
Electrochemical co-deposition of magnesium based alloy from molten salts
SUN Ning-lei(孙宁磊), REN Jia-lin(任甲林), LIU Heng-yang(刘恒阳), ZHU Hong-min(朱鸿民)
School of Metallurgical and Ecological Engineering, University of Science and Technology Beijing,
Beijing 100083, China
Received 15 July 2007; accepted 10 September 2007
Abstract: Magnesium based alloys with aluminum and zinc were obtained through electrochemical co-deposition from LiCl-NaCl-MgCl2 melt. The possibility of electrochemical co-deposition was discussed in detail by electro-analytical methods including cyclic voltametry, square wave voltametry, and chronopotentiometry. The co-deposition happens when the concentration of aluminum and zinc ions is kept at low value and the current density is high enough. The components of alloy elements can be controlled by fixing the components of the feeding salts. A laboratory experiment of the preparation by step-current co-deposition was also performed and certain compositions of the Mg-Al, and Mg-Zn were obtained. The alloys obtained from the co-deposition show a typical as-cast microstructure. The best conditions of electrolysis such as temperature, amount of addition and mode of feeding were discussed in detail.
Key words: magnesium based alloys; electrochemical co-deposition; molten salts
1 Introduction
Magnesium base alloys are attractive for applications in wide field and considered “green alloy” for their series of excellent properties[1]. The conventional process for magnesium alloy production is simple in principle and widely used in industry, in which the alloying agents such as Al and Zn are added into fused magnesium under some gaseous protecting agent containing SF6[2]. However, the whole process for alloy production is complex, which includes every alloying metal metallurgy process and subsequent smelting. High metal waste rate happens during the whole process especially in the smelting. Safeguard of SF6 cover against metal burning causes serious greenhouse effect[3].
Many efforts have focused on the electrolysis method of Mg base alloy preparation. SHARMA [4] proposed a relatively simple electrochemical method, in which magnesium was deposited on aluminum cathode previously added and diffused into the liquid metal to form alloy in NaCl-KCl-MgCl2 melt at 750 ℃. LIN and UAN[5] proposed the preparation of Mg-Li-Al-Zn master alloy in air by electrolytic diffusing method at 500 ℃. AZ91 was used as cathodic material. After the electrolysis experiments, Mg-12%Li-9%Al- 1%Zn (mass fraction) alloy sheet was obtained. ZHANG et al[6] presented an electrochemical method for the preparation of Mg-Li alloys at low temperature molten salt system, in which Mg was employed as cathodic and the electrolysis temperature was not higher than 510 ℃. DENG et al[7] proposed a process for preparing Mg-Y alloy by electrolysis. Mg was also used as cathode electrode. These processes above avoid the step of mixing, but still require the feeding of alloying metals in parallel. Electrochemical co-deposition is another traditional method to produce alloy by electroplating and electrowinning[8-10]. However there is no report on the Mg-Al, Mg-Zn and Mg-Al-Zn alloy preparation through co-deposition method.
In this work, Mg-Al alloys and Mg-Zn alloys were successfully obtained through electrochemical co-deposition from LiCl-NaCl molten salt. In this process, magnesium and the alloying elements are co-deposited from the molten salt and stay at the bottom of the bath. The composition of the magnesium alloy mentioned above can be adjusted in a wide range by changing the component and quantity of feed materials. A series of electro-analytical test were performed to confirm the feasibility of the co-deposition of Mg-Al[11], Mg-Zn and Mg-Al-Zn alloys.
2 Experimental
All the salts used were pre-dried and purified before the experiments. Anhydrous aluminum chloride was purified by distilling through a glass frit. Anhydrous mixture of LiCl and NaCl as well as anhydrous magnesium chloride was purified by bubbling HCl through their melt in a quartz container. The pure salts were stored and handled inside a glove box with argon atmosphere.
A three-electrode cell was applied for all the experiments (Fig.1). A tungsten wire with the diameter of 1 mm was used as the working electrode, a graphite rod was used as the counter electrode, and an Ag/AgCl electrode was used as the reference electrode. The Ag/AgCl reference electrode was calibrated against a Cl2/Cl- electrode, which was generated temporarily by constant current electrolysis on a graphite electrode. All the experiments were carried out under Ar atmosphere at 973 K. Cyclic voltammetry, square wave voltammetry and chronopotentiometry were used for the electrochemical analysis. Mg-Al and Mg-Zn alloys were prepared by constant current electrolysis. All the experiments were performed by a Potentiostat/ Calvanostat (PAR EG&G, 263A). The microstructures of alloy products were detected with optical microscope and SEM and their composition was analysed by ICP.
