Ag-Cu-Ti-(Ti+C)反应-复合钎焊SiC陶瓷和Ti合金的接头组织
林国标1, 黄继华1, 张建纲1, 刘慧渊1, 毛建英2, 李海刚2
(1. 北京科技大学 材料科学与工程学院, 北京 100083;
2. 中国航天科技集团公司 第一研究院703所, 北京 100076)
摘 要: 研究用合金化Ag-Cu-Ti粉、 Ti粉、 C粉组成的混合粉末真空无压钎焊再结晶SiC陶瓷和Ti合金, 采用X射线衍射、 扫描电镜和能谱仪对接头的组织结构进行了分析。 结果表明: 在67.6%Ag-26.4%Cu-6%Ti(质量分数)粉末中加入相当于15%~30%TiC(体积分数)的(Ti+C)粉末(Ti与C摩尔比为1∶1), 经920℃, 30min真空钎焊, Ti和C原位合成TiC, 形成以TiC晶粒强化的连接良好的复合接头; 形成的TiC分布于Ag相、 Cu-Ti相中; TiC的形成明显降低了接头的热应力。 过量的(Ti+C)粉末则导致反应不完全, 容易在连接层中产生孔洞, 影响接头强度; 焊接过程中, Ti由钛合金扩散进入连接层, Cu也有部分从连接层中扩散进入钛合金。
关键词: SiC陶瓷; Ti合金; 原位合成TiC; 连接; 复合钎焊 中图分类号: TG407
文献标识码: A
Microstructure of reactive composite brazing joints of SiC ceramics and Ti alloy by using Ag-Cu-Ti-(Ti+C) as bonding material
LIN Guo-biao1, HUANG Ji-hua1, ZHANG Jian-gang1,LIU Hui-yuan1, MAO Jian-ying2, LI Hai-gang2
(1. School of Materials Science and Engineering, University of Science and Technology Beijing,Beijing 100083, China;
2. 703 Institute of the First Academy, China Aerospace Science and Technology Corporation,Beijing 100076, China)
Abstract: By using the mixed powder of Ti, C (mole ratio of Ti to C is 1∶1) powders for in-situ synthesizing TiC in 15%-30%TiC (volume fraction) and alloying 67.6%Ag-26.4%Cu-6%Ti (mass fraction) powder as vacuum non-pressure brazing material, sound brazed joints of SiC ceramics /Ti alloy were acquired at 920℃ for 30min. The joints were investigated by X-ray diffractrometry, scanning electron microscopy, and energy dispersive spectrometry. The results show that TiC grains are in-situ synthesized and distribute in Ag and Cu-Ti phases of the bonding layers, distinctly lowering the thermal stress of the joints. However, excess amount of (Ti + C) powder easily brings about the formation of pores and incomplete reactions of Ti and C in the bonding layers, which are detrimental to the joints strengths. During brazing process, Ti element in Ti-alloy and Cu element in the bonding layer interdiffuse.
