文章编号:1004-0609(2008)08-1466-06
考虑预热情况的液固挤压复合材料模具非稳态温度场分析及实验验证
齐乐华,周计明,王玉山,苏力争
(西北工业大学 机电学院,西安 710072)
摘 要:基于辐射传热原理,建立液固挤压复合材料过程模具传热的非稳态有限元模型,采用有限元分析与实验研究相结合的方法研究模具初始温度场和液固挤压过程模具温度场的传热特性,得到了模具温度场的变化趋势及其对成形过程的影响规律,并对比研究了考虑模具预热和初始模具温度场恒定的数值模拟情况。结果表明,考虑预热情况的模拟结果更加接近实际,且模拟结果与实验结果吻合较好。
关键词:液固挤压;有限元法;模具温度场
中图分类号:TG 37; TB 331 文献标识码:A
Nonlinear heat transfer analysis of die during liquid-solid extruding composites considering preheating and its experimental verification
QI Le-hua, ZHOU Ji-ming, WANG Yu-shan, SU Li-zheng
(School of Mechatronics, Northwestern Polytechnical University, Xi’an 710072)
Abstract: The model of non-linear temperature field of the die for liquid-solid extruding composites process is established, which considers the preheating, the heat radiation and the contacting heat transfer between the die and other media. By combining the numerical analysis with experimental testing, the radiation heating and extruding process are simulated using the commercial finite element code MARC. On the basis of researching the heat transfer characteristics, the initial distribution of temperature field of the die and the effect on the shaping process are obtained. Through comparing the simulation results considering the preheating with the stationary temperature field, it concludes that the former approaches to actual forming process. The simulation results are in good agreement with experimental measurements. The research of this paper found the base for designing the technology parameters properly of liquid-solid extrusion composites process.
Key words: liquid-solid extrusion; finite element analysis; temperature field of die
