J. Cent. South Univ. Technol. (2008) 15(s1): 261-265
DOI: 10.1007/s11771-008-359-2

Dynamic damping property of magnetorheological elastomer
LI Jian-feng(李剑锋), GONG Xing-long(龚兴龙)
(CAS Key Laboratory of Mechanical Behavior and Design of Materials, Department of Modern Mechanics,
University of Science and Technology of China, Hefei 230027, China)
Abstract: Magnetorheological elastomer (MRE) is a new kind of smart materials, its dynamic mechanic performances can be controlled by an applied magnetic field. MRE is usually used as a stiffness-changeable spring in the semi-active vibration absorber. In order to get perfect vibration control effect, low dynamic damping of MRE is need. But the dynamic damping of MRE was not studied deeply in the past. The dynamic damping of MRE was studied and analyzed. The influences of different test conditions including test strain amplitude, test frequency and test magnetic field were deeply studied. MRE sample and pure silicone rubber sample were prepared and tested under different conditions. The test results show that the main source of dynamic damping is the friction between iron particles and rubber matrix. And the friction is mainly influenced by the strain amplitude and test magnetic field.
Key words: magnetorheological elastomer; dynamic damping; friction
1 Introduction
Magnetorheological (MR) materials including MR fluids, MR elastomer and MR foams[1] are important branchs of smart materials. MRE have good MR effects, the mechanical properties can be controlled by a magnetic field. The also have good mechanical performance for using rubber as matrix. Recently, MRE attracted considerable interests, and many applications of MRE were reported[2-5].
MRE was used as stiffness-changeable spring in semi-active vibration absorber[6]. Vibration absorber is kind of machine used for vibration control. It has a vibration system inside, including spring and vibration mass. MRE was used as the spring device. When MRE was fixed on the vibration object, the vibration energy will be transferred to the vibration system of the vibration absorber. In order to get perfect vibration control effect, the energy transfer ratio between the energy transferred and the total energy is good. The low dynamic damping of spring is need to get good energy transfer ratio. So, in order to get perfect vibration control effect, the dynamic damping of MRE should be controlled to lower.
The dynamic damping property of MRE was studied deeply. In the past, the dynamic damping of MRE is considered to be little change under different magnetic field[7-8]. MRE is prepared based on rubber, which rubber is a kind of viscoelastic materials. When MRE works under a dynamic stress, it will also act as a kind of viscoelastic materials. So, the dynamic properties of MRE are influenced strongly by test conditions. But in the past, the influence of test conditions was also little studied.
In this article, the dynamic damping property was studied. The influence of test conditions was discussed. MRE sample and pure silicone rubber sample were prepared and tested using a rheometer machine. These samples were tested under different test conditions and their results were also analyzed. The results show that the friction between iron particles and rubber matrix is main source for dynamic damping of MRE.
2 Experimental
2.1 Materials fabrication
The iron powder was carbonyl iron powder CN purchased from the BASF Company. The rubber matrix used was MVQ 110-2 (Dong Jue Fine Chemicals, Nanjing Co, Ltd). Double methyl double benzoyl hexane (DMDBH) from the Shenzhen Gujia Company was used as vulcanized agent. Di-2-ethylhexyl phthalate (DOP) from Shanghai Reagent Factory was used as plasticizer. The HTV rubber was first mixed with iron powders, silicone oil and vulcanized agent with a double-roll mill.
During this process, the magnetic field was set at 1 T, the temperature was 120 ℃. After this process, the mold with mixture was placed on a flat vulcanizer for vulcanizing. The mass continents of MRE sample were that HTV silicone rubber was 17.64%, iron powders was 80%, DOP was 2%, and vulcanized agent was 0.36%. In order to compare, a kind of pure silicone rubber sample was also prepared. The continents of pure silicone rubber sample were HTV silicone rubber 98.04% and vulcanized agent 1.96%.
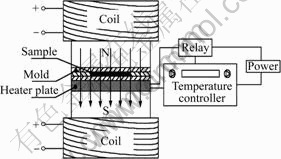
Fig.1 Schematic diagram of PS device
2.2 SEM images
The microphologies of samples were taken using a FE SEM machine from FEI Co. (model Sirion200). The accelerating voltage was set at 5 kV. All the samples, were coated with a thin layer of gold before observation.
2.3 Dynamic shear test
An Anton Paar physical MCR301 rheometer operated in either a stress or strain-control mode with an accessory of magnetorheological device MRD180 was used to study the dynamic properties of MRE in different magnetic fields. A fluid circulator with water is used to control the temperature of sample. In this paper, the temperature was set to 25 ℃ for all tests. The photograph of the rheometer was shown in Fig.2. The principle structure of the MRD-device was shown in Fig.3. A parallel-plate measuring system with a diameter of 20 mm was used at a gap of 1 mm. Oscillation tests were taken to investigate the viscoelastic properties.
