Trans. Nonferrous Met. Soc. China 23(2013) 2323-2328
Mechanical properties of tungsten nanowhiskers characterized by nanoindentation
Li-zhen HOU1,2, Shi-liang WANG1,3, Guo-Liang CHEN3, Yue-hui HE1, Ya XIE1
1. Key Laboratory of Powder Metallurgy, Central South University, Changsha 410083, China;
2. School of Physics and Information Science, Hunan Normal University, Changsha 410081, China;
3. School of Physics and Electronics, Central South University, Changsha 410083, China
Received 24 July 2012; accepted 18 January 2013
Abstract: The Mechanical properties of the hexagonal tungsten nanowhiskers, which were synthesized by chemical vapor deposition, were characterized by instrumented nanoindentation and atomic force microscope (AFM). The nanoindentation results show that tungsten nanowhiskers exhibit a hardness of (6.2±1.7) GPa and an elastic modulus of (225±20) GPa. According to the comparative test results, the tungsten nanowhiskers possess a comparable hardness to tungsten microwhiskers, and an hardness increase of 35% to the bulk single-crystal tungsten. The increase in the hardness of whiskers is attributed to the lacking of dislocation avalanche observed in the bulk single-crystal tungsten. The measured modulus is about 80% that of the tungsten microwhiskers, which can be contributed to the size effects of the nanowhiskers and the substrate effects in the nanoindentation test.
Key words: tungsten; nanowhiskers; mechanical properties; nanoindentation
1 Introduction
The refractory metal tungsten (W) has excellent physical and chemical properties, such as high melting point (about 3420 °C), high density (19.3 g/cm3), high strength and excellent creep resistance at room and elevated temperatures, high electron emissivity and low vapor pressure [1]. The applications of W have now covered quite various fields such as lighting, electronics, high-temperature technology, medicine, aviation and military uses. Among all the W-based materials, W micro-sized whiskers have attracted intensive attention due to their extremely high tensile strength of 27.5-32.8 GPa, and are generally considered ideal reinforcing materials in high-performance composites [1,2]. For example, micro-sized W whiskers can be used to fabricate W heavy alloy penetrators to replace the existing depleted uranium penetrators with the health hazards and risks involved in using the radioactive materials [1,3].
W nanowhiskers have recently attracted considerable interest due to their unique structural characteristics, properties and potential applications [4-10]. In particular, W nanowhiskers are expected to have superior mechanical properties compared with the corresponding micro-sized whiskers or bulk counterparts [11-14], just as some other metallic nanowhiskers, such as Cu [15], Au [16] and Ag [17]. Generally, the mechanical properties of W microwhiskers with diameters above 10 μm could be characterized by the micro-scaled tensile tester [18,19]. However, it is quite difficult to test the small W whiskers with diameters below 1 μm due to the technical difficulties. CIMALLA et al [11] used both AFM-based method and the resonant method to test the elastic modulus of the single-crystal W nanowhiskers, which were prepared from directionally solidified NiAl-W alloys by a chemical release from the resulting binary phase material. In the AFM-based method, the force-displacement measurements on single-clamped W nanowhiskers with diameters of 100-300 nm gave an elastic modulus of 332 GPa [11].
However, in the resonant method, the double- clamped W nanowhiskers, which were employed as resonant oscillators, exhibited an elastic modulus of 450 GPa [11]. Later, PUGACHEVSKII [12] also used the AFM-based method to measure single-crystal W nanowhiskers synthesized by Ni-catalyzed chemical vapor deposition (CVD), and achieved a quite low elastic modulus of (100±30) GPa. Obviously, all these values are quite different from ~400 GPa for bulk single-crystal W [1]. Considering their nearly perfect single-crystal structure [11,12], W nanowhiskers, although synthesized by different techniques, are expected to have the similar mechanical properties. The most possibility for the significant discrepancy should result from the measurement methods, because both AFM-based and resonant methods are quite sensitive to the boundary conditions, which are quite difficult to confirm in practice due to their nanoscale size of the tested whiskers [11].
In our previous works, hexagonal W whiskers with diameters ranging from tens of nanometers to tens of micrometers were successfully fabricated by catalyst-free CVD [13,14] and the mechanical properties of the W microwhiskers with diameters ranging from several to a dozen micrometers were tested by nanoindentation method [20]. In this work, the mechanical properties of the hexagonal W nanowhiskers with thickness below 300 nm were further reported by instrumented nanoindentation.
