J. Cent. South Univ. (2016) 23: 1584-1590
DOI: 10.1007/s11771-016-3212-z

Acid leaching decarbonization and following pressure oxidation of carbonic refractory gold ore
ZHANG Du-chao(张杜超)1, 2, XIAO Qing-kai(肖庆凯)1, LIU Wei-feng(刘伟锋)1, CHEN Lin(陈霖)1,
YANG Tian-zu(杨天足)1, LIU You-nian(刘又年)2
1. School of Metallurgy and Environment, Central South University, Changsha 410083, China;
2. School of Chemistry and Chemical Engineering, Central South University, Changsha 410083, China
Central South University Press and Springer-Verlag Berlin Heidelberg 2016
Abstract: Carbonate decomposition of carbonic refractory gold ore and the following pressure oxidation were studied. In the carbonate decomposition procedure, the effects of liquid-to-solid ratio and reaction time on decomposition ratio of carbonate were investigated. The experimental result shows that the decomposition ratio of carbonate is 98.24% under the conditions of liquid-to-solid ratio of 5:1, Fe3+ concentration of 20 g/L, sulfuric acid concentration of 20 g/L, reaction temperature of 80 °C and reaction time of 2 h. Then, the slurry obtained from carbonate decomposition was put into the titanium autoclave for pressure oxidation leaching. Effects of liquid-to-solid ratio, temperature, time and oxygen partial pressure on sulfur oxidation ratio were studied during pressure oxidation. With the prolonged time, pyrite and arsenopyrite are oxidized to ferric subsulfate, hydrated ferric sulfate and jarosite, resulting in the increasing residue ratio. The residue ratio and the sulfur content in the residue can be decreased by ferric subsulfate dissolution. The oxidation ratio of the sulfur is 99.35% under the conditions of oxidation time of 4 h, temperature of 210 °C, oxygen partial pressure of 0.8 MPa and stirring speed of 600 r/min.
Key words: carbonic refractory gold ore; carbonate decomposition; pressure oxidation; ferric subsulfate dissolution
1 Introduction
Refractory gold ores are characterized by low gold leaching ratio during direct cyanide leaching [1]. The gold in such so-called refractory ores is contained within sulphide minerals, such as particular pyrite and arsenopyrite present commonly in the form of microscopic or submicroscopic particles and impregnated ores. Besides, other impurity elements also affect the cyanide process. So, suitable pretreatment methods should be used to open inclusion in the minerals and eliminate the obstacles of cyanide leaching [2].
Carbonic refractory gold ore is one of the most difficultly-recovered materials due to the fact that its carbon generally exists in the forms of carbonate, organic carbon and graphite carbon. This is because carbonaceous material adsorbs the solubilised gold from the cyanide leaching solution, which is preg-robbing behavior in metallurgical operations, and appropriate pretreatment is required to destroy or passivate the carbonaceous material before cyanide leaching [3-5].
Currently, the main options for the pretreatment of refractory gold ores include ultrafine grinding, biological oxidation [6-7], oxidizing roasting [8-10], hypochlorite oxidation and pressure oxidation [10-11]. Ultrafine grinding cannot effectively remove carbonaceous material and also has no obvious recovery of gold by cyanide leaching [1]. Biological oxidation can promote the recovery of gold from refractory gold ore [12-13], and LANGHANS et al [12] have used this method to open the inclusion of refractory gold ore bearing arsenic, and then concluded that cyanide leaching ratio of gold increases from 49% to about 80%. But, its defect lies in that the oxidation time is too long [14].
Although atmospheric pressure hypochlorite oxidation method has a positive effect on decarburization and oxidation of the pyrite, it has no improvement on decomposition of arsenopyrite and pyrrhotite, and cannot effectively open the mineral inclusions of gold [10, 15-16]. Oxidizing roasting method can prompt the recovery of gold from refractory ore containing carbonate and arsenical, but the pollution gas including SO2and As2O3 is produced in the process, limiting its industrial application [17].
Acid pressure oxidation pretreatment is an extremely effective method to improve the gold recovery by cyanide leaching [18]. GUDYANGA et al [19] have studied the acid pressure oxidation process of the concentrate from the roasting plant and the result shows that the recovery ratio of gold can be significantly improved. However, carbonaceous material especially carbonate in the acid pressure oxidation leaching would produce CO2, resulting in pressure instability of the autoclave and security issues. Furthermore, ferric subsulfate produced in the process of acid pressure oxidation can absorb gold grains and inhibit cyanide leaching of gold.
