J. Cent. South Univ. Technol. (2011) 18: 331-336
DOI: 10.1007/s11771-011-0700-z
Pyrolysis kinetics and TG-FTIR analysis of waste epoxy printed circuit boards
ZHAN Zhi-hua(湛志华), QIU Ke-qiang(丘克强)
School of Chemistry and Chemical Engineering, Central South University, Changsha 410083, China
? Central South University Press and Springer-Verlag Berlin Heidelberg 2011
Abstract: Thermal decomposition of waste epoxy PCBs was performed in different atmospheres (nitrogen, argon, air and vacuum) at a heating rate of 10 °C/min by DSC-TGA, and the pyrolysis characteristic was analyzed. The gases volatilized from the experiment were qualitatively analyzed by TG-FTIR. Kinetics study shows that pyrolysis reaction takes place between 300 and 400 °C, and the activation energies are 256, 212 and 186.2 kJ/mol in nitrogen, argon and vacuum, respectively. There are two mass-loss processes in the decomposition under air atmosphere. In the first mass-loss process, the decomposition is the main reaction, and in the second process, the oxidation is the main reaction. The activation energy of the second mass-loss process is 99.6 kJ/mol by isothermal heat-treatments. TG-FTIR analysis shows carbon dioxide, carbon monoxide, hydrogen bromide, phenol and substituent phenol are given off during the pyrolysis of waste epoxy PCBs.
Key words: pyrolysis; kinetics; waste; printed circuit boards
1 Introduction
Every year, 20-50 million tons of electrical and electronic equipment (EEE) wastes are generated worldwide [1], which could bring serious risks to the human health and the environment. The production of printed circuit boards (PCBs) is the basis of the electronic industry as it is an essential part of almost all EEE. The PCB is indispensable to the manufacture and seld about $ 1 trillion each year [2]. In recent years, the average rate of worldwide PCBs manufacture has been increased by 8.7%, and this figure is much higher in Southeast Asia (10.8%) and the mainland of China (14.4%) [1]. A new environmental challenge is confronted by waste PCBs which consist of organic material, metals, and glass fiber [3]. The organic part in PCBs is mainly thermosetting resin with plenty of toxic substances [4]. They can cause serious environmental problems in the absence of proper disposal. Randomly discarding waste PCBs, burning or simple landfill will produce potential hazardous products, mainly including dioxins, furans, brominated organic pollutants and polycyclic aromatic hydrocarbons. Simple landfill or random discard will make the leachate infiltrate into groundwater and soil, in which the leachate may contain heavy metals [5-6]. Therefore, avoiding environmental pollution and recycling valuable resources from waste PCBs are of a great practical significance for continuous improvement of human living environment and resources recycling.
Pyrolysis is one of the promising thermal approaches that can be used to convert organic parts into energy or chemical feedstock, and to recycle the metals and glass fiber [3]. The pyrolysis process is highly complex and depends on several factors such as raw materials composition, and heating rate [7]. Thermo- gravimetric analysis is the preferred technique for obtaining thermal events and thermal decomposition kinetics during pyrolysis because of the relatively easy and straightforward manner for obtaining mass loss data needed for determination of pyrolysis kinetics. Knowledge of pyrolysis kinetics during thermal decomposition of PCBs is needed for design, operation and control of thermochemical conversion units such as gasifiers and pyrolysis reactors [8].
Most of the previous investigations on PCBs pyrolysis have focused on mass loss rate as a function of various parameters such as heating rate and sample size. CHIANG et al [9] investigated the effect of particle size and process temperature on the PCBs, and measured the thermal decomposition kinetics under nitrogen atmosphere. MOLTO et al [4] found that the following gas products were obtained from thermal decomposition of PCBs: CO2, CO, H2O, CH4, phenol and so on. However, the pyrolysis characterization under vacuum and the real time analysis of gas release during the course of pyrolysis are rarely studied. Information on the type, quantity and time of release of a gas product is essential to complete understanding of the mechanism involved in the pyrolysis of PCBs, and it is important to highly effective recovery of waste PCBs.
