Effect of hot extrusion on microstructure and mechanical properties of quasicrystal-reinforced Mg-Zn-Y alloy
ZHENG Ming-yi(郑明毅)1, QIAO Xiao-guang(乔晓光)1, XU Shi-wei(徐世伟)1, GAN Wei-min(甘为民)1,
WU Kun(吴 昆)1, S.Kamado2, Y.Kojima2, H.G.Brokmeier3
(1. School of Materials Science and Engineering, Harbin Institute of Technology,Harbin 150001, China;
2. Department of Mechanical Engineering, Nagaoka University of Technology,Nagaoka 940-2188, Japan;
3. Institute of Materials Engineering, GKSS-Research Center,D21502, Geesthacht, Germany)
Abstract: The microstructure and mechanical properties of as-cast and as-extruded Mg-Zn-Y alloy (Mg-11%Zn-0.9%Y, mass fraction) containing Mg3YZn6 quasicrystal were studied. The eutectic icosahedral quasicrystal phase (I-phase) is broken and almost distributes along the extrusion direction, and fine I-phase with nano-size is precipitated during the extrusion. The α-Mg matrix grains are refined due to recrystallization occuring during the hot extrusion. Some {101[TX-]2} twins are observed in the extruded ZW1101 alloy. And {0002}〈101[TX-]0〉 fiber texture is formed in matrix alloys after hot extrusion. The extruded alloy exhibits high strength in combination with large elongation at room temperature. The strengthening mechanism of the as-extruded alloy was discussed.
Key words: magnesium alloys; quasicrystal; extrusion; microstructure; mechanical properties CLC number: TG146
Document code: A
1 INTRODUCTION
Magnesium alloys have high potential as structural materials because of their low density[1]. Considerable effort is currently being devoted to the development of magnesium alloys with high strength and ductility in order to satisfy the demand for aerospace and outer space applications. One way to strengthen magnesium alloys is to introduce second phases in the alloys. Recently, it was observed that a quasicrystalline icosahedral phase (I-phase) with chemical composition of Mg3REZn6 was formed as a second phase in the α-Mg matrix during conventional solidification in the Mg-Zn-RE alloy system[2-4]. Quasicrystals are isotropic and possess quasiperiodic lattice structure[5]. Due to the difficulty of the movement of dislocations in the quasicrystals at room and elevated temperatures, quasicrystals exhibit high hardness and high strength[6]. Therefore, quasicrystals have been successfully used as strengthening phases in some structural materials, such as Al-Li-Cu-Mg alloy[7], 12Cr-9Ni-4Mo maraging stainless steel[8], Al-Mn-Ce alloy[9], and Mg-Zn-Al-Y alloy[10].
However, the I-phase in the Mg-Zn-RE alloy system was formed as a coarse eutectic structure on solidification[2]. In order to use the I-phase as a strengthening phase, the I-phase should be broken and distributed homogeneously in the alloy. Thermomechanical processes such as hot rolling[11, 12] and extrusion[13] have been employed to the Mg-Zn-Y alloys to achieve microstructural refinements and improvement of mechanical properties. Bae et al[11] employed hot rolling at 400℃ for Mg-4.3%Zn-0.7%Y(mole fraction) alloy to achieve a yield strength of 220MPa and ultimate tensile strength of 370MPa with 17.2% elongation in tensile tests at ambient temperature. Higher yield strength of 230MPa and ultimate tensile strength of 260MPa with 20% elongation were obtained in as-rolled Mg-5.8%Zn-1.2%Y(mole fraction) alloy by Taniuchi et al[12]. On the other hand, Singh et al[13] employed hot extrusion at 400℃ for Mg-4.2%Zn-0.8%Y(mole fraction) alloy to achieve a yield strength of 250MPa and ultimate tensile strength of 330MPa with 19% elongation in tensile tests at ambient temperature.
In this research, Mg-Zn-Y alloy with higher strength and ductility was developed by selecting proper chemical composition of the Mg-Zn-Y alloy and hot extrusion parameters. The microstructure, textures and mechanical properties of the Mg-Zn-Y alloy were investigated. The strengthening mechanism of the as-extruded alloy was discussed also.
