
Grain refining action of Ti existing in electrolytic low-titanium aluminum with Al-4B addition for superheated Al melt
WANG Ming-xing(王明星), PANG Jin-hui(庞金辉), LIU Zhi-yong(刘志勇),
LIU Zhong-xia(刘忠侠), SONG Tian-fu(宋天福), YANG Sheng(杨 昇)
Department of Physics, Key Laboratory of Materials Physics of Ministry of Education, Zhengzhou University, Zhengzhou 450052, China
Received 15 June 2009; accepted 30 September 2010
Abstract: The effects of superheating temperature on the grain refining efficiency of Ti existing in electrolytic low-titanium aluminum (ELTA) without and with the Al-4B addition and the Al-5Ti-1B master alloy in pure Al were comparatively investigated. The results show that the Ti existing in ELTA without Al-4B addition exhibits a certain grain refining efficiency when the melt superheating temperature is lower, but the efficiency decreases rapidly when the superheating temperature is higher. The grain refining efficiency of the Al-5Ti-1B master alloy is better than that of the Ti existing in ELTA without Al-4B addition at any superheating temperature, but it also decreases obviously with the increase of the superheating temperature. One important reason is that the TiB2 particles coming from the Al-5Ti-1B master alloy can settle down at the bottom of the Al melt easily when the superheating temperature is increased, thus decrease the number of the potent heterogeneous nuclei retained in the Al melt. If the Al-4B master alloy is added to the ELTA melt, the grain refining efficiency of the Ti existing in ELTA can be improved significantly, and does not decrease with the increase of the superheating temperature. This perhaps provides us a possible method to suppress the effect of the superheated melt on the microstructures of aluminum..
Key words: electrolytic low-titanium aluminum; grain refining efficiency; superheating; Al-4B; Al-5Ti-1B
1 Introduction
Fine equiaxed grains are very important for the casting of aluminum alloy, which leads to many benefits, such as improved feeding ability, uniform distribution of second phase and microporosity and uniformity of mechanical properties. The grain refinement of aluminum and its alloys is commonly achieved by adding Ti- and/or B-containing aluminum master alloys to the alloy melt. Al-Ti and Al-Ti-B master alloys are most widely used as the grain refiners in the aluminum industry. However, the grain refining efficiencies of the master alloys are affected by many factors which include Ti/B ratio, melt holding time, melt temperature and so on. Studies on the grain refinement of aluminum and its alloys have been done for over 50 years by many researchers. However, the researches mainly focused on the mechanism of grain refinement, fading behavior of grain refining efficiency as well as the effect of Ti/B ratio on grain refining efficiency[1-6]. Superheat of aluminum alloy melt often occurred in industrial production. Generally speaking, the microstructure of the aluminum alloy refined by the grain refiners will coarsen when the melt temperature is increased. LI et al[7] investigated the effect of the melt superheating temperature on the average grain size of the Al ingots, and the results showed that the average grain size of the Al ingots increased with the increase of the superheating temperature. Coarse microstructure lowers the mechanical properties of the aluminum alloy. So, it is meaningful to study how to reduce the effect of the superheated aluminum alloy melt on the microstructure of the aluminum alloy.
Electrolytic low-titanium aluminum(ELTA) is a type of aluminum containing low Ti content produced directly by adding a small amount of TiO2 powder into an industrial aluminum electrolyzer. The details about the production of the ELTA were described in Refs.[8-9]. In this work, we investigated the effect of the superheating temperature on the grain refining efficiencies of the ELTA without and that of with Al-4B addition and the Al-5Ti-1B master alloy on pure aluminum comparatively. The aim of the investigation is to learn the role of the superheated melt in the grain refinement of aluminum alloy and to find out a way of suppressing the effect of the superheating temperature on the microstructure of the aluminum alloy.
2 Experimental
Three types of the ELTA with different Ti contents, commercial pure aluminum, Al-4B and Al-5Ti-1B master alloys were used in the present study. The chemical compositions of the ELTA and pure aluminum are listed in Table 1.
Table 1 Components of ELTA and pure Al (mass fraction, %)

Three sets of samples were prepared in this experiment. The first one was prepared using the ELTA, the second using the pure aluminum with Al-5Ti-1B addition, the third using the ELTA with the Al-4B addition. While adding the Al-4B master alloy to the ELTA melt, the amount of the Al-4B addition was calculated in terms of the Ti content of the ELTA and the Ti/B mass ratio was 5:1, which is the same as that of the Al-5Ti-1B master alloy. For each set of sample, three Ti contents, 0.06%, 0.11% and 0.13%, were tested, respectively.
