
Effect of nanocrystallization on hot corrosion resistance of
Ti-48Al-8Cr-2Ag alloy in molten salts
XI Yan-jun(席艳君)1, 2, LU Jin-bin(卢金斌)1, WANG Zhi-xin(王志新)1,
HE Lian-long(贺连龙)3, WANG Fu-hui(王福会)2
1. Department of Materials and Chemical Engineering, Zhongyuan University of Technology,
Zhengzhou 450007, China;
2. State Key Laboratory for Corrosion and Protection, Institute of Metal Research,
Chinese Academy of Sciences, Shenyang 110016,China;
3. Shenyang National Laboratory for Materials Sciences,
Institute of Metal Research, Chinese Academy of Sciences, Shenyang 110016, China
Received 9 August 2005; accepted 9 December 2005
Abstract: Magnetron-sputter deposition was used to produce Ti-48Al-8Cr-2Ag coating on a cast alloy substrate with the same composition. Hot corrosion was carried out in molten (Na,K)2SO4 and Na2SO4+NaCl at 900 ℃. The sputtered nanocrystalline coating shows much better hot-corrosion resistance in molten (Na,K)2SO4 as a result of the formation of a continuous and compact Al2O3 scale. The nanocrystallization of TiAlCrAg alloy prolongs the incubation of breakaway corrosion and improves the hot-corrosion resistance of TiAlCrAg alloy in molten Na2SO4+NaCl. The relevant corrosion mechanism was discussed.
Key words: Ti-48Al-8Cr-2Ag alloy; magnetron sputter; nanocrystallization; hot corrosion; oxide scale
1 Introduction
There was considerable interest in the use of γ-TiAl alloys within advanced gas turbines where they offered greater high temperature capability over conventional titanium at reduced mass. These factors would enable engines with greater thrust to mass ratio to be developed. Thus γ-TiAl offered the potential of replacing nickel based alloys within the high pressure compressor and potential the fourth stage turbines[1].
Service in both of these locations would require that the γ-TiAl be resistant not only to oxidation, but also to hot salt corrosion. The hot corrosion of heat-resistant alloys was accelerated in the presence of fuel combustion products of impurities such as NaCl, SO2, and Na2SO4 [2]. The Na2SO4-NaCl induced hot corrosion of nickel- based superalloys was examined.
A considerable body of data on the oxidation of γ-TiAl was available[3-7]. In order to solve the poor high temperature resistance of γ-TiAl, the effects of alloying elements [8], surface treatment [9,10], and protective coatings[11-17] on the oxidation resistance of γ-TiAl were investigated widely. It must be noted that a series of TiAl alloys with Cr and Ag additions were investigated, and TiAlCrAg exhibited also excellent oxidation resistance[18]. Therefore, TiAlCrAg coatings may become a promising protective coating for TiAl-based intermetallics. The present authors have also examined the effect of nanocrystalline TiAlCrAg coating on the oxidation resistance of TiAlCrAg alloy[19]. The results indicated that the oxidation resistance of TiAlCrAg was improved by nanocrystallization. GENG et al [20] verified that nanocrystallization could improve the hot corrosion resistance of K38G in molten sulfate. However, there were no data concerning the hot corrosion behavior of the sputtered nanocrystalline coating of TiAlCrAg in molten salt, which is the subject of this study.
2 Experimental
The Ti-48Al-8Cr-2Ag (mole fraction, %) coating was prepared on the same cast alloy by magnetron sputtering technique. The target and the specimens, with the sizes of 380 mm×126 mm×7 mm and 10 mm×10 mm×2.5 mm respectively, were cut from the ingot. The specimens were ground down to No.600 emery paper, peened and ultrasonically cleaned in ethanol. The peening treatment was to improve the adhesive energy. The deposition procedure and the morphology and microstructure of the coating were narrated in detail elsewhere[19].
The hot corrosion test was carried out in melt of 75% Na2SO4+25% K2SO4 (mass fraction, %) and 75% Na2SO4+25% NaCl at 900℃. The specimens were immersed completely into the molten salts and moved at regular intervals, cooled in air, cleaned in boiling water, and dried with hot air for mass measurements. The sensitivity of the balance used in the study was 10-4 g.
The specimens were analyzed using scanning electron microscopy(SEM) with energy dispersive X-ray diffraction(EDX) and electron probe microanalysis (EPMA).
