
Microstructure evolution of processed Mg-Al-Zn alloy by equal channel angular extrusion in semi-solid isothermal treatment
JIANG Ju-fu(姜巨福), LUO Shou-jing(罗守靖)
School of Materials Science and Engineering, Harbin Institute of Technology, Harbin 150001, China
Received 27 March 2006; accepted 20 July 2006
Abstract: Microstructure evolution of processed Mg-Al-Zn alloy by equal channel angular extrusion(ECAE) in semi-solid isothermal treatment was investigated. The results show that with increasing semi-solid isothermal treatment temperature, the α phase solid grain size of processed Mg-Al-Zn alloy by ECAE increases firstly due to coarsening of α phase solid grains, then decreases due to melting of α phase solid grains. With the increase of extrusion passes during ECAE, the α phase solid grain size in the following semi-solid isothermal treatment decreases. The α phase solid grain size of processed Mg-Al-Zn alloy by ECAE under route BC is the smallest, while the α phase solid grain size of processed material by ECAE under route A is the largest. The primary mechanism of spheroid formation depends on the melting of recrystallizing boundaries and diffusion of solute atoms in the semi-solid state.
Key words: magnesium alloy; Mg-Al-Zn alloy; equal channel angular extrusion; isothermal treatment; semi-solid processing
1 Introduction
Thixoforming is one of the best methods regarding manufacture of Mg-Al-Zn alloy components because of its low resistance of deformation compared with solid metal forging and high mechanical properties of formed components compared with liquid metal die casting[1,2]. Thixoforming is one branch of semi-solid processing of alloy, which is the forming process of alloys in the semi-solid state to near net shaped products. It relies on the thixotropic behavior of alloys which have a spheroidal rather than a dendritic microstructure in the semi-solid state. TZIMAS et al[3] studied the evolution of near-equiaxed microstructure in the semisolid state. HAGA et al[4] studied the thixoforming of laminate made from semisolid cast strips. CAMACHO et al[5] carried out some research on the thermodynamic predictions of wrought alloy compositions amenable to semi-solid processing. For thixoforming of magnesium alloy, the most important is to prepare the semi-solid billets, that is, to obtain alloy with non-dendritic, or spheroidal microstructure.
Strain induced and melt activation(SIMA) is a good method for preparing semi-solid billet[6,7]. However, for magnesium alloy, the coarse and non-globular grains often exist in the microstructure of semi-solid billets prepared by common SIMA method, that is, semi-solid isothermal treatment of upsetted cast materials. This is due to the difficulties of obtaining severe plastic deformation with respect to the magnesium alloy in SIMA resulted from the nature of crystal structure[8]. Therefore, a new strain induced technique for SIMA needs to be adopted to obtain severe plastic deformation, by which large deformation and fine grains of processed material can be obtained. Equal channel angular extrusion(ECAE) is a promising technique for obtaining ultra-grained bulk materials with strength and ductility increased through severe plastic deformation [9-12]. During ECAE, a billet is pressed through a die that consists of two channels with equal cross-section, intersecting at some angle φ. Since the cross-sectional shape of billet remains nearly the same, ECAE processing can be repeated for many passes to control the microstructure and properties of the material[13-15].
The microstructure has a great influence on the handling of semi-solid billet and ability to deform alloys in the semi-solid state. It is therefore important to understand the microstructure evolution in semi-solid alloy in relation with thixoforming. The current study represents the spheroidization of processed Mg-Al-Zn alloy by ECAE in semi-solid isothermal treatment in order to prepare Mg-Al-Zn alloy semi-solid billet with fine spheroidal grains and promote the commercial and engineering application of ECAE technique to prepare the semi-solid billet of magnesium alloy.
2 Experimental
The alloy used in the present study was a commercial Mg-Al-Zn alloy, AZ91D, which contained 9% aluminum, 1% zinc, 0.15% Mn, 0.005% Fe, 0.03% Cu, 0.002% Ni and balance Mg. The AZ91D alloy was processed ranging from 1 pass to 4 passes by an equal channel die that consists of two channels with equal cross-section, intersecting at an angle 90?, at 573 K. The experimental cylindrical specimens were processed by ECAE under four processing routes. They are termed A, BA, BC and C according to the rotation about the sample’s longitudinal axis or extrusion direction[16]. Route A refers to pressing the billet repetitively without any rotation; routes BA and BC refer to rotations of 90? in the opposite direction and the same direction between consecutive passes respectively; route C refers to rotating by 180? between each pass. The diameter of equal cross-section channel is 58 mm. The ECAEed, i.e., equal channel angular extrusion processed, material was machined into samples with the height of 10 mm and diameter of 10 mm, which were isothermally treated in semi-solid state.
