离心式空压机内固粒对叶轮磨损的数值模拟
李剑峰,龚宝龙,贾秀杰,王光存,李方义
(山东大学 机械工程学院 高效洁净机械制造教育部重点实验室,山东 济南,250061)
摘要:通过对气固两相流场中固相颗粒运动轨迹的拉格朗日追踪,应用雷诺时均N-S方程、标准两方程模型(气相)、离散相流动模型(固相)和塑性材料冲蚀磨损模型,利用正交模拟试验手段和数值模拟方法,研究离心式空气压缩机全流道内气固两相湍流场的固相颗粒对叶轮叶片压力面的冲蚀磨损分布情况及磨损规律。研究结果表明:在离散相颗粒的3个几何参数中,固粒直径的改变对叶片磨损的影响最大,质量流量次之,固粒初速度的影响最小;叶轮中的冲蚀磨损最严重的部位是叶片压力面;固粒对叶片压力面的冲蚀磨损部位主要集中在叶片后缘根部,叶片中部也有一定程度的磨损。数值模拟的结果可解释相关的实际失效情况,研究成果可应用于抗冲蚀磨损叶轮的设计与修复。
关键词:离心式空压机;冲蚀磨损规律;正交试验;气固两相流;叶轮叶片
中图分类号:TH452 文献标志码:A 文章编号:1672-7207(2013)10-4047-08
Numerical simulation of solid particle erosion in centrifugal air compressor impeller
LI Jianfeng, GONG Baolong, JIA Xiujie, WANG Guangcun, LI Fangyi
(School of Mechanical Engineering & Key Laboratory of High Efficiency and Clean Mechanical Manufacture,
Ministry of Education, Shandong University, Jinan 250061, China)
Abstract: Based on Lagrangian tracking of solid particles’ motion trajectories in a gas-solid flow, and by applying Reynolds time-averaged control equations, standard two-equation turbulent model, discrete phase model and ductile materials erosion model, numerical simulation was adopted to study the distribution of erosion wear on blade pressure surface and the erosion rules in the centrifugal air compressor through orthogonal test. According to the simulation results, in the geometric parameters of discrete particles, particle diameter has most influenced on erosion wear of blade, and the particle mass flow ranks the second place and the particle initial speeds impact is minimal. The most serious erosion wear part in impeller is blade pressure surface. The erosion wear position on blade pressure surface caused by particles impacting primarily locates on blade trailing edge roots, and blade middle part also has a certain degree of wear and tear. The results of numerical simulation can explain some actual impeller failure cases and can be applied to anti-erosion wear impeller design and repair.
