
Rapid synthesis of Ti(C, N) powders by mechanical alloying and subsequent arc discharging
YUAN Quan1, 2, ZHENG Yong1, YU Hai-zhou1, 2
1. College of Material Science and Technology, Nanjing University of Aeronautics and Astronautics,Nanjing 210016, China;
2. College of Mechanical and Materials Engineering, China Three Gorges University, Yichang 443002, China
Received 23 July 2010; accepted 18 November 2010
Abstract: Ti(C,N) powders were synthesized by mechanical alloying (MA) from a mixture of pure titanium and graphite under a nitrogen atmosphere in a planetary mill. Effects of arc discharging on phase transformation and microstructure of MA powders milled for 1-7 h were explored. The results show that Ti(C,N) powders were prepared after mechanical milling for 1 h and subsequent arc discharge treatment, whereas the synthesis reaction did not occur in 7 h by mechanical milling alone. The ions produced during arc discharging interacted with powder particles and accelerated the diffusion of atoms and the nucleation on the surface of the as-milled powder, which results in fast synthesis of Ti(C,N) powders. The formation mechanisms of the two synthesis processes are self-propagating reactive synthesis.
Key words: Ti(C,N) powders; mechanical alloying; self-propagating reactive synthesis
1 Introduction
Ti(C,N) is a promising material with excellent properties such as high melting temperature, high hardness, good oxidation and corrosion resistance combined with good electrical and thermal conductivity [1-2]. When combined with metal binders (i.e. Ni, Co, Mo), it is a popular source powder for making cermet cutting tools and wear resistant parts. Moreover, Ti(C,N) has been widely used as a reinforcement for composites employed in mechanical, electronic and chemical industries.
Conventionally, Ti(C,N) powders are produced by high temperature solid state diffusion from TiC-TiN, high temperature nitrogen treatment of TiC and a carbonitriding reaction of Ti and carbothermal reduction of TiO2 in a nitrogen atmosphere [3-4]. In recent years, mechanical alloying (MA) attracted much attention as one of the most versatile solid-state material processing techniques for the non-equilibrium materials such as amorphous alloys, quasi-crystals, nanocrystalline solids and compounds [5-7]. ZHANG and TAM [8] prepared a Ti(C,N) solid solution from TiC (2-5 ?m) and TiN (10-20 ?m) powders by mechanical alloying for 40 h in a Fritsch P5 planetary ball mill. Ti(C,N) (about 2 ?m) and Al2O3 composite powders were prepared by ball milling for 100 h under a nitrogen atmosphere [9]. Nanosized TiB2 and TiN/Ti(C,N) mixture particles were fabricated by high-energy ball milling for 30 h and subsequent heat treatment at 1 300 °C [10]. YIN et al [11] synthesized nanocrystalline titanium carbonitride directly by reaction ball milling a mixture of Ti and C under a nitrogen atmosphere using a vibration high-energy ball mill. In our previous study, we synthesized the Ti(C,N) by mechanical alloying from titanium, graphite and titanium nitride. The reaction did not finish until the mixture was milled for 20 h, but the product was contaminated with tungsten carbide, which came from the abrasion of WC-Co milling balls [12]. SURYANARAYANA [7] and ABE and KUJI [13] reported these serious drawbacks, also. Recently, BISHOP and CALKA et al [14-15] reported that electric discharge assisted mechanical milling (EDAMM) could be an effective tool for inducing rapid reaction rates in solid-solid systems and solid-gas systems. In the present work, Ti(C,N) powder is prepared by mechanical alloying from a mixture of titanium and graphite under a nitrogen atmosphere and subsequent arc discharging. The effect of arc discharging on the phase transformation of MA powders and the reaction mechanism of synthesizing Ti(C,N) is also investigated.
2 Experimental
Titanium powders (purity 99%, <20 μm) and graphite powders (purity 99%) were used in this work. SEM images of the raw materials are illustrated in Fig. 1. These powders were mixed at a mole ratio of 1:0.7. Mechanical alloying was performed for different durations using a planetary mill (QM-1SP4) in pure nitrogen gas pressurized up to 0.4 MPa at rotational speed of 350 r/min and a ball-to-powder mass ratio of 10:1. Stainless vial and cemented carbide balls with 8 mm and 10 mm in diameter were used, respectively. The samples were then subjected to arc discharging under ?owing nitrogen in a stainless steel vessel. The time of arc discharge treatment varied from 0.5 min to 3 min. The power supply unit was a low temperature plasma power source (CTP-2000K) that generated impulses with voltages in kV range and currents in mA range. The phase structures of the powders were characterized with X-ray diffractometer (XRD) with Cu Kα radiation, operating at 40 kV and 40 mA. The powder morphology and particle size were observed by a QUANTAN200/FEI scanning electron microscope (SEM).
