
Treatment of stable oil/water emulsion by novel felt-metal supported PVA composite hydrophilic membrane using cross flow ultrafiltration
QIU Yun-ren(邱运仁)1, ZHONG Hong(钟 宏)1, ZHANG Qi-xiu(张启修)2
1. School of Chemistry and Chemical Engineering, Central South University, Changsha 410083, China;
2. School of Metallurgical Science and Engineering, Central South University, Changsha 410083, China
Received 13 October 2008; accepted 18 February 2009
Abstract: The novel felt-metal supported PVA composite hydrophilic ultrafiltration membrane was used for the treatment of oil/water(O/W) emulsion. The effects of transmembrane pressure(TMP), cross flow velocity, feed concentration on membrane performance were investigated, and ultrasonic cleaning of the fouled membrane was also investigated. The results show the flux increases with the increase of cross-flow velocity and TMP within the given TMP range from 0.20 MPa to 0.40 MPa. With increase of initial oil concentration increases, the oil rejection increases while the permeate flux decreases. The composite membrane shows more than 90% oil rejection within the initial oil concentration range from 0.05% to 0.50% (mass fraction) at TMP of 0.30 MPa. The fouling of the composite membrane increases rapidly during the initial 20 min at given TMP range from 0.20 MPa to 0.40 MPa, and it increases slowly after 30 min. The results also show that ultrasound is very effective in removing oil fouling of the fouled membrane, and the properties of the composite ultrafiltration membrane can be completely recovered by 10 min of sonication.
Key words: ultrafiltration; concentration polarization; membrane fouling; emulsion; polyvinylalcohol
1 Introduction
A large volume of wastewater containing oily emulsion is generated from various process industries such as metallurgical industry, cutting, transportation, food processing, petrochemical industry and petroleum refineries. The main kinds of oily wastewater are free-floating oil, unstable oil/water(O/W) emulsion and stable O/W emulsion[1]. Free-floating oil or unstable O/W emulsions can be easily removed by using conventional separation processes such as chemical, mechanical and thermal methods[2]. The chemical methods involve chemical pretreatment of emulsified oil to destabilize the emulsion followed by gravity separation, the mechanical and thermal methods primarily based on the phenomenon of gravitational and thermal emulsion breaking. However, the conventional methods for treatment of oil emulsions have several disadvantages, such as a low efficiency, operational difficulties and high operation costs. Furthermore, these conventional processes are not effective enough for removing stable O/W emulsion.
Membrane separation is a useful method for the treatment of micron sized oily wastewater. Ultrafiltration (UF) is considered to be a versatile separation method [3-5]. This pressure-driven process is widely used in the treatment of colloidal suspensions and O/W emulsions in environmental applications[6-9]. Oily water with emulsion droplets of size higher than 50 μm is in unstable state[10]. Those less than 10 μm are considered to be highly stable. So, it is very difficult to separate particularly when oil concentration is small. However, little reports on treating oily emulsion with droplets below 5 μm have been reported.
Although ultrafiltration is a suitable technique to treat oily wastewaters[11], membranes suffer severe fouling as a result of adsorption and accumulation of rejected oil and other components on the membrane surface. To minimize fouling, the cross-flow, where the feed flows parallel to the membrane surface, has been widely applied to reducing the formation of a cake layer. Several studies have reported that cross flow membrane filtration is an effective process in concentrating O/W emulsions[1,4,8,12].
Generally, organic membranes have good selectivity but poor mechanical strength, while inorganic membranes have good thermal and chemical stability, and immunity to microorganism, but poor flexibility. The novel felt-metal–PVA composite membrane has combined the good selectivity of the PVA membrane and the high mechanical strength of the felt-meta[13]. Furthermore, it can be easily reused by removing the organic layer when the composite membrane gets deteriorated. To our best knowledge, there have been less reports on felt-metal–PVA composite hydrophilic ultrafiltration membrane used in ultrafiltration of oil emulsion.
In this study, a novel felt-metal–PVA composite hydrophilic ultrafiltration membrane was used to treat stable O/W emulsion by cross-flow ultrafiltration. The effects of transmembrane pressure(TMP), flow velocity, feed initial oil concentration, and filtration time, etc., on the permeate flux and oil rejection were investigated. In addition, the cleaning of the fouled membrane by sonication was also studied.
2 Experimental
2.1 Preparation of felt-metal modified PVA composite UF membrane
The pretreated felt-metal was coated by 12%(mass fraction) polyvinyl alcohol(PVA) solution, then was heat-treated at 120 ℃ for half an hour, and the supported membrane was prepared. The felt-metal modified PVA composite UF membrane was prepared by casting PVA solution on the surface of the supported layer by phase inversion[13].
