
Effect of extrusion on properties of Al-based composite
R. DASGUPTA, S. DAS, S. CHATURVEDI, A. K. JHA
Advanced Materials and Processes Research Institute, CSIR Bhopal 462064, Madhya Pradesh, India
Received 23 December 2009; accepted 7 May 2010
Abstract: An aluminium alloy and its composite with dispersed SiC particles made by liquid metallurgy route were extruded under optimized conditions. The properties were characterized in terms of microstructure, hardness and sliding wear behaviour and then compared between the extruded and cast alloys and composites, in order to understand the benefits of composite and extrusion on the alloy. It was observed that composites drastically increased the hardness and the extruded composites further increased this value. The advantage of composites was realized in sliding wear tests.
Key words: extrusion; Al-alloy; composites; microstructure; wear
1 Introduction
All aluminium alloys can be extruded, but some of them are less suitable, requiring higher pressures, low extrusion speed and/or less surface finish and section complexity, resulting in a set of materials with strength ranging from 150 to 350 MPa, with good toughness and formability[1]. A requirement for extruded Al alloys of particular importance is its flexibility in design, which helps to solve the problem that aluminium and its alloys have only 1/3 the modulus of elasticity of steel. Since the stiffness is dependent not only on the modulus but also the section geometry, stiffness equal to that of steel is obtained at half of its weight by deepening an aluminium beam by around 1.5 times of the steel component which is intended to replace. Also, features can be introduced into the section shape at less die cost, which increases torsional stiffness and provides grooves for fluid removal, service cables, anti-slip ridges, etc. Such features in a steel beam would require joining and machining, thus increase the cost and narrow the cost gap between initial steel and aluminium. The challenge for extruded Al-alloys is the interaction between design and microstructural control, which is critical in optimizing the manufacturing process. Repeatable high quality products by improved fabrication and assembly techniques should be produced. Extruded products constitute more than 50% of the market of aluminium products and aluminium extrusions used in window and door frame systems, prefabricated houses/building structures, roofing and exterior cladding, curtain walling, shop fronts, etc in commercial and domestic buildings. Furthermore, aluminum extrusions are also used in transport for airframes, road and rail vehicles in marine applications[2].
In many applications, Al alloys are replaced by composites for their improved properties; the particle dispersed composites made by the liquid metallurgy route stand a fair chance due to their easier fabrication and lower cost of production[2-4]. Use of discontinuous reinforcement minimizes the problems associated with the fabrication of continuous-reinforced metal matrix composites, such as fiber damage, microstructural heterogeneity, fiber mismatch and inter-facial reactions. For applications subjected to severe loads, or extreme thermal fluctuations, such as in automotive components, the discontinuously-reinforced metal matrix composites show near isotropic properties with substantial improvements in strength and stiffness, relative to those available monolithic materials[5]. The most common particle composite is an aluminum alloy reinforced by silicon carbide. So far, most of the alloys chosen as matrices are A356, 2xxx and 6xxx series alloys. Few studies reported the 7xxx series alloys reinforced by silicon carbide particles, even less attention was given to the 7xxx series Al alloy matrix composites which show the highest strength of commercially available Al alloys and was widely used for structural applications[6-7]. Stronger matrix alloys tend to produce stronger composites. However, within these composite systems there are variables, such as ageing condition, mass or volume fraction of particles and particle size, which exerts an influence on mechanical properties. Most work on Al-based metal matrix composites (MMCs) is based on the cast products[8-13]. In this work, an Al-alloy and its composite were extruded under identical conditions and the effect of both extrusion and composite on microstructure, hardness and sliding wear behaviour properties of the alloy was correlated. Additional benefits of extrusion attained in the composite were discussed by comparing the properties of the composite and the alloy in the cast condition.
2 Experimental
2.1 Material
7075 alloy was selected for the study. The chemical composition of the alloy was analysed to be Al-1.6%Cu- 2.5%Mg-5.6%Zn-0.3%Cr using a SPARKMET optical spectrometer.