All of the samples were prepared in an electrical resistance furnace. The ELTA or pure aluminum was first put into a graphite crucible and heated. After it was melted, the Al-4B master alloy or the Al-5Ti-1B master alloy was added to the melt at about 700 ℃ (for the first set of sample, the ELTA was used, but no master alloy was added to the melt). After that, the melt was heated up to 720, 780, 840, 900 and 950 ℃, successively. That is, the superheating temperature was 60, 120, 180, 240 and 290 ℃, respectively. When each assigned temperature was reached, the melt was fully stirred, and then poured into a steel mould immediately (see Fig.1) which was preheated at 200 ℃. The specimens for observing grain structure were sectioned at the height of 40 mm from the bottom of the castings. The specimens for SEM and XRD analysis were taken at the bottom of the castings. All of the specimens were polished and etched with a mixed acid to reveal their macroscopic grain structures. After the pictures were taken, each specimen was further polished and etched with a Keller’s reagent to reveal their microstructures. A MBA2100 metalloscope was used to analyze the microstructure quantitatively. Grain size analysis was carried out using the linear intercept method. The SEM and XRD analysis were performed using JSM-6700F type scanning electrical microscope and PANalytical X’Pert PRO X-ray diffractometer, respectively.

Fig.1 Schematic diagram of mould (unit: mm)
3 Results and discussion
The macrographs of the specimens containing 0.11%Ti (mass fraction) prepared using the ELTA melt under different superheating temperatures are shown in Fig.2. It can be seen that the Ti in the ELTA shows a certain grain refining effect on the melt under lower superheating temperature, but the grains of the specimens coarsen severely when the superheating temperature is increased from 60 to 290 ℃, and the grains transfer from fine equiaxed ones into coarse columnar ones. Fig.3 shows the micrographs of the specimens containing 0.11%Ti prepared using the pure aluminum with the Al-5Ti-1B addition at different superheating temperatures. It can be seen that the grain morphologies of all the specimens exhibit an equiaxed grain structure, and do not vary obviously even if the superheating temperature is up to 290 ℃. However, the grain sizes increase obviously. The micrographs of the specimens containing 0.11%Ti prepared using the ELTA with the Al-4B master alloy addition are shown in Fig.4. It can be seen that the grain morphologies of all the specimens are fine equiaxed grain structure, and the grain sizes are almost not affected by the superheating temperature. We also obtained the similar experimental results from the specimens containing 0.06% and 0.13%Ti. The grain size analysis of the specimens containing different contents of Ti is demonstrated in Fig.5. It is seen that the grain refining efficiency of the Al-5Ti-1B master alloy is much better than that of the Ti existing in ELTA at any superheating temperature. The boron contained Al-5Ti-1B master alloy significantly suppresses the effect of the superheating temperature on the grain refining efficiency of the master alloy. We also see from Fig.5 that though the Ti content and Ti/B mass ratio in the specimens prepared using the ELTA with the Al-4B addition are the same as those in the specimens prepared using the pure aluminum with the Al-5Ti-1B addition, the action of refining titanium grains of the trace boron added to the ELTA melt by the Al-4B master alloy is stronger. The grain sizes of the specimens decrease slightly with the increase of the superheating temperature. Fig.6(a) shows the SEM micrograph of the specimen taken at the bottom of the casting, which was prepared using the pure aluminum with the Al-5Ti-1B addition at the superheating temperature of 290 ℃. It is seen that many heterogeneous phases are present, and these phases seem to be located mainly in the grain boundaries. Through X-ray diffraction analysis, they are proved to be TiB2 phases. The X-ray diffraction analysis pattern is shown in Fig.6(b).
