J. Cent. South Univ. Technol. (2008) 15: 706-711
DOI: 10.1007/s11771-008-0131-7

Analysis and modeling of error of spiral bevel gear grinder based on multi-body system theory
CHEN Shu-han(陈书涵)1, YAN Hong-zhi(严宏志)1, MING Xing-zu(明兴祖)1, 2
(1. School of Mechanical and Electrical Engineering, Central South University, Changsha 410083, China;
2. School of Mechanical Engineering, Hunan University of Technology, Zhuzhou 412008, China)
Abstract: Six-axis numerical control spiral bevel gear grinder was taken as the object, multi-body system theory and Denavit-Hartenberg homogeneous transformed matrix (HTM) were utilized to establish the grinder synthesis error model, and the validity of model was confirmed by the experiment. Additionally, in grinding wheel tool point coordinate system, the errors of six degrees of freedom were simulated when the grinding wheel revolving around C-axis, moving along X-axis and Y-axis. The influence of these six errors on teeth space, helix angle, pitch, teeth profile was discussed. The simulation results show that the angle error is in the range from -0.148 4 rad to -0.241 9 rad when grinding wheel moving along X, Y-axis; the translation error is in the range from 0.866 0 μm to 3.605 3 μm when grinding wheel moving along X-axis. These angle and translation errors have a great influence on the helix angle, pitch, teeth thickness and tooth socket.
Key words: six-axis; grinder; spiral bevel gear; error model; analysis
1 Introduction
The six-axis numerical control (NC) spiral bevel gear grinder was firstly made in 2002 in China (South Central University) after USA’s GLEASON, German’s KLINGBERG and Swiss’s OERLIKON. But a gap between the machining precision of six-axis NC spiral bevel gear grinder developed independently and that of the spiral bevel gear grinder made in USA, Germany and Switzerland exists.
At present, in the research of enhancing spiral bevel gear machining precision, the gear tooth surface error back adjusting correction technology is mainly researched[1-3]. The error of spiral bevel gear grinder and the relationship between the error and spiral bevel gear processing precision are rarely researched, but the research on machining center, numerical control machine of 2-axis, 3-axis and so on are universal. In order to improve machining quality, conservative cutting parameters are usually selected during machining and thus the boost of productivity is limited. Error compensation is an effective solution[4-5]. In developing machine error models, multi-body system theory and HTM are widely applied to deriving complete error models with geometric error and thermal deformation[6-10]. Additionally, dynamic neural network model[11], adaptive model[12] and robust thermal error model[13] of these models have been also discussed. So, the error synthesis model of six-axis numerical control spiral bevel gear grinder was also established by using the multi-body system theory and HTM in this work. The fractional errors having an influence on teeth space of gear, helix angle of gear, pitch of gear, teeth profile of gear and so on, were analyzed. It provides a theoretic basis for improving precision and the error compensations of six-axis NC spiral bevel gear grinder.
2 Topology structure description of spiral bevel gear grinder
The object of this research is the independent developmental six-axis spiral bevel gears numerical control grinder (see Fig.1). Three translations and three rotations are included as shown in Fig.1. In the cutting process, the grinding wheel rotation angle is excluded and only five axes are relative.
In order to describe topology structure of six-axis spiral bevel gears numerical control grinder by the multi-body system theory, firstly, serial numbers of every part were made. According to Fig.1, various parts of the grinder were disposed as follows.
The earth was taken as B0 body and the lathe bed 1 was taken as B1 body. The grinder system can be divided into two branches: the branch one including lathe bed 1, machine saddle 2, work table 3, work piece spindle 4, work piece 5; the branch two including lathe bed 1, column 6, headstock 7, grinding wheel spindle 8, and grinding wheel 9.
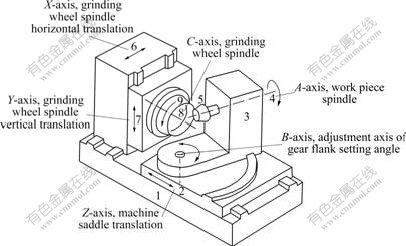
Fig.1 Schematic of six-axis NC spiral bevel gear grinder
For the branch one, B1 body was taken as the beginning along the direction far away from B1, and serial number of each part was marked B1-Bn (n was part numbers in branch one) according to the sequence which naturally grows, then serial number of each part in grinder along the branch two was marked Bn+1-Bn+m-1 (m was part number of the branch two) until the marking was finished.
