
Orthogonal experiment and microstructure analysis on TiC-TiB2 multi-phase ceramic coating prepared by SHS reactive spraying
DU Xin-kang(杜心康)1, 2, WANG Jian-jiang(王建江)1, WANG Tian-min(王天民)2,
LIU Hong-wei(刘宏伟)1, LI Wei-bo(李伟波)1
1. Advanced Materials Institute, Mechanical Engineering College, Shijiazhuang 050003, China;
2. Center of Condensed Matter Physics and Material Physics, Beihang University, Beijing 100083, China
Received 15 July 2007; accepted 10 September 2007
Abstract: Utilizing self-propagating high-temperature synthesis (SHS) reactive spraying technology, the feeding self-combustion agglomerated particles composed of Ti, B4C and C powders, TiC-TiB2 multi-phase ceramic coatings were prepared on the steel substrates. Orthogonal experiment was carried out to optimize the spraying parameters. The phase component and microstructure of the coating fabricated at the optimized parameters were studied by XRD and SEM. The reactive mechanism in flying agglomerated particles was discussed. The optimized conditions, spraying distance of 220 mm, powders delivering gas pressure of 0.3 MPa and preheating temperature of 240 ?C to sprayed particles, were obtained from orthogonal experiment. For the coating, porosity of 2.5% and HV 1 595 are achieved under the optimized parameters. The coatings are mainly composed of TiC0.3N0.7, TiB2 and a little TiO2. The SEM analysis shows the morphology of TiC0.3N0.7 matrix in which the fine granular TiB2 crystals evenly disperse. It is concluded that, as solo reactive units, the agglomerated particles would finally form into the coatings after going through four successive stages in the flame, which are, respectively, pregnant reaction, flight combustion, collision and structure transformation and solidification. The solid diffusion and dissolution-precipitation are the two mechanisms to control the synthesis reaction.
Key words: TiC-TiB2 ceramic coating; SHS reactive spraying; orthogonal experiment; reactive mechanism
1 Introduction
SHS (self-propagating high temperature synthesis) reactive spraying which is a comprehensive technology from SHS and traditional thermal spraying attracted many scholars concerns to produce the ceramic coatings in recent years. A number of self-propagating systems such as Ti-C, Ti-B, Mo-Si, Cr-C, Al-CuO, and Ti-B-N etc[1-4] have been developed. Different from the traditional thermal spraying, SHS reactive spraying process has an exciting characteristic of blazing chemical energy emission from in-situ reaction, by which the reactant particles and ceramic products can even be melted into the liquid droplets. Fused droplets can be atomized and sprayed onto the surface of substrate to form protective ceramic coating with higher density and binding intensity.
Titanium carbide-titanium boride multi-phase ceramic has promising applications for protective armors, tool knife materials, shaping moulds and so on, due to high melting point, high micro-hardness, especially high performance and thermal stability at high temperatures[5-6]. As one of the surface coating material, TiC-TiB2 composite also plays more and more important role in the field of re-manufacture to the mechanical subassembly or equipment[7-8].
Generally, TiC-TiB2 multi-phase ceramic can be chemically synthesized by the reaction between Ti, B4C and C[9]. In this work, taking Ti-B4C-C as combustion system, TiCxNy-TiB2 coating was fabricated on steel substrate by SHS flame spraying. The spraying parameters were optimized by orthogonal experiment. The properties of the coatings were tested. The phase component and microstructure were analyzed. Spraying procedure and reactive mechanism were discussed.
2 Experimental
The chemical purification Ti powders, B4C powders and graphite powders with particle size of less than 20 μm were chosen as reactive raw materials. After dried and sifted, Ti B4C and C powders were mixed in the ball-grinding machine in proper proportion, and then prepared into agglomerated particles in proper size range. The substrate was 45 carbon steel flat sample with dimensions of 50 mm×50 mm×6 mm. The substrate was cleaned by grinding wheel to remove the rust. And then the surface was roughened and preheated before spraying. Ni-Al alloy powders were used as the intermediate.
High energy flame spraying gun was used to prepare coatings. The input energy was the mixture of oxygen and acetylene. The pressures of oxygen and acetylene were adjusted to 0.6 MPa and 0.11 MPa, respectively. During spraying, faint carbide flame was maintained. Nitrogen was used as carrier and sluggish gas. Powder delivering ratio was about 20 g/min.
Three key spraying parameters, namely spraying distance, delivering gas pressure and preheating temperature to agglomerated particles, were optimized by orthogonal experiment.
The ceramic coating sample prepared at optimized conditions was incised along the cross section, and was polished for observation. The phase structure of the coating was investigated by X-ray diffraction (XRD) on a Dmax diffractometer with Cu Kα (40 kV, 20 mA, λ=0.154 06 nm) radiation with the 2θ angles ranging from 10? to 80? in steps of 0.02?. The surface morphology was observed with a JEOL JXA-840 scanning electron microscope (SEM) under 25 kV. Optical microscope was used to quantitatively analyze the porosity of the coatings. The micro-hardness of the coating was tested with MT-4 micro-hardness machine.