Based on differential scanning calorimetry(DSC) experimental result, isothermal treatment temperature was determined to vary from 788 to 833 K, corresponding to solid fraction from 0.85 to 0.55. Holding time was selected from 10 min to 25 min. After the samples were isothermally treated, they were quenched quickly in water to keep its microstructure and then observed microstructure by metalloscopy.
3 Results and discussion
3.1 Microstructures of cast and ECAEed Mg-Al-Zn alloys
Fig.1 presents the optical micrographs of cast and four-pass ECAEed under route BC Mg-Al-Zn alloys. As shown in Fig.1(a), the cast material consists of two phases, α and β phase. α phase is magnesium matrix and β phase is Mg17Al12. α phase has the morphology of coarse dendrites with grain size of larger than 200 μm. β phase distributes around the grain boundaries of α phases. As shown in Fig.1(b), when material is four-pass processed under route BC by ECAE, α phase of Mg-Al-Zn alloy is refined heavily and the average grain size of α phase solid grains is about 10 μm. Furthermore, the morphology of α phase changes from dendrite to fine equiaxed grains, which will promote the spheroidization of α phase during the following semi-solid isothermal treatment.

Fig.1 Optical micrographs of cast Mg-Al-Zn alloy (a) and four-pass processed Mg-Al-Zn alloy (b) under route BC at 573 K by ECAE
3.2 Influence of holding time on microstructure evolution
Fig.2 shows the microstructure evolution of ECAEed Mg-Al-Zn alloy in semi-solid isothermal treatment at 803 K. Evidently, a large morphology change of α phase occurs in the Mg-Al-Zn alloy. As shown in Fig.2(a), when the ECAEed material is heated to 803 K and held for 0 min, the morphology of α phase still remains equaixed shape. However, compared with the microstructure of ECAEed material at 573 K, a coarsening phenomenon occurs in the microstructure of ECAEed material only just heated to 803 K. Accordingly, the average grain size is 18 μm. When the ECAEed material is held for 10 min (Fig.2(b)), the morphology of α phase changes evidently, close to spheroidal shape. During the holding process, the whole β phase and some α phase with low melting point become into liquid state. Accordingly, two phases coexist in the material, liquid phase and solid phase. Furthermore, due to solute atoms
Fig.2 Optical micrographs of four-pass processed Mg-Al-Zn alloy under route BC by ECAE after semi-solid isothermal treatment at 803 K for different times: (a) 0 min; (b) 10 min; (c) 15 min; (d) 20 min; (e) 25 min
diffusion between two phases, solid phase, that is, α phase with high melting point, has a trend to spheroidization. At the same time, a coarsening trend also accompanies with spheroidization of α phase. Compared with ECAEed material held 0 min in semi-solid isothermal treatment at 803 K, the average grain size of ECAEed material held for 10 min becomes larger and reaches 22 μm. As shown in Fig.2(c), when the holding time increase to 15 min, the morphology of α phase is closer to spheroidal shape. Accordingly, the spheroidization effect of α phase in material becomes better.
Further solute atoms diffusion between liquid phase and solid phase leads to better spheroidization of α phase. During the solute atoms diffusion, solid phase part with high curvature in the α phase is melted into liquid phase and crystallization mass from liquid phase is deposited on the solid part with low curvature, which leads to the spheroidization of α phase together. As shown in Figs.2(d) and (e), with the increase of holding time in semi-solid isothermal treatment, the grains of ECAEed material will grow evidently. For example, when the holding time is 25 min, the average grain size of ECAEed material is about 45 μm. This demonstrates that suitable holding time is necessary to obtain fine spheroidal solid phase, that is, α phase during semi-solid processing.
