
Characterization of plasma electrolytic oxide formed on AZ91 Mg alloy in KMnO4 electrolyte
Duck-Young HWANG1, Ki-Ryong SHIN1, Bongyoung YOO1,
Dong-Heon LEE, Deok-Yong PARK2, Dong-Hyuk SHIN1
1. Department of Metallurgy and Materials Science, Hanyang University, Ansan,426-791, Korea;
2. Department of Applied Materials Engineering, Hanbat National University, Daejon, 305-719,Korea
Received 18 June 2008; accepted 10 March 2009
Abstract: The aim of this work is to investigate microstructure, corrosion resistance characteristics and nanohardness of the oxide layer on AZ91 Mg alloy by applying different voltage with KMnO4 contained solution. There are lots of closed pores that are filled with another oxide compound compared with the typical surface morphology with pore coated until 350 V of coating voltage. The thickness of oxide layer increases with increasing coating voltage. The oxide layer formed on AZ91 Mg alloy in electrolyte with potassium permanganate consists of MgO and Mn2O3. Corrosion potential of the oxide layer on AZ91 Mg alloy obtained at different plasma electrolytic oxidation(PEO) reaction stages increases with increasing coating voltage. The corrosion resistance of AZ91 Mg alloy depends on the existence of the manganese oxide in the oxide layer. The inner barrier layer composed of the MgO and Mn2O3 may serve as diffusion barrier to enhance the corrosion resistance and may partially explain the excellent anti-corrosion performance in corrosion test. Nanohardness values increase with increasing coating voltage. The increase in the nanohardness may be due to the effect of manganese oxide in the oxide layer on AZ91 Mg alloy coated from electrolyte containing KMnO4.
Key words: magnesium alloy; plasma electrolytic oxidation; corrosion; nanohardness; potassium permanganate
1 Introduction
Plasma electrolytic oxidation(PEO) is one of the most prospective methods of surface treatment which could improve the corrosion resistance of Mg alloys[1]. The most important feature of PEO is plasma discharge that occurs at the interface between metal and electrolyte when the applied voltage exceeds a critical point. The microstructure and other properties of oxide layer obtained by PEO process depend on the processing conditions, including bath condition, current density, and alloy composition of substrate[2-4]. Especially, corrosion protection capability of oxide layers is highly relied on the chemical composition of electrolyte. Therefore, it is imperative to select proper electrolyte composition for improving the corrosion resistance of Mg alloys. Manganese is known to have a beneficial effect on the passivity of magnesium[5]. Some researchers have studied the non-chromate treatments that use acids and potassium permanganate in order to find effective substitutes for chromate treatments. ZHANG et al[6] proposed a permanganate-based bath, which improved the corrosion resistance of AZ91D. UMEHARA et al[7] also used permanganate, incorporated with HNO3 or HF, as the constituents for the conversion treatment. However, there is lack of detailed studies concerning the role of manganese on oxide layer of Mg alloys coated by PEO process. The aim of this work is to investigate microstructure, corrosion resistance characteristics and nanohardness of the oxide layer on AZ91 Mg alloy by applying different PEO reaction stages with KMnO4 contained solution.