2 EXPERIMENTAL
The material used in this investigation was a Mg-Zn-Y alloy having a composition of Mg-11%Zn-0.9%Y(mass fraction) (ASTM designation: ZW1101). The alloy was initially produced by conventional ingot casting under a dynamic SF6 and CO2 mixed gas atmosphere. The ingot was then hot extruded at 350℃ at a rate of 0.2m/min to give rectangular bars with 15mm in thickness and 15mm in width corresponding to a reduction ratio of 9∶1.
The microstructures of the as-cast and as-extruded alloy were examined with an Olympus DP11 optical microscope(OM) and a Philips CM 12 transmission electron microscope (TEM) operated at 120kV. Thin foil specimens for TEM observation were prepared by a standard combination of mechanical thinning and ion-beam milling techniques. Phase analyses were performed with a Philips XPert X-ray diffractometer (XRD) with CuKα radiation.
Pole figures of {0001} and {101[TX-]0} of the as-extruded ZW1101 alloy were measured using neutron texture diffractometer TEX-2 in GKSS Research Center of Germany[14]. Cubic samples with the size of 1cm×1cm×1cm were prepared for the neutron diffraction experiment by electro-discharge cutting from the extruded alloy. The measurement of textures was performed on the section perpendicular to the extrusion direction.
Specimens for tensile tests were machined from the as-cast and as-extruded alloys. The specimens have a gauge length of 15mm and cross-sectional areas of 6mm×2mm. Tensile tests were performed at room temperature using an Instron 5569 universal test machine at a crosshead speed of 1mm/min. The tensile axis was selected to be parallel to the extrusion direction for the as-extruded alloy.
3 RESULTS AND DISCUSSION
3.1 Microstructure of as-cast ZW1101 magnesium alloy
The XRD pattern of the as-cast ZW1101 alloy is shown in Fig.1. The peak analysis reveals that the alloy consists of two phases of α-Mg and icosahedral quasicrystal phase (I-phase).
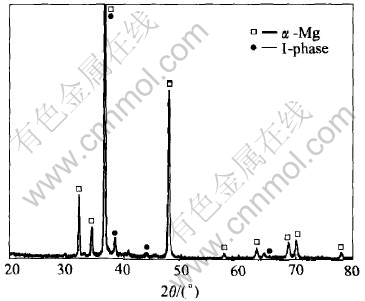
Fig.1 XRD pattern of as-cast ZW1101 alloy
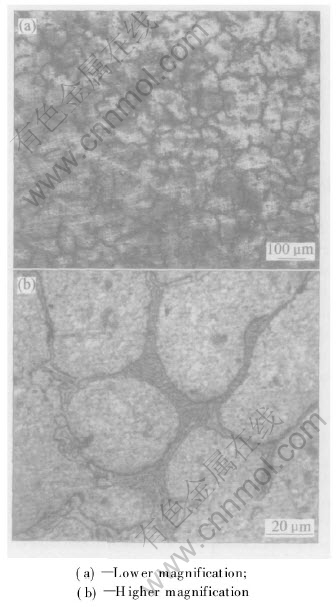
Fig.2 Typical optical microstructures of as-cast ZW1101 alloy
Fig.2 shows the typical microstructure of the as-cast ZW1101 alloy. The alloy exhibits dendritic solidification structure, and the grain sizes of the α-Mg are in the range of 80-120 μm, as shown in Fig.2(a). Eutectic I-phases located in the interdendritic region are clearly observed in Fig.2(b). The volume fraction of the I-phase in the alloy is about 10%.
To further confirm the existence of the I-phase, TEM observation was performed for the as-cast ZW1101 magnesium alloy. Fig.3 shows the TEM morphology and its selected area diffraction patterns (SADP). In Figs.3(b)-(d), the SADPs taken from the eutectic lamellar phase show 2-, 3- and 5-fold symmetries, respectively, which is a distinct characteristic of the icosahedral quasi-crystalline phase (I-phase).