2 Experimental
The W nanowhiskers were fabricated by the catalyst-free CVD [13,14]. The morphological and structural characteristics of the synthesized W nanowhiskers were characterized by scanning electron microscopy (SEM: FEI Nova Nano SEM 230) and transmission electron microscopy (TEM: FEI Tecnai F20). The synthesized nanowhiskers were immersed in acetone and dispersed by an ultrasonic cleaning device. A Si (111) wafer and a 1 μm-thick SiO2 layer on Si (SiO2/Si) wafer, used as the substrates, were then dipped into the solution and pulled out. After drying, mono-dispersed nanowhiskers lying on the Si and the SiO2/Si substrate were prepared. The elastic moduli of the Si substrate and SiO2/Si substrate were determined to be (180±5) GPa and (85±5) GPa, respectively, by nanoindention tests.
The nanoindentation tests were performed on a nanomechanical comprehensive test system (CSM OPX) by a three-sided Berkovich indenter with tip radius of about 50 nm. An atomic force microscope (AFM, Veeco Nanoman VS) was used to examine the surface topographies of the nanowhiskers before and after indentation. Nanoindentation hardness is normally defined as the indentation load divided by the projected contact area of the indentation. It is the mean pressure that a material will support under load. From the load—displacement curve, hardness can be obtained at the peak load as [20]
(1)
where H, Pmax and A are hardness, the maximum applied load and the projected contact area at the maximum applied load, respectively. The elastic modulus was calculated using the reduced or effective modulus measured from nanoindentation using the following equation [20]:
(2)
where Eeff is the effective modulus determined from the load—displacement curve; Ei and νi are the modulus and Poisson ratio of the diamond indenter; and E and ν are the modulus and Poisson ratio of the specimen. The values of Ei=1141 GPa, νi=0.07 and ν=0.28 [20] were used in this study.
3 Results and discussion
Figure 1(a) shows the typical SEM image of the synthesized W nanowhiskers with length about 50 μm grown on a Si substrate. High-magnification SEM image further reveals that the as-synthesized W whiskers possess a hexagonal cross-section (the inset in Fig. 1(a)). TEM analyses demonstrate that the hexagonal W nanowhiskers grow along the [111] directions of body-centered cubic (BCC) W (Fig. 1(b)). In the high-resolution TEM image (HRTEM) (the inset in Fig. 1(b)), the lattice fringes with the interplanar spacing of 0.22 nm correspond to the {110} planes of BCC-structured W, and no visible oxide layer exists on the whisker surface as the sample was characterized right after being synthesized. The three-dimensional (3D) AFM image (Fig. 1(c)) and the corresponding section analysis profile (Fig. 1(d)) of a representative hexagonal nanowhisker reveal that the W nanowhiskers have a smooth surface with a thickness of 248 nm.
In the nanoindentation characterization, the peak indentation depths were controlled to be less than 20% of the thickness of the corresponding nanowhiskers, in order to minimize the possible substrate effects [21-23]. It was reported that the substrate effect on the measured hardness and elastic modulus might be ignored if the indentation depth is less than 30% of the whisker/film thickness [21]. Figures 2(a) and (b) show the representative AFM image and the corresponding section analysis profile of an indentation impression made on a W nanowhisker with thickness of 200 nm. It can be found that a slight pile-up, but no cracks, appears in the area surrounding the indentation impression. Figure 2(c) displays the representative nanoindentation load—displacement curve and the corresponding load—time segments. The peak indentation depth is about 29.9 nm, which is about 15% of the whisker thickness. It should be noted that the sudden jump in displacement, usually observed in the nanoindentation of bulk single-crystal W, was not observed in the test of W nanowhiskers [24,25].
