
Low cycle fatigue properties and cyclic deformation behavior of
as-extruded AZ31 magnesium alloy
S. KWON1, K. SONG2, K. S. SHIN2, S. I. KWUN1
1. Department of Materials Science and Engineering, Korea University, Seoul 136-701, Korea;
2. School of Materials Science and Engineering, Seoul National University, Seoul 151-744, Korea
Received 23 September 2009; accepted 30 January 2010
Abstract: The low cycle fatigue(LCF) properties of as-extruded AZ31 Mg alloy were investigated under total strain amplitudes in the range of 0.4%-1.2% with strain rate of 1×10-2 s-1. Due to the twinning effect in compression during loading and the detwinning effect during unloading, the alloy showed an asymmetric hysteresis loop. The cyclic stress response exhibited cyclic hardening at high total strain amplitudes. The cyclic deformation behaviors were discussed using the Coffin-Manson plot, which divided the plastic strain amplitudes into the tension side and the compression side. Through the LCF tests that were started from either tension or compression under a total strain amplitude of 1.0%, the interaction between the twinning effect and dislocation was analyzed. The twinning effect during the LCF test and the variation of the dislocation density were investigated using optical microscopy and transmission electron microscopy, respectively.
Key words: AZ31 magnesium alloy; low cycle fatigue; twinning; dislocation
1 Introduction
Due to the increased demand for environmental protection and energy efficiency, the need for lightweight materials for transportation has increased in recent years. At this point, magnesium alloys, which are considered as structural materials, are attractive due to their low density, high specific strength and stiffness[1-13]. When magnesium alloys are extruded, the formation of a strong crystallographic texture with the basal planes parallel to the prior working direction, has previously been recognized[10-13]. The plastic strain parallel to the c-axis cannot be accommodated by basal slip {0001} <
>, because the Burgers vector lies on the basal plane. Since the critical resolved shear stress of prismatic slip {
} <
> and pyramidal slip {
} <
> are nearly 100-fold greater than that of basal slip, and the secondary slip modes are also hard to deform. However, such strain parallel to the c-axis can be produced by twinning[13-14]. The c/a (c and a represent the length of a HCP single crystal along vertical and
horizontal axis, respectively) ratio for magnesium alloy is less than
, so twin will be generated in compression but not in tension perpendicular to the c-axis. Therefore, the compressive yield stress is lower than the tensile yield stress under monotonic loading[15]. The anisotropic property between the tension and compression of magnesium alloys strongly affects their fatigue behaviors. Understanding the cyclic behaviors of structural materials is essential for satisfying the safety requirements, because these materials are often subjected to cyclic loading. Many studies are reported on fatigue of magnesium alloys[2, 4-9]. However, only limited work is done on their low cycle fatigue behavior, which is particularly affected by the cyclic deformation caused by twinning at higher total strain amplitudes in the case of extruded magnesium AZ31 alloy. The objective of this investigation is to evaluate the low cycle fatigue properties of as-extruded magnesium AZ31 alloy and study its cyclic deformation behavior based on the twinning effect and the variation of the dislocation density.
2 Experimental
The as-extruded AZ31 magnesium alloy was used in this study and its chemical composition is shown in Table 1.
The samples were homogenized at 400 ?C for 12 h,
Table 1 Chemical composition of as-extruded AZ31 magne- sium alloy (mass fraction, %)

extruded at 260 ?C and followed by air cooling. Tensile tests using ASTM B557M-06 subsized specimens were carried out with an Instron servo-hydraulic testing system at a constant strain rate of 1×10-2 s-1. The hardness test was conducted with a Shimadzu Vickers hardness tester. The mechanical properties of the AZ31 alloy obtained from the tensile test and Vickers hardness test are shown in Table 2.
