
Effects of solution treatment and aging process on microstructure refining of semi-solid slurry of wrought aluminum alloy 7A09
WU Xin(吴 欣), HAN Fei(韩 飞), WANG Wei-wei(王卫卫)
School of Material Science and Engineering, Harbin Institute of Technology at Weihai, Weihai 264209, China
Received 10 June 2009; accepted 15 August 2009
Abstract: A new method was exploited using solution treatment and aging process as a pretreatment in preparing semi-solid slurry with fine microstructure before isothermal treatment of wrought aluminum alloy 7A09. Parameters of pretreatment were optimized by orthogonal experiment design and proper precursor was prepared. The evolution of microstructure of semi-solid slurry during isothermal treatment was analyzed and the mechanism of microstructure refining was discussed. The result of orthogonal experiment design shows that the optimum parameters are 462 ℃ for solution temperature, 40 min for solution time, 132 ℃ for aging temperature and 14 h for aging time. Microstructure of isothermal treatment is fine, homogenous, with globular solid grains and a solid fraction between 50% and 70%, which is qualified for later semi-solid forming process. Mechanism of microstructure evolution includes the agglomeration of α-phase and Ostwald ripening. Precipitations prepared by solution and aging treatment prevent the grains from coarsening and promote the grain ripening to globular shape.
Key words: wrought aluminum alloy; semi-solid slurry; microstructure refining; solution treatment; aging
1 Introduction
Semi-solid metal processing (SSM) has been developed to a new technique in forming near-net-shape components since 1970s[1-2]. In such a process, semi-solid slurry, with non-dendrite microstructure prepared by stirring, is reheated or isothermal treated to semi-solid state and then formed through extrusion or die casting process. Compared with traditional forming process, semi-solid forming technology has a series of extraordinary advantages, such as lower forming temperature, better mechanical properties of the products, and other comprehensive advantages over metal forging of solid or die casting of liquid[3-4].
Semi-solid slurry with fine and homogeneous microstructure and proper solid fraction is the key of properties excellent forming, which also qualifies the products with good mechanical properties[5]. Much effort has been devoted to obtain slurry with fine and homogeneous microstructure, such as mechanical stirring[6-7], electromagnetic stirring[8-9], strain inducing[10], liquids casting[11-12] though it is regretful that most of these methods require complicated processing or special devices. Recently, applications of SSM with wrought alloys increase rapidly. Wrought alloys are commercial products widely used in a variety of fields. Generally, they are used directly without melting. Moreover, there are also some circumstances in which melting or any composition variation are prohibited, which requires that new methods should be developed to obtain slurry with proper microstructure for semi-solid processing. Cyclic heating treatment process before reheating has been reported to obtain semi-solid slurry with fine solid grains[13].
In this paper, a new method, solution treatment and aging process was exploited as a pretreatment before isothermal treatment of wrought aluminum alloy 7A09. Parameters of pretreatment were optimized by orthogonal experiment design and proper precursor was prepared. The evolution of microstructure of semi-solid slurry during isothermal treatment was analyzed. The effects of solution treatment and aging process on microstructure refining of semi-solid slurry were discussed.
2 Experimental
Rods of commercial wrought aluminum alloy 7A09 were used in the experiment. The composition (mass fraction) of 7A09 is: 1.2%-2% Cu, 2%-3% Mg, 5.1%- 6.1% Zn, 0.5% Si, 0.5% Fe, 0.15% Mn, 0.16%-0.3% Cr, 0.1% Ti and balanced Al. As-extruded rods were cut into pieces of 10 mm×10 mm×20 mm. To obtain proper precursors with fine microstructure, solution treatment and aging process were operated. In order to reduce the amount of process experiment, orthogonal experiment design was exploited to optimize the parameters in solution treatment and aging process. In the design, four key parameters in solution treatment and aging process, i.e. time and temperature for solution treatment as well as for aging process, were taken as four factors and there were also three levels set for each factor. The design is shown in Table 1. For the difficulty of showing grain size of the matrix in the microstructure after aging process, it was hardness that was taken as an indicator to evaluate the result of experiment.