液固挤压复合材料工艺[1]是近年来开发的一种复合材料近净成形新工艺,在民用、建筑、国防等领域具有广阔的应用前景[2] 。其实质是利用金属液-固态期间变形抗力低、容易流动的特点对其进行大塑性变形,使之由液态金属一次复合、成形出复合材料管、棒、型材类制件[3] 。由于在成形过程中,材料的塑性变形与结晶凝固同时进行,需要保证液固挤压速度与凝固速度匹配协调[4],使工艺过程参数的控制比较困难。而挤压过程的模具温度场,尤其是模具的初始温度场,是影响液态金属凝固速度的关键因素之一,对于保证复合材料成形过程顺利进行和制件成形质量有着不容忽视的作用。目前,对于液固挤压复合材料工艺成形过程温度场的研究已有报道[5?6],而有关模具温度场的研究还较少。在已有的研究中,利用有限元法模拟成形过程温度场和传热特性时,通常是将模具的初始温度简化为一个定值[7?8],但由于模具在加热过程中的边界条件和接触条件各异,其内部温度并非处处相等,会与实际情况有所差异,从而影响模拟精度。本文基于辐射传热原理建立了考虑模具预热情况的有限元分析模型,结合试验研究,利用MARC软件对液固挤压复合材料工艺过程的模具温度场(含预热情况)进行了有限元分析,得到了更为切合实际情况的模拟结果,为合理拟定液固挤压复合材料工艺参数提供了理论依据。
1 模具温度场的有限元建模
1.1 瞬态热传导问题的数学描述
根据热力学第一定律,系统从外界吸收热量的方式包括辐射,对流及热传导,每一种热交换方式分别遵从不同的定律。对于热传导而言,遵循傅立叶定 律[9],即:
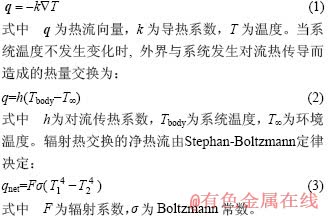
公式~分别是系统与外界进行热交换时热流的数学表达式。对于系统与外界只发生热传导的情况而言,其能量守恒方程即为热扩散方程:

对于系统与外界只发生对流传热的情况而言,根据能量守恒定律,可以得出:

当材料处于不同状态时,其传热方式也有所不同。对于固体而言,粒子之间主要通过彼此间的接触碰撞传递能量,因而以热传导为主;对于液体和气体而言,由于流动和不定形的特点,在热传导的同时还伴有对流传热的特点,在式中加入对流传热项,可以导出热传导、对流、扩散过程的控制方程[10]:
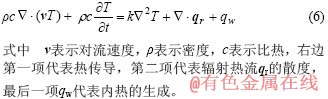
采用变分法将式(6)的求解问题转化为求泛函极值问题,并在泛函中引入具体的边界条件。经过离散化处理后,可以得到如下的矩阵方程[11]:
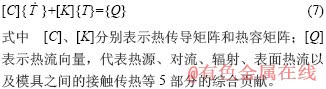
1.2 有限元模型的建立
液固挤压过程中模具温度场的有限元分析,既涉及电炉对模具的辐射传热,又涉及液态金属与模具之间的接触热传导,以及模具与环境之间通过辐射与对流的向外散热,所以模具温度场分析是一个很复杂的过程,建立准确的有限元模型对于得到可靠的分析结果至关重要。
1.2.1 模具预热有限元模型
模具预热主要靠热电阻对模具的辐射传热。由于液固挤压复合材料模具传热为轴对称问题,为计算方便,可以取其1/2纵剖面进行求解。依据实际情况,将热电阻划分为90个热传导四边形单元,初始温度为1 000 ℃;挤压模具划分为819个热传导四边形单元,初始温度和环境温度设为室温25 ℃,如图1所示。模具与热电阻的距离为8 cm,模具的上表面施加绝热边界,下表面与底座之间定义为接触传热。模具材料3Cr2W8V的热物性参数如表1所示。利用MARC软件中的自适应加载方法进行瞬态热传导分析,当节点的前后温差小于1 ℃时,停止计算;将前述分析结果文件作为初始条件加载即可进行后续相关问题的分析。
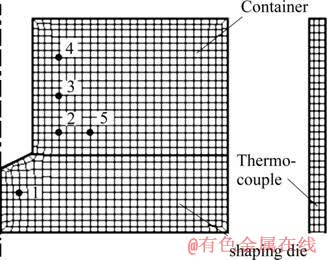
图1 模具预热有限元模型
Fig.1 FEM model for die preheated (Points 1?5 are thermocouple stations)
表1 模具材料3Cr2W8V的热物性参数
Table 1 Thermal-physical properties of 3Cr2W8V
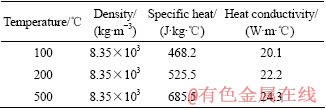
1.2.2 液固挤压过程有限元模型
液固挤压复合材料过程一般可以分为模具预热、金属浇注、浸渗保压和液固挤压4个阶段,其中后3个阶段主要是坯料和模具之间的接触传热,以及坯料在凸模作用下产生的塑性变形和坯料与模具之间的摩擦所产生的热。为了能更为准确的反映实际成形状况,本研究将上述过程分为相应的3个工况进行模拟。第一个工况模拟液态金属的浇注情况:液态金属与模具的接触时间设为1 s,冲头施加一很小的位移,以保证液态金属与模具充分接触;第二个工况模拟浸渗保压情况:持续时间设为29 s,使坯料与模具进行充分的热传导;第三个工况模拟加载成形过程:冲头施压并以一定的速度下行,为了保证此阶段模拟结果的收敛性,采用自适应步长加载。