3 Results and discussion
Table 1 lists the schedule of the orthogonal test in which the key parameters including spraying distance (A), delivering gas pressure (B) and preheating temperature to agglomerated particles (C) are selected as three factors. And every factor has four levels to be optimized. The porosity and micro-hardness of the coatings are taken as the index points to evaluate the coatings performance under different factors and levels.
Detailed spraying conditions and the property results tested are listed in Table 2. From the mathematical processing of the data, some results can be concluded as follows. First, the factor of delivery gas pressure shows the most notable influence on whichever index point. Then preheating temperature is the relatively remarkable factor comparing with spraying distance. Second, coating with the lowest porosity and the highest micro-hardness would be prepared when 0.3 MPa, 240 °C and 220 mm were selected, respectively, for delivering gas pressure, preheating temperature and spraying distance. Moreover, 2.5% porosity and HV 1 595 micro-hardness were achieved under the optimized spraying parameters.
Table 1 Factors and levels selected for orthogonal experiment
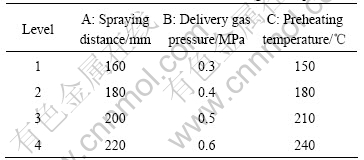
Table 2 Detailed scheme of orthogonal test and property results of sprayed coatings
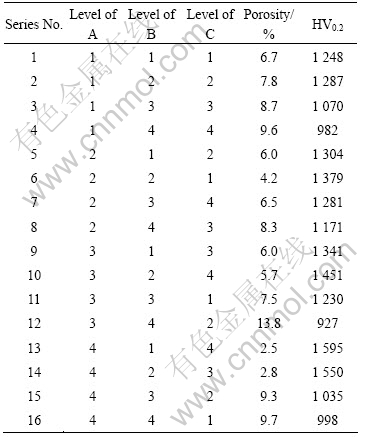
XRD analysis was used to distinguish phase structure of the coating sprayed at the optimized condition. As shown in Fig.1, the diffraction pattern indicates that the coating is mainly composed of TiC0.3N0.7 and TiB2 as well as a little TiO2.
Accordingly, Fig.2 gives the morphology of the microstructure. From Fig.2(a), dense coating with low porosity can be seen. As shown in Fig.2(b), phase distribution can be clearly observed that numerous irregular black TiB2 particles evenly immerse into grey TiC0.3N0.7 matrix.
In SHS reactive flame spraying, chemical combustion and phase transformation synchronously occur and mutually affect with physical process. Once agglomerated particles are fed and dispersed into the flame, acting as solo reactive units, they would finally form into the coatings after going through four successive stages in the flame, which are, respectively, pregnant reaction, flight combustion, collision and structure transformation and solidification.
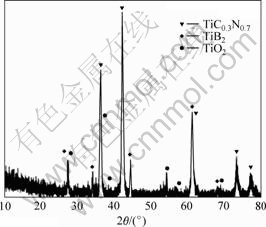
Fig.1 XRD patterns of multi-phase ceramic coating prepared at optimized parameters
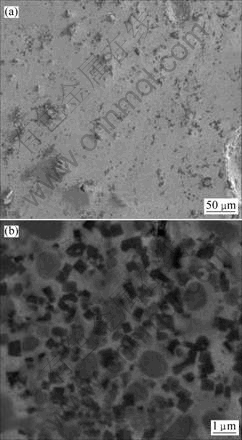
Fig.2 SEM microstructures of multi-phase ceramic coating observed under different magnifications
First of all, the state of fed particles is crucial for spraying process. In-situ SHS reaction between Ti and B4C powders merely occurs in an agglomerated particle. Fig.3 shows the morphology of agglomerated particles.
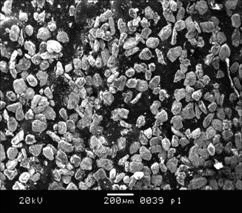
Fig.3 SEM morphology of agglomerated particles
At the beginning of the flight, SHS chemical reaction would be ignited at the moment when the particles are heated to the critical temperature due to the rapid energy accumulation. SHS combustion synthesis takes place as described in Eqns.(1) and (2).
4Ti+B4C=2TiC+2TiB2 (1)
Ti+C=TiC (2)
The adiabatic temperature of this reaction is about 3 200 K calculated from thermodynamics. The exothermic reaction with the accessorial flame energy can melt the particles into liquid droplet, which are very helpful to produce high performance multi-phase coating with low porosity and good component dispersion between various phases. So from Fig.2 even and homogenous coating shows great variation from the lamella-like structure obtained by traditional thermal spraying.
Water quenching method, which was initially used to study the structure transformation by ROGACHEV et al[10], was carried out to observe the change and state of the particles in flight. Fig.4 gives the morphology of the particles water quenched at the flight distance of 220 mm. It clearly indicates that the original particles are almost melted and become spherical.
The phase transformation and solidification perform with the propagating of combustion wave.
Two modes exist in the ignition of reactive agglomerated system and the spread of the combustion wave. One is self-propagating mode and the other is thermal explosion mode. Self-propagating mode often takes place in particles with smaller size. And thermal explosion occurs intensively in bigger particles at an instant due to energy accumulation.
