Cr-N涂层高速钢在Na3PO4水溶液中的
摩擦-腐蚀电化学噪声行为
范爱兰1, 唐宾1,田林海1,吴培强1,刘道新2
(1. 太原理工大学 表面工程研究所, 山西 太原,030024;
2. 西北工业大学 航空学院,陕西 西安,710072)
摘要:在M2高速钢表面磁控溅射制备Cr-N耐磨减摩涂层,用SEM观察涂层组织,采用XPS及GDOES分析涂层表面价态及主要元素分布情况,利用附带电化学噪声装置的微动摩擦学试验机测试涂层及基材在0.02 mol/L Na3PO4溶液环境下的摩擦学性能及其同步电化学噪声变化规律,并与涂层及基材在干摩擦条件下的摩擦学性能指标进行对比。研究结果表明:涂层为双层及双组分结构,组成相为Cr+CrN;涂层在空气介质中表现出优异的耐磨减摩特性,但在Na3PO4水溶液环境下介质中,由于涂层接触区域的去钝化/再钝化以及界面点蚀使腐蚀和磨损相互加速,导致Cr-N涂层丧失了减摩及抗磨作用,失效行为完全不同于干摩擦条件。
关键词:Cr-N涂层;摩擦学性能;电化学噪声
中图分类号:TG115.5 文献标志码:A 文章编号:1672-7207(2012)05-1690-06
Wear-electrochemical noise behavior of Cr-N coating on M2 HSS in Na3PO4 solution
FAN Ai-lan1, TANG Bin1, TIAN Lin-hai1, WU Pei-qiang1, LIU Dao-xin2
(1. Institute of Surface Engineering, Taiyuan University of Technology, Taiyuan 030024, China;
2. School of Aeronautics, Northwestern Polytechnical University, Xi’an 710072, China)
Abstract: Cr-N hard coating was synthesized on M2 HSS surface by magnetron sputtering deposition. Scanning electron microscope (SEM), X-ray photoelectron spectroscopy (XPS) and glow discharge optical emission spectroscopy (GDOES) analysis were used to characterize coating microstructure, electronic state of Cr and N elements in the surface and main elements distribution. Corrosion-wear behaviors of M2 substrate and coating sliding against corundum were studied using an electrochemical noise technique in 0.02 mol/L Na3PO4 solution. Wear behaviors of the M2 steel and Cr-N coating in ambient air were also investigated for comparison. The results show that the Cr-N coating has duplex-layer structure, where Cr and CrN are mainly of coating composition, and wear resistance of the M2 substrate in ambient air is significantly improved by the Cr-N coating. In Na3PO4 solution, as the depassivation-repassivation and interface pitting accelerate both corrosion and abrasion, the Cr-N coating has no antifriction and antiwear effect on the M2 substrate, and its failure characteristic is completely different from that of in ambient air condition.