Key words: SiC ceramics; Ti-alloy; in-situ synthesizing TiC; bonding; composite-brazing
SiC陶瓷具有优异的高温强度、 良好的耐腐蚀抗氧化及耐磨性能, 是应用于高温场合的一种重要的材料, 其中烧结SiC陶瓷性能较高, 反应烧结SiC陶瓷次之, 再结晶SiC陶瓷由于没有加入反应助剂性能较低。 与其它陶瓷材料一样, SiC类陶瓷也存在延性和冲击韧性低、 加工性能差等缺点。 为了充分发挥陶瓷和金属的性能优势, 有时需要进行SiC陶瓷与金属的连接, 如在航空航天领域具有重要的应用价值SiC陶瓷与钛合金的可靠连接。 目前, SiC陶瓷与金属的连接方法主要有扩散焊 [1-3]和钎焊[4, 5]。 扩散焊需要焊接件、 中间层表面光滑平整, 且需要较高的焊接压力以实现原子间距的结合和扩散, 这些要求使得扩散焊的使用范围受到局限, 如难以对复杂构件进行焊接。 钎焊可在无压或小压力下进行焊接, 为便于施加, 使用粉末状钎料应较易实现复杂构件的连接。 因此研究使用粉末状钎料, 在无压或小压力下钎焊连接SiC陶瓷和金属应具有更广阔的应用前景。 目前, 对SiC陶瓷和金属的钎焊连接多选用Ag-Cu-Ti活性钎料, 如连接烧结SiC陶瓷和TiAl合金[4]、 Cu、 Zn[5], 并借用一些扩散焊的手段, 如将焊接面表面抛光、 使用合金化的箔状钎料、 施加一定的焊接压力。 也有研究用Ni、 Ti、 C粉末压坯自蔓延高温合成(SHS)连接再结晶SiC陶瓷与Ni基高温合金[6, 7], 发现由于两种受焊母材的热膨胀系数不匹配在焊接过程中产生的热应力, 导致接头强度很低, 甚至连接失败。 总得来说, 目前研究的SiC陶瓷和金属钎焊连接过程尚未完全显示钎焊的优势, 且普遍存在两个重要问题: 一是钎焊接头高温性能较差; 二是陶瓷和大部分金属连接所共同面临着的热应力问题。 基于这些方面考虑, 本文作者探索研究在合金化的Ag-Cu-Ti粉末中加入Ti粉和C粉连接再结晶SiC陶瓷和钛合金, 以期在钎焊过程中原位合成低膨胀系数的陶瓷增强相TiC, 由于原位合成比直接加入陶瓷增强相应与基体有更好的结合, 一般不存在润湿性问题, 这样一方面可以缓解陶瓷与金属的热膨胀失配, 降低接头的热应力; 另一方面, 借助陶瓷增强相的强化, 以提高接头的高温性能。
1 实验
焊接母材为市售的再结晶SiC陶瓷与TC4钛合金。 再结晶SiC的密度为2.60~2.70g/cm3, 气孔率为15%~16%, 纯度大于99%, 室温抗弯强度80~90MPa, 尺寸为30mm×25mm×7mm的方块。 TC4钛合金的组分为Ti-6Al-4V(质量分数, %), 钛合金直径为15mm的棒状。 钎焊所使用的合金化粉末钎料成分为67.6%Ag-26.4%Cu-6%Ti(质量分数), 平均粒度1.1μm。 Ti粉平均粒度1.5μm, 纯度均大于99.9%。 C粉为胶体石墨粉, 平均粒度为7μm, 水分含量低于0.5%(质量分数)。
将棒状钛合金切割成5mm厚的圆柱体, 焊接面用60#砂纸研磨, 以除去表面氧化层, 与SiC陶瓷块一起用酒精清洗干净。 在Ag-Cu-Ti合金粉末中, 根据TiC的密度及Ag-Cu-Ti粉末中每种组分的密度, 计算加入相当于一定量TiC体积分数的(Ti+C)粉, Ti与C的摩尔比为1∶1。 将配好的粉末加分散剂、 连接剂, 研磨、 混合均匀成膏状, 涂在SiC陶瓷与钛合金之间, 控制好焊料预置间隙, 用一高比重合金压在上面以固定相对位置, 压力约为2.2×10-3MPa。 钎焊连接在多功能真空钎焊炉内进行, 真空度高于6×10-3Pa, 连接温度为890~920℃, 保温时间为10~30min, 升温速率10℃/min, 降温速率3℃/min。