3.3 Influence of semi-solid isothermal temperature on microstructure evolution
Fig.3 shows the microstructure evolution of four-pass ECAEed material held for 10 min at various temperatures in semi-solid isothermal treatment. As shown in Fig.3, with increasing semi-solid isothermal temperature, the gain size of α phase increases firstly, then decreases. When ECAEed material is held at 788 K for 10 min in semi-solid isothermal treatment, fine spheroidal solid grains with average grain size of 20 μm occur in the material (Fig.3(a)). The material with fine spheroidal solid grains has desirable ability to flow or fill the die cavity during the following thixoforming. As shown in Fig.3(b), when semi-solid isothermal treatment temperature is elevated to 803 K, the coarsening of α phase occurs in the microstructure of ECAEed material. When two or more particles coalesce, they become interconnected by solid necks and spheroidize by material transport essentially restricted to the neck regions. It differs from the LSW theory which mainly describes the growth of semi-solid alloy with low fraction solid. Furthermore, as shown in Figs.3(a) and (b), the fraction solid does not change evidently. However, when the ECAEed material is held at 823 K and 833 K for 10 min (Figs.3(c) and (d)), the solid fraction decreases evidently, that is, fraction liquid increase evidently. Furthermore, the grain size of α phase also decreases. In fact, there are two important trends during elevating the semi-solid isothermal temperature, growth or coarsening trend of α phase solid grains and melting trend of α phase solid grains due to the elevated temperature. These two trends coexist during elevating the semi-solid isothermal temperature.

Fig.3 Optical micrographs of four-pass processed Mg-Al-Zn alloy under route BC by ECAE after semi-solid isothermal treatment at different temperatures held for 10 min: (a) 788 K; (b) 803 K; (c) 823 K; (d) 833 K
When the semi-solid isothermal temperature is below 823 K, the former trend is predominant, that is, the trend of growth of α phase solid grains is stronger, leading to coarsening of α phase solid grains by coalescence of two or more solid grains (Figs.3(a) and (b)). Otherwise, when the semi-solid isothermal temperature is above 823 K, the latter is predominant, which results in the melting of α phase solid grains and decrease of solid α phase grains (Figs.3(c) and (d)). Furthermore, as shown in Fig.3, when semi-solid isothermal treatment temperature is very high, the microstructure is inhomogeneous, that is, the grain size of solid α grains has large difference, which is unfavorable to the thixoforming and leads to the reduction of mechanical properties of final components. Therefore, the semi-solid isothermal temperature should also be determined properly in semi-solid processing, such as thixoforming and thixocasting.
3.4 Influence of extrusion passes on microstructure evolution
Fig.4 shows the micrographs of ECAEed Mg-Al-Zn alloy for various extrusion passes held at 803 K for 10 min in semi-solid isothermal treatment. As shown in Fig.4, with the increase of extrusion passes in ECAE, the grain size of α phase of ECAEed material in semi-solid isothermal treatment decreases evidently. When the material is processed by ECAE for 1 pass, the average grain size of α phase of ECAEed material in semi-solid isothermal treatment is about 50 μm. With the increase of extrusion passes, the average grain size of α phase of ECAEed material in semi-solid isothermal treatment is 45, 35 and 33 μm, respectively.
Furthermore, the spheroidization effect also becomes better with the increase of extrusion passes. During ECAE, samples can obtain severe plastic by
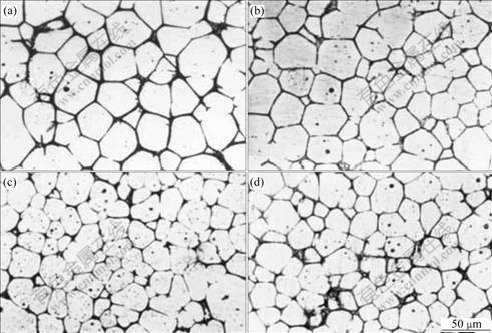
Fig.4 Optical micrographs of ECAEed Mg-Al-Zn alloy held at 803 K for 10 min in semi-solid isothermal treatment for different extrusion passes: (a) 1 pass; (b) 2 passes; (c) 3 passes; (d) 4 passes
increasing the extrusion passes. When the extrusion passes are increased from 1 pass to 4 passes, the obtained severe plastic deformation also increases evidently. Therefore, due to the increase of severe plastic deformation, the refinement effect of grains of cast Mg-Al-Zn alloy become better, leading to finer equiaxed grains occurring in the ECAEed material. It should be noted that these ECAEed material with finer equiaxed grains will result in formation of finer spheroidal α solid grains in the following semi-solid isothermal treatment. This demonstrates that increasing extrusion passes during ECAE is beneficial to the formation of finer spheroidal α solid grains. However, it should be noted that limiting the extrusion passes is very important. As shown in Figs.4(c) and (d), the grain size difference of α phase between three-pass ECAEed and four-pass ECAEed materials in semi-solid isothermal treatment is not very evident. Furthermore, the semi-solid alloy with α phase solid grain size of about 35 or 33 μm has completely satisfied the requirement of semi-solid processing. Therefore, in this method for preparing semi- solid billet or semi-solid alloy, four extrusion passes is suitable to deform semi-solid billet. If the requirements for mechanical properties of final components are not very high, one extrusion pass is also suitable.