2 Experimental
Chemical composition of AZ91 alloy used in this study was analyzed to be 8.29% Al, 0.83% Zn, and 0.31% Mn (mass fraction). AZ91 Mg alloy plate with 2 mm in thickness was cut into samples of 30 mm×50 mm. PEO process was conducted with 20 kW power supply, which had a glass-vessel container as the electrolyte cell with a sample holder. A stainless steel was used as the cathode, and stirring and cooling system were equipped to maintain the stable electrolyte temperature. Temperature of electrolyte was maintained at 20-30 ℃ during PEO process. Applied current density was controlled at 5 A/dm2. The specimens were PEO-coated in an electrolyte constituted by 0.18 mol/L potassium hydroxide, 0.09 mol/L potassium fluoride, 0.08 mol/L sodium silicate and 0.07 mol/L potassium permanganate. Surface morphology and cross-sectional image of the oxide layer were observed using a scanning electron microscope (HITACHI, S-4800), coupled to energy dispersive X-ray spectroscope(EDS). Cross-sectional TEM (TECHNAI G2 instrument) was used to characterize the oxide layer (30 nm-thick) formed on AZ91 Mg alloy. Samples for TEM observation were prepared using focused ion beam (FIB) milling. For surface chemical analysis, X-ray photoelectron spectroscopy(XPS) was performed with ESCA(PHI 5800) system. Potentiodynamic polarization to evaluate corrosion resistance of the coated AZ91 Mg alloy was carried out in 3.5% NaCl solution using potentiostat (Reference 600, Gamry Instruments). Nanoindentation test was performed to a peak load of 5 mN at constant strain rate of 0.2 s-1 using Nanoindenter- XP (MTS, Corp., Oak ridge, TN, USA) with a common Berkovich indenter.
3 Results and discussion
Fig.1 shows the surface morphologies of oxide layer in AZ91 Mg alloy obtained at different PEO reaction stages. The surface of the sample treated until 150 V exhibits dense and small pore sizes, as shown in Fig.1(a). The traces of scratches formed during mechanical polishing before PEO process is observed. The oxide layer seems to be very thin with thickness of about 2 μm because the traces of scratches are still visible. When the cell potential is not too high (150 V), these reactions will uniformly take place on the magnesium electrode in alkaline permanganate solution. After being treated until 250 V, the sample surface represents many evident micro-pores and typical surface morphology with pore for PEO process is formed (Fig.1(b)). As the coating voltage increases, the sample shows less dense pores and larger pore sizes. As cell potential reaches 350 V, plasma spark discharge becomes much bright with stronger intensity. There are lots of closed pores which are filled with another oxide compound compared with the typical surface morphology with pore for PEO process. Interestingly, the color of oxide layer on AZ91 Mg alloy turns from gray to brown, when KMnO4 is added in electrolyte. As process time increases, the color of oxide layer changes to deeper brown color. From the result of the EDS analysis of the oxide layer on the surface of AZ91 Mg alloy, the component of the oxide layer in the KMnO4 solution consists of oxygen, manganese, silicon, magnesium, and aluminum, which strongly supports that manganese is successfully incorporated in oxide layer (Fig.2).
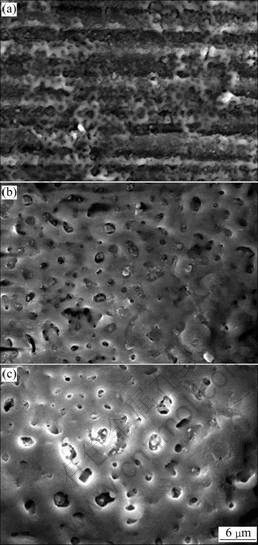
Fig.1 Surface morphologies of oxide layer of AZ91 Mg alloy obtained at different PEO reaction stages: (a) 150 V; (b) 250 V; (c) 350 V
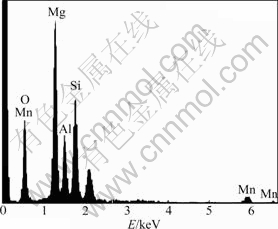
Fig.2 Energy-dispersive spectrum of oxide layer on AZ91 Mg alloy treated until 350 V of coating voltage
Fig.3 shows the variation of coating thickness with PEO reaction stage. The result indicates that total coating thickness increases gradually and the growth rate increases with increasing coating voltage. Thickness of oxide layer treated until 375 V is measured to be about 8.8 μm.
