
Cycling stability of La-Mg-Ni-Co type hydride electrode with Al
SUN Xian-zhong(孙现众), PAN Hong-ge(潘洪革), GAO Ming-xia(高明霞),
LI Rui(李 锐), LIN Yan(林 燕), MA Shuai(马 帅)
Department of Materials Science and Engineering, Zhejiang University, Hangzhou 310027, China
Received 10 April 2006; accepted 25 April 2006
Abstract: The mechanism of the improvement of the cycling stability of the La-Mg-Ni-Co based hydrogen storage alloy electrode was systematically investigated. The results show that the cell volume expansion upon hydrogenation is obviously decreased after the partial substitution of Al for Ni. Therefore a decrease in the pulverization of the alloy particles is obtained, which leads to the decrease of the contact area of the fresh alloy surface with alkaline electrolyte and the increase of the charge/discharge efficiency. Moreover, the occurrence of Al in the alloy can create a dense Al oxide film on the surface of the alloy during charge/discharge cycling. This dense oxide film can prevent further oxidation of the active components in the alloy, which is believed to be the most important factor responsible for the improvement of the cycling stability of the La-Mg-Ni-Mn-Co-Al type alloy electrodes.
Key words: Ni/MH batteries; Li-Mg-Ni-Co based alloy; hydrogen storage alloys; cycling stability; Al substitution
1 Introduction
A new type R-Mg-Ni (R= rare earth or Ca element) system hydrogen storage alloy with high hydrogen storage capacity has been studied and reported in the present period[1-13]. Kadir et al[1-3] found that the maximum hydrogen storage capacity of (La0.65Ca0.35)(Mg1.32Ca0.68)Ni9 alloy reached 1.87% (mass fraction, the same below if not mentioned), and that of (Y0.5Ca0.5)(MgCa)Ni9 alloy went up to 1.98%. Meanwhile, it was also reported that some of the R-Mg-Ni based alloys exhibited promising electrode properties[4-13]. For example, the La-Mg-Ni-Co system AB3-3.5 type alloys were found to have high discharge capacity of 387-410 mA·h/g[4]. Moreover, PAN et al[5, 6] found that the alloys of La0.7Mg0.3(Ni0.85Co0.15)x (x=2.5-5.0) with x=3.5 had a maximum discharge capacity of 395.6 mA?h/g and good electrochemical kinetic properties. In addition, the proper heat treatment or the partial substitution of Mn for Ni could improve the overall properties of the La-Mg-Ni-Co type electrode alloys[8-13]. Especially, the cycling stability of the La-Mg-Ni-Co alloy could be obviously improved by the addition of Al, but the mechanism has not been clearly elucidated yet.
In this paper, in order to reveal the effect of Al on the electrochemical properties and microstructures of La-Mg-Ni-Co type alloys, the La0.7Mg0.3-Ni2.65-x-Mn0.1-Co0.75Alx (x=0, 0.3) alloy electrodes were selected and studied by XRD, SEM and AES measurements during their electrochemical cycling.
2 Experimental
La0.7Mg0.3Ni2.65-xMn0.1Co0.75Alx (x=0, 0.3) alloys were prepared by vacuum induction levitation melting on water-cooled copper crucible under argon atmosphere. High purity metal agents (≥99.0 %) were used. The alloy ingots were turned over and remelted twice for homogeneity. Then, part of the alloys were mechanically crushed and ground into powders with size of less than 47 μm.
Two kinds of test electrodes were prepared. One was by cold pressing 400 mg pure alloy powder up to a pressure of 20 MPa. The other was prepared by cold pressing a mixture of 100 mg alloy powders and 400 mg carbonyl nickel powders up to a pressure of 16 MPa. The mixture electrode was only used in the test of discharge capacity. Each alloy pellet was then interposed between two foamed Ni plates (55 mm×20 mm), the outer rims of which were tightly spot-welded to keep a sufficient contact with the foamed Ni plates. Electrochemical measurements were conducted in a standard tri-electrode cell consisting of a working electrode (MH electrode), a sintered Ni(OH)2/NiOOH counter electrode and a reference electrode of Hg/HgO, and a 6 mol/L KOH solution was used as electrolyte. Each electrode charged at 60 mA/g for 7 h followed by a 10 min intermission, subsequently being discharged at 60 mA/g to the cut-off potential of -0.6 V (vs Hg/HgO).