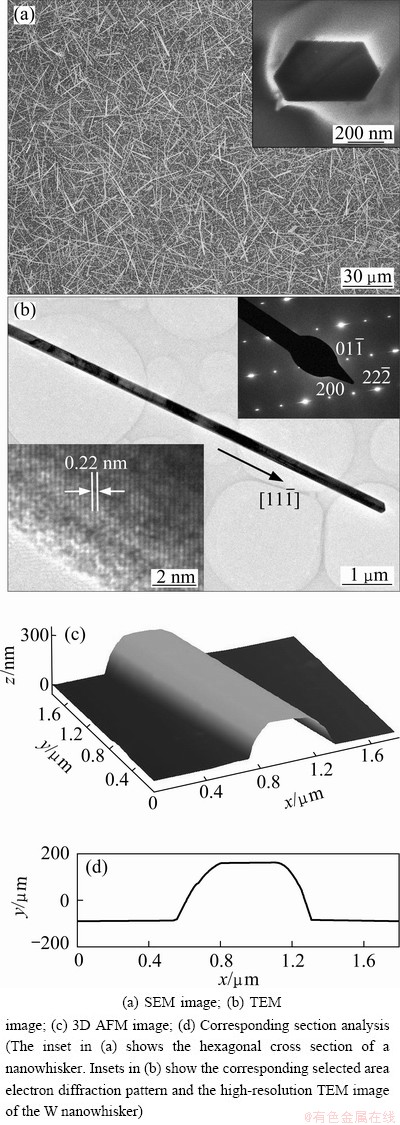
Fig. 1 Hexagonal W nanowhiskers
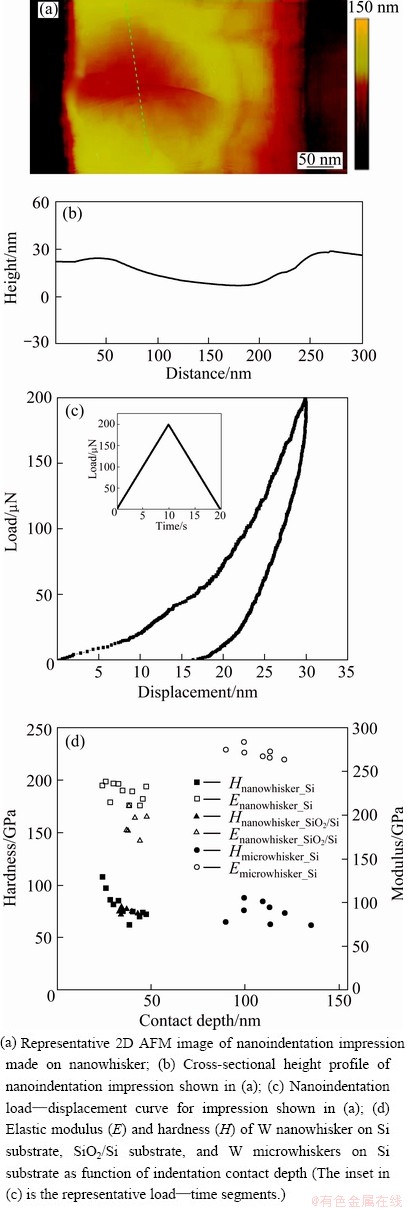
Fig. 2 Nanoindentation results of W nanowhiskers
The indentation hardness of the W nanowhiskers on Si substrate was measured to be (6.2±1.7) GP for the contact depth ranging from 25 to 48 nm, and an obvious increase of the hardness appeared when the contact depth was less than 30 nm (Fig. 2(d)). These results are higher than the reported value of 3.4-5.8 GPa for the bulk W [20]. It has been well demonstrated that there is usually a sudden jump in displacement in the load—displacement curves of bulk single-crystal W [24,25]. This yield discontinuity, also named as dislocation avalanche, could make up more than half of the total indentation displacement [24,25]. However, as mentioned above, no such yield discontinuity was ever observed in the load—displacement curves of the W nanowhiskers. The measured W nanowhiskers exhibit a nearly perfect structure (Fig. 1(b)), which should be the reason that the indentation-induced dislocation avalanche was not observed in the W nanowhiskers. Therefore, it is rational to suggest that the hardness increase is attributed to the perfection of microstructure of the W nanowhiskers. In addition, the phenomenon of hardness increase at low contact depth is now generally accepted as the result from the surface effects and the shallow indentation effects [26-29].
The elastic modulus was measured to be (225±20) GPa, which is significantly lower than that of 332 GPa for W nanowhiskers measured by AFM-based method and 450 GPa measured by resonant method [11], and 400 GPa for bulk single-crystal W measured by the nanoindentation [24,25], but is (100±30) GPa higher than that for W nanowhiskers measured by AFM-based method [12]. The significant decrease of the measured elastic modulus, compared with bulk single-crystal W, might come from the following three factors.