The objectives of this study were to determine the pyrolysis characterization of waste PCBs in different atmospheres (N2, Ar, air and vacuum), and the kinetic parameters, such as activation energy (E), pre- exponential factor (A), and the rate constants at several temperatures (kT), were obtained from the analysis of mass-loss of the samples in different atmospheres, and to qualitatively analyze the composition of gas evolved during the thermal pyrolysis process by TG-FTIR.
2 Experimental
2.1 Materials
Bare epoxy printed circuit boards without any electronic components and metals were used in this study, and the waste PCBs were provided by China Changsha PCB Co., Ltd. Bare PCBs were chosen because the existence of metal and electronic components may influence the pyrolysis characteristics [10]. The component and their contents were significantly different from one PCB to anther [4-5, 8]. The received samples were re-shredded by a laboratory hammer mill to homogenize the samples, and prepared for TG analysis, elemental analysis and SEM-EDS analysis.
Elemental analysis and proximate analysis of PCBs were carried out in an Elementar Vario ELⅢ and an industrial analyzer 5E-MAG600, respectively, and the content of Br in PCBs was analyzed with a SEM (Inca, JSM-6700F) equipped with an energy dispersive X-ray spectrometer (EDS; KIVEX SIFMATM). The results are listed in Table 1.
Table 1 Elemental analysis and proximate analysis results of PCBs
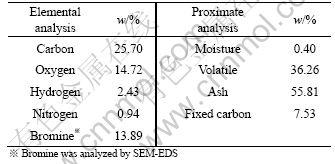
2.2 Methods
All TG curves were recorded on an SDT Q600 V8.0 Build 95 thermalanalyzer, using powdered samples with an initial mass of 10-15 mg placed in open crucibles. The thermal behavior of the sample was tested by recording TG curves under Ar, N2 and air flow, respectively, with a heating rate of 10 °C/min up to 650 °C. The flow velocity of carrier gas was 70 mL/min. These curves defined the range of temperature for the implementation of the kinetic study.
For the kinetic analysis of oxidation decomposition, isothermal TG curves were recorded under an air flow of 70 mL/min, with a heating-rate of 10 °C/min up to the oxidation temperature, which varied from 400 to 480 °C. The mass-loss curve was then recorded, with residence time at each oxidation temperature which was defined by the time needed for mass-loss stabilization, limited to 45 min for the PCBs sample. The range of temperature for isothermal experiments was defined by the TG curve obtained from the thermal decomposition under air with the final temperature of 650 °C.
The usual procedure for the test under vacuum was to introduce a nitrogen flow into the thermogravimetric analyzer for 30 min at room temperature after loading the sample into the crucible, close the system and turn on the vacuum pump. When the total pressure was stabilized at 1.35 kPa, the heating was started. The PCBs sample was heated up to a final temperature of 650 °C, after the decomposition of the sample was accomplished. The mass loss curve (TG) and the mass loss derivative curve (DTG) were recorded as a function of time and temperature.
Several kinetic models commonly reported in the literature were tested to analyze the non-isothermal mass-gain curves [4]. The first-order model manifested the best agreement with the experimental data, which was in accordance with the previous similar studies [8]. The kinetic parameters of PCBs pyrolysis were determined by the integral method [11-12]. For a first-order reaction, the following equations of kinetics in Arrhenius form were derived for the PCBs conversion rate [13]:
(1)
where t is time; α is pyrolysis conversion rate which can be calculated by α=(m0-mt)/(m0-mf), where m0 is the original mass of the sample, mt is the mass at t time and mf is the final mass at the end of pyrolysis; kT is the rate constant at an absolute temperature T.
The temperature dependence of the rate constant kT was assumed to be of the Arrhenius type:
(2)
where E is the activation energy; A is the pre-exponential factor.
For a constant heating rate β during pyrolysis process, β=dT/dt, rearranging and integrating Eqs.(1) and (2) can obtain the following equation:
(3)
For most values of E, and for the narrow temperature range of the pyrolysis, it may be shown that the expression ln[(AR/βE)?(1-2RT/E)] in Eq.(3) is essentially constant. If the left side of Eq.(3) is plotted versus 1/T, a straight line may be obtained if the process can be assumed as a first order reaction. From the slope, -E/R, the activation energy E can be determined. Taking the temperature at which mt=(m0+mf)/2 in the place of T in the intercept term of Eq. (3), the pre-exponential factor A can also be determined.