Key words: centrifugal air compressor; erosion wear rule; orthogonal test; gas-solid flow; impeller blade
离心式空压机是石油化工产业中的核心设备,常使用在重工业地区,导致环境污染严重,空气质量差。旋转叶轮工作在高速高温高压环境下,并且压缩介质中含有微小固粒及腐蚀物质,故叶轮失效的频率较高[1],其中叶片是最容易失效的零件[2-4]。固粒的冲蚀磨损是叶片失效的重要原因之一。因此,研究叶轮机械内气固两相流流场中固粒与叶轮表面的相互撞击磨损规律,对研究材料的磨损机理及指导零部件的再制造有重要意义。目前,在流体机械领域,对固液两相的磨损和离心泵的失效研究比较深入,Ariely等[5]对冷却水系统离心泵叶轮的磨损进行观察,发现叶片表面有树突状的凹痕,是典型的磨损-腐蚀失效机制,有缺陷的叶片改变了液态流场,进而先对焊缝造成冲蚀磨损。Lathabai等[6]研究固粒对不锈钢、陶瓷、聚合物涂层等叶轮材料的冲蚀磨损机理,发现硬度高、有棱角的固粒对材料磨损更严重,涂层的微观结构对磨损机制有重要的影响。由于叶轮机械内气固两相流动的复杂性,相关试验研究主要采用PIV测量技术,许洪元等[7]将PIV技术应用于叶轮机械流道中固粒速度场的研究,认为固粒的密度影响其在叶轮中的相对运动轨迹,固粒的粒径和形状则主要影响其运动速度。但是,PIV试验装置复杂、费用高并且耗时长。数值模拟技术是目前研究叶轮机械内部流动经常采用的重要方法和手段[8-11],数值模拟与实验测量比较具有投资小、研究周期短、风险低等特点。本文在总结前人研究成果的基础上,采用数值模拟技术,结合对叶轮失效的调研,对离心空压机叶轮叶片压力面的冲蚀磨损规律进行研究,旨在为揭示叶轮失效机理提供理论参考。
1 叶轮冲蚀磨损概述
1.1 调研资料
对沈阳鼓风机厂的失效叶轮调研中发现,2MCL803离心式空压机叶轮叶片压力面后缘根部变薄,有明显的材料流失,图1所示为叶片变薄部位。根据叶轮失效的宏观形貌分析,表面有细而长的划痕,没有较深的裂纹,判断其变薄现象是由固粒的冲蚀磨损造成的。

图1 叶轮叶片压力面后缘根部材料流失
Fig. 1 Material loss on blade trailing edge roots
1.2 冲蚀磨损分析
大气颗粒物主要来自6类源:扬尘(土壤尘、道路尘、建筑尘)、燃煤、工业排放、机动车排放、生物质燃烧、SO2或NOx氧化产生的二次颗粒物[12],粒径一般为1~20 μm,颗粒物质量浓度一般为100~200 μg/m3;重工业大气中颗粒物的质量浓度更高。颗粒物的种类有硅铝酸盐、富钙颗粒、碳质颗粒和富铁颗粒等[13],本文中以石英粒子作为固相颗粒进行研究。
压气机内气固两相流中固相颗粒的来源如下:
(1) 重工业地区空气质量差,空压机前虽然采用空气过滤器,但粒径为10 μm以下的固粒难以过滤。
(2) 过滤器在固粒的冲击下容易损坏,易使大量灰尘被带入压缩机。
(3) 在空压机内,某个部位生锈后,锈蚀片会被气流冲刷脱落,使它们夹在气流中进入叶轮[14]。