Key words: Cr-N coating; wear behavior; electrochemical noise
氮化铬(CrN)金属陶瓷涂层具有高硬度、良好的抗磨性和热稳定性,同时,具有比氮化钛(TiN)涂层更强的耐蚀性和韧性以及更低的沉积温度,不但可用于工模具、耐磨结构件的表面强化,而且适用于不锈钢、铜合金及铝合金等较低硬度材料的表面改性,适用范围更广[1-6]。对于Cr-N涂层的制备、组织结构和摩擦磨损性能,国内外学者已进行广泛探讨和研究,研究普遍认为,随N含量不同,Cr-N涂层通常由金属态Cr,β-Cr2N和CrN及其混合相组成[7],涂层硬度随沉积方法和结构的不同差异较大,一般为17~23 GPa[8],但也有文献报道其硬度可达44.9 GPa[9]。在干摩擦条件下,Cr-N涂层一般表现为磨粒磨损,考虑涂层多数工作于不同介质环境中,腐蚀介质与摩擦磨损共同作用使涂层失效机理更为复杂,例如涂层的磨损率和摩擦因数强烈依赖于实验环境相对湿度[10],特别是由于涂层制备过程中存在的一些结构缺陷如针孔等是影响涂层腐蚀和摩擦学性能的关键因素[11]。近年来,一些研究者采用摩擦磨损过程中引入各种电化学测试方法来研究摩擦-腐蚀行为,其中恒电位法可以量化机械损伤导致的腐蚀电位或电流变化,应用较为广泛[12]。但人为电位的加入加强了已有的电化学腐蚀,造成额外腐蚀现象,加速了腐蚀磨损过程。也有应用如开路电位法、动电位阳极极化法和电化学阻抗等电化学方法与滑动摩擦磨损相结合研究腐蚀磨损过程,但与这些测试方法相比,原位无损的电化学噪声(Electrochemical noise,EN)技术反映电学状态参量随时间随机非平衡波动特征,而且对腐蚀过程中的点蚀、裂蚀等局部腐蚀敏感,更适合于实时在线监测涂层腐蚀磨损过程动力学行为[13]。本文作者针对食品生产加工领域中比较广泛的弱酸环境,借鉴国外先进的摩 擦-电化学噪声试验方法,研究Cr-N涂层在Na3PO4溶液环境下的摩擦学性能,通过电化学噪声全程同步监测摩擦过程的噪声电压及电流的变化,分析涂层的腐蚀-磨损实验现象,并和干摩擦条件下的性能进行比对,探讨基材及涂层在大气及弱酸环境中的磨损-腐蚀交互作用机理。
1 实验
试验用基材为M2高速钢(HRC64,试样表面平均粗糙度Ra≤0.05 μm)。所用的Cr靶材由纯度为99.99%、粒度为75~300 μm的Cr粉,真空热压成形。磁控溅射镀膜设备工业方法制备Cr-N涂层,施镀时间为120 min,涂层厚度约为2.0 μm,试样表面平均粗糙度Ra≤0.05 μm。
用JSM-6700F场发射扫描电子显微镜观察镀层组织,ESCALAB 250实时化学成像X线光电子能谱仪(XPS,ESCA能谱仪)分析涂层表面结构,GDA750辉光放电成分分析仪分析镀层成分分布。利用比利时鲁文大学材料系微动摩擦学试验机(Fretting wear tester,附带电化学噪声测量装置)测试M2基材及Cr-N涂层在空气介质中和0.02 mol/L Na3PO4水溶液中的摩擦学性能,试验装置见文献[14]。用WYKO NT3300三维激光形貌测量仪观察测量磨痕轮廓,并计算磨损体积。为减少摩擦副的影响,选择化学性质稳定的Φ10 mm Al2O3陶瓷球(Ceratec, The Netherlands),直径为10 mm,粗糙度平均值Ra=0.20 μm。试验条件是:载荷为5 N,往复摩擦频率为10 Hz,微动摩擦间距为200 μm,环境温度为23 ℃,相对环境湿度为50%。为获得稳定的电化学噪声实验参量,摩擦实验开始前,试样在溶液中统一静置500 s,电化学噪声测量装置为Solartron IS1287电化学界面,参比电极为Ag/AgCl (3 mol/L KCl),微电极为Pt电极,与系统绝缘的磨损试样为工作电极。