In order to solve these above problems from direct acid pressure oxidation of carbonic refractory gold ore, the acid leaching of decarburization has been firstly proposed to eliminate carbonate phase. And then, pressure oxidation leaching is used to oxidize pyrite and arsenopyrite to open the inclusion of gold. Finally, basic ferric sulfate dissolution is carried out to decrease the residue amount. This work provides a valuable and effective method for the pretreatment of refractory gold ore.
2 Experimental
2.1 Materials
The carbonic refractory gold ore with particle size less than <212 μm was supplied by the Jinchiling Gold Mine of Zhaojin Mining Industry Co., Ltd (China). The chemical composition of the refractory gold ore is given in Table 1.
Table 1 Chemical composition of refractory gold ore
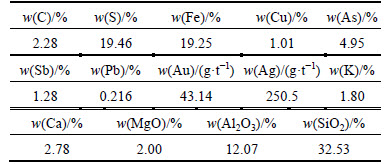
The analysis results of sulfur phase and carbon phase are given in Table 2 and Table 3, respectively. It can be seen from Table 3 that, the total carbon in the refractory gold ore is 2.28%, with 1.13% existing in the form of carbonate. The other components are graphite carbon and organic carbon. From Table 2, the total sulfur in the gold ore is 19.46%, most of which is sulfide.
Table 2 Sulfur phase analysis of refractory gold ore (%)

Table 3 Carbon phase analysis of refractory gold ore (%)

2.2 Carbonate decomposition
The carbonate decomposition experiments were performed in a 1 L beaker placed in a thermostatic water bath. The initial leaching solution of 20 g/L Fe3+ concentration and 20 g/L sulfuric acid concentration was prepared by adding analytically pure ferric sulfate and 98% sulfuric acid. With the solution heated to the settled temperature, 120 g gold mineral was added into the initial solution by a certain liquid-to-solid ratio and then the stirring device was turned on. After a period of reaction, the heating device was turn off. The pH value of the solution was measured when the solution was cooled to room temperature. Then, the slurry was filtered, washed and dried. Finally, the residue ratio was calculated and carbon phase in the residue was analyzed.
2.3 Pressure oxidation
The slurry from the acid leaching pretreatment was added into a 1 L titanium autoclave after reacting at 80 °C for 2 h. The liquid-to-solid ratio was controlled during the decarbonization process. When the autoclave was heated to the settled temperature, stirring device was turned on. And then, the oxygen partial pressure was adjusted to the desired value and the oxygen was pumped into the autoclave. After a period of reaction, the heating device and the oxygen were shut down, and the autoclave was rapidly water-cooled to ambient temperature. With the pressure removed, the autoclave was turned on. Finally, the solid residue in the autoclave was filtered, washed and dried. The chemical components of sulfur phase and other metals in the dried residue were analyzed.
2.4 Ferric subsulfate dissolution
120 g gold concentrate was decarburized by acid pressure leaching of 600 mL initial leaching solution at 80 °C for 2 h. Then, the slurry was added into a 1 L titanium autoclave to perform pressure oxidation under the conditions of 210 °C temperature, 800 r/min stirring rate and 0.8 MPa oxygen partial pressure while the time of pressure oxidation experiments were 2, 4, 6 and 8 h. In order to avoid the dried procedure bringing impact, two groups of experiments were run under the same conditions above, respectively. In the first group, the obtained slurry was sampled to analyze the contents of sulfur and iron, and then, the left was transmitted into the beaker and stirred for 6 h at 90 °C. The variation of the phases containing sulfur and the change of the iron contents in the dissolved basic ferric sulfate were determined. In the second group, the obtained slurry was directly stirred at 90 °C for 6 h. Then, the residue ratio was calculated and the contents of the major elements in the residue were determined.
3 Results and discussion
3.1 Carbonate decomposition
1) Effect of liquid-to-solid radio on carbonate decomposition ratio
As is shown in Fig. 1, the carbonate decomposition ratio increases with the increase of liquid-to-solid ratio. When the ratio is up to 2:1, the carbonate decomposition ratio exceeds 90%. Moreover, the carbonate is nearly completely decomposed under the condition of liquid-to-solid ratio 4:1 and 5:1. The reason can be inferred that the decomposition ratio of the carbonate increases with the increased acidity under the condition of higher liquid-to-solid ratio.