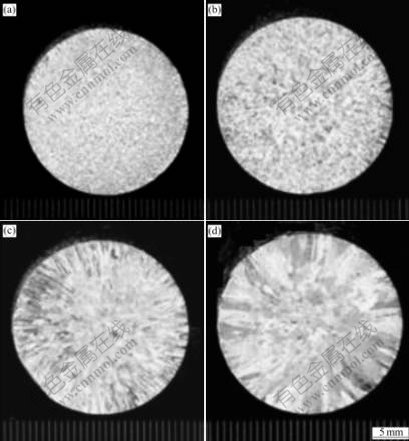
Fig.2 Macrographs of specimens containing 0.11%Ti prepared using ELTA at different superheat temperatures: (a) 60 ℃; (b) 120 ℃; (c) 180 ℃; (d) 290 ℃
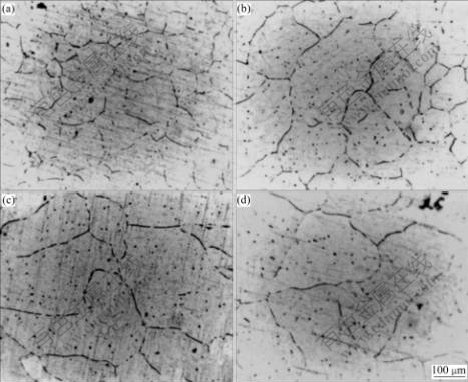
Fig.3 Micrographs of specimens containing 0.11%Ti prepared using pure Al with Al-5Ti-1B addition at different superheat temperatures: (a) 60 ℃; (b) 120 ℃; (c) 180 ℃; (d) 290 ℃
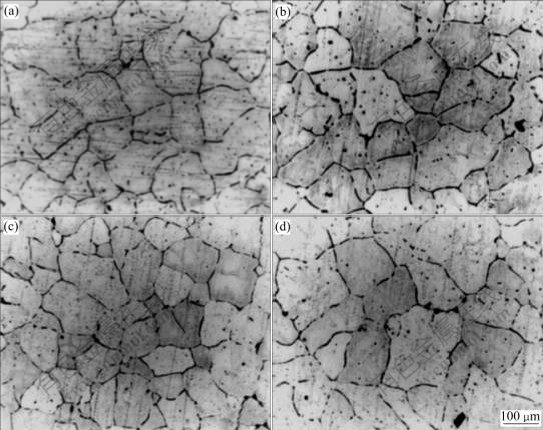
Fig.4 Micrographs of specimens containing 0.11%Ti prepared using ELTA with Al-4B addition at different superheat temperatures: (a) 60 ℃; (b) 120 ℃; (c) 180 ℃; (d) 290 ℃
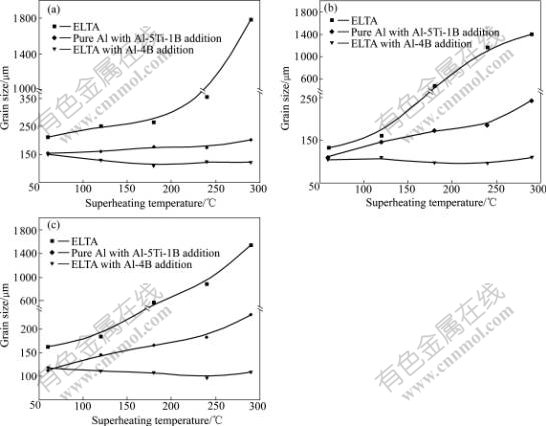
Fig.5 Variations of grain sizes in specimens with superheating temperature under different Ti contents: (a) 0.06%; (b) 0.11%; (c) 0.13%
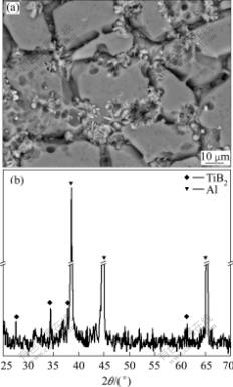
Fig.6 SEM image (a) and XRD pattern (b) of TiB2 particles found at bottom of casting prepared using pure Al with Al-5Ti-1B addition at superheating temperature of 290 ℃ and Ti content of 0.13%
As shown in Fig.2 and Fig.5, the grain morphologies of the specimens prepared using only ELTA exhibit fine equiaxed grain structure when the superheating temperature is low. This indicates that the Ti existing in the ELTA has a certain grain refining efficiency. The ELTA used in this study was produced by adding a small amount of TiO2 powder into an industrial aluminum electrolyzer. Since the Ti content in the ELTA is lower than 0.15% (the solid solubility of Ti in solid aluminum, see Table 1), there are not much TiAl3 phases in the ELTA. Ti element should be present in the ELTA mainly in the form of atoms. When the ELTA is re-melted, Ti atoms disperse evenly throughout the melt. When the melt is used to cast, there are not much TiAl3 phases formed during solidification of the melt. So, there are not potent heterogeneous nuclei appearing in the melt during solidification. Two reasons might be responsible for the grain refinement of the Ti existing in the ELTA. Firstly, the solubility of Ti in the solid aluminum is different from that in liquid aluminum. When the aluminum melt containing Ti solidifies, Ti atoms are enriched in the liquid near solid/liquid interface, resulting in constitutional undercooling. Many crystal nuclei which act as the nuclei of aluminum melt are formed heterogeneously. As a result, the grains of aluminum are refined. Secondly, grain growth rate has a great influence on grain size. Previous studies showed that the solute elements in liquid metal could restrict the growth of grains[1-2]. The growth-restricting factor (GRF), F=mC0(k0+1), was used to evaluate the grain growth-restricting ability of different solute elements in the melt, where m is the slope of liquidus line, C0 is the solute content and k0 is the equilibrium partition coefficient for the solute element. The larger the GRF of a solute element is, the stronger the grain growth- restricting ability is. Of all the alloying elements of aluminum, the GRF of Ti element is the largest. So, Ti is the most effective element that restricts the growth of grains[1]. In a word, the grain refining action of Ti existing in the ELTA is mainly ascribed to the heterogeneous nucleation caused by the constitutional undercooling and the grain growth-restricting action of Ti atoms. However, if the superheating temperature is higher, the Ti atoms diffuse more quickly in the melt and it takes a longer time to solidify after casting. These would greatly weaken the constitutional undercooling and the grain growth-restricting actions of the Ti atoms. As a result, the grain refining efficiency of the Ti vanishes almost completely when the superheating temperature is increased up to about 290 ℃ (see Fig.2(d)).