3 Results
Fig.1 shows the hot corrosion kinetics of specimens in molten salts at 900 ℃. It is seen that the Ti-48Al- 8Cr-2Ag coating exhibits much better hot-corrosion resistance than the cast alloy in (Na,K)2SO4 melts at 900 ℃ when the immersion time surpasses 20 h. During the initial 20 h, the coating almost shows the same mass gain as the cast alloy. The coating possesses a rougher surface. The sputtered surface with globe-shaped protrusions gives a larger oxidation surface area than that of the polished surface of the original alloy. Besides, there exist boundaries or free surfaces between columns, which may induce extra surface area for the coating. Hence, the mass gain is high for the coating at the initial stage.
From Fig.1, we can also see that the sputtered coating shows better hot corrosion resistance than the cast alloy during the initial corrosion stage in Na2SO4+NaCl melts. However, the cast alloy and nanocrystalline coating exhibit serious mass loss after 50 h hot corrosion in Na2SO4+NaCl melts. The grain size reduction enhances the diffusivities of Al because the grain-boundary diffusion is favorable to the formation of an external Al2O3 scale. Hence, the grain size reduction improves the corrosion resistance during the initial 20 h. After 20 h, Al content is not enough to supply the liquated scale, the protective scale is destroyed. Thus, the coating exhibits high corrosion rate.
Fig.2 shows the surface morphology and cross sectional microstructure of TiAlCrAg alloy in molten (Na,K)2SO4 at 900 ℃ after 100 h. The main corrosion product is TiO2. Al2O3 scale disappears, and layered structure scale forms on the alloy. According to the EPMA analysis shown in Fig.3, the outer layer is mainly TiO2, the intermediate one is TiO2 and Al2O3, and sulfide exists at the scale/substrate interface.
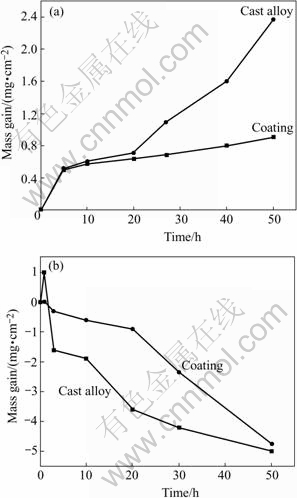
Fig.1 Hot-corrosion kinetics of specimens in molten salts at 900 ℃: (a) (Na,K)2SO4; (b) Na2SO4+NaCl
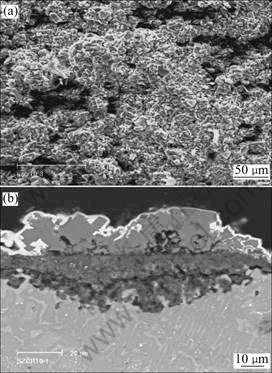
Fig.2 Surface morphology(a) and cross sectional structure(b) of cast alloy in molten 75%Na2SO4+25% K2SO4 at 900 ℃ for 100 h
(Fig.4 shows the surface morphology and cross- sectional microstructure of the alloys with coating after 100 h in the molten (Na,K)2SO4 at 900 ℃. The Al2O3 scale forms on the most of areas, and in few areas layered structure scale forms.
Fig.5 shows the cross-sectional microstructure of the alloys after 20 h in the molten Na2SO4+NaCl at 900 ℃. The EPMA analyses corresponding to the scale are shown in Fig.6. The outer layer is mainly TiO2, Al2O3 and oxide of Cr. Beneath the mixed layer, sulfide exists at the scale/substrate interface with many pores.
Fig.7 shows the cross-sectional microstructure of the alloys with sputtered nanocrystalline coating after 20 h in the molten Na2SO4+NaCl at 900 ℃. In most areas a very thin uniform Al2O3 scale exists on the surface, and beneath the scale there is an Al-depletion layer.
Fig.8 shows the cross-sectional microstructures of the alloy and sputtered nanocrystalline coating after 50 h in the molten Na2SO4+NaCl at 900 ℃. Thick oxide scales form on the alloy and the coating. The protection effect of coating disappears.