2) Effect of time on carbonate decomposition ratio
The effect of time on the carbonate decomposition ratio is shown in Fig. 2. It can be observed that the decomposition ratio of the carbonate increases with the prolonged time. After 0.5 h reaction time, the carbonate decomposition ratio is 93.78%. When the reaction time exceeds 1 h, the decomposition ratio of carbonate is over 98%. Therefore, the available reaction time with high carbonate decomposition ratio is from 1.5 h to 2 h for the acid leaching process.
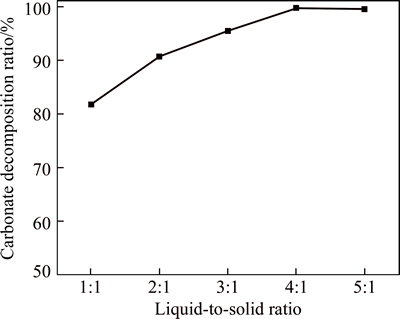
Fig. 1 Effect of liquid-to-solid ratio on carbonate decomposition ratio (Conditions: 20 g/L Fe3+ concentration,20 g/L sulfuric acid concentration, 80 °C and 3 h)
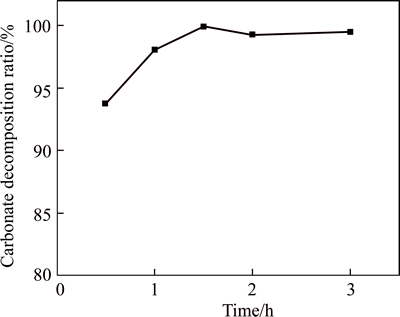
Fig. 2 Effect of time on carbonate decomposition ratio (Conditions: 20 g/L Fe3+ concentration, 20 g/L sulfuric acid concentration, liquid-to-solid ratio of 4:1 and 80 °C)
3) Comprehensive experiment of carbonate decomposition
The initial solution with Fe3+ concentration of 20 g/L and sulfuric acid concentration of 20 g/L was prepared by adding 120 g refractory gold ore, ferric sulfate and sulfuric acid by the liquid-to-solid ratio of 5:1. The experiment was run for 2 h at the temperature of 80 °C. The effect of the comprehensive conditions on the ratio of carbonate decomposition was studied.
The acid leaching residue ratio obtained under the comprehensive conditions is 96.50%, where the carbon content is 1.08% and decomposition ratio of the carbonate is 98.24%. Furthermore, the major elements in the residue were analyzed with the results shown in Table 4.
Table 4 Chemical composition of acid leaching residue
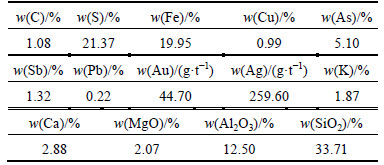
In Table 4, it can be observed that the ratio of carbonate decomposition is over 98% during acid leaching, indicating that nearly complete decomposition of the carbonate is achieved under the condition, beneficial to the further pressure oxidation. The comparison of X-ray diffraction patterns of the raw ore and the residue obtained by acid leaching is shown in Fig. 3.
From Fig. 3, it can be found that remarkable peaks representing FeS2 and SiO2 are observed in the X-ray diffraction pattern of both raw ore and acid leaching residue. There is very little difference between Fig. 3(a) and Fig. 3(b). The reason can be attributed to the fact that that it is easy to dissolve carbonate in the acid leaching system, but it has no obvious effect on other components.
3.2 Pressure oxidation
1) Effect of liquid-to-solid radio on pressure oxidation
After the above acid leaching pretreatment, solution with the corresponding liquid-to-solid ratios of 2:1, 3:1,4:1 and 5:1 was added into titanium autoclave. Pressure oxidation was run for 1.5 h at 210 °C, with stirring speed of 600 r/min and the oxygen partial pressure of 0.8 MPa. The effect of liquid-to-solid ratio on pressure oxidation is given in Table 5.