1) The surface oxide layer. Usually, metal nanowhiskers are easily oxidized and then encapsulated by the corresponding oxidation layer, which may change the surface mechanical properties of the nanowhiskers. For the W nanowhiskers tested in our experiments, the oxidation layer thickness is typically below 2 nm, which is not presumed to be the domain factor for the significant decrease. Actually, this is also supported by the fact that the measured modulus does not show an obvious dependency on the indentation depth as shown in Fig. 2(d).
2) The surface effects [22,23]. It is reported that the modulus of nanowhiskers measured by nanoindentation might be 50% of the corresponding values for bulk materials due to the surface effects [22,23,26]. In our test, the surface effects are expected to be one of the domain factors for the decreased modulus.
3) The substrate effects [27,28]. It was also reported that the critical indentation depth to ignore the substrate effect might be 10%, instead of 30%, of the film or whisker thickness [27-29]. Moreover, when the modulus of the film or nanowhisker is higher than that of the substrate, the nanoindentation measurement will underestimate the modulus of the film or nanowhisker due to the substrate effects [28]. In our case, the modulus of W nanowhiskers is higher than that of the Si substrate (about 180 GPa). As a result, the decrease of the modulus might also be introduced by these effects.
To further confirm the substrate effects, nanoindentation tests were also performed on W nanowhiskers on the SiO2/Si substrate and W microwhiskers on the Si substrate, respectively. As for the W nanowhiskers on the SiO2/Si substrate, the obtained elastic modulus and hardness were determined to be (195±20) GPa, and (6.0±1.1) GPa (Fig. 2). As for the test of W microwhiskers, the peak indentation depths were controlled to be less than 10% of the whisker thickness, which was well-accepted to be able to avoid the substrate effects [29,30]. Figure 3(a) shows the AFM image of a hexagonal W microwhisker with three indentation impressions on its upper surface. Figure 3(b)
exhibits the typical high-magnification 3D image of the indention impression. The hardness and elastic modulus of the W microwhisker on Si substrate were measured to be (6.5±0.8) and (271±11) GPa with contact depth ranging from 90 to 150 nm (Fig. 2(d)). These results show that the microwhiskers have a similar hardness as the nanowhiskers, but about 20% increase in the modulus. Based on these results, it is reasonable to deduce that the lower elastic modulus of the SiO2/Si substrate (85 GPa) might lead to an underestimate, and the minimized substrate effects might increase the measured modulus for W nanowhisker. Therefore, the elastic modulus of the W nanowhiskers is expected to fall in the range of 225-270 GPa.
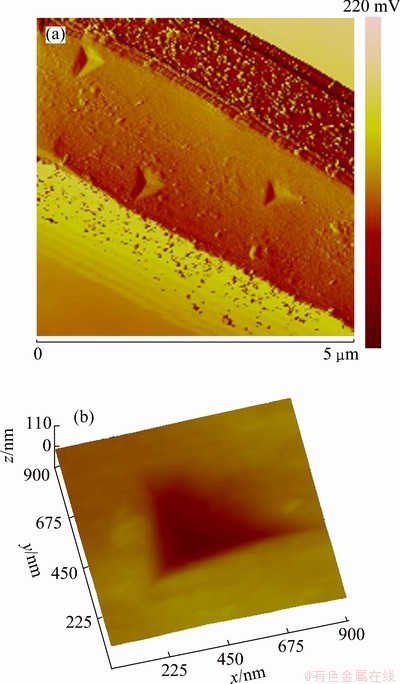
Fig. 3 Representative 2D AFM image of three nanoindentation impressions made on W microwhisker (a) and typical 3D image of nanoindentation impression (b)
4 Conclusions
1) The mechanical properties of hexagonal W nanowhiskers with thickness below 300 nm were characterized using nanoindentation method. The W nanowhiskers exhibit an average hardness of (6.2±1.7) GPa, which is increased by 35% compared with that of bulk single-crystal W. The hardness increase is attributed to the lack of dislocation avalanche in the W nanowhiskers.
2) The measured elastic modulus of W nanowhiskers is (225±20) GPa, which is significant lower than that of ~ 400 GPa for the bulk W. The decrease in modulus results from the size effects of the measured nanowhiskers and the substrate effects in the nanoindentation measurement.
References
[1] LASSNER E, SCHUBERT W D. Tungsten: Properties, chemistry, technology of the element, alloys, and chemical compounds [J]. New York: Kluwer Academic/Plenum Publishers, 1998.