4 Discussion
Ti-48Al-8Cr-2Ag alloy possesses layered structure scale after 100 h corrosion in molten (Na,K)2SO4 at 900℃. Nonprotective TiO2+Al2O3 of mixture forms on some areas of the cast alloy in air at 900 ℃. The scale may allow sulfur transport inwards the scale to the scale/alloy interface. Because Ti has greater affinity to S than Al, the following reaction may occur:
3TiAl+S2=2TiS+TiAl3 (1)
Thus, TiS forms near the scale.
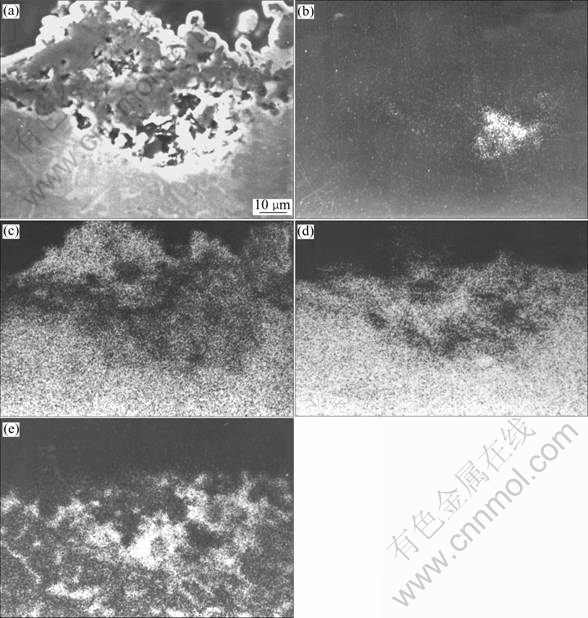
Fig.3 EPMA analyses of alloy after corrosion in molten 75 % Na2SO4+25% K2SO4 for 100 h at 900 ℃: (b) S; (c) Ti; (d) Al; (e) Cr
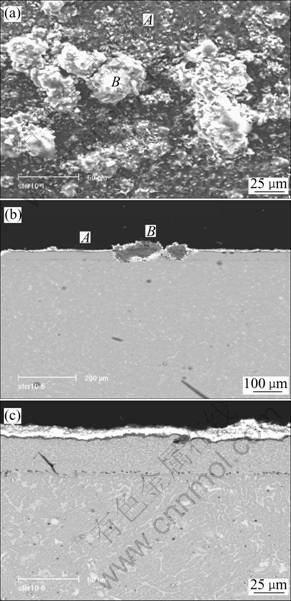
Fig.4 Surface morphology(a) and cross sectional structure(b) of cast alloy with coating in molten 75%Na2SO4+25% K2SO4 for 100 h at 900 ℃ and magnified feature A(c)
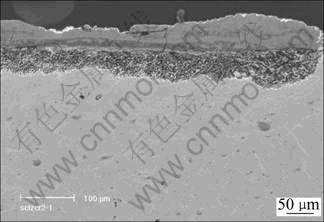
Fig.5 Cross sectional structure of cast alloy in molten 75% Na2SO4+25% NaCl for 20 h at 900 ℃
For the nanocrystalline TiAlCrAg coating, a continuous Al2O3 scale forms on the surface after 50 h in molten salt at 900 ℃. Because the dissolution of O in sulfate melts is limited, O potential may result mainly from the following equilibriums:
Na2SO4=Na2O+SO3 (2)
SO3=(1/2)S2+(3/2)O2 (3)
When the equilibrium(3) occurs, the partial pressure of S increases. When it is up to a critical value, S can transport across the scale to the substrate. The internal sulfide forms, then the alkaline dissolution of Al2O3 occurs. The protective scale is destroyed, and hot corrosion resistance decreases. In the present study, a continuous Al2O3 scale interrupts S inward diffusion. The change of alkalinity at the salt/scale does not occur. Therefore, the protective Al2O3 scale can exist on the surface stably. The nanocrystalline TiAlCrAg provides excellent hot corrosion resistance in molten 75% Na2SO4+25% K2SO4 at 900 ℃.