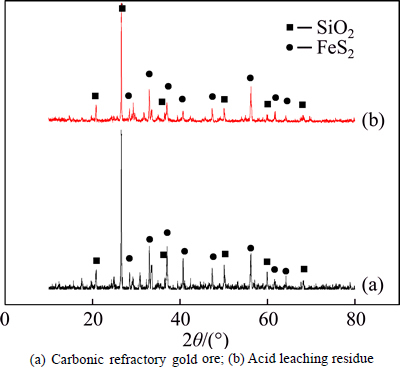
Fig. 3 X-ray diffraction patterns:
From Table 5, it can be seen that when the pressure oxidation lasts for 1.5 h, the total sulfur content reduces and the oxidation ratio of sulfur increases with the increased liquid-to-solid ratio, while pH value of the solution gradually decreases. The reason is that the pyrite is oxidized to ferrous sulfate and sulfuric acid during pressure oxidation. The corresponding reaction equations can be expressed as follows:
2FeS2+7O2+2H2O=2FeSO4+2H2SO4 (1)
2FeAsS+5.5O2+H2O=2FeSO4+2HAsO2 (2)
With oxidation proceeding, ferrous sulfate and arsenious acid are oxidized to ferric sulfate and arsenate. And then, Fe3+ in the sulfuric acid system reacts with pyrite and arsenopyrite. The reaction equations can be expressed as follows:
FeS2+7Fe2(SO4)3+8H2O=15FeSO4+8H2SO4 (3)
2FeAsS+13Fe2(SO4)3+16H2O=28FeSO4+2H3AsO4+13H2SO4 (4)
However, elemental sulfur can be also produced during the oxidation process when oxidation reaction is incomplete. The reaction equations can be expressed as follows:
2FeAsS+7Fe2(SO4)3+8H2O=2H3AsO4+16FeSO4+2S+5H2SO4 (5)
FeS2+Fe2(SO4)3=3FeSO4+2S (6)
As is shown in the equations and the results, elemental sulfur and
are produced during the oxidation process. Because elemental sulfur hinders the cyanide leaching of the residue, the elemental sulfur should be avoided and the related condition experiments should be carried out to obtain a thorough oxidation reaction result.
2) Effect of temperature on pressure oxidation
The solution with the corresponding liquid-to-solid ratio of 5:1 was added into titanium autoclave. Pressure oxidation was run for 5 h at 200, 210 and 220 °C, with stirring speed of 600 r/min and the oxygen partial pressure of 0.8 MPa. The effect of liquid-to-solid ratio on pressure oxidation is given in Table 6.
From Table 6, it can be known that the oxidation ratio of sulfur remains over 98% while the temperature ranges from 200 °C to 220 °C. Generally, the temperature during pressure oxidation of refractory gold ore under acidic condition should be controlled at a value higher than 160 °C. Therefore, temperature range should be selected to ensure a relatively complete oxidation of sulfur and promote the conversion of intermediate elemental sulfur to sulfuric acid or ferric sulfate.
3) Effect of oxygen partial pressure on pressure oxidation
The solution with the corresponding liquid-to-solid ratio of 5:1 was added into titanium autoclave. Pressure oxidation was run for 5 h at 210 °C with stirring speed of 600 r/min and the oxygen partial pressure of 0.8 MPa. The effect of liquid-to-solid ratio on pressure oxidation is given in Table 7.
Table 5 Effect of liquid-to-solid radio on pressure oxidation

Table 6 Effect of temperature on pressure oxidation

As is shown in Table 7, the oxygen partial pressure has no remarkable effect on the oxidation ratio of sulfur in the pressure range of 0.4-0.8 MPa. The higher oxygen partial pressure can ensure oxygen concentration in the solution and the oxidation reaction of pyrite and arsenopyrite. And under these conditions, most of the sulfur is oxidized to sulfate. Based on industrial production, low oxygen partial pressure may result in backward flow of solution into the pipe and longer reaction time, unfavorable for operation efficiency. However, higher oxygen partial pressure may lead to accidents. The available oxygen partial pressure range is supposed to be 0.4-0.8 MPa.
4) Effect of reaction time on pressure oxidation
The liquid-to-solid ratio of the corresponding initial solution is 5:1. The experiment was run under the conditions of reaction temperature of 210 °C, oxygen partial pressure of 0.8 MPa and stirring speed of 600 r/min. After a period of reaction, the available slurry was filtered, washed, dried and weighed. Then, sulfur phase in the residue was analyzed. The analysis results are given in Table 8.