3.2 Microstructure of as-extruded ZW1101 magnesium alloy
Fig.4 shows the typical microstructures of the as-extruded ZW1101 magnesium alloy. Figs.4(a) and (c) are the micrographs on the section parallel to the extrusion direction, while Figs.4(b) and (d) are the micrographs on the section perpendi- cular to the extrusion direction. It is obvious that the I-phases are distributed homogeneously in the as-extruded alloy compared with the as-cast alloy. The eutectic pockets are broken into small particles due to the brittleness of the I-phase. Most of the I-phase particles are dispersed on the refined grain boundaries, while some I-phase particles are also observed inside the grains. Bands of small I-phase particles are observed to be oriented approximately parallel to the extrusion direction, as shown in Figs.4(b) and (d). The average grain size in the as-extruded alloy is measured as about 12μm. The grain boundaries are well-defined and the grains are reasonably equiaxed, suggesting that dynamic recrystallization(DRX) takes place during the extrusion at 350℃. Some fine DRX grains are formed around the I-phase particles, indicating that the I-phase particles stimulate nucleation for DRX during hot extrusion. In addition, some twins are observed in the as-extruded alloy.
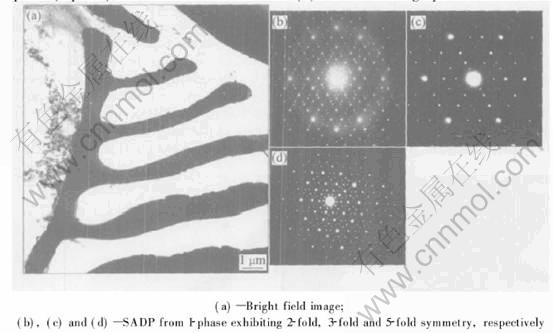
Fig.3 TEM micrographs of eutectic I-phase
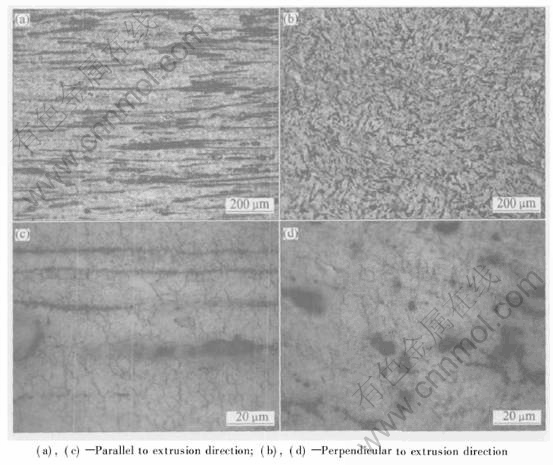
Fig.4 Optical micrographs of as-extruded ZW1101 magnesium alloy on sections
Fig.5 shows the TEM micrographs of the as-extruded ZW1101 alloy. As shown in Fig.5(a), the eutectic I-phases are broken into fine irregular shaped particles of 1-2μm in size. Some DRX grains are observed clearly around the I-phase particles. Dutta et al[15] pointed out that the fracture of the particles and the degradation of the particle-matrix interface occur during hot working of SiCp/5083Al composite. In this work, the I-phase particles are broken by hot extrusion, however, no cavity and crack are observed at the I-phase/α-Mg interface in the ZW1101 alloy after hot extrusion, in spite of the different strength and plastic deformation behavior of I-phase and α-Mg. Fig.5(b) shows
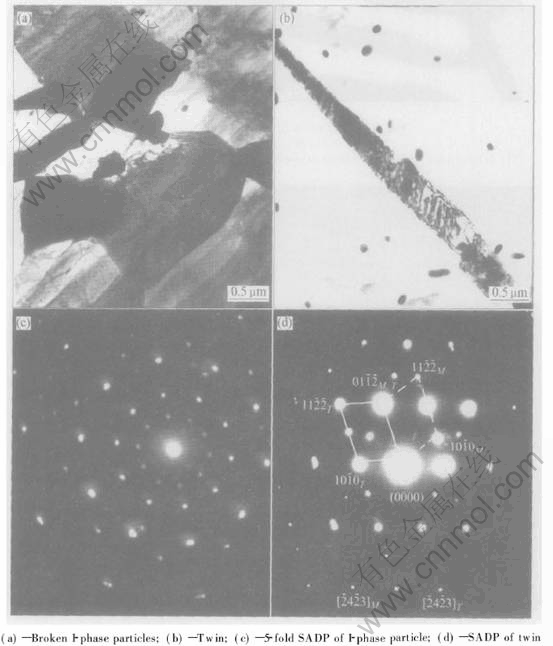
Fig.5 TEM micrographs of as-extruded ZW1101 magnesium alloy
a twin in the as-extruded alloy. The SADP analysis shown in Fig.5(d) indicates the twin occurs on the {1012} plane. Furthermore, very fine particles with the size less than 100nm are precipitated in the as-extruded ZW1101 alloy, as shown in Figs.5(a) and (b). The fine I-phase precipitates have been observed to form during hot extrusion and hot rolling of Mg-Zn-Y alloy systems[11, 13]. This suggests that the fine precipitates formed in the as-extruded ZW1101 alloy may also be I-phase.