模拟材料为液固挤压短纤维增强铝基复合材料Al2O3sf/LY12,其热物性参数如表2所示。材料的变形行为采用刚粘塑性双曲正弦本构模型[11]进行描述:
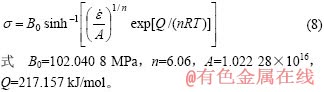
表2 Al2O3sf/ LY12的热物性参数
Table 2 Thermal-physical properties of Al2O3sf/ LY12
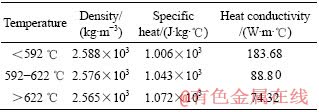
将挤压坯料划分为570个单元,均为热力耦合全积分四边形单元,如图2所示。数值模拟时将模具视为刚性传热体,同时考虑模具与底座之间的传热,以及模具和坯料与外界环境的对流换热。利用MARC的网格重划功能对坯料的变形过程不断进行网格重新划分,每两个增量步重划一次,以保证模拟的准确性。坯料与模具之间的摩擦力采用剪切摩擦模型[12],即
(9)
式中 摩擦因数取0.3,摩擦与塑性变形功的热转化系数取0.9。
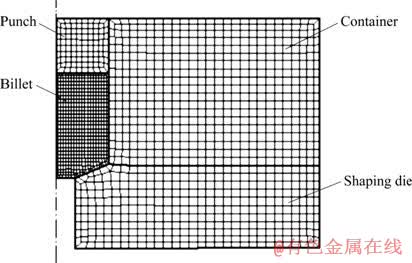
图2 液固挤压过程有限元模型
Fig.2 FEM model for calculating temperature fields of liquid-solid extrusion process
为了便于比较分析,研究了两种初始温度场对液固挤压复合材料工艺的影响:一是不均匀模具温度场的情况(模拟Ⅰ),即模具预热达到稳态时的初始温度场;二是均匀模具温度场(模拟Ⅱ),即将模具的初始温度场视为定值,其工艺参数取值示于表3。
表3 两种模拟条件下的工艺参数取值
Table 3 Processing parameters for two simulated conditions
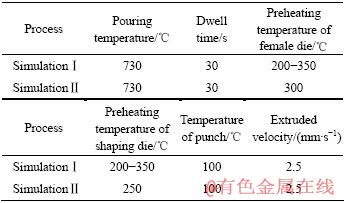
2 模拟结果分析与实验验证
为了将模拟结果与试验结果进行对比分析,本文采用自行开发的计算机数据采集系统对液固挤压复合材料模具内不同位置的温度进行数据采集,热电偶在模具中的位置示于图1,其中热电偶1位于成形模中,热电偶2、3、4沿挤压筒纵向同直径不同高度布置,热电偶2、5位于挤压筒同一高度不同径向处。
图3所示为不同热电偶在模具加热过程中的温度变化曲线。可以看出,模具各点的温度随加热时间延长而不断趋于稳定,当模具加热至2 000 s时,其温度变化在1 ℃以内,可以认为此时的模具温度已达到稳态。因此,在实验过程中,在保证模具温度场稳定的同时应尽量缩短加热时间以减少能耗。
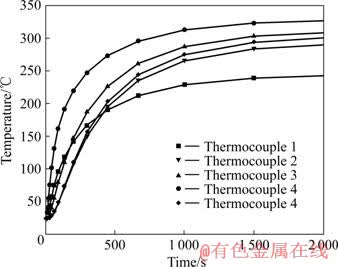
图3 模具加热过程中热电偶测量点的温度变化
Fig.3 Variations of temperature of thermocouple stations during preheating die
图4所示为两种不同模具初始温度场(模拟Ⅰ与模拟Ⅱ)的热电偶测量点的模拟值与实验值的对比。从图4可以看出,模拟Ⅰ的分析结果更加接近实验值, 而模拟Ⅱ与实验值有一定的偏差。图4也表明,传热达到稳态后,模具内各点的温度并非均匀分布,靠外层的5号热电偶由于接近加热器, 所以温度比靠内层的2号热电偶高, 而靠近模具底部的1号热电偶由于与底座的热传导较快, 且模具上部有绝缘层保温,故其温度相对于上部的其他热电偶要低一些。
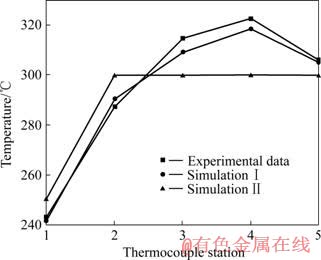
图4 热电偶测量点温度的模拟值与实验值对比
Fig.4 Comparisons between results of numerical simulation and experiment of thermocouple stations
图5所示为浸渗保压30 s时,模拟Ⅰ与模拟Ⅱ中不同测量点的模拟结果与实验结果的对比。可见,模拟Ⅰ更加接近实验结果。由于模拟Ⅱ将模具初始温度场视为定值,与实验结果差别较大,5号测量点的模拟值与试验值的误差超过5%。由图4可知,模拟Ⅱ的5号测量点的初始温度即比实际温度低,且由于视整个模具的初始温度为均匀分布,忽略了外层温度高于内层温度这一事实,故由内层向外层传热的速度也较快,导致最终的温度值偏低。