Table 2 Mechanical properties of as-extruded AZ31 magnesium alloy

The low cycle fatigue test was performed on the specimens under total strain amplitudes ranging from 0.4% to 1.2% in a computerized Instron servo-hydraulic testing system at room temperature under a constant strain rate of 1×10-2 s-1. To study the interaction between the twinning effect and dislocation, fatigue tests were conducted from either tension or compression under a total strain amplitude of 1.0%. For the microstructural observation, the specimen surfaces were polished with SiC papers up to 2 000 grit and then with alumina powder solution. Then, the gage of the polished specimen was etched with a drop of picric acid solution (4.2 g picric acid, 10 mL acetic acid, 10 mL H2O and 70 mL ethanol) for 5-10 s. The polished and etched specimen was used to investigate the microstructural changes during the low cycle fatigue test, after first tension (1/4 cycle), first compression (3/4 cycle) and 150 cycles. For the transmission electron microscopy observation, the foils were thinned by the twin-jet polishing technique using an electrolyte consisting of 5% HClO4, 35% butanol and 60% methanol at 15 V and -20 ?C. A JEM-2000EX TEM at 200 kV was used for the morphology observation.
3 Results and discussion
3.1 Change of hysteresis loop and microstructure during low cycle fatigue
Fig.1 shows the hysteresis loops of the 1st and 2nd cycles of fatigue under a total strain amplitude of 1.0%.
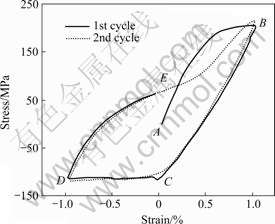
Fig.1 Hysteresis loops of 1st and 2nd cycles of fatigue under a total strain amplitude of 1.0%
The typical hysteresis loops of magnesium alloys loaded along the extrusion direction are asymmetric with sigmoidal shape characteristics due to mechanical twinning[16-17]. When the low cycle fatigue test is started with the specimen under tension, compressive yielding occurs at a lower stress than that of the tensile yield stress due to the twinning generated at point C. Upon unloading from point D to E, the hysteresis loop exhibits an increase in strain due to detwinning. At this stage, the material exhibits pseudoelastic behavior, which is mainly caused by detwinning[18-19]. The dotted line represents the second cycle. During the tension from point E to B in the second cycle, the loop shows an inflection point and the hardening rate rapidly increases beyond this point. This increase in the hardening rate is correlated with the completion of the detwinning mechanism[16]. Once the grains are completely detwinned, deformation by basal slip becomes more difficult to occur, resulting in cyclic hardening[20-21]. Thus, the cyclic tensile stress in the 2nd cycle is higher than that at the 1st cycle.
Fig.2(a) shows the microstructure before fatigue. Fig.2(b) shows the unloaded state after +1.0% strain in tension, and shows no observable difference compared with Fig.2(a). In the case of the tensile-deformed magnesium alloy, twins were generated when the strain was high[15, 22]. However, 1.0% strain seems to be insufficient to induce a large amount of twinning. Fig.2(c) shows that the tensile-deformed specimen is compressed until -1.0% strain and then the load is removed. Fig.2(c) shows several twins in grains after compression, as compared with Figs.2(a) or (b). The twins generated by compressive strain are detwinned by the subsequent tension loading, and the sample subsequently shows cyclic twinning-detwinning behavior during the fatigue test[18]. WU et al[16] found that the volume fraction of
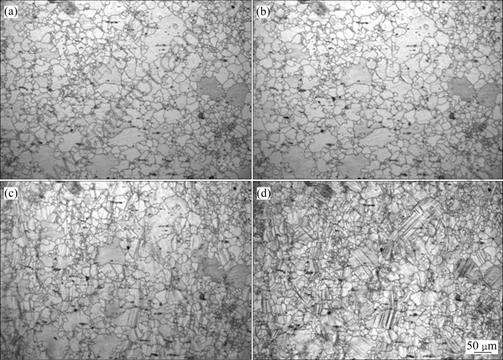
Fig.2 Microstructure evolution of specimen: (a) Initial state; (b) Unloading state after first tension; (c) Unloading state after first compression; (d) After 150 cycles of fatigue at ?ε/2=1.0%
twins gradually increases with increasing number of cycles during the low cycle fatigue test. Fig.2(d) shows a lot of twins after 150 cycles of fatigue under a total strain amplitude of 1.0%.
