文章编号: 1004-0609(2005)12-1974-06
沉淀前驱物制备AlN陶瓷粉末
秦明礼1, 杜学丽1, 2, 李 帅1, 孙 伟1, 曲选辉1, 3
(1. 北京科技大学 材料科学与工程学院, 北京 100083; 2. 天津理工大学 材料科学与工程学院, 天津 300191;
3. 中南大学 粉末冶金国家重点实验室, 长沙 410083)
摘 要: 以硝酸铝和碳黑为原料, 利用化学沉淀法制备出混合均匀的Al2O3+C前驱物, 并以该前驱物为原料采用碳热还原法制备了AlN粉末。 研究了氮化反应温度、 pH值、 表面活性剂、 溶液浓度、 氮气流量和碳铝比等工艺参数对氮化反应的影响, 得出的最佳工艺参数分别为: 以0.4mol/L的硝酸铝溶液和比表面积为156m2/g的碳黑为原料, 控制原料中碳铝比为3∶1, 添加适量的硬脂酸(SA)和聚乙二醇(PEG)作为表面活性剂, 控制沉淀过程中pH=9, 通过共沉淀工艺得到分散性好、 团聚程度小的前驱物, 并将此前驱物在常压和氮气流量为5L/min的条件下于1550℃煅烧4h, 最后将反应产物在650℃的空气中除碳4h, 制备出氮含量为33.20%, 氧含量为0.98%, 比表面积为4.26m2/g的AlN粉末。
关键词: AlN粉末; 沉淀前驱物; 碳热还原 中图分类号: TB484.5
文献标识码: A
Preparation of AlN powders from precipitated precursor
QIN Ming-li1, DU Xue-li1, 2, LI Shuai1, SUN Wei1, QU Xuan-hui1, 3
(1. School of Materials Science and Engineering,
University of Science and Technology Beijing, Beijing 100083, China;
2. School of Materials Science and Engineering,Tianjin University of Technology, Tianjin 300191, China;
3. State Key Laboratory of Powder Metallurgy,Central South University, Changsha 410083, China)
Abstract: A homogenous mixture precursor of Al2O3+C was prepared by the chemical precipitation method and AlN powders were fabricated by carbon thermal reduction nitridation of the precipitated precursor. The effect factors on the nitridation conditions and the properties of AlN powders, including nitridation temperature, pH value, surface active agent, solution concentration, N2 flow rate and molar ratio of carbon to aluminum, were investigated. An optimal process was obtained through synthesizing fine and pure AlN powders. Firstly, a homogenous and good dispersion precursor was prepared by the precipitation process using 0.4mol/L Al(NO3)3 solution and 156m2/g carbon black as materials at pH=9, the molar ratio of carbon to aluminum was controlled to 3∶1 and a certain amount of stearic acid and ethylene glycol was added as surface active agents. Then, the precursor was heated at 1550℃ for 4h under common pressure at N2 flow rate of 5L/min. Finally, AlN powders with nitrogen content of 33.20%, oxygen content of 0.98%, specific surface area of 4.26m2/g were produced after decarbonization of the nitridation products in air for 4h at 650℃.