After a certain number of charging/discharging cycles, the electrodes were taken out and then washed with distilled water followed by drying in vacuum. To investigate the difference of the crystal structure, surface morphology and concentration profiles of the degraded electrodes before and after cycling, XRD (ARL, Cu Kα, 45 kV, 40 mA), SEM(Hitachi S-4700, FESEM) and AES(PHI-550, 3 kV, 10 μA) were performed, respec- tively. The electrode surface was sputtered with Ar+ on an area of 1.5 mm×1.5 mm at 4 kV and 15 mA.
3 Results and discussion
Fig.1 shows the variation of the discharge capacity of the La0.7Mg0.3Ni2.65-xMn0.1Co0.75Alx (x=0, 0.3) as-cast alloy electrodes vs cycle number at 303 K. It can be seen that the cycling stability of the alloy electrode with Al (x=0.3) is markedly improved compared with that of the alloy without Al. After 100 charge/discharge cycling, the discharge capacity retention (C100/Cmax) of the alloy electrodes increases from 32.0% (x=0) to 73.8% (x=0.3), which is considerably beneficial to the practical application of the La-Mg-Ni-Co type hydrogen storage electrode alloy in the Ni/MH secondary batteries though the initial discharge capacity decreased from about 400 to 350 mA·h/g.
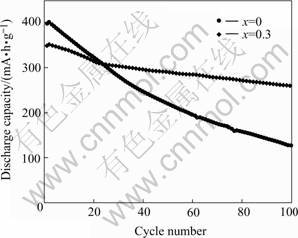
Fig.1 Discharge capacity vs cycle number of La0.7Mg0.3Ni2.65-x- Mn0.1Co0.75Alx (x=0, 0.3) alloy electrodes at 303 K
Fig.2 shows the XRD patterns of the La0.7Mg0.3Ni2.65-xMn0.1Co0.75Alx (x=0, 0.3) alloys after charging. LIU et al[14] reported that the La0.7Mg0.3Ni2.65-x-
Mn0.1Co0.75Alx (x=0, 0.3) as-cast alloys mainly consist of (La,Mg)Ni3 phase and LaNi5 phase in the above alloys still maintain the rhombohedral PuNi3-type structure and hexagonal CaCu5-type structure, respectively. Moreover, from Fig.2, it can be seen that the diffraction peaks for the hydride phase in the alloy with Al move toward higher angles compared with the alloy without Al, which indicates that the cell volume upon hydrogenation decreases after the partial substitution of Al for Ni. The lattice parameters and unit cell volumes of the hydride phases of (La,Mg)Ni3 phase and LaNi5 phase calculated by the Rietveld method are listed in Table 1. It can be seen that the cell volume expansion ratio (?V/V) of (La, Mg)Ni3-H phase decreases from 19.58% to 14.38%, and that of LaNi5-H phase decreases from 18.62% to 15.13%. This phenomenon indicates that the alloy with Al can undergo a smaller cell volume expansion and contraction during the charge/discharge cycling process and a subsequent lower pulverization of the alloy particles as well. Thus, the oxidation/corrosion of the active constituents in the alloys decreases and the electric conductivity increases, which leads to the improvement of the cycling stability of the alloy electrodes.

