. 5 SEM images of Ti-coated diamond-Ni-Co composite coatings prepared in plating bathes with different Co2+ contents
图6所示为当电流密度为1.5 A/dm2、电镀温度为(48±2) ℃、电镀时间为15 min时所制备的镀Ti金刚石-Ni-Co复合镀层中Co含量随镀液中Co2+含量增加的变化情况。MAKSIMOVI
等[28]认为Ni-Co共沉积时,Ni先沉积在阴极表面。Co2+会吸附于Ni表面,这部分Co2+一方面会在Ni表面沉积,另一方面会阻碍Ni2+的还原。镀液中Co2+含量对镀Ti金刚石的上砂效果也存在影响。
图7所示为当电流密度为1.5 A/dm2、电镀温度为(48±2) ℃、电镀时间为15 min时镀液中Co2+含量对镀Ti金刚石-Ni-Co复合镀层中金刚石上砂效果的影响。在本实验中,不锈钢工作基体表面呈45°朝下,镀Ti金刚石的沉积需克服重力作用,并在流体动力学和电泳力作用下运动至阴极表面而发生沉积。当搅拌速度不变时,镀Ti金刚石的带电量越多,电泳力作用越大,沉积量越多[1]。未添加Co元素前,镀Ti金刚石的上砂效果较好。此外,由于金刚石表面镀覆金属Ti,金刚石表面可导电,Ni2+可在镀Ti金刚石表面被还原,将金刚石包覆于镀层内,但仍存在部分未被完全包覆的镀Ti金刚石颗粒。镀液中添加Co元素后,复合镀层中的镀Ti金刚石颗粒基本完全包覆于镀层内,这也表明镀液中Co元素的存在可以促进Ni-Co固溶体的形核与生长。随着镀液中Co2+含量由0增至6%时,镀Ti金刚石的上砂效果略微改善,但当镀液中Co2+含量为8%时,镀Ti金刚石的上砂量明显减少,甚至远少于未添加Co元素的复合镀层内镀Ti金刚石的数量。这表明镀液中Co2+含量为8%时,Co元素对镀Ti金刚石的沉积起抑制作用。这是由于随着镀液中Co2+含量的增加,阴极表面聚集的Co2+数量增加,在静电斥力的作用下,镀Ti金刚石需克服更大的阻力迁移至阴极表面。LARI等[10]研究Ni-Co-SiC的共沉积行为时发现:当SiC表面吸附的Co2+数量越多,SiC的沉积率越高。这是因为当SiC表面的带电量越大时,SiC与阴极间的静电引力越大,对SiC的沉积率提高起促进作用。根据上述研究可知,镀液中Co2+含量为8%时,镀Ti金刚石表面吸附的离子数量减少,即带电量降低,电场对其作用效果减弱,这也就导致镀Ti金刚石的上砂效果变差。
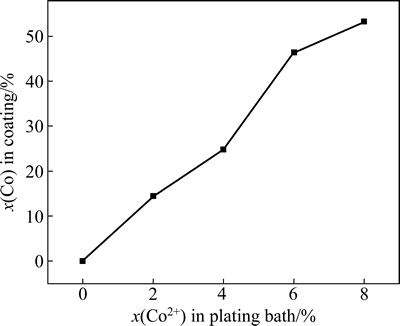
图6 镀液中Co2+含量和镀层中Co含量的关系
Fig. 6 Relationship between x(Co2+) in plating bath and x(Co) in coating
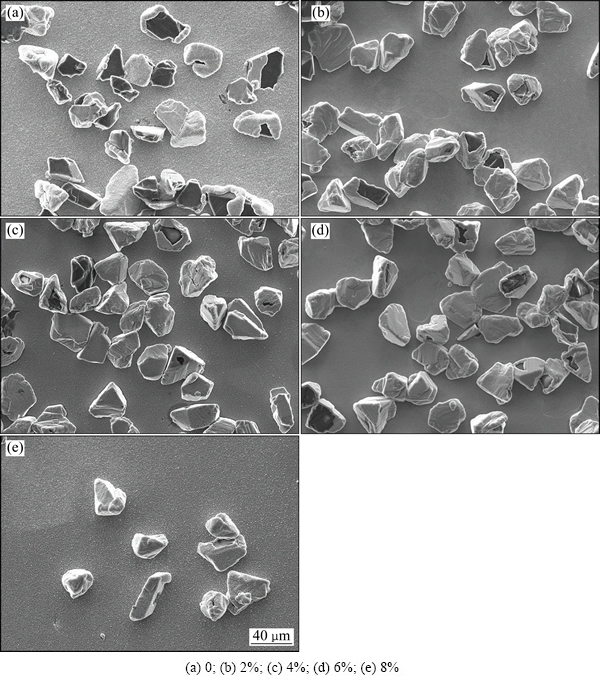
图7 不同Co2+含量镀液所制备的镀Ti金刚石-Ni-Co复合镀层中镀Ti金刚石SEM像
Fig. 7 SEM images of Ti-coated diamond in Ti-coated diamond-Ni-Co composite coatings prepared in plating bathes with different Co2+ contents:6%
2.4 Co2+含量对镀层显微硬度的影响