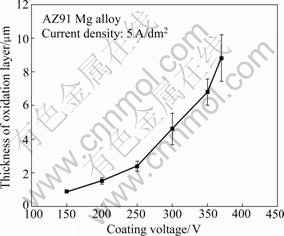
Fig.3 Variation of coating thickness with PEO reaction stage
In general, the oxide layer formed on the AZ91 Mg alloy applied in the PEO process is composed of two different layers: an outer porous layer and an inner barrier layer that is very thin layer with the thickness of 100- 300 nm[8-9].
In order to evaluate microstructure in the oxide layer in detail, the oxide layer was analyzed using cross- sectional TEM. Fig.4 shows cross-sectional TEM images of the sample coated from the electrolyte with KMnO4 until 350 V of coating voltage, which exhibits the most excellent corrosion resistance in this study. According to TEM observation in Fig.4(a), it is observed that the oxide layer has two layers. The outer porous layer consists of mainly amorphous structure as shown in Fig.4(b). It is deduced that the melted magnesium ejected out of the channel by occurring spark are cooled rapidly due to their immediate contact with the electrolyte. On the other hand, crystalline structure mainly exists in the barrier layer. Also no pore is observed in the dense barrier layer as shown in Fig.4(c). By comparing Fig.4(b) with Fig.4(c), the SAD pattern in the outer layer (Fig.4(b)) is dim, indicating amorphous structure, while the spot pattern in inner layer (Fig.4(c)) is more distinct, indicating nanocrystalline oxide rather than amorphous oxide. Therefore, it is clear that the microstructure of the inner layer is close to nanocrystalline MgO from SAD pattern. It is known from Fig.4(c) that the substrate and inner layer are compatible each other and no pore is observed.
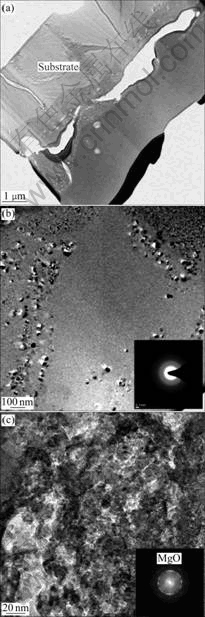
Fig.4 TEM micrographs of oxide layer coated from electrolyte containing KMnO4 until 350 V of coating voltage: (a) Bright field image of oxide layer; (b) Bright field image for porous layer; (c) Bright field image for barrier layer
In order to analyze phases existing in the oxide layer coated from electrolyte containing KMnO4, X-ray photoelectron spectroscopy(XPS) was performed. An XPS survey spectrum of the oxide layer in an AZ91 Mg alloy coated with the electrolyte containing KMnO4 until 350 V is shown in Fig.5. The oxide layer is composed of manganese, magnesium, oxygen, aluminum, fluorine, silicone, and zinc. To observe the chemical condition (binding condition) of elements in the surface layer, an individual spectrum is respectively measured for Mg 2p3/2 and Mn 2p3/2 to clarify the reacting products in the oxide layer formed in the electrolyte with KMnO4. From the Mg 2p3/2 analysis (Fig.6(a)), it can be found that magnesium takes the form of MgO showing the binding energy of 50.4 eV. The binding energy of 641.4 eV analyzed by XPS spectra (Fig.6(b)) indicates the formation of Mn2O3. It is deduced that Mn2O3 may be produced in the anodic reaction through the decomposition of the electrolyte containing manganese ions (MnO4-) during the PEO process. It is considered that manganese in the electrolyte has poor reaction for magnesium and dominantly reacts with oxygen by impact ionization and exists as manganese oxide in the oxide layer rather than magnesium-manganese compound. The evidence for the mentioned reaction is evident, because the peak of manganese oxide is detected in XPS analysis and surface color of the oxide layer is brown compared with white color of oxide layer coated from the electrolyte without KMnO4.