2.3 TG-FTIR analysis of waste PCBs pyrolysis
The equipment utilized was a thermogravimetric analyzer (NETZSCH, TG209) coupled with a Fourier transform infrared (FTIR, BRUKER, VECTOR22) spectrometer for analysis of evolved gases. In this study, the nitrogen was used as the carrier gas. The initial sample mass was 59 mg, and the N2 flow rate was 40 mL/min. The sample was heated to 850 °C at a heating rate of 10 °C/min. The transfer line was maintained at 250 °C to prevent the condensation of the volatile gases evolved during the pyrolysis process. The software provided by the FTIR spectrometer manufacturer was used to obtain the spectra of the gas through the measurement cell.
3 Results and discussion
3.1 Raw material composition
The representative compositions of the analyzed PCBs are listed in Table 1. The main elements are carbon and oxygen. The carbon content is higher than the data reported by GUAN et al [3] and CHEN et al [12]. This may be caused by the different types of PCBs and analytical methods; furthermore, the sample used in this study is bare PCBs without metal and electronic components. In addition, the moisture, volatile, ash, and fixed carbon of the PCBs were analyzed by an industrial analyzer, and their contents are 0.40%, 36.26%, 55.81% and 7.53%, respectively.
In Table 1, the total content of carbon, oxygen, hydrogen, nitrogen and bromine is 57.68%. The elemental analyzer measured the elemental content of samples by thermal volatilization, and there is residue in the reaction tank of the elemental analyzer and it is a mixture of glass fiber and carbon.
3.2 Kinetics of pyrolysis process
Fig.1 and Fig.2 show the TG and DTG plots for the thermal decomposition of waste PCBs in nitrogen, argon, air and vacuum. In these figures, the mass fraction represents the residual mass fraction of the solid, which is the sum of the residue formed and the non-reacted initial solid.
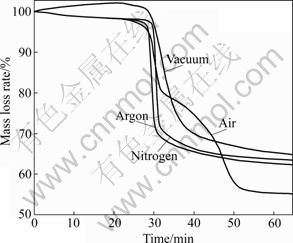
Fig.1 TG curves of waste PCBs pyrolysis under different conditions
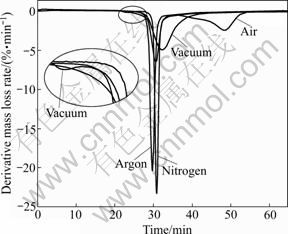
Fig.2 DTG curves of waster PCBs pyrolysis in different atmospheres
From the DTG curve (Fig.2) for a pyrolysis run in vacuum, it can be seen that there are two degradation stages during the PCBs vacuum pyrolysis process. One is a small peak at 237-277 °C with a mass loss of about 1.5%. This peak is due to the loss of moisture and small molecule materials, such as H2O and CO2 [4, 8, 13]. It is noticeable that the peak is not found on the curves of pyrolysis in N2 and Ar atmospheres, maybe because the small molecules are easier to form and escape under vacuum environment. The other peak is sharp and large ranging from 287 to 460 °C in Fig.2, and there is a mass loss of 31.8% at 460 °C. The main reaction corresponds to the second peak. Fig.3 shows the TG plot for PCBs pyrolysis in argon atmosphere alone, and the value of increment of temperature difference is also plotted in a convenient scale. It can be observed that there is an exothermic peak at around 308 °C.
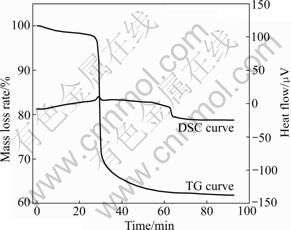
Fig.3 TG and DSC curves of PCBs pyrolysis in argon
Table 2 lists the PCBs pyrolysis kinetic parameters (only the main reaction was taken into account in this study), including the activation energy, pre-exponential factor and corresponding fractional conversion. The activation energies are 186.2, 212 and 256 kJ/mol under vacuum, argon and nitrogen conditions, respectively. The results indicate that the pyrolysis under vacuum can reduce the activation energy effectively compared with pyrolysis under argon or nitrogen atmosphere.