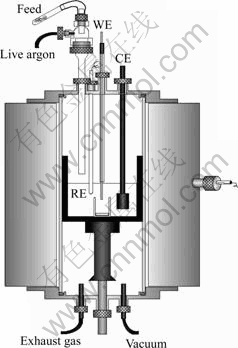
Fig.1 schematic of cell used in experiment
3 Results and discussion
3.1 Electrochemical analysis
The cyclic valtammogram of the system consisting of both Al3+ and Zn2+ in LiCl-NaCl-MgCl2 melt is shown in Fig.2. Three cathodic peaks, A, B and C are observed at the cathodic sweep, and followed by three anodic peaks, A′, B′ and C′ at the reverse sweep, which correspond to the deposition and dissolution of Zn, Al and Mg, respectively.
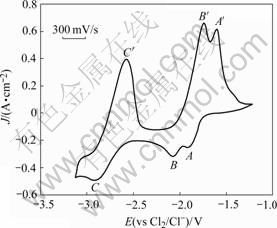
Fig.2 Voltammogram of LiCl-NaCl-MgCl2-AlCl3-ZnCl2 system on tungsten electrode (Scanning rate: 0.3 V/s, [Mg2+]=40 mol/m3, [Zn2+]=30 mol/m3, [Al3+]=30 mol/m3)
Generally, electrochemical co-deposition takes place when the deposition potential of the ions is the same under certain current density, that is, the nearer the potentials are, the more easily the co-deposition happens. However, the difference of deposition potential between Mg, Al, and Zn is so significant (Fig.2) that it is impossible to narrow the difference only by adjusting the concentration of the ions according to the Nernst equation. The co-deposition of Mg-Al, Mg-Zn and Mg-Al-Zn becomes possible only when the current reaches diffusion limits of Al3+ and Zn2+ and the reduction of Mg2+ happens.
3.2 Electrolysis product
The electrolysis was carried out at 700 ℃ which is about 70 ℃ higher than the melting point of the alloys. The liquid alloy formed on cathode electrode dropped to a MgO crucible set at the middle bottom of the cell, being protected by the lower density electrolytes from corrosion of chlorine.
Fig.3 presents the images of the alloys obtained after several hours electrolysis. The Mg-Al and Mg-Zn alloy displays a typical as cast microstructure which shows interdendritic network structure among the α-Mg dendrites comprised eutectic α-Mg and Mg17Al12. EDS and ICP analysis indicate that Al or Zn element has a more uniform distribution in the whole bulk obtained by electrochemical co-deposition method than that by smelting method.
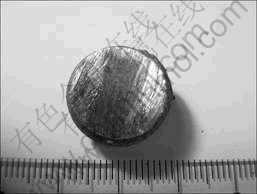
Fig.3 Image of Mg-9.89%Al alloy after 10 h electrolysis
3.3 Effect of electrolysis temperature on current efficiency(CE)
A series of electrolysis tests were carried out under various temperatures from 650 ℃ to 730 ℃. The results indicate that the highest CE is at about 700 ℃ wherever the electrolysis for 1 h or 5 h, but at 650 ℃ EC after 1 h electrolysis is much lower than that after long time electrolysis. Because the temperature was too close to the melting point of the alloy, the fish-roe-like and powdered products were collected instead of bulk after a short electrolysis period. These sorts of products owning a large surface area has high dissolvability in the melt, which leads to a low CE. With the expanding of electrolysis time, the amount of the alloy increased and the products became aggregating. The CE of 5 h electrolysis at 650 ℃ could reach 85%. Because the vapor pressure of AlCl3 or ZnCl2 in the melt increased with the temperature, high temperature caused serious loss of Al and Zn in the product. 700 ℃ is considered the optimum temperature.
3.4 Effect of fluoride additions on current efficiency (CE)
Fluoride additions have the capability of reducing the surface tension of the electrolyte, removing the oxide on the surface of the product as well as improving the wetting between the liquid alloy and tungsten electrode, which contributes to the aggregation and glomeration of products so as to enhance CE.
In Fig.4, the effect of fluoride additions on CE was studied. The alloy appeared to be fish-roe-like and powdered and CE was no more than 60%. The glomera- tion of products and CE were improved obviously as the content of LiF increased. When LiF reached 3% (mass fraction) in the electrolyte, product had grown as a whole ball and CE was high as expected.

Fig.4 Effect of fluoride additions on CE
3.5 Effect of mode of feeding on content of alloying metal
Feeding modes are the composition of the feed material and feeding periodic time, which affects the content of alloying metal in the product directly. It is found in preparation experiments that Mg-Al and Mg-Zn have the same situation at this aspect.