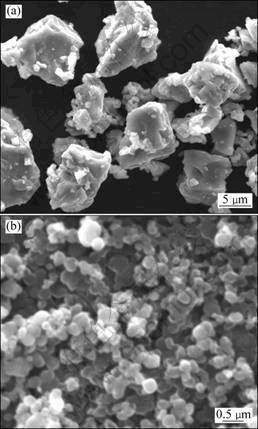
Fig. 1 SEM images of starting powders: (a) Ti powder; (b) Graphite powder
3 Results and discussion
3.1 Mechanical alloying
XRD patterns of the as-milled powders with different milling time are shown in Fig. 2. After milling for 1 h, C peaks disappeared completely and Ti diffraction peak intensity obviously decreased and broadened due to the refinement of the grains and the introduction of internal strain. The pattern of the sample milled for 4 h displayed the diffraction peaks of Ti, but shifted into lower angles. This suggests that the C and N atoms dissolved into the Ti lattice and formed supersaturated solid solutions. The peaks of Ti disappeared completely and the peaks of Ti(C,N) phase occur after milling for 8 h. Ti(C,N) is a single compound formed through a continuous solid solution of TiC and TiN. The lattice parameter of the solid solution ful?lls Vegard’s law and is related to the molar ratio between C and N and the stoichiometric lattice parameters of TiC (a(TiC)=4.327 4 ?) [16] and TiN (a(TiN)=4.247 3 ?) [17]. According to calculation, the ratio of C to N in the resultant is 0.57:0.43.

Fig. 2 XRD patterns of Ti-C mixture milled in nitrogen atmosphere for different time
SEM images of the powders milled for different time are shown in Fig. 3. At the initial stage of mechanical alloying, the titanium and graphite were not mixed homogeneously, as shown in Fig. 3(a). The light gray titanium particles with size of about 5 μm were obviously refined and adhered to the nanosized graphite (about 400 nm). In Fig. 3(b), the Ti powders had a flaky shape, and the size of particle was about 3 μm after milling for 4 h. The brittle graphite was fragmented by the ball-powder-ball collisions and trapped in the ductile Ti particles. The powders continued to refine after milling for 7 h (Fig. 3(c)). When milling up to 8 h, the particle size and morphology changed significantly, as shown in Fig. 3(d). According to the XRD analyses mentioned above, this obvious change resulted from the synthesis of Ti(C,N). The resultant Ti(C,N) powders were angular, with a size of about 6 μm.
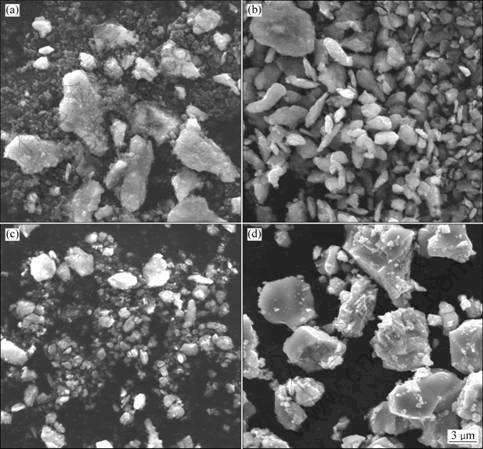
Fig. 3 SEM images of powders milled for different time: (a) 1 h; (b) 4 h; (c) 7 h; (d) 8 h
According to the empirical criteria, the mechanically induced self-propagating reaction (MSR) would not occur unless Tad (reaction adiabatic temperature) >1 800 K [18]. It was reported that the adiabatic temperatures for the formation of TiC and TiN are 3 210 K and 4 900 K, respectively [11]. It is thus reasonable to assume that the formation of the Ti(C,N) phase must be sufficiently exothermic to proceed in a self-sustaining mode when ball milling a mixture of Ti and C in a nitrogen atmosphere. In the present study, the XRD diffraction patterns (Fig. 2) shows that Ti(C,N) was synthesized in 7-8 h of milling. After milling for 8 h, the powder morphology and size changed greatly (see Fig. 3(d)). Meanwhile, an abrupt increase in the temperature of the bowl surface was detected. Furthermore, no interphase diffraction peak was observed in the whole process of mechanical alloying. Therefore, it can be concluded that the reaction was ignited after milling for 7 h and then propagated through the whole milled powders in 8 h. A phase transformation in such short time indicates that the synthesis mechanism was MSR.