图8所示为当电流密度为1.5 A/dm2、电镀温度为(48±2) ℃、电镀时间为15 min时镀液中Co2+含量变化对镀Ti金刚石-Ni-Co复合镀层中Ni-Co金属基显微硬度的影响。由图8可看出,未添加Co元素时,镀Ti金刚石-Ni复合镀层中Ni基体的显微硬度为268.5 HV。添加Co元素后,镀Ti金刚石-Ni复合镀层中Ni-Co基体的显微硬度随着Co2+含量的增加呈先增大后减小的趋势。当镀液中Co2+含量为2%时,Ni-Co基体显微硬度为197.25 HV,是各实验组中显微硬度最小的。PELLICER等[29]认为当Ni-Co复合镀层中Ni和Co的质量比为1:1时,Ni-Co镀层的硬度最大。由于电镀条件的不同以及镀Ti金刚石的存在,当镀液中Co2+含量为6%时,Ni-Co复合镀层内Ni和Co质量比为1.147:1,显微硬度为316 HV,是本实验中最大的。根据上述金刚石上砂量对比可知,此时镀Ti金刚石的上砂效果也最佳。
ZKAN等[30]研究了SiC颗粒对Ni镀层显微硬度的影响,研究发现镀层中SiC颗粒越多,其显微硬度越大,同时Ni基体可以择优生长使其硬度提高。随着镀液内Co2+含量由0增至8%时,镀Ti金刚石-Ni-Co复合镀层的显微硬度呈先减小后增加再减小的变化规律,这与BAKHIT等[1]的研究结果基本一致。在固溶强化的作用下,复合镀层显微硬度随着Co元素固溶度的增加而增加,当镀液中CoSO4·7H2O质量浓度为50 g/L时,复合镀层的显微硬度最大。
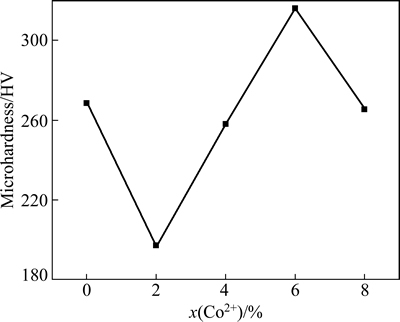
图8 镀液中Co2+含量与镀层显微硬度的关系
Fig. 8 Relationship between Co2+ contents in plating bath and microhardness
3 结论
1) 当镀液Co2+含量由0增至6%时,镀Ti金刚石对H+的吸附量减少,而对Co2+、Ni2+的吸附量增加。当镀液中Co2+含量为6%时,镀Ti金刚石对H+、Co2+和Ni2+的吸附达到饱和;当镀液中Co2+含量为8%时,将抑制镀Ti金刚石对H+、Co2+和Ni2+离子的吸附。
2) 复合镀液的电化学阻抗谱测试中,在-0.45 V电位下,Co2+含量为0、2%、4%和8%时,电化学阻抗谱为双容抗弧的组合,Ni和Co电荷转移过程基本同时发生;Co2+含量为6%时,电化学阻抗谱为三容抗弧的组合,Co先于Ni发生电荷转移。在-0.85 V电位下,当Co2+含量为0~8%时,电化学阻抗谱均为容抗弧和感抗弧的组合;当Co2+含量为6%时,Ni-Co共沉积的电荷转移电阻最大。
3) 镀液中未添加Co元素时,镀Ti金刚石-Ni复合镀层存在凹痕,晶粒尺寸不均匀,镀Ti金刚石未被完全包覆于镀层内。添加Co元素后,镀Ti金刚石-Ni-Co表面无明显缺陷,晶粒尺寸均匀,镀Ti金刚石基本包覆于镀层内。随着镀液中Co含量的增加,所制备的复合镀层内Ni-Co晶粒尺寸增加。当镀液中Co2+含量为0~6%时,促进镀Ti金刚石的沉积;当Co2+含量为8%时,镀Ti金刚石的沉积过程被抑制。
4) 当镀液中Co2+含量为0~8%时,镀Ti金刚石-Ni-Co镀层内Co含量呈非线性增加,镀层显微硬度先减小后增加再减小;当镀液中Co2+含量为6%时,制备的镀Ti金刚石-Ni-Co复合镀层的显微硬度最大。
REFERENCES
[1] BAKHIT B, AKBARI A. Synthesis and characterization of Ni-Co/SiC nanocomposite coatings using sediment co-deposition technique[J]. Journal of Alloys and Compounds, 2013, 560: 92-104.