固粒在气流的夹带和自身惯性的综合作用下,以非零攻角碰撞壁面,然后又反弹进入流道内,引起壁面材料的磨损,是典型的冲蚀磨损。当含有固粒的流体作为工作介质通过叶轮时,被流体夹带的固粒将对所流经的固体壁面产生磨损作用。由固相冲蚀磨损所造成的叶轮材料流失、寿命缩短等问题广泛存在。叶轮材料磨损主要是工作介质中具有相当硬度的固粒对零件表面冲击破坏作用的累积效应[15]。
冲蚀磨损是造成叶片断裂或掉块的重要原因之一。根据王文俊等[16]的相关研究,压气机第1级1个叶片在后缘叶根处出现掉块现象,呈半圆弧状缺损形态。由于叶轮工作中微小固粒随气流在叶片表面冲蚀形成显微缺陷,它们的存在加重局部应力的集中,在冲蚀磨损和疲劳的共同作用下,叶片发生掉块和断裂现象。气固两相介质中固粒对叶片及叶轮的不均匀磨损等原因会引起的转子不平衡,导致振动值随着运行时间的延长而逐渐增大,容易引起磨损失效或其他形式的失效。
在离心式空压机叶轮内部,固粒对叶片的碰撞都集中在压力面上,对吸力面的碰撞很少发生,这与叶轮内气相的流场有关,因此,冲蚀磨损失效都发生在压力面上,这和本文的数值模拟结果相吻合。
2 数值模拟的理论基础
2.1 计算模型
计算模型为离心空压机第二级叶轮,采用Pro/E软件生成三维计算区域模型。为保证模拟的稳定性,对叶轮流道进口与出口做适当延伸。叶轮示意图和三维造型如图2所示,叶轮三维造型包括轮盘、轮盖和叶片。
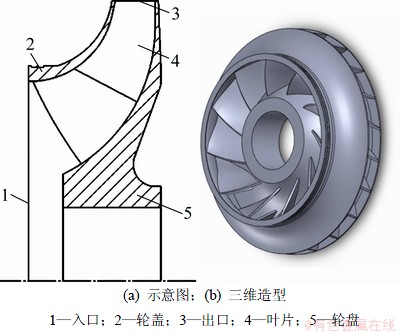
图2 叶轮示意图和三维造型
Fig. 2 Schematic diagram and 3D model of impeller
2.2 网格划分
由于结构化网格质量好,数据结构简单,对曲面或空间的拟合大多数采用参数化或样条插值的方法得到,区域光滑,与实际的模型更容易接近,在此采用结构化网格划分。三维全流场网格长度为6 mm,整个计算域网格数为823 899个,节点数为198 742个。
2.3 连续相的控制方程及湍流模型
离心式空压机叶轮内部的三维气固两相流动是典型的湍流流动,连续相工作介质为可压缩气体。采用三维雷诺时均N-S方程和标准k-ε两方程湍流模型为基础,利用Simple算法,对其进行连续相流场的数值模拟[8]。连续性方程为
(1)
动量方程为
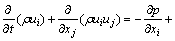
(2)
动量方程中采用湍流的动力黏性概念,湍流动力黏性系数为
(3)
其中:Cμ=0.084 5。
标准k-ε模型的输运方程为:

(4)

(5)
2.4 离散相的控制方程
离散相模型(DPM)适用于体积分数低于10%的多相流,工业大气中固相颗粒物体积分数远小于10%,故离散相模型适用于本数值模拟。由于体积分数较低,气固两相之间的耦合作用是单向的,不计固粒对气流产生的影响并忽略固粒之间的相互作用。再次,假定流场中作用于粒子的力只有气固两相的速度差对粒子产生的黏性力,忽略其他多种耦合作用。离散相的计算是独立的,被安排在连续相计算中指定的间隙内完成。固粒在x方向受力控制方程为[17]
(6)
其中:vp和vf分别为固粒速度、气相速度;ρp和ρf分别为固粒密度、气相密度;FD(vf-vp)为固粒的单位质量阻力;g为重力加速度。
(7)
其中:Fx为其他外力的总和,主要包括虚假质量力、巴西特加速度力、马格努斯升力、萨夫曼升力等作用力。 本文固粒粒径属于微米级,在进行数值模拟时近似忽略固粒的自身旋转效应,故不考虑由于横向速度梯度使固粒旋转产生的马格努斯升力和萨夫曼升力。
2.5 边界条件
连续相:入口处质量流量Qf=26 kg/s,入口压强pin=0.17 MPa,转速n=6 180 r/min。同时,给定湍流强度I和水力直径D。
离散相:固粒从入口处均匀分布释放,设置离散相的初速度、质量流量、固粒直径等几何参数。离散相固粒进入第二级叶轮之前会与扩压器、弯道及回流器发生碰撞,固粒会有能量损失,故初速度小于气相的初速度,在本文研究中固粒的初速度设定在5~25 m/s之间。
固粒与部件壁面碰撞会产生能量损失,固粒反弹恢复比(即反射速度与入射速度之比)可表示为入射角α1的函数。本文采用针对石英粒子与不锈钢板碰撞时得到的反弹恢复比表达式[9]:
(8)
(9)
其中:vpt和vpn分别为固粒的切向和法向速度;下标1和2分别代表碰撞前、后。
2.6 塑性材料冲蚀磨损模型
在进行磨损的数值模拟计算时,叶轮材料选用塑性材料不锈钢,用单位时间在单位面积内的质量磨损率Wm(kg·m-2·s-1)来研究不同条件下固粒对叶轮壁面的冲蚀磨损规律,质量磨损率定义为[17]
(10)
其中:C(dp)为固粒直径的函数,α为固粒对壁面的冲击角,f(α)为冲击角的函数,v是固粒相对于壁面的速度,b(v)是相对速度的函数。
3 正交模拟试验及结果分析
3.1 试验目的
(1) 探索选定的几何参数对磨损率分布及数值的影响规律,找出因素对磨损率影响的主次顺序。
(2) 选择确定对叶片磨损最严重的参数组合,具体研究固粒的某一个几何参数对磨损率的影响规律。
3.2 试验因素
选择固粒初速度v1、固粒直径d、固粒质量流量Q等3个因素为正交试验的变化因素,其水平选定如表1所示。
本研究是一个多指标试验设计,主要考察分析磨损率均值Wavg、磨损率峰值Wmax来研究叶片的磨损情况,在2个指标中,磨损率峰值对叶片磨损的影响较大。由因素及水平,选择正交试验方案为L25(56),共计25次试验,其对应设计方案如表2所示。
表1 因素水平表
Table 1 Factor level

3.3 模拟实验结果,进行极差分析
表2列出了对25个设计模型的预测结果,由预测结果可知,叶轮磨损最严重的部位是叶片压力面,固粒初速度、粒径和质量流量的变化引起固粒冲击速度和冲击角度的变化,进而影响磨损规律。
表2 正交模拟试验方案及结果
Table 2 Orthogonal simulated test scheme and results
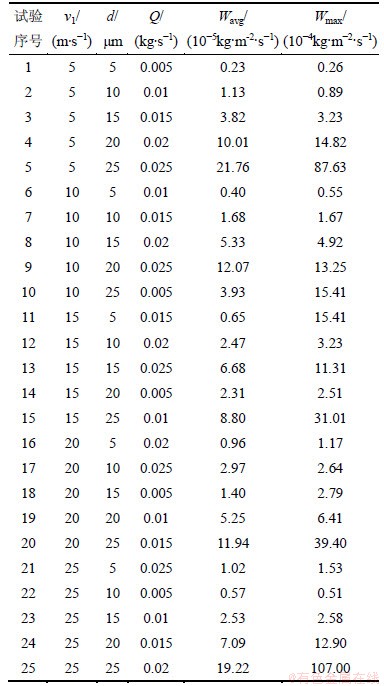
一般来说,各因素的水平改变对试验结果的影响不同,因此,各列的极差不同。极差越大,该因素的水平对试验结果影响越显著。分别比较各因素对磨损率均值、磨损率峰值这2个性能指标的极差大小,按极差大小可以确定各因素对各性能指标影响的主次顺序,极差分析结果如表3所示。
对磨损率均值和磨损率峰值这2个指标,各因素影响的主次顺序都为:d>Q>v1,也就是说,固粒直径变化带来的影响最显著,质量流量其次,固粒初速度的影响最小。随着粒径的增大,叶轮叶片压力面磨损率迅速升高,对叶轮的损坏带来很严重的影响,所以,要定期对过滤装置进行的检修,缩小检修周期,严格限制进入压缩机微小固体颗粒粒径。
表3 模拟结果分析
Table 3 Analysis of simulation results
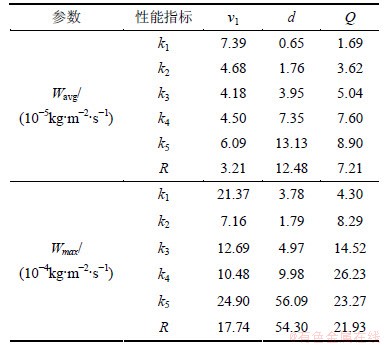
选出的磨损率均值最大组合参数为:A1,B5和C5,磨损分布情况如图3所示。磨损率峰值最高组合参数为:A5,B5和C4。磨损分布情况如图4所示。
选出的磨损率均值最大组合参数为:A1,B5和C5,磨损分布情况如图3所示。磨损率峰值最高组合参数为:A5,B5和C4。磨损分布情况如图4所示。
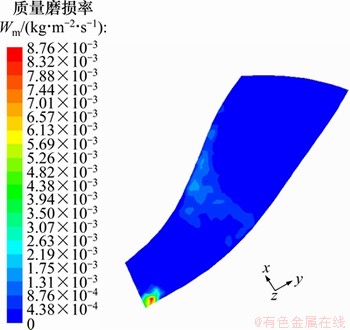
图3 磨损率均值最大组合参数对应的磨损分布
Fig. 3 Distribution of erosion with parameters of most average wear rate
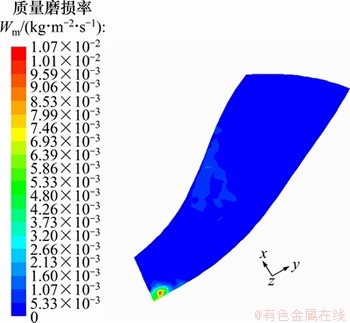
图4 磨损率峰值最高组合参数对应的磨损率分布
Fig. 4 Distribution of erosion with parameters of most maximum wear rate
4 单因素分析
4.1 固粒直径对叶片磨损的影响