3.2 Arc discharging
The structure evolution of the powders during milling under arc discharging is presented in Fig. 4. A new phase corresponding to Ti(C,N) appeared in the diffraction pattern of the sample milled for 1 h. This suggests that a synthesis reaction occurred quickly under the subsequent arc discharging. Moreover, the synthesis of Ti(C,N) under arc discharging was dependent on the pre-milling time. Only a small amount of titanium remained in the mixture milled for 1 h. With increasing the milling time, the amount of un-reacted Ti powder decreased gradually. As the milling time prolonged to 7 h, the synthesis reaction proceeded completely. According to Vegard’s law, the compositions of the Ti(C,N) phases obtained by mechanical alloying and subsequent arc discharging from the carbon and nitrogen were TiC0.63N0.37, TiC0.79N0.21 and TiC0.76N0.24.
SEM images of the powders treated with arc discharging are shown in Fig. 5. In Fig. 5(a), agglomerated Ti(C,N) particles with size of about 500 nm can be seen. As shown in Figs.5(b) and 5(c), the sizes of the particles after subsequent arc discharging obviously increased to size of 2-7 μm and 1-4 μm, respectively, as compared to the as-milled particles.
Thus, the resultant velocity of the Ti(C,N) powders under mechanical alloying and subsequent arc discharging was accelerated greatly. The time of Ti(C,N) synthesis by mechanical alloying and subsequent arc discharge was about 1 h. In contrast, under the same milling conditions by mechanical alloying alone, no Ti(C,N) was detected after 7 h of milling. In the pre-milling process, the increase in energy stored in the mixture induced by the ball-powder-ball collisions activated atoms to interdiffuse and supplied more diffusion channels, and the activation energy barriers were reduced [19]. In the following arc discharging treatment, nitrogen plasma formed. Nitrogen ions bombarded the powder surface under an electric field effect and caused second ionization, which produced ions and radicals. The interaction between the particle surface and the ions and radicals accelerated the diffusion of atomic nitrogen and carbon into the titanium lattice and the formation of a titanium carbonitride solid solution. Simultaneously, the powder surfaces were heated by Joule heating generated from the arc discharge, which also speeded up the diffusion of atoms and the formation of Ti(C,N). Similar phenomena have been reported by CALKA et al [20]. Due to the exothermic reaction, once the synthesis reaction of Ti(C,N) on the powder surface was ignited, it propagated through the whole mixtures. Similarly, the synthesis mechanism of MA and the subsequent arc discharging were self-propagating reactive synthesis.
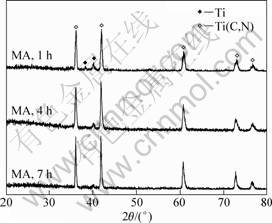
Fig. 4 XRD patterns of MA powders after arc discharging

Fig. 5 SEM images of powders after arc discharging: (a) MA, 1 h; (b) MA, 4 h; (c) MA, 7 h
4 Conclusions
1) The synthesis reaction occurred after about 1 h of mechanical milling and a subsequent arc discharge treatment, but Ti(C,N) powders were not obtained after being milled for 7 h using mechanical alloying alone.
2) The interaction between the as-milled particle surface and the ions and radicals which were produced by arc discharging treatment accelerated the diffusion and formation of Ti(C,N).
3) The formation mechanisms of the two synthesis processes are self-propagating reactive synthesis.
References
[1] ETTMAYER P, KOLASKA H, LENGAUER W, DREYER K. Ti(C, N) cermets-metallurgy and properties [J]. Int J Refract Met Hard Mater, 1995, 13(6): 343-351.
[2] XU Zhi-mou, YI Xin-jian, ZHEN Jia-shen, XIONG Wei-hao, HU Mao-zhong, XU Shang-zhi, TANG Hong-hui, LI Qiang-hui, JIANG Bin-wu, PENG De-ling, XIANG Yang-kai. A study of preparation and microstructure of nanocrystalline Ti(C,N) solid solution powders [J]. Journal of Functional Materials, 2003, 34(5): 559-561. (in Chinese)
[3] YANG J, LI F, LIU Y. Research and development of synthesis techologies of Ti(C,N) powders [J]. Cemented Carbide, 2005, 22(1): 51-54. (in Chinese)
[4] XIANG Dao-ping, LIU Ying, GAO Sheng-ji, TU Ming-jing. Evolution of phase and microstructure during carbothermal reduction-nitridation synthesis of Ti(C,N) [J]. Mater Charact, 2009, 59(3): 241-244.