Table 2 Kinetic parameters obtained for pyrolysis in different atmospheres of PCBs
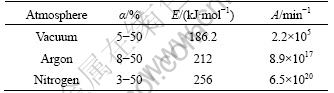
3.3 Kinetics of oxidation process
Fig.4 shows the experimental TG plot of thermal decomposition in air atmosphere at a heating rate of 10 °C/min. The corresponding DSC curve is also plotted, and there is a small endothermic band due to the loss of moisture and small molecule materials at 272 °C, and later two significant exothermic processes take place at around 323 and 505 °C, respectively.
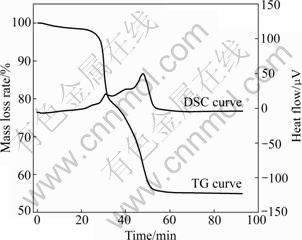
Fig.4 TG and DSC curves of PCBs combustion in air
There are two reactions, thermal decomposition and oxidation, considered for the decomposition of waste PCBs in air and one competes with the other [4]. Under the oxidizing atmosphere, the PCBs sample shows a significant mass-loss between 302 and 338 °C. In conformance, the TG curves obtained in N2 and Ar show significant mass variation between 302 and 338 °C, indicating that the mass-loss due to the decomposition of PCBs becomes dominant in this temperature range. At higher temperature, there is a significant mass-loss between 410 and 536 °C. In contrast, the TG curves obtained in N2 and Ar show light mass variation between 410 and 536 °C, indicating that the main reaction is the oxidation of the residue which includes raw material and the residue possibly formed in the decomposition [14-15].
After the definition of the range of temperature corresponding to the thermal decomposition associated with the air, isothermal runs were performed at selected temperatures in this range. Fig.5 presents the time dependence of the mass of the PCBs sample during the isothermal oxidation decomposition at 420, 440 and 460 °C. These experiments started with a heating rate of 10 °C/min until the desired temperature was reached, and then the final temperature was maintained constant throughout the decomposition process.
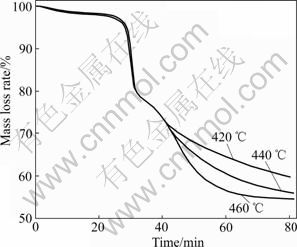
Fig.5 Isothermal curves of PCBs combustion under air
The first-order model was adjusted for the isothermal curves, as shown in Fig.6, in a time interval from the beginning of the isothermal regime. The good linearity of these plots shows that the first-order reaction model (Eq.(1)) is indeed appropriate to describe the oxidation process of PCBs. The slope of each straight line yield the value of the rate constant kT for each temperature [16], 0.050 9, 0.057 81 and 0.131 55 min-1 at 420, 440 and 460 °C, respectively. With these values, the Arrhenius equation (Eq.(2)) was used to construct a plot to obtain the values of E and ln A. The determined activation energy is 99.6 kJ/mol, and the pre-exponential factor ln A is 14.2, which gives the value of A of 1.4×106 min-1.
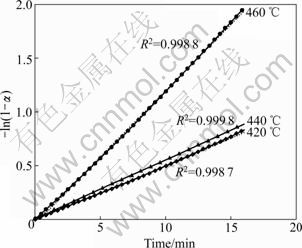
Fig.6 Linearization of second mass-loss curves of combustion in air according to first-order reaction model
3.4 TG-FTIR analysis of gas products
A typical three-dimensional plot of the spectra was obtained from the gas evolved during the pyrolysis of PCBs by TG-FTIR. All absorption peaks are present between 300 and 400 °C and the highest peak is at 332 °C. Fig.7 shows the FT-IR spectra of the gas evolved at 223, 296, 332, 369 and 500 °C, respectively. From Fig.7(c), the peaks at 2 500 and 2 800 cm-1 are distinct, and can be associated with the H—Br stretching. The peaks coincide with the absorption peaks of O—H (3 566 cm-1) in bromophenol and O—H (3 650 cm-1) in phenol [17-18]. This indicates the generation of hydrogen bromide and the decomposition of epoxy resin linkage occur at the same time. This is different from the pyrolysis of PVC [19-20]. Most of the HBr is formed at the quick mass lost stage (300-400 °C), and above 400 °C the bands of HBr cannot be found on the IR spectra.