将用于微观分析的SiC/TC4接头, 采用金刚石砂轮片和线切割沿接头的轴截面切开, 用金刚石研磨膏进行研磨、 抛光, 利用LEO-1450扫描电镜背散射相、 能谱仪进行了组织观察和成分分析。 将接头一侧的SiC陶瓷母材完全剥离并研磨后, 用X射线衍射仪对连接层进行了物相分析。
2 结果与讨论
用Ag-Cu-Ti合金粉末真空钎焊再结晶SiC陶瓷和TC4钛合金, 冷却到室温, 接头从邻近焊缝的SiC陶瓷中自行开裂。 分析其原因, 是由于金属和陶瓷的热膨胀系数不同, 所产生的较大热应力造成的[8]。 文献[6]也报道了类似的热应力作用而破坏的现象, 且实验结果证明陶瓷与金属连接的接头热应力大于陶瓷与陶瓷的接头热应力。 理论计算[9-11]和实验检测[12]均表明, 金属和陶瓷连接, 最大热应力在近连接层的陶瓷中。 再结晶SiC陶瓷强度和韧性较低, 所能承受的热应力比其他烧结类SiC陶瓷要低, 因而接头强度也会较低, 如文献[13]报道用同样方法连接的反应烧结SiC陶瓷接头获得了一定的强度, 但连接的再结晶SiC陶瓷接头强度很低。
但研究表明, 在同样的工艺条件下, 于Ag-Cu-Ti合金粉末中, 加入相当于20%~30%TiC(体积分数)的Ti和C混合粉末, 均能形成连接良好的完整接头, 热应力得到了有效地缓解, 并具有一定的接头强度。 为进一步研究, 对接头的组织结构进行了分析。
图1所示为在Ag-Cu-Ti合金粉末中加入相当于体积分数为30%TiC的(Ti+C)粉末经920℃, 30min真空钎焊连接再结晶SiC陶瓷和钛合金的接头和放大的连接层组织的背散射照片。 图2所示为连接层剖面的X射线衍射谱。 图1(a)中上部分黑色区域是SiC陶瓷, 中间为连接层, 下面为Ti合金; 图1(b)所示为连接层组织的放大相。 结合能谱和X射线衍射分析可知, 图1(a)、 (b)连接层中白色相为Ag相, 其中含少量的Cu; 颜色深浅不一的灰色基体为不同含Ti量的Cu-Ti相, 颜色深的地方含Ti量高, 由此可见图1(a) 连接层中, 靠近钛合金侧连接层含Ti 量高, 由此到连接层另一侧的含Ti量逐渐降低, 因此连接层中不同地方的Cu-Ti相含Ti量也不尽相同。 由于本实验所做的X射线衍射是垂直于图片焊缝的某一剖面, 未能涵盖整个焊缝宽度, 根据Ag-Cu-Ti三元相图[14]中可能存在的Cu-Ti相及能谱分析, 除了图2显示的Ti2Cu和Cu3Ti相, 应含有它们之间的其他不同含Ti量的相, 如CuTi、 Cu4Ti3、 Cu2Ti。 图1(c)、 (d)所示分别为连接层两代表性区域——图1(b)中A和B所指区域的放大相。 图1(c)中黑色方块及散布的黑色颗粒状, 能谱分析显示主要含Ti及部分C, 结合X射线衍射分析应为TiC; 长条状中间的黑色部分见图中所示为未完全反应剩余的C, 由于连接层含C量较少, 所以X射线衍射峰不明显; 白色和灰色的基体分别为Ag相、 Cu-Ti相。 图1(d)显示大块呈浅色的Ag相中有很多弥散分布呈黑点状的细小晶粒(小于0.2μm), 且靠近Cu-Ti相(图中黑色部分)周围比较密集, 这种细小晶粒应是反应过程中形成的。 由于Ti是一种活性元素, 不可能单独存在, 根据连接层的X射线衍射分析(图2), Ti存在形式为TiC、 Ti-Cu相; Ag相中固溶少量Cu, 经对含黑点Ag相和不含黑点Ag相的扫描电镜能谱对比分析可知, Cu含量没有明显变化, 仅Ti含量明显升高; 由于C含量很少时, 能谱难以确定, 根据上述分析,细小晶粒应为TiC。 TiC晶粒存在于Ag相中将有利于强化Ag相, 甚至提高接头的高温强度。 由图1(c)、 (d)可见, 原位合成的TiC与周围基体的
