
Interface reaction and thermodynamic analysis on
Al2O3-SiO2(sf)/AZ91D composite
LI Wen-fang(李文芳)1, LIU Guan-jun(刘贯军)1,2, PENG Ji-hua(彭继华)1, DU Jun(杜 军)1
1. College of Mechanical Engineering, South China University of Technology, Guangzhou 510640, China;
2. Department of Mechanical and Electronic Engineering, Henan Institute of Science and Technology,
Xinxiang 453003, China
Received 28 July 2006; accepted 15 September 2006
Abstract: Al2O3-SiO2(sf)/AZ91D composite was fabricated by squeezing infiltration using preform made of crystallized aluminum silicate short fibers as reinforcement and aluminum phosphate as binder. The interfacial reaction products were investigated by optical microscopy, X-ray diffractometry, scanning electron microscopy, and the thermodynamics was discussed. It is shown that alumina silicate fibers are ideal candidates for the reinforcement of the Mg alloy matrix composites, and the perfect strong interfaces were formed by the chemical reaction between Mg in the magnesium alloy matrix and aluminum phosphate binder through generation of MgO particles. In addition, brittle Mg2Si phase was precipitated at the interface through the reaction between amorphous SiO2 and Mg in the magnesium alloy matrix, which affects the mechanical property of the composite.
Key words: Al2O3-SiO2(sf)/AZ91D composite; magnesium matrix composite; interface reaction; alumina silicate short fiber; aluminum phosphate binder; thermodynamic analysis
1 Introduction
Magnesium alloys are the lightest among structural metal materials. Magnesium matrix composites are recognized as green environment-friendly materials in the 21st century due to their high specific strength and specific stiffness[1-3]. However, the practical appli-
cation of magnesium matrix composites is mainly located in the field of sport, space-aeronautical craft and other advanced weapon, because of high cost of fabrication. In fact, the high cost of fabrication of magnesium matrix composites mainly comes from reinforcement, such as Al2O3 fiber, SiC fiber, BC4 fiber, C fiber, SiC whisker and so on. It is a trend to reduce the cost of reinforcements and develop new kind of reinforcement with high ratio of property to cost. Crystallized alumina silicate fiber has lower cost and better physical and mechanical properties, so it has potential as reinforcement in magnesium matrix composites[4]. Up to now, less research focuses on magnesium alloy matrix composites reinforced with alumina silicate short fibers than aluminum alloy matrix composites[5-6]. In this study, the interface reaction and interface binding between magnesium matrix and alumina silicate fibers were studied by thermodynamics, XRD and SEM. The feasibility on fabrication of AZ91D matrix composite reinforced with alumina silicate short fibers was evaluated, which will provide theoretic gist to farther investigation in the field.
2 Experimental
Alumina silicate short fiber preform was made using Al(H2PO4)3 solution as binder and crystallized aluminum silicate short fibers as reinforcement by mixing, pressing molding, airing, baking and calcining at 800 ℃ for 3 h. AZ91D alloy (the composition shown in Table 1) was melted and poured into a die with constant preheat temperature at 760 ℃. Al2O3-SiO2(sf)/
AZ91D composite was fabricated by squeezing infiltr-
ation .
The alumina silicate short fibers and others phases were extracted from the composite by NH4Cl water solu- tion to investigate little interfacial reaction products, and its X-ray diffraction spectrum was gained by Philipx’pert X-ray diffraction instrument. Furthermore, the preform and the composite were analyzed by the same method for comparison with it. In order to illuminate the extent of the interfacial reaction, the morphology from the fibers extracted and fracture surface of impact specimen of the composite were analyzed by scanning electronic microscopy.
Table 1 Compositions of AZ91D alloy (mass fraction, %)

3 Results and discussion
Fig.1 shows XRD pattern from the preform using Al(H2PO4)3 solution as binder, showing that there exists AlPO4 phase, no Al(H2PO4)3 in the preform. This is because Al(H2PO4)3 undergoes a calcination process from room temperature to 800 ℃ and becomes AlPO4, which strengthens the preform to support the pressure from the liquid metal during the infiltration process. There are two possible sources of SiO2 phase: 1) It came from the crystallizing process of alumina silicate fibers when there is a high SiO2 composition in the fibers; 2) It might be one of the reaction products of alumina silicate fiber and little H3PO4 from weakly acidic Al(H2PO4)3 solution, shown as equality (1). A thin amorphous SiO2 layer covering alumina silicate fibers reported in Ref.[7] could not be found by the XRD testing instrument.