Fig.2 XRD patterns of La0.7Mg0.3Ni2.65-xMn0.1Co0.75Alx (x=0, 0.3) alloys after charging: (a) x=0.3; (b) x=0
Fig.3 shows the SEM images of the La0.7Mg0.3Ni2.65-x-Mn0.1Co0.75Alx (x=0, 0.3) alloys before and after cycling. As can be seen from Fig.3, with the increasing cycle number, the alloy particles are gradually pulverized due to the cell volume expansion and contraction during charging/discharging cycles. Furthermore, it can also be seen that the particle size of the alloy with Al is larger than that of the alloy without Al under the same condition. This result indicates that the process of the pulverization is inhibited and the rate of pulverization is decreased by the partial substitution of Ni by Al. In addition, it can be seen that the surface is very fresh and
Table 1 Characteristics of hydride phases in La0.7Mg0.3Ni2.65-xMn0.1Co0.75Alx (x=0, 0.3) alloys

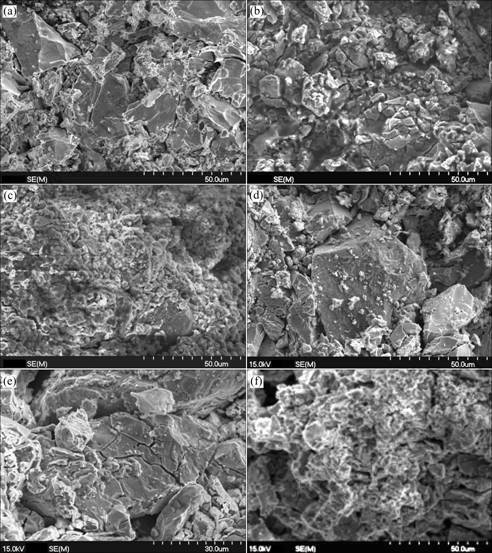
Fig.3 SEM images of La0.7Mg0.3Ni2.65-xMn0.1Co0.75Alx alloys before and after cycling: (a) x=0, as-cast; (b) x=0, after 30 cycles; (c) x=0, after 80 cycles; (d) x=0.3, as-cast; (e) x=0.3, after 30 cycles; (f) x=0.3, after 80 cycles
activated for the as-cast alloys. After electrochemical charge/discharge cycling, the particle surface becomes rough, and a passive layer forms. However, the oxidation/corrosion progress of the active components is obviously inhibited after partial substitution of Ni by Al. It is obvious that, after 80 cycles, the surface of the alloy without Al has been fully covered by the passive layers (Fig.3(c)), but the grey alloy matrix can be clearly observed for the alloy with Al as shown in Fig.3(f), which is also one of the reasons for the improvement of the cycling stability for the alloy electrode after the partial substitution of Al for Ni.
Figs.4 and 5 show the AES profiles of the La0.7Mg0.3Ni2.65-xMn0.1Co0.75Alx (x=0, 0.3) alloy electro-
des before and after cycling. For the alloy without Al, it can be seen that the oxygen content on the alloy surface increases with cycling, which indicates that the oxidation/corrosion of the alloy components becomes more and more serious during the charge/discharge cycling process. However, in the case of Ni being partially substituted by Al, the oxygen content on the alloy surface is only slightly changed, which implies that
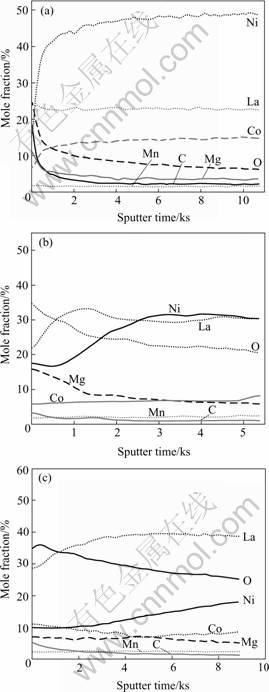
Fig.4 AES profiles of La0.7Mg0.3Ni2.65Mn0.1Co0.75 alloy electrodes before and after cycling: (a) As cast; (b) After 10 cycles; (c) After 30 cycles
the oxidation/corrosion of the active components of the alloy is effectively inhibited. From Figs.4(a) and 5(a), it is found that the oxygen content decreases drastically inside the alloy although it is high on the surface, which indicates that the high oxygen content on the alloy surface can be attributed to the adsorption of oxygen during exposure of the alloy in the air.