[2] GIRIDHAR P, WEIDENFELLER B, ABEDIN S Z, ENDRES F. Electrodeposition of iron and iron-aluminium alloys in an ionic liquid and their magnetic properties[J]. Physical Chemistry Chemical Physics, 2014, 16(20): 9317-9326.
[3] LIU Z, BORISENKO N, ABEDIN S Z, ENDRES F. In situ STM study of zinc electrodeposition on Au (111) from the ionic liquid 1-ethyl-3-methylimidazolium trifluoromethylsulfonate[J]. Journal of Solid State Electrochemistry, 2014, 18(9): 2581-2587.
[4] EUG
NIO S, SILVA T, CARMEZIM M, DUARTE R, MONTEMOR M. Electrodeposition and characterization of nickel-copper metallic foams for application as electrodes for supercapacitors[J]. Journal of Applied Electrochemistry, 2014, 44(4): 455-465.
[5] DHANAPAL K, REVATHY T, RAJ M A, NARAYANAN V, STEPHEN A. Magnetic anisotropy studies on pulsed electrodeposited Ni/Ag/Ni trilayer[J]. Applied Surface Science, 2014, 313: 698-703.
[6] HERRAIZ-CARDONA I, ORTEGA E, PREZ-HERRANZ V. Impedance study of hydrogen evolution on Ni/Zn and Ni-Co/Zn stainless steel based electrodeposits[J]. Electrochimica Acta, 2011, 56(3): 1308-1315.
[7] 黄小兵, 陈红辉, 周诗彪, 杨基峰, 张海涛. 电镀 Fe-Ni 合金工艺的研究[J]. 电镀与环保, 2014, 34(4): 32-34.
HUANG Xiao-bing, CHEN Hong-hui, ZHOU Shi-biao, YANG Ji-feng, ZHANG Hai-tao. A study of Fe-Ni alloy plating technology[J]. Electroplating and Pollution Control, 2014, 34(4): 32-34.
[8] 李远会, 万明攀, 陈 阵, 张晓燕, 郭忠诚. 电镀 Cu-W-Ni 合金的热力学分析[J]. 表面技术, 2013, 42(5): 8-10.
LI Yuan-hui, WANG Ming-pan, CHEN Zhen, ZHANG Xiao-yan, GUO Zhong-cheng. Thermodynamics analysis of electrodeposited Cu-W-Ni alloys[J]. Surface Technology, 2013, 42(5): 8-10.
[9] 杨海涛, 陈步明, 郭忠诚, 黄 惠, 张永春, 徐瑞东. Pb-Ag-Sb-Ca合金在锌电沉积过程中阳极性能的研究[J]. 电镀与精饰, 2014, 36(2): 33-35.
YANG Hai-tao, CHEN Bu-ming, GUO Zhong-cheng, HUANG Hui, ZHANG Yong-chun, XU Rui-dong. Quasi-stationary polarization investigations of Pb-Ag-Sb-Ca quaternary alloy anode during zinc electrowinning[J]. Plating and Finishing, 2014, 36(2): 33-35.
[10] LARI B S, HEYDARZADEH S M, AMADEH A. A functionally gradient nano-Ni-Co/SiC composite coating on aluminum and its tribological properties[J]. Surface and Coatings Technology, 2012, 206(19): 4032-4039.
[11] JEGAN A, VENKATESAN R. Characterization and optimization of pulse electrodeposition of Ni/nano-Al2O3 composite coatings[J]. International Journal of Minerals, Metallurgy, and Materials, 2013, 20(5): 479-485.
[12] 周言敏, 李建芳. 镁合金电镀 Ni-Al2O3薄膜的研究[J]. 电镀与环保, 2014, 34(1): 10-12.
ZHOU Yan-min, LI Jian-fang. A study of electrodepositing Ni-Al2O3 film on magnesium alloy[J]. Electroplating and Pollution Control, 2014, 34(1): 10-12.
[13] ARUNA S, MUNIPRAKASH M ,GRIPS V W. Effect of titania particles preparation on the properties of Ni-TiO2 electrodeposited composite coatings[J]. Journal of Applied Electrochemistry, 2013, 43(8): 805-815.
[14] ZAMBLAU I, VARVARA S, MURESAN L M. Corrosion behavior of Cu-SiO2 nanocomposite coatings obtained by electrodeposition in the presence of cetyl trimethyl ammonium bromide[J]. Journal of Materials Science, 2011, 46(20): 6484-6490.