3Al2O3.2SiO2+6H3PO4?6AlPO4+2SiO2+9H2O,
DG1 000 K=-627 kJ (1)
Fig.2 shows the microstructure of Al2O3-SiO2(sf)/
AZ91D composite fabricated. It reveals that the alumina silicate short fibers are evenly distributed on the metal matrix, which ensures stable mechanical properties of the composite.
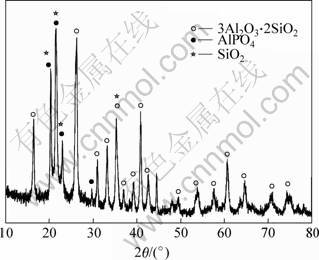
Fig.1 XRD pattern of preform made from alumina silicate fibers and aluminum phosphate
X-ray diffraction pattern of Al2O3-SiO2(sf)/AZ91D composite is shown in Fig.3. It reveals that there are at least MgO, Mg2Si and Mg17Al12 in the composite besides alumina silicate fibers and Mg. Among the phases, Mg17Al12 comes from AZ91D alloy matrix, which is a kind of aging phase. MgO and Mg2Si are interfacial chemical reaction products, shown in Eqns.(2) and (3)[8-9]. Firstly, Mg element in the molten AZ91D alloy reacts with binder AlPO4 and produces MgO during the squeezing infiltration process. With reducing binder layer, Mg element reacts with amorphous SiO2 on surface of the fibers and produces Mg2Si and MgO. Mg2Si is precipitated around the fibers as Chinese-script structure, as shown in Fig.2.
AlPO4+4Mg?4MgO+Al+P, DG1 000 K=-627 kJ (2)
SiO2+4Mg?2MgO+Mg2Si, DG1 000 K=-890 kJ (3)
According to Eqn.(4), MgAl2O4 should be produced, but it is not found in Fig.3. It is possible that the amount of MgAl2O4 is too little to be found by X-ray diffracto-meter. In order to confirm whether MgAl2O4 phase exists, reaction products besides the alumina silicate fibers are extracted from the composite with NH4Cl water solution. As a result, MgAl2O4 phase is found among the extractant by the XRD testing instrument, as shown in Fig.4. In addition, by comparing Fig.4 with Fig.1, it is found that the location of the diffraction peaks of the AlPO4 phase is different from each other, it may be because the crystal lattice of AlPO4 is changed while the preform is preheated and infiltrated during squeezing infiltration.
5Mg+2Al+2SiO2?MgAl2O4+2Mg2Si,
DG1 000 K=-578 kJ (4)
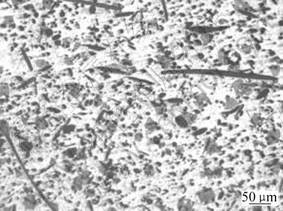
Fig.2 Microstructure of Al2O3-SiO2(sf)/AZ91D composite
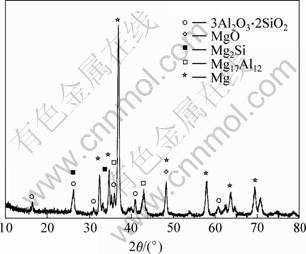
Fig.3 XRD pattern of Al2O3-SiO2(sf)/AZ91D composite
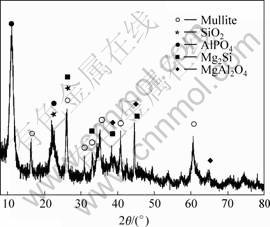
Fig.4 X-ray diffraction pattern of extractant from Al2O3-SiO2(sf)/AZ91D composite
Mg element is so active under high temperature that it is oxidized easily (see Eqns.(2) and (3)). The impact fractural morphology of the composite was observed by LEO 1530VP scanning electronic microscope, and the surface morphology of the reinforced fibers(shown in Fig.5(a), it was gained at tectorium of the composite) and its EDS spectrum (shown in Fig.5 (b)) demonstrates that the puckers on the surface of the fibers should be MgO. It is the result of the reaction between Mg and AlPO4 and SiO2 on the surface of the fibers. It is the MgO puckers that strengthen the binding between the fibers and matrix metal.
Fig.6 shows the morphology of fracture section of the composite, showing well binding between the fibers and the metal matrix. Because the interface is strong enough to change the extension direction of cracks into fibers and, no crack is found on the interface between them. In addition, the surface morphology of the reinforced fibers extracted from the composite, as shown in Fig.7, reveals that no visible damage is found on the surface of the reinforced fibers, which accords with the second characteristic of interface reaction from Ref.[10].