It can also be found from Figs.4(b) and 5(b) that Mg content on the surfaces of the two alloys strongly
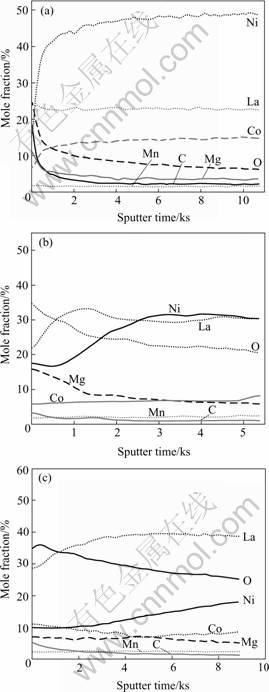
Fig.5 AES profiles of La0.7Mg0.3Ni2.35Mn0.1Co0.75Al0.3 alloy electrodes before and after cycling: (a) As cast; (b) After 10 cycles; (c) After 30 cycles
increases after 10 cycles, which exhibits that Mg is firstly oxidized/ corroded for La-Mg-Ni-Co-based alloy electrodes, and subsequently forms a loose and permeable Mg(OH)2 oxide layer on the alloy surface during the initial cycling stages. This oxide layer is very loose and has less protection to the alloy from being further corroded[15, 16], leading to the decrease of quantities of the active elements of Mg and La in the further cycling process, and consequently, lowering the discharge capacity of degradation as shown in Fig.1.
However, from Fig.5(c), it is seen that Al content on the alloy surface increases for the alloy with Al after 30 cycles. It can be concluded that Al is also oxidized/corroded and an Al oxide film gradually forms during cycling. Such an oxide film is very dense and protective[17]. Once Al oxide film forms on the alloy surface, further oxidation of the active components is inhibited, and the anti-oxidation/corrosion capability of the alloy is increased. The formation of the Al oxide film is concluded to be the main factor of the improvement of the cycling stability of the alloy with Al during electrochemical cycling.
4 Conclusions
The improvement of the cycling stability of the La-Mg-Ni-based alloy electrodes by the partial substitution of Al for Ni can be attributed to the two factors, one is the decrease of the pulverization of the alloy particles, the other is the increase of the anti-oxidation/corrosion of the alloy due to the formation of a dense Al oxide film during cycling. After Ni is partially substituted by Al, the cell volume expansion ratio, ΔV/V, of the alloy upon hydrogenation decreases and the alloy particles pulverization is inhibited. The dense Al oxide film prevents further oxidation of the active components in the alloy, which is concluded to be the most important reason for the improvement of cycling stability of the La0.7Mg0.3Ni2.35Co0.75Al0.3 alloy electrode.
References
[1] Kadir K, Sakai T, Uehara I. Synthesis and structure determination of a new series of hydrogen storage alloys: RMg2Ni9 (R=La, Ce, Pr, Nd, Sm and Gd) built from MgNi2 Laves-type alternating with AB5 layers [J]. J Alloys Compd, 1997, 257(1-2): 115-121.
[2] Kadir K, Sakai T, Uehara I. Structural investigation and hydrogen capacity of YMg2Ni9 and (Y0.5Ca0.5)(MgCa)Ni9: new phase in the AB2C9 system isostructural with LaMg2Ni9 [J]. J Alloys Compd, 1999, 287(1-2): 264-270.
[3] Kadir K, Sakai T, Uehara I. Structural investigation and hydrogen capacity of LaMg2Ni9 and (La0.65Ca0.35)(Mg1.32Ca0.68)Ni9 of the AB2C9 type structure [J]. J Alloys Compd, 2000, 302(1-2): 112-117.
[4] Kohno T, Yoshida H, Kawashima F, Inaba T, Sakai I, Yamamoto M, Kanda M. Hydrogen storage properties of new ternary system alloys: La2MgNi9, La5Mg2Ni23, La3MgNi14 [J]. J Alloys Compd, 2000, 311(2): L5-L7.
[5] PAN H G, LIU Y F, GAO M X, LEI Y Q, WANG Q D. A study of the structural and electrochemical properties of La0.7Mg0.3(Ni0.85Co0.15)x (x=2.5-5.0) hydrogen storage electrode alloys [J]. J Electrochem Soc, 2003, 150(5): A565-A570.