From Table 8, it can be observed that the oxidation ratio of sulfur increases gradually with the increase of reaction time. When the reaction time is over 4 h, the oxidation ratio of sulfur keeps constant. However, the higher content of total sulfur and lower content of sulfate in the residue are observed at 2 h reaction time. It can be deduced that the oxidation ratio of sulfur is low due to incomplete oxidation reaction. Moreover, when the reaction time is 6 h or 8 h, the ratio of solid residue goes up and the sulfate content in the residue is higher.In Fig. 4, the presence of FeS2indicates that reaction timeof 2 h is insufficient to ensure a complete oxidation reaction. When reaction time is 4 h, SiO2 and jarosite appear. And the hydrated ferric sulfate exists in the residue from 6 h to 8 h reaction, showing that the oxidation process proceeds and ferric sulfate in the solution combines with water to form hydrated ferric sulfate. Most of the ferric sulfate is left in the solution and the content of hydrated ferric sulfate in the residue is low with reaction time of 4 h. With oxidation reaction proceeding, the hydrated ferric sulfate increases and gradually precipitates out.
It can be concluded that the ferric sulfate is hydrolyzed to basic ferric sulfate, hematite or jarosite and then enters into the solid residue with increasing the reaction time. The reaction equations can be expressed as follows:
Fe2(SO4)3+2H2O=2Fe(OH)SO4+H2SO4 (7)
Fe2(SO4)3+3H2O=Fe2O3+3H2SO4 (8)
3Fe2(SO4)3+14H2O=2H3OFe3(SO4)2(OH)6+5H2SO4(9)
The generated precipitate such as basic ferric sulfate Fe(OH)SO4 or jarosite H3OFe3(SO4)2(OH)6, enters into the residue, resulting in the high content of sulfur existing in the form of sulfate. The selected reaction time of pressure oxidation is 4 h for the purpose of ensuring complete oxidation of sulfur to sulfate and low residue ratio.
5) Ferric subsulfate dissolution
Ferric subsulfate dissolution experiments were conducted using the residue obtained from pressure oxidation process under the above-mentioned conditions. Sulfur and iron content was analyzed before and after ferric subsulfate dissolution experiments, with the results given in Table 9. No. 1, No. 3 and No. 5 are the residues from different pressure oxidation time, and No. 2, No. 4 and No. 6 are the residues obtained from the ferric subsulfate dissolution after different pressure oxidation time, respectively. The corresponding XRD patterns are shown in Fig. 5.
Table 7 Effect of oxygen partial pressure on pressure oxidation

Table 8 Effect of reaction time on pressure oxidation
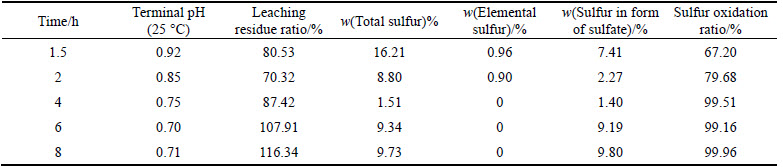
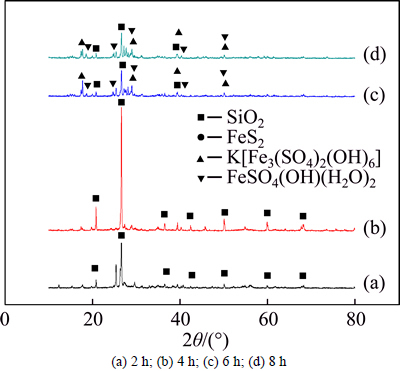
Fig. 4 X-ray diffraction pattern of pressure oxidation at different time:
Table 9 Sulfur and iron content analysis results after ferric subsulfate dissolution
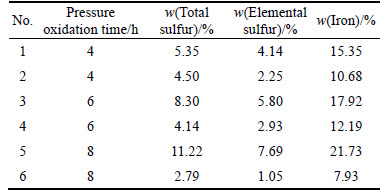
It can be seen from Table 9 that the content of sulfur and iron increases with increasing oxidation time. As the reaction time increases to 8 h, sulfur content and iron content in the residue are up to 7.69% and 21.73%, respectively. The results show that jarosite and hydrated ferric sulfate form in the residue with prolonged oxidation time. After the residue is subjected to ferric subsulfate dissolution experiment, the content of sulfur and iron in the residue shows a descent tendency, indicating that effective decrease of sulfur and iron content and residue ratio are achieved by ferric subsulfate dissolution.