3.5 Influence of processed route on microstructure evolution
Fig.5 shows the optical micrographs of four-pass ECAEed material under different processed route held at 803 K for 10 min in semi-solid isothermal treatment. As shown in Fig.5, the α phase solid grains are all fine and their grain size is below 40 μm. This demonstrates that the four-pass ECAEed material under route A can obtain desirable semi-solid billet in the following semi-solid isothermal treatment. However, it should be noted that there exists a little grain size difference among these four optical micrographs. The α phase solid grain size of ECAEed material under route BC is the smallest, the α phase solid grain size of ECAEed material under route A is the largest. This little difference among α phase solid grain sizes is due to the grain size of ECAEed material under different routes. Under route BC, the ECAEed material is refined were and its grain size is the smallest, leading to the smallest α phase solid grain size in the following semi-solid isothermal treatment. Similarly, the ECAEed material is not refined well and its grain size is the largest, leading to the largest α phase solid grain size in the following semi-solid isothermal treatment.
3.6 Formation mechanism of spheroidal α phase
The microstructure evolution mechanism of ECAEed Mg-Al-Zn alloy in semi-solid isothermal treatment differs from other mechanisms of spheroid formation from liquid state, such as dendrite arms breaking off at the roots due to shear forces, dendrite arms melting off at their roots and dendrite arm bending causing dislocation generation, the formation of grain boundaries and grain boundary wetting. Firstly, the starting microstructure of ECAEed Mg-Al-Zn alloy is
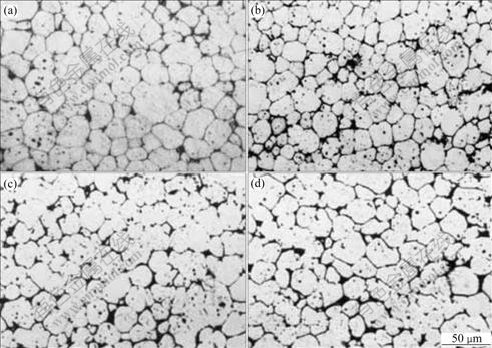
Fig.5 Optical micrographs of four-pass ECAEed Mg-Al-Zn alloy held at 803 K for 10 min in semi-solid isothermal treatment: (a) Route A; (b) Route BA; (c) Route BC; (d) Route C
not coarse dendrites, but fine equiaxed grains. Secondly, the formation of spheroidal grains of ECAEed material in semi-solid isothermal treatment does not depend on the breaking off of dendrites or melting of roots of dendrite. The primary mechanism of spheroid formation depends on the melting of recrystallizing boundaries and diffusion of solute atoms in the semi-solid state. Fig.6 presents the spheroidization process of α phase of ECAEed Mg-Al-Zn alloy in semi-solid isothermal treatment. During ECAE, heavily dynamic resrystalli- zation occurs in severe plastic deformation. As a result, fine equaixed grains are created during the dynamic resrystallization and many recrystallizing boundaries are also created. As shown in Fig.6, when the ECAEed material with many recrystallizing boundaries is held in semi-solid isothermal treatment, the recrystallizing boundaries will be melted firstly.
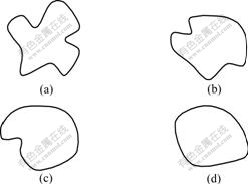
Fig.6 Schematic diagram of spheroidization of α phase of ECAEed Mg-Al-Zn alloy in semi-solid treatment: (a) Equiaxed grain; (b), (c) Spheroidized equiaxed grains; (d) Spheroidal grain
With increasing holding time, the solid α phase is enclosed by liquid phase and strong solute atoms diffusion occurs. With further increasing holding time, due to the diffusion of solute atoms, solid phase part with high curvature in the α phase is melt into liquid phase and crystallization mass from liquid phase is deposited on the solid part with low curvature, which lead to the spheroidization of α phase together. During the spheroidization of α phase of ECAEed material, the coarsening or growing trend also coexist. The coarsening of ECAEed material mainly depends on the coalescence of two or more solid α phase grains.
4 Conclusions
1) When ECAEed Mg-Al-Zn alloy is held for 10 min, solid α phase has spheroidized and the grain size reaches 22 μm. When ECAEed Mg-Al-Zn alloy was held for 15 min, the semi-solid billet with fine spheroidal α phase solid grains were obtained. Furthermore, with the increase of holding time, evident coarsening phenomenon occurs.
