热等静压对等离子喷涂成形制备钼制品的影响
解路1,熊翔1,王跃明1,徐玄1,闵小兵2
(1. 中南大学 粉末冶金国家重点实验室,湖南 长沙,410083;
2. 湖南省冶金材料研究所,湖南 长沙,410014)
摘要:先采用球磨加喷雾干燥制备喷涂钼粉,然后通过等离子喷涂制备预设厚度的钼沉积层,再对其进行热等静压处理制备钼制品。使用阿基米德法测量钼沉积层和钼制品的相对密度,用显微硬度计测量它们的维氏硬度,用万能材料试验机测试它们的拉伸强度,用扫描电镜观察它们的外表面、截面和断口微观形貌。研究结果表明:采用等离子喷涂技术能制备致密度达89.7%、拉伸强度达44 MPa、显微硬度(HV)约152、厚度达5 mm的钼沉积层。钼沉积层经过低压热等静压处理后,其显微结构得到改善,相对密度达92%,力学性能提高(拉伸强度达到54 MPa,显微硬度(HV)约246);经二次高压热等静压处理后,钼沉积层的层状结构特征完全消失,颗粒结合紧密,出现等轴晶粒,伴随晶粒长大,断口出现穿晶解理断裂,相对密度达到97.3%,拉伸强度提高到110 MPa,显微硬度(HV)达到321。
关键词:等离子喷涂成形;钼构件;热等静压;力学性能
中图分类号:TB31 文献标志码:A 文章编号:1672-7207(2011)10-3009-06
Molybdenum products produced by plasma spray forming and hot-isostatic pressing
XIE Lu1, XIONG Xiang1, WANG Yue-ming1, XU Xuan1, MIN Xiao-bing2
(1. State Key Laboratory of Powder Metallurgy, Central South University, Changsha 410083, China;
2. Hunan Research Institute of Metallurgy and Materials, Changsha 410014, China)
Abstract: Molybdenum feedstock for plasma spraying was fabricated by mechanical alloying and spray drying. Molybdenum products were produced by plasma spray forming (PSF) followed by hot-isostatic pressing (HIP). The relative density, micro-hardness and tensile strength of Mo products were investigated. Microstructures of surface, cross section and fracture of these products before and after HIP were observed by scanning electron microscope (SEM). The results show that the relative density, tensile strength and micro-hardness of PSF products increase from 89.7%, 44 MPa and 152 to 97.3%, 110 MPa and 321, after two-step hot-isostatic pressing, respectively.
Key words: plasma spraying forming; molybdenum products; hot-isostatic pressing; mechanical property