2.2 Composites and homogenization
The composites were prepared by liquid metallurgy technique. To prepare composites from these alloys, 10% (volume fraction) SiC dispersoids with size between 10-20 μm were used. The alloys were melted in a gas fired furnace in a graphite crucible and then fluxed with Coveral 11 and degassed with dry nitrogen gas. Coveral is a skimming flux suitable for all types of aluminium alloys added in proportionate quantity of the melt (1.0 kg/m2 of melt surface is added). It was thoroughly sprinkled onto the metallic melt surface evenly to provide a continuous layer and left for 3-4 min to react, then stirred. This process produces ash-like dross that is easily separated from the liquid metal. Thus, skimming is facilitated and the melt loss due to aluminium entrapment in the dross is reduced.
The preweighed and preheated dispersoids were poured into the melt after passing through a sieve. During insertion of the dispersoids, the melt was stirred constantly by a stirrer placed in the melt operated by a motor. The stirring speed was controlled as required. After complete insertion of the dispersoids in the molten alloy, the alloy was simultaneously stirred and heated for a certain time at a certain temperature. The melt with dispersoids were then poured into preheated permanent moulds of required size and shape.
For homogenization, the alloys and composites were heated at 490 °C for 8 h and water quenched. The quenched samples were heat treated at 120 °C for 24 h and furnace cooled corresponding to T6 ageing.
2.3 Extrusion of alloys and composites
The optimized condition for extruding the homogenized alloy and composite was respectively determined from the load required for extrusion at a billet soaking temperature of 350-375 °C and soaking time of 2 h; however, the tonnage required for extrusion of the composites is nearly two times that of the alloy. In the present study, both the alloy and composite were extruded at 350 °C.
2.4 Metallographic polishing and etching
Samples with a diameter of 20 mm were polished by conventional polishing techniques and then etched to reveal the phase constituents using Kellar’s reagent of composition: 2 mL HF, 3 mL HCl, 5 mL HNO3 and 190 mL H2O. The microstructure of the sample was observed along both the longitudinal and transverse direction with optical microscope and scanning electron microscope operating at 20 kV.
The following properties were evaluated and compared between the extruded alloys and composites.
Hardness was tested on the Vicker’s scale using a diamond indentation on a Leica VMHT 30A tester. The indentation was produced using 136° square base Vickers diamond pyramid with a load of 4.9 N.
Sliding wear tests were carried out on a vertical pin-on-disc wear testing machine with loads of 29.4 and 49 N and speeds of 400 and 640 r/min corresponding to 2.512 and 4.019 m/s, respectively. The mass of the sample was taken before the test and after every 500 m sliding distance. The mass loss was calculated as the difference between the initial mass and the mass after the specified distance was traversed. The volume loss was calculated from the mass loss and the density can be determined by Archimedes’ principle. The wear rate was calculated from the volume loss and sliding distance. The volume loss and wear rate were used for comparing the sliding wear behaviour of the samples.
The worn surface of the samples was observed by SEM to understand the mechanism of wear removal, surface damage and the wear mechanism prevalent in each case.
3 Results and discussion
3.1 Microstructure
The cast alloy in the homogenized condition shows a granular structure with grains of varied size and distribution of very fine phases in the grains of aluminium matrix resulting from nonuniform solidification rates during casting (see Fig.1(a)). The extrusion direction is along the longitudinal direction and the grain structure is completely broken down as shown in Fig.1(b). The cast composite exhibits a nearly uniform distribution of the particles within the matrix and clear dendrites are seen in the matrix of aluminium in Fig.1(c). The extrusion directionality and the uniform distribution of particles are also observed. In the transverse section of the extruded composite, particles can be seen distributed uniformly in the matrix as shown in Fig.1(f). A few particles (dispersoids) are seen conglomerated in the extruded condition.