Table 1 Orthogonal design for solution treatment and ageing process
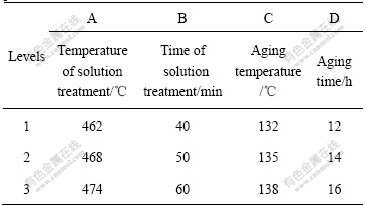
Using the optimum parameters according to the orthogonal experiment, precursors treated with solution treatment and aging process were prepared and isothermal treatment (partial remelting) was then performed at 615 ℃. The samples were kept at this temperature for 15, 20, 25 and 30 min, and semi-solid slurry was thus prepared. After that, the samples were quenched into water to examine the microstructure of semi-solid slurry.
The hardness after solution and aging was tested with a Brinell-Rockwell-Vickers hardness tester. Microstructures of solution treatment, aging, and isothermal treatment were examined by optical microscope. The solid fraction in the semi-solid slurry was estimated by DT-2000 system.
3 Results and discussion
3.1 Microstructure of solution treated and aged wrought 7A09
Fig.1 shows the microstructure of as-extruded 7A09 alloy. Coarse particles of secondary phase, generated from solidification at high temperature, disperse among α(Al) matrix and precipitations, which may initiate the crack easily during forming process.
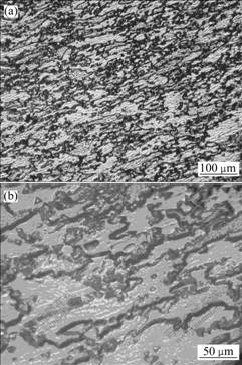
Fig.1 Microstructure of as-extruded wrought aluminum alloy 7A09 ((b) is magnification of (a))
The aim of solution treatment and aging process is to modify the microstructure of coarse secondary phase. Key parameters in solution treatment and aging process include time and temperature in solution treatment as well as in aging process. For 7A09 alloy, temperature for solution treatment is in the range of 460-475 ℃ and that for aging process is (135±5) ℃. Parameters are adjusted carefully within above range. Though there is evidence through trial experiments that time for solution treatment is never longer than 60 min, the maximum time for solution treatment is fixed on 60 min in our orthogonal experiment. The microstructure after solution and aging treatment is shown in Fig.2. By means of solution treatment, coarse particles of secondary phase resolute into matrix of solution and then re-precipitate from supersaturated solid solution during aging process. The microstructure is fine and the secondary phases are homogenously dispersed in the matrix.
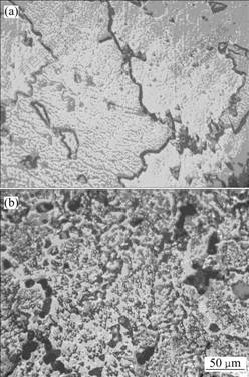
Fig.2 Microstructure of wrought aluminum alloy 7A09 after solution treatment and aging process: (a) After solution treatment (468 ℃, 50 min); (b) After solution treatment and aging process (468 ℃, 50 min and 135 ℃, 14 h)
3.2 Orthogonal experiment design
9 groups of tests were carried out according to the orthogonal table L9(34)[14] with 4 factors and 3 levels shown in Table 2. Hardness (HRB) tests were operated with every microstructure of the 9 combination of solution treatment and aging process. The value of range (R) and mean square deviation (
) are also listed in Table 2.
From the value of R and
, it is evident that among four factors, the time of aging process (D) affects hardness the most and then the temperature of aging process. The intuitive analysis diagram is shown in Fig.3. Based on the hardness for each factor/level combination, the best levels for four factors are A1B1C1D2. The optimum parameters are 462 ℃ for solution temperature, 40 min for solution time, 132 ℃ for aging temperature and 14 h for aging time. Precursor qualified for isothermal treatment is then prepared with these optimum parameters. Fig.4 shows microstructure of the precursor. Plenty of fine particles of precipitation distribute homogeneously in the matrix of α(Al), which contributes high hardness value of the samples. When reheated, these fine particles can help to prevent the migration of grain boundary and preserve fine and homogeneous solid grains.