At 296 °C, the FT-IR bands at 925 and 960 cm-1 suggest the presence of NH3 in the pyrolysis product. From Fig.7, the bands (925 and 960 cm-1) are strong at 296 °C, while they become weak at 332 °C, and the bands cannot be found on the IR spectra of 369 °C. This indicates that NH3 is formed at the initial stage of the pyrolysis reaction. It should be noted that nitrogen is derived from curing agent of epoxy resin, which suggests that the part connected with the curing agent ruptures first before the main chain of epoxy resin breaks.
The main gases identified from the spectra are carbon monoxide (2 030-2 235 cm-1), carbon dioxide (2 240-2 400 cm-1), hydrogen bromide (2 500- 2 750 cm-1), phenol (3 649 cm-1, 3 057 cm-1, 1 600 cm-1, 1 176 cm-1), bromined phenol (O—H, 3 566 cm-1), H2O (3 924 cm-1, 1 506 cm-1) and substituent phenol [17-18]. These gases are typically obtained from the pyrolysis of PCBs [19-20]. The peaks at 1 338 cm-1 and 2 970 cm-1 are associated with —CH3. The peaks at 2 942 cm-1 and 2 883 cm-1 are associated with —CH2— [21-22], and the peaks are very weak. This indicates that the aliphatic hydrocarbon is not produced in the pryolysis process of PCBs.
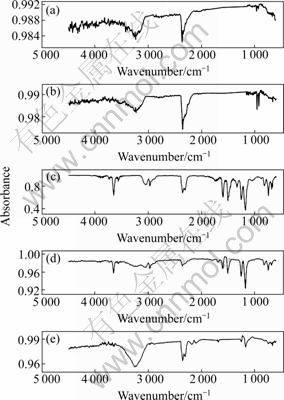
Fig.7 FT-IR spectra of gas evolved during pyrolysis of PCBs: (a) 223 °C; (b) 296 °C; (c) 332 °C; (d) 369 °C; (e) 500 °C
4 Conclusions
1) The thermal decomposition of waste PCBs mainly occurs within the temperature range of 300- 400 °C. Beyond 400 °C, there is only a slight change in mass loss.
2) Pyrolysis kinetics indicates that the pyrolysis in vacuum (E=186 kJ/mol) can reduce the activation energy effectively compared with the decomposition in argon and nitrogen atmosphere (E=212 and 256 kJ/mol, respectively). The oxidation reaction competes with the thermal decomposition in the experiment under air atmosphere. The decomposition reaction is dominant between 302 and 338 °C (the first mass-loss process). In the second mass-loss process between 410 and 536 °C, the main reaction is the oxidation of the residue including raw materials and the residue possibly formed in the decomposition, and the activation energy is 99.6 kJ/mol.
3) The part connected with the curing agent ruptures first before the main chain of epoxy resin breaks and most of the HBr is formed at the quick mass loss stage (300-400 °C) during the pyrolysis of PCBs. The major gases evolved are carbon dioxide, carbon monoxide, hydrogen bromide, phenol and substituent phenol.
References
[1] HUANG Kui, GUO Jie, XU Zhen-ming. Recycling of waste printed circuit boards: A review of current technologies and treatment status in China [J]. J Anal Appl Pyrol, 2009, 164(2/3): 399-408.
[2] LADOU J. Printed circuit board industry [J]. Int J Hyg Environ Health, 2006, 209(3): 211-219.
[3] GUAN J, LI Y S, LU M X. Product characterization of waste printed circuit board by pyrolysis [J]. J Anal Appl Pyrol, 2008, 83(2): 185-189.
[4] MOLTO J, FONT R, GALVEZ A, CONESA J. Pyrolysis and combustion of electronic wastes [J]. J Anal Appl Pyrol, 2009, 84(1): 68-78.
[5] HALL W J, WILLIAMS P T. Separation and recovery of materials from scrap printed circuit boards [J]. Resour Conserv Recy, 2007, 51(3): 691-709.
[6] BALABANOVICH A L, LUDA M P, OPERTI L. GC/MS identification of pyrolysis products of fire-retardant brominated epoxy resin [J]. J Fire Sci, 2005, 23(3): 227-245.