在2个指标中,磨损率峰值的数值及位置对叶片磨损的影响最大,选定磨损率峰值最高组合参数中v1和Q,v1=25 m/s,Q=0.02 kg/s,改变d,分析固粒直径的改变对叶片磨损的影响。
图5所示为叶片压力面磨损率均值及磨损率峰值随固粒直径变化曲线。由图5可见:
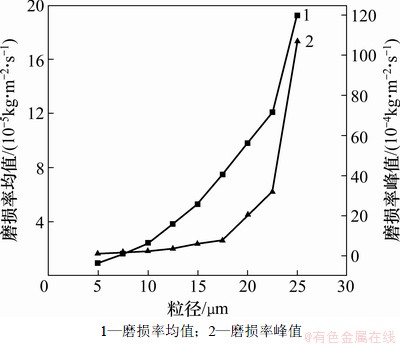
图5 压力面磨损率均值及磨损率峰值随固粒直径变化
Fig. 5 Average and maximum erosion rates of pressure surface vs particle diameter
(1) 固粒初速度和固粒质量流量固定情况下,压力面磨损率均值随固粒直径的增大而增加,增加幅度均匀,几乎为线性变化,固粒粒径超过20 μm后增长速度逐渐增加。
(2) 固粒初速度和固粒质量流量固定情况下,压力面磨损率峰值随固粒直径增大而增加,粒径小于17.5 μm增长速度缓慢,对叶片磨损轻微;粒径大于17.5 μm增长速度急剧增高,对叶片磨损严重。
图6所示为Q=0.02 kg/s,v1=25 m/s,d分别为5,15和25 μm时叶片压力面磨损分布图。由图6可见:当固粒直径较小时,磨损率峰值位于叶片压力面中部。这是因为粒径小的颗粒惯性小,气流黏性作用的影响相对较大,固粒随着气流冲击叶片压力面的中部。随着固粒直径的增加,磨损率峰值位于压力面后缘根部,中部磨损仍较为严重。磨损率的分布与入射固粒的径向位置有关。远离转轴的固粒碰撞到叶片中部,冲击速度不是很大,磨损情况不是最严重。靠近转轴的固粒碰撞到叶片后缘根部,冲蚀速度较大,固粒较密集,磨损情况严重。当固粒直径增大至25 μm,磨损率峰值仍位于叶片压力面后缘根部,压力面中部也有轻微磨损。

图6 粒径不同的固粒对叶片压力面的磨损对比
Fig. 6 Comparison of erosion on pressure surface particles with different diameters
4.2 固粒初速度对叶片磨损的影响
选定d=25 μm、Q=0.02 kg/s,改变v1,分析固粒初速度的改变对叶片磨损的影响。
图7所示为叶片压力面磨损率均值及磨损率峰值随固粒初速度变化曲线。由图7可见:
(1) 固粒直径和质量流量固定情况下,压力面磨损率均值随固粒初速度的增大变化规律不明显,固粒初速度超过17.5 m/s后磨损率均值逐渐增长。
(2) 固粒直径和质量流量固定情况下,压力面磨损率峰值随固粒初速度的增加先无明显变化后迅速增大,当v1=12.5 m/s时,磨损率峰值达到最小值;当固粒初速度大于15 m/s时,压力面磨损率峰值增长速度逐渐增大,对压力面的磨损越来越严重。当固粒初始速度大于某一个临界值时,初速度越大,与气相的速度差就越小,气相对固粒的速度影响更明显,与叶片压力面的碰撞速度越大,在碰撞角度、碰撞恢复系数等因素不变的情况下,局部磨损率峰值也越大。
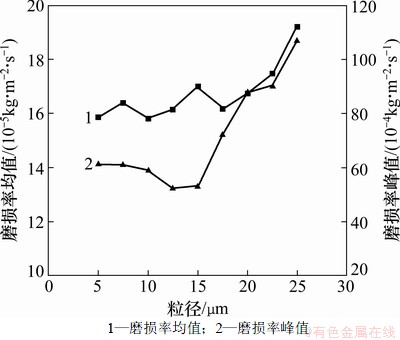
图7 压力面磨损率均值及磨损率峰值随固粒速度变化
Fig. 7 Average and maximum erosion rates of pressure surface vs particle velocity
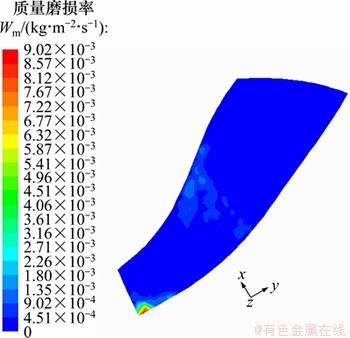
图8 初速度不同的固粒对叶片压力面的磨损分布
Fig. 8 Distribution of erosion on pressure surface with different initial velocities
图8所示为d=25 μm,Q=0.02 kg/s,v1=22.5 m/s时叶片压力面磨损分布图。入口处固粒不同初速度所对应的磨损分布情况与图8相似,仅磨损率不同。由图8可见:磨损率峰值位于叶片压力面后缘根部,压力面中部也有轻微磨损。叶片压力面磨损的分布主要由固粒直径大小决定,固粒初速度的改变只对磨损率有作用,对磨损分布的影响很小。