3.3 Texture in as-extruded ZW1101 magnesium alloy
The {0001} and {1010} pole figures of the as-extruded ZW1101 alloy are shown in Figs.6 (a) and (b), respectively. It is evident that {0001} basal planes and 〈1010〉 directions in most grains are distributed parallelly to the extrusion direction (ED). That is, the as-extruded ZW1101 alloy
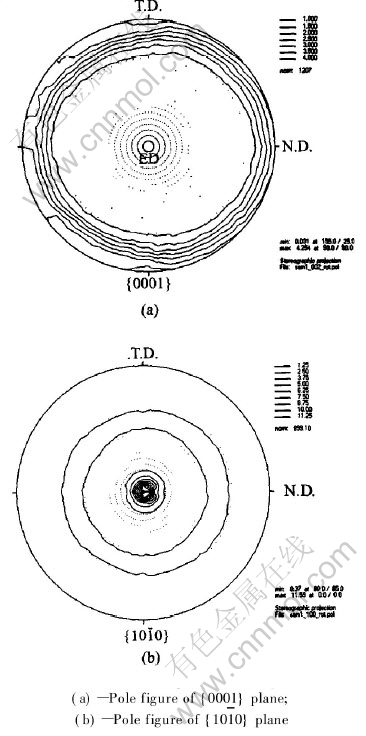
Fig.6 Textures in as-extruded ZW1101 magnesium alloy
exhibits an ED∥〈1010〉 fiber texture. Similar tendency of basal planes lying parallelly to the extrusion direction after extrusion has been observed in many Mg alloys[16, 17]. This indicates that the presence of I-phase does not change the nature of the extrusion texture of magnesium alloys.
3.4 Tensile properties of ZW1101 magnesium alloy
Fig.7 shows the typical tensile stress—strain curves of the as-cast and as-extruded ZW1101 magnesium alloys. The tensile properties of the as-cast and as-extruded ZW1101 alloys are listed in Table 1. The as-cast alloy shows a premature failure with straining, and exhibits very low tensile strength and low elongation to failure. Both the coarse grain size and the network distribution of eutectic I-phase are responsible for the poor tensile properties of the as-cast alloy.
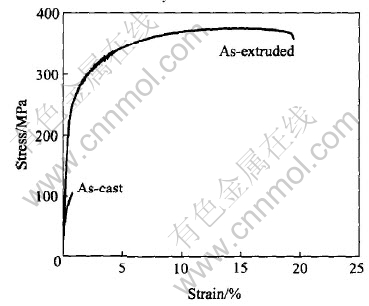
Fig.7 Stress—strain curves of as-cast and as-extruded ZW1101 magnesium alloys
Table 1 Mechanical properties of as-cast and as-extruded ZW1101 magnesium alloy
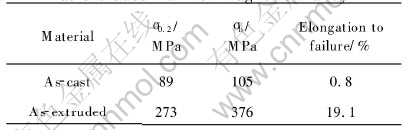
It can be found that both tensile strength and elongation are improved significantly after hot extrusion, and the as-extruded alloy experiences obvious strain hardening before fracture. The as-extruded alloy exhibits yield strength of 273MPa and ultimate tensile strength of 376MPa with 19% elongation. Both the tensile strength and elongation of the as-extruded ZW1101 alloy obtained in this research are superior to those of the other hot processed Mg-Zn-Y alloys developed by other researchers[11-13].