[15] MOHAJERI S, DOLATI A, REZAGHOLIBEIKI S. Electrodeposition of Ni/WC nano composite in sulfate solution[J]. Materials Chemistry and Physics, 2011, 129(3): 746-750.
[16] WANG H T, SHEU H H, GER M D, HOU K H. The effect of heat treatment on the microstructure and mechanical properties of electrodeposited nanocrystalline Ni-W/diamond composite coatings[J]. Surface and Coatings Technology, 2014, 259: 268-273.
[17] HE X Z, ZHANG X W, ZHOU X L, FU Z H. Study on electrodeposition of ni-graphite composite coatings in sulfamate bath[J]. Advanced Materials Research, 2011, 150: 1546-1550.
[18] WANG H, NI Z, YAO L, QIAN Q, MING X. Research progress in composite electroplating fixed technology for preparing diamond wire saw[J]. Materials Review, 2013, 27(4): 115-120.
[19] 高 伟, 张景涛, 吴 平, 高荣奇, 马伯江. 金刚石线锯悬浮上砂法制作工艺的研究[J]. 金刚石与磨料磨具工程, 2013, 33(193): 1-5.
GAO Wei, ZHANG Jing-tao, WU Ping, GAO Rong-qi, MA Bo-jiang. Manufacturing process of diamond wire saw by the sand-suspension-electroplated method[J]. Diamond and Abrasives Engineering, 2013, 33(193): 1-5.
[20] 王美娟, 王日初, 彭超群, 冯 艳, 张 纯. 金刚石粉体对 Ni 电结晶初期行为的影响[J]. 中国有色金属学报, 2013, 23(3): 765-772.
WANG Mei-juan, WANG Ri-chu, PENG Chao-qun, FENG Yan, ZHANG Chun. Effect of diamond powder on Ni electrocrystallization behavior at initial stages[J]. The Chinese Journal of Nonferrous Metals, 2013, 23(3): 765-772.
[21] VAZQUEZ-ARENAS J, PRITZKER M. Steady-state model for anomalous Co-Ni electrodeposition in sulfate solutions[J]. Electrochimica Acta, 2012, 66: 139-150.
[22] TURY B, LAKATOS-VARS N M, ROY S. Ni-Co alloys plated by pulse currents[J]. Surface and Coatings Technology, 2006, 200 (24): 6713-6717.
[23] 周海飞, 祝郦伟, 钱洲亥, 杜 楠, 田刚强. 温度对 Ni-金刚石复合电沉积电化学行为的影响[J]. 中国有色金属学报, 2013, 23(8): 2229-2234.
ZHOU Hai-fei, ZHU Li-wei, QIAN Zhou-hai, DU Nan, TIAN Gang-qiang. Effect of temperature on electrochemical behaviors during Ni diamond compositeelectrodeposition[J]. The Chinese Journal of Nonferrous Metals, 2013, 23(8): 2229-2234.
[24] BAKHIT B, AKBARI A, NASIRPOURI F, HOSSEINI M G. Corrosion resistance of Ni-Co alloy and Ni-Co/SiC nanocomposite coatings electrodeposited by sediment codeposition technique[J]. Applied Surface Science, 2014, 307: 351-359.
[25] QIAO G, JING T, WANG N, GAO Y, ZHAO X, ZHOU J, WANG W. High-speed jet electrodeposition and microstructure of nanocrystalline Ni-Co alloys[J]. Electrochimica Acta, 2005, 51(1): 85-92.
[26] HASSANI S, RAEISSI K, GOLOZAR M. Effects of saccharin on the electrodeposition of Ni-Co nanocrystalline coatings[J]. Journal of Applied Electrochemistry, 2008, 38(5): 689-694.
[27] CORREIA A, MACHADO S. Electrodeposition and characterisation of thin layers of Ni-Co alloys obtained from dilute chloride baths[J]. Electrochimica Acta, 2000, 45(11): 1733-1740.
[28]
. Morphology and composition of Ni-Co electrodeposited powders[J]. Materials Characterization, 2011, 62(12): 1173-1179.
[29] PELLICER E, PAN S, SIVARAMAN K, ERGENEMAN O, SURI A S, BAR M, NELSON B, SORT J. Effects of the anion in glycine-containing electrolytes on the mechanical properties of electrodeposited Co-Ni films[J]. Materials Chemistry and Physics, 2011, 130(3): 1380-1386.
[30]
, KAZMANLI K. Electrodeposited Ni/SiC nanocomposite coatings and evaluation of wear and corrosion properties[J]. Surface and Coatings Technology, 2013, 232: 734-741.
(编辑 王 超)
基金项目:国家军品配套项目(JPPT-125-GH-039)
收稿日期:2014-10-15;修订日期:2015-03-06
通信作者:王日初,教授,博士;电话:0731-88836638;E-mail:wrc910103@163.com