4.3 固粒质量流量对叶片磨损的影响
选定d=25 μm和v1=25 m/s,改变Q,分析固粒质量流量的改变对叶片磨损的影响。
图9所示为叶片压力面磨损率均值及磨损率峰值随固粒质量流量变化曲线。由图9可见:入口固粒初速度和质量流量固定情况下,压力面磨损率均值和磨损率峰值都随固粒质量流量的增大而增加,几乎呈线性增长,增长速度较快。当固粒直径、性质确定时,固粒质量流量越大,单位时间内流过叶轮的固粒数量越多,固粒的浓度越大,与叶片碰撞的次数越多,对叶片压力面的磨损就越严重。
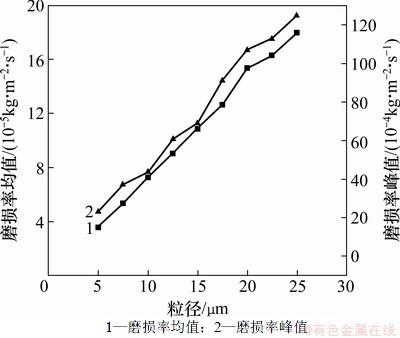
图9 压力面磨损率均值及磨损率峰值随固粒质量流量变化
Fig. 9 Average and maximum erosion rates of pressure surface with particle mass flow
图10所示为d=25 μm,Q=0.025 kg/s,v1=25 m/s时叶片压力面磨损分布图。不同固粒质量流量所对应的磨损分布情况与图10相似,仅磨损率不同。由图10可见:磨损率峰值位于叶片压力面后缘根部,压力面中部也有轻微磨损。叶片压力面磨损的分布主要由固粒直径决定,质量流量的改变只对磨损率有较大作用,对磨损分布的影响很小。

图10 质量流量不同的固粒对叶片压力面的磨损分布
Fig. 10 Distribution of erosion on pressure surface with different mass flows
5 结论
(1) 应用气固两相流的离散相模型,对气固两相流中体积分数低的离散相固粒在离心式压缩机叶轮中的磨损结果进行数值模拟,得到固粒对叶片碰撞的冲蚀磨损分布,得出离散相固粒与叶轮叶片的冲蚀磨损规律。
(2) 叶轮叶片压力面的磨损远大于吸力面,由固粒冲蚀所造成的磨损部位集中在叶片后缘根部,叶片中部也有轻微磨损。
(3) 固粒初速度、粒径和质量流量3个变量中,固粒直径的改变对叶片的磨损影响最大,质量流量次之,初速度的影响最小。所以,要严格限制进入压缩机微小固粒粒径。
参考文献:
[1] Farrahi G H, Tirehdast M, Masoumi K A. Failure analysis of a gas turbine compressor[J]. Engineering Failure Analysis, 2011, 18(1): 474-484.
[2] Kubiak J, Urquiza G, Rodriguez J A. Failure analysis of the 150 MW gas turbine blades[J]. Engineering Failure Analysis, 2009, 16(6): 1794-1804.
[3] Kermanpur A, Sepehri Amin, Ziaei-rad S. Failure analysis of Ti6Al4V gas turbine compressor blades[J]。 Engineering Failure Analysis, 2008, 15(8): 1052-1064.
[4] Sivaprasad S, Narasaiah N, Das S K. Investigation on the failure of air compressor[J]. Engineering Failure Analysis, 2010, 17(1): 150-157.
[5] Ariely S, Khentov A. Erosion corrosion of pump impeller of cyclic cooling water system[J]. Engineering Failure Analysis, 2006, 13(6): 925-932.