2.2 Preparation of emulsion
0.1% O/W emulsion was prepared by adding 1 g kerosene and a certain mass of Tween-20 to 1 L distilled water, then stirring for 2 min at the rate of 10 000 r/min by JRJ-300-I high-speed cutting emulsifier, and the average size of the oil droplets was about 0.3 μm. R is retention defined as follows:
(1)
where Cf and Cp are the oil concentrations of the feed and the permeate, respectively, expressed by chemical oxygen demand(COD).
2.3 Membrane characterization
Pure water flux J0 and rejection R of O/W emulsion were determined in a dead-end UF apparatus under different transmembrane pressures. The permeate flux and the oil concentration were the average values for the first 5 min, and the results are listed in Table 1, where Rm is the intrinsic resistance of the membrane.
Table 1 Properties of composite membrane
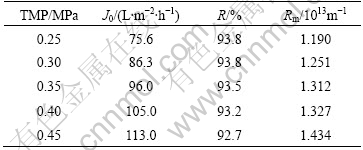
2.4 Cleaning of composite membrane
SB2200 Ultrasound Cleaner (Shanghai Binengxin Ultrasound Co. Ltd., China) was used to clean the fouled membrane, and properties of the cleaned composite membranes with different cleaning time from 3 min to 15 min were compared.
2.5 Apparatus for cross-flow ultrafiltration
Fig.1 shows schematic diagram of cross-flow ultrafiltration. One-side plate UF module was used in this experiment. The height of the channel could be adjusted from 0.025 m to 0.040 m, and the effective ultrafiltration area was 4.95×10-3 m2.
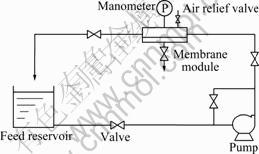
Fig.1 Schematic diagram of cross flow ultrafiltration
3 Results and discussion
3.1 Flux declination
Fig.2 shows the flux declination curves for the treatment of 0.10% O/W emulsion when the flow velocity is 0.053 m/s under different TMP from 0.25 MPa to 0.40 MPa, where w is the mass fraction of oil. The fluxes decline rapidly during the initial 20 min, and then gradually decrease, finally become almost constant with time, which is called the steady state. The flux declination is caused by pore blocking due to the existence of size distribution of membrane pores and oil droplets, settling of oil droplets on membrane surface, and concentration polarization due to the increase in retentate concentration. However, at the initial stage of the experiment, since the retentate concentration is not very high, the concentration polarization effect can be negligible[14-15]. In this case, pore blocking by oil droplets is the major factor for initial flux declination.
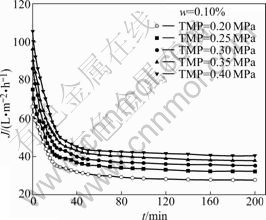
Fig.2 Flux decline curves for cross-flow ultrafiltration at different TMP
3.2 Effect of TMP on permeate flux
Fig.3 shows the effect of TMP on permeation flux at steady state for different concentrations of oily emulsions. The flux increases with the increase of TMP within the given pressure range, but the permeate flux increases a little slowly with the TMP for the emulsion with mass fraction of 0.50%, because the settling of oil droplets on membrane surface gets a little easy as oil concentration increases. The increase of permeate flux with TMP is due to the increase in driving force across the membrane. The increase of flux with TMP is not seen to be exactly linear. The reason is the existence of additional resistance due to adsorption and concentration polarization[15], and the increase of the membrane intrinsic resistance due to the increase of TMP (Table 1).
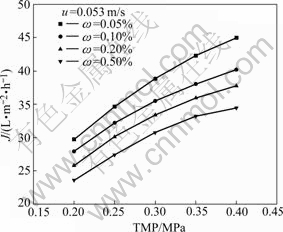
Fig.3 Effect of TMP on permeate flux at stead state
3.3 Effect of cross-flow velocity on permeate flux
The effect of cross-flow velocity on the permeate flux at TMP of 0.30 MPa is shown in Fig.4. Permeate flux increases with the increase of cross-flow velocity, because the concentration polarization decreases with the increase of the flow velocity. Another reason is that it gets a little difficult for the oil droplets adsorbed on the membrane surface as the flow velocity increases, and the membrane fouling resistance decreases with the increase of flow velocity.