Table 2 Orthogonal experiment table and results of solution treatment and aging process
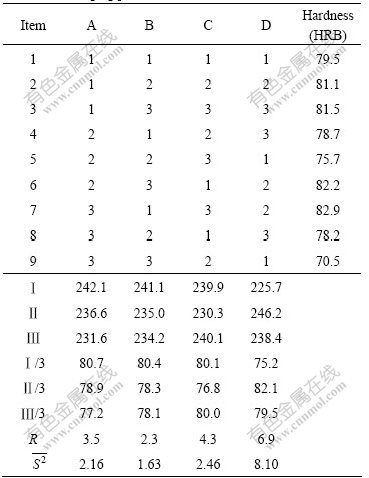
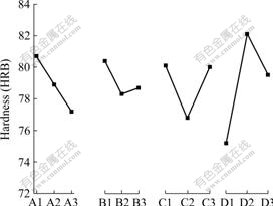
Fig.3 Intuitive analysis diagram of solution treatment and ageing process
3.3 Microstructure of semi-solid slurry of isothermal treatment
Using precursor with microstructure shown in Fig.4, isothermal treatment (partial remelting) was operated. The morphologies of semi-solid slurry are shown in Fig.5.
In Fig.5, globular, non-dendrite grains are found in the morphology of semi-solid slurry after isothermal treatment at 615 ℃. The grain is fine, globular shaped and distributed homogeneously. When hold for longer time, grain size increases gradually. After hold at 615 ℃ for 30 min or more, samples are almost melted to be out of shape and no further forming process could be operated.
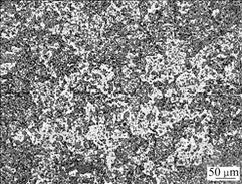
Fig.4 Microstructure of precursor prepared with optimum parameters of solution and aging process (Solution treatment: 462 ℃, 40 min; Aging process: 132 ℃, 14 h)
Solid fraction is estimated to be 65.5%, 59.7% and 51.5% in Fig.5(a), (b) and (c) respectively, and the microstructure is qualified for later semi-solid forming process[5]. However, in Fig.5(d), the solid fraction is as high as 89.8%.
Compared the morphology in Figs.5(a), (b) and (c) with Fig.5(d), except for the difference in solid fraction, the grain diameter and the radius of curvature of solid grain boundary in the latter are both bigger than that in the former. Also, the degree of spheroidizing of solid grains in Fig.5(d) is not as good as that of in the former.
It’s interesting to show that the previous solution treatment and aging process can help to restrict solid
grain size in semi-solid slurry. It seems that fine precipitations prepared through solution treatment and aging process restrict the growing space of solid grains and prohibit grain coarsening by preventing the migration of grain boundary during isothermal treatment, which will improve the processing properties of 7A09 alloy in later semi-solid forming process. In Liu’s research about liquidus casting of Al alloy 7075[12], in-situ synthesized TiC particulate also plays the same role.
3.4 Effects of solution treatment and aging process on microstructure refining of semi-solid slurry
The effects of solution treatment and aging process on microstructure refining of semi-solid slurry are closely related to the evolving progress of the microstructure of isothermal treatment. When reheated at isothermal temperature, the microstructure evolution of semi-solid slurry can be analyzed as the following two-stage progress.
At the beginning of reheating, when the operating temperature is lower than melting temperature or the holding time is not long enough, the microstructure of alloy contains mainly α-phase of matrix and precipitations retained at this moment. Though there is little liquid, grains of α-phase contact each other closely. Because of the orientation difference among neighbor grains, there exists surface tension in grain boundaries. As a result of surface tension, grains will agglomerate to
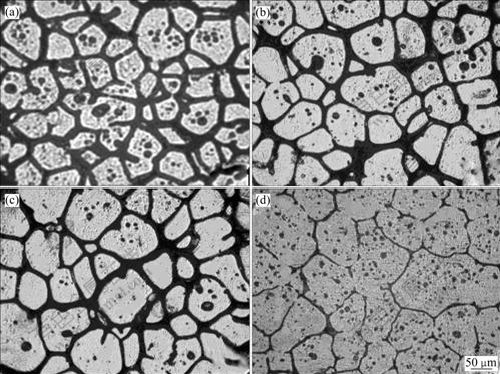
Fig.5 Morphologies of semi-solid slurry after isothermal treatment at 615 ℃ using precursor for different times: (a) 15 min; (b) 20 min; (c) 25 min; (d) 25 min (using as-extruded rod)
reduce the surface energy. This progress develops mainly through a way of bigger grains consuming smaller ones or a way of grains agglomeration between neighbor grains with similar orientation. Such growth is a spontaneous progress of system energy reduction.