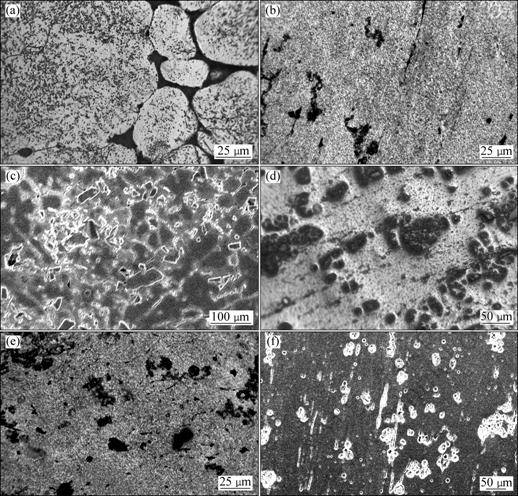
Fig.1 SEM images of alloy and composite: (a) Cast and homogenized alloy; (b) Extruded alloy in longitudinal direction; (c) Cast composite; (d) Extruded composite in longitudinal direction; (e) Extruded alloy in transverse direction; (f) Extruded composite in transverse
3.2 Hardness
The hardness of the composites is drastically increased by nearly 40% and extrusion of them further increases the value by 10% due to the strain strengthening during the process, as shown in Table 1.
3.3 Sliding wear behaviour
The sliding wear properties are compared between the extruded and cast alloys and composites. It is noticeable that the extruded alloy seizes itself at 9.8 N load at both sliding speeds (see Fig.2). At 400 r/min, the seizure was reflected in a marked increase in the volume loss at sliding distance of around 2 000 m, after which tests were discontinued. At a higher rotation speed, a similar seizure occurred at a slightly higher sliding distance, because the faster movement results in lower contact time and less material degradation. Since the extruded alloy seized at 9.8 N load and both speeds of rotation, tests for the alloy were not carried out at higher loads. It is interesting to note that at a load of 9.8 N, the volume loss after a sliding distance of approximately 2 000 m becomes nearly the same irrespective of the rotation speed for the extruded composite (see Figs.2 and 3). The effect of speed seems to be more pronounced on material loss for the extruded composite as seen in Fig.3. Higher speed results in less material loss under a constant load whereas more load results in higher material loss under the same rotation speed, as shown in Figs.4 and 5.
Table 1 Hardness of alloy and composites
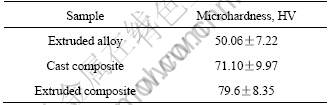
The microstructures of final worn surface after the tests, that is either after seizure or traversing a sliding distance of 3 000 m are shown in Fig.6. It is seen that there is less volume loss on the worn surface by lower degradation of the surface and less material conglomeration between wear tracks and thinner wear tracks. In cases where the volume loss is more, the surface degrades more and the disintegrated particles are found to be scattered on the surface (see Fig.6), which provides more opportunities for higher material loss at further sliding distances if tests were carried out. Seizure is seen by metal flow cut across wear tracks, the seized material in turn does not show any structure which looks like a lump of mass on the surface (see Fig.6(e)). The material from the inner surface is also exposed (Fig.6(f)).
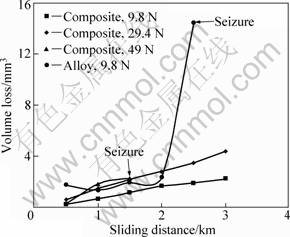
Fig.2 Variation of volume loss with sliding distance for alloy and composites at rotation speed of 400 r/min at different loads
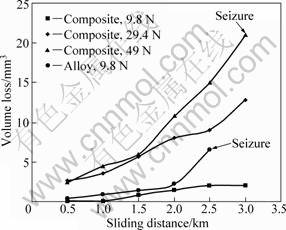
Fig.3 Variation of volume loss with sliding distance for alloy and composites at rotation speed of 640 r/min at different loads
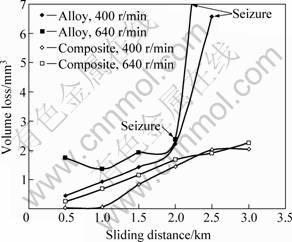
Fig.4 Variation of volume loss with sliding distance for alloy and composite at load of 9.8 N at different rotation speeds

Fig.5 Variation of volume loss with sliding distance for composite at different loads and rotation speeds
4 Conclusions
1) The hardness of the composites drastically increase by nearly 40% compared with the Al matrix and the extrusion of them further increases the hardness value by 10%.
2) The advantages of composites are realized even at the minimum applied load where the alloy seizes, but the composites in both the cast and extruded state do not seize even at long sliding distances.
3) The effect of sliding speed is more pronounced on material loss for the extruded composite than the applied load.
4) Under all conditions, the extruded composites fare much better in terms of lower material loss than their cast counterparts.