According to the above marking principle, various parts of six-axis spiral bevel gear numerical control grinder were listed as follows: lathe bed B1, machine saddle B2, work table B3, work piece spindle B4, work piece B5, column B6, headstock B7, grinding wheel spindle B8 and grinding wheel B9. Among them, work piece B5 and grinding wheel B9 were respectively terminal bodies of the branch one and the branch two.
According to the above topology description of six-axis spiral bevel gear numerical control grinder, the lower body array and the topology structure of grinder were obtained (Table 1 and Fig.2).
Table 1 Lower body arrays of grinder
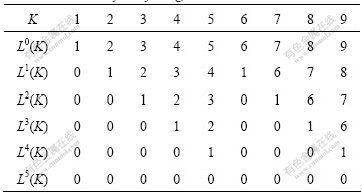
3 Establishment of error model of grinder
3.1 Error analysis of grinder
The grinder considered in this work has three translational axes with three rotational axes in the table. The coordinate systems for each body of grinder were determined. As shown in Fig.3, X1, Y1 and Z1 represent 3-linear axes respectively of lathe bed B1 coordinate system S1(O1, X1, Y1, Z1); X2, Y2 and Z2 represent 3-linear axes respectively of machine saddle B2 coordinate system S2(O2, X2, Y2, Z2) and so on.
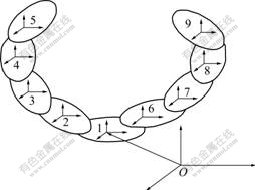
Fig.2 Topology structure of grinder
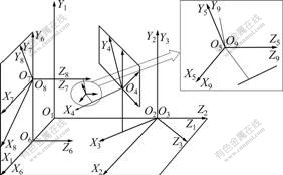
Fig.3 Coordinate frames of grinder
With the influence of grinder assembly and manufacturing error and all else factors, arbitrary body has the angular errors {α, β, γ} of three directions and three translational errors {Δa, Δb, Δc} along the coordinate axes whether arbitrary body Bv moves or rotates relatively to its neighboring lower body Bs, and all of them are micro-small amount. Based on small erroneous supposition, the position error matrix is
(1)
In the grinder actual machining process, the working state of grinding transforms from the non-steady state to steady state, and these errors change with the temperature t. 36 geometrical and thermal erroneous elements of grinder were contained[6].
1) When column B6 moving, 6 erroneous elements were analyzed, i.e. linear displacement error ΔX(x, t), straight line error
and
along Y6, Z6-axis direction, roll error α(x, t), pitch error β(x, t) and yaw error γ(x, t).
2) When headstock B7 moving, 6 erroneous elements were analyzed, i.e. linear displacement error ΔY(y, t), straight line error
and
along X7, Z7-axis direction, roll error β(y, t), pitch error α(y, t) and yaw error γ(y, t).
3) When machine saddle B2 moving, 6 erroneous elements were analyzed, linear displacement error ΔZ(z, t), straight line error
and
along X2, Y2-axis direction, roll error γ(z, t), pitch error α(z, t) and yaw error β(z, t).
4) When work piece spindle B4 rotating, 6 erroneous elements were analyzed, i.e. motion error ΔX(θx, t), ΔY(θx, t) and ΔZ(θx, t) along coordinate system S4 direction, angle errors α(θx, t), β(θx, t) and γ(θx, t) circling coordinate system S4.
5) When work table B3 rotating, 6 erroneous elements were analyzed, i.e. motion error ΔX(θx, t), ΔY(θy, t) and ΔZ(θz, t) along coordinate system S3 direction, angle errors α(θy, t), β(θy, t) and γ(θy, t) circling coordinate system S3.
6) When wheel spindle B8 rotating, 6 erroneous elements were analyzed, i.e. motion error ΔX(θz, t), ΔY(θz, t) and ΔZ(θz, t) along coordinate system S8 direction, angle errors α(θz, t), β(θz, t) and γ(θz, t) circling coordinate system S8.