Almost all AlCl3 was lost when feeding pure AlCl3 into electrolyte, since there was less than 1% (mass fraction) Al detected in the alloy obtained. When pre-molten salt of AlCl3 and MgCl2 on planned proportion was applied, Al in the product is up to 5.7% (mass fraction), which is still much lower than that of the planed value (10%). This is mainly because AlCl3 vaporizes drastically at electrolysis temperature. If the content of AlCl3 in feed material is too high, high partial pressure of AlCl3 leads to serious vaporization before Al3+ diffuses into the electrolyte at the moment of feeding. As Fig.5 presents, pre-molten AlCl3-MgCl2 with LiCl-NaCl before feeding (AlCl3 is diluted from 13.2% to 6.3%) reduces the partial pressure of AlCl3 so as to minimize the loss of Al in the alloy.
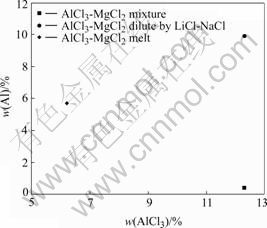
Fig.5 Effect of composition of feeding material on content of alloying metal
Shortening feeding periodic time means reducing the amount of feed material proportionally at each feeding point. The increase of concentration of AlCl3 in the electrolyte after feeding reduced consequently. Through this method, the vaporization of AlCl3 can be controlled at an acceptable low level. As shown in Fig.6, when feeding periodic time reduced to 5 min, the content of Al in the product was close to the plan of 10%.
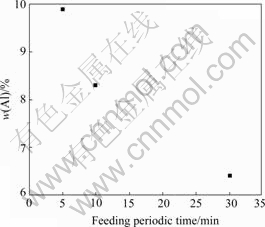
Fig.6 Effect of feed periodic time on content of alloying metal
Fig.7 shows the relationship of components of the alloying elements (Al and Zn) in the obtained alloy to that in feeding material under optimum electrolysis condition. They are almost completely identical as the plan, which means the components of alloy can be adjusted as required.
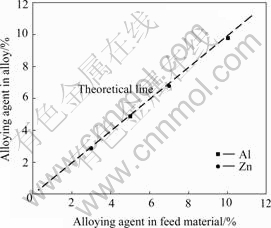
Fig.7 Experimental data (point) and theoretical data (dashed line) about content of alloying agent in feed material vs that in alloys
4 Conclusions
1) Electrochemical co-deposition of magnesium alloys with aluminum and zinc was proved to be feasible by electro-analytical techniques.
2) Alloys with various compositions from 2% to 15% were obtained.
3) Temperature of 700 ℃ and 3% fluoride addition were considered to be the optimum conditions.
4) The content of the alloying elements in obtained alloy was identical with that in the feeding materials.
References
[1] Nair K S, Mittal M C. Development of rapidly solidified(RS) magnesium-aluminum-zinc alloy [J]. Materials Science and Engineering A, 2001, 304/306(1/2): 520-523.
[2] Cashion S P, Ricketts N J, Hayes P C. The mechanism of protection of molten magnesium by cover gas mixtures containing sulfur hexafluoride [J]. Light Metals, 2002, 2(1): 37-42.
[3] Hillis J E. New alternatives for magnesium melt protection [J]. Magnesium Industry, 2000, 1(1): 37-39.
[4] Sharma R A. Electrolytic production process for magnesium and its alloy [P]. EP 0747509, 1996.
[5] Lin M C, Uan J Y. Preparation of Mg-Li-Al-Zn master alloy in air by electrolytic diffusing method [J]. Materials Transactions, 2005, 46(6): 1354-1359. (in Japanese)
[6] Zhang M L, Yan Y D, Hou Z Y, Fan L A, Chen Z, Tang D.X. An electrochemical method for the preparation of Mg-Li [J]. J Alloys Compd, 2007, 440(1/2): 362-366.
[7] Deng W P, Zeng X D, Chi X D. Process for preparing Mg-Y alloy and yttrium metal by electrolysis [J]. Rare Metal, 1997, 18(2): 57-60.
[8] Yang B G, Qiu Z X, Gao B L. Electrolytic preparation of Al-Ca master alloy on liquid Al cathode [J]. Trans Nonferrous Met Soc China, 2000, 10(2): 246-249.
[9] Polyakova L P, Taxil P, Gpolykov E. Electrochemical behavior and co deposition of titanium and niobium in chloride-fluoride melts [J]. J Alloys Compd, 2003, 359(1/2): 244-255.
[10] Iida T, Nohira T, Ito Y. Electrochemical formation of Sm-Co alloys by co-deposition of Sm and Co in a molten LiCl-KCl-SmCl3-CoCl2 system [J]. Electrochimica Acta, 2003, 48(17): 2517-2521.
[11] Zhang X, Jiao S Q, Zhu H M. Electrochemical co-deposition of magnesium-aluminum alloys in alkali chloride melts [J]. JOM, 2004, 56(11): 30.
Foundation item: Project(50374012) supported by the National Natural Science Foundation of China
Corresponding author: ZHU Hong-min; Tel: +86-10-62332267; E-mail: hzhu@metall.ustb.edu.cn
(Edited by PENG Chao-qun)