[2] STARLIPER A G, KENWORTHY H. Tungsten whiskers by vapor-phase growth [J]. Electrodeposition and Surface Treatment, 1974, 2(4): 249-262.
[3] LEVITT A P. Tungsten penetrators: US Patent 5440995 [P]. 1995.
[4] HASSEL A W, MILENKOVIC S, SMITH A J. Large scale synthesis of single crystalline tungsten nanowires with extreme aspect ratios [J]. Physica Status Solidi A, 2010, 207(4): 858-863.
[5] MILENKOVIC S, HASSEL A W. Spatial features control of self-organised tungsten nanowire arrays [J]. Physica Status Solidi A, 2009, 206(3): 455-461.
[6] KARPOVICH N F, LEBUKBOVA N V, ZAVODINSKY V G, MAKAREVICH K S. Mechanism of the single-crystal tungsten whiskers growth in the process of the NiWO4 reduction by CO [J]. The Journal of Physical Chemistry C, 2008, 112(47): 18455-18458.
[7] WANG S L, HE Y H, ZOU J, JIANG Y, XU J, HUANG B Y, LIU C T, LIAW P K. Synthesis of single-crystalline tungsten nanowires by nickel-catalyzed vapor-phase method at 850 oC [J]. Journal of Crystal Growth, 2007, 306(2): 433-436.
[8] WANG S L, HE Y H, XU J, JIANG Y, HUANG B Y, ZOU J, WANG Y, LIU C T, LIAW P K. Growth of single-crystalline tungsten nanowires by an alloy-catalyzed method at 850 oC [J]. Journal of Materials Research, 2008, 23(1): 72-77.
[9] WANG S L, HE Y H, ZOU J, WANG Y, HUANG H, HUANG B Y, LIU C T, LIAW P K. Catalytic growth of metallic tungsten whiskers based on the vapor-solid-solid mechanism [J]. Nanotechnology, 2008, 19(34): 345604.
[10] WANG S L, HE Y H, ZOU J, WANG Y, HUANG H. Growth of single-crystal W whiskers during humid H2/N2 reduction of Ni, Fe-Ni, and Co-Ni doped tungsten oxide [J]. Journal of Alloys and Compounds, 2009, 482(1-2): 61-66.
[11] CIMALLA V, ROHLIG C C, PEZOLDT J, NIEBEL S M, AMBACHER O, BRUCHKNER K, HEIN M, WEBER J, MILENKOVIC S, SMITH A J, HASSEL A W. Nanomechanics of single crystalline tungsten nanowires [J]. J Nanomaterials, 2008, 2008: 638947.
[12] PUGACHEVSKII M A. Determining elastic moduli of tungsten nanowires [J]. Technical Physics Letters, 2010, 36(7): 639-641.
[13] WANG S L, HE Y H, FANG X S, ZOU J, WANG Y, HUANG H, COSTA P M F J, SONG M, HUANG B Y, LIU C T, LIAW P K, GOLBERG D. Structure and field-emission properties of sub-micrometer-sized tungsten-whisker arrays fabricated by vapor deposition [J]. Advanced Materials, 2009, 21(23): 2387-2392.
[14] WANG S L, HE Y H, LIU X L, ZHANG Q, ZOU J, HUANG H, SONG M, HUANG B Y, LIU C T, DU Y. Large-scale synthesis of tungsten single-crystal microtubes via vapor-deposition process [J]. Journal of Crystal Growth, 2011, 316(1): 137-144.
[15] RUNTHER R, KARLA H, DANIEL S G, REINER M, OLIVER K, CYNTHIA A V. Ultrahigh strength single crystalline nanowhiskers grown by physical vapor deposition [J]. Nano Letters, 2009, 9(8): 3048-3052.
[16] WU B, HEIDELBERG A, BOLAND J J. Mechanical properties of ultrahigh-strength gold nanowires [J]. Nature Materials, 2005, 4: 525-529.
[17] ZHAI A X, CAI X H, JIANG X Y, FAN G Z. A novel and facile wet-chemical method for synthesis of silver microwires [J]. Transactions of Nonferrous Metals Society of China, 2012, 22(4): 943-948.
[18] JIANG G Y, DUANG H L, SUN X M, ZHANG Z S, XU J, LI Y D, WANG J X, YU D P. Surface effects on elastic properties of silver nanowires: Contact atomic-force microscopy [J]. Physical Review B, 2006, 73(23): 235409.