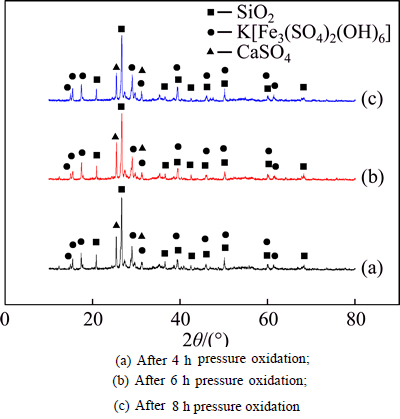
Fig. 5 X-ray diffraction patterns of residue from ferric subsulfate dissolution under different conditions:
Figure 5 shows that peaks of the residue from the pressure oxidation and ferric subsulfate dissolution with different oxidation time are basically identical. The main phases in the residue are SiO2, jarosite and calcium sulfate. Compared with Fig. 4, hydrated ferric sulfate is absent in the residue, indicating that hydrated ferric sulfate is dissolved into the solution during the experiments. It can be concluded that ferric subsulfate dissolution can decrease the residue ratio, which is beneficial to the subsequent cyanide leaching.
3.3 Comprehensive experiment
The pressure oxidation experiment was performed with a 1 L titanium autoclave using slurry obtained after the carbonate decomposition process. The liquid-to-solid ratio of the corresponding initial solution was 5:1. The experiment was run for 4 h under the conditions of temperature of 210 °C, oxygen partial pressure of 0.8 MPa and stirring speed of 600 r/min. Four repeated experiments were conducted. After 4 h of reaction, the obtained slurry was mixed, sampled, washed and dried. Sulfur phase and the content of main elements in the treated residue were analyzed and calculated. Detailed analysis results of sulfur phase and content determination of main elements are given in Tables 10 and 11.
The results of the experiment performed with temperature of 210 °C, oxygen partial pressure of 0.8 MPa, stirring speed of 600 r/min and oxidation time of 4 h are given in Table 10. The ratio of solid residue is89.43% and the sulfur is nearly completely oxidized with oxidation ratio of 99.35%. Only 0.034% copper is determined in the residue, suggesting that effective leaching of copper is realized in the process of pressure oxidation, while such elements as arsenic and antimony are partly leached. Furthermore, low iron content of the residue is observed and iron mainly exists in the form of basic iron sulfate or jarosite.
Table 10 Results from comprehensive experiment of pressure oxidation
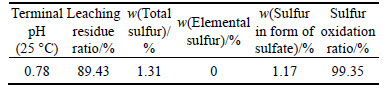
Table 11 Chemical composition of pressure oxidation residue
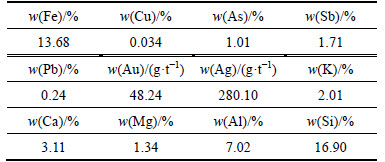
4 Conclusions
1) The optional experimental conditions of acid pretreatment are liquid-to-solid ratio of 4:1 or 5:1, 2 h, Fe3+ concentration of 20 g/L and sulfuric acid concentration of 20 g/L. The decomposition ratio of carbonate is proven to be over 98%, which is beneficial for further pressure oxidation.
2) The results of pressure oxidation experiments show that sulfur content in the solid residue is lower with oxidation time of 4 h. The content of sulfur and iron increases with the reaction time prolonging to 6 and 8 h. Therefore, it is necessary to precisely control the experimental conditions of pressure oxidation in the production process. Ferric subsulfate dissolution can decrease the residue ratio and the sulfur content. Under the conditions of oxidation time of 4 h, temperature of 200-220 °C, oxygen partial pressure of 0.6-0.8 MPa and stirring speed of 600 r/min, the residue ratio is 89.43% and the sulfur oxidation ratio is over 98%.
References
[1] PANGUM L S, BROWNERT R E. Pressure chloride leaching of a refractory gold ore [J]. Minerals Engineering, 1996, 9(5): 547-556.
[2] WARRIS C J, MCCORMICK P G. Mechanochemical processing of refractory pyrite [J]. Minerals Engineering, 1997, 10(10): 1119-1125.