For the cast alloy, after 20 h corrosion in Na2SO4+NaCl melts, the outer layer is mainly TiO2, Al2O3 and Cr oxide. Beneath the mixed layer, sulfide exists at the scale/substrate interface porously. Generally, Al2O3 and TiO2 form on the alloy surface at the beginning of corrosion. NaCl penetrates through the oxide scale along the cracks and pores, and reacts with the alloy to form the volatile chlorides. When the volatile chlorides concentrate to certain content, the oxide scale cracks. At the surface of the scales, where oxygen potential is high, the chlorides may reoxidize to release Cl2. Cl2 then reacts with the alloy to form the new chlorides. This process repeats, and the alloy exhibits high corrosion rate. The cross sectional microstructure shows that a larger number of pores exist around the corrosion grains in the inner corrosion layer. This results from the volatile chlorides. S diffuses along defect to pores to form the sulfate around the pores. When a larger number of Ti and Al are consumed, Cr is rich on the surface of the alloy. When Cr concentration reaches certain content, Cr reacts with O to form Cr oxide because the mixed TiO2+Al2O3 can not prohibit O diffusion effectively. In addition, O is consumed and the partial pressure of O decreases at the oxide scale/melts interface, at the same time the partial pressure of S increases. S can transport across the scale to the substrate to form sulfate.
For the nanocrystalline TiAlCrAg coating, after 20 h corrosion in Na2SO4+NaCl melts, a continuous Al2O3 scale forms because nanocrystallization and Cr effect increase the Al activity. When the scale is liquated to destroy, new Al2O3 scale forms due to the continuous supply of Al in the coating. Therefore, after 20 h corrosion, the kinetics curves show a little mass loss, and an Al2O3 scale forms on the surface of the coating. Underneath the oxide scale an Al-depletion layer exists
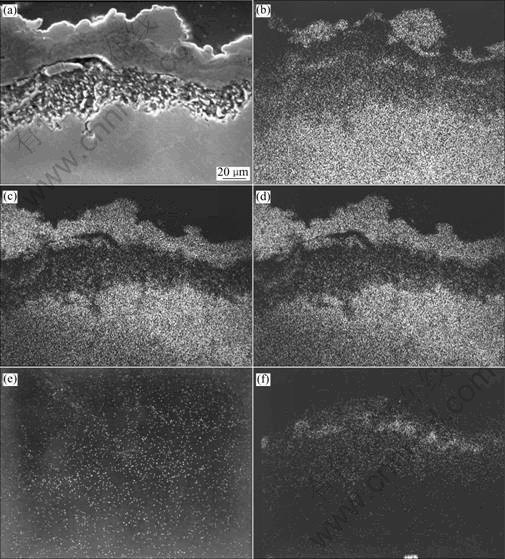
Fig.6 EPMA analyses of TiAlCrAg alloy in 75% Na2SO4+25% NaCl after corrosion for 20 h at 900 ℃: (b) Ti; (c) Al; (d) Cr; (e) Cl; (f) S
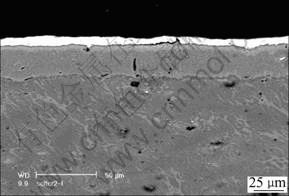
Fig.7 Cross sectional structure of coating in molten 75% Na2SO4+25% NaCl for 20 h at 900 ℃
because new scale formation needs a larger number of Al supply. The continuous formation and spallation of Al2O3 scale make Al content decrease quickly. When Al content is not enough to supply the liquated scale, the protective scales destroyed. Thus, after 50 h corrosion, the coating forms thick oxide scale. Therefore, nanocrystallization increases Al activity to supply new scale, and elongates the protective Al2O3 scale time on the surface.
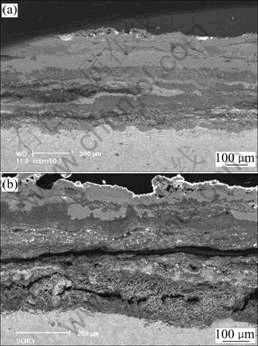
Fig.8 Cross sectional structure of cast alloy(a) and sputtered coating(b) in molten 75%Na2SO4+25% NaCl after 50 h at 900 ℃
5 Conclusions
The sputtered nanocrystalline coating shows much better hot-corrosion resistance in molten (Na,K)2SO4 as a result of the formation of a continuous and compact Al2O3 scale. The nanocrystallization of TiAlCrAg alloy prolongs the incubation of breakaway corrosion and improves the hot-corrosion of TiAlCrAg alloy in molten Na2SO4+NaCl.
References
[1] Nicholls J R, Leggett J, Andrwes P. Hot salt corrosion of titanium aluminides[J]. Mater and Corr, 1997, 48: 56-64.
[2] Shinata Y, Takahashi F, Hashiura K. NaCl-induced hot corrosion of stainless steels[J]. Mater Sci Eng, 1987, 87: 399-406.