We can see from Fig.3 and Fig.5 that the gain refining efficiency of the Al-5Ti-1B master alloy is better than that of the Ti existing in the ELTA, and the effect of the superheating temperature on the gain refining efficiency is relatively small. The Ti and B contents of the Al-5Ti-1B master alloy are high up to about 5% and 1%, respectively. Because of this, a large number of TiAl3, TiB2, AlB2 etc are formed in the process of the production of the Al-5Ti-1B master alloy, and the sizes of these compounds are bigger. When the Al-5Ti-1B master alloy is added to the pure aluminum melt, the heterogeneous phases can be brought into the melt. The TiAl3 compounds coming from the master alloy will dissolve gradually into Al and Ti atoms. The dissolving speed of the TiAl3 compounds is relevant to the melt superheating temperature. If casting is carried out at a relatively low superheating temperature, some TiAl3 compounds might not dissolve completely before casting. These remaining TiAl3 compounds would act as the potent heterogeneous nuclei of the melt during solidification. The TiB2 particles combined with the solute titanium atoms released by the dissolution of the TiAl3 compounds could also nucleate α(Al)[10]. In fact, there are many potent heterogeneous nuclei in the melt at lower superheating temperature. So, the Al-5Ti-1B master alloy shows a good grain refining efficiency. But more and more TiAl3 compounds would dissolve with the increase of the superheating temperature, thus decrease the number of the potent heterogeneous nuclei. What is more important, the sediment of the TiB2 particles would take place more easily. So far as TiB2 particle is concerned, it could exist in the melt stably with high superheating temperature for a long time[7]. However, because the density of TiB2 is about 4.48 g/cm3, while the density of pure aluminum melt is only about 2.363 g/cm3 at 700 ℃ and decreases with the melt temperature (see Table 2[11]), the TiB2 particles tend to settle down at the bottom of the aluminum melt. According to the Stokes’s law, the settling velocity of TiB2 particles can be calculated by
(1)
Table 2 Density and viscosity of pure aluminum melt at different temperatures[11]
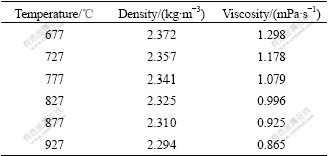
where r is the average radius of TiB2 particle, ρ and ρ0 are the densities of the aluminum melt and TiB2 particle, respectively, η is the viscosity of the aluminum melt, and g is gravity acceleration. We can see from the equation that the settling velocity of TiB2 particle is directly proportional to the square of the radius of the particle and yet to the difference of the densities between the aluminum melt and TiB2 particles, but inversely proportional to the viscosity of the aluminum melt. Because the TiB2 particles coming from the Al-5Ti-1B master alloy are bigger in size, the difference of the densities between the aluminum melt and the TiB2 particles increases with the melt temperature, while the viscosity of the aluminum melt decreases with the melt temperature (see Table 2[11]); at the last, the settling velocity of the TiB2 particles increases significantly in the aluminum melt with increasing the superheating temperature. In addition, it takes long time to solidify for the aluminum melt with high superheating temperature, so the TiB2 particles have more opportunity to settle down at the bottom of the melt after casting. We can see from Figs.6(a) and (b) that there are indeed many TiB2 particles at the bottom of the casting prepared using the pure aluminum with the Al-5Ti-1B addition at superheating temperature of 290 ℃. The sediment of the TiB2 particles further decrease the number of the potent heterogeneous nuclei in the melt. As a result, the grain refining efficiency of the Al-5Ti-1B master alloy fades away with the increase of the superheating temperature, resulting in the coarsening of the microstructure of the specimens (see Fig.3 and Fig.5).