[5] LI J L, HU K, ZHOU Y. Formation of TiB2/TiN nanocomposite powder by high energy ball milling and subsequent heat treatment [J]. Mater Sci Eng A, 2002, 326(1-2): 270-275.
[6] JOARDAR J, PABI S K, MURTY B S. Milling criteria for the synthesis of nanocrystalline NiAl by mechanical alloying [J]. J Alloys Compd, 2007, 429(1-2): 204-210.
[7] SURYANARAYANA C. Mechanical alloying and milling [J]. Prog Mater Sci, 2001, 46(1-2): 1-184.
[8] ZHANG S, TAM S C. Mechanical alloying of a TiC-TiN ceramic system [J]. J Mater Process Technol, 1997, 67(1-3): 112-116.
[9] SHEN G Z, TANG K B, AN CH, YANG Q, WANG C R, QIAN Y T. A simple route to prepare nanocrystalline titanium carbonitride [J]. Mater Res Bull, 2002, 37(6): 1207-1211.
[10] LI J L, LI F, HU K, ZHOU Y. Formation of TiB/TiN/Ti (Cx,N1-x) nanocomposite powder via high-energy ball milling and subsequent heat treatment [J]. J Alloys Compd, 2002, 334(1-2): 253-260.
[11] YIN F S, LI Z, XU F Z, XUE B, JIANG X B. Synthesis of nanocrystalline titanium carbonitride during milling of titanium and carbon in nitrogen atmosphere [J]. J Alloys Compd, 2009, 470(1-2): 369-374.
[12] YUAN Q, ZHENG Y, YU H J. Synthesis of nanocrystalline Ti(C, N) powders by mechanical alloying and influence of alloying elements on the reaction [J]. Int J Refract Met Hard Mater, 2009, 27(1): 121-125.
[13] ABE M, KUJI T. Hydrogen absorption of TiFe alloy synthesized by ball milling and post-annealing [J]. J Alloys Compd, 2007, 446-447: 200-203.
[14] BISHOP D, CALKA A. Phase transformations in ilmenite induced by electric discharge assisted mechanical milling [J]. J Alloys Compd, 2009, 469(1-2): 380-385.
[15] CALKA A, MOSBAH A, STANFORD N, BALAZ P. Rapid synthesis of Bi and Sb sul?des using electric discharge assisted mechanical milling [J]. J Alloys Compd, 2008, 455(1-2): 285-288.
[16] 1995 JCPDS-Internal Center for Diffraction Data. PDF Number: 32-1383 [R].
[17] 1995 JCPDS-Internal Center for Diffraction Data. PDF Number: 38-1240 [R].
[18] GRAS C H, ZINK N, BERNARD F, GAFFET E. Assisted self-sustaining combustion reaction in the Fe-Si system: Mechanical and chemical activation [J]. Mater Sci Eng A, 2007, 456(1-2): 270-277.
[19] YUAN Q, ZHENG Y, YU H J. Mechanism of synthesizing nanocrystalline TiC in different milling atmospheres [J]. Int J Refract Met Hard Mater, 2009, 27(4): 696-700.
[20] CALKA A, MOSBAH A, STANFORD N, BALAZ P. Reduction of PbS and Sb2S3 with elemental Fe and Mg in dusty plasma environment created during electrical discharge assisted mechanical milling (EDAMM) [J]. J Alloys Compd, 2009, 467(1-2): 477-484.
放电辅助机械合金化快速合成Ti(C, N)粉体
袁 泉1, 2,郑 勇1,余海州1, 2
1. 南京航空航天大学 材料科学与技术学院, 南京 210016;
2. 三峡大学 机械与材料学院,宜昌 443002
摘 要:利用机械合金化方法以Ti粉、石墨粉为原料,采用行星式球磨机在高纯氮气气氛下制备出Ti(C, N)粉体。研究放电处理对机械合金化1~7 h试样的相变及显微组织的影响。实验结果表明:球磨1 h后的样品在放电辅助下合成了Ti(C, N)粉体;而仅采用机械合金化方法,球磨7 h不能合成Ti(C, N)粉体。放电处理产生的等离子体作用于粉体上,提高了原子间的扩散速度和Ti(C, N)在球磨粉体表面的形核速度,这是加速Ti(C, N)合成的主要原因。两种合成方法都遵循机械诱发自蔓延反应机制。
关键词:Ti(C, N)粉;机械合金化;自蔓延反应合成
(Edited by YANG Hua)
Foundation item: Project (50674057) supported by the National Natural Science Foundation of China
Corresponding author: YUAN Quan; Tel: +86-25-84236039; E-mail: yyuan_1975@126.com
DOI: 10.1016/S1003-6326(11)60894-7