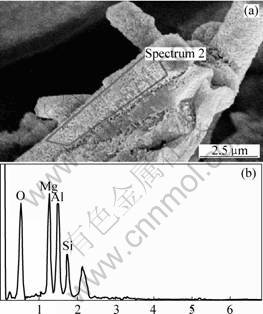
Fig.5 Morphology and superficial constituents of fibers surface: (a) Morphology of fracture of tectorium of composite; (b) EDS spectrum of fiber surface of composite
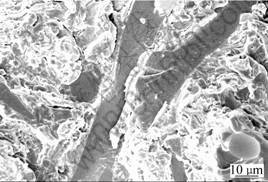
Fig.6 Morphology of fracture surface of Al2O3-SiO2(sf)/AZ91D composite
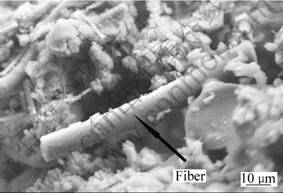
Fig.7 Surface morphology of fibers from Al2O3-SiO2(sf)/AZ91D composite
4 Conclusions
1) Al2O3-SiO2(sf)/AZ91D composite was fabricated by means of complex squeezing infiltration. The consti-
tuent phases of the preform, the composite and fiber extracted from the composite were investigated by XRD. The Microstructure and fractograph of the composite were studied by SEM.
2) Using Al(H2PO4)3 as binder and crystallized alumina silicate as reinforcement, Al2O3-SiO2(sf)/AZ91D composite with an ideal strong interface between AZ91D alloy matrix and short fiber can be made by suitable complex squeezing infiltration process.
3) The ideal interface is due to the uniformly covering of MgO and little MgAl2O4, which are the products of interface chemical reaction between the matrix and the fiber.
References
[1] LI Shu-bo, ZHENG Ming-yi, GAN Wei-min, et al. Hot deformation behavior of SiCw/AZ91D magnesium matrix composite and AZ91D alloy[J]. Acta Materiae Compositae Sinica, 2005, 22(3): 103-108.(in Chinese)
[2] SARAVANAN R A, SUPRAPPA M K. Fabrication and characteriz-
ation of pure magnesium-30 % SiCp particle composite[J]. Mater Sci Eng A, 2000, A276(1/2): 108-116.
[3] BRALOWER P M. Automotive die casting magnesium reviving up for the 21st century[J]. Die Casting, 1997, 41(3): 68-70.
[4] ZHOU Yao-min, LI Xian-gan, CHEN Mei-yi. Crystallized aluminum-silica short fiber reinforced metal matrix composites[J]. Acta Materiae Compositae Sinica, 1995, 12(4): 12-16. (in Chinese)
[5] WU Jing, LI Wen-fang, MENG Ji-long. Study on the mechanical properties of ZL109 matrix composite reinforced with alumina silicate short fiber[J]. Journal of South China University of Technology(Natural Science), 2003, 31(2): 62-65. (in Chinese)
[6] FU Zhi-qiang, MENG Ji-long, LI Wen-fang. Study on the wear properties of ZL101 matrix composite reinforced with alumina silicate short fiber[J]. Mech Eng Mater, 1998, 22(5): 32-34. (in Chinese)
[7] ZHU Pei-nan, WENG Zhen-pei, WU Tian-di. Fine Texture Atlas of Inorganic Non-metal Material[M]. Wuhan: Wuhan University of Technology Press, 1994. (in Chinese)
[8] ZHANG Ming-yi, WU Kun, YAO Cong-kai. Characterization of interfacial reaction in squeeze cast SiCw/Mg composite[J]. Materials Letters, 2001, 47: 118-124.
[9] ZHANG Ming-yi, WU Kun, YAO Cong-kai. Effect ion of interfacial reaction on mechanical behavior of SiCwAZ91 magnesium matrix composites[J]. Mater Sci Eng A, 2001, A318: 50-57.
[10] YE Heng-qiang, ZHU Jing, ZHANG Guo-di, et al. The Interfacial Microstructure and Characteristic of Material[M]. Beijing: Science Press, 1999. (in Chinese)
(Edited by CHEN Wei-ping)
Foundation item: Project(305-E5040440) support by the Natural Science Foundation of South China University of Technology
Corresponding author: LI Wen-fang; Tel: 020-87110201(O); E-mail: mewfli@scut.edu.cn