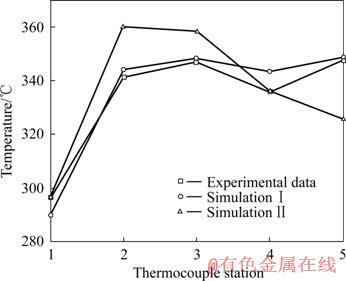
图5 模拟Ⅰ、模拟Ⅱ与实验值的对比
Fig.5 Comparisons between results of simulation Ⅰ, Ⅱ and experimental value
图6所示为模拟Ⅰ和模拟Ⅱ中,测量点1和2在浸渗保压及挤压过程中的温度变化曲线。由图可见,仍然是模拟Ⅰ的结果与实验结果比较接近,特别是在液固挤压后期阶段,模拟Ⅱ与实验值偏差较大。
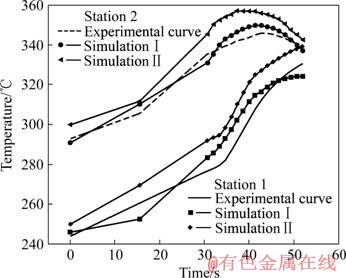
图6 热电偶测量点1、2的模拟值与实验值对比
Fig.6 Comparisons between results of simulation and experiment of thermocouple stations 1 and 2
图7和8所示分别为模拟Ⅰ、模拟Ⅱ中, 成形模沿径向不同时刻的温度变化曲线,横坐标为模拟点与模具内壁之间的距离。由图可见,靠近内壁处,特别是与坯料接触的内壁,温度波动大,而距内壁60 mm处,温度变化较小,由于模具与外界的传热,外层温度有所下降。同时,两种模拟结果在外层的温度分布存在明显差异,这主要是因为模拟Ⅱ假设成形模温度均匀分布,故无法反映外层温度高于内层温度这一事实。同时,由于模拟Ⅰ靠近内壁的初始温度比模拟Ⅱ的假设温度要低,故在10 s左右时模拟Ⅰ中靠近内壁的温度比模拟Ⅱ中同一位置要低一些。
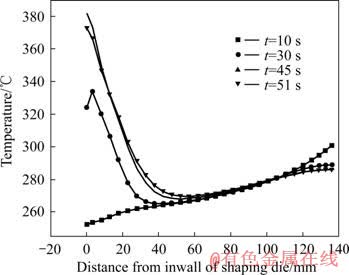
图7 模拟Ⅰ中不同时刻成形模径向温度分布
Fig.7 Distributions of radial temperature of shaping die at different times in simulationⅠ
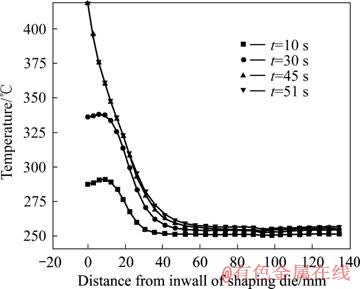
图8 模拟Ⅱ中不同时刻成形模径向温度分布
Fig.8 Distributions of radial temperature of shaping die at different times in simulation Ⅱ
图9和10显示了浸渗保压为30 s和液固挤压为5 s时的坯料与模具温度场的分布云图,其中暗灰色代表液态金属。可以看出,温度变化主要集中在模具内部,越靠近外层,温度变化越小。实验结果[4]也表明,在此模拟工艺参数下成形复合材料时可以得到良好 制件。
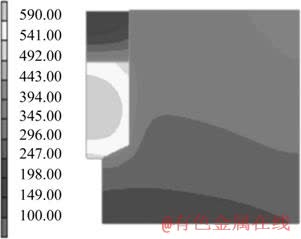
图9 浸渗保压30 s时坏料与模具温度场的分布云图
Fig.9 Temperature field of billet and die during pressure maintaining process (t = 30 s)
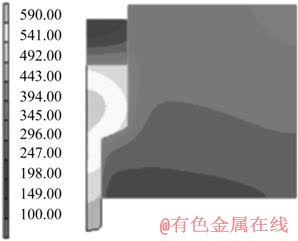
图10 液固挤压5 s时坯料与模具温度场的分布云图
Fig.10 Temperature field of billet and die during liquid- solid extrusion process (t = 5 s)
3 结论
1) 基于辐射传热原理建立了液固挤压复合材料过程模具传热的非稳态有限元模型,得到了模具加热过程的温度变化规律。当模具加热时间达2 000 s时即可进入稳态过程。通过与实验数据的对比,验证了所建模型的准确性。
2) 研究了两种初始温度场对液固挤压复合材料工艺过程的影响,其中基于非均匀初始温度场模拟的浸渗挤压过程可以得到更为接近实际情况的模拟结果。实验及模拟结果表明,当浸渗保压时间为30 s时可以成形良好制件,为液固挤压复合材料工艺参数的设计奠定了基础。
REFERENCES
[1] HU Lian-xi, LUO Shou-jing, HUO Wen-can WANG Zhong-ren. Microstructure and properties of AlO/Al-1.5Mg composite manufactured by extrusion directly following liquid infiltration[J]. Trans Nonferrous Met Soc China, 1995, 5(4): 146?150.