由于钼具有很高的熔点,较大的热强度,良好的导热和导电性能,以及对酸、碱和熔融金属有很高的抗蚀能力,在现代工业和科技中的作用越来越重要[1]。为了满足更多更苛刻的使用环境,人们对于钼制零部件的制备方法和性能有更高的要求。传统的钼制零部件的制备方法主要是用粉末冶金方法。粉末冶金方法只适用于制备小尺寸以及简单形状的零部件。由于模具形状复杂以及薄壁容易在脱模过程中破碎,采用粉末冶金法难以制备大尺寸(直径大于1 m)、复杂形状(回转体、多台阶零部件等)、壁厚太小(小于10 mm)的零部件。在高温烧结过程中黏结剂的挥发会导致零部件收缩率高,变形大,孔洞较多,从而使制品密度减小,强度降低,在使用过程中容易断裂、破碎。所有这些因素导致通过粉末冶金法制备的尺寸大、形状复杂、零部件壁薄的成品率低,成本高。因此,必须寻求新的成形技术制备大尺寸以及复杂形状零部件和薄壁零部件。等离子喷涂因其具有极高的火焰中心温度(10 000 ℃以上),可以熔化任何金属材料,加之熔融液滴具有很高的飞行速度,使其冷凝粉末颗粒能够很好地黏结成形,逐渐发展成为一种新型的零部件成形技术,可以用于制备各种复杂形状金属零部件[2-6]。吴子健等[7]采用等离子喷涂成形技术制备了大直径钨管发热体,分析了钨管发热体成形沉积模具类型、喷涂工艺参数对沉积管坯密度、热应力、抗裂性的影响,得到性能优良的钨零部件。但是,国内对难熔金属的等离子喷涂成形研究较少,目前还没有见到等离子喷涂制备钼制品的相关研究报道。钼制零部件的成形与应用已经越来越被人们所关注[8-12],所以,应该加强等离子喷涂成形技术制备钼制零部件的研究工作。在此,本文作者采用球磨加喷雾干燥制备喷涂钼粉,通过等离子喷涂制备预设厚度的钼沉积层,经过热等静压处理制备钼制品,并用常规测试手段对它们的各种性能进行检测,分析热等静压工艺参数对其组织性能的影响。
1 实验
使用平均粒度约为3 μm、形状为多角形、纯度为99.5%的商用钼粉作为原材料。因其流动性较差,容易堵塞送粉管,必须先对其进行处理,得到粒度适中、球形度好的可喷涂粉末。为此,采用XQM-4L型号的行星式球磨机对商用钼粉进行球磨。球磨参数如下:球料质量比为5:1,球磨时间为50 h,转速为250 r/min,研磨介质为酒精,滚球是直径为7.5 mm的硬质合金球。将球磨得到的粉末加至预先溶解于蒸馏水中的黏结剂PVA(聚乙烯醇)与分散剂PEG(聚乙二醇)混合溶液中,制得料浆;然后,把料浆经由蠕动泵送入高速离心式雾化器进行喷雾干燥。喷雾干燥参数如下:进口温度为300 ℃,出口温度为150 ℃,转盘转速为 15 000 r/min,料浆输送速度为60~100 mL/min。将干燥后收集到的粉末在850 ℃的氢气气氛下脱脂1 h。采用Micro-Plus激光粒度分析仪测定粉末颗粒的粒度分布。
所用等离子喷涂设备的型号为DH-1080,其最大功率为80 kW。以直径×高为30 mm×80 mm的石墨筒为芯模,转速为60 r/min,在大气环境下进行喷涂。为防止涂层烧损和氧化,采用压缩氮气进行冷却。表1所示为喷涂过程中的工艺参数。
表1 等离子喷涂过程中的工艺参数
Table 1 Plasma spray forming (PSF) parameters

等离子喷涂成形后,采用机加工去除芯模。将沉积层切割成2份:一份采用低压热等静压进行处理(在1 500 ℃和10 MPa下烧结90 min);对另一份先进行低压热等静压,然后,进行高压处理(即先在1 500 ℃和10 MPa下烧结90 min,冷却后,再在1 600 ℃和125 MPa下烧结120 min)。每次热等静压处理的加热和冷却速度分别为10 ℃/min和20 ℃/min。
用阿基米德排水法测定成形件的密度。沉积层和成形件的显微硬度测试过程如下:施加载荷0.25 N,持续15 s,每个样品至少测试6个点,取其平均值。按照GB 2975—82标准制备拉伸试样,用线切割沿沉积层和成形件的轴线方向切取厚为2.5 mm、总长为15 mm、宽为5 mm的“工”字形样品(“工”字中部长为11 mm、宽为2.5 mm)。在Instron3369试验机上测量样品的抗拉强度,拉伸速率为1×100 s-1。先用金刚石砂纸磨平,再分别用金刚石抛光液对其进行抛光制备金相试样。采用JEOL JSM-6360LV扫描电镜对喷涂粉末和沉积层以及成形件的显微结构进行观察。