[3] Dettenwanger F, Schumann E, Ruhle M, Rakowski J, Meier G H. Microstructure study of oxidized γ-TiAl[J]. Oxid Met, 1998, 50: 269-305.
[4] Lang C, Schutze M. TEM investigations of the early stages of TiAl oxidation [J]. Oxid Met, 1996, 46: 255-285.
[5] YANG M R, WU S K. Oxidation behavior and oxide layers of Ti-50Al intermetallics by preoxidation in high-pressure oxygen [J]. Oxid Met, 2000, 54: 473-490.
[6] Schmitz-Niederau M, Shutze M. The oxidation behavior of several Ti-Al alloys at 900 ℃ in air [J]. Oxid Met, 1999, 52: 225-240.
[7] Copland E H, Gleeson B, Young D J. Formation of Z-Ti50Al30O20 in the sub-oxide zones of γ-TiAl-based alloys during oxidation in 1 000 ℃ [J]. Acta Mater, 1999, 47: 2937-2949.
[8] Shida Y, Anana H. The influence of ternary element addition on the oxidation behavior of TiAl intermetallic compound in high temperature air [J]. Corro Sci, 1993, 25: 945-953.
[9] Taniguchi S, Shibata T, Murakami A. Improvement in the oxidation resistance of TiAl by preoxidation in a SiO2-power pack [J]. Oxid Met, 1994, 41: 103-113.
[10] KIM Y W. Ordered intermetallic alloys(Part three): gamma titanium aluminides[J]. JOM, 1994, July: 30-35.
[11] TANG Zhao-lin, WANG Fu-hui, WU Wei-tao. Effect of a sputtered TiAlCr coating on the oxidation resistance of TiAl intermetallic compound [J]. Oxid Met, 1997, 48: 511-525.
[12] ZHOU Chun-gen, YANG Ying, GONG Sheng-kai, XU Hui-bin. Effect of Ti-Al-Cr coatings on the high temperature oxidation behavior of TiAl alloys[J]. Mater Sci Eng A, 2001, 43: 182-187.
[13] Leyens C, Schmist M, Peters M, Kaysser W A. Sputtered intermetallic Ti-Al-X coatings: phased formation and oxidation behavior [J]. Mater Sci Eng A, 1997, 239: 680-687.
[14] Tang Z, Niewolak L, Shemet V, Singheiser L, Quadakkers W J, Wang F, Wu W, Gil A. Effect of Cr addition on oxidation behavior of Ti-48Al-2Ag alloy [J]. Mater Sci Eng A, 2002, 328: 297-301.
[15] Murris I, Acob Y P, Haanappel V A C, Stroosnijder M F. High-temperature oxidation behavior of chromium: effect of different batches [J]. Oxid Met, 2001, 55: 307-331.
[16] WANG Fu-hui, TANG Zhao-lin, WU Wei-tao. Effect of chromium on the oxidation resistance of TiAl intermetallics [J]. Oxid Met, 1997, 48: 381- 390.
[17] Haanappel V A C, Hofman R, Sunderkotter J D, Glatz W, Clemens H, Stroosnijder M F. The influnence of microstructure on the isothermal and cyclic-oxidation behavior of Ti-48Al-2Cr at 800 ℃ [J]. Oxid Met, 1997, 48: 263-287.
[18] Tang Z, Shemet V, Niewolak L, Quadakkers W J. Effect of Cr addition on oxidation behavior of Ti-48Al-2Ag alloys [J]. Intermetallics, 2003, 11: 1-8.
[19] XI Yan-jun, WANG Fu-hui, HE Lian-long. Oxidation and hot-corrosion behavior of sputtered Ti-48Al-8Cr-2Ag nanocrystalline coating [J]. Mater Sci Forum, 2004, 461: 1181-1187.
[20] Geng S J, Wang F H, Zhu S L, Wu W T. Hot-corrosion resistance of a sputtered K38G nanocrystalline coating in molten sulfate at 900 ℃ [J]. Oxid Met, 2002, 51: 549-557.
Foundation item: Project(59971052) supported by the National Natural Science Foundation of China
Corresponding author: XI Yan-jun; Tel: +86-371-67698114; E-mail: yjxi@sina.com; yjxi@zzti.edu.cn
(Edited by YUAN Sai-qian)