[2] 罗守靖, 田文彤, 谢水生, 毛卫民. 半固态加工技术及应用[J]. 中国有色金属学报, 2000, 10(6): 765?773.
LUO Shou-jing, TIAN Wen-tong, XIE Shui-sheng, MAO Wei-min. Technology and applications of semi-solid forming[J]. The Chinese Journal of Nonferrous Metals, 2000, 10(6): 765?773.
[3] HU L X, LUO S J, HOU W C, WANG Z R. Development of the technique of extrusion directly following infiltration for the manufacturing of metal-matrix composites[J]. Journal of Materials Processing Technology, 1995, 49(3/4): 287?294.
[4] QI L H, LI H J, CUI P L, SHI Z K. Forming of tubes and bars of alumina/LY12 composites by liquid extrusion process[J]. Transactions of nonferrous metals society of China, 2003, 13(4): 803?808.
[5] QI L H, SHI Z K, LI H J, CUI P L, HAN H M. Simulation of liquid infiltration and semi-solid extrusion for composite tubes by quasi-coupling thermal-mechanical finite element method[J]. Journal of Materials Science, 2003, 38: 3669?3675.
[6] 胡连喜, 罗守靖, 霍文灿. 液态浸渗后直接挤压过程模具与坯料内部温度变化的研究[J]. 热加工工艺, 1995, (2): 3?5.
HU Lian-xi, LUO Shou-jing, HUO Wen-can. Study on the variation of temperature inside the die and the extruded-billet during extrusion directly following liquid infiltration[J]. Thermal processing and technology, 1995, (2): 3?5.
[7] MAGNABOSCO I, FERRO P, TIZIANI A, BONOLLO F. Induction heat treatment of a ISO C45 steel bar: Experimental and numerical analysis[J]. Computational Materials Science, 2006, 35(2): 98?106.
[8] LIN Chia-chin, CHANG Yu-choung, LIANG Kun-yi, HUNG Ching-hua. Temperature and thermal deformation analysis on scrolls of scroll compressor[J]. Applied Thermal Engineering, 2005, 25(11/12): 1724?1739.
[9] SHIOMI M, TAKANO D, OSAKADA K, OTSU M. Forming of aluminium alloy at temperatures just below melting point[J]. International Journal of Machine Tools & Manufacture, 2003, 43: 229?235.
[10] ROUSSE D R. Numerical predictions of two-dimensional conduction, convection, and radiation heat transfer. I. Formulation[J]. International Journal of Thermal Sciences, 2000, 39(3): 315?31.
[11] LEWIS R W, RANSING R S. A correlation to describe interfacial heat transfer during solidification simulation and its use in the optimal feeding design of castings[J]. Metallurgical and Materials Transactions B, 1998, 29B: 437?448.
[12] LOF J. Elasto-viscoplastic FEM simulations of the aluminium flow in the bearing area for extrusion of thin-walled sections[J]. Journal of Materials Processing Technology, 2001, 114: 174?183.
基金项目:国家自然基金资助项目(50575185);航空科学基金资助项目(05G53048);陕西省自然基金资助项目(2005E23)
收稿日期:2007-11-23;修订日期:2008-02-03
通讯作者:齐乐华,教授,博士,电话:029-88460447;E-mail: qilehua@nwpu.edu.cn
(编辑 何学锋)