In the case of the ELTA with the Al-4B master alloys addition, when the Al-4B master alloy is added to the ELTA melt, the Ti atoms in the melt would react with the B atoms released by the fusion of the Al-4B master alloys to form TiB2 particles. Such a reaction can be expressed by the following equation:
Ti+2B=TiB2(s) (2)
According to thermodynamic calculation[12], the change of Gibbs’ free energy of the reaction is ΔG=-73 381+ 38.996 T, where T is the temperature of the melt. It can be seen that ?G is negative when the temperature increases from 720 ℃ to 950 ℃. The reaction is a spontaneous process within the melt temperature range of this experiment. Because of the even distribution of the Ti in the melt and the low Ti content, as well as the quick diffusion of the B atom coming from the Al-4B due to the small atom size in the melt, TiB2 particles formed by the reaction are very fine, thus the number of the TiB2 particles is larger under conditions of the same Ti and B contents. The settling velocity of the TiB2 particles would also decrease because of the small size. As a result, the number of the TiB2 particles that settled down at the bottom of the melt after casting decreases, whilst more TiB2 particles retain throughout the melt. In fact, we find only a small amount of TiB2 particles at the bottom of the casting prepared using the ELTA with the Al-4B addition at the superheating temperature of 290 ℃ in the experiment. In a word, the number of the potent heterogeneous nuclei would not significantly decrease in the ELTA melt with the Al-4B addition with the increase of the superheating temperature. Therefore, the grain refining efficiency of the Ti existing in the ELTA with the Al-4B addition does not decrease with the increase of the superheating temperature (see Fig.4 and Fig.5).
For those TiB2 particles settling down at the bottom of the melt after casting, we can see from Fig.6 that the majority of the TiB2 particles are located in the grain boundaries among the equiaxed α(Al) grains. Some TiB2 particles are also located within the α(Al) grains, but there is an obvious interface between the TiB2 particles and α(Al) matrix, which suggests that the wetting between the TiB2 particles and α(Al) matrix is very poor. UHLMAN[13] pointed out that the interfacial energy between TiB2 particles and solid aluminum was much higher than that between TiB2 particles and liquid aluminum. MOHANTY and GRUZLESKI[10] believed that the lattice mismatch between TiB2 and α(Al) was large, resulting in the poor wetting and the high interfacial energy between TiB2 particles and α(Al). Because of these facts, the TiB2 particles alone could not serve as the potent heterogeneous nuclei of aluminum melt to appear inside α(Al) grains unless there are enough free solute titanium atoms in the melt[10, 14]. In other words, the TiB2 particles would be pushed to grain boundaries by the solidifying interface during solidification of the melt. In this experiment, many TiB2 particles settle down at the bottom of the melt after casting for the specimens prepared using the pure aluminum with the Al-5Ti-1B addition in the case of high superheating temperature. However, the free solute Ti atoms are apparently not enough at the bottom of the melt. Thus, the TiB2 particles are pushed to the grain boundaries (see Fig.6). It is also seen from Fig.6 that there are a few TiB2 particles (shown by arrows) located within the α(Al) grains, and the wetting between them is very good. According to the study by SCHAFFER[15], there might be two low-energy crystallographic orientation relationships between the TiB2 particle and α(Al). When the crystallographic orientation between the TiB2 particle and α(Al) is consistent with one of these two low-energy orientation relationships, the interfacial energy between the TiB2 particle and α(Al) would be minimized. And the TiB2 particles would be engulfed by the advancing solid/liquid interface, thus locate within the α(Al) grains.