3.2 Establishment of transformation matrix consider- ing errors between two grinder system neigh- boring bodies
According to the above analysis, when grinder base coordinate system S1 moving x along X1-axis, its reality homogeneous transformed matrix should be as follows[6,14-15]:
(2)
where α(x, t), β(x, t), γ(x, t), ΔX(x, t),
and
include both of their geometric and thermal errors.
Similarly, transformation matrices were obtained between lathe bed B1 and machine saddle B2, and between column B6 and headstock B7.
(3)
(4)
With the influence of the manufacturing and the assembly errors, displacements and its inclinations lay in the actual rotation axis and the ideal rotation axis. The transformation matrix was listed when grinder system grinding wheel spindle B8 rotating [θZ+γ(θZ, t)], where γ(θZ, t) is the error when grinding wheel circling C-axis(Z7 direction) around the neighboring body headstock B7.
(5)
In formula (5): θZ=θZ(t), γ=γ(θZ, t), α=α(θZ, t), β=β(θZ, t), ΔXz=ΔX(θZ, t), ΔYz=ΔY(θZ, t), ΔZz=ΔZ(θZ, t).
Similarly, transformation matrices were obtained between machine saddle B2 and work table B3, between work table B3 and the work piece spindle B4.
(6)
(7)
3.3 Establishment of error model of grinder
1) If all kinds of errors are zero in machine processing process, tool point space coordinate system S9 and work piece space coordinate system S5 are superposition. Actually, all kinds of errors lead to the separation between the tool point space coordinates and the work piece space coordinate. So the coordinate transformation matrix between tool point and the work piece is the error model matrix.
According to the multi-body system theory and the grinder structure in Fig.1, the error model of grinder was obtained as
(8)
where
.
2) Based on small erroneous supposition, the synthesis error matrix E″ was expressed as
(9)
Deploying Eqn.(8) and omitting two order and more small amounts, then combining with Eqn.(9), the error synthesis model of three positions and three angles of grinder were obtained. As a result of paper length, the error synthesis model expressions were abbreviated.
4 Analysis of geometric errors rules of grinding wheel tool point and spiral bevel gear
Because processing error mainly comes from grinding wheel spindle movement pair and the thermal error, these errors were analyzed according to the error synthesis model.
With the influence of the manufacture and the assembly errors, the relationships between six degrees of freedom errors (as known) of grinding wheel spindle coordinate system {X8, Y8, Z8} and six degrees of freedom errors of grinding wheel tool point coordinate system {X9, Y9, Z9} due to the grinding wheel circling C-axis, grinding wheel moving along X-axis and grinding wheel moving along Y-axis are shown in Fig.4.
1) When grinding wheel revolving around C-axis, Figs.4(a) and (f) show that angle error circling X9-axis and translation error along Z9-axis direction are fixed values that will have an influence on the helix angle and tooth addendum. Figs.4(b) and (c) show that angle errors circling Y9, Z9-axis can be omitted because they are very small. But translation errors along X9, Y9-axis direction are larger and have a great influence on the spiral bevel gear helix angle, pitch, tooth thickness and tooth socket, as shown in Figs.4(d) and (e).
2) When grinding wheel moving along X-axis, Fig.4(f) shows that translation error along Z9-axis is larger and has a great influence on tooth addendum error. But Figs.4(a) and (b) show that angle errors circling X9-axis and Y9-axis are also larger and have a great influence on helix angle and tooth profile of the spiral bevel gear. Direction translation error along the Y9-axis is bigger and has a great influence on pitch, tooth thickness and tooth socket of the spiral bevel gear, as shown in Fig.4(e). Angle error circling Z9-axis will have an influence on pitch of the spiral bevel gear as shown in Fig.4(c), and translation error along X9-axis will have an influence on helix angle error of the spiral bevel gear, as shown in Fig.4(d).
3) When grinding wheel moving along Y-axis, Fig.4(f) shows that translation error along Z9-axis direction is larger and has a great influence on tooth addendum error. Figs.4(a) and (b) show that angle errors circling X9, Y9-axis are larger and have a great influence on helix angle and tooth profile errors of the gear. Figs.4(d) and (e) show that translation errors along X9, Y9-axis are also larger and have a great influence on the helix angle, pitch, tooth thickness and tooth socket of the gear. Angle error along Z9-axis will have an influence on gear pitch error, as shown in Fig.4(c).