Key words: AlN powders; precipitated precursor; carbothermal reduction
氮化铝(AlN)具有热导率高 (理论热导率为320W·m·K, 实际值可达260W·m·K, 为氧化铝陶瓷的10~15倍)、 介电常数低(约为8.8)、 电绝缘性可靠(电阻率>1016 Ω·m)、 耐高温、 耐腐蚀、 无毒、 良好的力学性能以及与硅相匹配的热膨胀系数(20~500℃, 4.6×10-6 K-1)等一系列优良性能, 是继氧化铝和氧化铍后新一代高密度集成电路和高功率电子器件的理想基片和封装材料, 且在电子工业中的应用日益受到重视[1-3]。 AlN粉末的制备方法有多种, 其中碳热还原法合成的粉末在纯度、 粒度以及稳定性等方面占较大优势。 但是, 该方法也存在不足之处, 具体表现在原料难于混合均匀, 对Al2O3和碳黑的性能要求较高, 反应温度高, 合成时间长, 因此成本高。 为了改善氮化条件和提高粉末性能, 人们进行了大量的研究工作, 许多研究表明[3-5], 原料的种类、 粒度以及混合的均匀程度对碳热还原法的反应温度和粉末性能有重要影响, 选择不同种类的原料和不同的混料工艺, 氮化温度可以相差200℃左右。 因此, 选择合适的原料以及如何制备粒度细小、 分散均匀的反应前驱物已成为碳热还原法合成氮化铝陶瓷粉末的关键技术之一。
通过化学方法制备 Al2O3+C 混合前驱物可以改善氧化铝粉末与碳粉难以混合的缺点, 提高了铝源和碳源混合的均匀性, 同时减小了原料的粒度, 使两种亚微粒子直接接触反应, 从而提高了反应活性, 降低了反应温度[6]。 湿化学法合成粉体是在液相中生成颗粒, 通过控制适当的工艺条件, 可以生产高纯、 超细、 团聚程度小、 成分精确而均匀的粉料[7, 8]。 由于具有上述特点, 湿化学法已被广泛用于制备各种陶瓷粉末, 其中沉淀法由于工艺简单, 适合规模化生产, 且在工业生产中得到广泛应用[9-11]。 与传统以氧化铝和碳黑为原料合成氮化铝粉末的工艺相比较, 采用沉淀法制备的Al2O3+C混合前驱物, 不仅有利于铝源和碳源的充分分散混合, 而且省去了由氢氧化铝到氧化铝的煅烧工艺, 缩短了工艺, 降低了成本。
1 实验
实验原料主要有: 分析纯硝酸铝(Al(NO3)3·9H2O); 高纯工业炭黑(槽黑), 灰分小于0.05%, 比表面积为156m2/g; 氨水, 尿素(CO(NH2)2), 聚乙二醇(PEG), 硬脂酸(SA)。
首先配制出适当浓度的硝酸铝溶液, 按一定的配比加入适量的尿素, 在80~90℃时搅拌水解, 并加入少量PEG作为表面活性剂, 起到分散作用。 将碳黑加入氨水溶液中, 制备出稳定的悬浮液, 并将硝酸铝水解后的溶液滴加到悬浮有碳黑的氨水溶液中。 沉淀反应结束后, 将所得胶状沉淀物经过滤、 洗涤、 干燥、 粉碎、 过筛处理后得到前驱物。
前驱物的氮化反应在立式碳管炉中进行。 将脱水处理后前驱物置于石墨坩埚中装炉, 先将炉内抽真空, 用氮气洗炉后, 维持炉内流动氮气气氛, 将前驱物在流动氮气中加热至1250~1650℃进行反应, 反应产物在600~700℃的空气中进行脱碳处理后得到AlN粉末。
不同温度下氮化产物的物相分析在日本产3014-Z2型X射线衍射仪上进行(XRD), Cu Kα辐射。 利用JSM-5600LU 型扫描电镜观察颗粒的粒度和形貌(SEM)。 利用ST-03型比表面积测定仪测定前驱物及反应产物的比表面积(BET)。 采用碱溶法测定粉末氮含量, SP-2304气相色谱仪测定氧含量。 根据氧、 氮含量计算铝含量。 利用原子激发光谱法测定杂质元素含量(ICP)。
