
Dissimilar friction stir welding between 5052 aluminum alloy and AZ31 magnesium alloy
YAN Yong(鄢 勇), ZHANG Da-tong(张大童), QIU Cheng(邱 诚), ZHANG Wen(张 文)
School of Mechanical and Automotive Engineering, South China University of Technology,Guangzhou 510640, China
Received 23 September 2009; accepted 30 January 2010
Abstract: Dissimilar friction stir welding between 5052 Al alloy and AZ31 Mg alloy with the plate thickness of 6 mm was investigated. Sound weld was obtained at rotation speed of 600 r/min and welding speed of 40 mm/min. Compared with the base materials, the microstructure of the stir zone is greatly refined. Complex flow pattern characterized by intercalation lamellae is formed in the stir zone. Microhardness measurement of the dissimilar welds presents an uneven distribution due to the complicated microstructure of the weld, and the maximum value of microhardness in the stir zone is twice higher than that of the base materials. The tensile fracture position locates at the advancing side (aluminum side), where the hardness distribution of weld shows a sharp decrease from the stir zone to 5052 base material.
Key words: dissimilar friction stir welding; 5052 aluminum alloy; AZ31 magnesium alloy; microstructure evolution; mechanical property
1 Introduction
Aluminum alloys are widely used in automotive, aerospace and ship industries due to the combination of mass reduction and high strength. Magnesium alloys are also attractive in these fields due to their lower density and high specific strength. Therefore, it can be expected that the joining of aluminum alloys and magnesium alloys needs to be solved in industrial application. However, it is difficult to obtain sound dissimilar welds of these two kinds of alloys through conventional fusion welding techniques since large inter-metallic compounds, which have a strong negative effect on the mechanical properties of the weld, are easy to form in these processes[1].
Friction stir welding (FSW), a solid-state welding process patented by The Welding Institute (TWI) in 1991[2], is a potential candidate for the joining of dissimilar materials due to the lower processing temperature over conventional fusion welding[3]. Defect-free welds have now been made by FSW in the joining of different Al alloys (e.g. Al 2024/Al 7075)[4-5], Al/steel[6-7], Al/copper[8-9] and Al/Mg[3, 10-13]. For Al/Mg dissimilar FSW, YAN et al[11] investigated the microstructure of AZ31 Mg alloy and 1060 Al alloys, and found that the complicated microstructure characterized by the intercalation lamellae band was formed during dissimilar FSW. SOMASEKHARAN et al[12] reported that microhardness profiles exhibited uneven distribution and suggested that the complexed intercalation structures should be responsible for microhardness distribution. SATO et al[3] investigated the dissimilar welding of AZ31 Mg alloy and 1050 Al alloy and attributed the intermetallic compound Al12Mg17 to the uneven microhardness profiles. Due to the complicated flow mechanism during dissimilar FSW, the mechanism of microstructure evolution is not fully understood up to now. The present study concentrated on the understanding of microstructure evolution and mechanical properties of the dissimilar FSW between 5052 Al alloy and AZ31 Mg alloy.
2 Experimental
5052 aluminum alloy and AZ31 magnesium alloy plates with thickness of 6 mm were used in the present study, and the chemical compositions are listed in Table 1.
Table 1 Chemical compositions of AZ31 Mg and 5052 Al alloy (mass fraction, %)

Before welding, the surfaces of the plates were ground with grit paper to remove the oxide film and then cleaned by ethanol. During FSW process, 5052 aluminum alloy and AZ31 magnesium alloy were placed at the advancing side (AS) and the retreating side (RS) of the tool pin, respectively. Dissimilar FSW was carried out on the FSW-3LM-003 welding machine made by the China Friction Stir Welding Center, at a tool rotation rate of 600 r/min and a traverse speed of 40 mm/min. The butt joint was produced parallelly to the rolling direction of the plates. A tool with a concaved shoulder of 15 mm in diameter and a cone-threaded pin of 6 mm in diameter and 5 mm in length was used. The tilt angle was 2? from the normal surface of plates.
Microstructural analysis was performed on the cross section perpendicular to the welding direction. A solution of 4.2 g picric acid, 8 mL acetic acid, 10 mL distilled water and 70 mL ethanol was used as the etchant of the specimen. Microstructure of the weld was observed by optical microscope (OM, KEYENCE VHX-600) and scanning electron microscope (SEM, Quata200) equipped with an EDX system. The measurement of hardness was performed on a HVS-1000 digit hardness tester with a load of 1 N and dwelling time of 20 s.
3 Results and discussion
3.1 Microstructure of dissimilar weld zones
Defect-free weld was successfully obtained by FSW with a rotation speed of 600 r/min and welding speed of 40 mm/min, as shown in Fig.1. A zigzag line showing the interface between Mg alloy and Al alloy was observed from the smooth surface.