3.2 Cyclic stress responses
The cyclic stress response curves for this alloy at various total strain amplitudes are shown in Fig.3. In general, the cyclic stress response curve in the low cycle fatigue test is represented using the absolute mean value of either the tensile/compressive stress amplitude or tensile stress amplitude with respect to the number of cycles. As mentioned above, however, since the extruded magnesium alloy has asymmetric mechanical properties of tension and compression, it is difficult to explain its fatigue properties using the normal cyclic stress response curves of this alloy. Therefore, it is reasonable to show the response of cyclic stresses to tension stress and compression stress separately at a given fatigue strain. The cyclic tensile stresses of the alloy at various total strain amplitudes are shown in Fig.3(a). At relatively high total strain amplitudes, cyclic hardening occurs rapidly during the first few cycles and then gradually until final failure. At a lower total strain amplitude of 0.4%, the stress amplitudes remain almost constant in the initial stage and then slightly increase until fracture. The cyclic strain hardening can be generally attributed to the increase of the dislocation density and the dislocation

Fig.3 Cyclic stress response curves at various total strain amplitudes: (a) Tensile stress; (b) Compressive stress
interactions with precipitates during plastic deformation[7].
Fig.3(b) shows the cyclic compressive stress amplitudes with respect to the number of cycles at various strain amplitudes. The sample exhibits a cyclic stress response which is lower than the tensile stress due to the effect of twinning on compression. Moreover, a small amount of cyclic hardening can be observed until failure at all total strain amplitudes. This tendency may be caused by the absence of detwinning and microcracks, which influence the cyclic tensile stress amplitudes.
3.3 Effect of twinning and dislocation on cyclic stress responses
Fig.4 shows the stress—strain hysteresis loops at low cycle fatigue conducted at total strain amplitudes of 0.4% and 0.6%. Compared with Fig.4(a), Fig.4(b) shows a more asymmetric hysteresis loop than Fig.4(a), suggesting that the alloy exhibits stronger twinning deformation characteristics at higher total strain amplitudes[6].
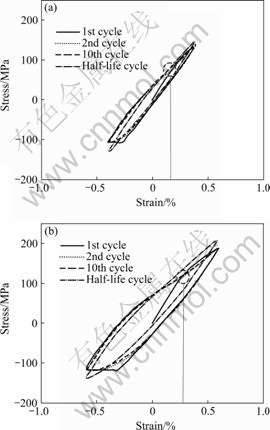
Fig.4 Hysteresis loops after various cycles at different total strain amplitudes: (a) 0.4%; (b) 0.6%
Because the strain generated by detwinning at 0.6% fatigue was greater than that at 0.4% fatigue, the inflection points as shown in the circles in Fig.4(a) and (b) indicate that the completion of detwinning in the case of 0.6% fatigue was located at a higher strain than that in the case of 0.4% fatigue. As shown in Fig.4(b), the hardening rate increases after the inflection point in the second cycle, but the total strain amplitude of 0.6% do not provide sufficient strain for cyclic hardening. Therefore, the tensile stress in the second cycle is lower than that in the first cycle. Since the volume fraction of twins increases during initial fatigue at 0.6% of strain, the cyclic stress response at 0.6% fatigue exhibits slight softening up to 10 cycles, as shown in Fig.3(a). However, as the rate of increase in the number of twins decreases during compression, the rate of increase in the amount of strain caused by detwinning during tension also decreases. At the same time, the dislocation density will continuously increase due to cyclic deformation. When the increase of the dislocation density is able to inhibit the initial softening, cyclic hardening starts.
3.4 Bi-linear behavior of Coffin-Manson law
Fig.5 shows the strain amplitudes at given numbers of fatigue cycles to failure.