2 结果与分析
2.1 喷涂粉末显微形貌
经过激光粒度分析检测得知,制备的喷涂钼粉粒度为30~50 μm。按照ISO4490,用霍尔流动计测得粉末的流动性为13 s/50 g(流动计口径2.5 mm,粉末在重力作用下自动流下),满足喷涂要求。图1所示为所制备的喷涂钼粉显微形貌照片。
从图1可以看到:大部分粉末已经团聚成为空心球形团聚体(由许多细小颗粒互相黏结而成)。形成空心颗粒的原因是喷雾干燥料浆的固体含量(质量分数)较低(约50%)。在料浆离开雾化器后的下落干燥过程中,毛细管力以及外部热量促使液相向外蒸发(当固体含量低时,不足以填充原来液相的位置,于是,在颗粒内部形成孔隙)。这种在液体全部蒸发完之后,形成空心粉末颗粒的机制在料浆固体含量较低时起主导作用[13]。
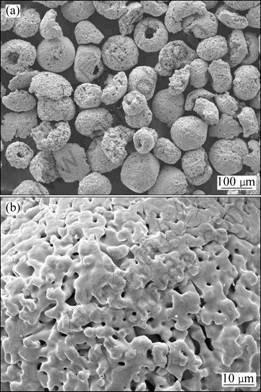
图1 喷涂钼粉的显微形貌
Fig.1 SEM micrographs of plasma sprayed Mo powders
空心颗粒的存在会导致喷雾干燥后粉末的松装密度降低,进而影响粉末的流动性。所以,在喷雾干燥过程中,选择合适的固体含量是制备料浆的关键因素。
2.2 喷涂沉积层的显微形貌
图2所示为喷涂沉积层外表面的显微形貌。从图2(a)和2(b)可以看出在表1中的工艺参数下喷涂获得的沉积层表面液滴凝固次序,但是,有个别地方没有完全覆盖,形成孔洞(图中深黑色部分)。说明在该工艺参数下,熔融颗粒在基体上铺展得很充分,单个片层很薄,其差异是喷涂钼粉本身的粒度差异造成的。
从图2(c)可以看到:在沉积层的表面有一些大的椭球状凹坑。通过对喷涂粒子的飞行过程进行分析,认为这可能是由于一些大颗粒以高温高速从喷枪飞向沉积层的过程中没有完全熔化,到达沉积层时仅仅是表面熔融而中心仍然是固体未熔颗粒;当它们高速撞击基体时,熔融部分顺利铺展开成为沉积层,但是,固体未熔颗粒因为高速撞击反弹,脱离熔融部分,在沉积层上留下了一个个椭球形的凹坑[14]。
在图2(c)中还可以看到沉积层中的裂纹。这是因为高温粒子在迅速冷却时,有部分热应力未能得到释放,残留在沉积层中;当热应力足够大时,这部分热应力通过在沉积层中形成裂纹而释放。
从图2(d)可以看到沉积层表面有一些较浅的孔洞,这是高温熔融粒子在飞行过程中表面溶解了部分气体所致(粒子撞击基体冷却形成沉积层时,气体挥发逸出形成小孔)。
图3所示为喷涂沉积层横截面的SEM照片。从图3(a)可以看出:沉积层基本由变形的条带状颗粒堆积而成,呈典型层状结构;颗粒间存在孔洞和微观缝隙。由于熔融粒子撞击沉积表面后冷却速度较高(陶瓷粒子的冷却速度为1×104~1×106 ℃/s,金属粒子的冷却速度为1×106~1×108 ℃/s 甚至更高[15]),前一颗熔滴撞击沉积表面形成涂层与后一颗熔滴撞击相隔大约0.1 s,所以,可以认为每个喷涂粒子的行为都是独立的[16]。在后一颗熔滴到来之前, 前一熔滴有足够的时间变形凝固和充分冷却,最终涂层由一个个熔滴经过撞击→扁平变形→冷却凝固堆积而成。
从图3(b)可以看到沉积层中有少量灰色圆形颗粒,这是由于一些大颗粒沉积时没有完全熔化,大部分保持固体颗粒夹杂在沉积层中。
图3(c)所示是经低压热等静压处理后的沉积层截面形貌。由图3(c)可以看出:由于压力低,时间短,经低压热等静压处理后,温度和压力对沉积层的效果只体现在外层,未能深入。沉积层外层的孔洞和微观缝隙大大减少,层状结构特征已基本消失,但是,沉积层内部显微结构无明显变化。
图3(d)所示经二次高压热等静压处理后的沉积层截面形貌。从图3(d)可以看出:由于高温与高压的作用充分发挥,经过二次热等静压处理后,沉积层内外层显微结构一致,层状结构特征也完全消失。
2.3 喷涂成形件断口形貌观察
图4所示为沉积层的断口形貌照片。从图4(a)可以看到部分断口呈现层间剥离。由图4(b)可以观察到垂直生长的定向凝固柱状晶组织,断口呈现典型的沿晶脆性断裂。由此结合表2可知:由于等离子喷涂沉积层的相对密度较低,层间结合不紧密,主要为柱状晶组织,导致成形件的性能偏低(见表2,相对密度为89.7%,拉伸强度为44 MPa,显微硬度(HV)为152)。