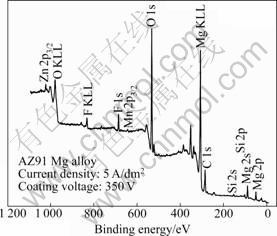
Fig.5 XPS spectrum of oxide layer on AZ91 Mg alloy coated from electrolyte containing KMnO4 until 350 V of coating voltage
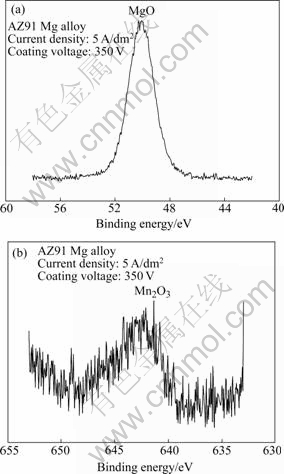
Fig.6 XPS spectra of oxide layer on AZ91 Mg alloy coated from electrolyte KMnO4 at 350 V of coating voltage: (a) Mg 2p3/2; (b) Mn 2p3/2
Corrosion resistances for the uncoated AZ91 Mg alloy and the coated AZ91 Mg alloys obtained at different PEO reaction stages are evaluated by electrochemical potentiodynamic polarization in 3.5% NaCl solution. Fig.7 exhibits the potentiodynamic polarization curve of the uncoated AZ91 Mg alloy and the coated AZ91 Mg alloys obtained at different PEO reaction stages. Corrosion potential of the oxide layer in AZ91 Mg alloy obtained at different PEO reaction stages increases with increasing coating voltage. Compared with the uncoated AZ91 Mg alloy, corrosion current density of oxide layer treated until 350 V decreases by approximately two times. The corrosion potential of the oxide layer treated until 350 V is approximately -1.35 V (vs SCE), which is much positive than that of uncoated AZ91 Mg alloy (-1.56 V). These data clearly show that the corrosion resistance with increasing the coating voltage results in the better corrosion protective property of AZ91 Mg alloy in electrolyte containing Cl- ion. It was reported that manganese oxides improved corrosion resistance when they formed on the surface of the Mg alloys[7]. This improvement of corrosion resistance with increasing the coating voltage may attribute to the effects of manganese ions on the reacting products, Mn2O3, in oxide layer formed in electrolyte containing KMnO4 by PEO process.
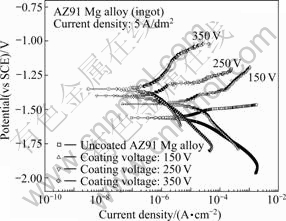
Fig.7 Potentiodynamic polarization curves of oxide layer obtained at different PEO reaction stages
From the result of the load—displacement curve of the oxide layer obtained at different PEO reaction stages, the applied load for oxide layer increases with increasing coating voltage (Fig.8(a)). The nanoindentation hardness values were calculated according to Oliver-Pharr method[10], and the results are summarized in Fig.8(b). It is known that nanohardness values increase with increasing coating voltage. Nanohardness of oxide layer treated until 350 V is measured to be about 6.68 GPa. In other words, it is considered that thickness and composition of the oxide layer play considerable influence on the hardness of oxide layer. This is the reason that the increase in the nanohardness may be due to the increase of the content of manganese into the oxide layer with increasing coating voltage.