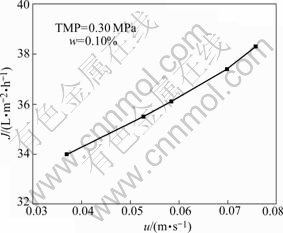
Fig.4 Effect of cross-flow velocity on permeate flux
3.4 Effect of oil concentration on permeate flux and oil rejection
The effects of feed oil concentration on the permeate flux and oil rejection are shown in Fig.5 and Fig.6, respectively. Fig.5 indicates that as initial oil concentration increases, permeate flux decreases, which may be attributed to the increase of resistance due to the formation of oil layer on the membrane surface with the increase of oil concentration. As the oil concentration increases, the oil rejection increases. Oil droplets are retained by the membrane to build up a boundary layer on the membrane surface which accumulates the oil droplets and reduces the permeate flux. An increase of oil concentration in the feed would increase the oil concentration in the boundary layer resulting in more reduction of flux and at the same time increase the oil rejection. From Fig.6, the membrane shows more than90% oil rejection within the initial oil concentration range from 0.05% to 0.50% at TMP of 0.30 MPa. At a lower oil concentration (i.e., w=0.10%), the rejection is a little low; while at a higher oil concentration (i.e., w=0.50%), the oil rejection is over 95%.
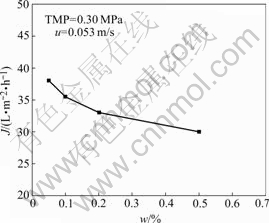
Fig.5 Effect of initial feed oil concentration on permeate flux at steady state
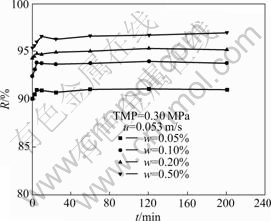
Fig.6 Effect of initial feed oil concentration on rejection
3.5 Resistance of ultrafiltration
Fig.7 shows the correlation of the total resistance (Rt) with ultrafiltration time at TMP of 0.30 MPa and 0.40 MPa, and feed velocity of 0.053 m/s. The resistance increases quickly during the initial 20 min, because the oil droplets may be adsorbed on the inner surface of the pores and on the membrane surface, which may block some pores of the membrane. As pore blocking is a very fast process, fouling resistance increases rapidly. After 30 min, the resistance increases slowly. Because the permeate flux is small, the concentration polarization resistance is relatively small compared with membrane fouling resistance. Total membrane resistance(Rt) consists of three parts, the membrane intrinsic resistance(Rm), the fouling resistance (Rf) and concen- tration polarization resistance(Rc). In the early stage of ultrafiltration, most of the oil droplets participate in the blocking by pore sealing, causing flux declination at a higher rate. As time passes, pore blocking process is gradually stopped, and the oil layer, formed by settling of oil droplets on membrane surface, begins to dominate the total membrane resistance.
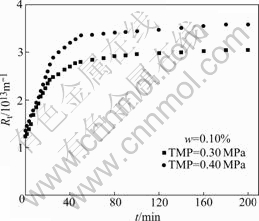
Fig.7 Total resistance of ultrafiltration with ultrafiltration time at TMP of 0.30 MPa and 0.40 MPa
3.6 Cleaning of membrane
A number of approaches are available to reduce membrane fouling, and the most common approaches are backwashing and chemical membrane cleaning. However, backwashing does not generally remove strongly adherent films or material trapped within the porous substructure of the membrane. Sonication is a possible method for cleaning membranes. When ultrasound is introduced into water, cavitation bubbles are formed, associated with ultrasound and cavitation bubbles, and acoustic streaming, microstreaming, microstreamers, microjets, and shock waves are generated, which may be capable of removing portions of the fouling layer from the membrane surface.
Fig.8 shows the effect of sonication time on the flux of the composite membrane. The cleaned membranes are used to filtrate 0.10% oily emulsion at TMP of 0.30 MPa and flow velocity of 0.053 m/s. It is indicated that ultrasound is very effective in removing oil fouling of the fouled membrane and can increase the permeate flux. The permeate flux of the cleaned membrane can increase a lot by 3 min and 6 min sonication, and the flux can completely recover by 10 min cleaning. When the cleaning time is 15 min, the flux of the cleaned membrane gets much greater than that of the new membrane, and the rejection of 0.10% oily emulsion decreases to 80.6%, as seen in Table 2. This may be caused by the damage of the composite membrane. So, the suitable sonication time is about 10 min.
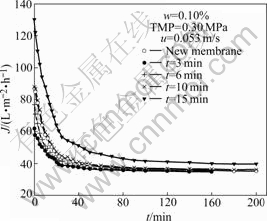
Fig.8 Effect of sonication time on flux of composite membrane
Table 2 Effect of sonication time on rejection of composite membrane

Sonication can supply sufficient agitation energy to the composite membrane to remove the adsorbed oil from the membrane surface and membrane pores, andcavitation phenomena produced by the ultrasonic wave may help to displace the cake on the membrane structure which in turn promotes fouling prevention and facilitates improved separation rates[16-18].
4 Conclusions
1) The novel prepared felt-metal supported PVA composite hydrophilic ultrafiltration membrane is used for the treatment of O/W emulsion. The permeate flux increases with the increase of TMP within the given pressure range from 0.20 MPa to 0.40 MPa; the flux increases with the increase of cross-flow velocity and decreases with the increase of the oil concentration.