2) With increasing semi-solid isothermal treatment temperature, the grain size of α phase of ECAEed Mg-Al-Zn alloy firstly increases due to the coarsening of α phase solid grains, and then decreases due to melting of α phase solid grains. With increasing extrusion passes during ECAE, the grain size of α phase solid grains in the following semi-solid isothermal treatment decreases.
3) The α phase solid grain size of ECAEed material under route BC is the smallest, the α phase solid grain size of ECAEed material under route A is the largest. The primary mechanism of spheroid formation depends on the melting of recrystallizing boundaries and diffusion of solute atoms in the semi-solid state. During the spheroidization of α phase of ECAEed material, the coarsening or growing trend also coexist. The coarsening of ECAEed material mainly depends on the coalescence of two or more solid α phase grains.
References
[1] CHAYONG S, ATKINSON H V, KAPRANOS P. Thixoforming 7075 aluminium alloys [J]. Mater Sci Eng A, 2005, 390(1/2): 3-12.
[2] LIU D,ATKINSON H V,KAPRANOS P A. Microstructural evolution and tensile mechanical properties of thixoformed high performance aluminium alloys [J]. Mater Sci Eng A, 2003, A361(1/2): 213-324.
[3] TZIMAS E, ZAVALIANGOS A. Evolution of near-equiaxed microstructure in the semisolid state [J]. Mater Sci Eng A, 2000, A289(1/2): 228-240.
[4] HAGA T, KAPRANOS P. Thixoforming of laminate made from semisolid cast strips [J]. J Mater Process Technol, 2004, 157-158(complete): 508-512.
[5] CAMACHO A M, AKINSON H V, KAPRANOS P. Thermodynamic predictions of wrought alloy compositions amenable to semi-solid processing [J]. Acta Mater, 2003, 51(8): 2319-2330.
[6] JAE C C, HYUNG J P. Microstructural characteristics of aluminum 2024 by cold working in the SIMA process [J]. J Mater Process Technol, 1998, 82(1-3): 107-116.
[7] NURSEN S, I E S, METIN Z. Mechanical properties and microstructural evaluation of AA5013 aluminum alloy treated in the semi-solid state by SIMA process [J]. J Mater Process Technol, 2004, 148(1): 103-107.
[8] JIANG J F, LUO S J. Reheating microstructure of refined AZ91D magnesium alloy in semi-solid state [J]. Trans Nonferrous Met Soc China, 2004, 14(6): 1074-1081.
[9] MAHESH S, BEYERLEIN I J, TOME C N. Loading and substructure-induced irreversibility in texture during route C equal channel angular extrusion [J]. Scripta Mater, 2005, 53(8): 965-969.
[10] YU C Y, SUN P L, KAO P W. Mechanical properties of submicron-grained aluminum [J]. Scripta Mater, 2005, 52(5): 359-363.
[11] CONRAD H, JUNG K. On the strain rate sensitivity of the flow stress of ultrafine-grained Cu processed by equal channel angular extrusion (ECAE) [J]. Scripta Mater, 2005, 53(5): 581-584.
[12] SENNONV O N, SENKOVA S V, SCOTT J M, et al. Compaction of amorphous aluminum alloy powder by direction extrusion and equal channel angular extrusion [J]. Mater Sci Eng A, 2005, 393(1-2): 12-21.
[13] HAOUAOUI M, HARTWIG K T, PAYZANT E A. Effect of strain path on texture and annealing microstructure development in bulk pure copper processed by simple shear [J]. Acta Mater, 2005, 53(3): 801-810.
[14] SUN P L, KAO P W, CHANG C P. High angle boundary formation by grain subdivision in equal channel angular extrusion [J]. Scripta Mater, 2004, 51(6): 565-570.
[15] SEGAL V M. Equal channel angular extrusion: from macro- mechanics to structure formation [J]. Mater Sci Eng A, 1999, A271(1/2): 322-333.
[16] HUANG W H, CHANG L, KAO P W, et al. Effect of die angle on the deformation texture of copper processed by equal channel angular extrusion [J]. Mater Sci Eng A, 2001, A307(1/2): 113-118.
(Edited by LONG Huai-zhong)
Foundation item: Projects(50475029, 50605015) supported by the National Natural Science Foundation of China
Corresponding author: JIANG Ju-fu; Tel: +86-451-86415464; E-mail: jiangjufu@hit.edu.cn