The excellent tensile properties of the extruded ZW1101 alloy may be attributed to the following factors, such as the size and distribution of the fine I-phase particles, grain refinement, texture and twinning.
The main strengthening phase in the extruded ZW1101 alloy is I-phase, which exists in two forms: small broken particles distributed parallelly to the extrusion direction, and fine precipitates with nano-size distributed homogeneously in the matrix. The high symmetry and quasiperiodicity of quasicrystal ensure a good atomic match at the interface between quasicrystal and magnesium matrix[18]. Therefore, the interfacial energy between I-phase and magnesium matrix is low, and the quasicrystal-Mg matrix interface is very stable with high interfacial bonding strength[11]. The strong I phase/Mg matrix interface may allow effective load transfer from the matrix to I-phase. After extrusion, I-phase particles in the alloy are mainly distributed along the extrusion direction. Since the tensile direction is parallel to the extrusion direction, the unidirectional distribution of I-phase is beneficial to tensile strength. In addition, the broken I-phase particles and the fine I-phase precipitates can provide effective obstacles to dislocation movement during deformation[9, 11] and have a dispersive strengthening effect on the alloy. Furthermore, the stable quasicrystal-matrix interface with a low interfacial energy[16] can provide the improved elongation in the as-extruded alloy.
The influence of the grain size on the yield stress can be estimated using a standard Hall-Petch equation of the form: Δσ0.2=kd-1/2, where k is a constant. According to Armstrongs analysis[19], there is a relationship between Hall-Petch constant k and the Taylor factor M, that is, k∝M2τc, where τc is the shear stress required to operate a dislocation source in the slip plane of the source. The Taylor factor M generally depends on the number of the slip systems. Because the slip systems are limited and the Taylor factor is larger for hcp metals than that for fcc and bcc metals, hcp metals exhibit the strong influence of grain size on strength. Therefore, grain refinement due to dynamic recrystallization gives rise to a large increase in strength for as-extruded ZW1101 alloy.
Texture strongly affects the mechanical properties of magnesium alloys because the crystallography orientation has a significant relationship to slip and twining systems which correspond to the deformation modes[16]. {0001} basal planes in most grains are distributed parallelly to the extrusion direction in the as-extruded ZW1101 alloy. This kind of texture is unfavorable for the occurrence of basal slip when the tensile direction is parallel to the extrusion direction. Therefore, the as-extruded ZW1101 alloy is strengthened. Considerable strengthening was also achieved in other extruded or rolled magnesium alloys by having intense basal texture[17]. Twin boundaries can block dislocation movement during plastic deformation[20]. Therefore, twins in the as-extruded ZW1101 alloy can also strengthen the alloy. Recent researches[20] indicated that the grain boundaries could not only resist dislocation motion upon plastic deformation but also absorb dislocations at twin boundaries. This may provide an effective approach to strengthen metals with fine grain size while keeping an impressive ductility.
4 CONCLUSIONS
1) The as-extruded ZW1101 alloy exhibits yield strength of 273MPa and ultimate tensile strength of 376MPa with 19% elongation, which are much higher than those of the as-cast alloy.
2) After hot extrusion, the α-Mg matrix grains are significantly refined due to dynamic recrystallization, the eutectic I-phases network in the as-cast alloy are broken and almost distributed along the extrusion direction, and fine I-phase with nano-size is precipitated. And {0002}〈101[TX-]0〉 fiber texture is formed in the as-extruded ZW1101 alloy.
3) The excellent tensile properties of the extruded ZW1101 alloy is mainly attributed to the strengthening mechanisms due to dispersed I-phase particles and fine precipitates, grain refinement and basal texture.
REFERENCES
[1]Kojima Y, Aizawa T, Kamado S, et al. Progressive steps in the platform science and technology for advanced magnesium alloys[J]. Mater Sci Forum, 2003, 419-422: 3-20.