[3] TAN H, FENG D, LUKEY G C, van DEVENTER J S J. The behaviour of carbonaceous matter in cyanide leaching of gold [J]. Hydrometallurgy, 2005, 78: 226-235.
[4] PYKE B L, JOHNSTON R F, BROOKS P. The characterization and behavior of carbonaceous material in a refractory gold bearing ore [J]. Minerals Engineering, 1999, 12(8): 851-862.
[5] FARAZ S, HOSSNA D, REZGAR B, PIROZ Z. Improved recovery of a low-grade refractory gold ore using flotation-preoxidation- cyanidation methods [J]. International Journal of Mining Science and Technology, 2014, 24: 537-542.
[6] LAWRENCE R W, BRUYNESTEYN A. Biological pre-oxidation to enhance gold and silver recovery from refractory ores and concentrates [J]. CIM Bulletin, 1983, 76(857): 107-110.
[7] DENG Tian-long, LIAO Meng-xia. Gold recovery enhancement from a refractory flotation concentrate by sequential bioleaching and thiourea leach [J]. Hydrometallurgy, 2002, 63(3): 249-255.
[8] LABROOY S R, LINGE H G, WALKER G S. Review of gold extraction from ores [J]. Minerals Engineering, 1994, 7(10): 1213- 1241.
[9] ANGELIDIS T N, KYDROS K A. Selective gold dissolution from a roasted auriferous pyrite-arsenopyrite concentrate [J]. Hydrometallurgy, 1995, 37 (1): 75-88.
[10] LI Qing-cui, LI Deng-xin, QIAN Fang-jun. Pre-oxidation of high- sulfur and high-arsenic refractory gold concentrate by ozone and ferric ions in acidic media [J]. Hydrometallurgy, 2009, 97: 61-66.
[11] MASON P G. Energy requirements for the pressure oxidation of gold-bearing sulphides [J]. JOM, 1990, 42(9): 15-18.
[12] LANGHANS D, LORD A, LAMPSHIRE D, BURBANK A, BAGLIN E. Biooxidation of an arsenic-bearing refractory gold ore [J]. Minerals Engineering, 1995, 8(1/2): 147-158.
[13] UBALDINI S,
F, TORO L, ABBRUZZESE C. Combined bio- hydrometallurgical process for gold recovery from refractory stibnite [J]. Minerals Engineering, 2000, 13(14/15): 1641-1646.
[14] YANG Hong-ying, LIU Qian, SONG Xiang-ling, DONG Jing-kui. Research status of carbonaceous matter in carbonaceous gold ores and bio-oxidation pretreatment [J]. Transactions of Nonferrous Metals Society of China, 2013, 23: 3405-3411.
[15] GAO Guo-long, LI Deng-xin, ZHONG Yong, SUN Xian-hao, SUN Wen. Kinetics of high-sulphur and high-arsenic refractory gold concentrate oxidation by dilute nitric acid under mild conditions [J]. Minerals Engineering, 2009, 22: 111-115.
[16] LONG H, DIXON D G. Pressure oxidation of pyrite in sulfuric acid media: a kinetic study [J]. Hydrometallurgy, 2004, 73: 335-349.
[17] NYAYOR K, EGIEBOR N O. Controlling SO2 emissions in the roasting of gold concentrate [J]. JOM, 1991, 43(12): 32-34.
[18] LEHMANN M N,
S, DUNN J G. An evaluation of pretreatments to increase gold recovery from a refractory ore containing arsenopyrite and pyrrhotite [J]. Minerals Engineering, 2000, 13(1): l-18.
[19] GUDYANGA F P, MAHLANGU T, ROMAN R J, MUNGOSHI J, MBEVE K. An acidic pressure oxidation pre-treatment of refractory gold concentrates from the Kwekwe roasting plant, Zimbabwe [J]. Minerals Engineering, 1999, 12(8): 863-875.
(Edited by YANG Bing)
Foundation item: Project(51404296) supported by the Young Scientists Fund of National Natural Science Foundation of China; Project(134414) supported by the Postdoctoral Funded Program of Central South University, China
Received date: 2015-03-30; Accepted date: 2015-07-22
Corresponding author: YANG Tian-zu, Professor; Tel: +86-731-88830923; E-mail: tianzuyang@csu.edu.cn