The total strain amplitude (?εt) can be expressed as the sum of the elastic strain amplitude (?εe) and plastic strain amplitude (?εp):
(1)
The elastic strain amplitude can be replaced by the Basquin equation:
(2)
where
is the fatigue strength coefficient; b is the fatigue strength exponent and E is the elastic modulus.
Also, the plastic strain amplitude can be expressed in terms of the Coffin-Manson law:
(3)
where
is the fatigue ductility coefficient and c is the fatigue ductility exponent.
In the evaluated fatigue parameters based on the Basquin equation, the fatigue strength coefficient (
) of 640 MPa and the fatigue strength exponent (b) of -0.18 are similar to the values reported in other studies related to the fatigue of AZ31 Mg alloy[8-9]. However, in the case of the parameters evaluated based on the Coffin-Manson law, the fatigue ductility coefficient (
) of 76.8% and the fatigue ductility exponent (c) of -0.82 differ from the previously reported values that
=1.78%, and c=-0.40. This difference results from the higher strain amplitudes employed in this study. MATSUZUKI et al[5] showed that the Coffin-Manson curve exhibited

Fig.5 Relationship between strain amplitudes at half-life and number of reversals to failure for extruded AZ31magnesium alloy: (a) Plastic, elastic and total strain amplitude; (b) Plastic strain amplitude on tension and compression side
bi-linear behavior when the strain amplitude became higher. The general plastic strain amplitude is described as ?εp/2, in other words, the total plastic strain range divided by 2. However, as the tension and compression properties of this alloy are asymmetrical, the plastic strain amplitudes on the two sides are also asymmetrical. Therefore, the plastic strains on the tension and compression sides are separately displayed in Fig.5(b). As shown in this figure, the compression side is linear, but the tension side is scattered around the average fitting line. However, if the line is divided at 0.6% as a reference point, the tension side will show bi-linear behavior, which is also plotted in Fig.5(b). The reason for the bi-linear behavior of this alloy can be explained as follows. At strain amplitudes of less than 0.6%, the plastic strain on the tension side exhibits little difference, whereas the compression side shows a definite difference from the average value. As twinning is dominant during the initial compression of the magnesium alloy, it seems that the fatigue behavior in the strain range below 0.6% is dominated by twinning, whereas in the strain range above 0.6% it is dominated by the plastic deformation caused by dislocation.
3.5 Interaction between twinning effect and dislocation
Fig.6(a) shows the cyclic stress response curves in the low cycle fatigue tests that were started from either tension or compression under a total strain amplitude of 1.0%.
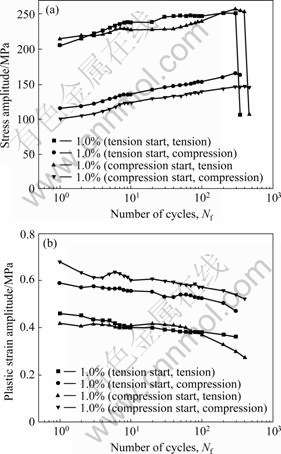
Fig.6 Low cycle fatigue tests started from either tension or compression under a total strain amplitude of 1.0%: (a) Cyclic stress response curve; (b) Cyclic plastic strain amplitude response curve
From Fig.6(a), it can be seen that the cyclic compressive stress response in the tension started (TS) test exhibits higher stresses at all number of fatigue cycles than that in the compression started (CS) test. The dislocation density in the CS test is thought to increase less than that in the TS test due to the large compression strain caused by twinning at the first compressive load. Therefore, the compressive stresses in the TS test at the point of every 3/4 cycle are higher than those in the CS test at the point of every 1/4 cycle. Fig.6(b) shows that the plastic compressive strain amplitudes in the CS test are higher than those in the TS test until fracture. As a result, it is considered that the increased dislocation density at the first cycle affects the remainder of the test, resulting in shorter fatigue life observed in the TS test.