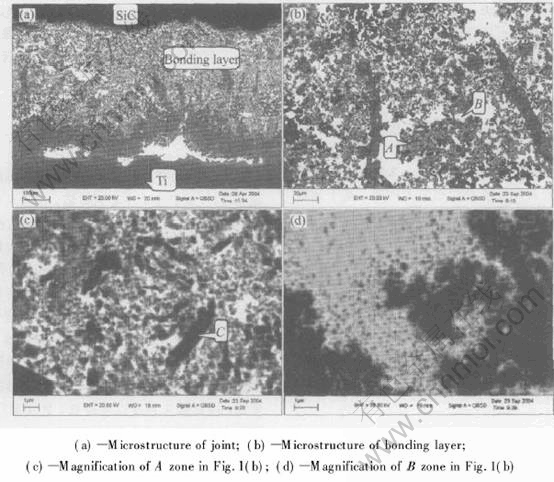
图1 Ag-Cu-Ti+30%(Ti+C)连接的接头和连接层内的SEM显微组织
Fig.1 SEM microstructures of joint brazed with Ag-Cu-Ti +30%(Ti+C) and its bonding layer
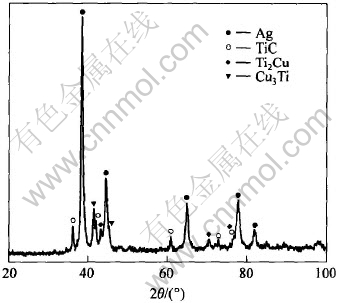
图2 连接层的X射线衍射谱
Fig.2 XRD pattern of bonding layer
边界比较模糊, 说明界面原子失配度是逐步过渡, 与基体结合比较好。
据文献[6, 7]报道, 用Ni、 Ti、 C粉末压坯在 1000~1200℃下可自蔓延高温合成TiC。 本实验表明在较低的温度下, TiC即可原位合成。 分析其形成机理, Ti、 C粉直接固态反应难以进行, 其原因是: 1) 固态反应温度很高; 2) 在混合粉末中Ti粉和C粉难以完全相互接触; 3) 也难以达到图1(d)所示的Ag相中TiC细小弥散分布。 根据Ni、 Ti、 C粉自蔓延高温合成TiC的形成机理[15]可知, 起主要作用的应是含Ti的Ag-Cu-Ti液相。 根据Ag-Cu-Ti三元相图[14], 在920℃的焊接温度下, 合金化的Ag-Cu-Ti粉末会成为液相, 将会润湿和包裹加入的Ti粉和C粉, Ti和C逐渐溶入液相中起反应形成TiC析出, 随着反应的进行, TiC不断析出, Ti和C将不断溶解。 冷却后, Ag-Cu-Ti液相转变成Ag相和Cu-Ti相, 形成TiC分布其中的组织, 如图1(c)、 (d)所示。 少量的C粉颗粒由于比较大, 心部可能反应不完全。
图1(a)中连接层衬度所显示的Ti浓度规律分布说明连接层与钛合金间存在物质交换。 图3所示为图1(a)中连接层和钛合金界面区域的背散射像。 由图可见, 钛合金界面附近形成了扩散带, 能谱分析表明, 扩散带中Ag含量极少, 主要为Ti和Cu。 在焊接过程中, Ti由钛合金扩散进入连接层, Cu则由连接层扩散进入钛合金。 根据Ti-Cu二元相图[16], Ti-Cu化合物按Ti含量由高向低排列为: Ti2Cu、 CuTi、 Cu3Ti2、 Cu2Ti、 Cu3Ti。 结合扩散规律和能谱分析, 图中扩散带中各层可区分为TC4钛合金/Ti+Ti2Cu/ Ti2Cu/CuTi/连接层(见图3)。 第一层为TC4钛合金基体; 第二层为黑色和灰色交替相间区域, 黑色相能谱分析的成分与钛合金母材成分近似, 判定为Ti相, 灰色相能谱成分分析结果与Ti2Cu成分接近, 因此应为Ti2Cu; 第三层为Ti2Cu相, 部分长入第二层中; 紧挨着的下一层, 颜色较浅, 含Ti量较低, 为CuTi相层, 附近连接层中白色为Ag相, 比基体颜色深的长条状, 能谱分析成分(摩尔分数, %)为15.84Al-50.17Ti-29.24Cu-4.74Ag, 颜色和成分均与Ti2Cu相接近, X射线衍射分析也证明连接层中有Ti2Cu相, 因此该相应为Ti2Cu相, 其中的Al来自母材TC4钛合金, 焊接时, 图3所示扩散带中原钛合金中的Al扩散溶入连接层, 冷却后分布在Ti-Cu相的组织中。