2 结果与讨论
2.1 前驱物氮化反应过程中的相变
图1所示为以沉淀法制备的前驱物为原料时,
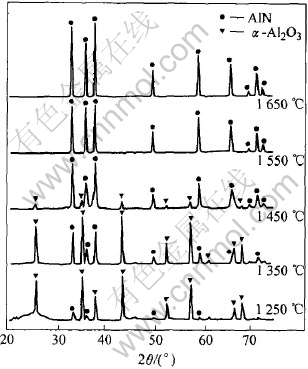
图1 沉淀前驱物体系氮化反应过程的X射线射谱
Fig.1 XRD patterns of precipitated precursor during nitridation process
不同温度下反应3h后反应产物的X射线衍射谱。 由图1可以看出, 在1250℃时, 主晶相为α-Al2O3, 但结晶不完善, 此外还可以观察到氮化铝衍射峰, 利用衍射峰的相对强度计算氮化铝的相对含量约为17%; 在1350℃时, 氮化铝衍射峰加强, α-Al2O3逐渐结晶完善; 当温度为1350~1450℃时, 氮化铝衍射峰迅速增强, 氧化铝衍射峰的强度逐渐减弱, 氧化铝衍射峰在1550℃完全消失而转化为氮化铝。 直接采用α-Al2O3和碳黑为原料时, 需要高于1600℃的反应温度, 反应时间往往大于5h, 采用沉淀前驱物为原料制备氮化铝粉末时, 明显降低了反应温度, 加快了反应速率。
2.2 pH值的影响
由于Al(OH)3为两性化合物, 既可以溶于酸, 又可以溶于碱, 因此, 既要保持铝盐完全沉淀, 又要防止生成的沉淀重新溶解, 从而造成铝源的损失, 控制沉淀过程中溶液的pH值是一个关键因素。 将硝酸铝和碳黑按照C与Al摩尔比为3∶1进行配料。 表1所列为沉淀过程pH值对前驱物粉末中C/Al的影响。 由表1可见, 随着pH值的增加, 所得前驱物的C/Al逐渐增加, 表明铝源由于溶解而损失的量增加。
表1 pH值对沉淀前驱物中C/Al的影响
Table 1 Effects of pH value on C/Al of precipitated precursor
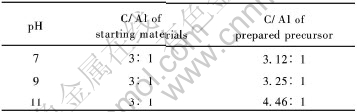
表2所列为不同pH值时合成的氮化铝粉末的比表面积和氮、 氧含量。 由表2可以看出, 当pH为9时, 沉淀前驱物中合成的氮化铝粉末比表面积最大, 为4.26m2/g; 而当pH为7和11时, 合成的氮化铝粉末的比表面积较小。 在沉淀过程中, pH值可以影响颗粒表面的电荷分布状况, 并进一步影响胶粒的生长加速和颗粒团聚程度。 不同pH值主要影响沉淀前驱物中Al(OH)3粒子的尺寸, 并进一步影响氮化铝粉末的粒度。
虽然pH值对合成氮化铝粉末的粒度有影响, 但对粉末氮, 氧含量影响不大, 经1550℃反应4h后, 粉末的氮含量超过了33%, 而氧含量在1%左右, 这说明沉淀前驱物中铝源的粒度不是影响氮化反应的关键因素, 而前驱物铝源存在的状态才是影响氮化反应速率的关键因素。
表2 pH值与AlN粉末性能的关系
Table 2 Relationship between pH value and properties of AlN powders
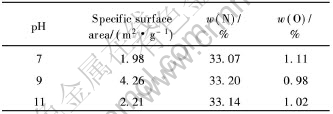
2.3 表面活性剂的作用
在湿法化学中, 表面活性剂是防止粉末团聚的一个重要措施。 在反应体系中加入适量表面活性剂后, 一方面表面活性剂能吸附于粒子表面, 使粒子间的势垒急剧增加, 减小粒子的表面张力; 另一方面, 表面活性剂分子吸附在已形成的前驱体颗粒上后, 可以减弱表面—OH的键合作用, 将颗粒间的非架桥羟基与吸附水屏蔽隔离, 有效地防止了在预烧过程中由于脱水产生的毛细管力造成的硬团聚。 因此, 在溶液中引入表面活性剂后, 可以在胶粒表面形成保护层而产生空间位阻效应, 从而提高颗粒的分散性能, 增加胶体的稳定性, 使胶粒均匀细小, 阻止胶粒的团聚。 