4 Conclusions
1) The Ti existing in the ELTA has a certain grain refining effect on the aluminum melt with lower superheating temperature, but the efficiency is very sensitive to the superheat of the melt. With the increase of the superheating temperature, the grain refining efficiency decreases rapidly, and almost vanishes when the superheating temperature is increased up to about 950 ℃.
2) The grain refining efficiency of the Al-5Ti-1B master alloy is obviously better than that of the Ti existing in the ELTA. But it is still affected by the superheating temperature. With the increase of the superheating temperature, the grain refining efficiency of the Al-5Ti-1B master alloy decreases obviously.
3) By adding Al-4B master alloy to the ELTA melt at the Ti/B mass ratio of 5:1, the grain refining efficiency of the Ti existing in the ELTA on the melt at high superheating temperature can be improved significantly, and does not decrease with the increase of the superheating temperature. This perhaps provides us a possible method to suppress the effect of the superheat of the melt on the microstructures of aluminum.
References
[1] MURTY B S, KORI S A, CHAKRABORTY M. Grain refinement of aluminium and its alloys by heterogeneous nucleation and alloying [J]. Int Mate Rev, 2002, 47(1): 3-29.
[2] EASTON M, St JOHN D. Grain refinement of aluminum alloys Part I: The nucleant and solute paradigms—A review of the literature [J]. Metallurgical and Materials Transactions A, 1999, 30(6): 1613-1623.
[3] GUZOWSKI M M, SIGWORTH G K, SENTNER D A. The role of boron in the grain refinement of aluminum with titanium [J]. Metallurgical Transactions A, 1987, 18: 603-619.
[4] GEOFFREY K, SIGWORTH. Communication on mechanism of grain refinement in aluminum [J]. Scripta Materialia, 1996, 34(6): 919-922.
[5] LIMMANEEVICHITR C, EIDHED W. Fading mechanism of refinement of aluminum-silicon alloy with Al-Ti-B grain refiners [J]. Materials Science and Engineering A, 2003, 349: 197-206.
[6] YANG Bin, ZHANG Ji-shan, DUAN Xian-jin, HU Shuang-chun. Effect of Ti/B addition on the Al3Ti of in situ TiB2/Al composites [J]. Journal of University of Science and Technology Beijing, 1999, 6(4): 285-288.
[7] LI H, SRITHARA T, LAM Y M, LENG N Y. Effects of processing parameters on the performance of Al grain refinement master alloys Al-Ti and Al-B in small ingots [J]. Journal of Materials Processing Technology, 1997, 66: 253-257.
[8] LIU Zhi-yong, WANG Ming-xing, WENG Yong-gang. Grain refinement effect of Al based alloys with low titanium contents produced by electrolysis [J]. Transactions of Nonferrous Metals Society of China, 2002, 12 (6): 1121-1126.
[9] LIU Zhong-xia, SONG Tian-fu, XIE Jing-pei. Production and grain refinement of direct electrolytic low-titanium aluminium alloys [J]. The Chinese Journal of Nonferrous Metals, 2003, 13(5): 1257-1261. (in Chinese)
[10] MOHANTY P S, GRUZLESKI J E. Mechanism of grain refinement in aluminium [J]. Acta Metall Mater, 1995, 43(5): 2001-2012.
[11] ASSAEL M J, KAKOSIMOS K, BANISH R M. Reference data for the density and viscosity of liquid aluminum and liquid iron [J]. J Phys Chem Ref Data, 2006, 35(1): 285-300.
[12] ZHAN Zuo-gui, LIU Xiang-fa, BIAN Xiu-fang. Influence of the TiB2 distribution morphologies on the refining characteristics of AlTi5B master alloys [J]. Special Casting and Nonferrous Alloys, 1999(5): 12-13. (in Chinese)
[13] UHLMAN D R, CHALMERS B, JACKSON K A. Interaction between particles and a solid-liquid interface [J]. J Appl Phys, 1964, 35(10): 2986-2993.
[14] MOHANTYP S, GRUZLESKI J E. Grain refinement mechanisms of hypoeutectic Al-Si alloys [J]. Acta Materialia, 1996, 44(9): 3749-3760.
[15] SCHAFFER P L, MILLER D N, ARNE K. Crystallography of engulfed and pushed TiB2 particles in aluminum [J]. Scripta Materialia, 2007, 57: 1129-1132
Corresponding author: WANG Ming-xing; Tel/Fax: +86-371-67767776; E-mail: wangmx@zzu.edu.cn
DOI: 10.1016/S1003-6326(09)60241-7
(Edited by FANG Jing-hua)