A cross-sectional macrograph of the dissimilar weld is presented in Fig.2. As shown in Fig.2, no obvious welding defect was found in the joint, indicating that
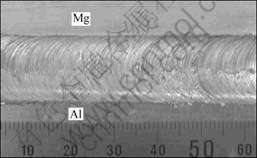
Fig.1 Surface appearance of dissimilar weld prepared by FSW
sound weld of 5052 Al alloy and AZ31 Mg alloy can be obtained by FSW. From Fig.2, it could be found that a simple bond interface was formed on the top of joint and an intermixed structure existed in the bottom of the joint due to the complicated materials flow during dissimilar FSW. The typical microstructural zones, including base material (BM), heat-affected zone (HAZ), thermo- mechanical affected zone (TMAZ) and stir zone (SZ), could be observed in Fig.2. Fig.3 presents the SEM microstructures of these zones. The base material consisted of large equiaxed grains of about 50 μm and fine grains of about 10 μm, as shown in Fig.3(a). Dynamic recrystallization occurred in SZ due to the plastic deformation and thermal cycle effect caused by rotational tool. It should be noted that the fine equiaxed recrystallized grains presented different structures in the different locations of SZ, such as region d, e and f in Fig.2. The grains with average size of 5.4 ?m and 6.9 ?m, which were much smaller than BM, were obtained in region d and e located in the Mg side and Al side of SZ, respectively. Intercalated structures were formed and the average grain size of AZ31 Mg alloy in these structures was about 2.8 μm, as shown in Fig.3(f).
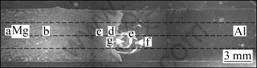
Fig.2 Optical macrograph of cross-section of dissimilar weld
Some interesting observations can be made about the region g in Fig.2, which was located at the bottom of the stir zone near the 5052 Al side and surrounded by the AZ31 Mg alloy. As shown in Fig.4(a), the microstructure consisted of two bands with different contrast. According to EDX analysis results, the gray band was mainly composed of Mg, while the white band was composed of Al. The banded structure looked like onion-ring pattern, but its shape was different from that of monolithic friction stir welds. In previous studies, SUTTON et al[14] and KRISHNAN[15] investigated the mechanism of formation of onion rings in Al alloys, and suggested that the spacing of the layer in onion ring pattern is equal to the forward motion of the tool in one rotation. However, the layer thickness of the onion ring was uneven in this study since the two alloys had different flow abilities. In consequence, complex flow patterns were formed during dissimilar FSW process. Fig.4(b) exhibits the EDX maps of Al and Mg distribution in region g. The chemical composition consisted of about 83% Al and about 17% Mg (mass fraction). From the EDX maps, it can be seen clearly that the lamella structures were composed of aluminum bands and magnesium bands.
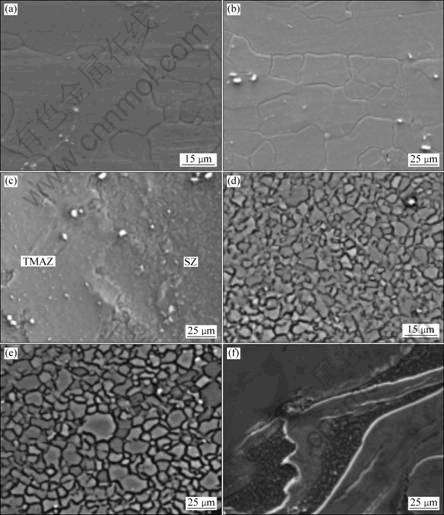
Fig.3 SEM images of AZ31 in different regions, marked with letters in Fig.2: (a) BM; (b) HAZ; (c) Interface of TMAZ/SZ; (d) SZ in Mg side; (e) SZ in Al side; (f) Intercalated microstructure

Fig.4 Microstructures of onion ring in dissimilar weld: (a) Optical microstructure; (b) EDS maps of Mg (c) and Al (d) distribution in onion ring
3.2 Distribution of microstructure
The Vickers microhardness values of the dissimilar weld were measured along the dashed lines marked in Fig.2, which were 1.5 mm (top), 3 mm (middle) and 4.5 mm (bottom) to the top surface, and the results are given in Fig.5. The microhardness presented an uneven distribution, and the hardness of the stir zone was much higher than that of the base material. The maximum value of hardness existing in the middle of the stir zone was twice higher than that of the base material. The hardness measured along the 1.5 mm line was generally lower than that of 3 mm and 4.5 mm due to almost no intermixing occurred between 5052 Al alloy and AZ31 Mg alloy in top region (shown in Fig.2). Onion ring structure and the intercalated microstructure were responsible for the sharp variations of hardness in the weld zone.
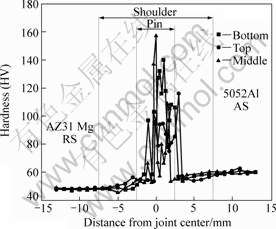
Fig.5 Microhardness profiles of microstructure from Mg to Al with different locations
3.3 Tensile testing
Fig.6 shows the tensile fracture location and the fracture morphology of the dissimilar weld, which was tested perpendicularly to the welding direction. The tensile specimen failed at a location which is 2.5 mm to the joint center at the advancing side, as shown in Fig.6(a). In this location, the hardness gradient was the sharpest according to Fig.5. Fig.6(b) shows the SEM fracture morphology observed from the normal direction to the fracture surface. Cleavage-like feature can be found in the fracture surface, indicating that the dissimilar weld failed through brittle facture.