另外, 由于碳黑为疏水性物质, 而Al(OH)3胶粒为亲水性物质, 碳粒和Al(OH)3胶粒极性不同, 二者很难结合紧密, 需要借助于表面活性剂的作用可以实现胶粒和碳粒的紧密结合。 表面活性剂的亲水性基团吸附在Al(OH)3胶粒表面, 而疏水基团吸附在碳粒表面, 碳粒借助于表面活性剂的作用, 紧紧包裹在Al(OH)3胶粒周围, 从而实现了铝源与碳源紧密结合与均匀分散的目的。 图2所示分别为不添加表面活性剂与加入适量的表面活性剂后合成的AlN粉末的SEM像。 由图2可以看出, 没有添加表面活性剂合成的氮化铝粉末硬团聚现象明显, 颗粒大小不均匀; 而添加表面活性剂合成的氮化铝粉末颗粒细小均匀, 分散性良好, 其主要原因是由于表面活性剂的作用, 提高了颗粒的分散性能, 实现了前驱物中铝源和碳源的均匀细分散, 从而制备出粒度均匀和分散良好的氮化铝粉末所致。
2.4 溶液浓度的影响
表3所列为Al(NO3)3溶液浓度分别为0.1、 0.4、 0.8和1.2mol/L时合成的前驱物氮化反应后生成的氮化铝粉末的性质。

图2 AlN粉末的SEM像
Fig.2 SEM images of AlN powders synthesized
without (a) and with (b) surface active agent
表3 Al(NO3)3溶液浓度与AlN粉末性能的关系
Table 3 Relationship between concentration of Al(NO3)3 solution and properties of AlN powders
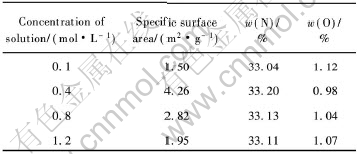
由表3可以看出, 虽然不同浓度的盐溶液合成的氮化铝粉末的氮和氧的含量相差不大, 但当Al(NO3)3溶液浓度为0.4mol/L时, 合成的氮化铝粉末的比表面积最大, 而盐溶液浓度过高或过低时, 合成的氮化铝粉末的比表面积都减小。
在溶液中沉淀出来的Al(OH)3粒子的大小主要取决于形核速度和成长速度, 这两种速度又与溶液中沉淀物质的过饱和度密切相关。 虽然一般认为增大金属盐的浓度可以使溶液的过饱和度升高, 使形成的Al(OH)3晶核数目迅速增加, 在其未充分长大前, 过饱和已消失, 有利于获得细颗粒粉末, 但是当浓度提高到一定程度后, 由于形核迅速, 数量多, 颗粒细小, 颗粒容易通过布朗运动相互碰撞而发生聚结, 使小颗粒不断向大颗粒沉聚, 通过表面反应、 表面扩散或体积扩散而溶合到大粒子中, 形成一个更大的整体粒子, 或发生局部溶合而形成一个更大的团聚粒子。 因此, 盐溶液浓度对形成颗粒粒度的影响具有两面性, 溶液浓度过高和过低都不利于制备细粒度的粉末。 本研究结果表明, 当盐溶液浓度为0.4mol/L时, 合成的氮化铝粉末的比表面积最大。
2.5 氮气流量的影响
图3所示为沉淀前驱物在不同氮气流量的体系中反应4h后, 反应产物中氮含量与氮气流量的关系。 由图3可以看出, 当氮气流量为1~5L/min时, 随着氮气流量的增加, 产物中氮含量逐渐增加; 当氮气流量大于5L/min后, 氮气流量对氮含量影响不大。 这是由于在反应体系中, 增加氮气的分压将会降低一氧化碳的分压, 有利于反应向右进行, 而当氮气流量增加到一定程度后, 一氧化碳浓度足够低, 氮气流量对反应影响不大。 当氮气流量大于10L/min后, 在合成的氮化铝粉末中可以观察到氮化铝纤维存在, 其长度可达200μm。 这与Forslund的研究结果相似[12], 说明在氮化反应过程中存在气相反应, 当氮气流速过大时, 沿氮气流动方向生长出晶须(见图4)。