[6] Lathabai S, Ottmuller M F. Solid particle erosion behavior of thermal sprayed ceramic, metallic and polymer coatings[J]. Wear, 1988, 221(2): 93-108.
[7] 许洪元, 卢达熔, 焦传国. 离心泵流道中固粒速度场的粒子成像测速(PIV)分析与研究[J]. 农业工程学报, 1988, 14(3): 112-116.
XU Hongyuan, LU Darong, JIAO Chuanguo. Particle image displacement velocity (PIV) and velocity field of solid particles in centrifugal pump[J]. Transactions of Chinese Society of Agricultural Engineering, 1988, 14(3): 112-116.
[8] Mazur Z, Campos-amezcua R, Urquiza G. Numerical 3D simulation of the erosion due to solid particle impact in the main stop valve of a steam turbine[J]. Applied Thermal Engineering, 2004, 24(13): 1877-1891.
[9] 刘娟, 许洪元, 唐澍, 等. 离心泵内固粒运动规律与磨损的数值模拟[J]. 农业机械学报, 2008, 39(6): 54-59.
LIU Juan, XU Hongyuan, TANG Shu, et al. Numerical simulation of erosion and particle motion trajectory in centrifugal pump[J]. Transactions of the Chinese Society for Agricultural Machinery, 2008, 39(6): 54-59.
[10] 吴波, 严宏志, 徐海良, 等. 渣浆泵内固相颗粒冲蚀特性的数值模拟[J]. 中南大学学报: 自然科学版, 2012, 43(1): 124-129.
WU bo, YAN Hongzhi, XU Hailiang, et al. Numerical simulation about erosion characteristics of solid particle inslurry pump[J]. Journal of Central South University: Science and Technology, 2012, 43(1): 124-129.
[11] 盛振国, 李陈峰, 任慧龙. 基于CFD的大型风力发电机组叶片气动性能研究[J]. 哈尔滨工程大学学报, 2012, 5: 595-600.
SHENG Zhenguo, LI Chenfeng, REN Huilong. Investigation on the aerodynamic performance of large wind turbine blade based on CFD[J]. Journal of Harbin Engineering University, 2012, 5: 595-600.
[12] 胡敏, 唐倩, 彭剑飞, 等. 我国大气颗粒物来源及特征分析[J]. 环境与可持续发展, 2011, 36(5): 15-19.
HU Min, TANG Qian, PENG Jianfei, et al. Study on characterization and source apportionment of atmospheric particulate matter in china[J]. Environment and Sustainable Development, 2011, 36(5): 15-19.
[13] 董树屏, 刘涛, 孙大勇, 等. 用扫描电镜技术识别广州市大气颗粒物主要种类[J]. 岩矿测试, 2001, 20(3): 202-207.
DONG Shuping, LIU Tao, SUN Dayong, et al. Identification of major particle classes in guangzhou aerosol by scanning electron microscopy[J]. Rock and Mineral Analysis, 2001, 20(3): 202-207.
[14] 马雷. 离心式压缩机故障原因分析及处理措施[J]. 风机技术, 2007(1): 83-84.
MA Lei. Trouble analysis an measure on centrifugal compressor[J]. Compressor Blower and Fan Technology, 2007(1): 83-84.
[15] Walker C I, Bodkin G C. Empirical wear relationships for slurry pump, partI: side-liners[J]. Wear, 2000, 242(1/2): 140-146.
[16] 王文俊, 唐海军. 民用航空器APU压气机第一级叶轮损伤分析[J]. 材料导报, 2009, 23(14): 230-232.
WANG Wenjun, TANG Haijun. Failure analysis of the failed stage 1 APU wheel of civil aviation aircraft[J]. Materials Review, 2009, 23(14): 230-232.
[17] Bozzini B, Marco E, Marco B. Evaluation of erosion–corrosion in multiphase flow via CFD and experimental analysis[J]. Wear, 2003, 255(1/6): 237-245.
(编辑 邓履翔)
收稿日期:2012-12-29;修回日期:2013-02-26
基金项目:国家重点基础研究发展计划(“973”计划)项目(2011CB013401)
通信作者:贾秀杰(1963-),男,山东昌邑人,博士,副教授,从事离心式压缩机叶轮失效机理的研究;电话:0531-88392003;E-mail:xjjia@sdu.edu.cn