[2]LUO Z P, ZHANG S Q, TANG Y L, et al. Quasi-crystals in as-cast Mg-Zn-Re alloys[J]. Scr Metall, 1993, 28: 1513-1518.
[3]Tsai A P, Niikura A, Inoue A, et al. Stoichiometric icosahedral phase in the Zn-Mg-Y system[J]. J Mater Res, 1997, 12(6): 1468-1471.
[4]Yi S, Park E S, Ok J B, et al. (Icosahedral phase +α-Mg) two phase microstructures in the Mg-Zn-Y ternary system[J]. Mater Sci Eng A, 2001, 300(1-2): 312-315.
[5]Shechtman D, Blech I, Gratias D, et al. Metallic phase with long-range orientational order and no translational symmetry[J]. Phys Rev Lett, 1984, 53: 1951-1954.
[6]Yoshida T, Itoh K, Tamura R, et al. Plastic deformation and hardness in Mg-Zn-(Y, Ho) icosahedral quasicrystals[J]. Mater Sci Eng A, 2001, A298(1-2): 786-789.
[7]Sainfort P, Dubost B. Coprecipitation hardening in Al-Li-Cu-Mg alloys[J]. J Phsiqu Colloque, 1987, C3(48): 407-415.
[8]Liu P, Stigenberg A H, Nilson J O. Quasicrystalline and crystalline precipitation during isothermal tempering in a 12Cr-9Ni-4Mo maraging stainless steel [J]. Acta Metall Mater, 1995, 43: 2881-2890.
[9]Schuracky F, Eckert J, Schultz L. Al-Mn-Ce quasicrystalline composites: phase formation and mechanical properties[J]. Phil Mag, 2003, 83: 807-825.
[10]Yuan G, Amiya K, Kato H, et al. Structure and mechanical properties of cast quasicrystal-reinforced Mg-Zn-Al-Y base alloys[J]. J Mater Res, 2004, 19(5): 1531-1538.
[11]Bae D H, Kim S H, Kim D H, et al. Deformation behavior of Mg-Zn-Y alloys reinforced by icosahedral quasicrystalline particles[J]. Acta Mater, 2002, 50: 2343-2356.
[12]Taniuchi S, Watanabe H, Okumur A, et al. Microstructures and tensile properties of Mg-Zn-Y alloys containing quasicrystals[J]. Mater Sci Forum, 2003, 419-422: 255-260.
[13]Singh A, Nakamura M, Watanabe E, et al. Quasicrystal strengthened Mg-Zn-Y alloys by extrusion[J]. Scr Mater, 2003, 49: 417-422.
[14]Yi S B, Brokmeier H G, Bohlenb J, et al. Neutron diffraction study on the texture development during extrusion of magnesium alloy AZ31[J]. Physica B, 2004, 350: e507-509.
[15]Duta I, Tiedemann C F, Mcnelley T R. Effect of hot working on the microstructure and properties of a cast 5083 Al-SiCp metal matrix composite[J]. Scr Met, 1990, 24: 1233-1238.
[16]WANG Y N, HUANG J C. Texture analysis in hexagonal materials[J]. Materials Chemistry and Physics, 2003, 81: 11-26.
[17]Rao G S, Prasad Y V R E. Grain boundary strengthening in hot rolled magnesium-5at.% thallium: importance of texture[J]. Scr Met, 1983, 17: 147-151.
[18]Dubois J M. New prospects from potential applications of quasicrystalline materials[J]. Mater Sci Eng A, 2000, 294-296: 4-9.
[19]Armstrong R W. Theory of the tensile ductile-brittle behavior of poly-crystalline h.c.p. materials, with application to beryllium[J]. Scr Met, 1968, 16: 347-355.
[20]LU K. Novel properties of nanostructured metals[J]. Mater Sci Forum, 2005, 475-479: 21-24.
(Edited by YUAN Sai-qian)
Foundation item: Project (50201005) supported by the National Natural Science Foundation of China
Received date: 2004-11-28; Accepted date:2005-03-18
Correspondence: ZHENG Ming-yi, Associate professor, PhD; Tel: +86-451-86402291; E-mail: zhenghe@hit.edu.cn