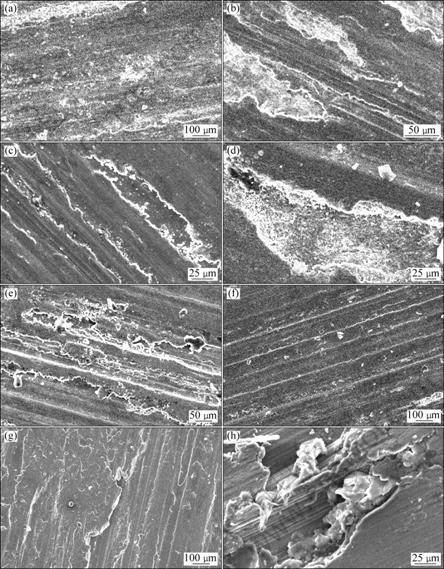
Fig.6 Worn surfaces of extruded composites and alloys under different experimental conditions: (a) Composite, 9.8 N, 400 r/min; (b) Composite, 9.8 N, 640 r/min; (c) Composite, 29.4 N, 400 r/min; (d) Composite, 49 N, 400 r/min; (e) Composite, 29.4 N, 640 r/min; (f) Composite, 49 N, 640 r/min; (g) Alloy, 9.8 N, 400 r/min; (h) Alloy, 9.8 N, 640 r/min
References
[1] HATCH J E. Aluminium properties and physical metallurgy [M]. Ohio: Metals Park, 1984: 2.
[2] SURAPPA M K. Aluminium matrix composites: Challenges and opportunities [J]. Sadhana, 2003, 28(1/2): 319-334.
[3] NUESBAUM. New Application for Al based MMC [J]. Light Metal Age, 1997, 55: 54.
[4] ZEDALIS M S, CILMAN P S, DAS S K, WARRENDALE P A. High performance composites for the 1990’s [M]. The Metallurgy Society of AIME, 1990: 61.
[5] SHAKESHEFF A J, PURDUE G. Designing metal matrix composites to meet their target: particle reinforced al alloys for missile applications [J]. Material Science and Technology, 1998, 14: 851-856.
[6] PITCHER P D, SHAKESHEFF A J, LORD J D. Aluminum based metal matrix composites for improved elevated temperature performance [J]. Material Science and Technology, 1998, 14: 1015-1023.
[7] MILLER W S, HUMPHREYS J. Strengthening mechanisms in metal matrix composites [C]// GUNGAR M N, LIAW P K. Fundamental relationship between microstructures and mechanical properties of metal matrix composites. 1994: 517-541.
[8] SHIN K S, CHUNG D S, LEE S H. The effect of consolidation temperature on microstructure and mechanical properties in powder metallurgy-processed 2××× aluminum alloy composites reinforced with SiC particle [J]. Metallurgical and Materials Transactions A, 1997, 28: 2625-2636.
[9] SINGH M, MONDAL D P, DASGUPTA R, JHA A K. Combined effect of load abrasive size and sliding distance on the high stress abrasive wear behaviour of an Al-alloy-10% granite particle composite[J]. Aluminium Transactions, 2000, 3(1): 7-15.
[10] SRIVATSAN T S. Microstructure, tensile properties and fracture behaviour of aluminium alloy 7150 [J]. Journal of Materials Science, 1992, 27: 4772-4781.
[11] TJONG S C, MA Z Y. Steady state creep deformation behaviour of SiC particle reinforced 2618 aluminium alloy based composites [J]. Materials Science and Technology, 1999, 15: 429-436.
[12] MA Z Y, LIANG Y N, ZHANG Y Z, LU Y X, BI J. Sliding wear behaviour of sic particle reinforced 2024 aluminium alloy composites [J]. Materials Science and Technology, 1996, 12: 751-756.
[13] ROHATGI P K. Metal matrix composites [J]. Journal of Defense Science, 1993, 43(4): 323-349.
(Edited by FANG Jing-hua)
Corresponding author: R. DASGUPTA; Tel: +91-755-2485078; Fax: +91-755-2457042; E-mail: dasguptarupa@gmail.com
DOI: 10.1016/S1003-6326(10)60633-4