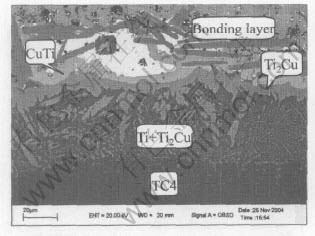
图3 Ag-Cu-Ti+30%(Ti+C)连接层与钛合金界面的SEM像
Fig.3 SEM image of interface between SiC Ti-alloy and Ag-Cu-Ti+30%(Ti+C) bonding layer
由于原子在液相中扩散快, Ti由钛合金向连接层液相扩散进入的速度应高于Cu向固相钛合金中的扩散速度, Ti的扩散进入使得钛合金侧连接层Ti浓度升高, 继而向连接层另一侧逐渐扩散; Cu扩散离开连接层使得钛合金侧连接层的Cu浓度降低, 导致连接层另一侧Cu向该处扩散, 两方面作用使得连接层内Ti/Cu浓度比形成扩散坡度, 靠近钛合金侧比值高。 冷却过程中, 连接层液相将会形成Ag相和不同含Ti量的Cu-Ti相, 相应地钛合金侧则含Ti量高。 其结果如图1(a)连接层背散射相衬度所示。
在Ag-Cu-Ti合金粉末中适量添加(Ti+C)粉所获得的连接层与钛合金形成了如图3所示的牢固的界面扩散结合, 与SiC陶瓷间也保持Ag-Cu-Ti合金对其良好润湿性、 连接性的特点, 并形成如图4所示的SiC陶瓷表面反应层, 图4所示为在Ag-Cu-Ti合金粉末中加入相当于体积分数为40%TiC的(Ti+C)粉末所获得的连接层与SiC陶瓷界面区域的放大背散射像。 电镜成分分析结果表明: 反应层主要含Si、 Ti、 C。 图4显示了随着(Ti+C)粉体积分数的增加, 连接层变得不致密, 存在较多的孔; X射线衍射分析表明连接层中有TiC、 Ti8C5、 C存在。 对比图1(a)与图4可知, 当(Ti+C)含量为30%时, 连接层基本致密, C的X射线衍射峰不明显; 当Ti和C混合粉末含量为40%时, Ti和C反应不完全现象严重, 同时形成的连接层的流动性变差, 连接层渗入再结晶SiC陶瓷母材开孔深度降低, 凝固后与再结晶SiC陶瓷形成的机械啮合作用也会降低。 因此, 过多的(Ti+C)粉可使接头强度降低。 (Ti+C)粉的添加量以15%~30%为宜。
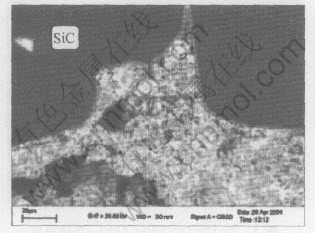
图4 Ag-Cu-Ti+40%(Ti+C)连接层与陶瓷界面区域放大相
Fig.4 Area including interface between SiC ceramics and Ag-Cu-Ti+40%(Ti+C) bonding layer
加入适量的Ti、 C粉, 大部分均原位生成TiC, 分布在连接层Ag-Cu-Ti合金基体(Ag相、 Cu-Ti相)中, 形成的接头连接良好、 完整致密。 由于TiC晶粒具有远低于金属的热膨胀系数, 通过接头中该陶瓷晶粒的复合化, 可降低连接层的热膨胀系数, 从而形成由钛合金金属到SiC陶瓷热膨胀系数逐步降低的过渡层, 致使接头的热应力降低, 连接强度得到提高; 同时TiC晶粒的形成和分布将会产生颗粒强化和弥散强化作用, 有利于提高连接层强度和接头高温性能。
3 结论
1) 在Ag-Cu-Ti合金粉末中加入适量的Ti粉和C粉, 经920℃, 30min真空钎焊连接Ti合金和再结晶SiC陶瓷, Ti粉和C粉能原位合成TiC, 形成以TiC晶粒强化的连接良好的复合接头; 形成的TiC分布于Ag相、 Cu-Ti相中; TiC的形成明显降低了接头的热应力。