图5所示为喷涂沉积层经过低压热等静压处理后的断口形貌照片。由图5可见:经过低压热等静压处理后,钼沉积层相对密度增加,仍然为层状结构。但晶粒明显长大,由原始柱状晶生长为等轴晶粒,断裂仍易沿层间剥离。
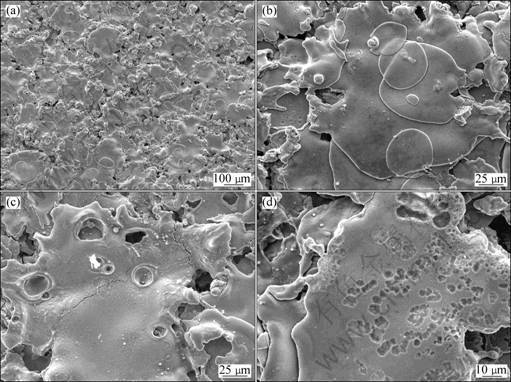
图2 沉积层表面形貌
Fig.2 Surface morphologies of plasma sprayed deposites fabricated according to parameters listed in Table 1
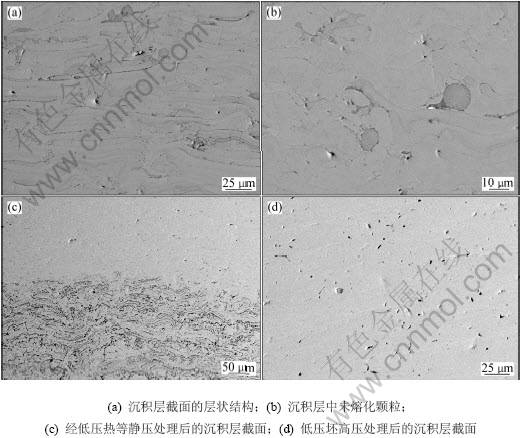
图3 沉积层的截面形貌
Fig.3 Morphologies of cross section of deposits
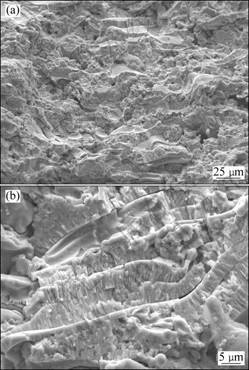
图4 沉积层的断口形貌
Fig.4 Morphologies of fracture of Mo deposits produced
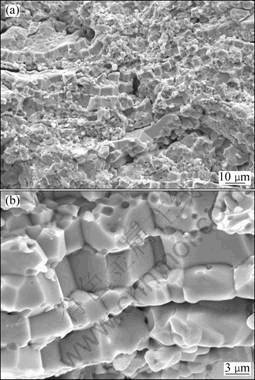
图5 沉积层经低压热等静压处理后的断口形貌
Fig.5 Morphologies of fracture surface of deposits after hot-isostatic pressing under low pressure
图6所示为是经2次高压热等静压处理后钼沉积层的断口形貌照片。从图6(a)可以看到:经过2次热等静压处理后,沉积层的相对密度大大增加,达97.3%(见表2)。部分断口呈现穿晶解理断裂,表明沉积层强度得到提高。由图6(b)可见:由于高温高压的联合作用,晶粒进一步显著长大,已完全破坏原始层状组织结构。
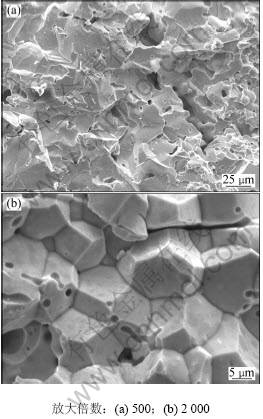
图6 低压坯高压处理后的Mo沉积层的断口显微形貌
Fig.6 Morphologies of fracture surface of Mo deposit after two hot-isostatic pressings
2.4 喷涂成形件的力学性能
表2所示为通过不同工艺制备的等离子喷涂钼成形件的性能。由表2可以看出:采用热等静压对等离子喷涂成形件进行处理可以大幅度提高其性能;随着热等静压工艺的改进,成形件性能也随之不断提高。经分析认为:这是由于在热等静压的过程中,高温高压的联合作用使得沉积层中的颗粒片层逐渐靠近,紧密贴合,发生颗粒再结晶、颗粒重排、塑性流动、扩散蠕变等变化,层状结构特征消失,从而沉积层更加致密,各项性能都得到提高。但是,晶粒的严重长大会影响力学性能的提高,所以,需采取有效措施控制晶粒长大,减小晶粒度。
表2 通过各种工艺制备的钼成形件的性能
Table 2 Properties of Mo products produced by various technologies
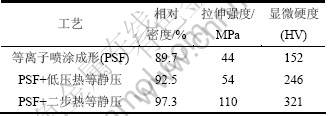
3 结论
(1) 等离子喷涂沉积层呈现出典型的层状结构,孔隙和裂纹较多,颗粒铺展充分。
(2) 对等离子喷涂成形件进行热等静压处理可以大幅度提高其力学性能;随着热等静压工艺的改进,成形件的力学性能不断提高。在低压热等静压之后再对成形件进行高压处理,其相对密度由89.7%提高到97.3%,拉伸强度由44 MPa提高到110 MPa,显微硬度(HV)由152提高到321。
(3) 经过低压和高压的二次热等静压处理后,喷涂成形件层状结构特征完全消失,颗粒结合紧密,出现再结晶等轴晶粒,晶粒显著长大;成形件部分断口呈现穿晶解理断裂,即晶粒界面强度提高。
参考文献:
[1] 张文钲. 世界钼业20年[J]. 中国钼业, 1997, 21(2/3): 15-21.