Two mechanisms, solid diffusion and dissolution- precipitation, respectively, control the synthesis reaction.
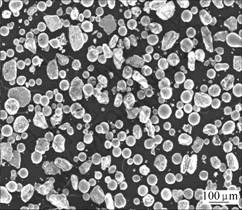
Fig.4 SEM morphology of particles water-quenched at flight distance of 220 mm
Before the presence of liquid titanium melted from solid powders, the reaction is controlled by solid diffusion between the individual powders in one agglomerated particle. After titanium is partially melted the procedure is determined by dissolution-precipitation mechanism. Atoms C and B dissolve and spread into the liquid Ti chemically combining with Ti atoms. Subsequently, the eutectic crystal resultant of TiC-TiB2 precipitates from the liquid.
However, not as ideal as described by chemical equation, nitrification and oxidation of the reactants during spraying are inevitable for the reason of exposure to the air. In-situ TiC and TiN trend to mix into Ti(C, N) solid solution. It can be deduced, that from Fig.2(b) that the matrix with different brightness is corresponding to the different solubility of both atoms C and N. Furthermore, the surrounding oxygen leads to oxidation of titanium and over-burning of B4C. Thermodynamic calculation of enthalpy and Gibbs free energy for all possible reactions indicates that B4C is easy to oxidize, which can further lead to the decrease of TiB2 content compared with as expected.
4 Conclusions
1) Using Ti-B4C-C as combustion system TiCxNy- TiB2 multi-phase ceramic coatings were prepared by SHS reactive flame spraying on steel substrate. By orthogonal experiment three key parameters were optimized. Spraying distance of 220 mm, delivery gas pressure of 0.3 MPa and preheat temperature to particles at 240 ℃. And the highest performance with 2.5% porosity and HV1 595 are achieved in the coating.
2) The coating is composed of Ti(C, N) solid solution (mainly TiC0.3N0.7) matrix with different solubilities of atoms C and N, in which irregular TiB2 particles disperse homogenously and evenly.
3) In-situ SHS reaction between Ti and B4C powders merely occurs in an agglomerated particle. The exothermic reaction with accessorial flame energy can melt the particles into liquid droplet, which can be proved by water quenching method. Self-propagating and thermal explosion are the two modes existing in the ignition of reactive agglomerated system. Solid diffusion and dissolution-precipitation are the two mechanisms which control of the synthesis reaction.
References
[1] ROBERTA L, ROBERTO O, GIACOMO C. Self-propagating combustion synthesis and plasma spraying deposition of TiC-Fe powders[J]. Ceramics International, 2003, 29: 519-526.
[2] KUNG H, LU Y C, BARTLETT A H, CASTRO R G. Structural characterization of combustion synthesized MoSi2-Si3N4 composite powders and plasma sprayed MoSi2-Si3N4 composites[J]. J Mater Res, 1998, 13(6): 1522-1529.
[3] DU Xin-kang, WANG Jian-jiang. Al2O3-Al2Cu3 coating produced by SHS reactive spraying[J]. Materials Science Forum, 2003, 423/425: 547-550.
[4] TEE K L, LU L, LAI M O. Improvement in mechanical properties of in-situ Al-TiB2 composite by incorporation of carbon[J]. Mater Sci Eng A, 2003, 349: 227-231.
[5] WANG H Y, JIANG Q C, ZHAO Y Q. Fabrication of TiB2 and TiB2-TiC particulates reinforced magnesium matrix composites[J]. Mater Sci Eng A, 2004, 372: 109-114.
[6] LEVASHOV E A, LARIKHIN D V. Self propagating high temperature synthesis of functionally graded PVD targets with a ceramic working layer of TiB2-TiN or Ti5Si3-TiN[J]. Journal of Materials Synthesis and Processing, 2002, 10(6): 319-330.
[7] KUSTAS F, MISHRA B, ZHOU J. Fabrication and characterization of TiB2/TiC and tungsten co-sputtered wear coatings[J]. Surface and Coatings Technology, 2002, 153: 25-30.
[8] KITTY W L, CHEN Y H, CHUNG Y W. Hardness, internal stress and thermal stability of TiB2/TiC multilayer coatings synthesized by magnetron sputtering with and without substrate rotation[J]. Surface and Coatings Technology, 2004, 177/178: 591-596
[9] KLINGER L, GOTMAN I, HORVITZ D. In situ processing of TiB2-TiC ceramic composites by thermal explosion under pressure: Experimental study and modeling[J]. Mater Sci Eng A, 2001, 302: 92-99.
[10] ROGACHEV A S, MUKAS A S, MERZHANOV A G. Structural transitions in the gasless combustion of titanium-carbon and titanium-boron systems[J]. Dokl Phys Chem, 1987, 297: 1240-1243.
(Edited by LONG Huai-zhong)
Foundation item: Project (50672130) supported by the National Natural Science Foundation of China
Corresponding author: DU Xin-kang; Tel: +86-311-87994091; E-mail: dxk2002@163.net