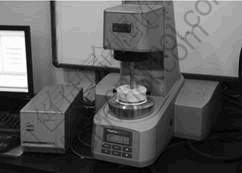
Fig.2 Photo of rheometer
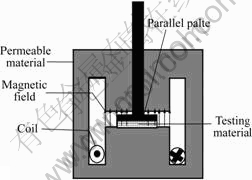
Fig.3 Principle diagram of MR-device of rheometer
3 Results and analysis
3.1 Test strain amplitude
In order to study the influence of strain amplitude, the MRE sample was tested at fixed frequency of 10 Hz and without applied test magnetic field. The test strain amplitude was 0.01%-100%. Two samples were tested by the MRE and the pure silicone rubber. The test results are shown in Fig.4.
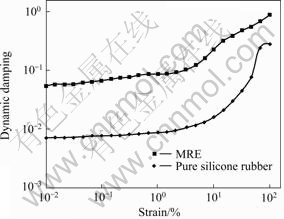
Fig.4 Change curves of dynamic damping with strain amplitude of MRE
From Fig.4, it can be seen that the dynamic damping of the two samples increases with the increase of the strain amplitude. When the strain amplitude is 0.01%, the dynamic damping of MRE is 0.056, and that of pure silicone rubber is 0.007. When the strain amplitude is 100%, the dynamic damping of MRE increases to be 0.895, and that of pure silicone rubber is 0.269. It can also be found that the dynamic damping of MRE is much larger than that of pure silicone rubber.
3.2 Test frequency
In this section, the MRE sample was tested with fixed strain amplitude 1% and without applied test magnetic field. The test frequency was 1-90 Hz. The MRE and the pure silicone rubber were tested. The test results are shown in Fig.5.
From Fig.5, it can be seen that the dynamic damping of MRE does not change with the change of test frequency. While the dynamic damping of pure silicone rubber has a great change with the change of test frequency. The lowest dynamic damping is about 0.0745 and the highest one is 0.086. The lowest dynamic damping value of pure silicone rubber is about 0.001 and the highest one is 0.016. It can also be found that the dynamic damping of MRE is much larger than that of pure silicone rubber.

Fig.5 Change curves of dynamic damping of MRE with frequency
3.3 Test magnetic field
In order to study the influence of test magnetic field, the MRE sample was tested using the rheometer machine with fixed strain amplitude of 1% and frequency of 10 Hz but different test magnetic field. The test results are shown in Fig.6.
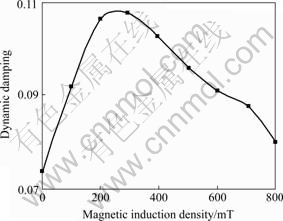
Fig.6 Change curve of dynamic damping of MRE with test magnetic field
It can be seen from Fig.6 that the dynamic damping of MRE is influenced by the test magnetic field greatly. When test magnetic field is below 200 mT, the dynamic damping of MRE increases with the change of test magnetic field. When test magnetic field is lager than 200 mT, the dynamic damping decreases with the increase of the test magnetic field. It means that there is a damping peak at about 200 mT.
4 Discussion
MRE is kind of complex materials with iron particles dispersed in rubber matrix. There are mainly two kinds of dynamic damping source for MRE. One is from the rubber matrix, and the other one is from the friction between iron particles and rubber matrix. Comparing the dynamic damping of MRE and pure silicone rubber, it can be found that dynamic damping of MRE is much lager than that of pure silicone rubber. So, it means that the dynamic damping of MRE meanly comes from the friction between iron particles and rubber matrix. When the materials are prepared, iron particles are blend into silicone rubber matrix. Iron particles are packed into rubber molecule, and it can be seen from the SEM image (see Fig.7). When iron particles and rubber matrix are different kinds of materials, they do not have perfect surface connection. Iron particles are partly connected with rubber molecules. When MRE are under dynamic stress, rubber matrix and iron particles will move together, but iron particles would not move as quickly as the rubber molecules. And there would be some relative shift between rubber molecule and iron particles. It can be seen from Fig.8 that there is friction between iron particles and rubber molecules. And it is the main source of dynamic damping of MRE. It can be found that the larger the test strain amplitude is, the larger the relative shift is. So, when test strain amplitude is larger, the dynamic damping of MRE will increase.