2 结果与讨论
2.1 Cr-N涂层组织结构
图1所示为Cr-N涂层截面组织。由图1可以看出:涂层厚度约为2 μm,涂层组织为明显柱状晶结构。XPS分析Cr2p电子结合能结果表明:镀层的Cr2p电子结合能为双峰,峰值分别为575.75 eV和574.30 eV,对应CrN和Cr的Cr2p标准电子结合能分别为575.80 eV和574.26 eV。另外,N1s结合能的测试值为396.95 eV,和CrN的N1s标准电子结合能396.70 eV相近,与Cr2N的N1s标准电子结合能297.40 eV相差明显,说明涂层中没有Cr2N相存在,镀层为Cr+CrN双相混合组织[15]。涂层成分分布GDOES测试结果(如图2所示)也证实,涂层中存在金属态Cr,涂层为明显双层结构,表层CrN组分约为70%,中间过渡层Cr和CrN各50%。

图1 Cr-N涂层截面SEM形貌
Fig.1 Cross-section SEM image of Cr-N coating
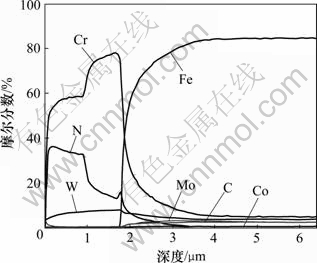
图2 Cr-N涂层GDOES成分分布
Fig.2 GDOES depth profiles of Cr-N coating
2.2 空气介质中的微动摩擦学性能
图3所示为空气介质试验条件下M2高速钢基体及相同基材上Cr-N涂层摩擦因数与摩擦循环周次关系曲线。从图3可见:高速钢和涂层起始摩擦因数分别为0.42和0.30。随着循环周次增加,高速钢基材摩擦因数持续上升,在循环10 000次处,摩擦因数基本趋于稳定,为0.60。Cr-N涂层的摩擦因数比基体有明显降低,且随着循环周次的增加,涂层摩擦因数有降低的趋势。循环6 000次后,涂层的摩擦因数稳定在0.20左右。循环20 000次后,磨痕磨损形貌观察及体积测量结果表明,高速钢基材磨痕深度为2.40 μm,Cr-N涂层磨痕深度仅为0.63 μm,对应磨损体积分别为109 000和15 000 μm3,Cr-N涂层磨损体积约为基材的1/7,磨痕轮廓如图4所示,耐磨特性显著提高,且未发生涂层剥落现象。在空气介质条件下,Cr-N涂层不但具有明显的减摩作用,而且耐磨特性优异。
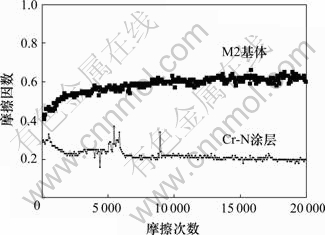
图3 空气介质中摩擦因数随摩擦周次变化曲线
Fig.3 Coefficient of friction for M2 HSS substrate and Cr-N coating sliding against corundum in ambient air
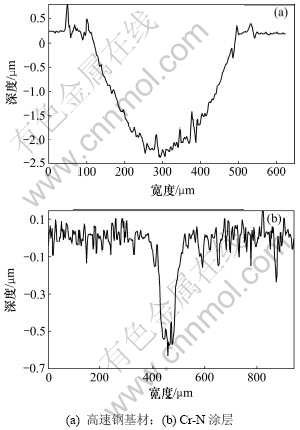
图4 空气介质中高速钢基材及Cr-N涂层20 000循环周次磨损轮廓
Fig.4 Profile across wear scar of M2 HSS substrate and CrN coating sliding against corundum in ambient air after 2 000 cycles