2.6 碳量的影响
表4所列为其它条件相同, 不同碳铝比的前驱物所得AlN粉末的氧和氮含量。 由表4可以看出, 当C与Al摩尔比为理论值(即1.5∶1时), 由于碳量不够, 氮化反应不完全, 反应产物氮含量很低[CM(22](为25.6%), 氧含量很高(为8.23%); 而当C与[CM)] Al摩尔比为3∶1和6∶1时, 碳已经过量, 能够保证氮化反应完全进行, 合成的AlN粉末的氮含量都可达33%左右, 接近理论值, 表明氮化反应进行较为完全。 当前驱物中C与Al摩尔比大于3∶1时, 虽然对整个氮化反应程度影响不大, 但后续二次除碳工艺的时间明显增长。 因此可以认为, 当C与Al摩尔比为3∶1时, 反应已经完全, 为较佳碳用量, 再继续增加碳量会延长二次除碳时间和增加成本。
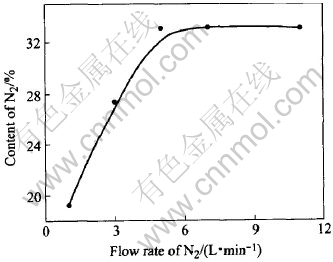
图3 氮气流量与氮含量的关系
Fig.3 Relationship between flow rate and content of nitrogen in products
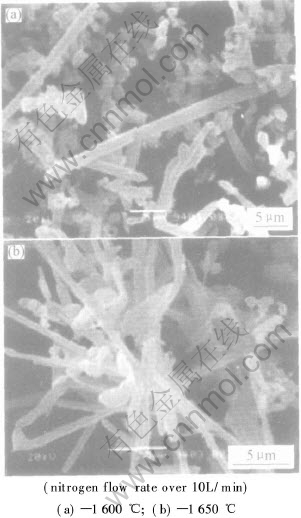
图4 AlN晶须的SEM像
Fig.4 SEM images of AlN whiskers
表4 碳量对AlN粉末中氮、 氧含量的影响
Table 4 Effects of carbon content on nitrogen and oxygen content of AlN powders
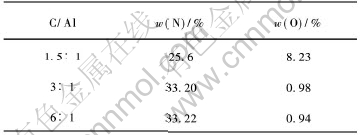
2.7 粉末性能
采用最佳制粉工艺: 以0.4mol/L的硝酸铝溶液和比表面积为156m2/g的碳黑为原料, 添加适量的硬脂酸(SA)和聚乙二醇(PEG)作为表面活性剂, 控制沉淀过程中pH为9, 通过共沉淀工艺得到分散性好、 团聚程度小的前驱物, 并将此前驱物在常压、 氮气流量为5L/min的条件下, 于1550℃煅烧4h, 最后将反应产物于650℃的空气中除碳4h, 制备的AlN粉末的性能如表5所列。 图5所示为沉淀前驱物合成的氮化铝粉末的SEM像。 由图5可看出, 采用沉淀前驱物体系制备的氮化铝粉末为形状规则的圆球形颗粒, 其分散性良好, 粉末的粒度细小均匀, 平均粒度约为0.4μm。
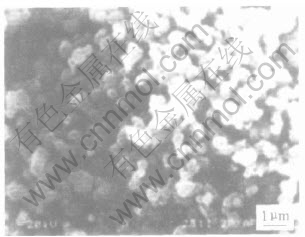
图5 沉淀前驱物体系制备的AlN粉末的SEM像
Fig.5 SEM image of AlN powders synthesized from precipitated precursor
表5 AlN 粉末的性能
Table 5 Properties of AlN powders

3 结论
以0.4mol/L的硝酸铝溶液和比表面积为156m2/g的碳黑为原料, 控制原料中碳铝比(C/Al)为3∶1, 添加适量的硬脂酸(SA)和聚乙二醇(PEG)作为表面活性剂, 控制沉淀过程中pH=9, 通过共沉淀工艺得到分散性好、 团聚程度小的前驱物。 将此前驱物在常压、 氮气流量为5L/min的条件下, 于1550℃煅烧4h, 最后将反应产物在650℃的空气中除碳4h, 制备出氮含量为33.20%, 氧含量为0.98%, 比表面积为4.26m2/g的AlN粉末。
REFERENCES
[1]Mussler B H. Advanced materials & powders[J]. Am Ceram Soc Bull, 2000, 79(6): 45-47.