、
Fig.7 SEM image of MRE
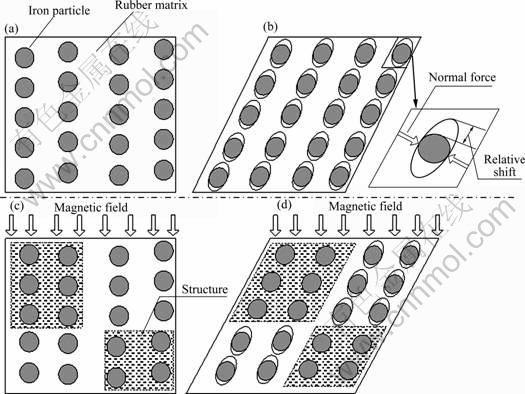
Fig.8 Schematic diagram of structures of MRE
When MRE is tested in different magnetic fields, the friction between iron particles and rubber molecules will change. It is the reason that the dynamic damping of MRE changes with the change of test magnetic field. The friction force F of MRE can be simply expressed as
. There are two parameters controlling the friction F. One is the strength of single friction force f between single particle and rubber. The other one is the number of single friction force n. When applying magnetic field, both the two parameters will change. When applying test magnetic field, the iron particles in MRE would be magnetized, and there would be interaction between iron particles. It will increase with the increase of the test magnetic field, until it reaches a saturation value. It is known that the single friction force f between two objects is direction proportion with the normal force F′. The normal force F′ is strengthened by the interaction between particles. So the interaction between iron particles increases the single friction force f. When the interaction between particles increases, the particles nearby will connect and form a unit structure (shown in Fig.8(c)). The kind of structure formed because of magnetic force will move as a unit part and the iron particles inside will not shift relatively. So there is no inner friction inside this structure. It means that the number of single friction force n will decrease with structure forming. So when test magnetic field increases, the single friction force f will increase but the number of it will decrease.
The dynamic damping of MRE is decided by the change of the single force strength f and the number of single force n caused by the increase of test magnetic field. When test magnetic field is weak, the number of structure of particles formed is small. Under this situation, the influence of increasing single friction strength f is stronger than the influence of decreasing the number of single friction force n. So when test magnetic field is weak, the dynamic damping of MRE will increase with the increase of the test magnetic field. When the test magnetic field is high, the number of structure of particles formed is much lager. Under this situation, the influence of increasing single friction strength f is weaker than the influence of decreasing the number of single friction force n. So, when test magnetic force is high, the dynamic damping of MRE will decrease with the increase of test magnetic field. So, the dynamic damping peak at about 200 mT appears because of the development of the two parameters with the increase of test magnetic field.
5 Conclusions
Three test conditions including strain amplitude, frequency and magnetic field were studied in this article. The strain amplitude and magnetic field influence the dynamic damping of MRE greatly and the frequency influence the dynamic damping of MRE little. The dynamic damping will increase with the increase of the strain amplitude. The change of dynamic damping caused by applied magnetic field is complex. When the magnetic field is weak, the dynamic damping will increase with the increase of the magnetic field. When the magnetic field is strong, it will decrease with the increase of magnetic field. There is a damping peak at around 200 mT. These test results were analyzed through studying the friction between iron particles and rubber matrix. And the results show that the mainly source of dynamic damping of MRE is the friction between particles and rubber.
References
[1] RABINOW J. The magnetic fluid clutch [J]. AIEE Transactions, 1948, 67: 1308-1315.
[2] JOLLY M R, BENDER J W, CARLSON J D. Properties and applications of commercial magnetorheological fluids [J]. Journal of Intelligent Material Systems and Structures, 1999, 10(1): 5-13.
[3] LOKANDER M, STENBERG B. Improving the magnetorheological effect in isotropic magnetorheological rubber materials [J]. Polymer Testing, 2003, 22: 677-680.
[4] BELLAN C, BOSSIS G. Field dependence of viscoelastic properties of MR elastomers [J]. International Journal of Modern Physics B, 2002, 16(17/18): 2447-2453.
[5] DAVIS L C. Model of magnetorheological elastomers [J]. Journal of Applied Physics, 1999, 85(6): 387-396.
[6] DENG H X, GONG X L, WANG L H. Development of an adaptive tuned vibration absorber with magnetorheological elastomer [J]. Smart Materials and Structures, 2006, 15: N111-N116.
[7] GINDER J M, NICHOLS M E, ELIE L D, TARDIFF I L. Magnetorheological elastomers: Properties and applications [C]// Part of the SPIE, Conference on Smart Materials Technologies. California: Newport Beach, 1999, 3675: 131-138.
[8] GINDER J M, SCHLOTTER W F, NICHOLS M E. Magnetorheological elastomers in tunable vibration absorbers [C]// INMAN D J. The SPIE Conference on Smart Structures and Materials: Damping and Isolation. California: Newport Beach, 2001: 103-110.
(Edited by LI Yan-hong)
Foundation item: Project (10672154) supported by the National Natural Science Foundation of China; Project (20050358010) supported by the Specialized Research Fund for the Doctoral Program of Higher Education of China
Received date: 2008-06-25; Accepted date: 2008-08-05
Corresponding author: GONG Xing-long, Professor; Tel: +86-551-3600419; E-mail: gongxl@ustc.edu.cn