选择制备的Cr-N涂层及M2高速钢基材为对比试材,分别进行0.02 mol/L Na3PO4水溶液中摩擦学性能对比测试,了解涂层在Na3PO4水溶液水环境条件下的摩擦学特性及其电化学噪声变化规律,实验结果如图5和图6所示。高速钢和Cr-N涂层起始摩擦因数分别为0.35和0.27,随着循环次数的增加,摩擦因数虽然有一定的上升,但这种趋势变化不大,2种试验材料的初始摩擦因数变化不大,即使在实验结束的20 000次循环处,高速钢基体及涂层的摩擦因数也仅仅分别为0.37和0.32。对比图3,Cr-N涂层在0.02 mol/L Na3PO4水溶液中的减摩效果远不如在空气介质中的效果显著,溶液对高速钢基材存在明显的减摩润滑作用,但对Cr-N涂层摩擦因数反而较空气介质中增大。
图7(a)和7(b)分别所示为高速钢基材及Cr-N涂层20 000循环周次后磨痕三维轮廓。测量显示高速钢基材及Cr-N涂层的磨痕深度分别为0.78和0.85 μm。高速钢基材及Cr-N涂层的计算磨痕磨损体积分别为 23 000和40 000 μm3。可见:在0.02 mol/L Na3PO4水溶液环境中,高速钢基材磨损量反而远低于硬质Cr-N涂层。Cr-N涂层不但没有明显改善材料的表面减摩性能,反而显著降低了材料的表面抗磨特性,在0.02 mol/L Na3PO4水溶液中,Cr-N涂层磨损机制显然不同于空气介质中相对简单的黏着/磨粒磨损机制。
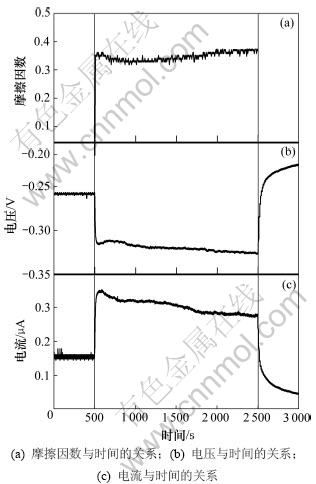
图5 M2高速钢基材在0.02 mol/L Na3PO4水溶液中20 000循环周次摩擦因数及电化学噪声变化规律
Fig.5 Coefficient of friction and potential-current noise for M2 HSS substrate sliding against corundum in 0.02 mol/L Na3PO4 solution (5 N, 10 Hz, 200 μm, 20 000 cycles)
对比图5(b)和5(c)与图6(b)和6(c)高速钢基材及Cr-N涂层在0.02 mol/L Na3PO4水溶液介质中摩擦前及摩擦试验过程中的电化学噪声电压及噪声电流发现,M2基材和Cr-N在0.02 mol/L Na3PO4水溶液介质中的稳态开路电极电位分别约为-0.26和-0.10 V,两者差值为0.16 V;M2高速钢在试验前及摩擦试验初始阶段的电位分别为-0.26和-0.32 V,差值为0.06 V,噪声电流分别为0.15和0.30 μA,且在随后的腐蚀-摩擦过程中,噪声参量基本稳定,变化不大;而Cr-N涂层摩擦开始前后,噪声电压分别约为-0.10和-0.27 V,绝对值相差0.17 V;噪声电流则从0.01 μA增加到0.10 μA左右,增加1个数量级。摩擦结束(20 000循环)时,噪声电压升至-0.34 V,噪声电流增大为0.15 μA。以上测量数据表明:Cr-N涂层在0.02 mol/L Na3PO4水溶液介质环境中,涂层在无摩擦的情况下,涂层自身拥有极强的耐蚀特性,但当涂层表面存在机械摩擦损伤的情况下,涂层表现出明显的活化现象。

图6 Cr-N涂层在0.02 mol/L Na3PO4水溶液中20 000循环周次摩擦因数及电化学噪声变化规律
Fig.6 Coefficient of friction and potential-current noise for Cr-N coating sliding against corundum in 0.02 mol/L Na3PO4 solution (5 N, 10 Hz, 200 μm, 20 000 cycles)