3.6 Microstructure evolution
The microstructural evolution during low cycle fatigue at a total strain amplitude of 1.0% is shown in Fig.7. Fig.7(a) shows the microstructure before fatigue. A small amount of dislocations generated by extrusion are observed. As shown in Fig.7(b), the dislocation density increased after 100 cycles. Further, as shown in Fig.7(c), it increased more after fracture. As previously stated in section 3.2, the cyclic stress response to fatigue at 1.0% strain exhibited cyclic hardening until final fracture (Fig.3), which was caused by the increase of the dislocation density.
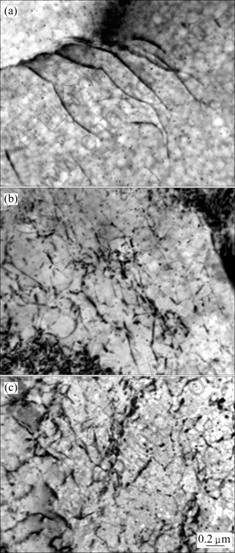
Fig.7 Variation of dislocation density during fatigue at ?ε/2=1.0%: (a) Before fatigue; (b) After 100 cycles; (c) After fracture
4 Conclusions
1) The low cycle fatigue behavior of AZ31 magnesium alloy exhibits asymmetric hysteresis loops due to the twinning/detwinning effect. The twins generated under compressive loading increases in number become easier to observe with increasing number of fatigue cycles.
2) The cyclic tensile stress responses show a large amount of cyclic hardening caused by the increase in the dislocation density at high strain amplitudes, but only a small amount of cyclic hardening at low strain amplitudes. The cyclic compressive stress responses show a small amount of continuous cyclic hardening until fracture.
3) The fatigue at 0.4% strain exhibits neither cyclic softening nor cyclic hardening. The fatigue at 0.6% strain shows initially a small amount of cyclic softening and then cyclic hardening. However, the fatigue at 0.8% strain shows only cyclic hardening until fracture.
4) When the plastic strain amplitudes at half-life cycle are divided into the tension and compression side in the Coffin-Manson plot, and the graph of the tension side shows bi-linear behavior, whereas that of the compression side shows only linear behavior.
5) The difference in the fatigue life at 1.0% strain in the tests that are started from either tension or compression is caused by the twinning effect and the variation of the dislocation density.
Acknowledgement
This study was supported by the Seoul Research and Business Development Program (10555) and the Fundamental R&D Program for Core Technology of Materials Funded by the Korean Ministry of Knowledge Economy Through Research Institute of Advance Materials.
References
[1] FRIEDRICH H, SCHUMANN S. Research for a “new age of magnesium” in the automotive industry [J]. J Mater Process Technol, 2001, 117(3): 276-281.
[2] TOKAJI K, KAMAKURA M, ISHIIZUMI Y, HASEGAWA N. Fatigue behavior and fracture mechanism of a rolled AZ31 magnesium alloy [J]. Int J Fatigue, 2004, 26(11): 1217-1224.
[3] MENDIS C L, OS-ISHI K, KAWAMURA Y, HONMA T, KAMADO S, HONO K. Precipitation-hardenable Mg-2.4Zn-0.1Ag-0.1Ca- 0.16Zr(at.%) wrought magnesium alloy [J]. Acta Mater, 2009, 57(3): 749-760.
[4] ISHIHARA S, NAN Z, GOSHIMA T. Effect of microstructure on fatigue behavior of AZ31 magnesium alloy [J]. Mater Sci Eng A, 2007, 468/470(15): 214-222.
[5] MATSUZUKI M, HORIBE S. Analysis of fatigue damage process in magnesium alloy AZ31 [J]. Mater Sci Eng A, 2008, 504(1): 167-174.
[6] LIN X Z, CHEN D L. Strain controlled cyclic deformation behavior of an extruded magnesium alloy [J]. Mater Sci Eng A, 2008, 496(1): 106-113.
[7] CHEN L, WANG C, WU W, LIU Z, GRIGORETA M, STOICA M, WU L, LIAW P K. Low-cycle fatigue behavior of an as-extruded AM50 magnesium alloy [J]. Metall Mater Trans A, 2007, 38(13): 2235-2241.