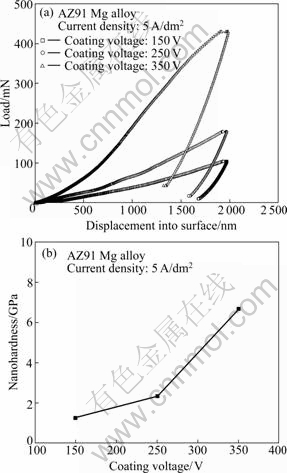
Fig.8 Nanoindentation results for oxide layer obtained at different PEO reaction stages: (a) Load—displacement curve; (b) Nanohardness with different coating voltages
4 Conclusions
PEO process of AZ91Mg alloy treated at different PEO reaction stages is investigated. The color of oxide layer on AZ91 Mg alloy turns from gray to brown, when KMnO4 is added in electrolyte. As process time increases, the color of oxide layer changes to deep brown color. The result indicates that total coating thickness increases gradually and the growth rate increases with increasing coating voltage. Thickness of oxide layer treated until 350 V is measured to be about 8.8 μm. The oxide layer formed on AZ91 Mg alloy in electrolyte with potassium permanganate consists of MgO and Mn2O3. Corrosion potential of the oxide layer in AZ91 Mg alloy obtained at different PEO reaction stages increases with increasing coating voltage. The corrosion resistance of AZ91 Mg alloy depends on the existence of the manganese oxide in the oxide layer. The inner barrier layer composed of the MgO and Mn2O3 may serve as diffusion barriers to enhance the corrosion resistance and may partially explain the excellent anti-corrosion performance in corrosion test. Nanohardness values increase with increasing coating voltage. Nanohardness of oxide layer treated until 350 V is measured to be about 6.68 GPa. The increase in the nanohardness may be due to the effect of manganese oxide in the oxide layer on AZ91 Mg alloy coated from electrolyte containing KMnO4.
Acknowledgement
The research was supported by a grant from the Center of Advanced Materials Processing(CAMP) of the 21st Centry Froniter R&D Program Funded by the Ministry of Knowledge Economy(MKE), Korea. This work was also supported by the Korea Science and Engineering Foundation (No.2009-0079807).
References
[1] YEROKHIN L, NIE X, LEYAND A, MATTEWS A, DOWEY S J. Plasma electrolysis for surface engineering [J]. Surf Coat Technol, 1999, 122: 73-93.
[2] LIANG J, GUO B, TIAN J, LIU H, ZHOU J, LIU W, XU T. Effects of NaAlO2 on structure and corrosion resistance of microarc oxidation coatings formed on AM60B magnesium alloy in phosphate-KOH electrolyte [J]. Surf Coat Technol, 2005, 199: 121-126.
[3] HSIAO H Y, TSUNG H C, TSAI W T. Anodization of AZ91D magnesium alloy in silicate-containing electrolytes [J]. Surf Coat Technol, 2005, 199: 127-134.
[4] SHI Z, SONG G, ATRENS A. Influence of anodising current on the corrosion resistance of anodised AZ91D magnesium alloy [J]. Corros Sci, 2006, 48: 1939-1959.
[5] CHONG K Z, SHIH T S. Conversion-coating treatment for magnesium alloys by a permanganate-phosphate solution [J]. Mater Chem & Physics, 2003, 80: 191-200.
[6] ZHANG H, YAO G, WANG S, LIU Y, LUO H. A chrome-free conversion coating for magnesium-lithium alloy by a phosphate- permanganate solution [J]. Surf Coat Technol, 2008, 202: 1825- 1830.
[7] UMEHARA H, TAKAYA M, KOJIMA Y. An investigation of the structure and corrosion resistance of permanganate conversion coatings on AZ91D magnesium alloy [J]. Mater Trans JIM, 2001, 42(8): 1691-1699.
[8] KHASELEV O, WEISS D, YAHALOM J. Structure and composition of anodic films formed on binary Mg-Al alloys in KOH-aluminate solutions under continuous sparking [J]. Corros Sci, 2001, 43: 1295-1307.
[9] SHI Z, SONG G, ATRENS A. Influence of the β phase on the corrosion performance of anodized coatings on magnesium- aluminium alloys [J]. Corros Sci, 2005, 47: 2760-2777.
[10] OLIVER W C, PHARR G M. An improved technique for determining hardness and elastic modulus using load and displacement sensing indentation experiments [J]. J Mater Res, 1992, 7(6): 1564-1583.
Corresponding author: Dong-Hyuk SHIN; Tel: +82-31-400-5224; E-mail: dhshin@hanyang.ac.kr
DOI: 10.1016/S1003-6326(08)60359-3
(Edited by YANG Bing)