[7] HALL W J, WILLIAMS P T. Pyrolysis of brominated feedstock plastic in a fluidized bed reactor [J]. J Anal Appl Pyrol, 2006, 77(1): 75-82.
[8] YOSHIKAGE O, ISAO H, KAZUHIRO M. Pyrolysis of the mixture of biomass and plastics in countercurrent flow reactor: Part I. Experimental analysis and modeling of kinetics [J]. Fuel, 2008, 87(13/14): 3105-3111.
[9] CHIANG H L, LIN K H, LAI M H, CHEN T C, MA S Y. Pyrolysis characteristics of integrated circuit boards at various particle sizes and temperatures [J]. J Hazard Mater, 2007, 149(1): 151-159.
[10] HALL W, PAUL T. Removal of organobromine compounds from the pyrolysis oils of flame retarded plastics using zeolite catalysts [J]. J Anal Appl Pyrol, 2008, 81(2): 139-147.
[11] ZHOU L, WANG Y, HUANG Q, CAI J. Thermogravimetric characteristics and kinetic of plastic and biomass blends co-pyrolysis [J]. Fuel Process Technol, 2006, 87(11): 963-969.
[12] CHEN K S, CHEN H C, WU C H, CHOU Y M. Kinetics of thermal and oxidative decomposition of printed circuit boards [J]. J Environ Eng, 1999, 125(3): 277-283.
[13] ALTOE G F, FREITAS J C C, CUNHA A G, ERNMERICH F G, SMITH M E. Kinetics and C-13 NMR study of oxygen incorporation into PVC- and pitch-derived materials [J]. Energ Fuel, 2009, 23(3): 1373-1378.
[14] HA H, LEE T, LEE S, KIM D, JOO H. Oxidative stabilization mechanism of poly(vinyl chloride) pitch [J]. Polym Degrad Stabil, 2000, 68(2): 247-252.
[15] LUDA M P, BALABANOVICH A I, ZANETTI M, GUARATTO D. Thermal decomposition of fire retardant brominated epoxy resins cured with different nitrogen containing hardeners [J]. Polym Degrad Stabil, 2007, 92(6): 1088-1100.
[16] BUKHARKINA T V, DIGUROV N G. Kinetics of aerobic liquid-phase oxidation of organic compounds [J]. Org Process Res Dev, 2004, 8(3): 320-329.
[17] BHASKAR T, KANEKO J, MUTO A, SAKATA Y, JAKAB E, MATSUI T, UDDIN M A. Pyrolysis studies of PP/PE/PS/PVC/HIPS-Br plastics mixed with PET and dehalogenation (Br, Cl) of the liquid products [J]. J Anal Appl Pyrol, 2004, 72(1): 27-33.
[18] DUAN Ji-an, CAI Guo-hua, SHUAI Ci-jun. The relationship between IR characteristic peak and microstructure of the glass used as optical fiber [J]. J Cent South Univ Technol, 2006, 13(3): 238-241.
[19] ZHU H M, JIANG X G, YAN J H, CHI Y, CEN K F. TG-FTIR analysis of PVC thermal degradation and HCl removal [J]. J Anal Appl Pyrol, 2008, 82(1): 1-9.
[20] GRAUSE G, FURUSAWA M, OKUWAKI A, YOSHIOKA T. Pyrolysis of tetrabromobisphenol-A containing paper laminated printed circuit boards [J]. Chemosphere, 2008, 71(5): 872-878.
[21] CHIEN Y C, WANG H P, LIN K S, HUANG Y J, YANG Y W. Fate of bromine in pyrolysis of printed circuit board wasters [J]. Chemosphere, 2000, 40(4): 383-387.
[22] DE M I, CABALLERO B M, CHOMON M J, LARESGOITI M F, TORRES A, FERNANDEZ G, ARNAIZ S. Pyrolysis of electrical and electronic wastes [J]. J Anal Appl Pyrol, 2008, 82(2): 179-183.
(Edited by YANG Bing)
Foundation item: Project(2006AA06Z375) supported by the National High-tech Research and Development Program of China
Received date: 2010-05-20; Accepted date: 2010-11-04
Corresponding author: QIU Ke-qiang, Professor, PhD; Tel: +86-731-88836994; E-mail: qiuwhs@sohu.com