[2]Sheppard L M. Aluminum nitride: a versatile but challenge material[J]. Am Ceram Soc Bull, 1990, 69(11): 1801-1812.
[3]周和平, 刘耀诚, 吴音. 氮化铝陶瓷的研究与应用[J]. 硅酸盐学报, 1998, 26(4): 517-522.
ZHOU He-ping, LIU Yao-cheng, WU Yin. Development of aluminum nitride ceramics[J]. Journal of the Chinese Ceramic Society, 1998, 26(4): 517-522.
[4]Pathak L C, Ray A K, Das S, et al. Carbothermal synthesis of nanocrystalline aluminum nitride powders[J]. J Am Ceram Soc, 1999, 82(1): 257-260.
[5]Hashimoto N, Yoden H, Nomura K. Preparation of aluminum nitride powder from aluminum polynuclear complexes[J]. J Am Ceram Soc, 1991, 74(6): 1282-1286.
[6]Cho Y W, Charles J A. Synthesis of nitrogen ceramic powders by carbothermal reduction and nitridation, Part 3: aluminum nitride[J]. Mater Sci Tech, 1991,7: 495-504.
[7]秦明礼, 曲选辉, 林建凉, 等. 碳热还原法合成氮化铝粉末的研究[J]. 材料导报, 2001, 15(7): 56-69.
QIN Ming-li, QU Xuan-hui, LIN Jian-liang, et al. Research on synthesis of AlN powders by carbothermal reduction method[J]. Materials Review, 2001, 15(7): 56-59.
[8]郑仕远, 陈健, 潘伟. 湿化学方法合成及应用[J]. 材料导报, 2000, 14(9): 25-27.
ZHNEG Shi-yuan, CHEN Jian, PAN Wei. Compositing by wet-chemical method and its application[J]. Materials Review, 2000, 14(9): 25-27.
[9]吴湘伟, 段学臣, 陈振华. 溶胶-凝胶法制备PZT纳米晶反应机理[J]. 中国有色金属学报, 2003, 13(1): 127-131.
WU Xiang-wei, DUAN Xue-chen, CHEN Zhen-hua. Reaction mechanism of synthesizing PZT nano-crystalline powder by sol-gel process[J]. The Chinese Journal of Nonferrous Metals, 2003, 13(1): 127-131.
[10]田玉明, 黄平, 冷叔炎, 等. 沉淀法的研究及其应用现状[J]. 材料导报, 2000, 14(2): 47-49.
TIAN Yu-ming, HUANG Ping, LENG Shu-yan, et al. Current status of precipitation research and its application[J]. Materials Review, 2000, 14(2): 47-49.
[11]娄彦良, 李春花, 肖建中. 溶胶共沉淀法制粉中影响粉末粒度的主要因素[J]. 中国粉体技术, 2002, 8(1): 15-17.
LOU Yan-liang, LI Chun-hua, XIAO Jian-zhong. Influential factors on particle size of ZrO2 powder prepared by sol-coprecipitional method[J]. China Powder Science and Technology, 2002, 8(1): 15-17.
[12]Forsland B, Zheng J. Carbothermal synthesis of aluminum nitride at elevated nitrogen pressure, Part Ⅰ: effect of process parameters on conversion rate[J]. J Mater Sci, 1993, 28: 3125-3131.
基金项目: 国家杰出青年科学基金资助项目(50025412); 国家重点基础研究发展规划资助项目(G2000067203)
收稿日期: 2004-09-25; 修订日期: 2005-01-21
作者简介: 秦明礼(1975-), 男, 博士, 副教授
通讯作者: 秦明礼, 博士; 电话: 010-62332727; E-mail: mlqin75@hotmail.com
(编辑李艳红)