On the other hand, Fig.4(a) shows that the angle error is -0.087 2 rad (“-” represents the direction) when grinding wheel circling with C-axis, and the angle error circling X9-axis is the maximal of three kinds of movement. Fig.4(b) shows that the angle error is from
to
rad when grinding wheel spindle moving along X, Y-axis, and the angle error circling Y9-axis is the maximal of three kinds of movement. Fig.4(c) shows that the angle error is from
to
and from
to
rad respectively when grinding wheel spindle moving along X, Y-axis, and the angle error circling Z9-axis is the maximal of three kinds of movement. Fig.4(d) shows that the translation error is from 0.100 0 μm to 2.700 1 μm when grinding wheel circling with C-axis, and the translation error along X9-axis is the maximal of three kinds of movement. Fig.4(e) shows that the translation
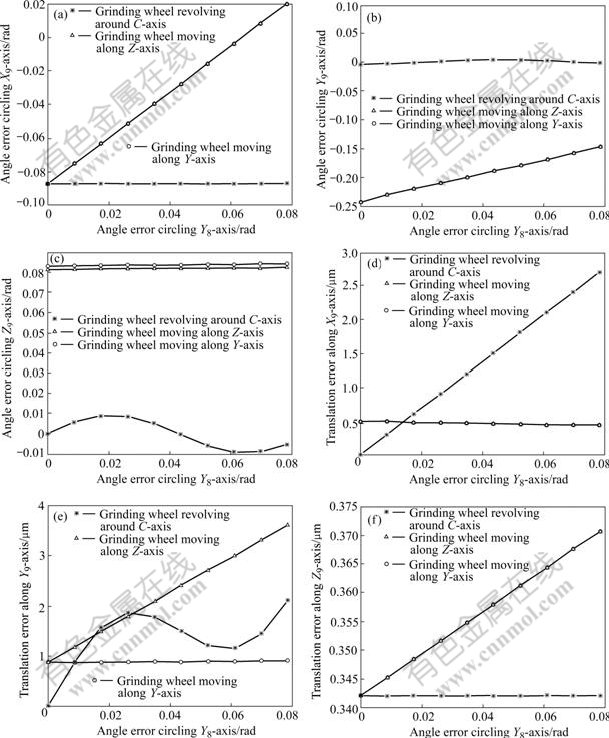
Fig.4 Analysis of angle error circling X9-axis (a), angle error circling Y9-axis (b), angle error circling Z9-axis (c), translation error along X9-axis (d), translation error along Y9-axis (e) and translation error along Z9-axis (f)
error is from 0.866 0 to 3.605 3 μm when grinding wheel moving along X-axis, and the translation error along Y9-axis is the maximal of three kinds of movement. Fig.4(f) shows that the translation error is from 0 μm to
when grinding wheel spindle moving along X, Y-axis, and the translation error along Z9-axis is the maximal of three kinds of movement.
But among six errors, angle errors circling X9, Z9-axis and translation errors along X9, Y9-axes are larger. It can explain that these angle and translation errors will have a great influence on the helix angle, pitch, tooth thickness and tooth socket.
In order to confirm the error synthesis model is true or not, the grinding wheel spindle translation errors along X, Y-axis were measured by Doppler displacement meter. The results are shown in Figs.5 and 6.
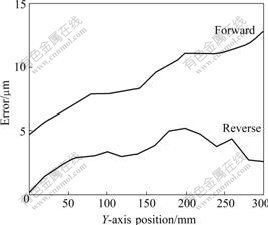
Fig.5 Translation error along Y-axis
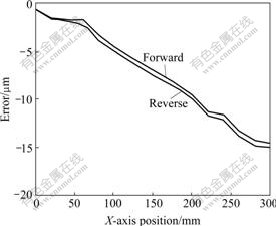
Fig.6 Translation error along X-axis
By comparing respectively Fig.5 and Fig.6 with Fig.4(e)(“○” represents the curve) and Fig.4(d) ( “Δ” represents the curve), their errors increase or reduce gradually, and they are the approximate linear variations. So, the above model is correct.
5 Conclusions
1) The multi-body system theory and Denavit- Hartenberg HTM are used to establish synthesis error mathematical model of the spiral bevel gear grinder with all kinds of erroneous source.