另外,从图6(c)可以看出:在涂层腐蚀-摩擦过程中,噪声电流存在明显突变奇异点,电化学噪声中这些突变点一般对应涂层的点蚀击穿现象。说明如图1中Cr-N涂层柱状结构,在腐蚀-摩擦交互作用下,本来耐蚀的Cr-N涂层存在明显点蚀现象。在随后的噪声恢复阶段,表面机械损伤的基材恢复速度明显快于相同实验后的涂层,且基材最终稳定开路电极电位为-0.225 V,高于基材原始开路电极电位的-0.26 V,耐蚀性能不但没有降低,反而有一定程度的提高;涂层最终稳定为-0.09 V,和实验开始时的数值基本相当。结果表明:M2基材在溶液中存在钝化倾向,而涂层基本没有变化。
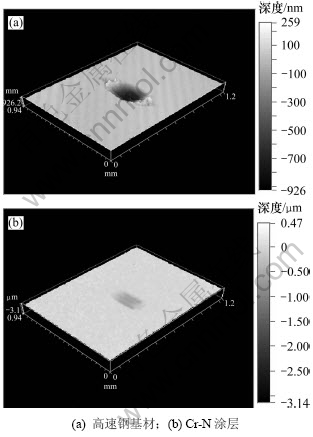
图7 高速钢基材及Cr-N涂层在0.02 mol/L Na3PO4水溶液中20 000循环周次后磨痕三维轮廓
Fig.7 3D profile across wear scar of M2 HSS substrate and Cr-N coating sliding against corundum in 0.02 mol/L Na3PO4 20 000 cycles for M2 substrate and for Cr-N coating
摩擦-磨损是摩擦机械结构部件的主要失效形式。在空气中干摩擦条件下,Cr-N涂层表现为磨粒磨损,抗磨性主要取决于材料表面硬度,Cr-N涂层硬度(本试验中为HV2046)较基体M2(约HV840)高许多,因而表现出比高速钢M2基体更好的减摩和抗磨性能。Na3PO4水溶液对高速钢基体摩擦过程中具有一定的润滑作用,降低摩擦因数和减小磨损体积。而溶液中涂层耐蚀性能一般与材料表面钝化层组织结构及自身缺陷密切相关,耐磨减摩硬质金属陶瓷涂层在一般钝化体系腐蚀环境中,其优异耐蚀性完全得益于表面致密、完整钝化层的存在[16],但在磨损-腐蚀条件下,一方面当摩擦部位表面钝化层发生变化后,该部位的电位降低、活性增加,造成磨损区域和其他钝化区域形成小阳极-大阴极电化学腐蚀,表面钝化层不断破坏又不断生成,这种循环可使腐蚀和磨损相互加速。另一方面,由于涂层自身制备过程中产生的柱状晶等缺陷,加之金属陶瓷涂层本身自腐蚀电位和基材电位通常存在较大差异(本试验中约为0.16 V),也可导致缺陷部位的基材腐蚀,加速涂层破坏。可见:在0.02 mol/L Na3PO4水溶液中,去钝化-再钝化过程(Depassivation-repassivation)以及膜基界面点蚀使Cr-N涂层磨损较空气中加剧,摩擦因数增大。因此,涂层在弱酸环境中的摩擦磨损行为明显不同于大气环境,应该引起重视。
3 结论
(1) Cr-N涂层为明显的Cr和CrN双层结构,表层CrN组分约为70%,中间过渡层Cr和CrN约各为50%。
(2) Cr-N涂层显著降低M2高速钢在大气环境中的摩擦因数,并明显提高M2高速钢表面耐磨性能。
(3) 在0.02 mol/L Na3PO4溶液介质环境下,高速钢基体由于润滑作用,表现出一定的减摩和抗磨效果,Cr-N涂层却由于机械磨损去钝化-再钝化以及界面点蚀反而加速磨损,摩擦因数反而比空气介质中的大。
参考文献:
[1] 唐宾, 李咏梅, 胡奈赛. 离子束增强沉积界面共混工艺对Cr-N镀层结合强度的影响[J]. 无机材料学报, 2000, 15(4): 740-746.
TANG Bin, LI Yong-mei, HU Nai-sai. Effect of intermixing parameters on the bonding strength of IBED Cr-N coatings[J]. Journal of Inorganic Materials, 2000, 15(4): 740-746.