[8] BEGUM S, CHEN D L, XU S, LUO A A. Low cycle fatigue properties of an extruded AZ31 magnesium alloy [J]. Int J Fatigue, 2009, 31(4): 726-735.
[9] HASEGAWA S, TSUCHIDA Y, YANO H, MATSUI M. Evaluation of low cycle fatigue life in AZ31 magnesium alloy [J]. Int J Fatigue, 2007, 29(9): 1839-1845.
[10] PARK N J, HWANG J O, ROH J S. Influence of texture on the tensile properties in AZ31 magnesium alloy [J]. J Kor Inst Met & Mater, 2009, 47(1): 1-6.
[11] CHEN Y J, WANG Q D, ROVEN H J, KARLSEN M, YU Y D, LIU M P, HJELEN J. Microstructure evolution in magnesium alloy AZ31 during cyclic extrusion compression [J]. J Alloy Compd, 2008, 462(1): 192-200.
[12] YANG F, YIN S M, LI S X, ZHANG Z F. Crack initiation mechanism of extruded AZ31 magnesium alloy in the very high cycle fatigue regime [J]. Mater Sci Eng A, 2008, 491(1): 131-136.
[13] KLEINER S, UGGOWITZER P J. Mechanical anisotropy of extruded Mg-6%Al-1%Zn alloy [J]. Meter Sci Eng A, 2004, 379(1): 258-263.
[14] GHARGHOURI M A, WEATHERLY G C, EMBURY J D, ROOT J. Study of the mechanical properties of Mg-7.7at.%Al by in-situ neutron diffraction [J]. Philos Mag A, 1999, 79(7): 1671-1695.
[15] CHINO Y, KIMURA K, MABUCHI M. Twinning behavior and deformation mechanisms of extruded AZ31 Mg alloy [J]. Meter Sci Eng A, 2008, 486(1): 481-488.
[16] WU L, JAIN A, BROWN D W, STOICA G M, AGNEW S R, CLAUSEN B, FIELDEN D E, LIAW P K. Twinning-detwinning behavior during the strain-controlled low-cycle fatigue testing of a wrought magnesium alloy, ZK60A [J]. Acta Mater, 2008, 56(4): 688-695.
[17] WU L, AGNEW S R, BROWN D W, STOICA G M, CLAUSEN B, JAIN A, FIELDEN D E, LIAW P K. Internal stress relaxation and load redistribution during the twinning-detwinning-dominated cyclic deformation of a wrought magnesium alloy, ZK60A [J]. Acta Mater, 56(14): 3699-3707.
[18] YIN S M, YANG H J, LI S X, WU S D, YANG F. Cyclic deformation behavior of as-extruded Mg-3%Al- 1%Zn [J]. Scr Mater, 2008, 58(9): 751-754.
[19] CACERES C H, SUMITOMO T, VEIDT M. Pseudoelastic behaviour of cast magnesium AZ91 alloy under cyclic loading-unloading [J]. Acta Mater, 2003, 51(20): 6211-6218.
[20] AGNEW S R, BROWN D W, TOME C N. Validation a polycrystal model for the elastoplastic response of magnesium alloy AZ31 using in situ neutron diffraction [J]. Acta Mater, 2006, 54(18): 4841-4852.
[21] YOO M H, AGNEW S R, MORRIS J R, HO K M. Non-basal slip systems in HCP metals and alloys: source mechanisms[J]. Mater Sci Eng A, 2001, 319: 87-92.
[22] JAIN A, DUYGULU O, BROWN D W, TOME C N, AGNEW S R. Grain size effects on the tensile properties and deformation mechanisms of a magnesium alloy, AZ31B, sheet [J]. Mater Sci Eng A, 2008, 486(1): 545-555.
(Edited by LIU Hua-sen)
Corresponding author: S. I. KWUN; Tel: +82-2-3290-3268; E-mail: sookkwun@korea.ac.kr