2) The composite membrane shows more than 90% oil rejection within the initial oil concentration range from 0.05% to 0.50% at TMP of 0.30 MPa, and the oil rejection is over 95% for the treatment of 0.50% O/W emulsion.
3) The fouling of the composite membrane increases rapidly during the initial 20 min at given TMP from 0.20 MPa to 0.40 MPa, and increases slowly after 30 min.
4) Ultrasound is very effective in removing oil fouling of the fouled membrane, and the properties of the composite UF membrane can be completely recovered by 10 min sonication.
References
[1] UM M J, YOON S H, LEE C H, CHUNG K Y, KIM K Y. Flux enhancement with gas injection in crossflow ultrafiltration of oily wastewater [J]. Water Res, 2001, 35(17): 4095-4101.
[2] HOSNY A Y. Separating oil from oil-water emulsions by electroflotation technique [J]. Sep Technol, 1996, 6(1): 9-17.
[3] ZHONG J, SUN X, WANG C. Treatment of oily wastewater produced from refinery processes using flocculation and ceramic membrane filtration [J]. Sep Purif Technol, 2003, 32(1/3): 93-98.
[4] BODZEK M, KONIECZNY K. The use of ultrafiltration membranes made of various polymers in the treatment of oil-emulsion wastewater [J]. Waste Manage Res, 1992, 12(1): 75-84.
[5] KARAKULSKI K, KOZLOWSKI A, MORAWSKI A W. Purification of oily wastewater by ultrafiltration [J]. Sep Technol, 1995, 5(4): 197-205.
[6] HAMZA A, PHAM V A, MATSUURA T, SANTERRE J P. Development of membranes with low surface energy to reduce the fouling in ultrafiltration applications [J]. J Membr Sci, 1997, 131(1/2): 217-227.
[7] BENITO J M, EBEL S, GUTIERREZ B. Ultrafiltration of a waste emulsified cutting oil using organic membranes [J]. Water Air Soil Pollut, 2001, 128(1/2): 181-195.
[8] FAIBISH R S, COHEN Y. Fouling-resistant ceramic-supported polymer membranes for ultrafiltration of oil-in-water microemulsions [J]. J Membr Sci, 2001, 185(2): 129-143.
[9] BULLON J, CARDENAS A, SANCHEZ J. Emulsion filtration through surface modified ceramic membranes [J]. J Dispersion Sci Technol, 2002, 23(1/3): 269-277.
[10] GRYTA M, KARAKULSKI K. The application of membrane distillation for the concentration of oil-water emulsions [J]. Desalination, 1999, 121(1): 23-29.
[11] CHERYAN M, RAJAGOPALAN N. Membrane processing of oily streams: Wastewater treatment and waste reduction [J]. J Membr Sci, 1998, 151(1): 13-28.
[12] LIN S H, LAN W J. Waste oil/water emulsion treatment by membrane processes [J]. J Hazard Mater, 1998, 59(2/3): 189-199.
[13] QIU Yun-ren, ZHANG Qi-xiu. Preparation of felt-metal supported modified polyvinyl alcohol composite hydrophilic ultrafiltration membrane [J]. J Cent South Univ Technol, 2005, 12(4): 448-452.
[14] OHYA H, KIM J J, CHINEN A, AIHARA M, SEMENOVA S I, NEGISHI Y. Effects of pore size on separation mechanisms of microfiltration of oily water using porous glass tubular membrane [J]. J Membr Sci, 1998, 145(1): 1-14.
[15] KOLTUNIEWIZ A B, FIELD R W. Process factors during removal of oil-in-water emulsions with cross-flow microfiltration [J]. Desalination, 1996, 105(1/2): 79-89.
[16] LAMMINEN M O, WALKER H W, WEAVERS L K. Mechanisms and factors influencing the ultrasonic cleaning of particle-fouled ceramic membranes [J]. J Membr Sci, 2004, 237(1/2): 213-223.
[17] CHAI G Y, GREENBERG A R, KRANTZ W B. Ultrasound, gravimetric, and SEM studies of inorganic fouling in spiral-wound membrane modules [J]. Desalination,2007, 208(1/3): 277-293.
[18] MUTHUKUMARAN S, YANG K, SEUREN A, KENTISH S, ASHOKKUMAR M, STEVENS G W, GRIESER F. The use of ultrasonic cleaning for ultrafiltration membranes in the dairy industry [J]. Sep Purif Technol, 2004, 39(1/2): 99-107.
Foundation item: Project(20776161) supported by the National Natural Science Foundation of China
Corresponding author: QIU Yun-ren; Tel: +86-731-8876675; E-mail: csu_tian @mail.csu.edu.cn
DOI: 10.1016/S1003-6326(08)60348-9
(Edited by YANG Hua)