In this beginning stage, fine precipitations play very important parts in refining the microstructure of semi-solid slurry. Considering the beginning of reheating, when the operating temperature is lower than melting temperature or the holding time is not long enough, there are many secondary phases reserved without melting. On one hand, grain boundary migrates driven by surface energy reducing. On the other hand, the retained secondary phases tow the grain boundaries and hamper their migration. When these two forces are balanced, the stable size of grains can be determined as:
(1)
where D stands for mean stable grain diameter of α-phase; r is for the size of secondary phase and f for its volume fraction. Solution and aging treatment, resulting in the refining of secondary phases, contribute to the microstructure refining of semi-solid slurry during the beginning period of reheating.
In the second stage, with more heat energy input, secondary phases of low melting point begin to melt into liquids which distribute mainly at grain boundaries. Grains of α-phase, originally closely contacting with each other, are now segregated by liquid and no longer contact directly (see Fig.5). Surface tensions are now developed at interfaces among liquid and solid particles. During this period, microstructure will also coarsen but in a different way. The mechanism of grain coarsening switches from the progress of grains agglomeration to the progress of interface diffusion controlled by the solubility difference of interface with different curvature. Gibbs-Thomson Law is often used to describe this effect:
(2)
where r is the size of α-phase particle; C(r) and C(∞) are the solubility of solute atom in liquid for particles of α-phase with size r and ∞; σ is the specific interface energy; V is the mole volume of α phase, T is thermodynamic temperature and k is Boltzmann constant. From Eq.(2), the smaller the α-phase particle is, the larger the solubility of solute atoms in liquid. Solubility gradient of solute atoms in liquid is thus developed. By this gradient, solute atoms diffuse in liquid from the interface of small α-phase particles to that of big ones. Thus, big α-phase particles consume small ones and become bigger. Through this Ostwald ripening progress, the curvature of different interface eventually goes uniform, and the solid grains become globular. This conclusion of two-stage microstructure evolution is supported by LU et al with the study of Al-4Cu-Mg alloy[15]. According to LU’s experiments, in the progress of heating, there are two different effects of holding time on grain diameter. Grains grow fast at the beginning of holding whereas in the second Ostwald ripening stage, grains keep on growing but with a lowered-down coarsening speed.
In this paper, fine precipitations prepared through solution treatment and aging process play very important parts in this two-stage microstructure evolution of isothermal treatment. After the pretreatment of solution treatment and aging, there’s a large amount of precipitations in the microstructure of the precursor, as shown in Fig.4. At the beginning stage of heating, these secondary phases evidently hamper the migration of grain boundaries in solid matrix α-phase from rapid agglomeration. According to Eq.(1), the smaller the precipitations are, the smaller the solid grains are. The coarsening of microstructure is hence very limited. During further heating, the retained precipitations with low melting point, melt into liquid and agglomerate at boundaries of solid particles. The liquid segregates solid particles from each other. The coarsening mechanism of matrix α-phase grains switches to an Ostwald ripening way. The coarsening speed of microstructure thus reduces. From these analyses, the precipitations not only prevent the rapid coarsening of grains in the first stage of few liquid fraction in the microstructure, because of their low melting point, but also improve the evolution of liquid and promote the growth of matrix particles to a ripening stage and hence fasten the evolution of globular grains. Moreover, after pretreatment of solution and aging, when isothermal treated, semi-solid slurry with the microstructure of fine solid grains and proper liquid fraction can be obtained in shorter holding time. In Figs.5(a), (b) and (c), proper liquid fraction makes grains ripening and globular shaped rapidly, the coarsening is limited. However, in Fig.5(d), because of the lack of plenty of fine precipitations in the as-extruded microstructure, liquid fraction is too low to segregate the solid grains properly. The grains have already coarsened in the beginning fast-coarsening stage. And, even after holding for 25 min, the spheroidizing of solid grains is still not acceptable.
4 Conclusions
1) Among four key parameters in the process of solution treatment and aging process, the time of aging process has the most effect on hardness and followed by the temperature of aging process, and the time of solution treatment has the least effect.
2) The optimum parameters determined through orthogonal experiment for pre-solution treatment and aging process before isothermal treatment are 462 ℃ for solution temperature, 40 min for solution time, 132 ℃ for aging temperature and 14 h for aging time.
3) Pre-treatment of solution and aging process before isothermal treatment change the primitive microstructure of as-extruded rods from coarse secondary phase to one with plenty of fine precipitations dispersed in the matrix. With such a fine precursor, microstructure of isothermal treatment is fine, homogenous, with globular solid grains and a solid fraction between 50% and 70%, which is qualified to later semi-solid forming process.