ZHANG Wen-zheng. 20 years of national Mo industry[J]. China Molybdenum Industry, 1997, 21(2/3): 15-21.
[2] Fang J C, Xu W J. Plasma spray forming[J]. Materials Processing Technology, 2002, 129(1/3): 288-293.
[3] Pawlowsky L. The science and engineering of thermal spray coatings[M]. New York: Wiley Blackwell, 1995: 43-79.
[4] Sampath S, Herman H, Rapid solidification and microstructure development during plasma spray deposition[J]. Therm Spray Technol, 1996, 5(4): 445-456.
[5] Choo S H, Lee S H, Kwon S J. Metall mater trans[M]. Plasma Spray Forming, 1999(12): 256-258.
[6] Suryanarayanan R. Plasma spraying[M]: Singapore, Theory and Applications, 1993: 137-145.
[7] 吴子健, 张虎寅, 堵新心. 大直径钨管发热体等离子体喷涂成形制造技术[J]. 粉末冶金工业, 2005, 10(5): 1-4.
WU Zi-jian, ZHANG Hu-yan, DU Xin-xin. Plasma spraying manufacturing technique for heating objection of tungsten tubular[J]. Powder Metallurgy Industry, 2005, 10(5): 1-4.
[8] 王慧芳, 方少垣. 高温钼粉的性能对其成形及烧结的影响[J]. 粉末冶金技术, 1994, 12(2): 103-108.
WANG Hui-fang, FANG Shao-yuan. Effects of properties of high temperature molybdenum powder on its compacting and sintering[J]. Powder Metallurgy Technology, 1994, 12(2): 103-108.
[9] 潘叶金. 钼深加工制品的研究与开发[J]. 湖南有色金属, 1994, 10(5): 302-305.
PAN Ye-jin. Research and exploiture of molybdenum product[J]. Hunan Nonferrous Metals, 1994, 10(5): 302-305.
[10] 朱勇, 秦勇. 纳米固体钼和氮化二钼的制备、结构和性能[J]. 功能材料, 1994, 25(5): 416-425.
ZHU Yong, QIN Yong. Preparation, structures and properties of nanostructured Mo and Mo2N[J]. Functional Meterials, 1994, 25(5): 416-425.
[11] 郭志俊, 张树才, 林勇. 田口方法在钼材料性能研究中的应用[J]. 中国钼业, 2006, 30(5): 36-38.
GIP Zhi-jun, ZHANG Shu-cai, LIN Yong. The application of taguchi methods in the study of molybdenum property[J]. China Molybdenum Industry, 2006, 30(5): 36-38.
[12] 卢景友. 金堆城钼业公司钼业现状及发展[J]. 中国钼业, 2001, 25(4): 3-5.
LU Jing-you. The present situation of development of Jinduicheng molybdenum mining corporation[J]. China Molybdenum Industry, 2001, 25(4): 3-5.
[13] Crosby J, Marshall W R Jr, Chemical engineering progress[M]. Aiche, New York, 1958: 56-63.
[14] Li C J, OhmoriA, Harada. Effect of WC particle size on the formation of HVOF sprayed WC-Co coatings[C]//Proceedings of the 14th International Thermal Spray Conference. Kobe, ASM International, 1995: 869-875.
[15] Vardelle M, Vardelle A, Leger A C, et al. Influence of particle parameters at impact on splat formation and solidification in plasma spraying process[J]. Therm Spray Technol, 1994, 4(1): 50-58.
[16] Houben J M, Liempd G G. Metallurgical Interactions of Mo and steel during plasma spraying[C]//Proceedings of the 10th International Thermal Spray Conference. Germany: Germany Welding Society, 1983: 66-71.
(编辑 陈灿华)
收稿日期:2010-11-15;修回日期:2011-03-05
基金项目:湖南省应用基础研究计划重点项目(S2007F12);国防基础科研计划项目(B3720061191)
通信作者:熊翔(1963-),男,湖南湘潭人,博士,教授,从事粉末冶金材料的研究;电话:0731-88836864;E-mail:xiong228@sina.com