[19] BRENNER S S. Plastic deformation of copper and silver whiskers [J]. Journal of Applied Physics, 1957, 28(9): 1023-1026.
[20] HUANG H, WU Y Q, WANG S L, HE Y H, ZOU J, HUANG B Y, LIU C T. Mechanical properties of single crystal tungsten microwhiskers characterized by nanoindentation [J]. Materials Science and Engeering A, 2009, 53(1-2): 193-198.
[21] OLIVER W C, PHARR G M. Improved technique for determining hardness and elastic modulus using load and displacement sensing indentation experiments [J]. Journal of Materials Research, 1992, 7(6): 1564-1580.
[22] BHUSHAN B, LI X D. Nanomechanical characterisation of solid surfaces and thin films [J]. International Materials Reviews, 2003, 48(3): 125-164.
[23] LI X, GAO H, MURPHY C J, CASWLL K K. Nanoindentation of silver nanowires [J]. Nano Letters, 2003, 3(11): 1495-8.
[24] LI X D, WANG X N, XIONG Q H, EKLUND P C. Mechanical properties of ZnS nanobelts [J]. Nano Letters, 2005, 5(10): 1982-1986.
[25] GERBERICH W W, YU W, KRAMER D, STROJNY A, BAHR D, LILLEODDEN E, NELSON J. Elastic loading and elastoplastic unloading from nanometer level indentations for modulus determinations [J]. Journal of Materials Research, 1998, 13(2): 421-439.
[26] GERBERICH W W, NELSON J C, LILLEODDEN E T, ANDERSON P, WYROBEK J T. Indentation induced dislocation nucleation: The initial yield point [J]. Acta Materialia, 1996, 44(9): 3585-3598.
[27] TAO X Y, WANG X N, LI X D. Nanomechanical characterization of one-step, combustion-synthesized Al4B2O9 and Al18B4O33 nanowires [J]. Nano Letters, 2007, 7(10): 3172-3176.
[28] SHU S Q, YANG Y, FU T, WEN C S, LU J. Can Young's modulus and hardness of wire structural materials be directly measured using nanoindentation? [J]. Journal of Materials Research, 2009, 24(3): 1054-1058.
[29] WU X X, AMIN S S, XU T T. Substrate effect on the Young's modulus measurement of TiO2 nanoribbons by nanoindentation [J]. J Materials Research, 2010, 25(5): 935-942.
[30] HUANG H, WINCHESTER K, LIU Y, HU X Z, MUSCA C A, DELL J M, FARAONE L. Determination of mechanical properties of PECVD silicon nitride thin films for tunable MEMS Fabry–Pérot optical filters [J]. Journal of Micromechanics and Microengineerging, 2005, 15(3): 608-614.
用纳米压痕法表征钨纳米晶须的力学性能
侯丽珍1,2,王世良1,3,陈国良3,贺跃辉1,谢 亚1
1. 中南大学 粉末冶金国家重点实验室 长沙 410083;
2. 湖南师范大学 物理与信息学院 长沙 410081;
3. 中南大学 物理与电子学院 长沙 410083
摘 要:通过化学气相沉积方法合成截面为六边形的单晶钨纳米晶须,利用纳米压痕仪和原子力显微镜对硅基底上的钨纳米晶须的力学性能进行表征。纳米压痕测试结果表明,钨纳米晶须的硬度为(6.2±1.7) GPa,弹性模量为(225±20) GPa。对比研究结果表明,钨纳米晶须的硬度与钨微米晶须的硬度相当,但比块体钨单晶高35%。这种硬度的增高是由于具有完好晶体结构的钨晶须在压痕测试中不会出现块体钨单晶中的位错崩。钨纳米晶须的弹性模量相当于钨微米晶须的80%,主要是由于纳米晶须的尺寸效应和测量过程中的基底效应所致。
关键词:钨;纳米晶须;力学性能;纳米压痕
(Edited by Xiang-qun LI)
Foundation item: Projects (50804057, 51074188) supported by the National Natural Science Foundation of China; Project (08C580) supported by the Scientific Research Fund of Hunan Provincial Education Department, China; Projects (2012T50703, 2011M500128) supported by China Postdoctoral Science Foundation Funded Project and Postdoctoral Science Foundation of Central South University, China
Corresponding author: Shi-liang WANG; Tel: +86-731-88877391; E-mail: shiliang@csu.edu.cn
DOI: 10.1016/S1003-6326(13)62736-3