4) Microstructure evolution of semi-solid slurry of 7A09 includes two stages: the agglomeration of α-phase and Ostwald ripening of solid grains. Precipitations prepared by solution and aging treatment prevent the grains from rapid coarsening in the agglomeration stage and promote the solid grains ripening in a slower Ostwald way to globular shape.
References
[1] FLEMINGS M C. Behavior of metals in the semi-solid state[J]. Metallurgical and Materials Transactions A, 1991, 22(5): 957-981.
[2] XIE Shui-sheng. PAN Hong-ping, DING Zhi-yong. The overview of study and application of semi-solid metals processing technology[J]. Journal of Plasticity Engineering, 2002, 9(2): 1-11. (in Chinese)
[3] VIVES C. Elaboration of semisolid alloys by means of new electromagnetic rheocasting processes[J]. Metallurgical and Materials Transactions B, 1992, 23(2): 189-206.
[4] WANG J L, SU Y H, TSAO C Y A. Structural evolution of conventional cast dendritic and spray-cast non-dendritic structures during isothermal holding in the semi-solid state[J]. Scripta Materialia, 1997, 37(12): 2003-2007.
[5] MANSON-WHITTON E D, STONE I C, JONES J R, GRANT P S, CANTOR B. Isothermal grain coarsening of spray formed alloy in the semi-solid state[J]. Acta Materialia, 2002, 50(10): 2517-2524.
[6] HAGHAYEGHI R, ZOQUI E J, HALVAEE A. An investigation on semi-solid Al-7Si-0.3Mg alloy produced by mechanical stirring[J]. Journal of Materials Processing Technology, 2005, 169(3): 382-387.
[7] ZHANG Song-yang, GENG Mao-peng, XIE Shui-sheng, GUO Xiao-qin, CHENG Jun-wei, LI Qian, LI Si-zhang, SHAO Yan-tao, ZHANG Ying. Optimization of processing of semi-solid slurry making based on artificial neural network[J]. Special Casting & Nonferrous Alloys, 2008, 28(7): 505-507. (in Chinese)
[8] MAO W M, ZHEN Z S, CHEN H T, ZHONG X Y. Microstructure of electromagnetic stirred semi-solid AZ91D alloy[J]. Transactions of Nonferrous Metals Society of China, 2004, 14(5): 846-850.
[9] SHI Hong-jun, YANG Yi-tao, SUN Bao-liang, SHAO Guang-jie. Simulation of aluminum alloy in continuous casting and aided optimization of processing parameters[J]. Special Casting & Nonferrous Alloys, 2005, 25(6): 344-346. (in Chinese)
[10] TOSHIO H, KAPRANOS P. Simple rheocasting process[J]. Journal of Material Processing Technology, 2002, 130/131: 594-598.
[11] DONG J, CUI J Z, LE Q C, LU G M. Liquidus semi-continuous casting, reheating and thixoforming of a wrought aluminum alloy 7075[J]. Mater Sci Eng A, 2003, 345(1/2): 234-242.
[12] LIU Hui-min, LIAO Qing-hua, YOU Guo-yan, GE Ri-le. Effect of in-situ synthesized TiC particulates on microstructure of liquidus casting semi-solid Al alloys[J]. Foundry Technology, 2008, 29(7): 905-908. (in Chinese)
[13] SUI Shao-hua, SONG Tian-ge, ZHAO Hong-yun. Cyclic heating treatment for microstructures evolution of LC9 aluminum alloy[J]. Foundry, 2007, 56(2): 10-13. (in Chinese)
[14] CHEN Kui. Experiment design and analysis[M]. Beijing: Tsinghua University Press, 2005.
[15] LU Ya-lin, LI Miao-quan, SHI Yan-pei. Microstructural evolution of the semi-solid Al-4Cu-Mg alloy during partial remelting[J]. Journal of Plasticity Engineering, 2007, 14(4): 82-86. (in Chinese)
(Edited by ZHAO Jun)
Foundation item: Project (2007-83) supported by Science and Technology Development Projects of Weihai, Shandong Province
Corresponding author: WU Xin; Tel: +86-631-5687157; E-mail: wx@hitwh.edu.cn