[6] Pan H G, Liu Y F, Gao M X, Zhu Y F, Lei Y Q, Wang Q D. An investigation on the structural and electrochemical properties of La0.7Mg0.3(Ni0.85Co0.15)x (x=3.15-3.80) hydrogen storage electrode alloys [J]. J Alloys Compd, 2003, 351(1-2): 228-234.
[7] Liu Y F, Pan H G, Jin Q W, Li R, Li S Q, Lei Y Q. Effects of temperatures on the electrochemical properties of the La-Mg-Ni-Co-Mn hydrogen storage electrode alloy [J]. The Chinese Journal of Nonferrous Metals, 2005, 15(5): 802-808.(in Chinese)
[8] Liu Y F, Pan H G, Gao M X, Zhu Y F, Lei Y Q. Hydrogen storage and electrochemical properties of the La0.7Mg0.3Ni3.825-x-Co0.675Mnx hydrogen storage electrode alloys [J]. J Alloys Compd, 2004, 365(1-2): 246-252.
[9] Liu Y F, Pan H G, Gao M X, Zhu Y F, Lei Y Q, Wang Q D. The effect of Mn substitution for Ni on the structural and electrochemical properties of La0.7Mg0.3Ni2.55-xCo0.45Mnx hydrogen storage electrode alloys[J]. Int J Hydrogen Energy, 2004, 29(3): 297-305.
[10] Liu Y F, Pan H G, Gao M X, Zhu Y F, Lei Y Q, Wang Q D. Electrochemical studies on La0.7Mg0.3Ni3.4-xCo0.6Mnx metal hydride electrode alloys [J]. Materials Chemistry and Physics, 2004, 84(1): 171-181.
[11] Pan H G, Liu Y F, Gao M X, Zhu Y F, Lei Y Q, Wang Q D. The structural and electrochemical properties of the La0.7Mg0.3-Ni2.975-x-Co0.525Mnx hydrogen storage electrode alloys[J]. J Electro-chem Soc, 2004, 151(3): A374-A380.
[12] Liu Y F, Pan H G, Gao M X, Zhu Y F, Lei Y Q. Influence of Mn content on the structural and electrochemical properties of the La0.7Mg0.3Ni4.25-xCo0.75Mnx hydrogen storage alloys[J]. Mater Sci Eng A, 2004, A372(1-2): 163-172.
[13] Liu Y F, Pan H G, Gao M X, Zhu Y F, Lei Y Q. Influences of heat treatment on electrochemical characteristics of La0.75Mg0.25Ni2.8Co0.5 hydrogen storage electrode alloy [J]. Trans Nonferrous Met Soc China, 2003, 13(1): 25-28.
[14] Liu Y F, Pan H G, Li R, Lei Y Q. Effects of Al on cycling stability of a new rare-earth Mg-based hydrogen storage alloy [J]. Materials Science Forum, 2005, 475-479: 2457-2461.
[15] Liu W H, Lei Y Q, Sun D L, Wu J, Wang Q D. A study of the degradation of the electrochemical capacity of amorphous Mg50Ni50 alloy [J]. J Power Soc, 1996, 58(2): 243-247.
[16] Zhang Y, Chen L X, Lei Y Q, Wang Q D. The reduction of cycling capacity degradation of Mg–Ni-based electrode alloys by Fe substitution [J]. Int J Hydrogen Energy, 2002, 27(5): 501-506.
[17] Sakai T, Miyamura H, Kuriyama N, Kato A, Oguro K, Ishikawa H. The influence of small amounts of added elements on various anode performance characteristics for LaNi2.5Co2.5-based alloys [J]. J Less-Common Met, 1990, 159: 127-129.
[18] Jurczyk M, Nowak M, Jankowska E, Jakubowicz J. Structure and electrochemical properties of the mechanically alloyed La(Ni,M)5 materials [J]. J Alloys Compd, 2002, 339(1-2): 339-343.
(Edited by CHEN Wei-ping)
Foundation item: Project (50131040) supported by the National Natural Science Foundation of China
Corresponding author: PAN Hong-ge; Tel: +86-571-87952576; Fax: +86-571-87951152; E-mail: honggepan@zjuem.zju.edu.cn