2) 焊接过程中, Ti由钛合金扩散进入连接层, Cu也有部分从连接层中扩散进入钛合金, 形成了连接层与钛合金的界面扩散反应带, 以及连接层中Ti浓度的梯度分布, 靠近钛合金侧连接层含Ti量高。
REFERENCES
[1]刘会杰, 冯吉才, 钱乙余, 等. SiC陶瓷与TC4钛合金反应钎焊的研究[J]. 焊接, 1998(11): 22-25.
LIU Hui-jie, FENG Ji-cai, QIAN Yi-yu, et al. Reaction brazing of SiC ceramics to TC4 titanium alloy[J]. Welding, 1998(11): 22-25.
[2]陈明和, 张中元, 余亚平. TC4/SiC扩散焊接工艺研究[J]. 航空制造技术, 2000(1): 22-23, 46.
CHENG Ming-he, ZHANG Zhong-yuan, YU Ya-ping. Study on TC4/SiC diffusion bonding technology[J]. Aeronautical Manufacturing Technology, 2000(1): 22-23, 46.
[3]冀小强, 李树杰, 马天宇, 等. 用Zr/Nb复合中间层连接SiC陶瓷与Ni基高温合金[J]. 硅酸盐学报, 2002, 30(3): 305-310.
JI Xiao-qiang, LI Shu-jie, MA Tian-yu, et al. Jointing of SiC ceramics to Ni-based superalloy with Zr/Nb multiple interlayers[J]. Journal of the Chinese Ceramic Society, 2002, 30(3): 305-310.
[4]LIU Hui-jie, FENG Ji-cai, QIAN Yi-yu. Microstructure and strength of the SiC/TiAl joint brazed with Ag-Cu-Ti filler metal[J]. Journal of Materials Science Letters, 2000, 19(14): 1241-1242.
[5]Tamai F, Naka M. Microstructure of interface of SiC/Cu-Ag-Ti/Cu, Ni[A]. Proceeding of Designing of Interfacial Structures in Advanced Materials and Their Joints[C]. Osaka: High Temperature Society of Japan, 2002. 634-639.
[6]李树杰, 刘深, 段辉平, 等. SiC陶瓷/SiC陶瓷及SiC陶瓷/Ni基高温合金SHS焊接中的界面反应及微观结构研究[J]. 硅酸盐学报, 1999, 27(6): 757-762.
LI Shu-jie, LIU Shen, DUAN Hui-ping, et al. Reaction on the interface between SiC ceramics/SiC ceramics as well as SiC ceramics/Ni-based superalloy and the microstructure[J]. Journal of the Chinese Ceramic Society, 1999, 27(6): 757-762.