[2] Yoo Y H, Hong J H , Kim J G, et al. Effect of Si addition to CrN coatings on the corrosion resistance of CrN/stainless steel coating/substrate system in a deaerated 3.5 wt.% NaCl solution[J]. Surface and Coatings Technology, 2007, 201(24): 9518-9523.
[3] Ortmannl S, Savan A, Gerbig Y H, et al. In-process structuring of CrN coatings and its influence on friction in dry and lubricated sliding[J]. Wear, 2003, 254(11): 1099-1105.
[4] CAI Feng, HUANG Xiao, YANG Qi, et al. Microstructure and tribological properties of CrN and CrSiCN coatings[J]. Surface and Coatings Technology, 2010, 205(1): 182-188.
[5] Paulitsch J, Schenkel M, Zufra? Th, et al. Structure and properties of high power impulse magnetron sputtering and DC magnetron sputtering CrN and TiN films deposited in an industrial scale unit[J]. Thin Solid Films, 2010, 518(19): 5558-5564.
[6] Elangovan T, Kuppusami P, Thirumurugesan R, et al. Nanostructured CrN thin films prepared by reactive pulsed DC magnetron sputtering[J]. Materials Science and Engineering B, 2010, 167(1): 17-25.
[7] Wei G, Rar A, Barnard J A. Composition, structure, and nanomechanical properties of DC-sputtered CrNx (0≤x≤1) thin films[J]. Thin Solid Films, 2001, 398/399: 460-464.
[8] Grant W K, Loomis C, Moore J J, et al. Characterization of hard chromium nitride coatings deposited by cathodic arc vapor deposition[J]. Surface and Coatings Technology, 1996, 86/87: 788-796.
[9] Barata A, Cunha L, Moura C. Characterisation of chromium nitride films produced by PVD techniques[J]. Thin Solid Films, 2001, 398/399: 501-506.
[10] Mohrbacher H, Blanpain B, Celis J P, et al. The influence of humidity on the fretting behaviour of PVD TiN coatings[J]. Wear, 1995, 180(1/2): 43-52.
[11] Conde A, Navas C, Cristób A B, et al. Characterisation of corrosion and wear behaviour of nanoscaled e-beam PVD CrN coatings[J]. Surface and Coatings Technology, 2006, 201(6): 2690-2695.
[12] Ponthiaux P, Wenger F, Drees D, et al. Electrochemical techniques for studying tribocorrosion processes[J]. Wear, 2004, 256(5): 459-468.
[13] Berradja A, Déforge D, Nogueira R P, et al. An electrochemical noise study of tribocorrosion processes of AISI 304 L in Cl- and SO42- media[J]. J Phys D: Appl Phys, 2006, 39: 3184-3192.
[14] WU Pei-qiang, QUAN Zhen-lan, TANG Lin, et al. Corrosion-wear monitoring of TiN coated AISI 316 stainless steel by electrochemical noise measurements[J]. Applied Surface Science, 2006, 253(3): 1194-1197.
[15] 唐宾, 李咏梅, 胡奈赛, 等. 离子束增强沉积制备CrNx薄膜[J]. 中国有色金属学报, 1999, 9(1): 69-72.
TANG Bin, LI Yong-mei, HU Nai-sai, et al. Fabrication of CrNx films by ibed technique[J]. The Chinese Journal of Nonferrous Metals, 1999, 9(1): 69-72.
[16] Mischler S, Debaud S, Landolt D. Wear-accelerated corrosion of passive metals in tribocorrosion systems[J]. J Electrochem Soc, 1998, 145(3): 750-758.
(编辑 杨幼平)
收稿日期:2011-05-23;修回日期:2011-08-16
基金项目:国家自然科学基金资助项目(51171125);山西省科技攻关项目(20110321051);山西省回国留学人员科研基金资助项目(2011-038)
通信作者:唐宾(1964-),男,湖南祁阳人,博士,教授,从事表面改性研究;电话:0351-6010540;E-mail: tangbin@tyut.edu.cn