2) The relationships between six degrees of freedom errors of grinding wheel spindle coordinate system and six degrees of freedom errors of grinding wheel tool point coordinate system are analyzed when the grinding wheel revolving around C-axis, grinding wheel moving along X-axis and grinding wheel moving along Y-axis.
3) In order to increase the spiral bevel gear’s machining precision and reduce the errors of the helix angle, pitch, tooth thickness and tooth socket of spiral bevel gear, it should compensate angle errors circling X9, Z9-axis and translation errors along X9, Y9-axis.
4) It provides a theoretical basis for the design and the error compensation of six-axis NC spiral bevel gear grinder.
References
[1] SHIH Y P, FONG Z H. Flank modification methodology for face-hobbing hypoid gears based on ease-off topography [J]. Journal of Mechanical Design, 2007, 129(12): 1294-1302.
[2] LIN C Y, TSAY C B, FONG Z H. Computer-aided manufacturing of spiral bevel and hypoid gears with minimum surface deviation [J]. Mech Mach Theory, 1998, 33(6): 785-803.
[3] LIN C Y, TSAY C B, FONG Z H. Computer- aided manufacturing of spiral bevel and hypoid gears by applying optimization techniques [J]. Journal of Materials Processing Technology, 2001, 114: 22-35.
[4] FAN Sheng-bo, WANG Tai-yong, WANG Wen-jin, WANG Wen-jin, LENG Yong-gang. Prediction of diameter errors compensation in bars turning [J]. Journal of Central South University of Technology, 2005, 12(S2): 264-268.
[5] LEI W T, SUNG M P. NURBS-based fast geometric error compensation for CNC machine tools [J]. Inter Mach Tools Manufact, 2008, 48: 1199-1213.
[6] SRIVASTAVA A K, VELDHUIS S C, ELBESTAWIT M A. Modeling geometric and thermal errors in a five-axis CNC machine tool [J]. Inter J Mach Tools Manufact, 1995, 35(9): 1321-1337.
[7] LIN Y, SHEN Y. Modeling of five-axis machine tool metrology models using the matrix summation approach [J]. The International Journal of Advanced Manufacturing Technology, 2003, 21: 243-248.
[8] BOHEZ E L J. Compensating for systematic errors in 5-axis NC machining [J]. Computer-Aided Dsign, 2002, 34: 391-403.
[9] OKAFOR A C, ERTEKIN Y M. Derivation of machine tool error models and error compensation procedure for three axes vertical machining center using rigid body kinematics [J]. Inter J Mach Tools Manufact, 2000, 40: 1199-1213.
[10] LEE J H, YANG S H. Measurement of geometric errors in a miniaturized machine tool using capacitance sensors [J]. Journal of Materials Processing Technology, 2005, 165: 1402-1409.
[11] YANG Hong, NI Jun. Dynamic neural network modeling for nonlinear, nonstationary machine tool thermally induced error [J]. Inter J Mach Tools Manufact 2005, 45: 455-465.
[12] YANG Hong, NI Jun. Adaptive model estimation of machine-tool thermal errors based on recursive dynamic modeling strategy [J]. Inter J Mach Tools Manufact, 2005, 45: 1-11.
[13] ZHAO Hai-tao, YANG Jian-guo, SHEN Jin-hua. Simulation of thermal behavior of a CNC machine tool spindle [J]. Inter J Mach Tools Manufact, 2007, 47: 1003-1010.
[14] FLORUSSEN G H J, DELBRESSINE F L M, VAN DE MOLENGRAFT M J G, SCHELLEKENS P H J. Assessing geometrical errors of multi-axis machines by three-dimensional length measurements [J]. Measurement, 2001, 30: 241-255.
[15] TONG Heng-chao, YANG Jian-guo, LIU Guo-liang, WANG Xiu-shan, LI Yong-xiang. The volumetric error modeling technique of the two-axis system in an NC lathe [J]. Journal of Shanghai Jiaotong University, 2006, 40(7): 1213-1217. (in Chinese)
(Edited by YANG Hua)
Foundation item: Project(2005CB724104) supported by the Major State Basic Research Development Program of China; Project(1343-77202) supported by the Graduate Students Innovate of Central South University
Received date: 2008-03-20; Accepted date: 2008-05-19
Corresponding author: YAN Hong-zhi, Professor, PhD; Tel: +86-731-8879351; E-mail: yhzcsu@mail.csu.edu.cn