4 Conclusions
1) Sound weld between 5052 Al alloy and AZ31 Mg alloy could be produced through FSW with a rotation speed of 600 r/min and welding speed of 40 mm/min.
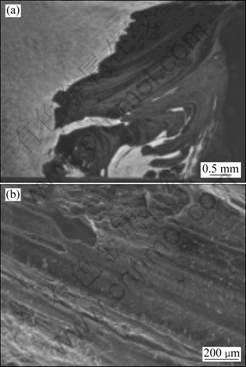
Fig.6 Fracture section of AZ31/5052 dissimilar friction stir weld: (a) Tensile fracture location; (b) SEM image of fracture surface
2) Microstructure of the base metal was replaced by equiaxed and fine grains in stir zone. At the top of the stir zone, 5052 and AZ31 alloys were simply bonded, while onion ring structure which consisted of aluminum bands and magnesium bands was formed at the bottom of the stir zone.
3) Microhardness profiles presented uneven distributions and the maximum value of microhardness in the stir zone was twice higher than that of the base materials. The fracture position located at a distance of 2.5 mm from the joint center leaning to the advancing side (aluminum side), where the hardness gradient was the sharpest.
References
[1] CHEN Y C, NAKATA K. Friction stir lap joining aluminum and magnesium alloys [J]. Scripta Mater, 2008, 58: 433-436.
[2] MISHRA R S, MA Z Y. Friction stir welding and processing [J]. Materials Science and Engineering R, 2005, 50: 1-78.
[3] SATO Y S, PARK S H C, MICHIUCHI M, KOKAWA H. Constitutional liquation during dissimilar friction stir welding of Al and Mg alloys [J]. Scripta Mater, 2004, 50: 1233-1236.
[4] KHODIR S A, SHIBAYANAGI T. Friction stir welding of dissimilar AA2024 and AA7075 aluminum alloys [J]. Materials Science and Engineering B, 2008, 148: 82-87.
[5] CAVALIERE P, NOBILE R, PANELLA F W, SQUILLACE A. Mechanical and microstructural behavior of 2024-7075 aluminium alloy sheets joined by friction stir welding [J]. International Journal of Machine Tools & Manufacture, 2006, 46: 588-594.
[6] UZUN H, DONNE C D, ARGAGNOTTO A, GHIDINI T, GAMBARO C. Friction stir welding of dissimilar Al 6013-T4 to X5CrNi18-10 stainless steel [J]. Materials and Design, 2005, 26: 41-46.
[7] LEE W B, SCHMUECKER M, MERCARDO U A, BIALLAS G, JUNG S B. Interfacial reaction in steel-aluminum joints made by friction stir welding [J]. Scripta Mater, 2006, 55: 355-358.
[8] OUYANG J H, YARRAPAREDDY E, KOVACEVIC R. Microstructural evolution in the friction stir welded 6061 aluminum alloy (T6-temper condition) to copper [J]. Journal of Materials Processing Technology, 2006, 172: 110-122.
[9] LIU Peng, SHI Qing-yu, WANG Wei, WANG Xin, ZHANG Zeng-lei. Microstructure and XRD analysis of FSW joints for copper T2/aluminium 5A06 dissimilar materials [J]. Materials Letters, 2008, 62: 4106-4108.
[10] KOSTKA A, COELHO R S, DOS SANTOS J, PYZALLA A R. Microstructure of friction stir welding of aluminum alloy to magnesium alloy [J]. Scripta Mater, 2009, 60: 953-956.
[11] YAN Jiu-chun, XU Zhi-wu, LI Zhi-yuan, LI Lei, YANG Shi-qin. Microstructure characteristics and performance of dissimilar welds between magnesium alloy and aluminum formed by friction stirring [J]. Scripta Mater, 2005, 53: 585-589.
[12] SOMASEKHARAN A C, MURR L E. Microstructures in friction-stir welded dissimilar magnesium alloys and magnesium alloys to 6061-T6 aluminum alloy [J]. Materials Characterization, 2004, 52: 49-64.
[13] KWON Y J, SHIGEMATSU I, SAITO N. Dissimilar friction stir welding between magnesium and aluminum alloys [J]. Materials Letters, 2008, 62: 3827-3829.
[14] SUTTON M A, YANG B, A. REYNOLDS P, TAYLOR R. Microstructural studies of friction stir welds in 2024-T3 aluminum [J]. Materials Science and Engineering A, 2002, 323: 160-166.
[15] KRISHNAN K N. On the formation of onion rings in friction stir welds [J]. Materials Science and Engineering A, 2002, 327: 246-251.
(Edited by YUAN Sai-qian)
Foundation item: Project(B01B7070270) supported by the Scientific Research Foundation for the Returned Overseas Chinese Scholars, State Education Ministry, China
Corresponding author: ZHANG Da-tong; Tel: +86-20-87112272; Fax: +86-20-87112111; E-mail: dtzhang@scut.edu.cn