[7]孙德超, 柯黎明, 邢丽, 等. 陶瓷与金属梯度过渡层的自蔓延高温合成[J]. 焊接学报, 2000, 21(3): 44-47.
SUN De-chao, KE Li-ming, XING Li, et al. Self-propagating high-temperature synthesis of gradient transitional layer between ceramics and metal[J]. Transactions of the China Welding Institution, 2000, 21(3): 44-47.
[8]Akselsen O M. Advances in brazing of ceramics[J]. Journal of Materials Science, 1992, 27: 1989-2000.
[9]Yamada T, Satoh M, Kohno A, et al. Residual stress estimation of a silicon carbide-kovar joint[J]. Journal of Materials Science, 1991, 26: 2887-2892.
[10]雷永平, 韩丰娟, 夏志东, 等. 陶瓷与金属钎焊接头残余应力的数值分析[J]. 焊接学报, 2003, 24(5): 33-39.
LEI Yong-ping, HAN Feng-juan, XIA Zhi-dong, et al. Numerical analysis of residual stress in ceramics metal joints[J]. Transactions of the China Welding Institution, 2003, 24(5): 33-39.
[11]程大勇, 陆善平, 郭义. 陶瓷/金属钎焊接头内残余应力计算[J]. 材料研究学报, 2000, 14(增刊): 49-52.
CHENG Da-vong, LU Shan-ping, GUO Yi. The calculation of the residual stresses in C/M joint[J]. Chinese Journal of Materials Research, 2000, 14(Suppl.): 49-52.
[12]熊柏青, 楚建新. 残余热应力对Si3N4/金属钎焊接头性能的影响[J].中国有色金属学报, 1998, 8(2): 210-213.
XIONG Bai-qing, CHU Jian-xin. Effect of residual thermal stress on properties of Si3N4/metal brazing joints[J]. The Chinese Journal of Nonferrous Metals, 1998, 8(2): 210-213.
[13]李世斌, 吕振林, 高积强, 等. 反应粘接碳化硅材料接头的研究[J]. 兵器材料科学与工程, 2003, 26(1): 51-54.
LI Shi-bin1, LU Zhen-lin, GAO Ji-qiang, et al. Study on joints of reaction-bonded silicon carbide ceramic materials[J]. Ordnance Material Science and Engineering, 2003, 26(1): 51-54.
[14]Villars P, Prince A, Okamoto H. Handbooks of Ternary Alloy Phase Diagrams[M]. USA: ASM International, 1997. 2353-2359.
[15]肖国庆, 范群成, 顾美转, 等. TiC-Ni 金属陶瓷自蔓延高温合成中的显微组织转变[J]. 中国有色金属学报, 2004, 14(6): 1013-1019.
XIAO Guo-qing, FAN Qun-cheng, GU Mei-zhuan, et al. Microstructural evolution during self-propagating high temperature synthesis of TiC-Al cermet[J]. The Chinese Journal of Nonferrous Metals, 2004, 14(6): 1013-1019.
[16]虞觉奇, 易文质, 陈邦迪, 等. 二元合金状态图集[M]. 上海: 上海科学技术出版社, 1984. 574.
YU Jue-qi, YI Wen-zhi, CHEN Bang-di, et al. Handbooks of Binary Alloy Phase Diagrams[M]. Shanghai: Shanghai Scientific Press, 1984. 574.
(编辑陈爱华)
基金项目: 武器装备预研基金资助项目(51418050503QT0203); 高等学校博士学科点专项科研基金资助项目(20030008014)
收稿日期: 2005-03-14; 修订日期: 2005-07-04
作者简介: 林国标(1964-), 男, 研究员, 博士研究生.
通讯作者: 黄继华, 教授; 电话: 010-62334859; E-mail: jihuahang47@sina.com